Flexibele koolstofvezelplaten maken hoogwaardige schoenen mogelijk
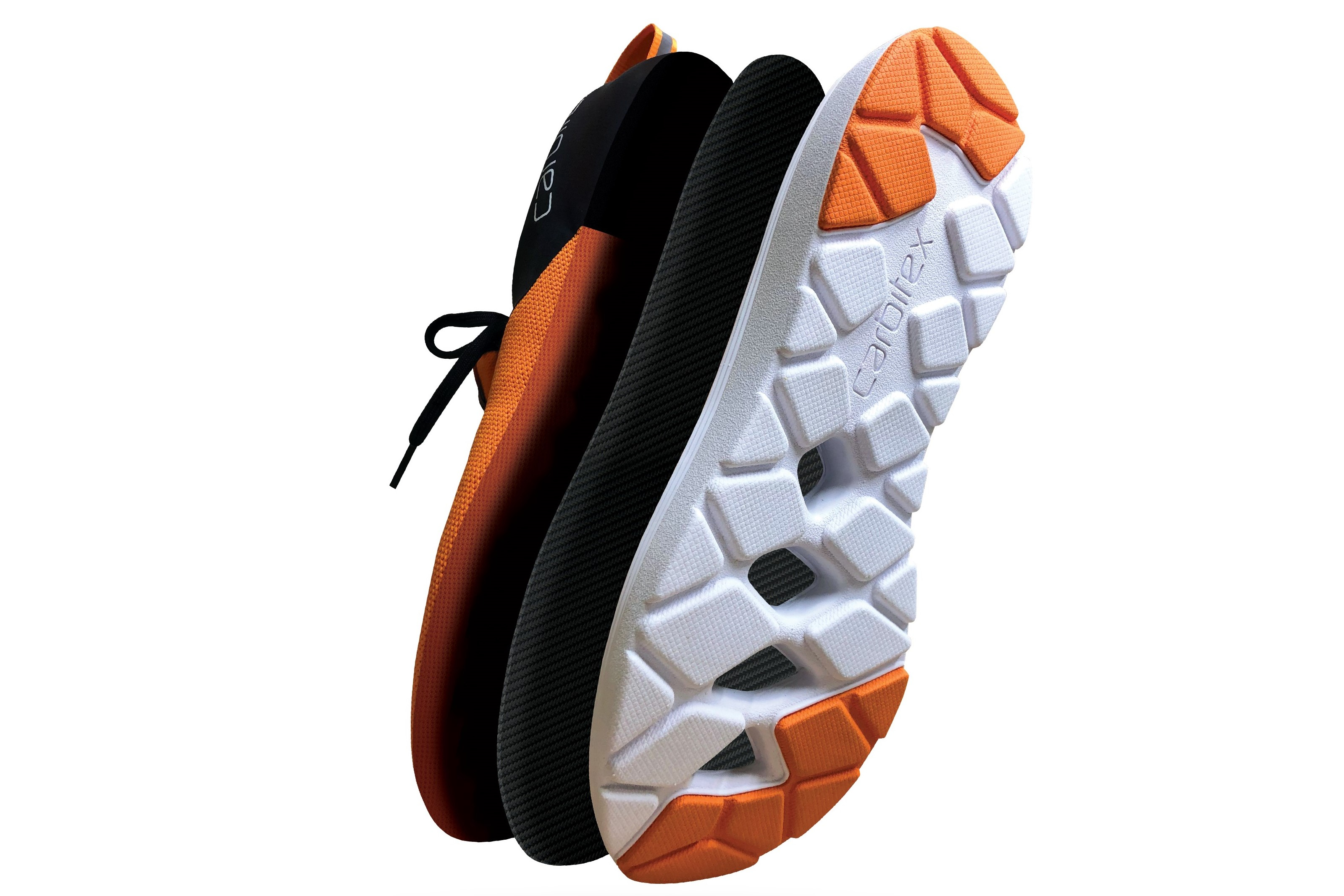
Tussenzoolplaten, schachten en andere componenten van koolstofvezel verbeteren al jaren de prestaties en verminderen het gewicht van topsportschoenen. Maar, legt Junus Khan, oprichter en voorzitter van Carbitex Inc. (Kennewick, Wash., VS) uit, zelfs met composieten moeten schoenontwikkelaars doorgaans compromissen sluiten als het gaat om materiaalkeuze voor tussenzoolplaten:de keuze is tussen een materiaal dat stijf genoeg is om ondersteuning van de voet tijdens de vereiste activiteit, hoewel deze inflexibel en zwaar kan zijn, of een materiaal dat licht en flexibel is, maar niet zoveel ondersteuning biedt. Ofwel de keuze, of een compromismateriaal dat ergens tussenin zit, maakt de schoen - en de drager - inherent inefficiënt, iets dat Carbitex zegt te hebben kunnen overwinnen door de ontwikkeling van zijn productlijn van flexibele koolstofvezel / thermoplastische composietmaterialen.
Khan merkt echter op dat hij oorspronkelijk niet van plan was de schoenenindustrie te transformeren. Iets meer dan 10 jaar geleden nam Khan, wiens achtergrond in economie is, maar die via zijn werk in de auto-industrie leerde over koolstofvezelcomposieten, een kijkje op de bagagemarkt en vroeg zich af waarom bagagefabrikanten probeerden de esthetiek van koolstofvezel na te bootsen. met behulp van ballistisch nylon en andere stoffen, in plaats van echte koolstofvezel te gebruiken. Omdat hij geen bedrijf kon vinden dat een zacht, buigzaam koolstofvezelproduct maakte dat geschikt was voor de bagagemarkt, besloot hij het zelf te gaan maken.
