RAPM-ontwikkeling met PtFS
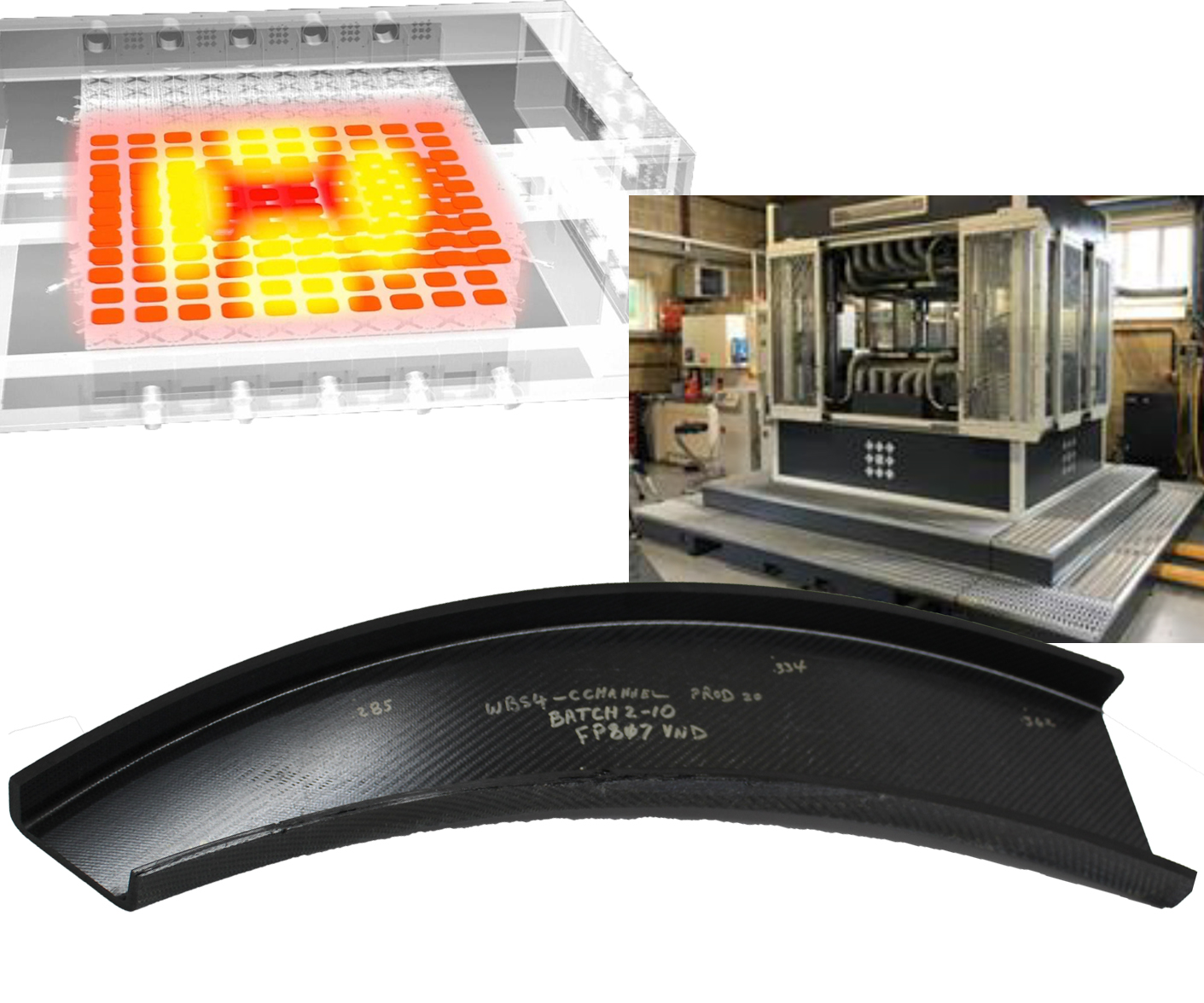
Deze blog is een online zijbalk voor de functie van mei 2020, "Revolutionizing the composites cost paradigm, Part 2:Forming", waarin het RApid high-Performance Manufacturing (RAPM, uitgesproken als "wrap-em") programma onder leiding van The Boeing Co. (Chicago, Illinois, VS), het "vormende" deel van DARPA's Tailorable Feedstock and Forming (TFF)-programma om een snelle, goedkope en flexibele productie van kleine, complexe composietonderdelen mogelijk te maken.
Alle drie materiaal- en procestracks in het RAPM-programma - harsinfusie, thermohardende prepreg en thermoplastische vorming - omvatten proeven met behulp van een Production to Functional Specification (PtFS) gepixeld verwarmingscontrole- en gereedschapssysteem, geleverd door Surface Generation, en gevestigd bij Boeing R&T in St. Louis (zie onderstaande tabel).
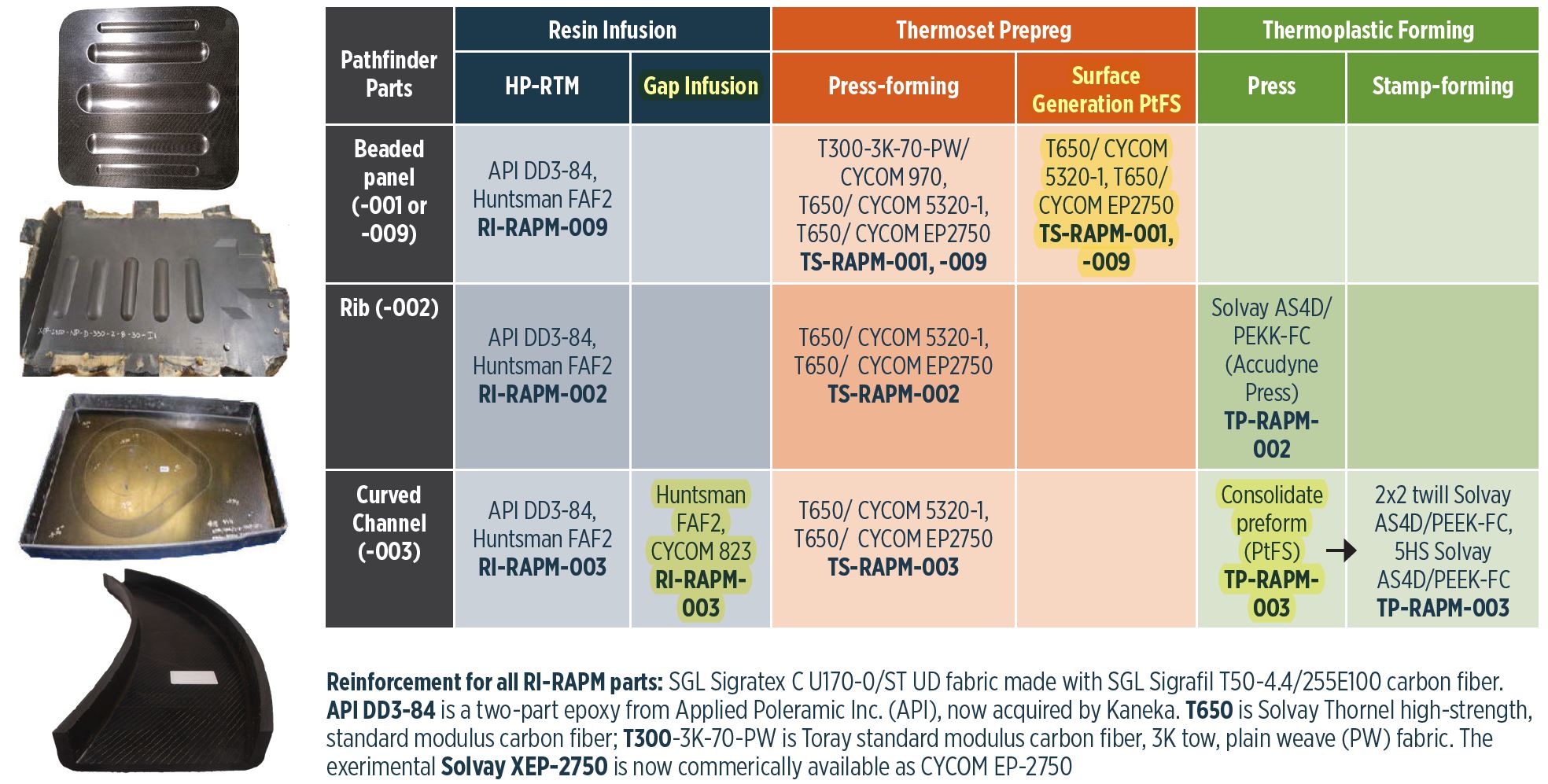
Merk op dat PtFS al jaren op de markt is. Deze blog gaat over de procesontwikkeling van RAPM met behulp van het PtFS-systeem. Referenties voor deze blog zijn onder meer:
- 2019 SAMPE (20-23 mei, Charlotte, N.C.) technische paper en diapresentatie, "Development of Scalable Dynamic Control Architectures for Flexible Composites Manufacturing Work Cells" door Steven M. Shewchuk 1 , Ben Halford 2 , Michael P. Matlack 1 , Andrew Sharpe 2 en Pete Massey 2 . 1 The Boeing Company, St. Louis, Mo., V.S. 2 Surface Generation Ltd. (Rutland, VK).
