Compressie-RTM voor de productie van toekomstige aerostructuren
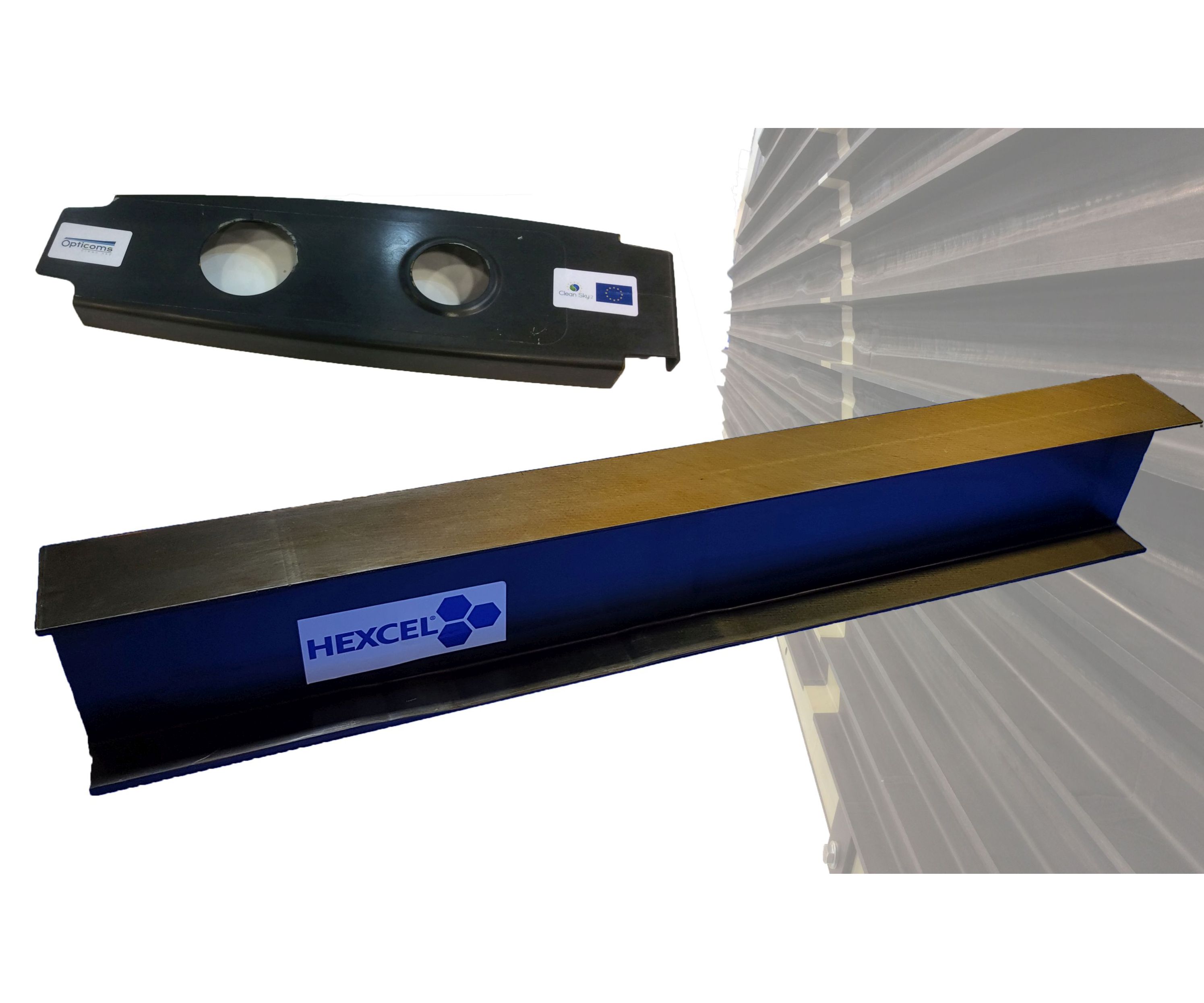
Composieten hebben een vaste plaats veroverd in de casco's van commerciële vliegtuigen omdat ze sterke, lichtgewicht constructies mogelijk maken die lagere onderhoudskosten opleveren dan metaal. De huidige prognoses voor de volgende generatie vliegtuigen met zowel brede als smalle romp laten een aanhoudende groei zien in composiet casco's, maar alleen als materialen en processen kunnen voldoen aan uitdagende doelstellingen voor lage kosten en hoge productiesnelheden. Hoewel autoclaaf-uitgeharde epoxy-prepreg tot op heden oppermachtig is geweest in casco's van koolstofvezelversterkt polymeer (CFRP), streven ontwikkelaars van vliegtuigen van de volgende generatie agressief naar out-of-autoclave (OOA)-technologieën met geïntegreerde automatisering en inline-inspectie als belangrijke factoren voor toekomstige Industrie 4.0-productie.
Apparatuur- en automatiseringsleverancier Techni-Modul Engineering (Coudes, Frankrijk) en zijn Amerikaanse dochteronderneming Composite Alliance Corp. (Dallas, Texas, VS) zijn een partnerschap aangegaan met de Britse en Franse business units van leverancier van geavanceerde materialen Hexcel (Stamford, Conn., VS) om geautomatiseerde OOA-productie van CFRP-ribben en stringers te demonstreren. De onderdelen zijn gemaakt met geautomatiseerde voorvorming van Hexcel droge koolstofvezelversterkingen en een compressieharsoverdrachtgietproces (C-RTM) dat snelle infiltratie van Hexcel HexFlow RTM6 vloeibare epoxyhars biedt om onderdelen te produceren met 60% vezelvolume en minder dan 1% lege ruimten in een cyclus van 2,5 tot 3,0 uur die kan worden geschaald om meerdere onderdelen te produceren voor een productie met hoge snelheid.
Ontwikkeling van droge versterkingen
"We zien vloeibaar composiet gieten (LCM) als een antwoord op de drieledige uitdaging om kosten te verlagen, prijsklaar te zijn en primaire structuurprestaties te leveren", legt Rémy Pagnac, uit. Technische ondersteuningsingenieur van Hexcel voor gieten van vloeibare composieten. Hexcel heeft zijn HiMax non-crimp stof (NCF) en HiTape unidirectionele (UD) koolstofvezelmaterialen ontwikkeld om te voldoen aan de prestatiebehoeften van de primaire structuur bij het gebruik van LCM-processen. Met HiMax kunnen grote, platte structuren zoals wingskins snel worden gelegd, terwijl HiTape op maat gemaakte layups mogelijk maakt voor grote, complexe structuren met minimaal afval. "We kunnen eigenschappen bereiken die gelijk zijn aan de nieuwste generatie UD-prepregs", voegt Pagnac toe.
Hexcel heeft gewerkt om het volume te verminderen en de drapeerbaarheid te verbeteren met HiMax NCF, inclusief een fijn, 20 dTex steekgaren. HiMax-materialen worden gemaakt in de vorige Formax-fabriek in Leicester, VK, die Hexcel in 2016 verwierf. De lichtgewicht multiaxiale multi-axiale multi-assen die in deze fabriek worden geproduceerd, hebben al een lange geschiedenis in het leveren van oplossingen voor veeleisende toepassingen zoals racejachten, supercars en Formule 1 1 raceauto's. Nu zijn NCF-materialen gebruikt in een vleugeldemonstratieproject dat is voltooid door Airbus Defense and Space (Airbus DS, Cadiz, Spanje) en Danobat (Elgoibar, Spanje) met behulp van de Automated Dry Material Placement (ADMP) -technologie van laatstgenoemde - een soort geautomatiseerde vezelplaatsing (AFP) voor NCF (zie "Levensvatbaarheid bewijzen voor infusie van droge weefsels voor grote aerostructuren") - en in het door Airbus gesponsorde ZAero-project voor foutloze CFRP-structuren zoals met stringers verstijfde wingskins (zie "Zero-defect fabricage van composietonderdelen ”).
Met zowel HiMax als HiTape integreert Hexcel lagen van dunne, lichtgewicht thermoplastische filamentsluiers die als bindmiddel fungeren, waardoor de noodzaak voor poederbindmiddelen die historisch werden gebruikt in droge materialen voor voorvormen en vloeibaar gieten, wordt geëlimineerd. Voor HiMax is deze sluier tussen NCF-lagen geschoven; voor HiTape wordt de sluier aan beide zijden van de unitape van koolstofvezel aangebracht. “Hierdoor hoef je geen poederbindmiddel te gebruiken om de UD-lagen op hun plaats te houden”, legt Pagnac uit. “HiTape is gekalibreerd en is geen slit-tape, dus er is geen fuzz en er is minder variatie in breedte voor verbeterde AFP-verwerking. De thermoplastische sluier voegt ook taaiheid toe aan het uiteindelijke laminaat en we hebben aangetoond dat we hoge materiaalafzettingssnelheden kunnen bereiken met de volgende generatie AFP-machines.” In een SAMPE-paper van mei 2015 beschrijft Hexcel een voorvorm met enkele kromming, vervaardigd met HiTape van 0,25 inch breed, aangebracht met een laser-uitgeruste Coriolis Composites (Quéven, Frankrijk) AFP-machine met een lay-upsnelheid van 1 meter/seconde. Het heeft ook gewerkt met AFP-apparatuur van Electroimpact (Mukilteo, Wash., V.S.) om afzettingssnelheden tot 150 kilogram/uur aan te tonen voor een aerodynamische constructie van volledige grootte.