In 2010 begon Khan in zijn vrije tijd met het onderzoeken van verschillende koolstofvezelmaterialen in zijn garage en in 2011 werden zijn eerste materiaal en proces getest in het Amerikaanse Department of Energy Pacific Northwest National Laboratory. Op dat moment zegt hij:"Ik had een levensvatbaar concept en een beter begrip van de materiële ruimte", en hij besloot om van dit concept een bedrijf te maken, met als doel de ontwikkeling voort te zetten en uiteindelijk het materiaal te verkopen. Carbitex Inc. is opgericht in februari 2012.
Van bagage tot schoeisel
Khan legt uit dat andere bedrijven semi-flexibele koolstofvezelstoffen hebben ontwikkeld door een enkele laag stof tussen twee thermoplastische films te hangen. "Maar als je dat materiaal onder spanning trekt, is de faalmodus die films die van het oppervlak van de koolstof scheuren", zegt hij, wat betekent dat een neiging tot delaminatie de hoeveelheid daadwerkelijke flexibiliteit die beschikbaar is voor het laminaat kan belemmeren.
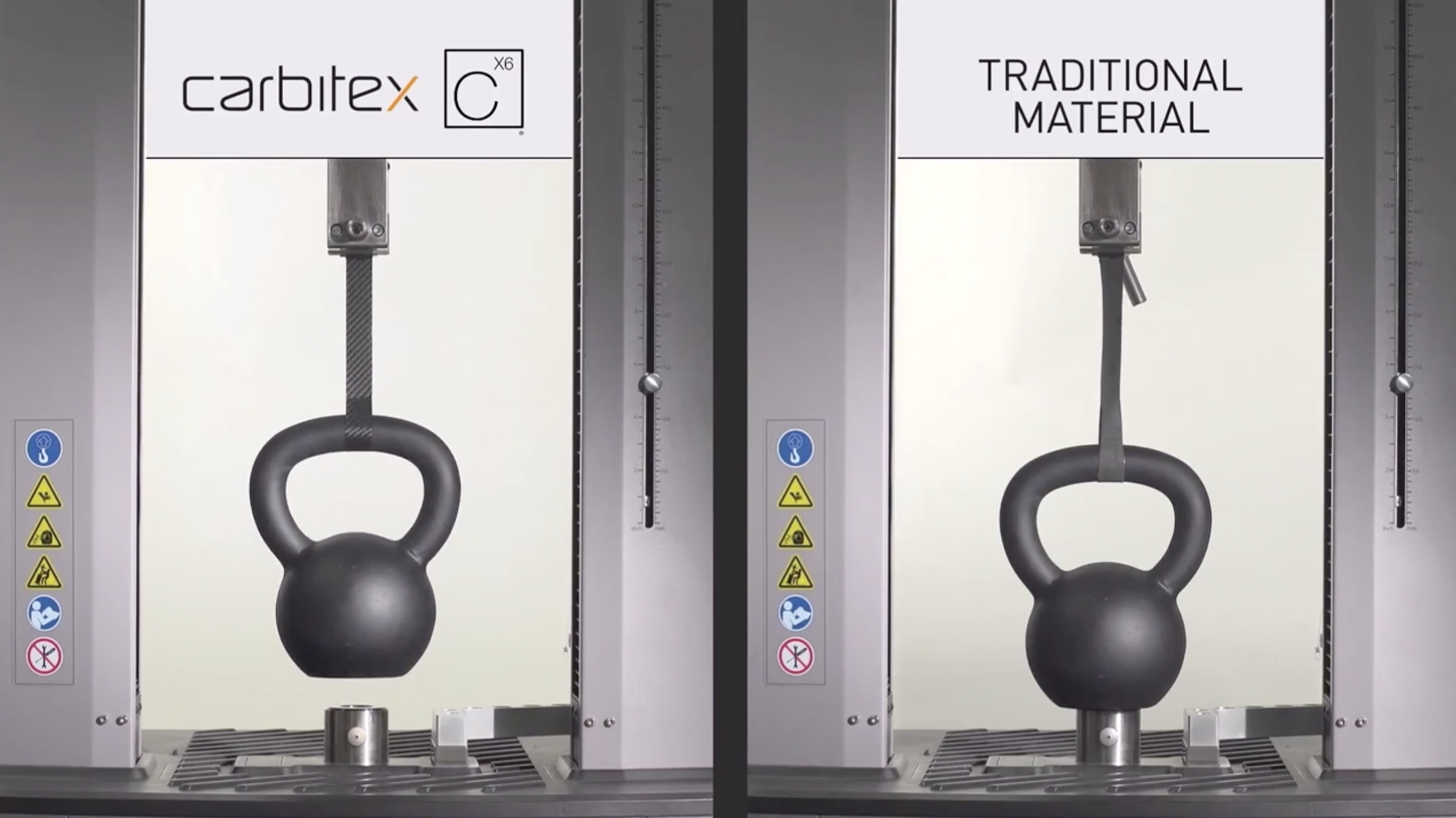
Het CX6-product van Carbitex, het oorspronkelijke productaanbod, is ook een enkele laag koolstofvezelstof gelamineerd tussen thermoplastische films. Maar, zegt Khan, de stof wordt eerst behandeld met een speciaal ontwikkeld bindmiddel dat, volgens een in 2015 ingediend Amerikaans octrooi Carbitex, de gelamineerde stof "flexibiliteit geeft die vergelijkbaar is met stof die niet is gelamineerd met polymeerfilms, en verbeterde hechting en treksterkte." Hij voegt eraan toe:"Als je ons CX6-materiaal onder spanning trekt, is de faalmodus dat de vezels daadwerkelijk breken, niet dat de film delamineert. Je krijgt echt die kenmerkende kracht van de koolstofvezel. ” Het materiaal zou ook zeer lage rekeigenschappen hebben in vergelijking met andere composietmaterialen, waarvoor Carbitex een toepassing vond in nauwkeurig vervaardigde schoencomponenten met verbeterde krachtoverdracht.