- Technisch document SAMPE 2020, "Compression Molding of Complex Thermoset Laminates" door Travis R. Adams, Timothy J. Luchini, Jared B. Hughes, Steven M. Shewchuk, Adam Martinez en Gail Hahn, The Boeing Company.
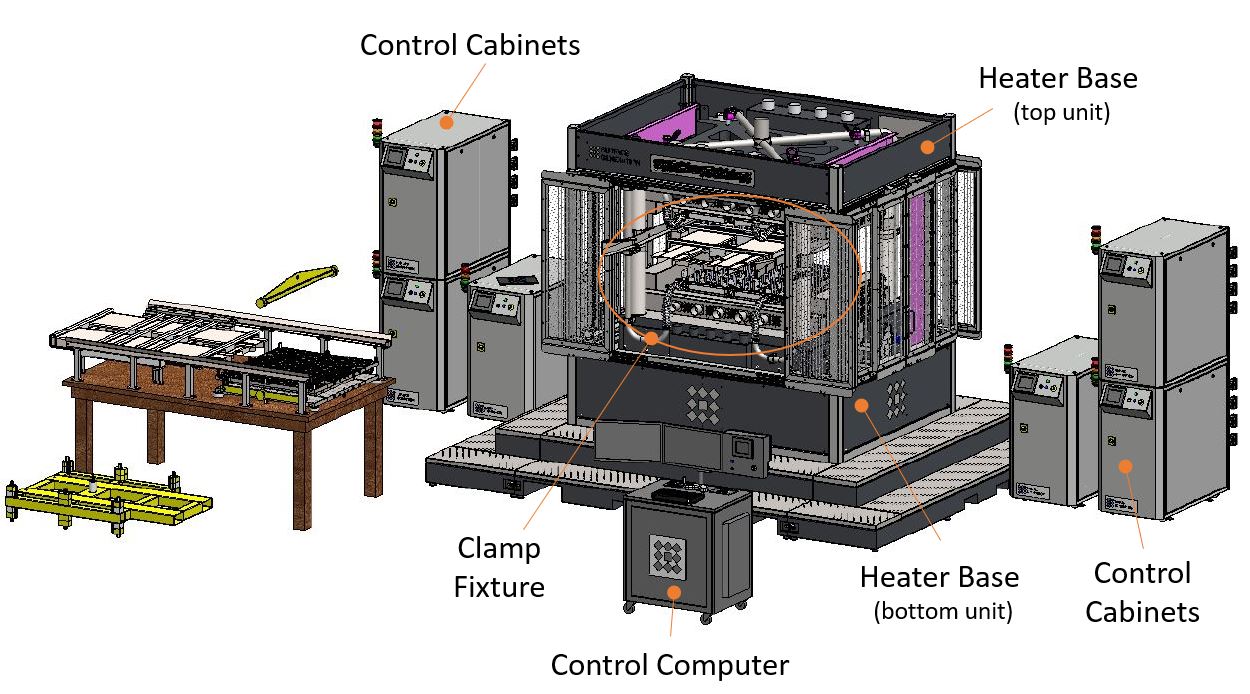
PtFS-systeemcomponenten
Het PtFS-systeem is modulair en kan volledig op zichzelf staan of delen van bestaande infrastructuur gebruiken. Voor verdichtings-/consolidatiedruk kan het systeem een bestaande hydraulische pers of een hydraulisch aangedreven gereedschapskleminrichting gebruiken. De Boeing St. Louis PtFS-cel is uitgerust met de laatste, een 150-tons klemarmatuur ontworpen door Surface Generation. Deze vormcel herbergt een deelvolume van 750 bij 750 bij 100 millimeter.
De Boeing St. Louis PtFS-cel omvat positie- en drukregeling. "De Orchestrator-software van Surface Generation wordt gebruikt om de CF-OaO-RAPM PtFS-werkcel te besturen", merkt Boeing-technicus en RAPM-programmamanager Gail Hahn op. “Elk gereedschap wordt in het systeem gekalibreerd door middel van verplaatsing en drukafstemming. Drukkalibratie wordt uitgevoerd om de hydrauliek af te stemmen op de verwachte druk die het gereedschap tijdens de verwerking zal ervaren. Gereedschapsscheiding en verplaatsingskalibratie worden gedaan om de open/dicht-positie van het gereedschap in te stellen, evenals de gebieden voor langzaam/snel sluiten, die het gereedschapsvlak beschermen tijdens handmatige en automatische besturing. Positiemetingen worden uitgevoerd met vier snaarpotentiometers, legt Boeing composietmaterialeningenieur en RAPM-onderzoeker Steven Shewchuk uit. "Elk exemplaar bevindt zich op een geleidepaal van de kleminrichting om de positie van de plaat te meten en om een veiligheidsmethode te bieden om plaatrekken tijdens bedrijf te identificeren. De drukregeling wordt aangevuld met een enkele in-line druktransducer om feedback te geven aan de hydraulische pomp van de kleminrichting."
Boven en onder de kleminrichting bevinden zich boven- en onder verwarmingsbasiseenheden . Deze bevatten alle verwarmings-/koelcomponenten en werken in reactie op de uitgangen van de schakelkasten (drie kasten voor elke verwarmingsbasis in de Boeing-opstelling). Gereedschapsvlakken zijn ontworpen voor elke verwarmingsbasis en geïnstalleerd met behulp van een rail- en laadsysteem.
Elk gereedschapsvlak wordt verwarmd en gekoeld met behulp van perslucht die naar de onderkant van elk gereedschapsvlak wordt geleid en via een diffusor wordt verspreid. Elke set bijpassende metalen gereedschapsvlakken zijn verdeeld in 180 individueel regelbare verwarmingskanalen — 90 voor de bovenkant van het gereedschap en 90 voor de onderkant. Verwarmingskanalen zijn 10,0 centimeter uit elkaar geplaatst in een raster over elk gereedschapsvlak. Elk kanaal heeft een verwarming, een tweetraps persluchtbron en twee feedback thermokoppels die veerbelast zijn om intiem contact met de achterkant van het gereedschapsvlak te verzekeren. Voor verwarming van de RAPM-gereedschapsvlakken werd 1 kubieke voet per minuut perslucht per verwarmingskanaal gebruikt, terwijl voor koeling 3 kubieke voet per minuut werd gebruikt.
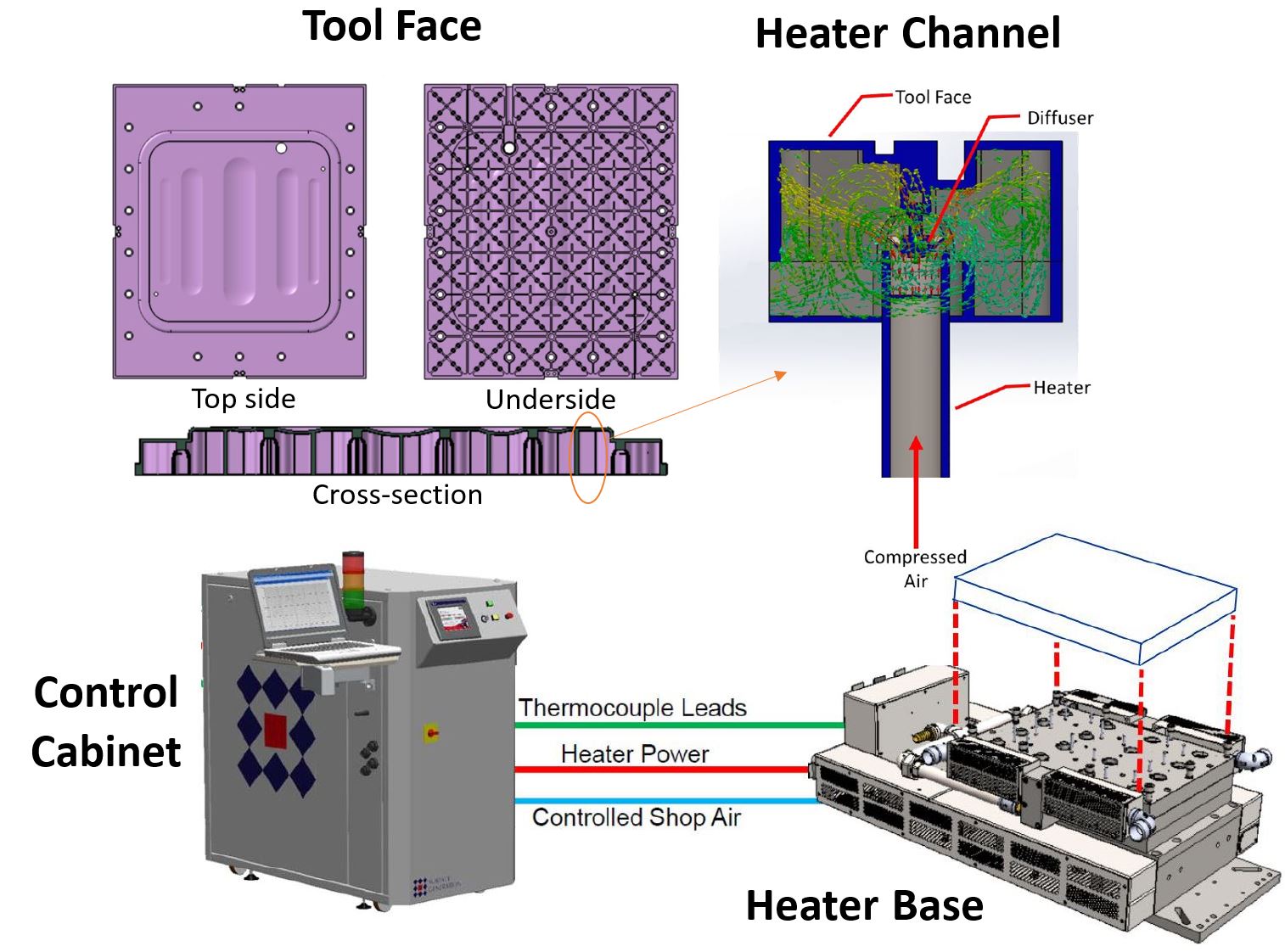
Gereedschapsvlakken
Gereedschapsvlakken in RAPM werden gefreesd uit gereedschapsstaal tot een dikte van ≈3 millimeter. Het onderste gereedschapsvlak voor TS-RAPM-001-201 wordt linksboven weergegeven in de bovenstaande afbeelding. De bovenkant van het gereedschapsvlak ziet eruit als een standaard stempelvormgereedschap, maar de onderkant onthult de verwarmingskanalen.
