Thermoplastische tapes versterkt met op textiel gebaseerde PAN-koolstofvezel
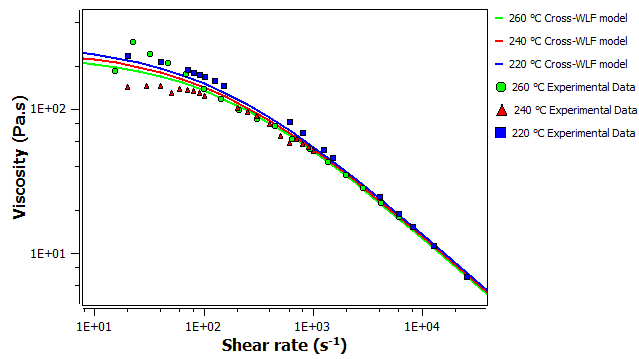
Een langdurige uitdaging in de geavanceerde composietenindustrie is om manieren te vinden om goedkopere koolstofvezel te produceren, zodat alle industrieën die deze waardevolle en effectieve composietversterking willen gebruiken, dit kunnen. De kosten van koolstofvezel zijn aanzienlijk gedaald dankzij tientallen jaren werk om de productiviteit te verbeteren via precursorchemie, machine-innovatie, procesverbeteringen en meer.
Een gebied dat veelbelovend is gebleken, is het gebruik van alternatieve voorlopers van conventioneel polyacrylonitril (PAN) van ruimtevaartkwaliteit. Het Amerikaanse ministerie van Energie (DOE, Washington, DC, VS) en Oak Ridge National Laboratory (ORNL, Oak Ridge, Tenn., VS) hebben bijvoorbeeld methoden ontwikkeld voor het produceren van koolstofvezel uit alternatieve voorlopers, variërend van polymeren tot lignine , naar steenkool.
Alternatieve voorlopers
Een van de meest veelbelovende van deze voorlopers, en degene die het dichtst bij commercialisering staat, is op textiel gebaseerde PAN, die vergelijkbaar is met de vezel die wordt gebruikt om acryltruien te produceren. Net als andere alternatieve voorlopers die ORNL heeft onderzocht, verschilt op textiel gebaseerde PAN-koolstofvezel (TCF) op verschillende manieren van speciale PAN-koolstofvezel voor de ruimtevaart.
Een van de verschillen is dat op textiel gebaseerde PAN-precursor, omdat het bedoeld is voor gebruik in de textielindustrie (denk aan gordijnen, kleding, meubelstoffen), wordt geleverd in een breed sleepformaat dat inherent goedkoper is dan gespecialiseerde luchtvaartkwaliteit PAN-voorloper. Tijdens de productie van koolstofvezel heeft dit tot gevolg dat de doorvoer wordt verhoogd en de conversiekosten worden verlaagd in vergelijking met conventionele PAN-vezel. Het heeft ook de neiging om veel grotere sleepvezel te produceren - in de orde van 300K tot 450K op de lijn bij ORNL's Carbon Fibre Technology Facility versus 3K tot 50K typisch voor conventionele PAN-koolstofvezel. Bovendien, hoewel het langer duurt om de TCF-precursor te verwerken, omdat het geen reactieversnellers bevat zoals conventionele PAN en typisch wordt gebruikt bij lagere temperaturen (een functie van de noodzaak om de verblijftijd en temperatuur in evenwicht te brengen), is het feit dat zoveel meer vezels op een bepaald moment kunnen worden verwerkt en dat het energieverbruik op basis van gewicht of volume lager is, helpt de kosten te verlagen. ORNL schat zelfs dat ~60% totale energiebesparing voor glasvezelconversie en ~50% kostenbesparingen mogelijk zijn.
Dit biedt op zijn beurt de mogelijkheid om minder kostbare vezels in ongebruikelijk grote hoeveelheden te produceren en deze te gebruiken om producten te maken met een kleinere ecologische voetafdruk. In industrieën zoals auto-/grondtransport, consumentenelektronica, sportartikelen, bouw/constructie en windenergie, is TCF een aantrekkelijke versterking omdat toepassingen de neiging hebben om door stijfheid te worden aangedreven, vergeleken met krachtgestuurde toepassingen in de lucht- en ruimtevaart. Met name niet-luchtvaartindustrieën kunnen mogelijk veel vezels verbruiken.