Carbitex begon zijn eerste CX6-product in de bagage- en handtassenindustrie te verkopen aan bedrijven als Tumi (South Plainfield, N.J., VS), zoals Khan oorspronkelijk van plan was te doen. Al snel begon Carbitex echter vragen te ontvangen van verschillende andere industrieën, zoals consumentenelektronica. Hoewel de groei opwindend was, zegt hij:"Tegelijkertijd begonnen we ons te realiseren dat we ons erg dun verspreidden." Ongeveer drie jaar geleden nam het bedrijf de beslissing om zich te concentreren op één markt met het meeste potentieel:schoenen.
Tegenwoordig levert Carbitex zijn koolstofvezelplaten aan de schoenenindustrie, waar ze worden gebruikt bij snowboarden, fietsen, watersporten, hardlopen, wandelen, modeproducten en meer. Een van de meest recente en best presterende schoenentoepassingen van het bedrijf is een voetbalschoen die in de herfst van 2020 door Adidas is uitgebracht.
AFX en DFX:schoeisel transformeren
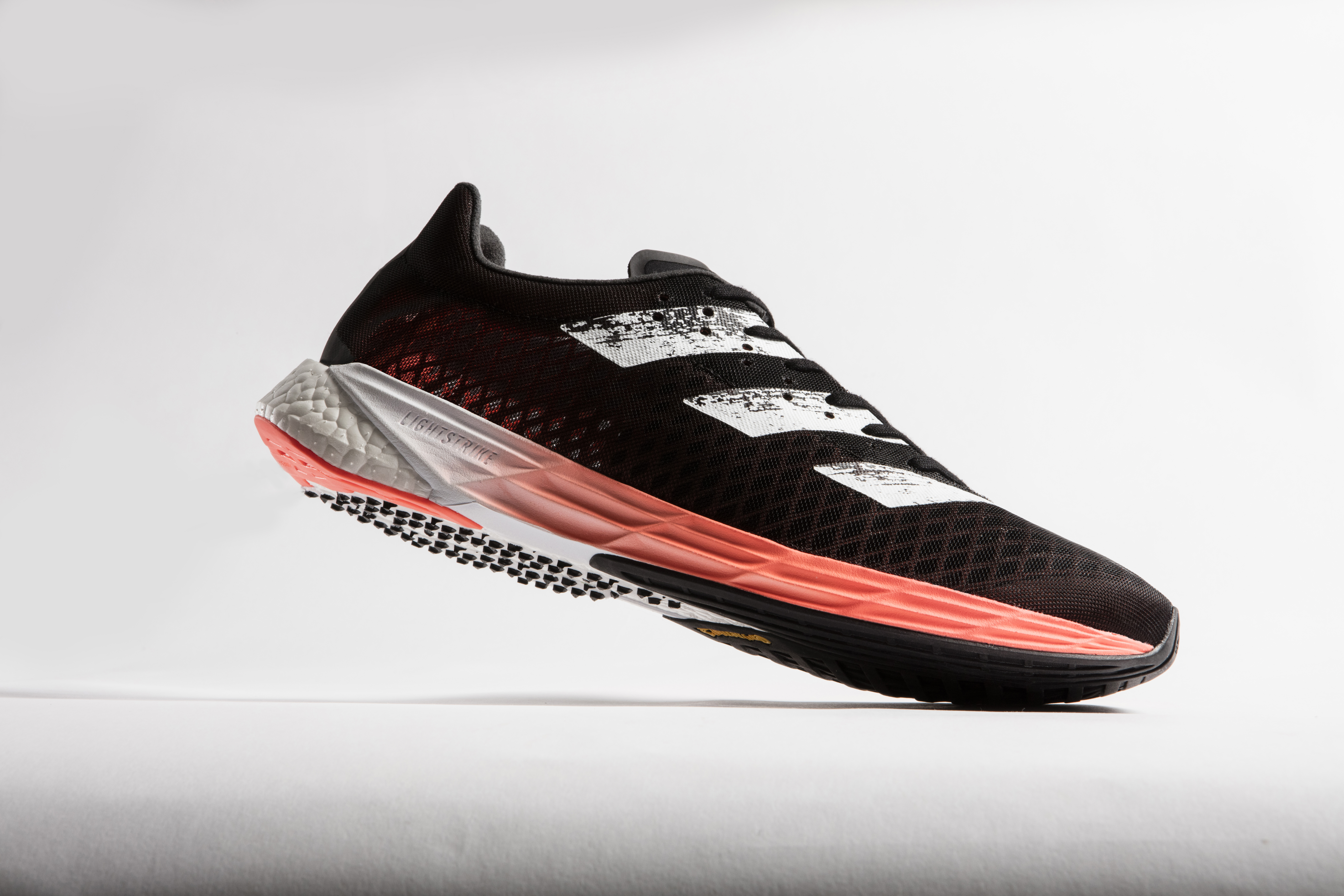
In de afgelopen jaren heeft Carbitex twee nieuwe composiettechnologieën uitgebracht, AFX en DFX genaamd. Volgens Khan is de stijfheid van een Carbitex-koolstofvezelplaat, in tegenstelling tot "typische composieten", waarvan de stijfheid wordt bepaald door de vezeloriëntatie en de laaglengte, uniform over de hele lengte. Waar andere composieten kunnen bestaan uit één type harssysteem en vezel, zegt hij, zijn de materialen van Carbitex complexer, met ingewikkelde lagen polymeervellen en weefsellagen, om de gewenste flexibiliteitseigenschappen te bereiken. "Een heel eenvoudige versie van ons AFX-materiaal kan twee verschillende soorten koolstofvezel bevatten tussen nog eens twee of drie verschillende soorten polymeer", zegt hij. "Het is een ingewikkeld lagensysteem en je moet begrijpen hoe die lagen moeten samenkomen voor [de vereiste] eigenschappen."
