CETMA:composieten R&D en innovatie in Italië
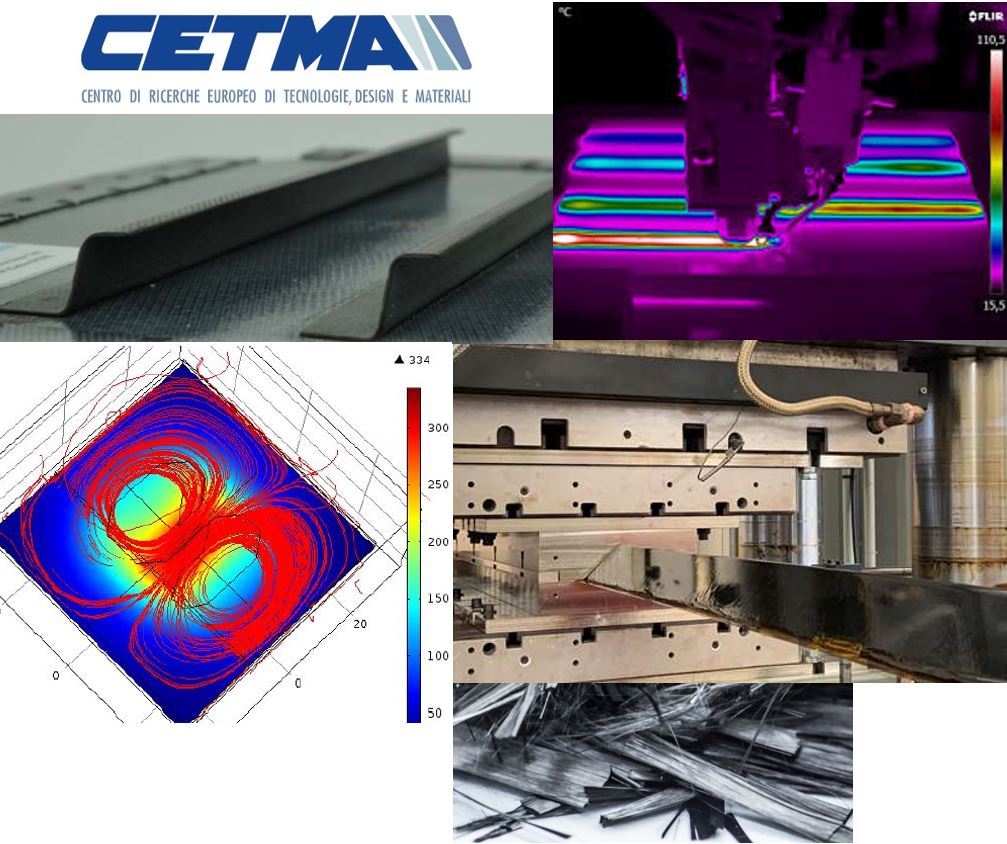
Centro di Ricerche Europeo di Technologie, Design e Materiali (CETMA, Brindisi, Italië), opgericht in 1994, is een van de grootste onafhankelijke onderzoeks- en technologieorganisaties in Italië, met een faciliteit van 4.000 vierkante meter en 75 medewerkers. CETMA investeert al meer dan 20 jaar sterk in composieten, wat resulteert in een breed scala aan expertise:
- Onderdeelontwerp en prototyping
- Nieuwe samengestelde processen
- Recyclingprocessen voor composieten en kunststoffen
- Procesoptimalisatie voor kosten, duurzaamheid, tarief, etc.
- Realtime procesbewaking
- Niet-destructief onderzoek (NDT)
- Structurele gezondheidsmonitoring (SHM) realtime en op afstand tijdens productie en service
- REACH-advies
- Thermoplastisch stempelen, continu persen (CCM) en prepreg persen (PCM)
- Vloeibare infusie, resin transfer molding (RTM) en dezelfde gekwalificeerde RTM (SQRTM)
- Prepreg uit autoclaaf (OOA)
- Inductielassen
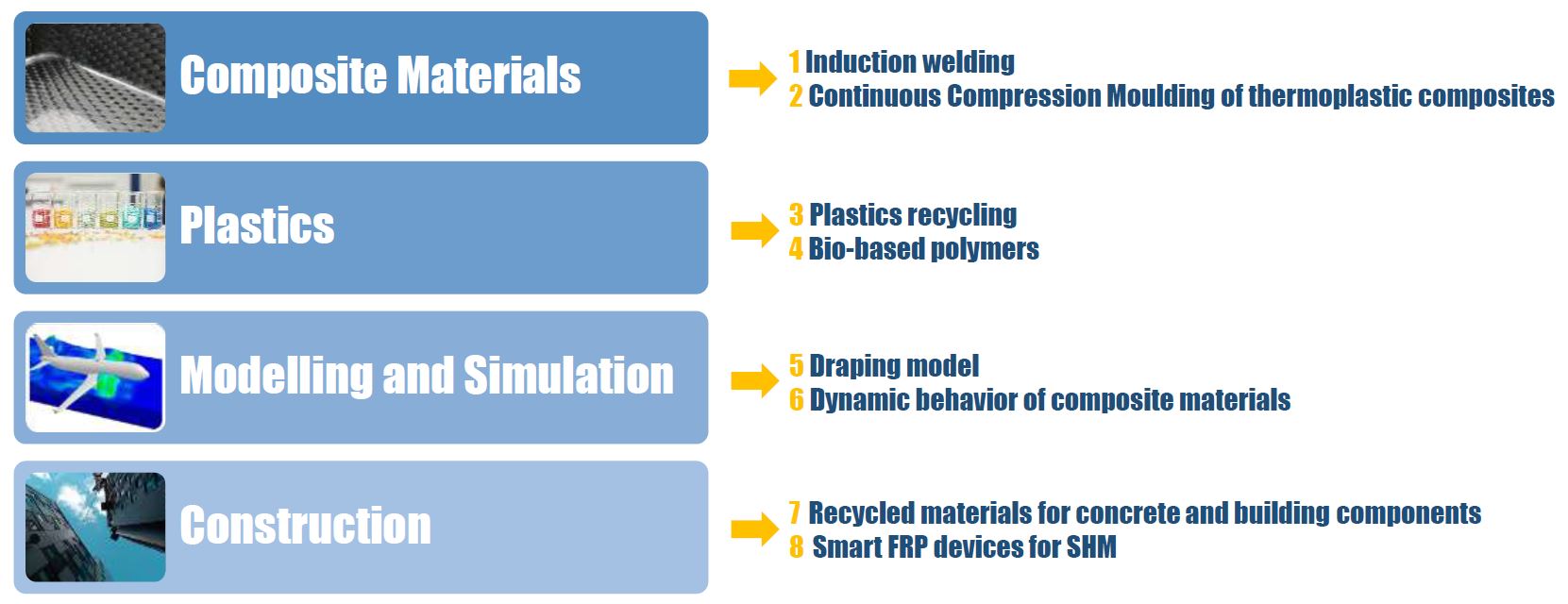
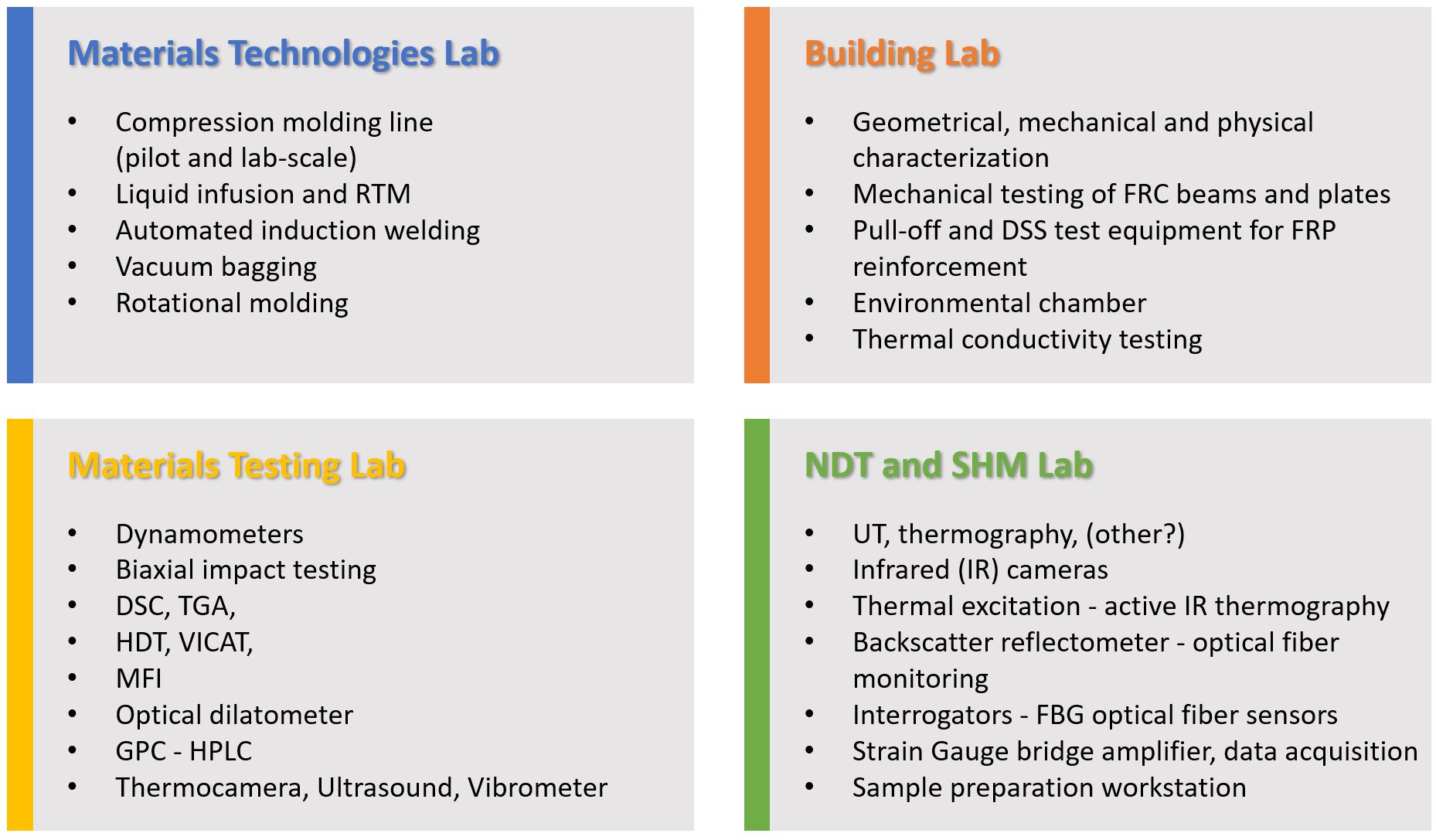
Het belangrijkste doel van CETMA is het ondersteunen van bedrijven en innovatie. De composietactiviteiten van CETMA worden bediend door vier hoofdlaboratoria en worden georganiseerd binnen de afdeling Advanced Materials and Processes (AMP), die ook uit vier gebieden bestaat:
- Materialen en karakterisering
- Technologieën en processen
- Modellen en simulatie
- Diagnose en structurele gezondheidsmonitoring
AMP heeft 30 medewerkers in dienst, waaronder materiaal-, luchtvaart-, civiele en chemische ingenieurs, evenals een chemicus, materiaalwetenschapper, architect en meerdere technici - in overeenstemming met zijn geloof in multidisciplinaire teams.