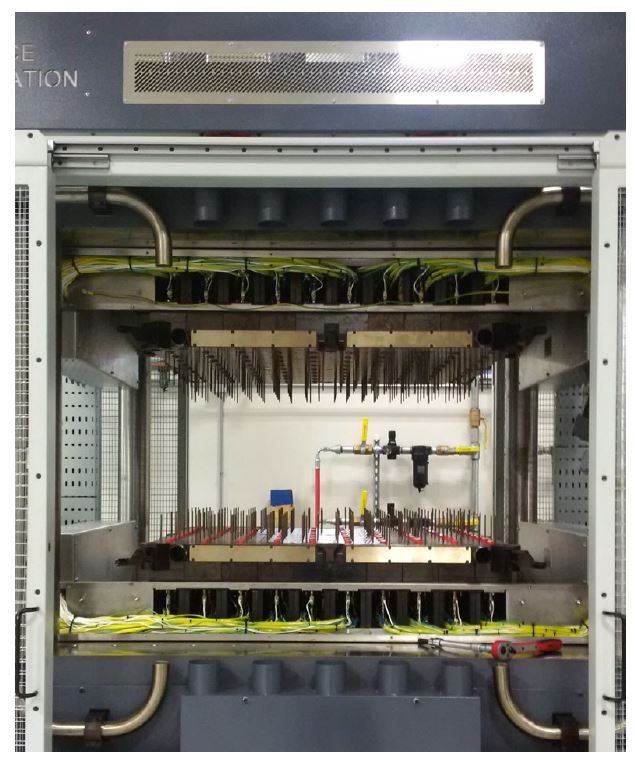
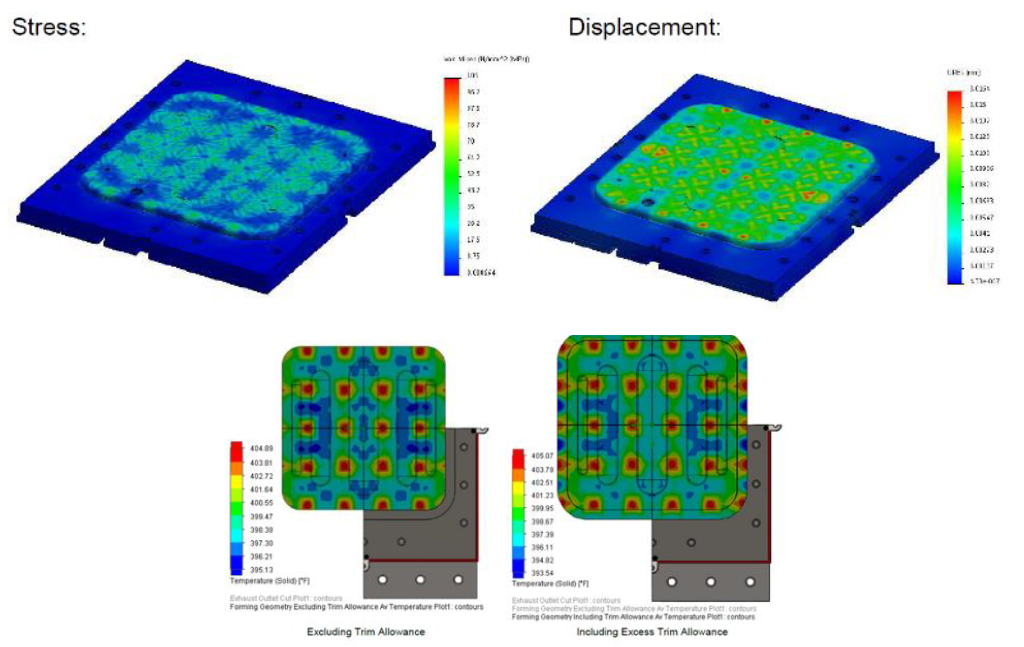
Gereedschapsvlakken met acceptabele geometrieën kunnen worden vervangen door andere gereedschapsvlakken die zijn ontworpen voor dezelfde verwarmingsbasis. Het gereedschap heeft dezelfde afmetingen van het verwarmingskanaal, de geschatte plaatsing van het thermokoppel en een diepte die binnen de veerbelaste slag van het thermokoppel valt.
Het raillaadsysteem dat wordt gebruikt om een gereedschapsvlak te veranderen, lijnt alle 180 veerbelaste feedbackthermokoppels uit in hulzen aan de achterkant van het gereedschapsvlak. Pinnen brengen het gereedschapsvlak op één lijn en zorgen ervoor dat het gereedschap kan worden geladen zonder nauwkeurige vorkheftruckbesturing. Het wisselen van gereedschap kan in 2-4 uur worden voltooid met twee operators, inclusief het demonteren en weer in elkaar zetten van het gereedschapsvlak in de fotolijst.
Er wordt zoveel mogelijk materiaal weggefreesd om de thermische massa te verminderen en de verwarmings- en koelsnelheden te verbeteren. Om deze reden vereiste elk gereedschapsoppervlak dat in RAPM werd gebruikt, structurele eindige-elementenanalyse (FEA) om te bepalen of het gereedschapsoppervlak de verwerkingstemperatuur en -druk kon overleven. De gereedschapsvlakken werden geoptimaliseerd met behulp van lineaire en niet-lineaire FEA, evenals thermische analyse in stabiele en tijdelijke computationele vloeistofdynamica (CFD). Dit laatste zorgde voor een gelijkmatige verwarming van het gereedschap. Zowel de gereedschapsdikte als de luchtdiffusors binnen elk verwarmingskanaal werden aangepast om de temperatuuruniformiteit te verbeteren. Een iteratieve lus tussen FEA en CFD maakte het mogelijk om de geometrie aan te passen om de gewenste temperatuur van het gereedschapsoppervlak te behouden en tegelijkertijd te voldoen aan de vereiste veiligheidsfactoren voor ondersteuning van het gereedschapsoppervlak.
Verwarmingszones en temperatuurregeling
Verwarmingskanalen zijn meestal gegroepeerd in zones, waarbij het aantal verwarmingskanalen per zone per onderdeel wordt gespecificeerd. Elke zone heeft een bijbehorende verwarmingsprofiel en toleranties kunnen naar wens binnen en tussen zones worden ingesteld. Hierdoor kunnen alle verwarmers in elke zone verwarmen, koelen of op temperatuur houden volgens het voorgeschreven verwarmingsprofiel door dynamisch variërende verwarmingsvermogensniveaus en persluchtstroomsnelheden.