Afb. 1 compressie-RTM
Bij C-RTM wordt de droge preform in een RTM-mal geplaatst, maar de mal is slechts gedeeltelijk gesloten, waardoor er een opening overblijft tussen de droge voorvorm en het bovenste matrijsoppervlak. Vervolgens wordt vacuüm aangebracht, hars wordt geïnjecteerd en de pers sluit de opening in de mal, waarbij de vloeibare hars in de z-richting over het hele onderdeel naar beneden in de voorvorm wordt geduwd. Bron | Hexcel

C-RTM aanpassen voor ruimtevaart
C-RTM werd voor het eerst geïntroduceerd met hogedruk-RTM (HP-RTM) voor autocomposieten. Net als bij conventionele RTM, houdt C-RTM in dat een voorvorm van droge vezels in een bijpassende metalen mal wordt geplaatst, vloeibare hars in de voorvorm wordt geïnjecteerd en vervolgens warmte en druk wordt uitgeoefend met behulp van een aangedreven pers. Bij C-RTM is de mal echter slechts gedeeltelijk gesloten, waardoor er een opening overblijft tussen de droge voorvorm en het bovenste matrijsoppervlak (Fig. 1). Vervolgens wordt vacuüm aangebracht, een precieze dosis gemengde hars wordt geïnjecteerd en de pers sluit de opening in de mal, waardoor de vloeibare hars in de z-richting over het hele onderdeel in de voorvorm wordt gedwongen. "Dit is veel sneller dan de hars in-plane door het onderdeel te injecteren", legt Techni-Modul Engineering procesingenieur Thomas Chevallet uit.
Techni-Modul Engineering zag een kans om C-RTM aan te passen voor de lucht- en ruimtevaart tijdens zijn rol als partner in het Clean Sky 2 "Optimized Composite Structures" (OPTICOMS)-project. OPTICOMS is georganiseerd in Work Package B-1.2 ("Betaalbare composietstructuren") en heeft tot doel de productiekosten van kleine vliegtuigen (bijv. regionale straalvliegtuigen) te verlagen via geïntegreerde structuren en geautomatiseerde productie, waarbij zowel prepreg- als vloeibare harsmethoden worden onderzocht. OPTICOMS heeft een composiet vleugeldemonstrator ontworpen die bestaat uit een bovenvleugel met drie rondhouten, geproduceerd als een geïntegreerde structuur in een one-shot-proces. De full-scale vleugel (Fig. 2) maakt deel uit van een AIRFRAME Innovative Technology Demonstrator (ITD) voor het evalueren en rijpen van technologieën naar technologiegereedheidsniveau (TRL) 6 voor vliegtuigen van de volgende generatie die vanaf 2025 in productie zijn. Israel Aerospace Industries (Lod, Israël) werd in juli 2016 geselecteerd als coördinator voor OPTICOMS. Het consortium omvat ook OEM voor kleine vliegtuigen Piaggio Aerospace (Savona, Italië), Techni-Modul Engineering en AFP-apparatuurleveranciers Coriolis Composites en Danobat.
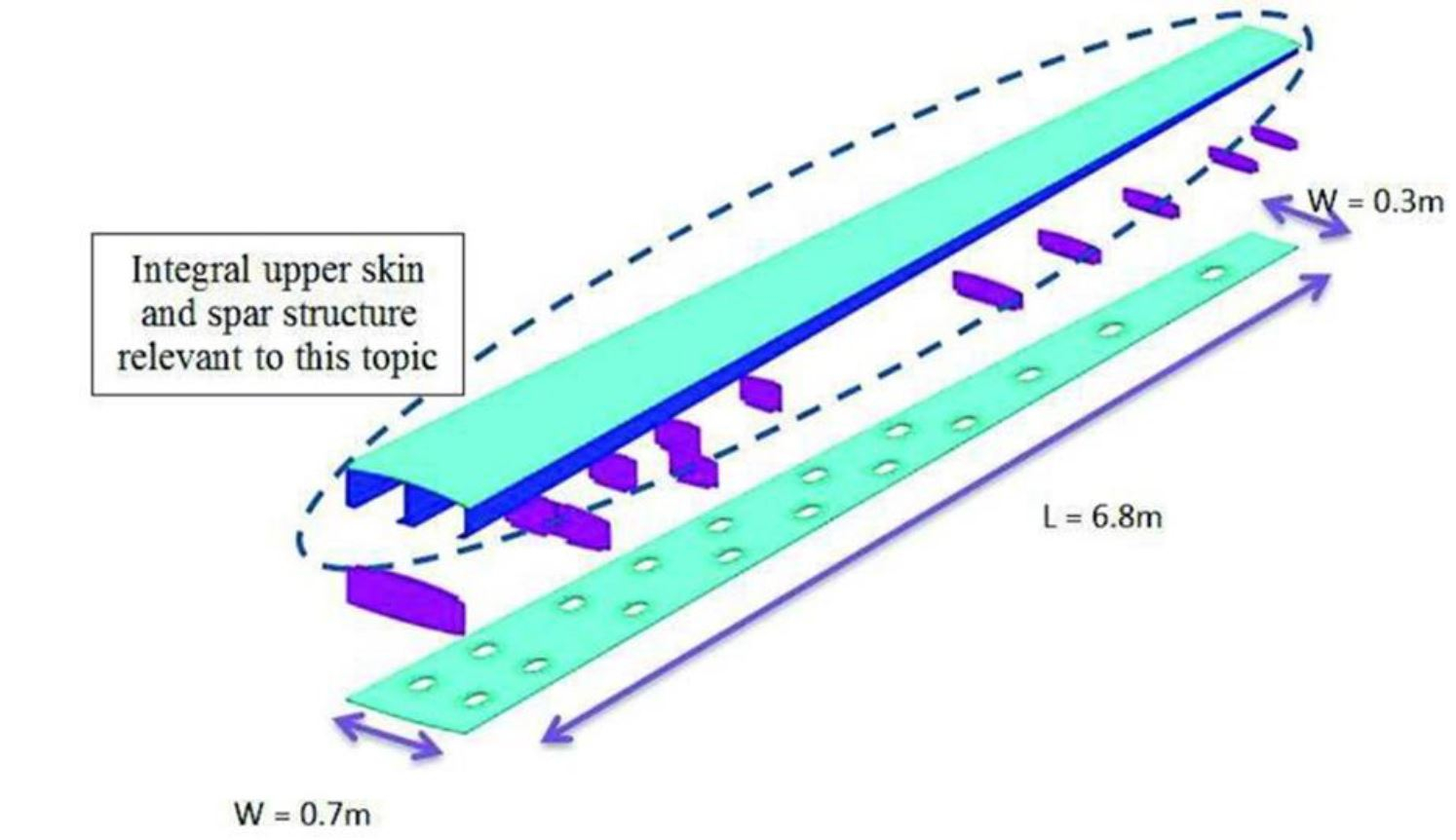
Afb. 2 Clean Sky 2 OPTICOMS rib
Techni-Modul is een partner in het Clean Sky 2 "Optimized Composite Structures" (OPTICOMS)-project, dat een composietvleugeldemonstrator heeft ontworpen die bestaat uit een onderste wingskin, meerdere ribben en een bovenste wingskin met drie rondhouten. Deze laatste wordt geproduceerd als een geïntegreerde structuur in een one-shot-proces. De demonstrator zal worden geëvalueerd voor vliegtuigen van de volgende generatie die vanaf 2025 in productie zullen zijn. Bron | Schone lucht 2
"C-RTM was goed bekend in de industrie", legt Chevallet uit, "maar met HP-RTM is nog steeds een grote pers nodig. Onze ontwikkeling was om C-RTM aan te passen voor snelle injectie met lagere drukken, waardoor een goedkopere productie van lucht- en ruimtevaartonderdelen mogelijk wordt met zeer strikte eisen voor een hoog vezelvolume, vezeluitlijning en weinig luchtruimte. De injectietijd voor de 0,7 meter lange en 0,2 meter brede vleugelrib in het OPTICOMS-project werd teruggebracht van 40 naar vijf minuten. In een apart testprogramma voor een I-beam stringer van 900 millimeter lang en 150 millimeter hoog, werd de injectietijd verkort van één uur tot minder dan vijf minuten.

"Deze vermindering van de injectietijd die door C-RTM wordt geboden, zou nog groter zijn voor grote onderdelen zoals volledige wingskins of rotorbladen voor helikopters", voegt Chevallet toe. Hij merkt op dat C-RTM ook injectie van harsen met een hoge viscositeit mogelijk maakt, evenals injectiesystemen met lagere druk en persen met een lager tonnage, wat de kosten verlaagt. "De matrijsdruk tijdens C-RTM is slechts 6 bar, veel lager dan wat wordt gebruikt in HP-RTM", legt Chevallet uit. "Het proces levert composieten van ruimtevaartkwaliteit op, maar werkt ook goed voor grote, dunne onderdelen en kleinere, complex gevormde onderdelen."
Geautomatiseerde voorvormen
Hoewel snellere, goedkopere harsinjectie en OOA-gieten belangrijke onderdelen zijn van deze benadering voor een meer betaalbare productie van aerocomposieten, vereist de procesketen nog steeds meerdere stappen voor het snijden en leggen van materialen en voorvormen. “Voor ons ging OPTICOMS ook over automatisering”, zegt Chevallet. Techni-Modul Engineering leverde niet alleen een C-RTM injectiesysteem voor het OPTICOMS project, maar ook een pick-and-place robot en een hot drapeforming (HDF) machine, allemaal geïntegreerd in een volledig geautomatiseerde productiecel.