Over het algemeen begint het fabricageproces met het in lagen aanbrengen van weefsels, die kunnen worden behandeld met bindmiddelen of andere weefselbehandelingen, en polymeervellen in een paneel. Er wordt een verscheidenheid aan vezels van verschillende leveranciers gebruikt, hoewel Khan zegt dat de meeste producten van Carbitex vezels van Toray Composite Materials America (Tacoma, Wash., V.S.) en vaak gespreide touwstoffen van Hexcel (Stamford, Conn., V.S.) bevatten. Polymeren verschillen ook per toepassing, maar zijn doorgaans thermoplastisch vanwege flexibiliteit en vormbaarheid, "hoewel het soms niet volledig thermoplastisch is, afhankelijk van de toepassing", voegt hij eraan toe.
Deze panelen worden geconsolideerd in verwarmde persen; eenmaal verwijderd, worden afzonderlijke delen met een waterstraal gesneden en gevormd. Het produceren in panelen in plaats van het leggen van afzonderlijke onderdelen leidt tot een hogere output dan traditionele lay-ups, zegt Khan.
Productieproces
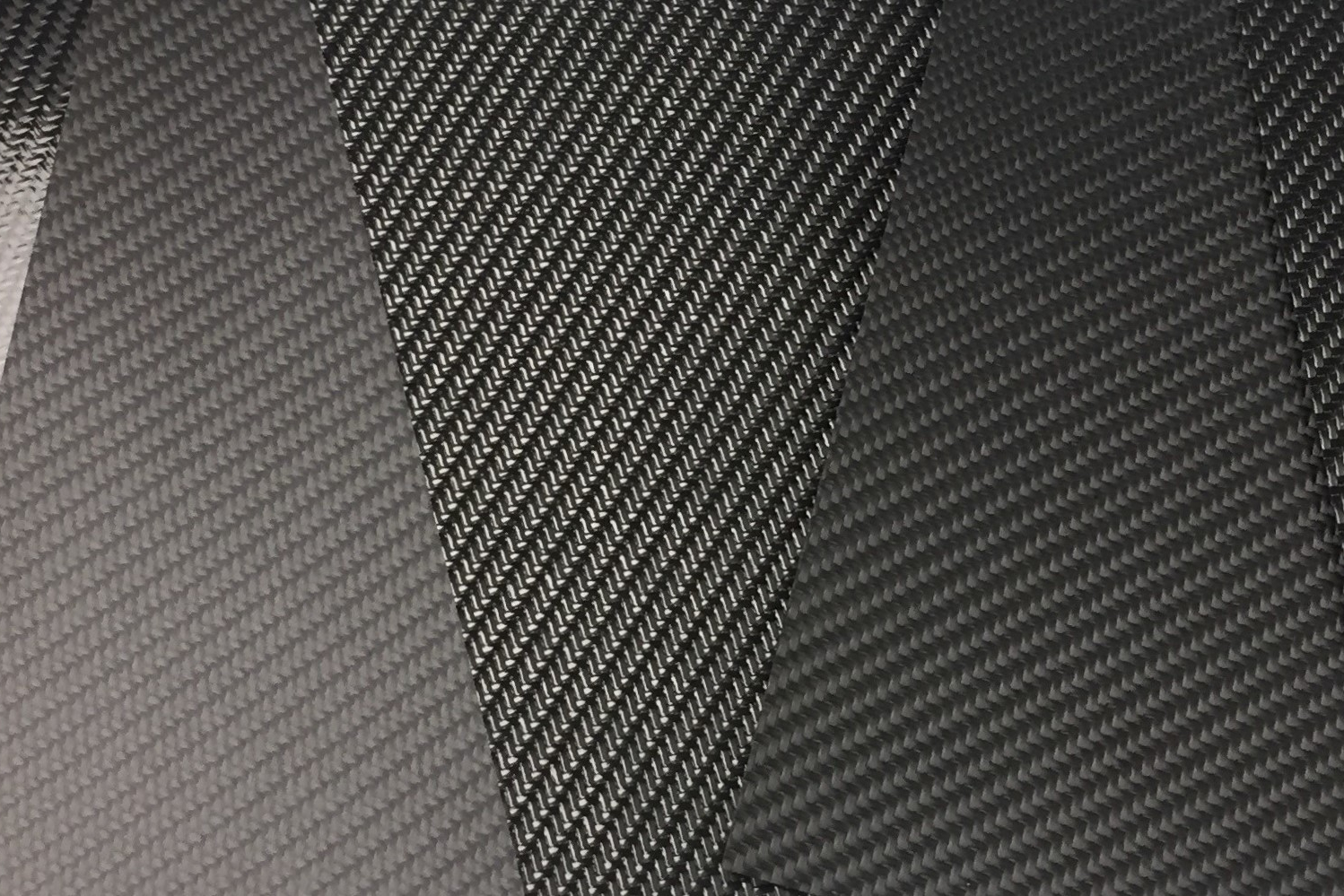
Eerst worden specifieke lagen geweven stoffen, prepregs en polymeerfilms op elkaar gestapeld tot een paneel.