Kracht in thermoplastische composieten
"We bieden een volledig spectrum aan diensten op het gebied van composieten", zegt Alessandra Passaro, hoofd van de AMP-afdeling bij CETMA, "maar onze activiteiten in thermoplastische materialen is momenteel een van onze prioriteitsgebieden. In ons lab zijn alle verschillende soorten thermoplastische matrixpolymeren verwerkt. We zijn in 2004 begonnen met TWINTEX gemengde vezels en ongeveer 15 jaar geleden met persvormen met een eenvoudige pers. Nu hebben we gepatenteerde CCM- en inductielastechnologieën ontwikkeld. We hebben alle thermoplastische composietmaterialen geanalyseerd die in deze processen kunnen worden gebruikt.”
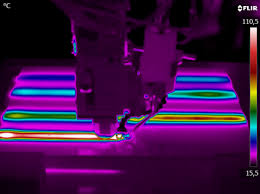
De CCM-lijn kan onderdelen met constante secties vervaardigen met behulp van PPS, PEEK, PEKK of PAEK. Maar hoe verschilt het CETMA-proces van wat wordt gebruikt door bedrijven als XELIS (Markdorf, Duitsland) en ATC Manufacturing (Post Falls, Idaho, VS)? (Zie CW-artikelen:"Compressievormen van ruimtevaartkwaliteit" en "Versnellen van thermoplastische composieten in de ruimtevaart".) Passaro legt uit:"Er zijn enkele specifieke details in het ontwerp van de mal die we gebruiken. Onze technologie is flexibeler wat betreft geometrieën en matrixmaterialen die kunnen worden gebruikt. Het is nog volop in ontwikkeling.” Hoewel gepatenteerd, wordt de technologie nog steeds ontwikkeld en zijn sommige aspecten gepatenteerd. De reden waarom CETMA CCM heeft nagestreefd, is dat niet. "We zagen het toegenomen gebruik en de behoefte aan continue thermoplastische composietprocessen", zegt Passaro. “XELIS is een productenbedrijf, geen machineleverancier. Wij zijn een onafhankelijke R&D-organisatie en investeren dus in en ontwikkelen de technologie vanuit een ander gezichtspunt.”
Een voorbeeld hiervan is de uitgebreide processimulatie om de temperatuurverdeling in de matrijs te analyseren. "De simulatieresultaten geven ons een volledig beeld van de temperatuurevolutie in het materiaal in de loop van de tijd", legt ze uit, "wat erg moeilijk is om van één kant inline te volgen, en toch is het cruciaal voor het minimaliseren van defecten in het composiet."
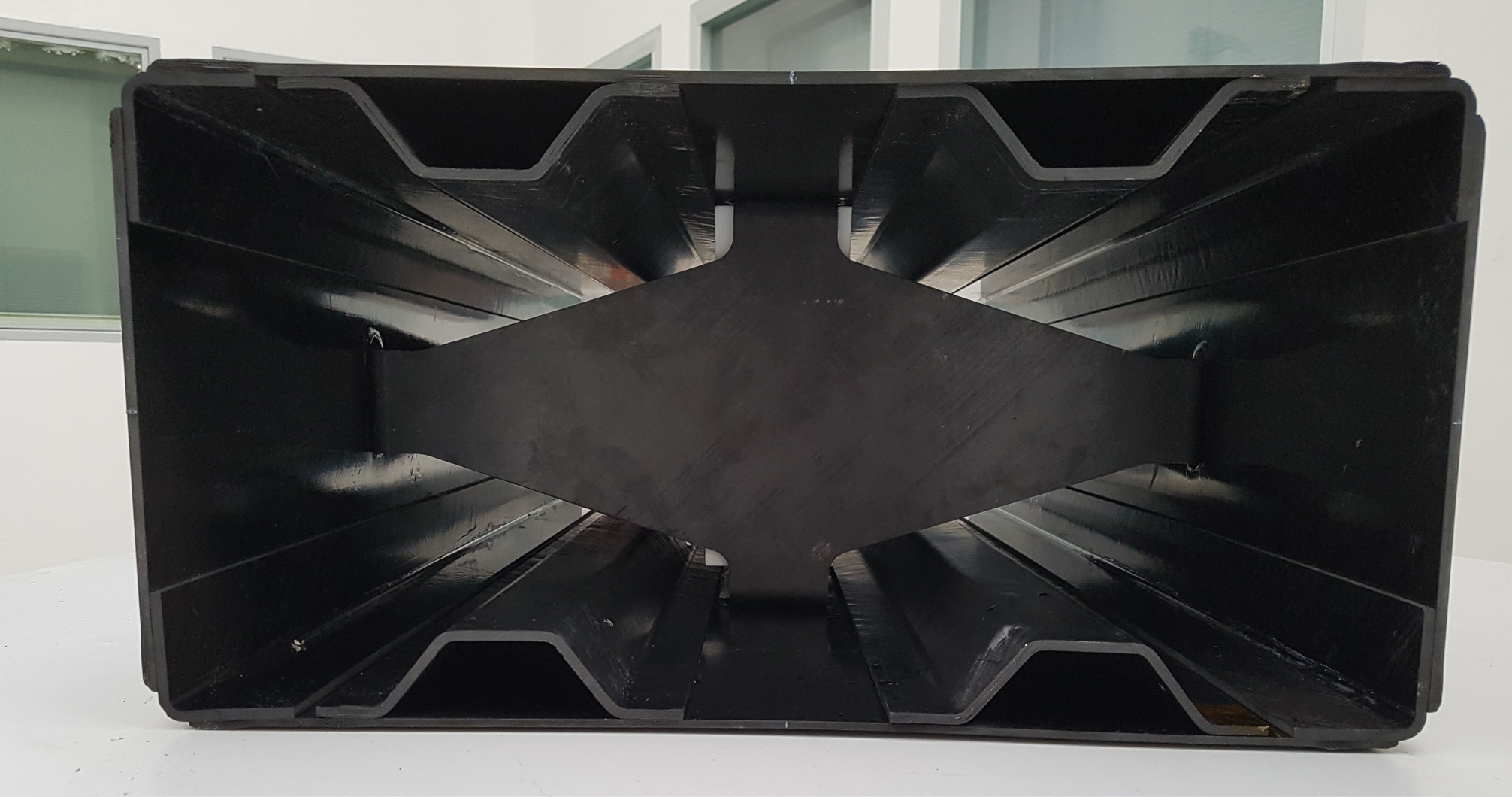
Inductielassen voor montage
Een ander belangrijk onderdeel van CETMA's expertise op het gebied van thermoplastische composieten is de gepatenteerde inductielastechnologie, die een controlesysteem en koeling omvat om de warmte binnen de laslijn te houden. CETMA gebruikte de technologie met partner EURECAT (Barcelona, Spanje) om CCM-profielen en platen te assembleren tot een thermoplastische composiet kielbalk voor een Airbus A320-vliegtuig in het Clean Sky 2 KEELBEMAN-project. Mijn blog van januari 2020, "Advancing thermoplastische composieten en RTM voor Clean Sky 2 ...", geeft meer details over dit project en de details van CETMA's lassen.
