Vervaardiging van polydimethylsiloxaan nanofluïdische chips onder AFM-tipgebaseerd nanofreesproces
Abstract
In het huidige onderzoeksgebied worden op polydimethylsiloxaan (PDMS) gebaseerde nanofluïdische apparaten veel gebruikt in medische, chemische en biologische toepassingen. In het huidige artikel werd een nieuwe nanofreestechniek (bestaande uit een AFM-systeem en een piëzo-elektrische actuator) voorgesteld om nanokanalen (met regelbare afmetingen) op PDMS-chips te fabriceren, en de nanokanaalgrootte werd geregeld door de stuurspanning en frequentie die werden ingevoerd in de piëzo-elektrische actuator . Bovendien werden microkanaal- en nanokanaalmallen respectievelijk vervaardigd door UV-lithografie en AFM-tipgebaseerde nanofrezen, en ten slotte werden PDMS-platen met micro / nanokanalen verkregen door middel van een overdrachtsproces. De invloeden van de PDMS-gewichtsverhouding op de grootte van nanokanalen werden ook onderzocht. Het bindingsproces van microkanaal- en nanokanaalplaten werd uitgevoerd op een zelfgemaakt uitlijnsysteem dat bestond uit een optische monoculaire microscoop en precisiestadia. Verder werden de effecten van nanokanaalgrootte op elektrische eigenschappen van KCl-oplossing (concentratie van 1 mM) geanalyseerd. Daarom kan worden geconcludeerd dat PDMS-nanofluïdische apparaten met meerdere nanokanalen met een diepte van minder dan 100 nm efficiënt en economisch kunnen worden vervaardigd met de voorgestelde methode.
Achtergrond
Vanwege hun aanzienlijke potentieel op chemisch, medisch en biologisch gebied, worden micro/nanofluidische systemen veel gebruikt in DNA-analyse [1,2,3,4], celscheiding [5], eiwitonderzoek [6,7,8], voedselveiligheid [9], en milieumonitoring [10]. Met de snelle ontwikkeling van nanofabricagetechnologie neemt de vraag naar nanofluïdische apparaten met een eendimensionale grootte kleiner dan 100 nm voortdurend toe [11]. Nanofluïdische chips kunnen ook effectief worden gebruikt voor virusdetectie [12], manipulatie van nanodeeltjes [13] en de studie van ionendiffusie [14]. De detectie-efficiëntie en gevoeligheid van de nanofluïdische chips zijn echter afhankelijk van de dimensies en distributie van de nanokanalen. Het is onmisbaar om de functiedimensies van de nanokanalen nauwkeurig te regelen voor op nanofluïdische gebaseerde labelvrije detectie. Hoe nanokanalen te fabriceren met controleerbare kenmerkdimensies en distributie is nog steeds een uitdaging voor de toepassing in het nanofluïdische veld.