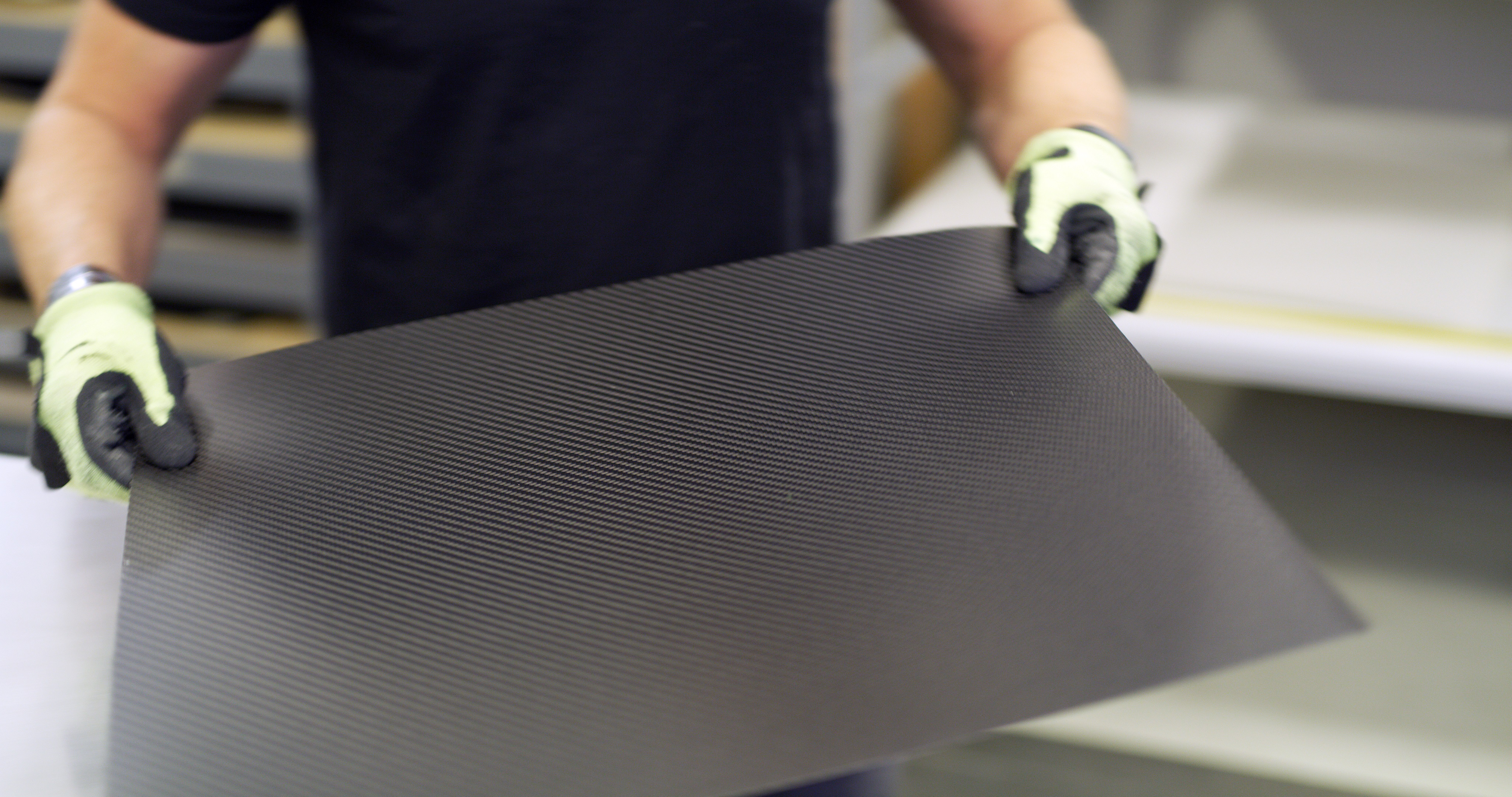
Vervolgens wordt het paneel geconsolideerd in een verwarmde pers.

Via waterjet worden specifieke componenten uit de uitgeharde panelen gesneden.
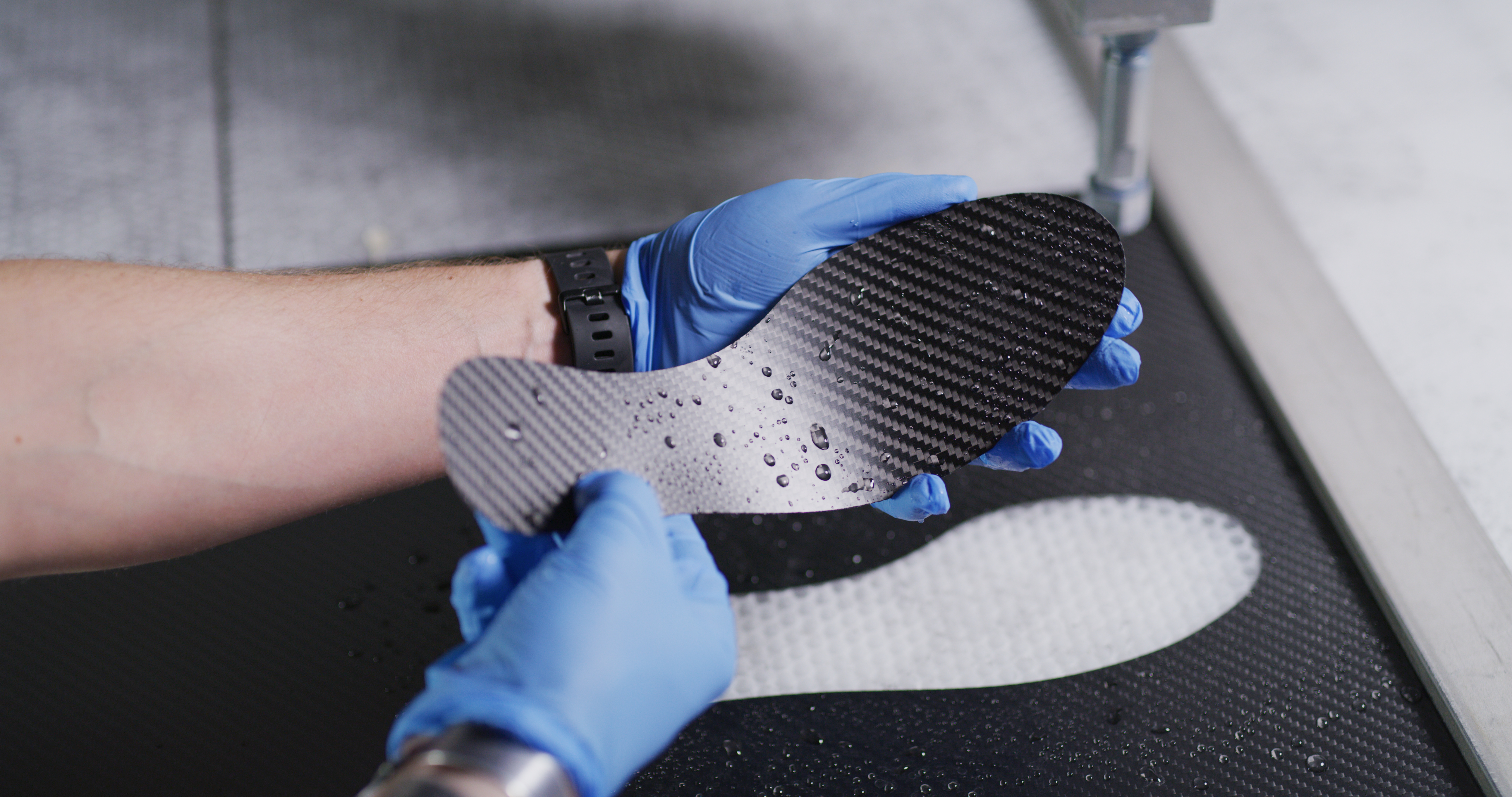
Door de lay-out van afzonderlijke onderdelen te vermijden, wordt een hogere doorvoer bereikt, zegt Carbitex.