Kort nadat OPTICOMS in 2016 van start ging, won Techni-Modul Engineering-dochteronderneming CAC de ACE Equipment and Tooling Innovation Award in de productiecategorie voor zijn geautomatiseerde 3D-voorvormcel op CAMX 2016 (26-29 september, Anaheim, Californië, VS). In staat om 3D-preforms te produceren van droge vezels of prepreg, gebruikte de cel vacuümzuiggrijpers om gesneden lagen op te pakken, te plaatsen en te vouwen op een verwarmde preform-matrijs. Techni-Modul Engineering en CAC hebben software ontwikkeld om de gesneden lagen van 2D-materialen voor te bereiden op het vormen tot complexe en ontwikkelbare oppervlakken. Deze cel is verder ontwikkeld in OPTICOMS en het I-beam testproject.
Stap 1
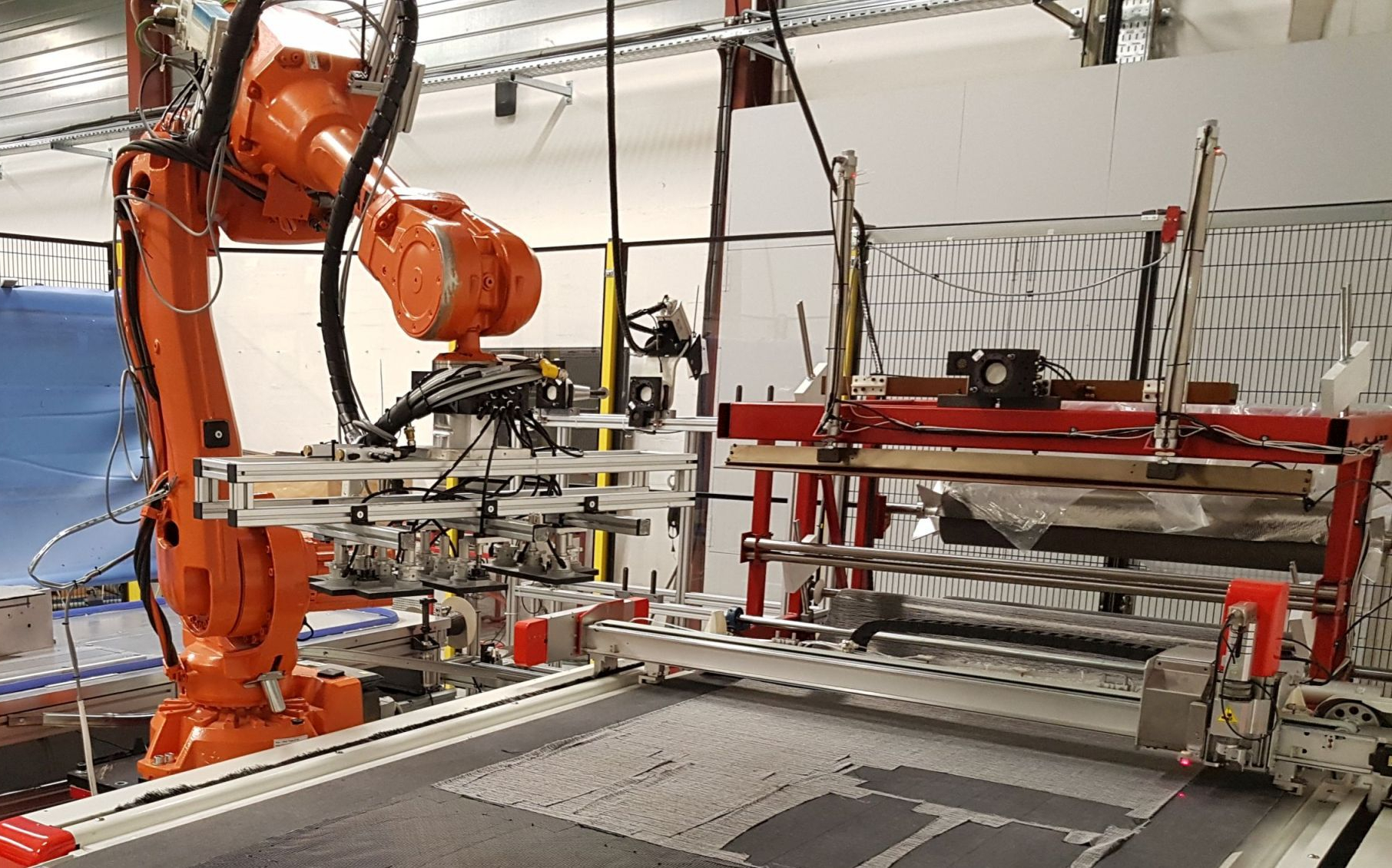
Bron, alle stapafbeeldingen | Techni-Modul Engineering
In de geautomatiseerde cel Techni-Modul Engineering verwijdert een pick-and-place-robot de lagen van een automatische snijplotter en brengt deze aan op een verwarmd voorvormgereedschap.
Stap 2

De voorvormgereedschappen bevinden zich op een verdichtingstafel met een scharnierend herbruikbaar vacuümmembraan (blauw, links) dat wordt gebruikt om elke 5-8 lagen een verwarmde debulk te voltooien tijdens het leggen.
Stap 3
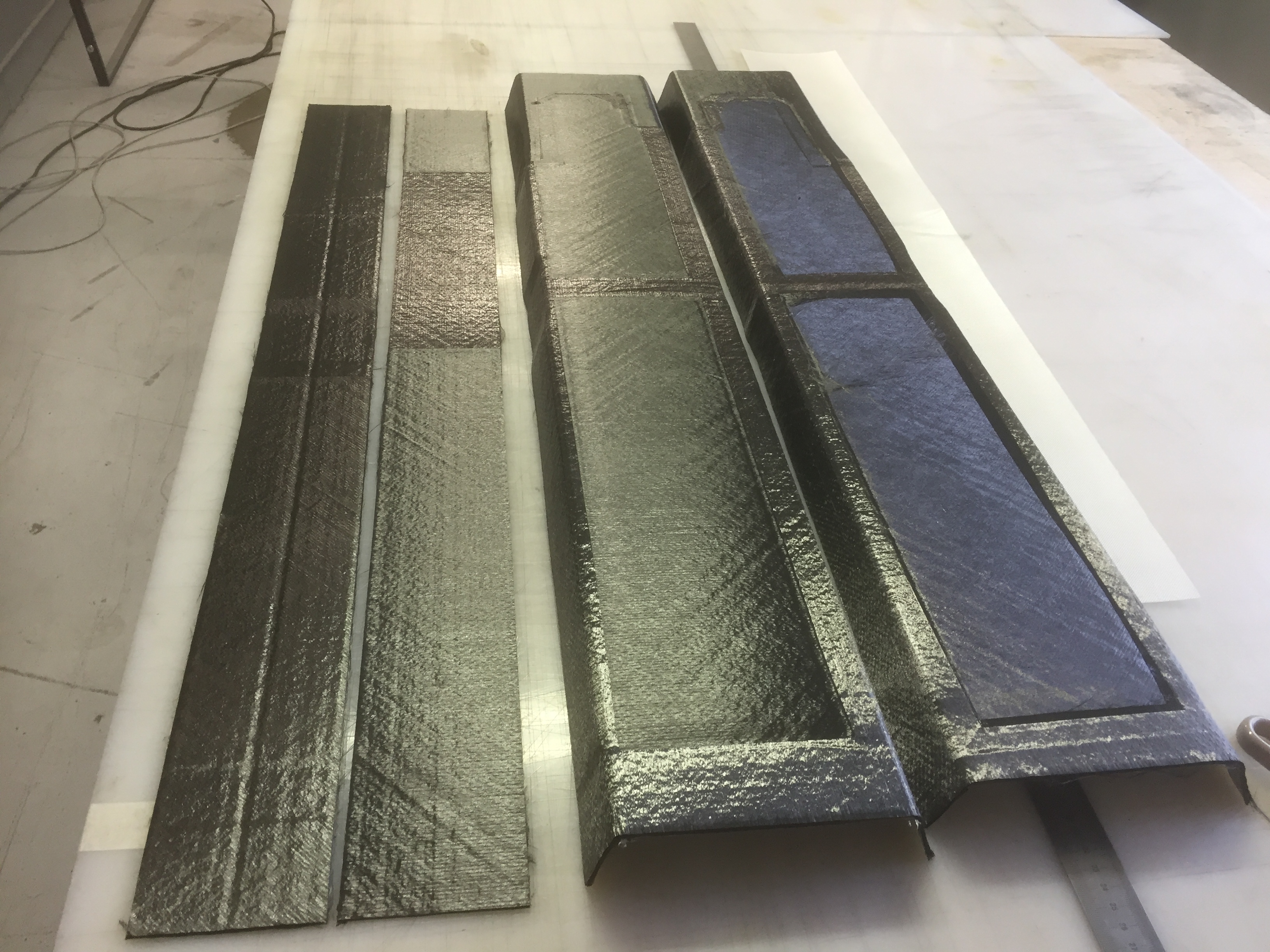
Elke voorvormcyclus van de stringer produceert één voorvorm met C-balk (twee omvatten het I-balkweb) en één voorvorm met platte flens. Twee sets die nodig zijn voor elke I-beam stringer worden hier getoond.