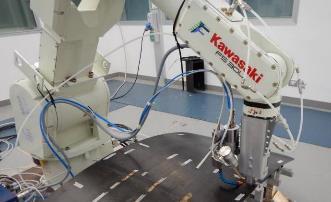
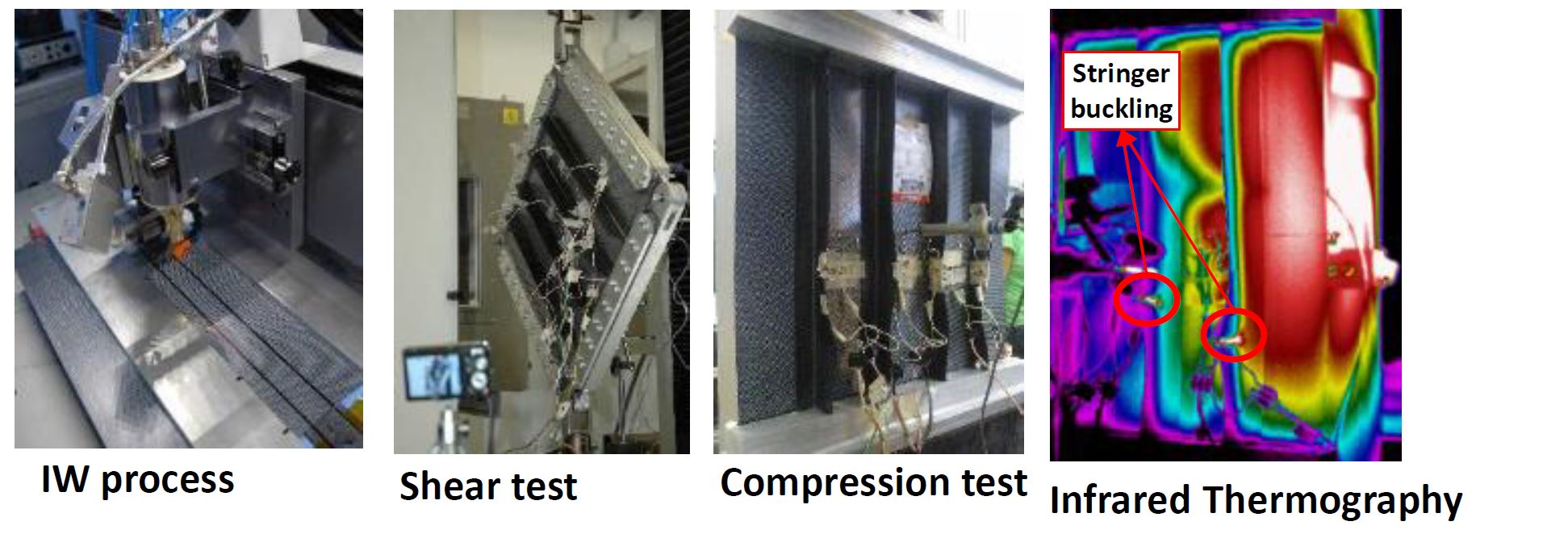
“We hebben twee soorten inductielassystemen ontwikkeld”, merkt Passaro op. “De ene is een vaste machine voor vlakke oppervlakken en de andere is robotgebaseerd voor complexe, 3D-geometrieën. Beide maken continue lassen op industriële schaal mogelijk zonder dat er extra materialen in de laslijn nodig zijn, maar leveren toch zeer hoge hechtingsprestaties in assemblages.”
CETMA heeft inductielassen gedemonstreerd op composietlaminaten gemaakt met koolstofvezelweefsel en unidirectionele (UD) tape, evenals een reeks matrixmaterialen:PPS, PEEK, PEI, PEKK, PP, PA6, PA12 en een hybride thermohardende epoxy/PVB ( polyvinylbutyral) thermoplastisch systeem.
Het heeft zijn expertise op het gebied van computermodellering en simulatie ook toegepast op het inductielasproces. "Dit stelt ons in staat om de temperatuurontwikkeling in het verbindingsgebied tijdens het lassen te voorspellen, wat een fundamentele hulp is bij het optimaliseren van de procesparameters", zegt Passaro.

Clean Sky 2 en composieten R&D-projecten
Naast KEELBEMAN is de AMP-afdeling van CETMA momenteel betrokken bij vier andere Clean Sky 2-projecten.
TRINITI - Thermoplastische hogedruk stikstoftanks van meerdere materialen voor vliegtuigen (JTI-CS2-CFP09-2018-02). Het tweejarige project, dat in 2019 van start ging, heeft tot doel een prototype vliegtuigtank te bouwen voor langdurige opslag van stikstof voor brandbestrijdingsdoeleinden. Diehl Aviation (Gilching en Dresden, Duitsland) is de topicmanager van het project. Partners omvatten ook ruimtevaart R&D-lab Novotech s.r.l. (Napels, Italië), Composites Testing Laboratory (Inverin, Co. Galway, Ierland). Het project zal thermoplastische composiettanks van meerdere materialen vervaardigen door middel van een combinatie van processen zoals co-extrusie om een meerlagige en multifunctionele voering/laminaat te vormen, gevolgd door in-situ consolidatie (ISC) met behulp van laserondersteunde geautomatiseerde vezelplaatsing (AFP ). (Voor meer informatie over ISC AFP, zie "Consolideren van thermoplastische composiet aerostructuren op hun plaats, deel 1 en deel 2".) Een doel van TRINITI is het verminderen of zelfs elimineren van microscheurtjes in cryogene omgevingen. Momenteel werkt CETMA aan het identificeren van alle thermoplastische materialen die kunnen voldoen aan de eisen van de lucht- en ruimtevaartdrukvaten.
SPARE - Innovatieve composiet pax- en laadvloerroosters op ware grootte voor demonstranten op de grond van regionale Aircraft Fuselage-vaten – (JTI-CS2-2017-CfP07-REG-01-14). Dit 18 maanden durende project, gestart in oktober 2018, heeft tot doel om volledige roosters voor passagiers- en vrachtvloeren te produceren die zijn gemaakt met koolstofvezelversterkte thermoplastische (TP) composieten. De sterk geautomatiseerde productie omvat progressief rolvormen en inductielassen voor montage. Het doel is om het gewicht en de terugkerende kosten te verminderen in vergelijking met traditionele metaal- en thermohardende composietoplossingen. De composietvloerroosters zullen worden geassembleerd in de Clean Sky 2 regionale vliegtuigrompdemonstrators voor testen op de grond en zullen worden geëvalueerd op technische en economische impact en vlamweerstandsprestaties volgens FAR 25.583-voorschriften. Themaleider is Leonardo, terwijl CETMA het project coördineert in samenwerking met machinefabrikant OMI S.r.l. (Fogliano Redipuglia, Italië).
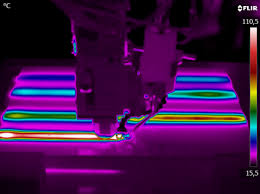
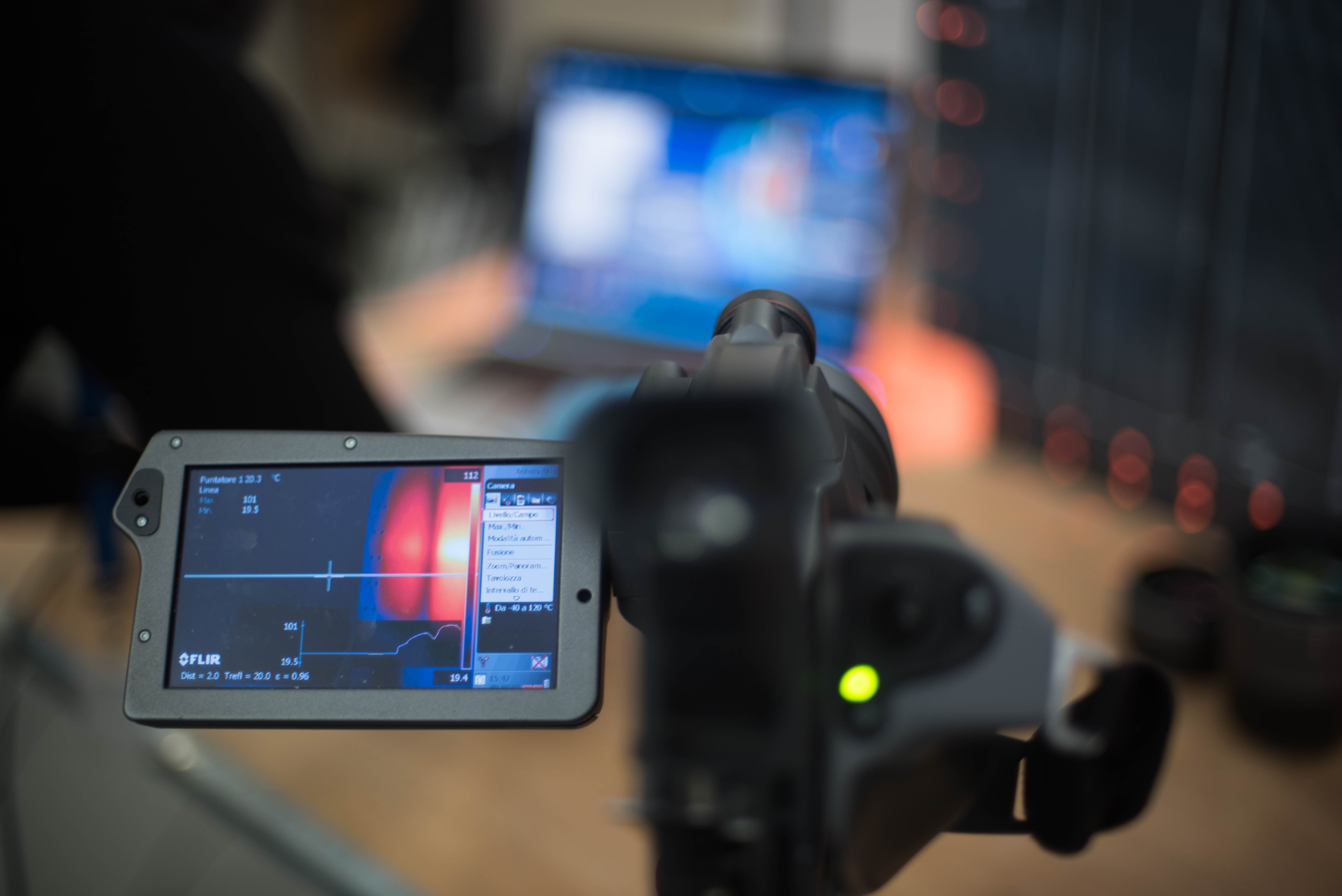
Een van de belangrijkste bijdragen van CETMA aan SPARE is de ontwikkeling van infraroodthermografie (IRT) voor inline monitoring van de progressieve rolvorming. Dit proces onderwerpt rollen TP-composietlaminaat aan verdichting en verwarming totdat de materiaalprocestemperatuur, complexe vorm en ontwerpdikte is bereikt. "Het is echter belangrijk om ervoor te zorgen dat de binnenste lagen volledig smelten van de matrix en consolidatie ondergaan", legt Passaro uit. “Bovendien is er een smal temperatuurvenster dat zorgt voor smelten maar het polymeer niet afbreekt. IRT is een contactloze methode die uitgestraalde warmte-energie over het oppervlak van het onderdeel met hoge nauwkeurigheid meet.”