Tot nu toe zijn er verschillende methoden die kunnen worden gebruikt voor de fabricage van nanofluïdische chips. Reactieve ionenetsen [15], conventionele fotolithografie [16], high-energy beam processing [17], interferentielithografie [18], nano-imprinting [19] en hot embossing-technologieën [20, 21] worden het meest gebruikt voor de fabricage van nanofluïdische apparaten; al deze methoden vertonen echter hun eigen beperkingen. Reactief ionen-etsen en conventionele fotolithografie zijn de belangrijkste methoden voor de fabricage van micro/nanofluidische kanalen. De laterale afmetingen van de gefabriceerde kanalen hangen echter af van de golflengte van het invallende licht, dus de breedte van de geproduceerde kanalen wordt vaak gevonden op micrometerschaal, niet op nanoschaal [22]. Bovendien is het onhandig om de fotomaskers te verwisselen wanneer gefabriceerde micro-/nanostructuren verschillende eigenschappen hebben. Gefocuste ionenbundellithografie (FIB) en elektronenbundellithografie (EBL) zijn beide hoogenergetische bundelverwerkingsmethoden, die gemakkelijk een zeer nauwkeurige nanofluïdische chip met sub-100 nm nanokanalen kunnen fabriceren. De investering voor de fabricagefaciliteit is echter extreem hoog en de strenge milieu-eis is noodzakelijk [23]. Interferentielithografie (IL) is geschikt voor het vervaardigen van eenvoudige periodieke structuren over een groot gebied; het is echter niet geschikt om een enkel nanokanaal te bewerken [24, 25]. De verwerkingsresolutie van nano-imprinting hangt af van sjablooneigenschappen, het cruciale probleem voor deze benadering is hoe de sjabloon kan worden gefabriceerd met zeer nauwkeurige nanostructuren [26]. Bovendien worden opofferingsvormen en op kraken gebaseerde methoden ook toegepast om apparaten op micro-/nanoschaal te fabriceren [27, 28]; de nauwkeurige controle van de grootte van nanokanalen is echter erg moeilijk in deze benaderingen. Er is dus een meer haalbare fabricagebenadering nodig met de eigenschappen van hoge bewerkingsprecisie, gebruiksgemak, groot verwerkingsbereik en lage omgevingsvereisten voor de fabricage van nanofluïdische apparaten.
Vanwege hun hoge bewerkingsnauwkeurigheden, worden ultraprecieze bewerkingsmethoden, zoals nanofrezen, precisieslijpen en ultraprecisiedraaien, veel gebruikt in de fabricage van micro-/nanostructuren [29,30,31,32]. Bovendien is sinds de uitvinding van de atomic force microscope (AFM) in 1986, op AFM-tips gebaseerde nanofabricage een krachtige methode om nanostructuren te maken [33]. De traditionele op tip gebaseerde nanoscratching heeft enkele beperkingen, zoals een beperkte bewerkingsbreedte en een lage fabricage-efficiëntie. De breedte van het door deze benadering vervaardigde nanokanaal is afhankelijk van de geometrie van de AFM-tip, wat de nanokanalen met een regelbare breedte aangeeft die ontoegankelijk zijn. Bovendien is de fabricage-efficiëntie van het traditionele op punt gebaseerde nanokrasproces relatief laag, vooral in het geval van het gebruik van een voeding in het bewerkingsproces om de diepte en breedte van de verkregen nanostructuur te vergroten. Vanwege de aanzienlijke voordelen, zoals de regelbare machinale bewerkingsgrootte en de hoge fabricage-efficiëntie, wordt op tip gebaseerde nanofrezen algemeen toegepast om nanokanalen te fabriceren. Gozen et al. [34, 35] vervaardigde nanostructuren op polymethylmethacrylaat (PMMA) door middel van een nanofreesproces. Zhang et al. [36,37,38] bereidde driedimensionale nanostructuren voor met behulp van AFM en bestudeerde de effecten van verschillende bewerkingsparameters. Park et al. [39] onderzocht het mechanisme van het nanobewerkingsproces en ontdekte dat de intensiteiten van de snijkracht aanzienlijk waren verminderd; in het voorgestelde systeem bleken de bewerkingsfaciliteiten echter relatief gecompliceerd te zijn en werd het materiaalverwijderingsproces niet in detail onderzocht. De relatie tussen de bewerkingsparameters, inclusief de aandrijffrequentie en spanning en de kenmerkdimensies van het verkregen nanokanaal, is niet onderzocht. Bovendien was hun werk niet gericht op de toepassing van de gefabriceerde nanokanalen. Daarom is er meer werk nodig om het toepassingsgebied van deze op AFM op tips gebaseerde nanofrezen-aanpak te verkennen. Polycarbonaat (PC) wordt vanwege zijn uitstekende bewerkbaarheid vaak gebruikt voor nanofabricage [40]; niettemin wordt het zelden geselecteerd om nanofluïdische chips te fabriceren. Daarentegen wordt polydimethylsiloxaan (PDMS) veel gebruikt om microfluïdische en nanofluïdische chips te verwerken. Mata et al. [41] bestudeerde de invloeden van PDMS-gewichtsverhouding op trekspanning. Park et al. [42] ontwikkelde een nieuwe methode om de stijfheid van PDMS te verbeteren. De toepassingen van nanofluïdische chips in een labelvrij testveld hangen voornamelijk af van de elektrische geleidbaarheid van nanokanalen [43], dus de meetresultaten worden vaak beïnvloed door de dimensionale afmetingen van nanokanalen [44].