Stap 4
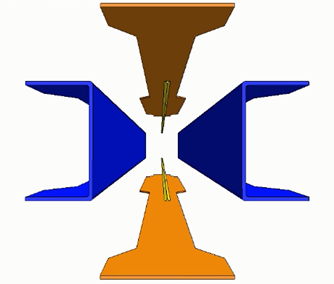
De vier voorvormen van de I-beam stringer worden in de RTM-mal geplaatst, vacuüm wordt aangebracht en de harsinjectie is in 5 minuten voltooid.
Stap 5
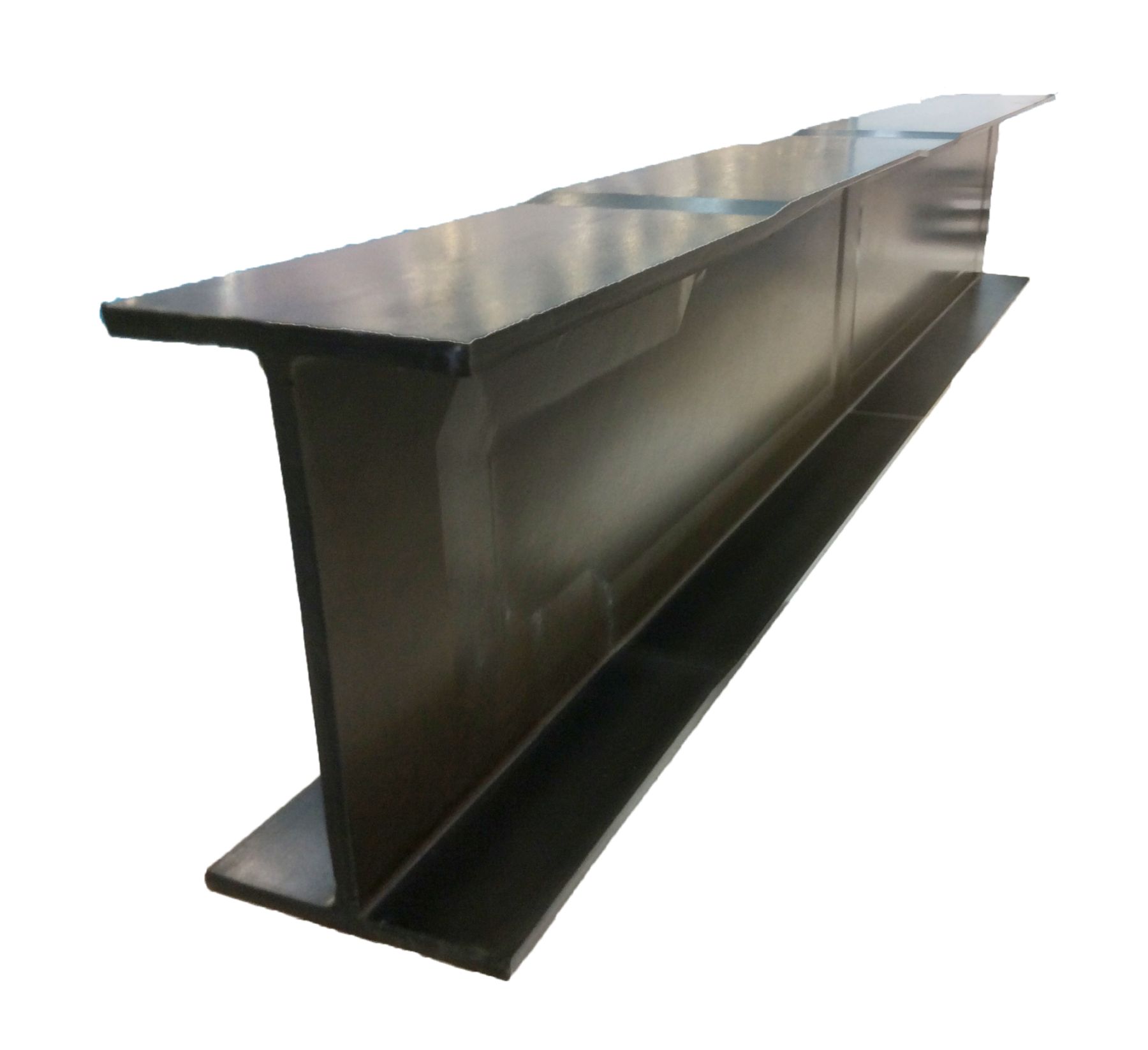
Na een uitharding van 90 minuten wordt de stringer uit de vorm gehaald en wordt de harsflits getrimd voor een volledige deelcyclus van 4,5 uur.

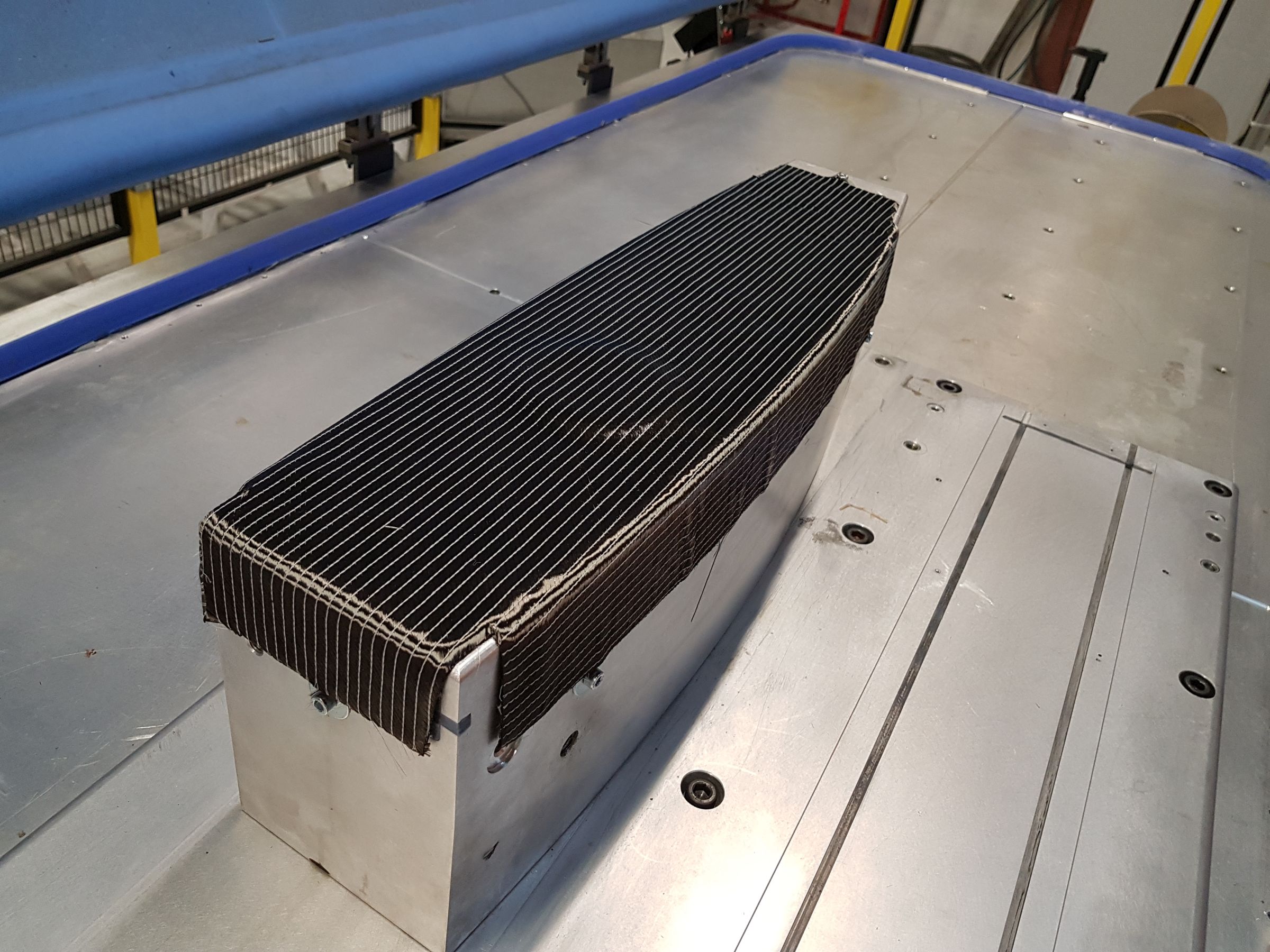
Een robot plaatst snijlagen op het verwarmde voorvormgereedschap. Elke 5-8 lagen wordt een verwarmde debulk voltooid om de preform te verdichten.

Voor het debulken wordt een blauwe lossingsfilm aangebracht.