CETMA gebruikte ramen van zinkselenurium (ZnSe) om in de gesloten apparatuur te kijken. Ze zijn transparant voor IR-golven en presteren bij temperaturen tot 500°C. Twee van dergelijke vensters werden geconstrueerd in de progressieve rolvormlijn van het SPARE-project met IRT-camera's erboven opgehangen om een bijna loodrecht zicht op het verwerkte materiaal te hebben. Bewerkbare besturingssoftware maakte het mogelijk om te controleren, op te nemen en te alarmeren als waarden buiten het gedefinieerde doelbereik vielen.
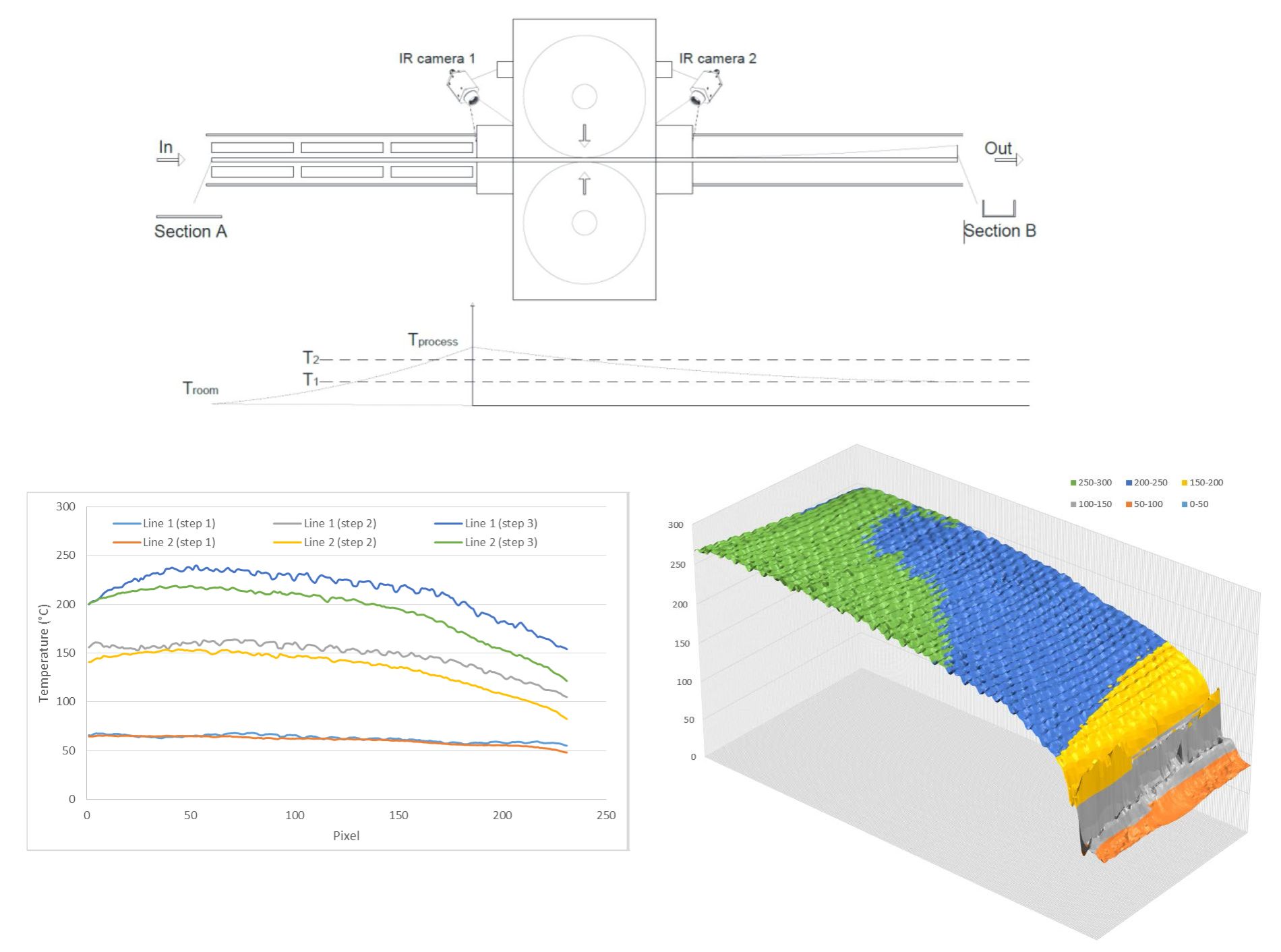
Uniformiteit van de materiaaltemperatuur door de profieldwarsdoorsnede werd geëvalueerd op de twee limietpunten - lijn 1 ligt dicht bij de verwarmingsstap en lijn 2 ligt verder langs het vormingsproces. Elk was verdeeld in 3 opeenvolgende stappen (Fig. 19):initiële fase (stap 1), vormingsproces gestart (stap 2) en vorming met verminderde snelheid (stap 3). IRT toonde aan dat de temperatuur aan de buitenranden van het laminaat lager was dan in het centrale gebied, wat leidde tot ongelijkmatige verwarming en mechanische eigenschappen. Een 3D-weergave van de IRT-geregistreerde oppervlaktetemperaturen (Fig. 20) bood een visueel hulpmiddel om de temperatuurverdeling beter te begrijpen.
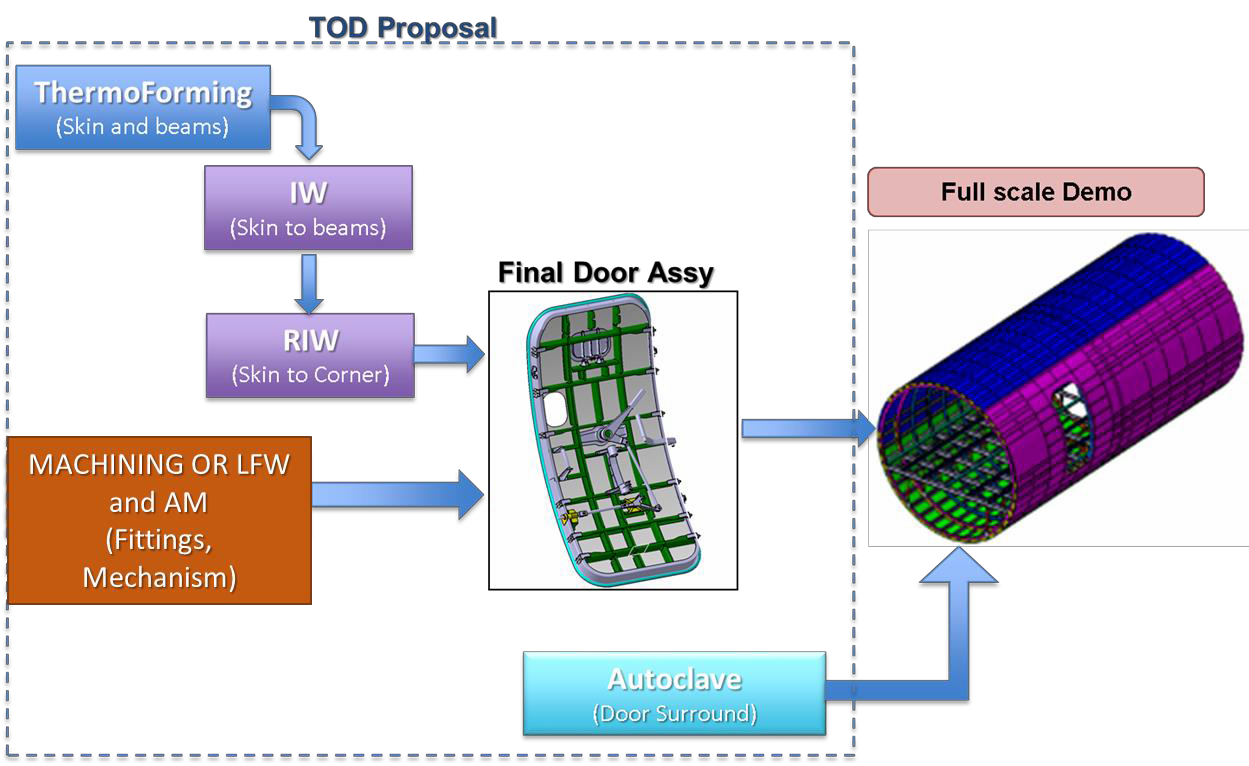
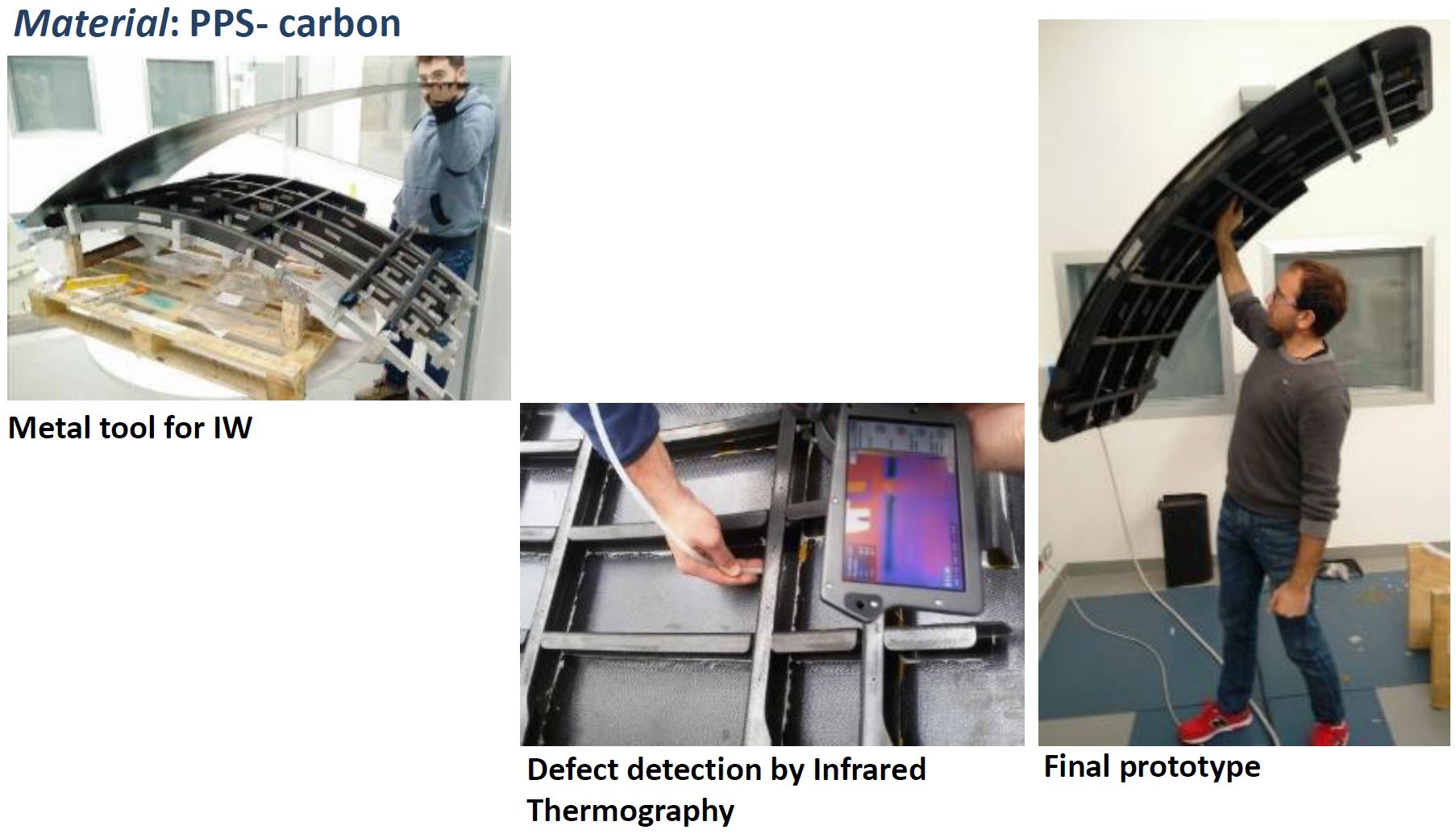
TOD – Thermoplast op deuren (JTI-CS2-2017-CfP07-REG-01-12). TOD heeft als doel het ontwikkelen en valideren van snelle productie en assemblage van een full-scale thermoplastische composietdeur (inclusief rompsubstructuren) voor een regionaal vliegtuig. TOD maakt deel uit van het Clean Sky 2 Regional Aircraft IADP (Innovative Aircraft Demonstrator Platform), dat de integratie van technologieën die zijn ontwikkeld in de Clean Sky-fase één Green Regional Aircraft ITD (Innovative Technology Demonstrator) naar een hoger niveau van complexiteit en volwassenheid brengt via twee vliegende proefbanken en drie grote geïntegreerde gronddemonstrators. Onder leiding van Leonardo zal CETMA samenwerken met projectpartners The Welding Institute (TWI, Cambridge, VK) en aerospace Tier 1 en engineering/industrialisatiebedrijf DEMA (Design Manufacturing SpA, Somma Vesuviana, Italië).