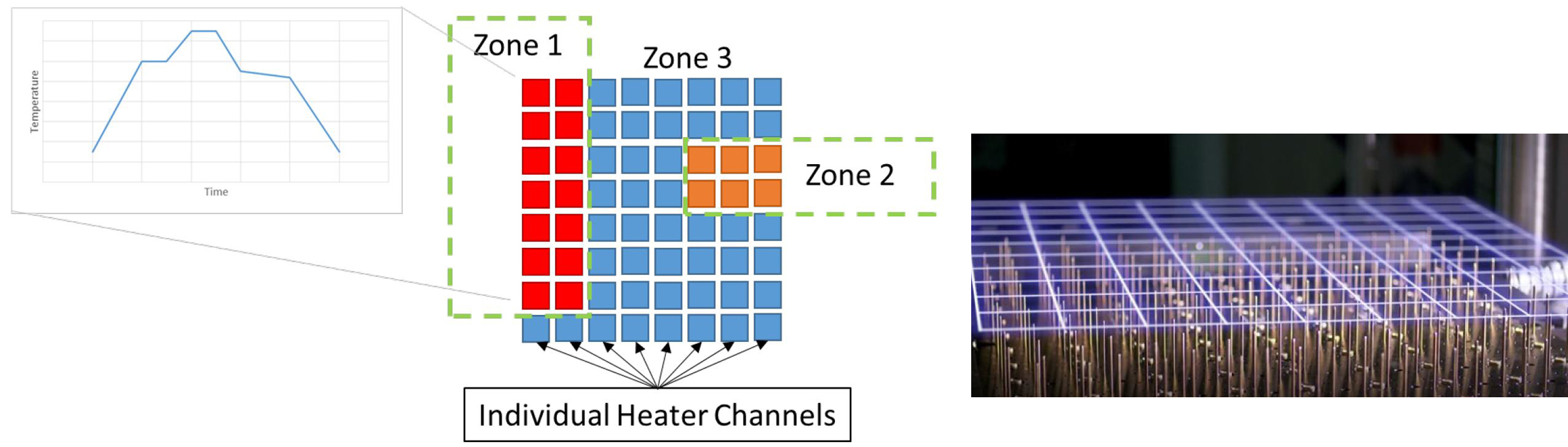
Hoewel de besturingssoftware van de PtFS-apparatuur zowel analoge als digitale verwarmingsstrategieën heeft die kunnen worden aangepast aan verschillende verwarmingsscenario's, gebruikt de RAPM-cel analoge regeling. Dit vereist auto-tuning van het systeem om het verwarmingsvermogen bij de beoogde temperaturen te bepalen. De vermogensniveaus voor elke verwarming worden ingesteld om over- of onderschrijding tijdens verwarming/koeling-hellingen te voorkomen en om temperatuurinstelpunten te handhaven. De auto-tune bepaalt automatisch constante waarden voor een gewijzigde Proportionele Integrale Afgeleide regelmethode voor elk verwarmingskanaal bij elke gespecificeerde temperatuur. Zodra de auto-tune is voltooid, kunnen voor elke zone verwarmingsprofielen worden geschreven. Alle thermische profielen zijn geverifieerd om er zeker van te zijn dat het composietonderdeel werd blootgesteld aan temperaturen binnen ±5,5 °C (±10 °F) van het gewenste instelpunt.
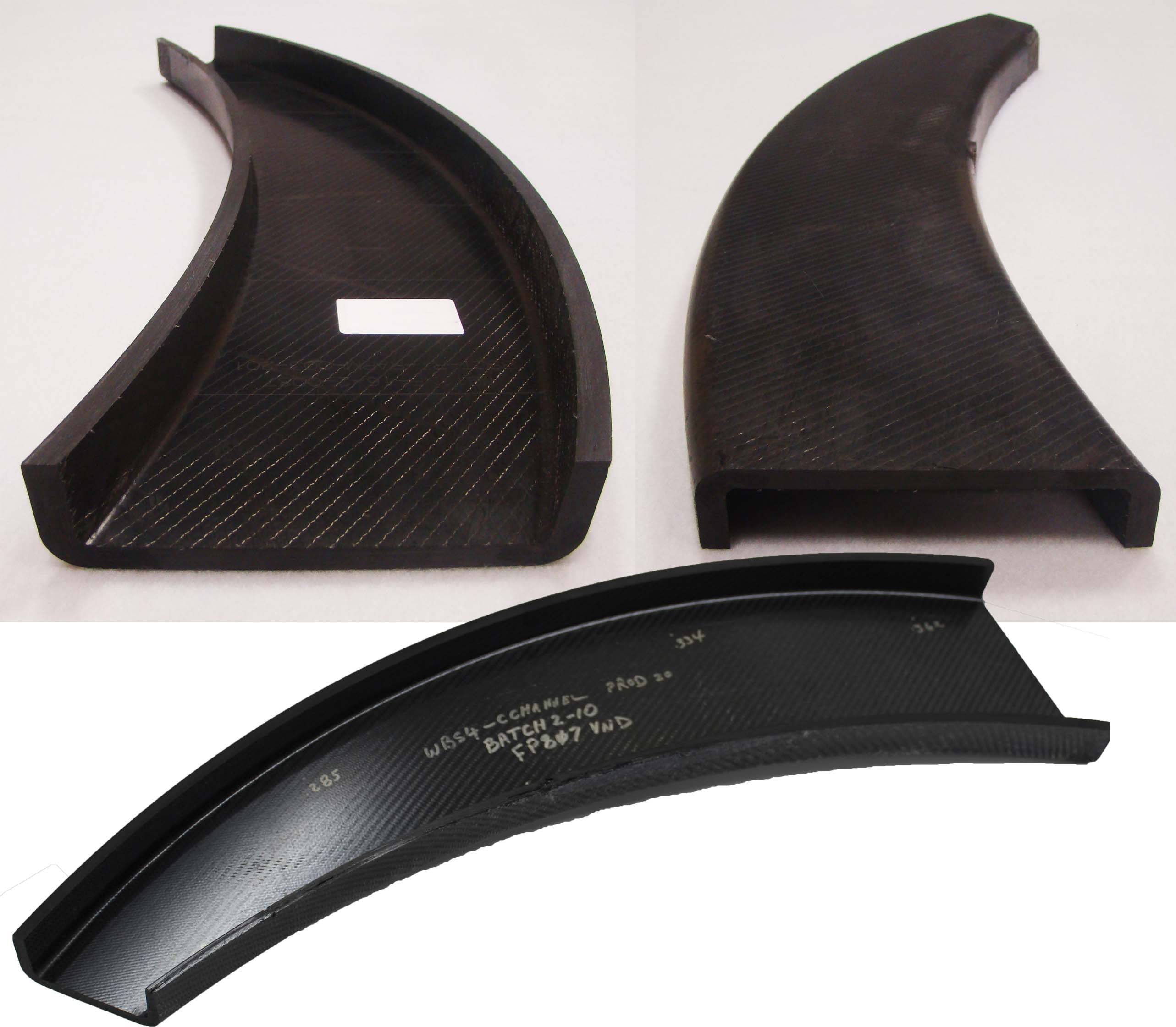
De Boeing PtFS-cel heeft een maximale temperatuur van 440°C. Aanvankelijk, toen Boeing meerdere cycli met hoge temperaturen per dag verwerkte, was er bezorgdheid dat bepaalde componenten beschadigd zouden kunnen raken door een gebrek aan koeling tussen de verwerkingscycli. Wel is het koelsysteem in sep-okt 2019 geüpgraded, inclusief extra ventilatorcapaciteit voor warmteafvoer. Met deze verbeterde koeling kan de cel continu verwerken bij 440 °C.
Door gebruik te maken van een groot volume perslucht bij omgevingstemperatuur als koelmethode, was de koeling van het gereedschapsoppervlak snel nabij de bovenkant van het temperatuurbereik, maar vertraagde het aanzienlijk toen het 60 °C (140 °F) bereikte. Tijdens verhitting tot thermoplastische temperaturen (>350°C) steeg de temperatuur van het gereedschapsoppervlak met een gemiddelde snelheid van 41°C/min (74°F/min). Tijdens het afkoelen van dezelfde run was de piekgemiddelde koelsnelheid 36°C/min (65°F/min). Het gebruik van perslucht voor koeling zorgde voor een meer continue koeling en in combinatie met actief thermisch beheer (d.w.z. verwarmen indien nodig), bleef de temperatuur redelijk lineair tijdens het afkoelen.
Isothermische TS prepreg-stempeling
De eerste deelproeven met behulp van de PtFS-werkcel waren voor TS-RAPM-001 toegangspanelen met kralen gemaakt met thermohardende prepreg compressievormen (stempelen). De tool voor dit onderdeel beslaat 112 van de 180 kanalen in de RAPM PtFS-werkcel. Dit omvat 56 kanalen op het bovenste gereedschapsvlak en 56 kanalen op het onderste gereedschapsvlak. Het eigenlijke deel beslaat echter niet het geheel van dat gereedschap - maar beslaat slechts 30 van die 56 kanalen voor elk gereedschapsvlak, boven en onder. De onderstaande afbeelding toont de plaatsing van de 78 thermokoppels (TC's) die worden gebruikt voor RAPM-001-onderdelen - 39 voor de bovenzijde en 39 voor de onderzijde met dezelfde plaatsing voor beide. Het aantal TC's omvat één per cel (verwarmingskanaal) plus extra TC's in warme en koude gebieden die zijn geïdentificeerd in de thermische CFD-analyse.