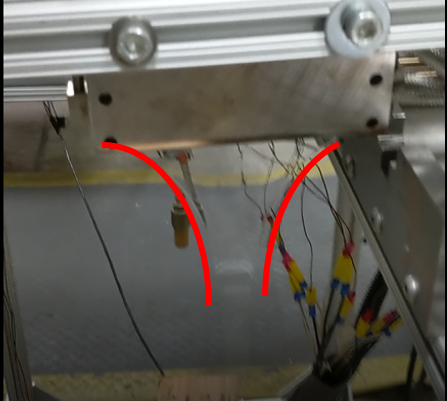
TCF is echter nog steeds een ander product dan conventionele PAN-koolstofvezel, dus er is niet alleen werk nodig om deze vezel beter te karakteriseren, maar ook om manieren te vinden om deze om te zetten en te gebruiken. Omdat het kan worden verwerkt in een ultrabrede trekband, vereist deze voorloper aanpassingen van de procesapparatuur tot het hele vezelproductieproces. Het verandert ook de oppervlaktemodificatie en verpakking na de productie, en het zal natuurlijk de conversieprocessen beïnvloeden, variërend van het maken van tapes en stoffen tot prepregs en preforms.
Het Institute for Advanced Composites Manufacturing Innovation (IACMI, Knoxville , Tenn., VS) heeft de afgelopen drie jaar aan een aantal door leden ondersteunde onderzoeksprojecten gewerkt om deze problemen aan te pakken. Een interessant project heeft gekeken naar manieren om de ultrabrede trekband TCF om te zetten in thermoplastische composiettapes.
Kosten verlagen
De belangstelling voor thermoplastische composiettapes is in veel industrieën toegenomen, maar deze producten zijn vaak duur, aangezien gespecialiseerde apparatuur en knowhow vereist zijn om elke vezel met succes te impregneren met geprepolymeriseerde, hoogmoleculaire en hoogviskeuze thermoplastische harsen in vergelijking met hun niet-gereageerde, laagviskeuze thermohardende tegenhangers. Het is maar al te gemakkelijk om tapes te produceren met veel holtes en een slechte vezeluitvloeiing, eindigend met definitieve onderdelen die er niet alleen slecht uitzien, maar ook het risico lopen op voortijdig falen.
Dr. Uday Vaidya, professor en voorzitter van de gouverneur voor Advanced Composites Manufacturing, University of Tennessee-Knoxville (UTK, Knoxville, Tenn., VS) en IACMI chief technology officer (CTO), werkt sinds het begin van de jaren 2000 samen met George aan programma's voor thermoplastische composieten Husman, president van Husman Consulting Inc. (Cape Coral, Florida, VS) en gepensioneerd bestuurder en CTO van Zoltek Co. Inc. (St. Louis, Mo., VS). Hun vele interacties leidden tot het idee van inline impregnatie van conventionele zware koolstofvezels (24K tot 50K) om thermoplastische composiettapes te produceren aan de achterkant van de vezelproductielijn. Het produceren van tapes direct na de vezelproductie zou een afzonderlijke tussenliggende processtap en alle bijbehorende transport- en verwerkingskosten elimineren. Gehoopt wordt dat dit zou helpen de kosten te verlagen van zowel banden als onderdelen die van deze banden zijn gemaakt.
Het bereiken van dit concept vereiste ontwikkeling in zowel het proces als de apparatuur om met koolstofvezel versterkte thermoplastische tapes in verschillende sleepgroottes te maken. Vaidya en Husman hebben in 2018 een voorlopig patent ingediend in samenwerking met de University of Tennessee Research Foundation (UTRF, Knoxville, Tenn., V.S.) voor een proces voor inline productie van thermoplastische tapes versterkt met tot 50K koolstofvezel. Het jaar daarop breidden Vaidya en zijn UTK-team dit werk uit met thermoplastische impregnering van ultrabreedband TCF (300K tot 450K sleep) met een tweede aanvraag.