De voorgestelde aanpak omvat optimalisatie en validatie van thermovormen voor de fabricage van componenten en verbindingsprocessen zoals inductielassen (IW) en resistief implantaatlassen (RIW), die gewichtsvermindering mogelijk maken door mechanische bevestigingsmiddelen te elimineren. TOD zal ook de automatisering van industrie 4.0 en inline monitoring bevorderen om een snelle productie van hoogwaardige onderdelen (zero defects) met robuuste procescontrole te ondersteunen. Verwachte voordelen zijn onder meer:
- Minimaal 15% gewichtsvermindering
- Vermindering van afval en schroot met 10% door sensoren en inline monitoring
- Tot 75% energiebesparing ten opzichte van standaard autoclaafverwerking
- Verlaagde terugkerende kosten via adaptieve slimme productie (verhoogde flexibiliteit, lagere kosten voor volledige tools)
- Verbeterde CO2-emissies tijdens productie en gebruik van lichtere vliegtuigen.
CETMA is betrokken bij tal van andere ontwikkelingsprojecten. Een voorbeeld is NHYTE (Nieuwe hybride thermoplastische composiet aerostructuren vervaardigd door Out of Autoclave Continuous Automated Technologies) die tot doel heeft innovatieve geïntegreerde aerostructuren te demonstreren gemaakt van hybride thermoplastische matrixmaterialen met multifunctionele mogelijkheden.
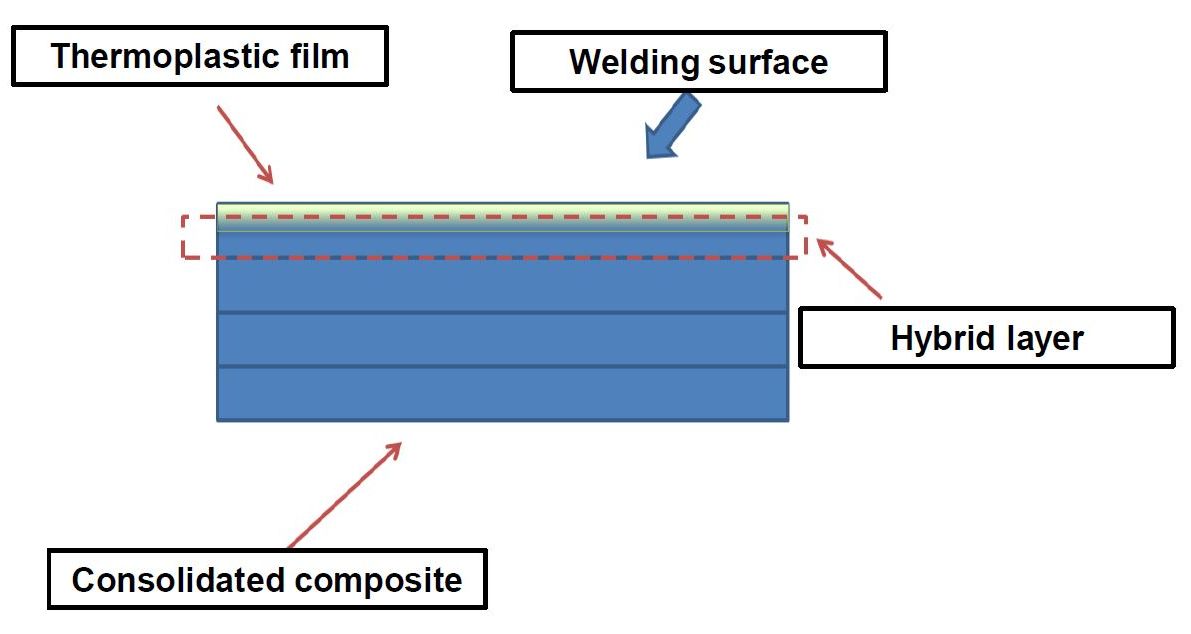
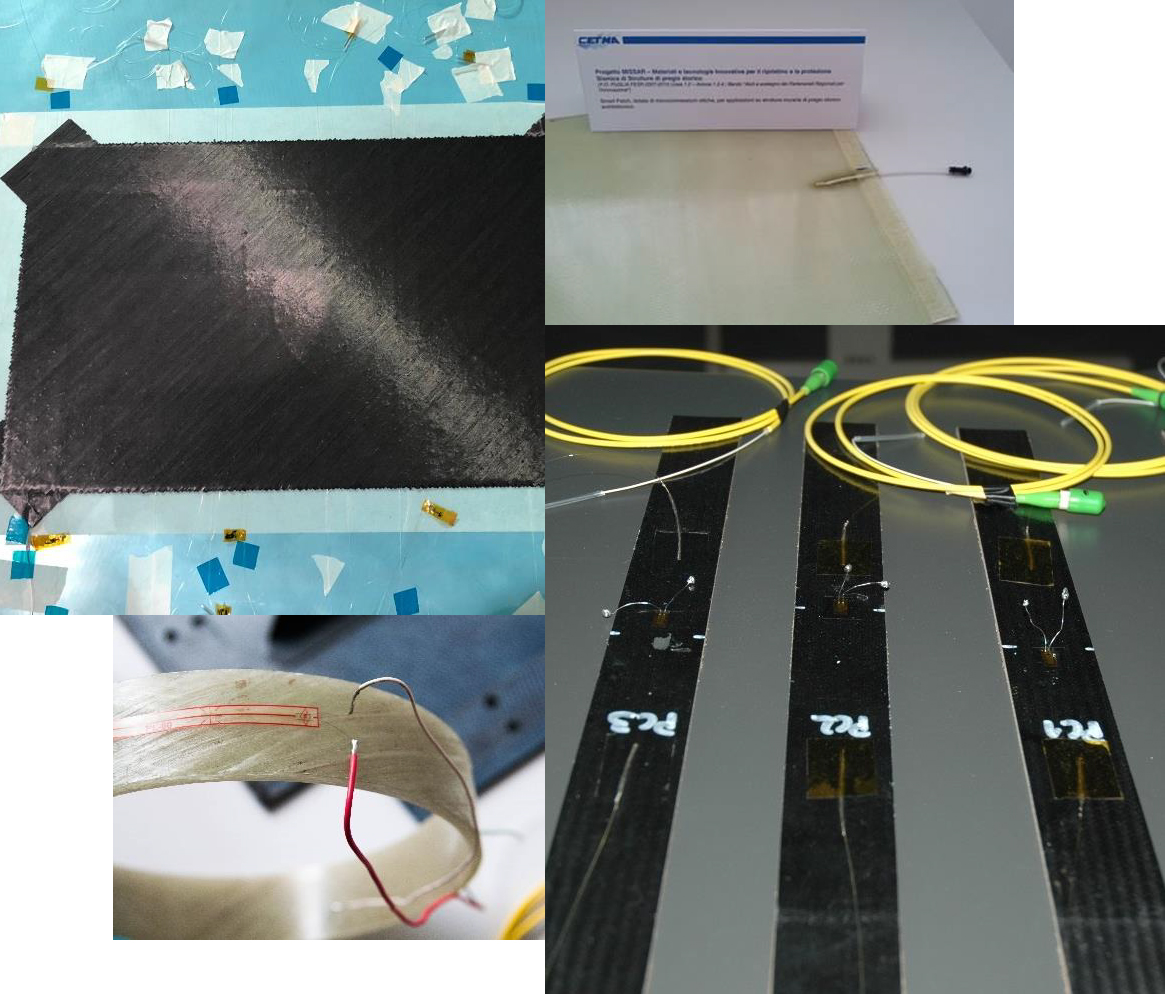
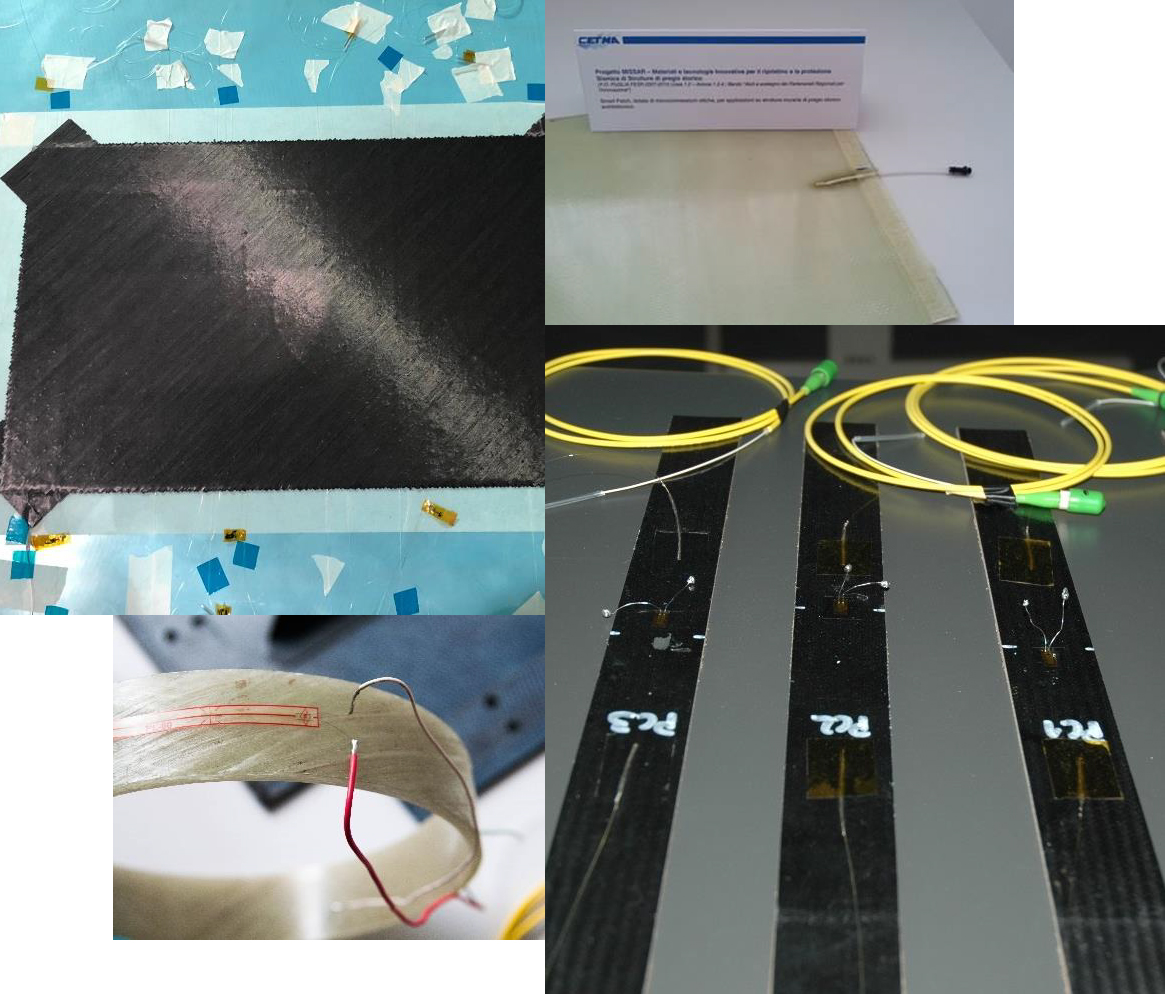
NHYTE, gefinancierd in het kader van het Horizon 2020-programma en geleid door NOVOTECH (Napels, Italië), begon in september 2018 en zou eindigen in januari 2020. Het hoogwaardige hybride materiaal is gebaseerd op een commerciële koolstofvezel/PEEK-prepreg met toegevoegde amorfe PEI films om in-situ consolidatie mogelijk te maken met geautomatiseerde vezelplaatsing (ISC AFP) en vervolgens assemblage via CETMA's gepatenteerde inductielastechnologie. CETMA heeft een brede karakteriseringscampagne voltooid, bestaande uit fysiek-mechanische en virtuele testen van het hybride composietmateriaal en de opstelling van het inductielasproces.