Om de nadelen van het traditionele op punt gebaseerde krasproces te overwinnen, wordt daarom de nanofreesbenadering gebruikt om het fabricageproces van nanokanaal in deze studie uit te voeren. Bovendien werd PC-sheet geselecteerd als het experimentele monster om de slijtage van de tip te verminderen en om de fabricagekosten te verlagen. Verder werd de grootte van het nanokanaal op het pc-blad geregeld door de stuurspanning en frequentie die werden ingevoerd in de piëzo-elektrische actuator. De invloeden van de PDMS-gewichtsverhouding op de grootte van nanokanalen werden ook onderzocht. Om de effecten van verschillende dimensionale afmetingen op de elektrische geleidbaarheid van nanokanalen te verifiëren, werd bovendien de huidige meettest uitgevoerd met KCl-oplossing.
Methoden
Nanomilling systeem instellen
Het voorgestelde op AFM-tip gebaseerde nanofreessysteem bestond uit een commerciële AFM (Dimension Icon, Bruker Company, Duitsland) en een piëzo-elektrische actuator (P-122.01, PI Company, Duitsland) (Fig. 1a). De verplaatsingsbereiken van de piëzo-elektrische actuator in zowel de x- als de y-richting waren beperkt tot 1 m. Bovendien werd de piëzo-elektrische actuator aangedreven door sinusvormige signalen met geschikte spanningen (gegenereerd door een commercieel signaalgeneratorapparaat (AFG1022; Tektronix, Inc., VS)) onder de versterking van een signaalversterker (PZD350A; TREK, Inc., VS). Op de zelfgemaakte houder (gemaakt van epoxyhars) werd een pc-blad bevestigd met een bevestigingsschroef. De nanobewerking werd uitgevoerd met behulp van een rechthoekige piramidale, met diamanten beklede punt met een dikte van 100 nm (DT-NCLR, Nanosensors, Zwitserland). De cantilever van de punt (normale veerconstante van 68 N/m) was gemaakt van silicium (Fig. 1b), en een siliciumpunt (straal van 10 nm) (TESPA, Bruker Company, Duitsland) werd gebruikt om de groeven te meten na bewerking.
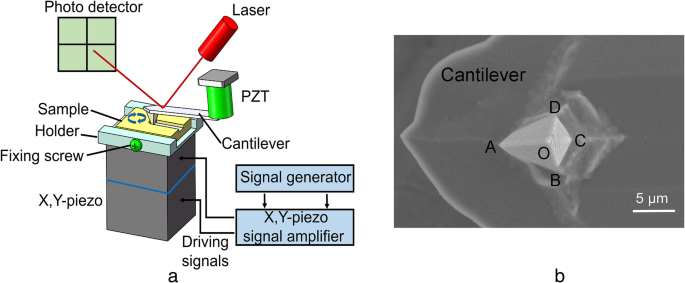
een Schematisch diagram van nanomilling-systeem. b SEM-microfoto van gediamanteerde AFM-tip
Vervaardiging van nanokanaal- en microkanaalmallen
De fabricageroute van nanokanalen op een PDMS-chip wordt weergegeven in Fig. 2. Het AFM-systeem en de piëzo-elektrische actuator werden gebruikt om nanokanaalmallen (met regelbare afmetingen) op pc-blad te fabriceren. Het pc-blad (molecuulgewicht van 35.000) van 15 mm x 12 mm x 1 mm werd gekocht bij Goodfellow. Het gemiddelde en de standaarddeviatie van oppervlakteruwheid (Ra) van het pc-blad werden gemeten als respectievelijk 0,6 nm en 0,2 nm (deze waarden werden verkregen door een gebied van 50 m × 50 m van het monster te scannen in de AFM-tikmodus). Om een cirkelvormige beweging te genereren, werd de piëzo-elektrische actuator aangedreven door sinusvormige signalen met een faseverschil van 90 ° in x- en y-richtingen. De breedte van de bewerkte nanokanalen was afhankelijk van