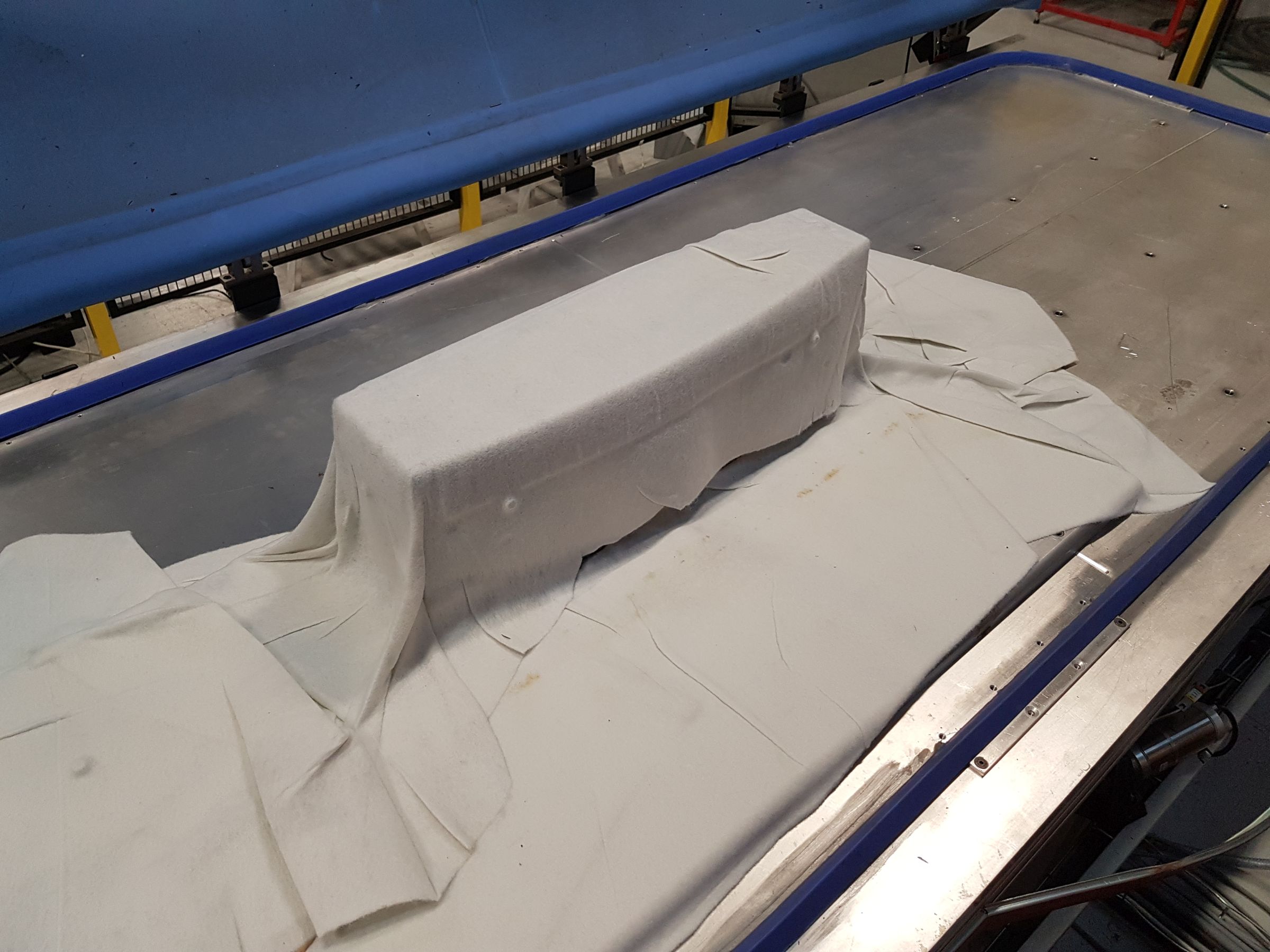
Ademhaling wordt gebruikt om lucht over de voorvorm te verwijderen.
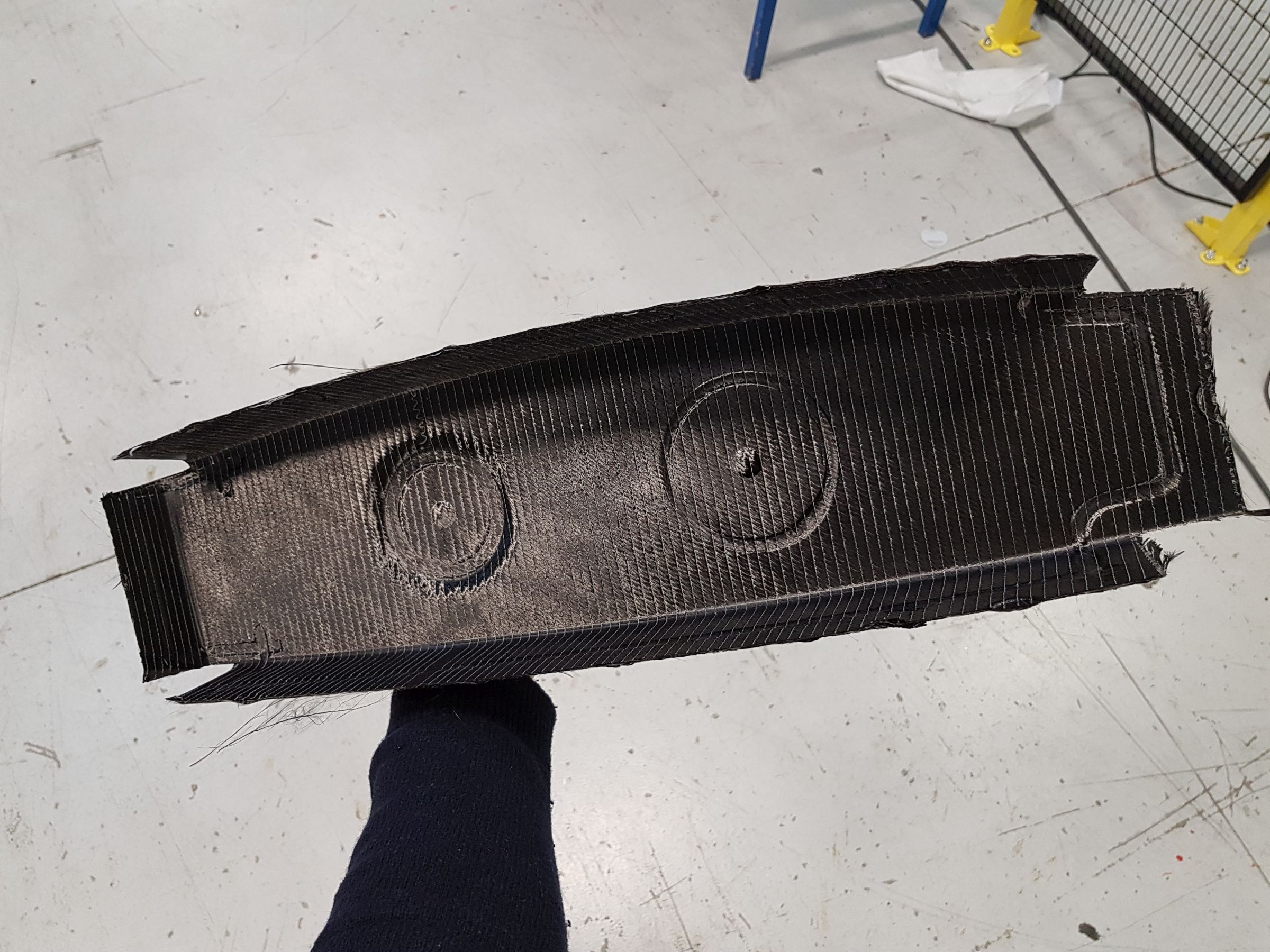
Na de laatste debulk wordt de preform op het gereedschap afgekoeld en worden de uitsnijdingen bijgesneden (hieronder).