Koolstofvezel recyclen
Een ander belangrijk gebied voor CETMA is recycling. De CIRCE Het doel van het project is om prepreg-schroot te gebruiken dat wordt gegenereerd tijdens de fabricage van composietonderdelen door het te recyclen tot een compressievormmassa, die vervolgens zal worden gebruikt om teeninzetstukken voor veiligheidsschoenen te vormen. CETMA zal deze secundaire grondstof karakteriseren en een numeriek model ontwikkelen om de structurele prestaties van de schoeninzetstukken te voorspellen. Dit model helpt bij het analyseren en verifiëren van het impactgedrag om te voldoen aan de veiligheidsvoorschriften, met resultaten die worden gebruikt om het ontwerp van de teeninzetstukken te verfijnen en af te ronden. Het Italiaanse projectteam omvat Base Protection (Barletta), fabrikant van composiet motorsport/auto-onderdelen HP Composites (Ascoli Piceno), machine- en productielijnspecialist Elks Group (Ascoli Piceno) en Petroceramics (Stezzano).
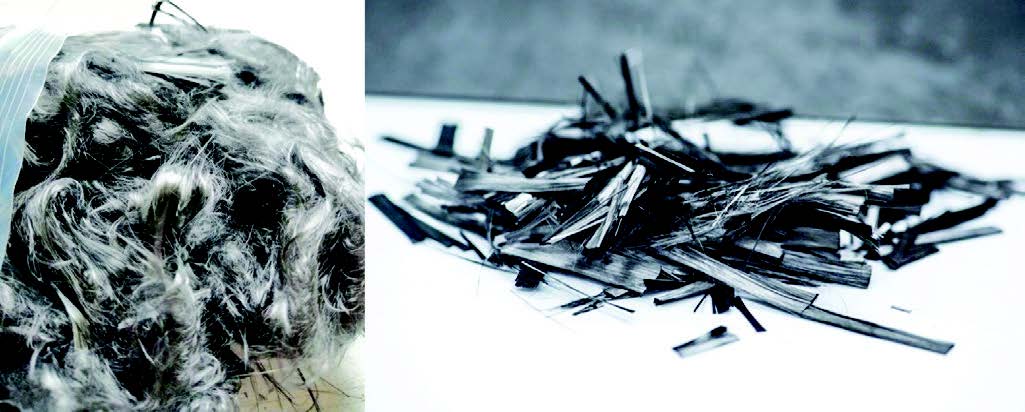
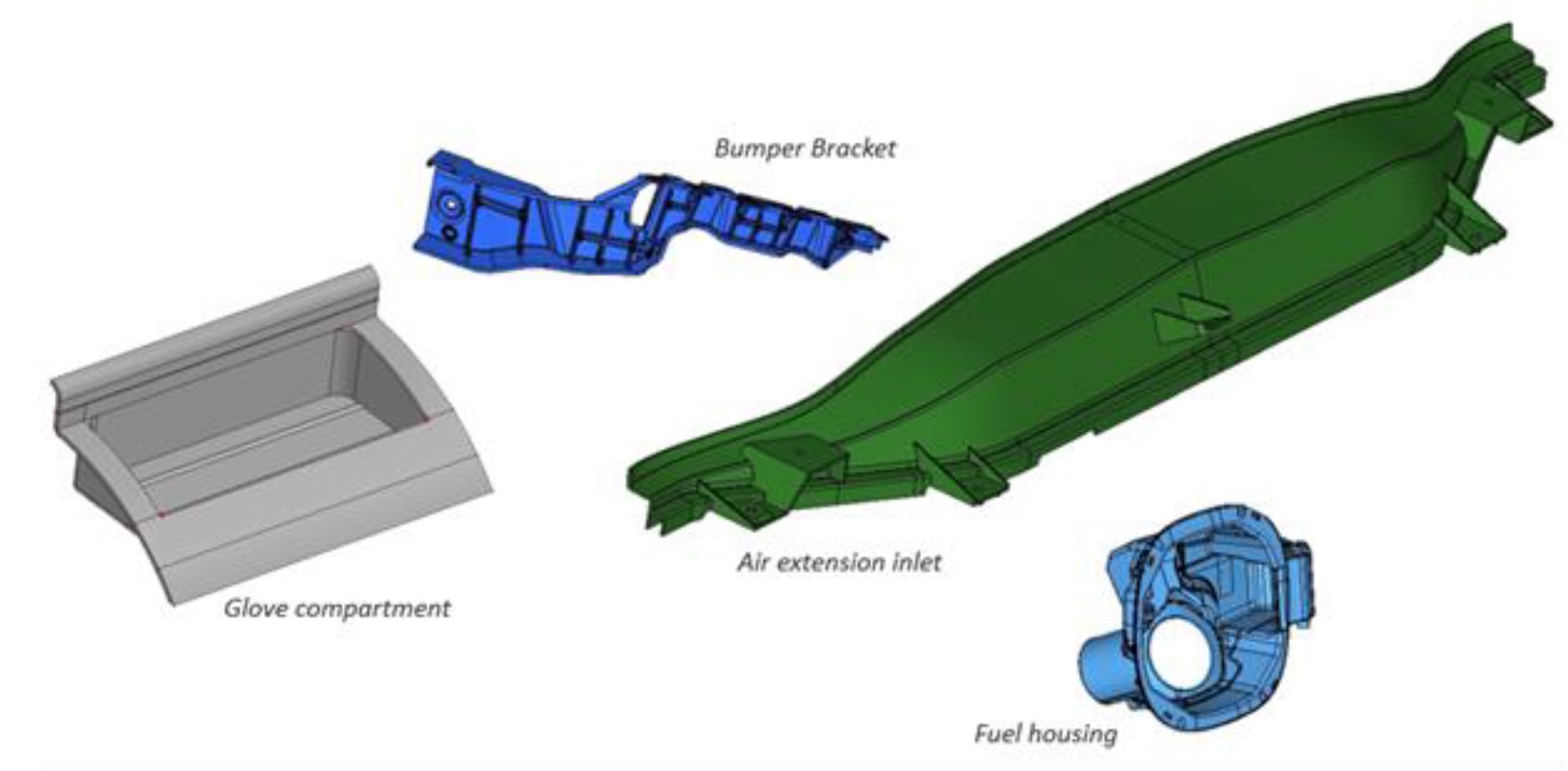
Misschien wel de grootste investering van CETMA in recycling tot nu toe was via de REVALUE project gericht op gerecyclede koolstofvezels voor hoogwaardige composieten. Het doel van het REVALUE-project, gefinancierd door het European Institute of Innovation &Technology (EIT, Boedapest, Hongarije), is om gerecyclede koolstofvezel (RCF) van de toonaangevende producent ELG Carbon Fiber (Coseley, VK) met behulp van pyrolyse te combineren met nieuwe en gerecyclede thermoplastische polymeren ter vervanging van de huidige materialen die worden gebruikt door Centro Ricerche Fiat (CRF, Turijn, Italië) voor de productie van geselecteerde auto-onderdelen.