de amplitude van de gegenereerde cirkelvormige beweging. Het bereik van de stuurspanning die naar de piëzo-elektrische actuator werd ingevoerd, was ingesteld van 30 V tot 150 V met een tussenruimte van 30 V, en daarnaast werden twee duikfrequenties van 100 Hz en 1500 Hz geselecteerd. Tijdens machinale bewerking langs de rand naar voren, worden materialen uitgestoten in stapelvorming en blijken ze vaak uniform verdeeld te zijn aan beide zijden van een nanokanaal [45], en het helpt bij het voorkomen van lekkage van nanofluïdische chips tijdens het hechtproces; daarom werd in de huidige studie de bewerkingsrichting naar voren geselecteerd. Nanokanalen met een lengte van 80 m werden gefabriceerd met behulp van de Nanoman-module van het AFM-systeem. Elk bewerkingsproces wordt beïnvloed door de voedingswaarde; daarom, om deze invloed te elimineren, moet de voedingssnelheid worden gevarieerd met de aandrijffrequentie. In de huidige studie was de voedingswaarde ingesteld op 10 nm en werden de voedingssnelheden voor 100 Hz en 1500 Hz frequenties berekend als respectievelijk 1 m/s en 15 m/s. De normale belasting van de tip hing af van de uitgangsspanning die werd gegenereerd door de positiegevoelige fotodetector (PSD); dus werden verschillende normale belastingen die in onze studie werden gebruikt, bereikt door een relatieve spanning (instelpunt) in te stellen. Volgens ons eerdere werk [46] werd de normale belasting voor machinale bewerking berekend door Vgl. (1) en de gevoeligheid werd gemeten vanaf de helling van de verkregen kracht-afstandscurve [47].
$$ {F}_{\mathrm{N}}={V}_{\mathrm{setpoint}}\times sensitivity\times {K}_{\mathrm{N}} $$ (1)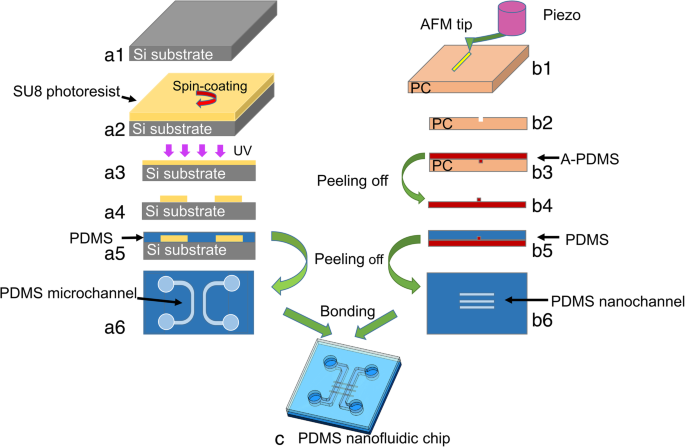
Stroomdiagram van fabricage van nanofluïdische chips:(a1) – (a6) Werkstappen van fabricage van microkanalen op een PDMS-chip; (a1) Siliciumfolie gebruikt voor lithografiesubstraat; (a2) Spin-coating van SU8-fotoresist op Si-substraat; (a3) Blootstelling van de SU8-laag aan UV-licht; (a4) verkregen convexe microstructuren; (a5) PDMS-coating op microkanaalvorm; (a6) Laatste PDMS-chip met microkanalen; (b1)–(b2) Werkstappen van nanokanaalfabricage op een PDMS-chip; (b1) AFM-tip krassen op pc-blad; (b2) Verkregen nanokanaalvorm na krassen; (b3) A-PDMS-coating op nanokanaalvorm; (b4) A-PDMS-chip met convexe nanostructuren; (b5) Normale PDMS-coating op A-PDMS-mal; (b6) Laatste PDMS-chip met nanokanalen; (c) PDMS nanofluïdische chip na binding
Daarom werden de normale belastingen voor het nanofreesproces ingesteld op 17 N en 25 μN. Verder werden ter vergelijking ook nanokanaalmallen op pc-plaat vervaardigd zonder trillingen, deze methode wordt single scratching genoemd. De normale belastingen voor het enkele krasproces waren ingesteld op 25 μN, 33 μN, 42 μN, 50 μN en 58 μN. Het schematische diagram van de doorsnede van de nanokanaalvorm wordt weergegeven in Fig. 2(b2).