De resulterende tussenzool van koolstofvezelcomposiet (afgebeeld is een DFX-component) zal worden geassembleerd tot een definitieve schoentoepassing.
Vorige volgendeNaast het balanceren van stijfheid en flexibiliteit is er een extra uitdaging bij het ontwikkelen van schoeisel:de menselijke voet kan maar in één richting buigen zonder te veel uit te rekken of te breken, dus schoenmaterialen moeten de veelzijdigheid hebben om in bepaalde richtingen te buigen, maar niet in andere.> . Carbitex bereikt dit, zegt Khan, door gecontroleerd knikken of buigen van de
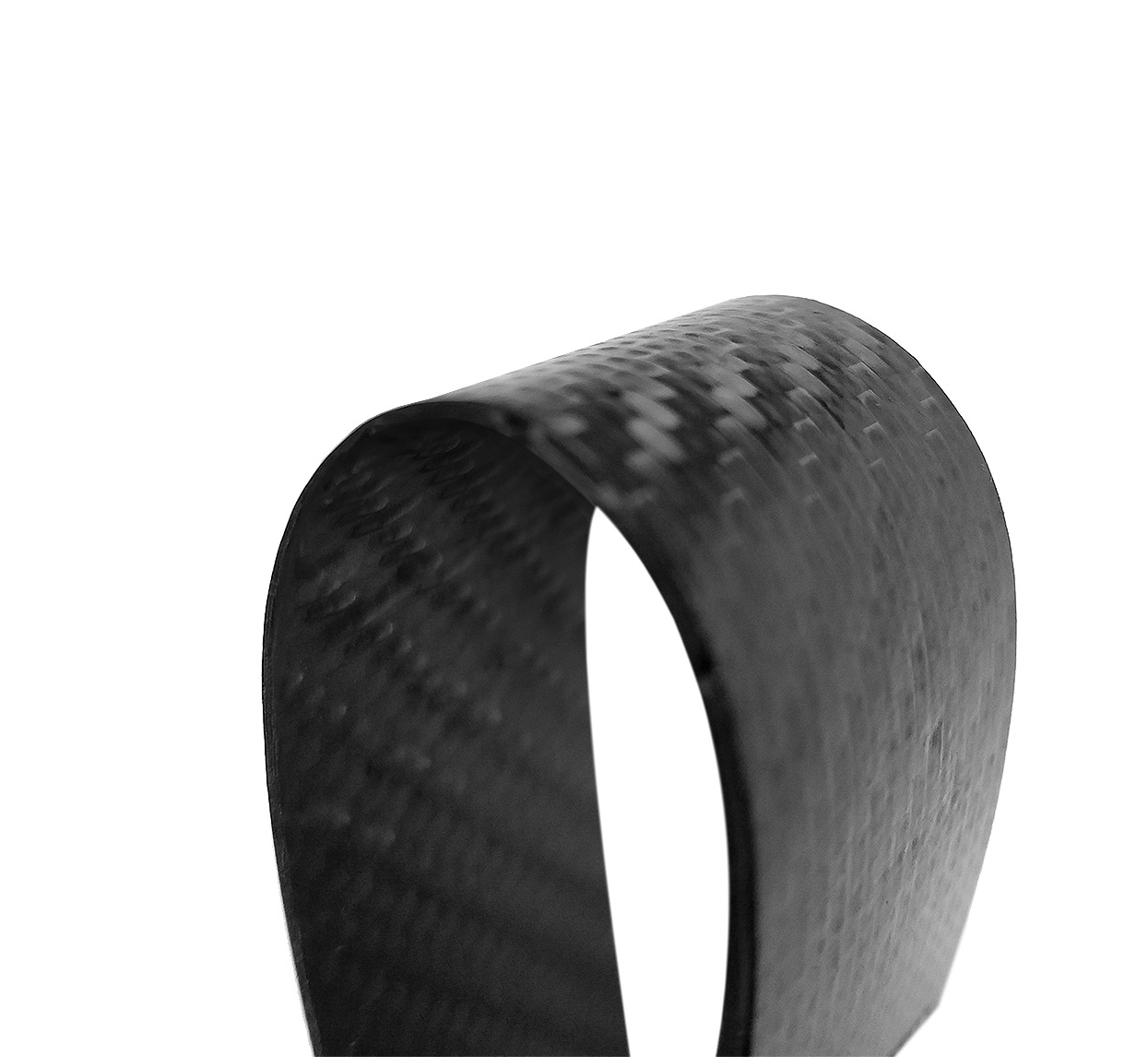
laminaat. "Typisch in composieten wordt het woord 'knik' toegeschreven aan falen," zegt Khan, "maar we hebben manieren bedacht om de vezel te laten knikken maar niet breken." Deze uitvinding, voegt hij eraan toe, werd aanvankelijk per ongeluk gemaakt, toen een collega zich realiseerde dat een bepaalde combinatie van vezel- en polymeerlagen had geleid tot een materiaal dat maar in één richting bezweek. "We realiseerden ons dat daar een bepaald voordeel aan moest zitten", zegt Khan, "dus begonnen we de lagen af te pellen, om te leren hoe het gebeurde en vervolgens te begrijpen hoe we het met opzet konden doen."