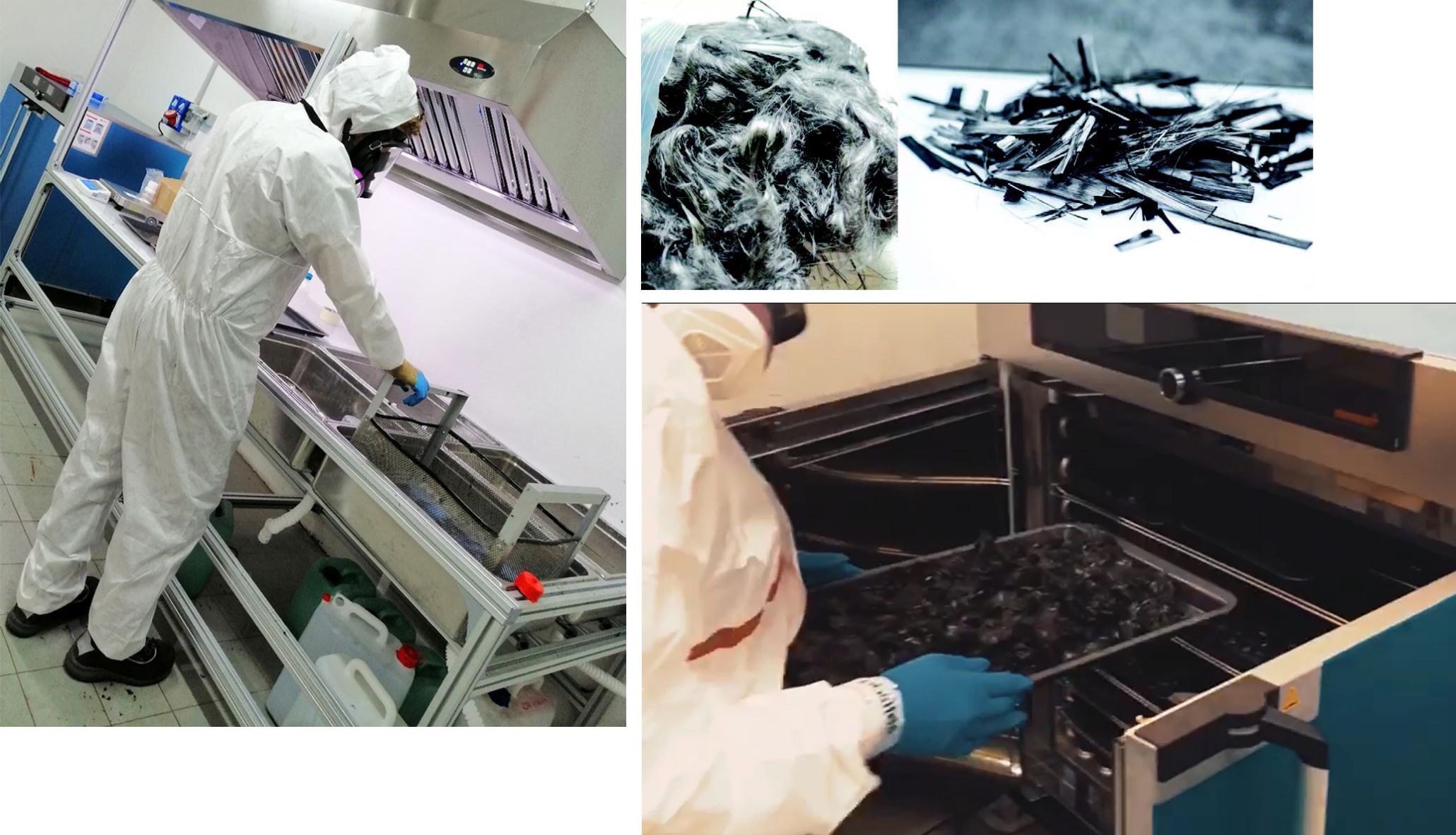
Echter, zoals opgemerkt in het JEC Composites magazine van januari-februari 2020 artikel, "Nieuwe maatformulering voor gerecyclede koolstofvezels" door Alessandra Passaro, et. al., RCF geproduceerd door pyrolyse heeft geen maatvoering, waardoor de broze vezels vatbaar zijn voor veelvuldig breken tijdens het hanteren en voor scheiding van de vezelkabels in filamenten, wat resulteert in een verstrengelde, "pluizige" vorm met een lage bulkdichtheid. Als onderdeel van REVALUE ontwikkelde CETMA een specifieke formule voor maatvoering voor RCF, compatibel met nieuw of gerecycled polypropyleen (PP) en PA6. Het evalueerde vervolgens het vermogen tot dimensionering om de RCF-verwerkbaarheid te verbeteren en de interface met de geselecteerde thermoplastische matrices te vergroten.
Om dit te doen, ontwikkelde CETMA een proefinstallatie voor het dimensioneren van RCF, die in staat is om de dimensionering in kilogramhoeveelheden toe te passen en tegelijkertijd het effect van de belangrijkste parameters op het depositieproces te evalueren. De fabriek omvat drie hoofdstations:behandeling van het lijmen en wassen van de vezels; het hanteren van de droge vezels voor en na de behandeling; en het drogen van de vezels in de oven. Per dag kan in een continue cyclus vier kilogram RCF worden behandeld.
Het formaat RCF van CETMA werd vervolgens gebruikt door het Franse onderzoekscentrum CEA en de Franse compounder SUEZ om een vormmassa te produceren met behulp van nieuwe en gerecyclede thermoplastische polymeren. De fysisch-chemische karakterisering van de verbindingen werd voltooid en het vermogen van de CETMA-sizing om de uiteindelijke mechanische prestatie van het composiet te verbeteren, werd geverifieerd.
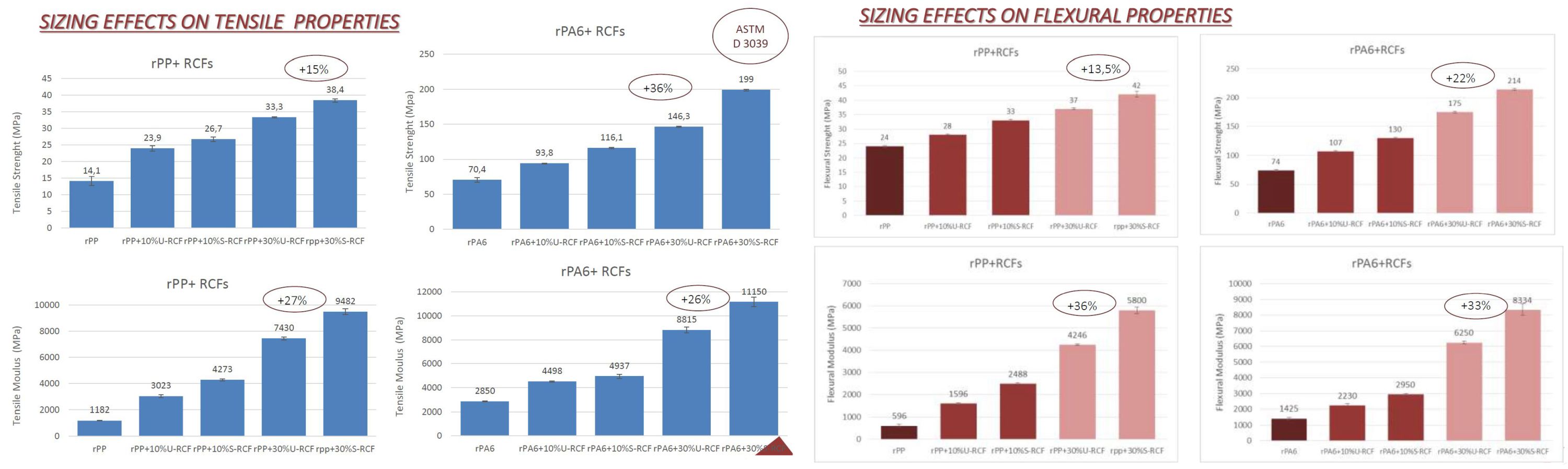
De innovatieve RCF-vormmassa's werden vervolgens gebruikt voor het spuitgieten van semi-structurele automobielcomponenten die momenteel worden gemaakt met glasvezelversterkt PP of PA6. Naast het voor de hand liggende voordeel bij recycling en hergebruik van materialen, werden ook de vermindering van het voertuiggewicht, het brandstofverbruik en de CO2-uitstoot aangetoond.