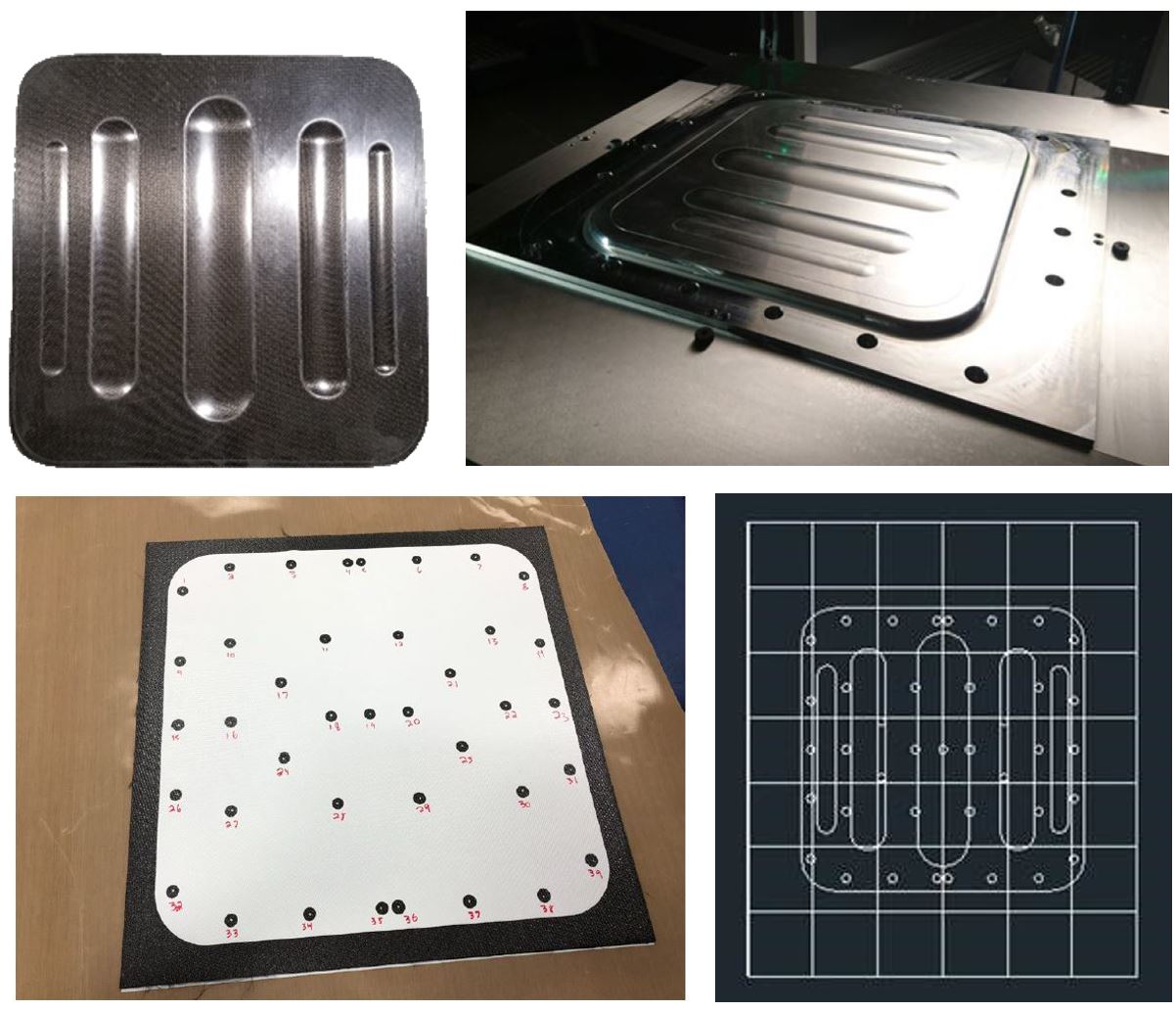
Het lege vlak van het gereedschap werd getest op temperatuuruniformiteit en de test werd vervolgens herhaald na het inbedden van thermokoppels in het midden van een 16-laags koolstofvezel geweven/epoxy laminaat. Zodra composietmateriaal is toegevoegd, wordt de temperatuurverdeling van het gereedschapsoppervlak strakker omdat het composiet fungeert als een warmteoverdrachtspad. Ook was de temperatuuruniformiteit binnen het composietlaminaat strakker dan de aflezingen van het gereedschapsoppervlak. De enkele TC in Run 1 (zie de afbeeldingen hieronder, bovenaan de grafiek aan de rechterkant) die oscilleerde boven het gewenste temperatuurbereik was nabij de rand van het onderdeel en wordt vermoedelijk veroorzaakt door temperatuurschommelingen van aangrenzende cellen buiten de snijlijn van het onderdeel.
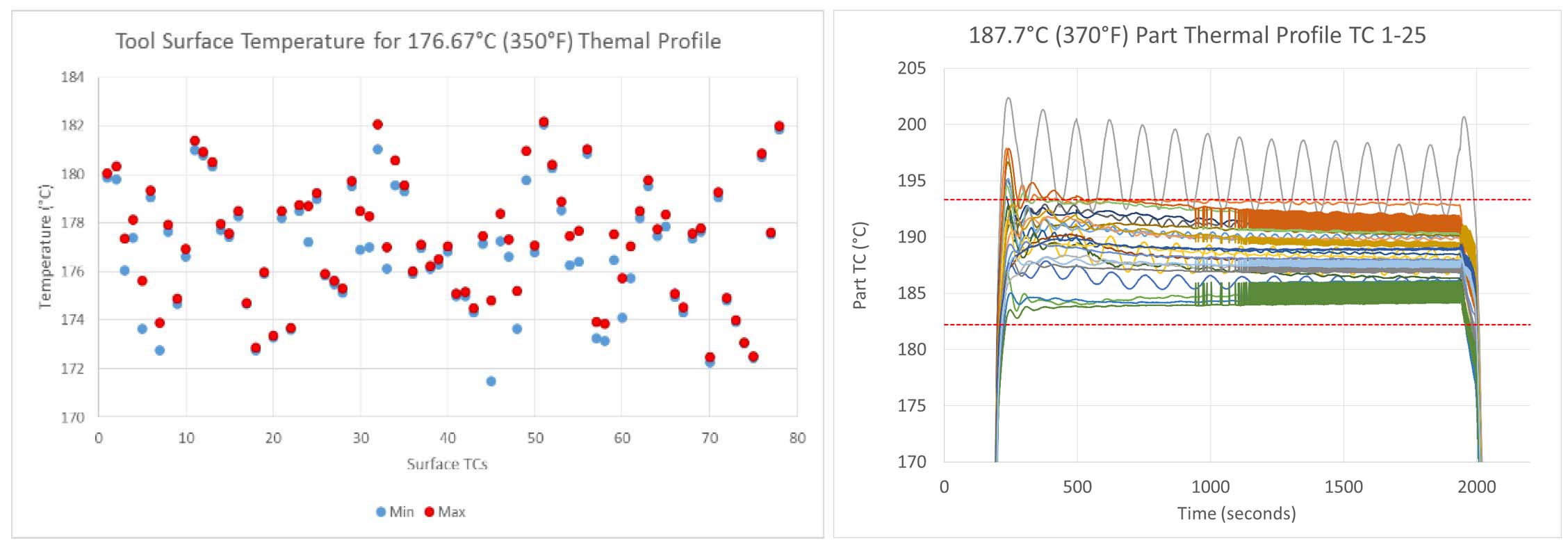
Isotherm persgieten van de bewerking hield het gereedschap op 176,7°C (350°F) binnen de tolerantie van ±5,5°C (±10°F). Voor TS-RAPM-001 werd de volgende volgorde gevolgd:
- Systeem verwarmt tot 187,7°C in app. 8 minuten
- Samengestelde blanco geladen in hot tool
- Tool gesloten om 12:09 (bijvoorbeeld)
- 30 minuten tijd op gereedschap om composiet te gelen
- Eerste drukfase:aanvankelijke snelle verwarming van de blanco terwijl het uitpersen van hars tot een minimum wordt beperkt
- Tweede druktrap:oplopend tot 300 psi om een goede consolidatie te garanderen en de groei van lege ruimten te voorkomen
- Verwijder "groene" composiet uit hot tool voor nabehandeling
Dit proces leverde onderdelen van hoge kwaliteit op en demonstreerde onderdelen met een lagere cyclustijd dan de huidige composietprocessen. Een hogere procestemperatuur zou het composiet nog sneller kunnen laten geleren, maar kan ook materiaaldegradatie en risico op exotherm veroorzaken. Dit was een punt van zorg omdat PtFS-gereedschap geen traditionele grote thermische massa gebruikt om exotherm te absorberen, maar in plaats daarvan vertrouwt op actieve koeling van de achterkant van gereedschappen met lage thermische massa om exotherm te verdrijven.
De PtFS-cel werd ook gebruikt om TS-RAPM-012 "wave"-uitdagingsonderdelen te maken. Met behulp van eerdere ontwikkelingsproeven werd vastgesteld om deze onderdelen uit te harden met behulp van een isotherme cyclus van 30 minuten bij 177°C, gevolgd door een nabehandeling van 2 uur bij dezelfde temperatuur. Verschillen met eerdere proeven waren echter een agressievere geometrie en een quasi-isotrope lay-up met behulp van CYCOM 5320-1 epoxy - standaard voor lucht- en ruimtevaartonderdelen buiten de autoclaaf - gecombineerd met 8-harnas satijn en unidirectionele koolstofvezellagen en een buitenlaag van stijl 108 geweven glasweefsel aan één kant. De RAPM PtFS-controller is geprogrammeerd om een minimale hoeveelheid druk op het laminaat uit te oefenen totdat een juiste viscositeit is bereikt. Na deze eerste stap werd de laatste druk uitgeoefend om de uitharding te voltooien. Eén proef werd nagehard in een oven, terwijl de rest werd nagehard in de PtFS-kleminrichting om de tijd tussen de proeven te verkorten. Er zijn meerdere hoogwaardige onderdelen geproduceerd.