TCF TP-tapes
Zoals te verwachten was, was er onderweg geen gebrek aan technische uitdagingen. De vezeltoevoer en -behandeling vereisten een aanzienlijke aanpassing van de apparatuur, aangezien TCF doorgaans breder is en meer filamenten bevat dan conventionele koolstofvezel. Het is ook gevoelig voor kettinggedrag tijdens de vezelimpregnatiestap van de tapeproductie. Dat betekent dat er een sinusoïdale golf ontstaat wanneer de kabels in de impregnatiematrijs worden gevoerd, waardoor de kabels ongelijkmatig splijten en de mal onder verschillende spanningen binnenkomen, wat leidt tot banden die verdraaien, vervormen en een slechte vezelbevochtiging bereiken.
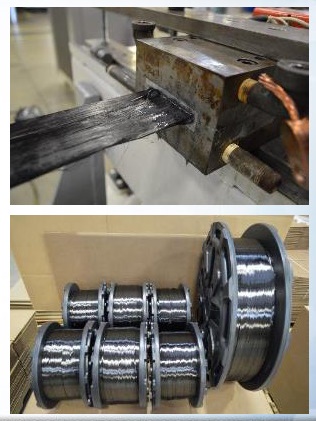
"Het vinden van een manier om een evenwicht te bewaren tussen vezelspanning en flexibiliteit bleek een hele uitdaging en vergde veel werk", legt Vaidya uit. "Ons team begon te begrijpen hoe belangrijk het was om de integriteit van het sleeptouw te behouden om de filamenten te verspreiden en een hoge mate van natheid te bereiken, wat natuurlijk van cruciaal belang is voor het produceren van kwaliteitstapes."
Dan was er nog het probleem met de maatvoering. TCF-trekbanden zijn zwaar bemeten om ervoor te zorgen dat de vezels soepel van de korf naar de impregneermatrijs kunnen gaan, waar ze worden bevochtigd met hars om tape te produceren. Eenmaal bij de matrijs had eerder onderzoek echter aangetoond dat om een goede bevochtiging te bereiken met thermoplasten met een hogere viscositeit, de aanwezigheid van lijm de impregnering in feite belemmerde, waardoor het zeer wenselijk werd om de lijmlaag te verwijderen. Met vallen en opstaan heeft het team uiteindelijk een techniek ontwikkeld om de maatvoering af te branden net voordat de kabels de impregneermatrijs binnendringen.
Om de harsreologie en polymeertoevoer door de impregnatiematrijs nauwkeurig te voorspellen en goede tape te maken, was nieuw simulatie- en validatiewerk nodig. Het team richtte zich op de productie van TCF-tapes met polypropyleen (PP) en polyamide 6 (PA6) - twee thermoplasten die veel worden gebruikt in de auto-industrie vanwege hun taaiheid en betaalbaarheid. Het team gebruikte PolyXtrue-ontwerpsoftware voor extrusiematrijs van Plastic Flow LLC (Hancock, Mich., VS), die is gebaseerd op het Williams-Landel-Ferry (WLF)-model en een uitstekende correlatie bood met gemeten reologie en afschuifsnelheidsresultaten.
Het ontwerp van de matrijs zelf was een ander belangrijk onderzoeksgebied, vooral toen het team overstapte van standaard 12K naar 50K-kabels en vervolgens naar ultrabreedband TCF-kabels. In dat stadium moest de matrijs volledig opnieuw worden ontworpen en een proces in twee fasen worden aangepast. Tijdens de eerste fase wordt de vezel geïmpregneerd; tijdens de tweede fase worden geoptimaliseerde breekhoeken ingesteld voor de span-/impregnatiepennen - die de spanning regelen waarbij de koolstofvezel wordt getrokken, de vezelgewichtsfractie (FWF), evenals kwaliteitscontrole - om de gewenste eigenschappen te bereiken in de voltooide banden. Momenteel heeft het team 30-50% FWF-tapes geproduceerd in zowel PP als PA6, zelfs met de zwaardere slepen.