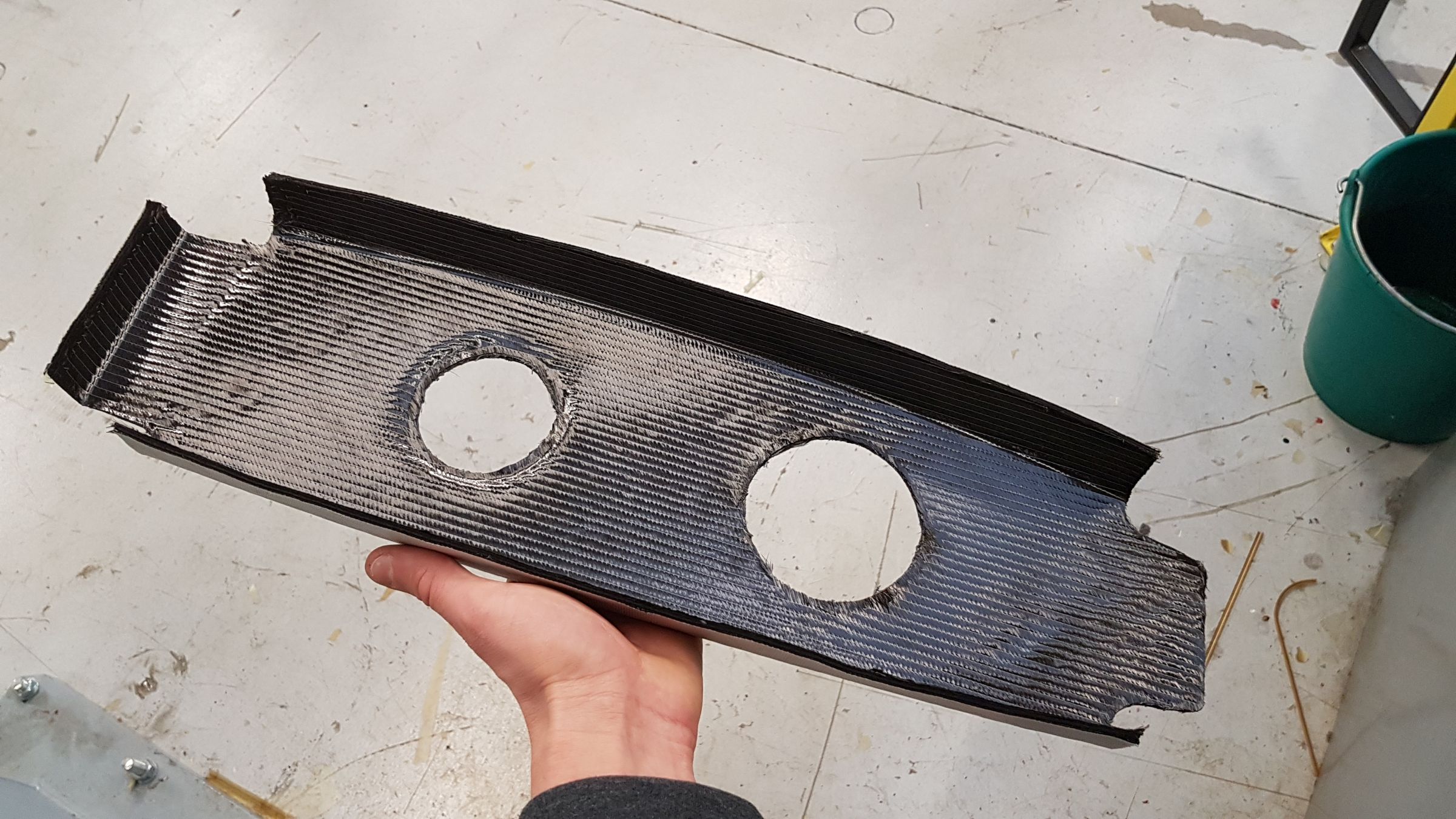
"We hebben het klassieke handmatige stapelen van lagen geautomatiseerd met behulp van robotpick and place", zegt Chevallet. "De robot pakt de lagen op van een geautomatiseerde snijder en brengt deze over naar het verwarmde voorvormgereedschap dat op een verdichtingstafel staat [stap 1 en 6]." Een peel-ply (blauwe film in stap 6), ontluchter (wit materiaal in stap 6) en scharnierend herbruikbaar vacuümmembraan (lichtblauw links in stap 2 en 6) worden aangebracht, gevolgd door vacuüm en warmte om de lucht voor te vormen en te verwijderen uit de textielstapel (hot drape-vorming, HDF) terwijl de dunne thermoplastische sluiers worden gesmolten om een verdichte voorvorm te creëren.
"Hoeveel lagen u in één keer kunt verdichten, hangt af van het materiaal en de vorm van het onderdeel", legt Chevallet uit. “Voor onderdelen met een lage kromming, zoals een wingskin, zou je eventueel elke 50 lagen kunnen verdichten. De OPTICOMS-rib heeft echter hoeken van 90 graden en de test I-beam stringer heeft T-vormen, dus je moet oppassen dat je tijdens het voorvormen geen plooien in de lagen vormt.” Hij voegt eraan toe dat dergelijke complexe vormen mogelijk elke 5-8 lagen verdichting vereisen, maar nog steeds deel kunnen uitmaken van een geïndustrialiseerd proces met grote volumes:stapellagen, 2 minuten HDF verdichting, heropenen en opnieuw stapelen, gevolgd door herhaalde verdichtingscycli met een laatste afkoeling van de preform op het gereedschap voordat deze naar de RTM-matrijs wordt overgebracht.
"Onze geautomatiseerde cel kan met een snelheid van 15 seconden per laag worden geplaatst", merkt Chevallet op. "De lay-up voor de OPTICOMS-rib, met in totaal minder dan 20 lagen, was in 20 minuten voltooid." Lay-up voor de I-beam stringer was langer — 45 minuten vanwege zijn complexe vorm en laminaatstapel, inclusief diktevariaties van 1,2 tot 6 millimeter. "Dit is nog steeds veel sneller dan handmatige processen en vermindert het risico op fouten, verhoogt de herhaalbaarheid en kwaliteit en verlaagt de kosten", voegt hij eraan toe.
Stap 7
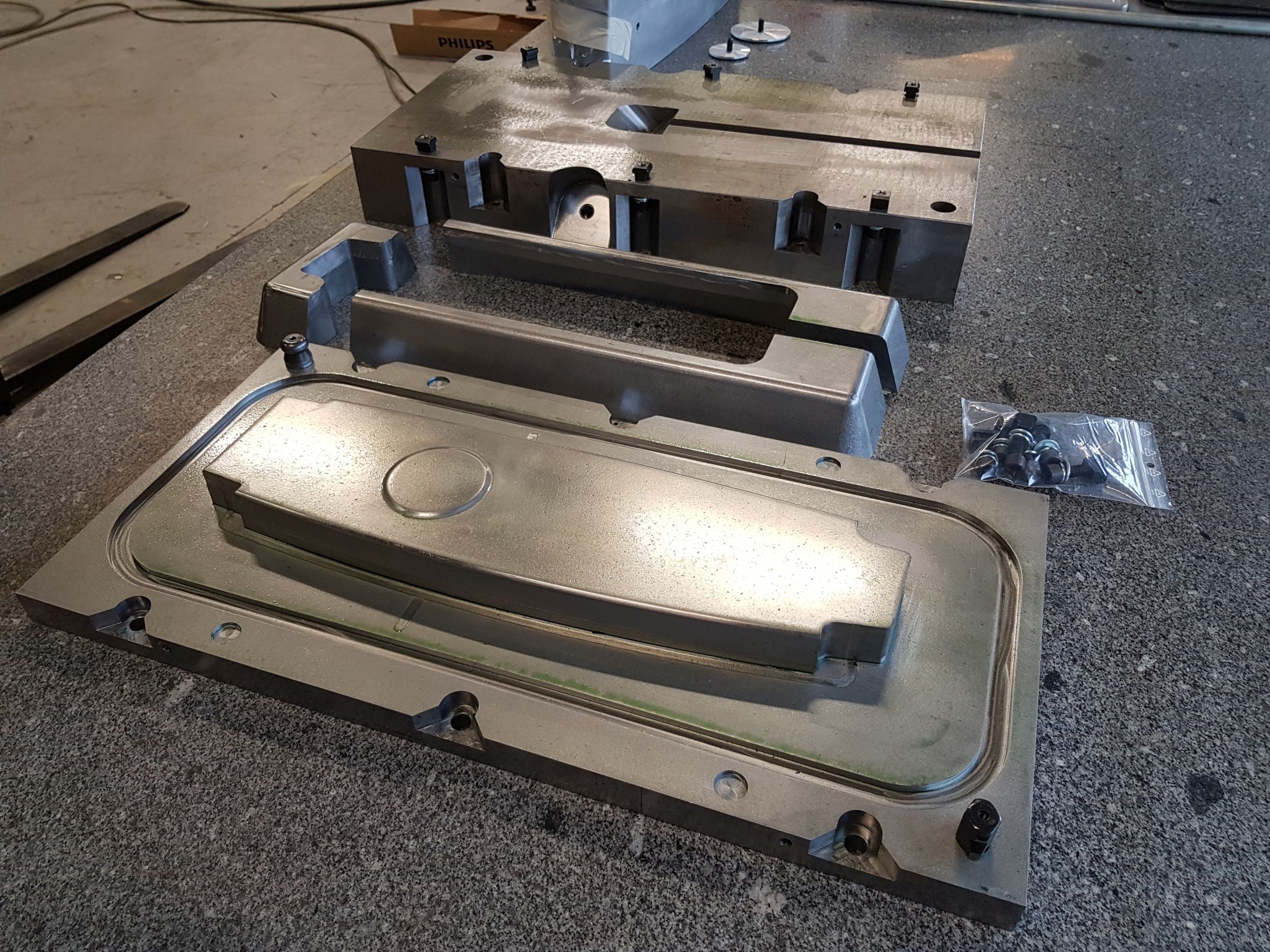
De RTM-tool voor de OPTICOMS-rib bestaat uit meerdere onderdelen.