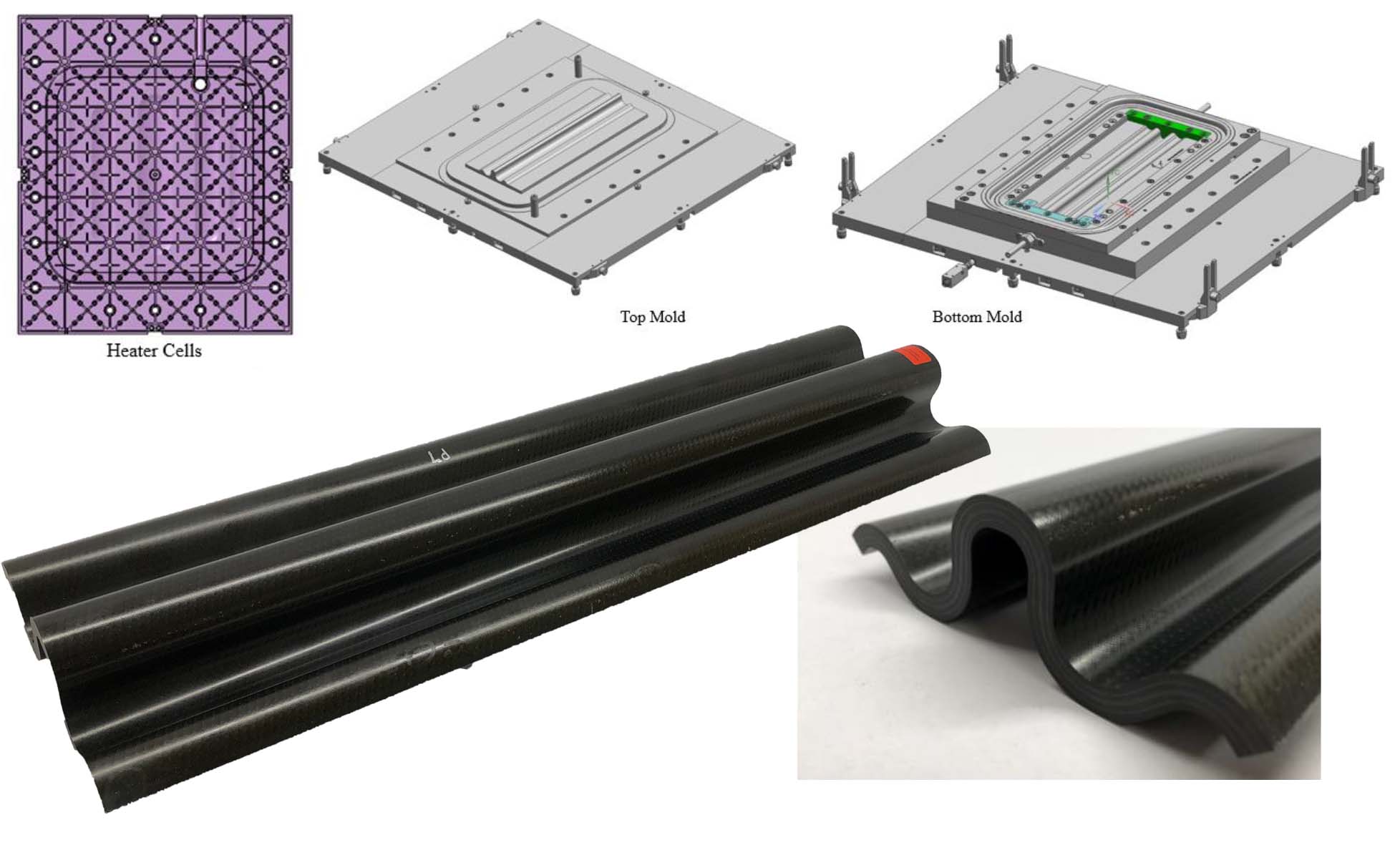
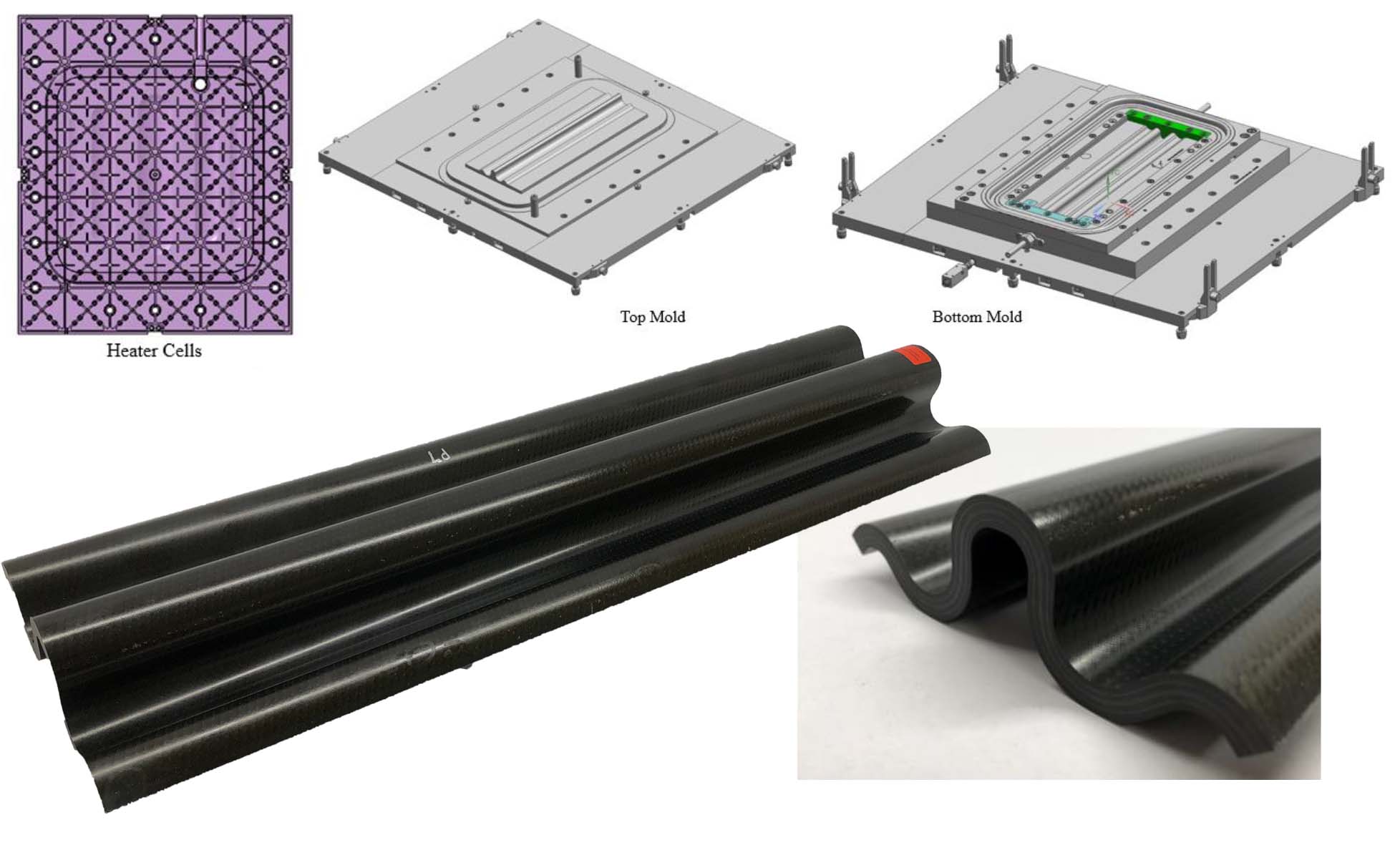
Dynamische temperatuurcycli voor harsinfusie
De proeven met harsinfusieonderdelen met behulp van de PtFS-werkcel begonnen met het RI-RAPM-003 gebogen C-kanaalonderdeel. Drie verschillende epoxyharssystemen werden aanvankelijk uitgeprobeerd:
- Solvay CYCOM 823, toegediend bij 80°C en daarna geleidelijk verhoogd tot 125 °C
- Huntsman FAF2 (quick-cure system) toegediend bij 100°C met een verblijf van 150°C
- Applied Poleramic (nu overgenomen door Kaneka) API DD3-84 (ook een snel uithardend systeem) toegediend bij 60°C met een verblijfstemperatuur van 160°C.
De voorvorm van het niet gekroesde weefsel werd geïnfuseerd, met 2°C/min verhoogd tot de gespecificeerde verblijfstemperatuur en vervolgens 60 minuten vastgehouden voor afkoeling. Voor de snel uithardende harsen paste de PtFS, naarmate de exotherme reactie vorderde, automatisch actieve koeling toe op specifieke gereedschapsgebieden om de gespecificeerde onderdeeltemperaturen te handhaven.