Het resulterende product wordt AFX genoemd, waarbij de "AF" staat voor "Asymmetrisch flexibel", wat aangeeft dat het in de ene richting buigt, maar volledig stijf is in de andere. Volgens een patentaanvraag uit 2018 bestaat het AFX-product van Carbitex uit een geweven stoflaag, een prepreg-laag en daartussenin ten minste één polymeerlaag, die worden gecombineerd tot een assemblage die vervolgens wordt gevormd en uitgehard. "De gelaagde opstelling heeft een hoge weerstand tegen buigen in een eerste richting en een lage weerstand tegen buigen in een tegengestelde tweede richting", zegt het patent.
"Onze technologie maakt het niveau van stijfheid en bescherming mogelijk in de richting die u het wilt", voegt Khan toe. Een wandelschoen met een AFX-tussenzool van koolstofvezel bevat bijvoorbeeld de ondersteuning en stijfheid die nodig zijn om de voet te beschermen tegen verkeerd buigen op oneffen of verticaal terrein, maar "wanneer je je voet gaat buigen om op een vlakke ondergrond te lopen, [ de laars is] net zo flexibel als bijvoorbeeld een hardloopschoen", zegt hij. AFX is ook lichter dan de combinatie van board en rubberen materialen die vaak worden gebruikt om wandelschoenen te versterken.
Het derde product van Carbitex heet DFX, een afgeleide van AFX dat staat voor "Dynamically Flexible", wat betekent dat de stijfheid van het materiaal in de schoen verandert als de voet beweegt. Met DFX "kunt u [een schoen] hebben die onder bepaalde hoeken superflexibel zal zijn, en vervolgens progressief of exponentieel stijver wordt bij hogere hoeken", zegt Khan. "Bij schoeisel hangt dit rechtstreeks samen met prestaties." Volgens de patentaanvraag voor 2020 bestaat DFX uit ten minste drie lagen die zijn geassembleerd en uitgehard tot één laminaat:een met bindmiddel versterkte, flexibele geweven stoflaag; een stijvere laag geweven stof; en ten minste één polymeerlaag.
Khan merkt op dat een hardloopschoen of schoenplaat zacht en flexibel kan zijn wanneer een atleet op een baan of een veld loopt, en als de hardloper dan eenmaal opstijgt en de voet in hogere hoeken begint te buigen, zal de schoen stijver worden om te ondersteunen de beweging . "Bedrijven hoeven niet langer compromissen te sluiten en een specifieke middenvoetstijfheid te kiezen - we kunnen de verschillende functies van een bepaalde activiteit identificeren en de stijfheid eromheen ontwikkelen."
"Een andere manier om ernaar te kijken is dat DFX de prestaties van de voet verbetert, zich gedragen als spieren of ligamenten die flexibel of stijf worden, afhankelijk van de manier waarop ze worden uitgerekt. Het AFX-materiaal werkt meer als een gewricht zoals je elleboog of je enkel - het is ontworpen om heel goed in één richting te buigen, "voegt hij eraan toe.