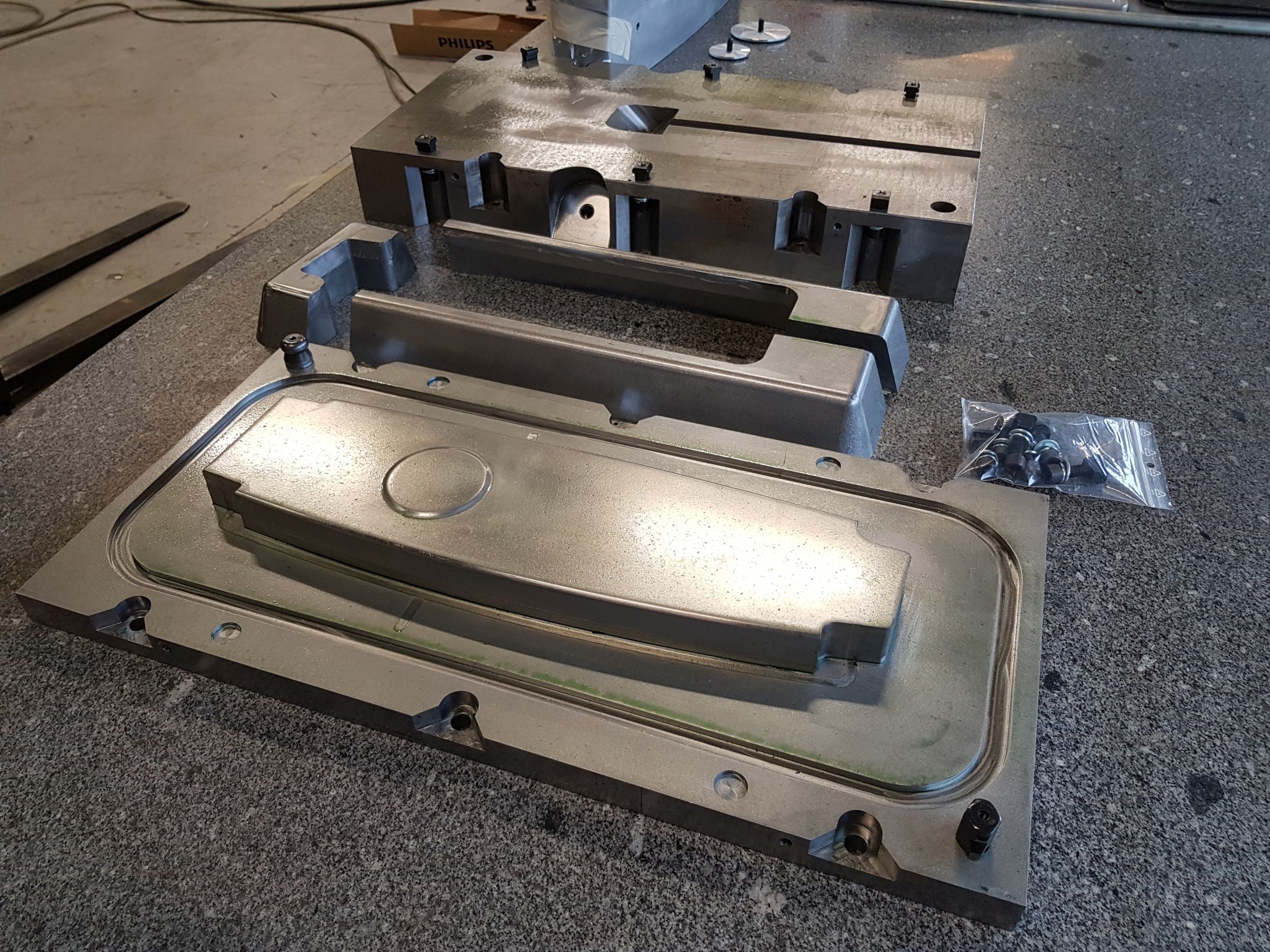
Stap 8
De ribpreform wordt in het RTM-gereedschap geplaatst.
Stap 9
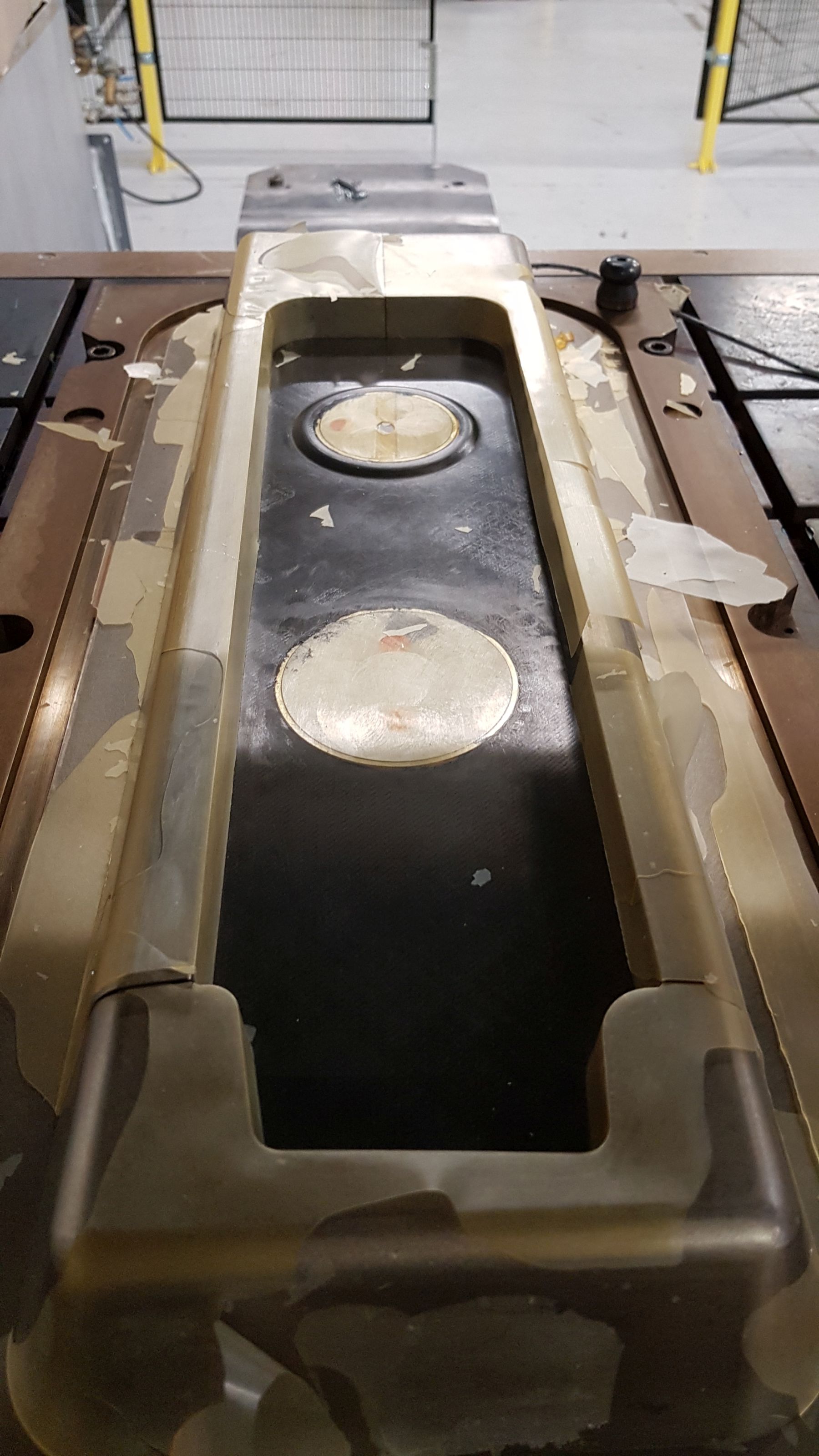
Er wordt vacuüm aangebracht, hars wordt geïnjecteerd en infiltreert in de voorvorm, gevolgd door een uitharding van 90 minuten. Hier is de pers geopend om het uitgeharde deel te onthullen.
Stap 10
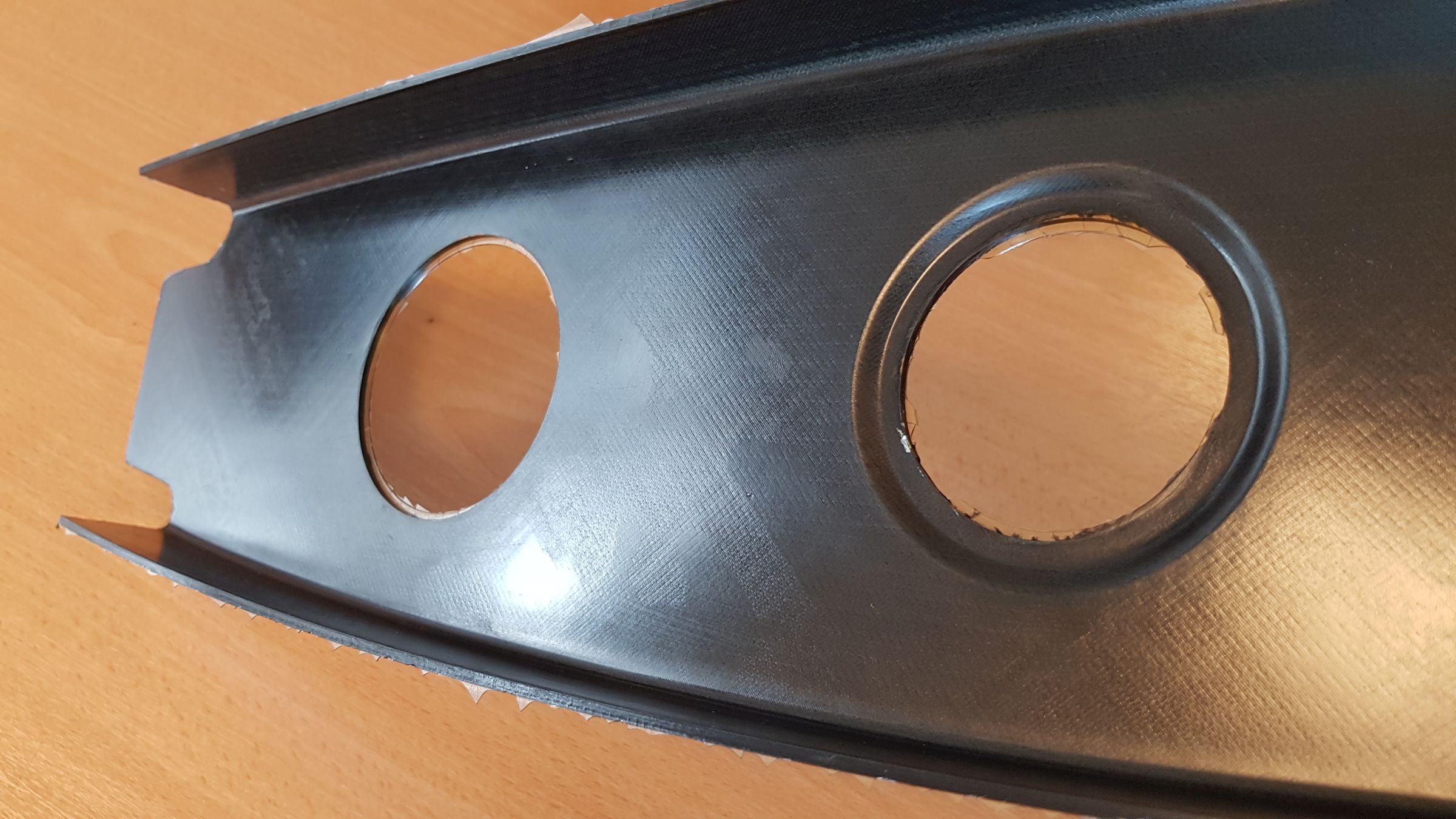
Nadat het ontvormen is voltooid, wordt de harsflits gedurende een volledige deelcyclus van 4 uur verwijderd.