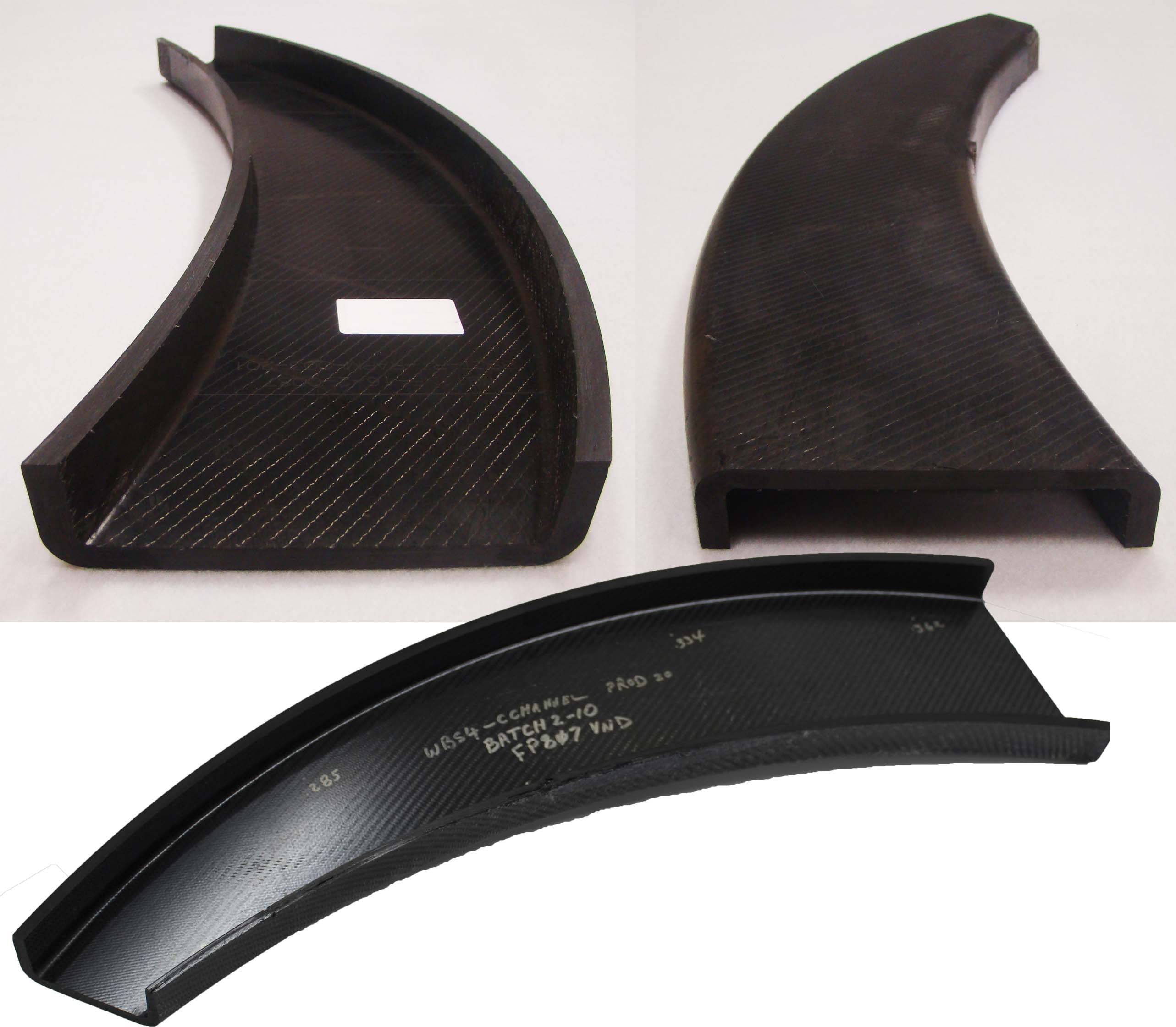
De PtFS-apparatuur was ook in staat om de positiecontrole te bieden ter ondersteuning van een gap-infusiemethode voor de RI-RAPM-003-onderdelen. Bij deze methode werd het hulpmiddel gesloten tot een initiële hoogte van de vacuümpakking, waardoor het hulpmiddel tijdens de infusie 1,3 millimeter open kon blijven. Nadat de infusie was voltooid, werd het gereedschap vervolgens de resterende afstand gesloten om de hars in de z-richting in de voorvorm te drijven. Onderdelen zijn met succes gemaakt met behulp van dit proces.
Dynamische temperatuurregeling voor thermoplastisch stempelen
De PtFS-apparatuur werd ook gebruikt om het RAPM-003 gebogen C-kanaal in thermoplastische composieten te maken. Het werd met name gebruikt om een complexe voorvorm, die van 32 naar 24 lagen over de lengte van het onderdeel viel, te consolideren tot een platte plano met een taps toelopende dwarsdoorsnede. De geconsolideerde blanco's werden vervolgens naar ATC Manufacturing (Post Falls, Idaho, VS) gestuurd, die het laatste deel met verticale flenzen afstempelde.
Het materiaal dat werd geconsolideerd voor het TP-RAPM-003 gebogen C-kanaal was een koolstofvezel 2x2 keperstof gepoedercoat met polyetheretherketon (PEEK). De PtFS-werkcel werd gebruikt om een AZ31-magnesiumblaas superplastisch te vormen over de thermoplastische lading, de blaas te verwarmen en op te laden tot een PEEK-procestemperatuur van 400°C in ca. 55 minuten.
Bij deze vormingstemperatuur werd argongas op de blaas aangebracht, waardoor consolidatiedruk op het thermoplastische composietmateriaal werd uitgeoefend. De cel koelde vervolgens de blaas af en laadde op tot onder de PEEK-kristallisatietemperatuur in 30 minuten, voor een totale cyclustijd van 3 uur.
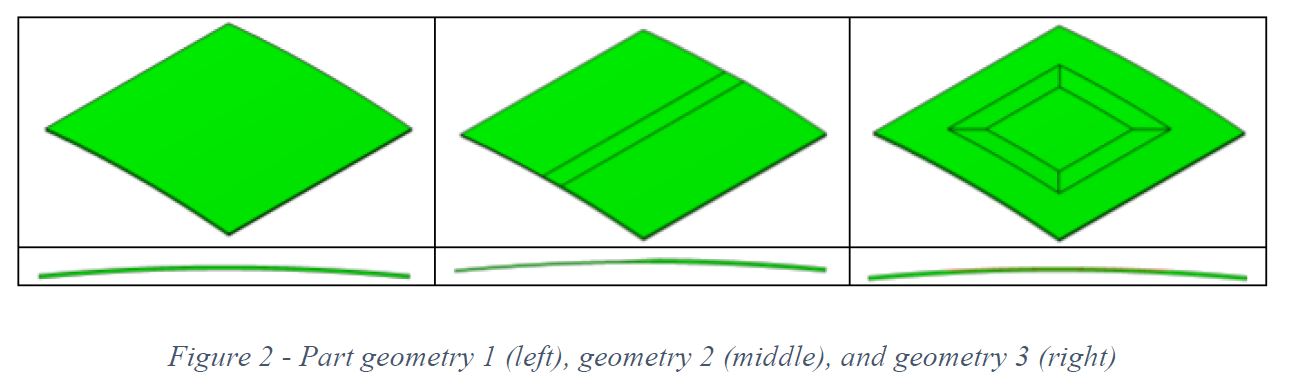
Dia 11 hierboven toont de progressie in uitgeoefende druk tijdens de superplastische vorming van de blaas en consolidatie van de thermoplast - toenemend van 20 psi tot 140 psi nadat de blaas de superplastische vormingstemperatuur had bereikt, die werd gehandhaafd door de koeling. Preforms werden met succes geconsolideerd en naar ATC Manufacturing gestuurd, waar onderdelen werden gestempeld voor deze uiterst uitdagende geometrie.
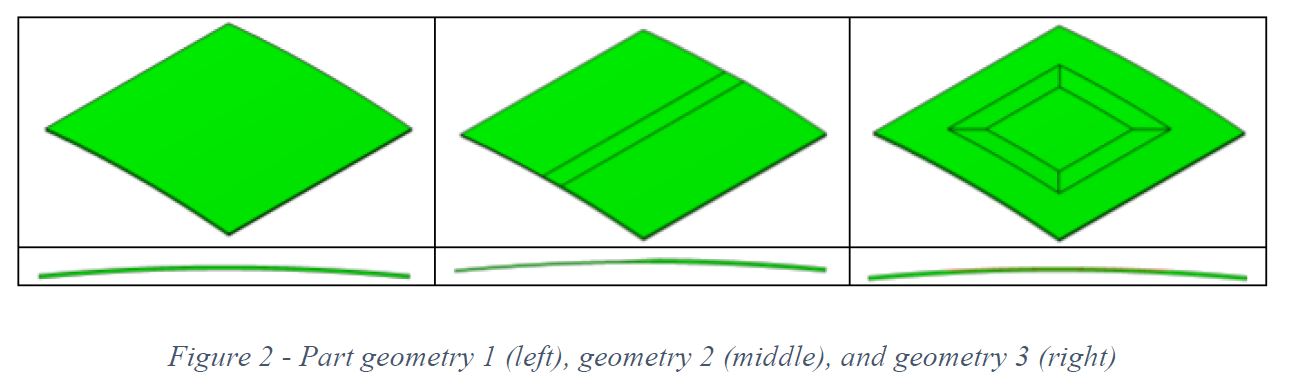
De PtFS-cel werd ook gebruikt voor het in één stap stempelen van blanco naar onderdeel van TP-RAPM-017-panelen gemaakt van een uitgebalanceerde en symmetrische lay-up van unidirectionele (UD) koolstofvezel/polyetherketoneketon (PEKK)-tape in een onderzoek naar hoe verschillende opties en onderdeelkenmerken beïnvloeden de blaasvorming. De TP-RAPM-017-panelen waren 40,6 bij 40,6 centimeter groot en hadden een zachte contour van 1,3 centimeter hoog. Drie verschillende onderdeelgeometrieën werden geëvalueerd - vlak (geen laagval), enkellaagse laaglaag en fotolijst - met 32 lagen in dikke gebieden, 16 lagen in dunne gebieden en een 20:1 laagsvalverhouding daartussenin. De onderdeelcyclustijd was 1,5 uur voor alle geometrieën.