Om tapes na het verlaten van de matrijs snel af te koelen, werd een luchtkoelsysteem voor na de impregnering ontwikkeld. Het team moest zelfs een methode uitwerken om voltooide banden op korven/spoelen op te nemen, vanwege de breedte van de producten en de uitdagingen van het stroomafwaartse gebruik van die banden.
Vaidya zegt dat het team zich momenteel richt op elektronische integratie, waaronder het bouwen van een formele grafische gebruikersinterface en het ontwikkelen van een op programmeerbare logische controller (PLC) gebaseerd systeem. Het doel van het team is uiteindelijk om een productiemodule voor thermoplastische tape te ontwikkelen die kan worden toegevoegd aan de achterkant van een TCF- of conventionele koolstofvezelproductielijn om de productie van secundaire/tussenliggende thermoplastische tapes te vergemakkelijken.
"Ons team heeft veel technische uitdagingen gehad, maar we hebben ook een aantal prestaties geleverd", legt Vaidya uit. "Het was moeilijk om zo'n brede sleepband te hanteren en met succes - en snel - de vezels te impregneren om hoogwaardige thermoplastische tapes zonder holtes te krijgen. Ons team heeft echter een aantal procesparameters onderzocht, waaronder meerdere iteraties van het matrijsontwerp; polymeerstroomsimulaties door de matrijs; en diverse aspecten van vezelaanvoer, spannen en voorverwarmen. We hebben niet alleen een aantal van de claims in ons patent bewezen, maar we hebben ook snelheden van impregnatielijnen bereikt van 3,7 meter/minuut [12 voet/minuut] terwijl we 30% FWF-polypropyleen- en PA6-tapes produceerden.”
Volgende stappen
Vaidya zegt dat de bescherming van intellectueel eigendom rond deze tapetechnologie is ingediend bij de UT Research Foundation - een met traditionele 24K- en 50K-vezels en een met de wide-tow-vezels. Commercialisering, zegt hij, zal zich richten op inline impregnatie binnen een koolstofvezellijn. "Dit zal de nabewerking aanzienlijk verminderen en gemakkelijk aanpassen, waardoor de totale kosten van het tussenproduct verder omlaag gaan", zegt hij.
Hoe kunnen deze tapes worden aangebracht? Vaidya zegt dat er veel opties zijn:"Het materiaal kan bijvoorbeeld in langvezelige vorm worden gehakt, gebruikt in pultrusiegrondstoffen, filamentwikkeling in grote tanks, overmolding (vergelijkbaar met organoblad) bij persvormen, plaatmateriaal in hybride processen - bijv. , met LFT [thermoplast met lange vezels], SMC [velvormmassa] en andere synergetische materialen.” Dit opent een reeks producttypes die baat zouden hebben bij stijfheidsverbeteringen, hoge slagvastheid en verbeterde verwerkbaarheid, zoals vormen, trekken en buigen, recycling en omkeerbare chemie.
Toepassingen, zegt hij, zijn onder andere automotive, vrachtwagens, windbladen, infrastructuur (bruggen), constructie, sportartikelen, maritieme en offshore producten. "Het thermoplastische tussenproduct van koolstofvezel met brede sleep kan nu mogelijkheden bieden om koolstofvezel te overwegen waar het eerder te duur was", concludeert Vaidya.
Hars
- Koolstofvezel
- Wat is koolstofvezel?
- Vezelversterkte kunststof (FRP) in actie!
- De opkomst van koolstofvezelversterkte kunststoffen
- Koolstofvezelversterkte kunststof (CFRP)
- PPS-gebaseerde thermoplastische unidirectionele tape van koolstofvezel
- Consortium streeft naar oplossingen voor thermoplastische composietstructuren van koolstofvezel
- 3D-print composieten met continue vezels
- Sterkere IM-onderdelen maken met vezelversterkte en gevulde materialen
- SIGRASIC® met koolstofvezel versterkt siliciumcarbidevilt
- SIGRASIC® Koolstofvezelversterkte siliciumcarbide korte vezels