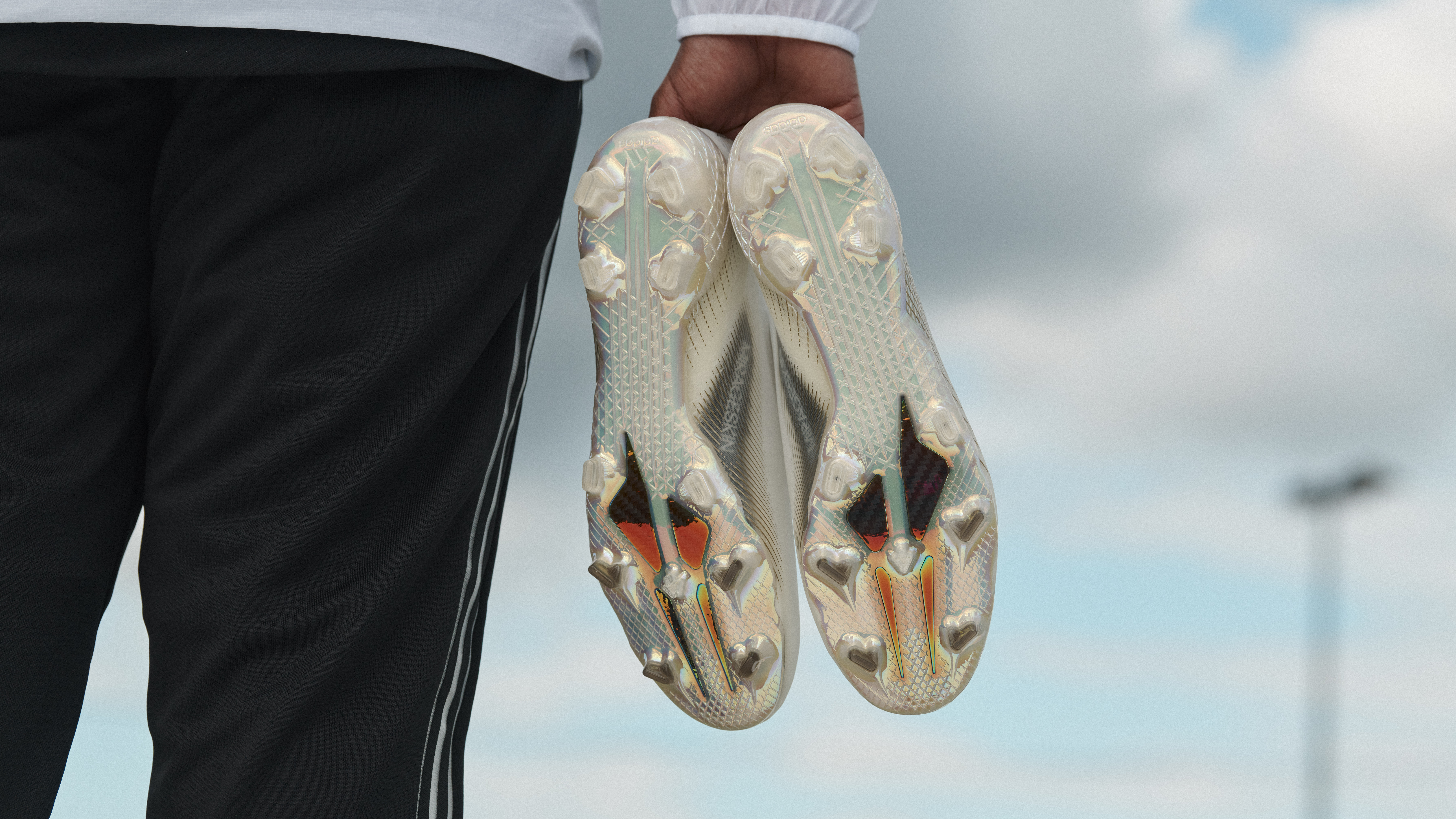
Elke materiaaliteratie tot nu toe is speciaal ontworpen voor een bepaald prestatiebereik en niveau van productie-integratie waarvan is vastgesteld dat het van toepassing is op de industrie, met ruimte voor maatwerk daarbinnen, zoals specifieke stijfheids- of duurzaamheidsvereisten. Het bedrijf biedt ook aangepaste monsters aan potentiële klanten. "We verzamelen voortdurend gegevens over onze composieten en hoe ze werken en waarom, en hebben onze eigen modelleringssystemen gebouwd om verschillende versies vrij snel om te draaien als dat nodig is. Meestal kunnen we binnen een dag of twee na ontvangst van een aanvraag een op maat gemaakt monster laten maken en de deur uit gaan”, voegt Khan toe.
Buiten schoenen
"Op dit moment is ons doel om door te gaan met het uitbreiden van schoenen en die kans te grijpen", zegt Khan. Het is echter een langetermijndoelstelling dat het bedrijf doorgroeit naar andere industrieën, zoals lucht- en ruimtevaart en medische toepassingen.
“Een sector die echt top of mind voor ons is, zowel als een markt waar onze producten een echt voordeel zouden hebben en ook als een sector die enige overeenkomsten heeft met schoenen, is de orthopedische en prothetische wereld, en misschien zelfs de robotische kant, " hij zegt. Dynamische flexibiliteit in prothetische ledematen, voegt hij eraan toe, wordt momenteel bereikt door zware en dure elektronische systemen en hydraulische actuatoren. Khan voorziet het gebruik van Carbitex-producten in toepassingen zoals knie- of rugbraces, waarbij het materiaal kan worden ontworpen om bepaalde bewegingen of hyperextensies te voorkomen, terwijl andere bewegingen mogelijk zijn. Hij voegt eraan toe:"Met een brace immobiliseer je meestal een deel van iemands lichaam vanwege slechts één beweging die er heel slecht voor zou zijn. De sleutel zou zijn om een beugel te maken die die ene bewegingsrichting beperkt, maar de persoon in staat stelt om vervolgens in andere richtingen te bewegen.” In lijn met dit doel is Carbitex onlangs begonnen met de ontwikkeling van een applicatie met een bedrijf dat beugels maakt voor kinderen. De materialen van het bedrijf zijn ook gebruikt, zegt Carbitex, om een koolstofvezelpad te ontwikkelen voor een compressiemouw die is ontworpen voor wandelaars, en een nekbrace die wordt aangesloten op de helm en schoudervullingen van een voetballer om te voorkomen dat de nek tijdens het spelen naar achteren klapt.
Bij het nastreven van andere toepassingen hoopt Carbitex zijn producten te gebruiken om materiële compromissen in andere industrieën te elimineren, zoals het voortdurend streeft naar schoeisel. Khan voegt toe:"Het klinkt cooler om te zeggen dat je streeft naar producten die je sneller, beter en sterker maken, en dat doen we - maar uiteindelijk streven we altijd naar efficiëntie."
Hars
- Koolstofvezel
- 3 voordelen van een horloge van koolstofvezel
- Koolstofvezelmateriaal in de lucht- en ruimtevaartindustrie:wat u moet weten
- Wat is unidirectionele koolstofvezel?
- De rol van composietmateriaal in de auto-industrie
- Waarom koolstofvezel een geweldig fabricagemateriaal is voor sieraden
- Wat is koolstofvezel?
- De opkomst van koolstofvezelversterkte kunststoffen
- Koolstofvezelversterkte kunststof (CFRP)
- Voordelen van koolstofvezelschoenen
- Recycling van composieten - geen excuses meer