Microkanaalmallen werden bereid door middel van een UV-lithografieproces. Het stroomschema in Fig. 2 (a1-a4) toont de bedieningsdetails van het lithografieproces. De fotoresist (SU-82015; MicroChem, VS) werd gespincoat op Si-substraat bij 500 rps gedurende 30 s en bij 4000 rps gedurende 120 s. Een paar "U"-vormige microkanalen vormden de microkanaalchip (Fig. 2 (a6)), die werd overbrugd door nanokanalen om de uiteindelijke nanofluïdische chip te vormen. De breedte van het microkanaal was 30 m en de diameter van het reservoir was 1 mm. Bovendien was de afstand tussen twee "U"-vormige microkanalen 50 m (Aanvullend bestand 1:Figuren S1 en S2).
Overdracht printen van microkanalen en nanokanalen
De convexe microkanaalvorm (Fig. 2 (a4)) en de concave nanokanaalvorm (Fig. 2 (b2)) werden overgebracht door PDMS (Sylgard 184, Dow Corining, VS) om de uiteindelijke nanofluïdische chip te bereiden. Figuur 2 (b3)–(b6) presenteert het technologische proces van nanokanaalvormoverdracht, dat uit twee stappen bestond:eerste overdracht en tweede overdracht. Om de effecten van de gewichtsverhouding van monomeer tot verharder op de nanokanaalgrootte te onderzoeken, werden drie verschillende PDMS-gewichtsverhoudingen (A-PDMS) gebruikt tijdens zowel het eerste als het tweede overdrachtsproces. De PDMS-gewichtsverhoudingen voor het eerste transferdrukproces waren ingesteld op 9:1, 7:1 en 5:1, terwijl de waarden voor de tweede transfer waren ingesteld op 10:1, 9:1 en 8:1. Afbeelding 2(a5) en (a6) tonen het overdrachtsproces van microkanaalmallen met behulp van een eenstaps overdrachtsbenadering. De PDMS-gewichtsverhouding van 10:1 werd gebruikt voor de overdracht van convexe microkanalen. Tijdens alle transferprintprocessen werd het tweecomponenten PDMS-elastomeer eerst gelijkmatig geroerd en vervolgens in een behuizing gegoten om de mal voor te bereiden. De behuizing werd vervolgens gedurende 30 min in een vacuümexsiccator bewaard en 2-3 keer ontgast om alle ingesloten luchtbellen te verwijderen. De voorbereide mal werd gedurende 4 uur in een verwarmingsoven op 80 ° C gehouden en ten slotte werd de PDMS-replica voorzichtig van de mal afgepeld.