Slimme bediening
Een ander belangrijk kenmerk van de geautomatiseerde voorvormcel van Techni-Modul Engineering is het geïntegreerde besturingssysteem. Aangeduid als SMART CONTROL, is de ruggengraat een camerasysteem en multifunctionele software die foto's die tijdens de verwerking zijn gemaakt vergelijkt met de CAD-database van het onderdeel, waardoor vormherkenning, vezeloriëntatiecontrole, laagpositionering en detectie van defecten en vuil van vreemde voorwerpen (FOD) mogelijk wordt. ). De SMART CONTROL-feedback instrueert de robot hoe hij de lagen in de juiste volgorde en timing moet oppakken en plaatsen, maar waarschuwt ook de celoperator wanneer hij fouten detecteert. "Het systeem kan zo worden geconfigureerd dat de operator de laag vervolgens handmatig verwijdert en het systeem opnieuw opstart om het te vervangen", legt Chevallet uit, "of we kunnen met de klant samenwerken om een geautomatiseerde oplossing te creëren voor het verwijderen van defecte lagen en het corrigeren van fouten."
Dezelfde optische beelden die worden gebruikt om laagranden en contouren te detecteren, worden ook gebruikt voor het regelen van de vezeloriëntatie. Chevallet geeft toe dat als het onderdeel erg groot is (bijv. 2 meter lang in vergelijking met 200 bij 200 millimeter), "je misschien een camera nodig hebt die foto's maakt [van een] hogere verticale positie om de randen van lagen te detecteren, en dan dichter bij het onderdeel voor het controleren van de vezeloriëntatie. U kalibreert deze volgorde voor elk type onderdeel. Voor het opsporen van rimpels en FOD is er een database met verschillende defecten en deze kun je aanvullen, zodat het deep learning-algoritme in de loop van de tijd verbetert. Het idee is om een systeem te hebben dat adaptief is.”
Cyclustijd en toekomstige productie
Preforms voor de OPTICOMS-rib werden gemaakt met HiMax en de I-beam stringer gebruikte HiTape. Het harssysteem voor beide was Hexcel's HexFlow RTM6 ééncomponent (1K) vloeibare epoxy, die een uithardingscyclus van 90 tot 120 minuten bij 180°C heeft. Deze uitharding is de langste stap in de cyclustijden van het onderdeel voor zowel de OPTICOMS-rib als de test I-balk stringer, zoals te zien is in tabel 1.
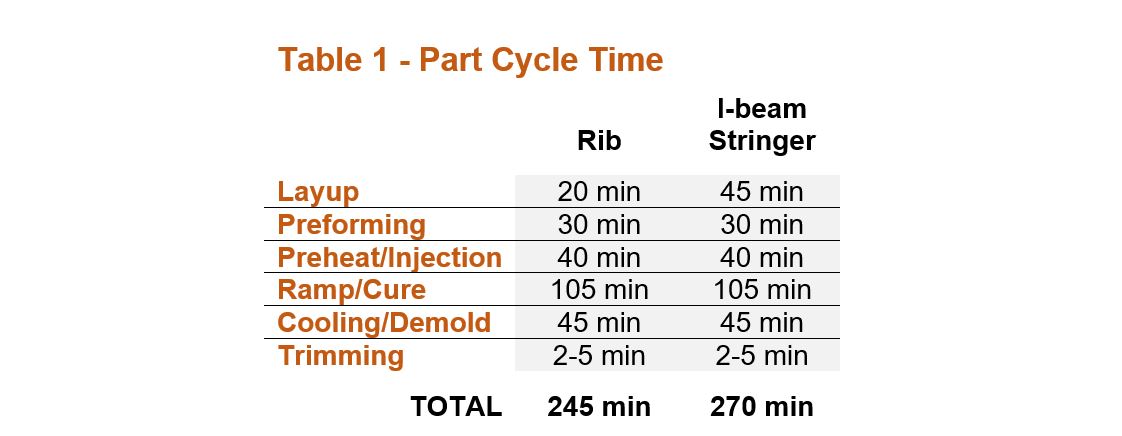
Bron | Techni-Modul Engineering
Tot op heden is dit de enige epoxy die gekwalificeerd is voor RTM van ruimtevaartconstructies. De belangstelling voor kwalificerende tweecomponentensystemen die bij de injectiekop worden gemengd, neemt echter toe, waardoor een grotere flexibiliteit van de uithardingscyclus wordt geboden en de noodzaak voor gekoelde verzending en opslag om voortijdige reactie van de voorgemengde RTM6 te voorkomen, wordt vermeden.
Airbus Helicopters (Donauworth, Duitsland) werkte samen met Alpex Technologies (Mils, Oostenrijk) in het SPARTA-project om een HP-RTM-proces te demonstreren met behulp van een tweecomponentenversie van HexFlow RTM6 om een uitharding van 30 minuten bij 180°C voor een A350-deur te bereiken frame, een complexe primaire structuur van 2 meter hoog, 200-250 millimeter breed en 8-10 millimeter dik (zie "HP-RTM voor serieproductie van kosteneffectieve CFRP-luchtstructuren"). Airbus heeft ook een CFRP-rib van 1,5 meter bij 0,5 meter gedemonstreerd die is gemaakt met HP-RTM door zijn dochteronderneming Composite Technology Center (CTC, Stade, Duitsland), waarmee vormcycli van 20 minuten worden bereikt voor onderdelen met 60% vezelvolume en minder dan 2 % leegtes. In het afgelopen jaar heeft CTC met een aantal tier-leveranciers samengewerkt om prepreg-onderdelen met de hand layup over te zetten naar HP-RTM voor de A320. 2K-harssystemen moeten echter gekwalificeerd zijn voor de productie van aerostructuren en CTC maakt zich zorgen over het vermogen om continu de mengkwaliteit van 2K-harssystemen in situ te waarborgen. Alpex gebruikt in-mold sensoren van Netzsch (Selb, Duitsland) en Kistler (Winterthur, Zwitserland) om dit te helpen bereiken, en er worden andere oplossingen ontwikkeld (zie "2-componenten epoxy voor verhoogde productie van composiet aerostructuren").
Zelfs zonder 2K-systemen zijn wellicht hogere productievolumes mogelijk. Deurkozijnen in het SPARTA-project werden verwijderd na de eerste 30 minuten uitharding bij 180°C en nagehard uit de pers, onder vacuüm om thermische spanning te verwijderen en mechanische eigenschappen te garanderen. Volgens het hoofd R&D van Alpex, Bernhard Rittenschober, zijn hiervoor extra sets gereedschappen nodig, maar slechts één pers- en injectie-eenheid. Hij legt uit dat de extra gereedschapskosten worden gecompenseerd door lagere proces- en perskosten en snel kunnen worden terugverdiend, zelfs met een laag volume van 500-1.000 onderdelen/jaar.
"De belangrijkste prestatie van deze demonstrators is het vermogen om primaire aerostructuren te maken met een korte harsinjectie in vergelijking met conventionele RTM-processen in de ruimte, waar het een moeilijk en langdurig proces was om hars in zulke grote delen te infiltreren met UD-koolstofvezelversterkingen", zegt Pagnac. . "We staan nog maar aan het begin van wat we kunnen bereiken met dit soort intelligente geautomatiseerde preforming en C-RTM-verwerking", voegt Chevallet toe. "Het heeft het potentieel om de meer kosteneffectieve, duurzame productie van verstijvingsgeïntegreerde huidstructuren te realiseren die worden overwogen voor toekomstige vliegtuigen."
Hars
- 3D-printmaterialen voor ruimtevaart?
- 3 manieren waarop bedrijven composieten gebruiken in de ruimtevaart voor de toekomst
- Top 3 sterkste materialen voor kunststof bevestigingsmiddelen
- Henkel biedt materiaalplatform voor additieve productie
- Materialen:lichtgewicht honingraatproductietechnologie op K 2019
- Materialen:vlamvertragend polyamide op hoge temperatuur voor 3D-printen
- Voorbereiden op een autonome toekomst
- Trelleborg kondigt nieuwe distributeur voor gereedschapsmaterialen aan
- Arkema Inc. bouwt Amerikaanse PEKK-productiefabriek
- 10 sterkste materialen voor 3D-printen
- Materialen voor Invar 36-componenten