Buiten REVALUE heeft CETMA ook de dimensionering voor RCF verder ontwikkeld en geëvalueerd in meerdere composietprocessen, waaronder persvormen, vacuüminfusie en RTM, met in alle gevallen verbeterde eigenschappen.
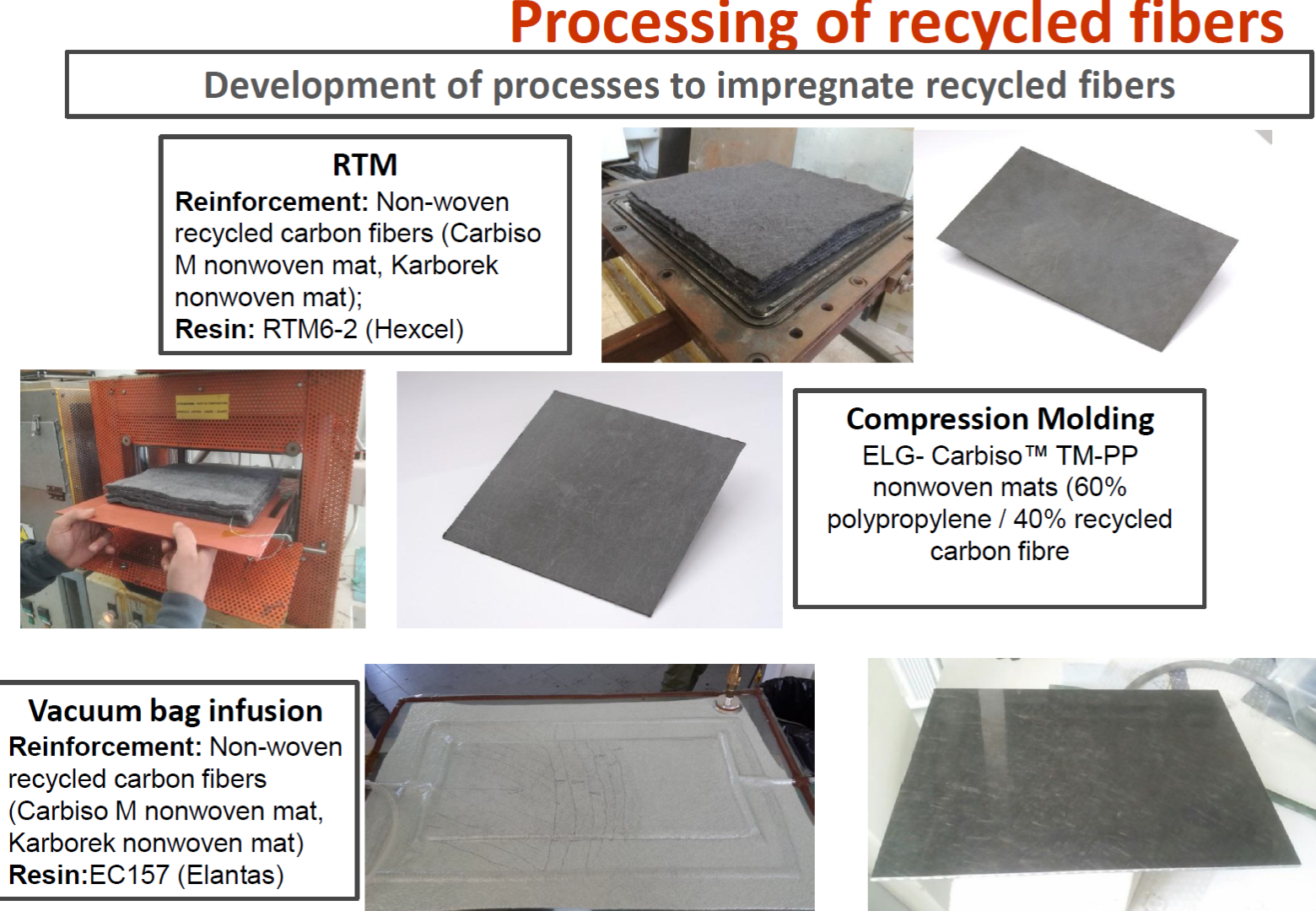
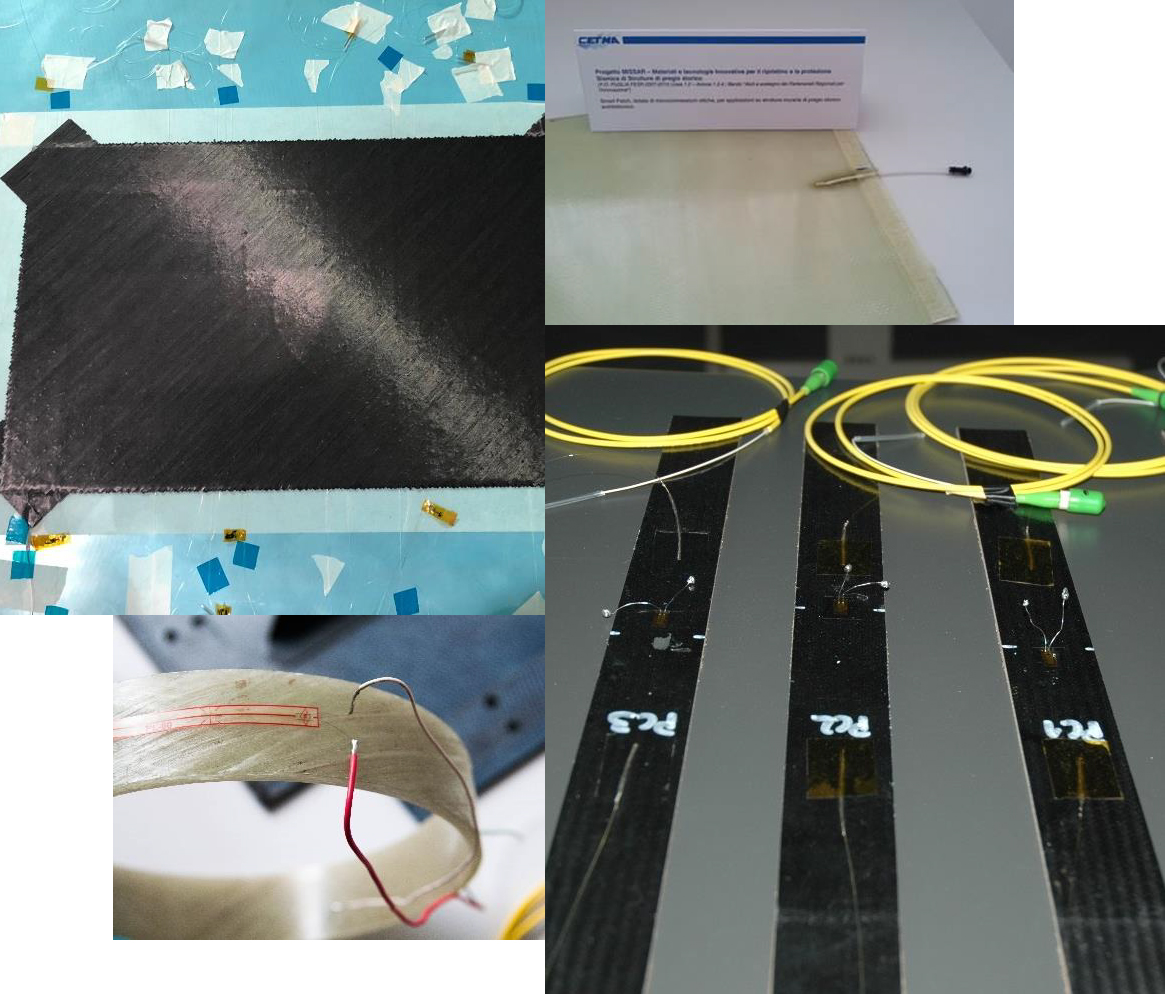
Structurele gezondheidsmonitoring (SHM)
Dit laatste belangrijke gebied van composietactiviteiten voor CETMA krijgt ook steeds meer de nadruk in de industrie. “We hebben jarenlange ervaring met het toepassen van SHM voor constructie- en bouwtoepassingen”, merkt Passaro op. “En ook in composieten hebben we veel met SHM gewerkt. We weten dat dit belangrijk zal zijn voor toekomstige toepassingen en we zijn geïnteresseerd om te blijven samenwerken met composietfabrikanten en de industrie om deze technologie vooruit te helpen.”
Hars
- Aanpassen van ultrasone sensoren voor procesoptimalisatie en controle van composieten
- Herverwerkbare, herstelbare en recyclebare epoxyharsen voor composieten
- Combinatie van AC- en DC-diëlektrische metingen voor het bewaken van de uitharding van composieten
- Composites One en IACMI organiseren tweedaagse workshop
- Het meten van de temperatuur in composieten en bondlines
- TPAC en TPRC ontwikkelen recyclingproces voor thermoplastische composieten
- PES-additief verhoogt de weerstand tegen breuk en microscheurtjes in epoxycomposieten
- SABIC en Nottingham Spirk werken samen om innovatieontwikkeling te versnellen
- De composietenwereld in Israël en de VS dienen
- Snij-uitdagingen:composieten met gemengde matrix en vezelversterkte composieten
- ABB Robotics:Technology Innovation and Robotics R&D