Chipbinding
De bereide nanofluïdische chips werden gebonden door zuurstof-plasmabehandeling (Zepto, Diener electronic, Duitsland) gedurende 32 s onder een kamerdruk van 1, 5 mbar en een kamervermogen van 81 W (Fig. 2 (c)). De oppervlakken van microkanalen en nanokanalen werden schoongemaakt met scotch-tapes en de vier reservoirs op PDMS-microkanaalchips werden geponst voordat ze werden gehecht. Gedeïoniseerd water werd gebruikt om de chips schoon te houden na plasmabehandeling, en de chips werden op één lijn gehouden met behulp van een zelfgemaakt uitlijnsysteem dat bestond uit een houder, een monoculaire microscoop en een eendimensionale precisietafel (TSDT-401S; SIGMAKOKI, Japan ) (Fig. 3a). De details van het zelfgemaakte uitlijnsysteem zijn te vinden in de ESI. De chips werden vervolgens gedurende 20 min bij een temperatuur van 95 °C aan elkaar gehecht om een ingesloten micro/nanokanaalchip te verkrijgen (Fig. 3b).
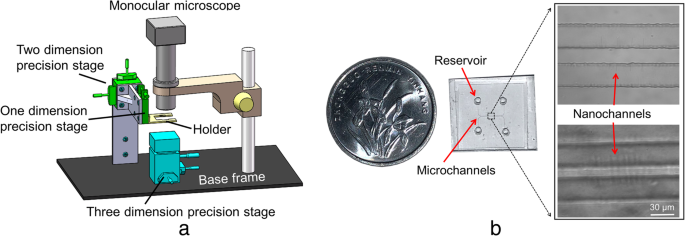
een Schematisch diagram van zelfgemaakt uitlijnsysteem en b nanofluïdische chip
Resultaten en discussie
Roterend traject van piëzo-elektrische actuator
De tweedimensionale piëzo-elektrische actuator is een cruciaal onderdeel om roterende beweging uit te voeren in een op AFM-tip gebaseerd nanofreessysteem. Om zijn bewegingen onder een reeks stuurspanningen en frequenties te karakteriseren, werden daarom voorlopige krastests uitgevoerd. Onder het contactmodel met een scanbereik van 0 nm, naderde de AFM-tip eerst het oppervlak van de pc-plaat onder een bepaalde normale belasting en werd hij statisch gehouden. De rotatie van de tweedimensionale piëzo-elektrische actuator werd geregeld door een vooraf ingestelde frequentie en spanning. Na het voltooien van het krasproces werd de AFM-tip van het oppervlak van het pc-blad opgetild. Zo werd de bewegingsamplitude van de piëzo-elektrische actuator verkregen als een functie van de stuurspanning en -frequentie. De stuurspanningen werden ingesteld in het bereik van 30-150 V met een tussenruimte van 30 V, terwijl de stuurfrequenties waren ingesteld op 100 Hz en 1500 Hz. De relatie tussen gemeten amplitudes en stuurspanningen bij twee stuurfrequenties wordt weergegeven in Aanvullend bestand 1:Afbeelding S3. Het is duidelijk dat de waarden van de bewerkingsamplitude toenam met de toenemende stuurspanningen, en de waarde van de bewerkingsamplitude bij 1500 Hz was groter dan die van 100 Hz. Het bleek dat de breedtes van het nanokanaal vervaardigd door onze voorgestelde methode varieerden van 350 nm tot 690 nm.
Vervaardiging van nanokanaalmallen op pc-plaat
De relaties tussen nanokanaalgrootte en bewerkingsparameters onder enkel krassen en nanofrezen worden respectievelijk weergegeven in Fig. 4a en b. De breedtes en diepten van de bewerkte nanokanalen worden weergegeven door W 0 en D 0 , respectievelijk (Fig. 5a).