De gereedschapsvlakken zijn vervaardigd uit Invar 42 om het beste te passen bij de thermische uitzetting van de UD thermoplastische composiettape. UD-tapeply-kits werden gesneden en verzameld, ultrasoon aan elkaar gelast en in het uithardingsgereedschap geplaatst, waar ze werden verwarmd tot 385 ± 15°C. Er werden verschillende drukcycli getest en het onderdeel werd vervolgens afgekoeld tot onder de 220 °C, waarna de druk werd afgelaten en het onderdeel uit de vorm werd gehaald.
Een voorbeeld van een drukcyclus voor geometrie 1 was 20 psi bij kamertemperatuur, oplopend tot 140 psi nadat het achterblijvende thermokoppel een smelttemperatuur van 310°C bereikte en vervolgens afgekoeld met 10°C/minuut onder druk totdat het deelthermokoppel onder 220°C gemeten werd . Initiële drukken van 20 psi, 30 psi, 50 psi en 70 psi werden getest. Drukhellingen werden ook gevarieerd van 10 psi per minuut tot 10 psi per 15 seconden, tot de maximale druk van 140 psi.
Een opmerkelijk resultaat was dat alle panelen slechte C-scanresultaten vertoonden waar de lagen ultrasoon waren vastgelast. Voor de beste resultaten moeten dergelijke hechtlassen dus buiten de trimlijn van het onderdeelnet worden geplaatst. Er werden acceptabele onderdelen geproduceerd, maar sommige onderdelen vertoonden een slechte consolidatie aan de randen van de lagen. Dit werd verholpen door de initiële verdichtingsdruk te verhogen tot 30 psi voorafgaand aan het opwarmen. Deze drukverhoging veroorzaakte echter enige oppervlakteruwheid/matte afwerking aan de blaaszijde van het onderdeel. Ook vertoonden sommige panelen met geometrie 2, gemaakt met behulp van de initiële verdichtingsdruk van 50 en 70 psi, rimpels in het midden van de onderdelen. Men geloofde dat deze hogere druk mogelijk heeft verhinderd dat de lagen langs elkaar schuiven tijdens de verwerking, waardoor de rimpels in de onderdelen werden vastgehouden.
Een andere geprobeerde variatie was het vervangen van argongas door goedkoper stikstofgas om de blaas onder druk te zetten, maar dit verminderde ook de kwaliteit van het onderdeel, inclusief oppervlakteruwheid/matte afwerking die hogere niveaus van verzwakking veroorzaakte in C-scanresultaten, hoewel er geen porositeit werd gevonden in kruis- secties.
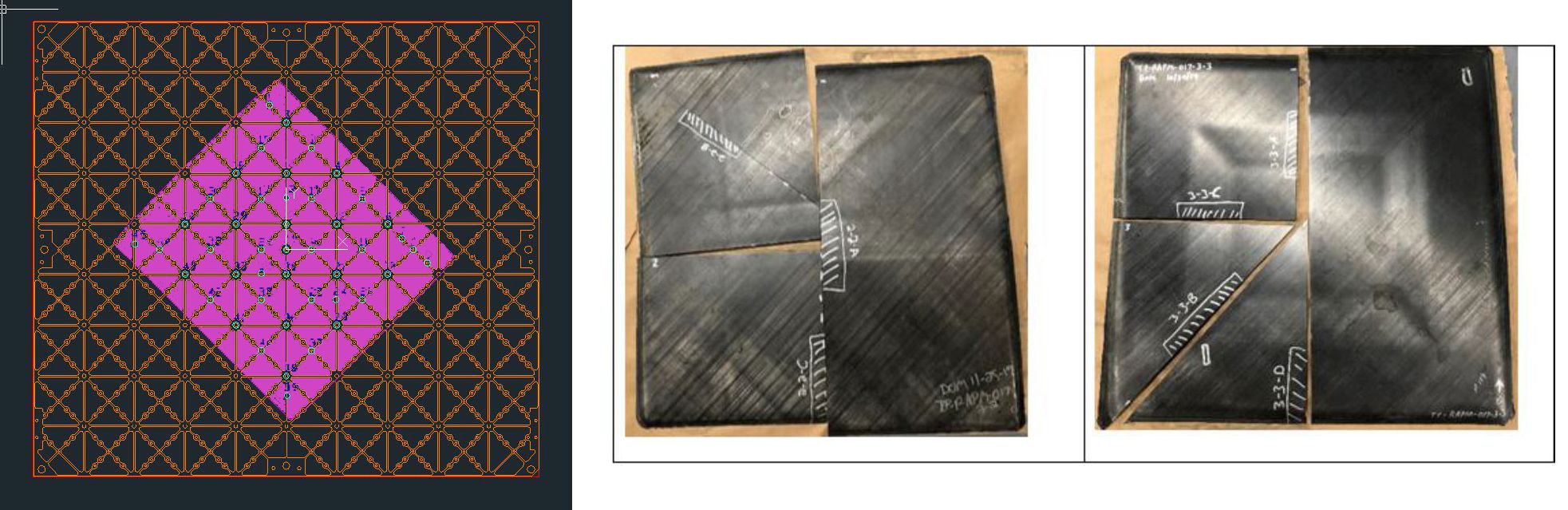
Voor- en nadelen van PtFS in RAPM
De PtFS-werkcel vertoonde wel een snelle verwarming (<10 minuten voor epoxy-uitharding bij -180°C). In combinatie met geautomatiseerde gereedschapswisselingen kan dit snelle onderdeelwisselingen mogelijk maken en de kosten van composietonderdelen voor korte productieruns verlagen. PtFS is ook zeer geschikt voor dynamische runs bij hoge temperaturen (in tegenstelling tot isotherme onderdeelcycli).
De capaciteit van de Boeing St. Louis PtFS-cel werd aanzienlijk vergroot tijdens het RAPM-programma, dankzij verbeterde software-upgrades voor een betere thermische uniformiteit en kleminrichtingcontrole, verbeterde koelcapaciteit en thermokoppelcontrole, evenals een geautomatiseerd pressclaafdrukcontrolesysteem. Verdere capaciteitsverhoging is mogelijk door gebruik te maken van de enorme hoeveelheid gegevens die elke seconde door het systeem worden gegenereerd en geregistreerd, inclusief elk instelpunt van het verwarmingskanaal, de vermogenshendel van de verwarming, het persluchtniveau, enz. Door machine learning toe te passen op deze gegevens kan de kwaliteit van de onderdelen en procesverbeteringen. Verdere softwareverbeteringen kunnen deze gegevens ook in staat stellen om verwerkingsanomalieën te identificeren, zoals overmatige benodigde energie en lage responsiviteit van specifieke gereedschapslocaties.
"PtFS biedt veel maatwerk, zoals de naam al aangeeft:productie tot functionele specificatie", zegt Hahn, "maar dat maatwerk kan tijdsinvestering vergen om het systeem op te zetten en te 'afstellen' voor een nieuwe gereedschap-/onderdeelconfiguratie." De meeste machinaal bewerkte metalen gereedschapsvlakontwerpen voor RAPM werden geproduceerd door Surface Generation in het VK. Boeing en Surface Generation hebben echter een Amerikaanse gereedschapsontwerper en een Amerikaanse gereedschapsfabrikant "opgeleid" om aan te tonen dat het ontwerp van het vormvlak in de VS kan worden uitgevoerd door andere bronnen dan Surface Generation. Dat gereedschapsvormvlak, CMD-TP-RAPM-008-503, is met succes gebruikt om TP-RAPM-008-203 toegangspanelen met korte vezels te maken.
"Terwijl een vorm van temperatuurregeling in het gereedschap en/of onderdeel helpt bij het gieten van alle composietonderdelen", legt Hahn uit, "is eigenlijk controle van de temperatuur op kritieke gebieden en tijden nodig, en dit varieert per onderdeel en proces. Het is dus van cruciaal belang om de temperatuurregeling te begrijpen die daadwerkelijk nodig is om een bepaald onderdeel te vormen. De 180 zones in PtFS zijn nuttig, maar ook duur omdat ze elk een bewerkt kanaal in het gereedschap vereisen. Als het onderdeel alleen een buitenste en binnenste zone of een specifieke zone langs een triggerpoint-geometrie nodig heeft, kan een andere oplossing goedkoper zijn. Dit opent echter wel het debat over wat de beste benadering is om een fabricagecel voor composietonderdelen te ontwikkelen die flexibel is voor meerdere soorten processen en onderdelen."
Boeing en DARPA zullen doorgaan met het toevoegen van informatie aan dit debat als ze het RAPM-programma in 2020 afronden en verdere resultaten publiceren.
Hars
- Uitdagingen bij de ontwikkeling van nieuwe producten
- Circuit met een schakelaar
- Rekenen met wetenschappelijke notatie
- Vraag en antwoord met een Industry 4.0 Solution Architect
- Boeing werkt samen met Microsoft om luchtvaartanalyse te verbeteren
- De ontwikkeling van moderne kunststoffen
- Solvay werkt samen met Boeing voor gezichtsschermen tegen coronavirus
- SABIC werkt samen met NUDEC om hernieuwbare pc te lanceren
- 3D-print composieten met continue vezels
- Projecten van de grond krijgen met outsourcing
- Boeing bevestigt overeenkomst met Siemens' Mentor Graphics