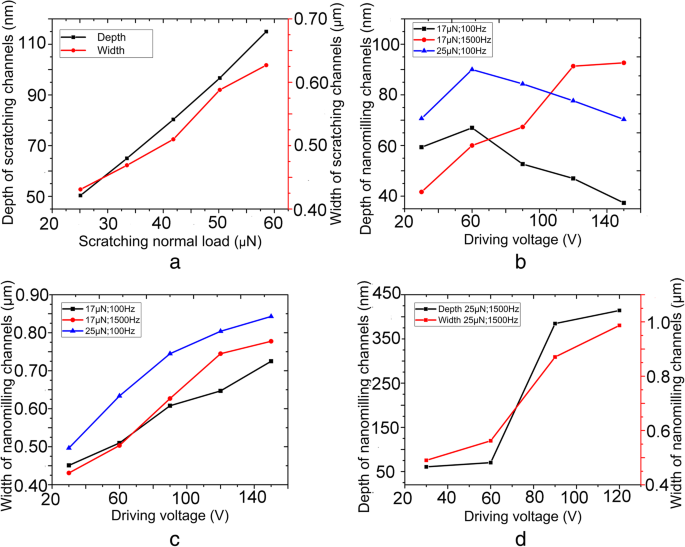
Relatie tussen machinaal bewerkte nanokanaalgrootte en bewerkingsparameters:a enkele krassen met normale belastingen variëren van 25 μN tot 58 μN, b diepte, en c breedte van de bewerkte kanalen bij fabricage met normale belastingen van 17 μN, 25 μN en aandrijffrequenties van 100 Hz, 150 Hz, d de diepte en breedte van de bewerkte kanalen wanneer vervaardigd met een normale belasting van 25 μN en een aandrijffrequentie van 1500 Hz
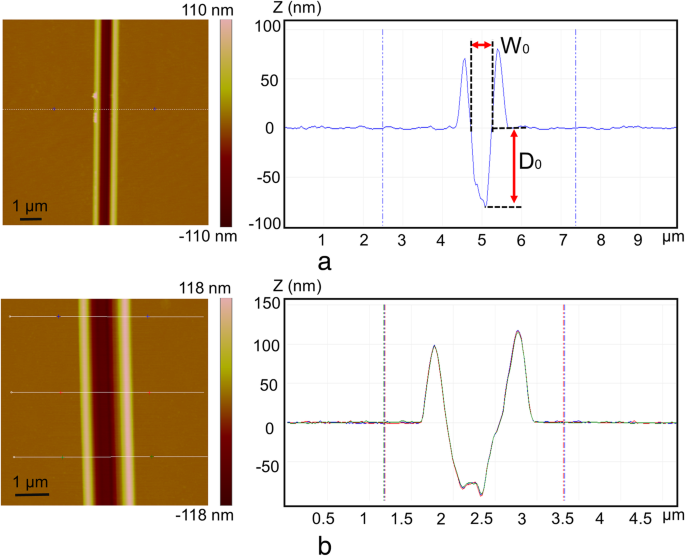
Typische AFM-beelden van het bewerkte nanokanaal met verschillende bewerkingsparameters:a Krabben onder een normale belasting van 42 μN. b Nanofrezen onder een normale belasting van 25 N, een frequentie van 100 Hz en een stuurspanning van 60 V
Uit figuur 4a is te zien dat de breedtes en diepten van de gefabriceerde nanokanalen toenam met de toenemende normale belastingen. Het typische AFM-beeld van krassen onder een normale belasting van 42 N wordt getoond in figuur 5a. Het valt op dat materialen uit het nanokanaal werden verdreven om opeenhopingen te vormen, die gelijkmatig aan beide zijden van het nanokanaal waren verdeeld. Omdat de vorm van de AFM-tip symmetrisch is met het oppervlak dat werd gevormd door de rand "OA" tijdens het bewerkingsproces (Fig. 1b). Zo werden materialen gelijkmatig uitgedreven door de voorrand van de punt tijdens edge-forward scratchen. Figuur 4b, c en d illustreren de relatie tussen machinaal bewerkte nanokanaalgrootte en stuurspanning. Uit figuur 4b blijkt duidelijk dat de diepte van het nanokanaal in het begin toenam en vervolgens begon af te nemen onder een frequentie van 100 Hz met normale belastingen van 17 N en 25 μN. De pc-plaat die in onze studie werd gebruikt, was een amorf polymeer, dat een elastisch-viscoplastisch gedrag vertoont in combinatie van een exponentiële rekverharding bij hoge spanningsniveaus [48, 49]. De normale belasting tijdens het machinaal bewerken werd berekend door Vgl. (2), waarbij \( \overrightarrow{n} \) en \( \overrightarrow{t} \) respectievelijk de eenheidsnormaal en de eenheidsraaklijn aan de stroomlijnvector zijn, p en τ betekent respectievelijk lokale normale druk en schuifspanning, en \( \overrightarrow{z} \) is de eenheid verticaal [50].
$$ {F}_{\mathrm{N}}=p\cdot \int \overrightarrow{n}\cdot \overrightarrow{z} ds-\tau \cdot \int \overrightarrow{t}\cdot \overrightarrow{zds } $$ (2)In de huidige studie werden de dimensionale afmetingen van de gefabriceerde nanokanalen gevonden op nanoschaal, dus de waarden van lokale normale druk en schuifspanning werden constant verondersteld. Verder, vgl. (2) werd omgezet in de vereenvoudigde vorm van Vgl. (3), waar S n en S h respectievelijk zijn de horizontale en de verticale projecties van de interface tussen AFM-tip en monster.
$$ {F}_{\mathrm{N}}=p\cdot {S}_n-\tau \cdot {S}_h $$ (3)De relatie tussen S n en S h wordt uitgedrukt in Vgl. (4), waarbij α en β respectievelijk zijn de ingesloten hoeken tussen het oppervlak van de punt en de verticale en horizontale vlakken.
$$ {S}_{\mathrm{n}}=\frac{S_{\mathrm{h}}}{\cos \alpha}\cdot \cos \beta $$ (4)De normale belasting werd berekend door Vgl. (5).
$$ {F}_{\mathrm{N}}=\left(p\cdot \frac{\cos \beta }{\cos \alpha }-\tau \right)\cdot {S}_h $$ (5 )Het blijkt uit vgl. (1) dat de waarden van de normale belasting constant waren gedurende het gehele bewerkingsproces. Volgens Briscoe et al. [51], de waarde van de gemiddelde reksnelheid werd berekend door Vgl. (6), waarbij V en w geven respectievelijk tipsnelheid en ongesneden spaandikte aan. De maximale waarde van ongesneden spaandikte werd gevonden als ~ 10 nm.
$$ {}_{\varepsilon}^{\bullet }=\frac{\mathrm{d}\varepsilon }{\mathrm{d}t}\circa \frac{V}{w} $$ (6)Bovendien werden de waarden van de tipsnelheid verkregen uit Vgl. (7), waarbij f is de frequentie van het ingangssignaal.
$$ V=\pi \cdot {W}_o\cdot f $$ (7)De waarden van de gemiddelde reksnelheid bij 100 Hz werden gevonden in het bereik van 1,42 × 10 4 s -1 ~ 2,27 × 10 4 s -1 . De waarden van de lokale normale druk (p ) begon te stijgen met de toename van de reksnelheden toen de reksnelheden varieerden van 1,42 × 10 4 s -1 tot 2,27 × 10 4 s -1 [52]. De waarde van τ was veel kleiner dan die van p , betekent dit dat de normale belasting voornamelijk afhing van p . Om de waarden van normale belasting (FN ) constant is tijdens het gehele bewerkingsproces, moeten de waarden van de bewerkingsdiepte kleiner zijn bij hogere stuurspanningen. De uiteindelijke afmeting van het gefabriceerde nanokanaal werd echter beïnvloed door het herstel van het monstermateriaal. Het herstel van het monster nam af met de toenemende bewerkingssnelheden in het bereik van 142 ~ 227 m / s [53]:het geeft dus aan dat een hoger elastisch herstel plaatsvond bij 30 V. Bijgevolg is de diepte van het gefabriceerde nanokanaal bij 30 V (~ 142 m/s) was ondieper dan die van 60 V (~ 161 m/s). Aanvullend bestand 1:figuur S4(a) en figuur 5b zijn de typische AFM-afbeeldingen van het nanokanaal dat is bewerkt bij 100 Hz onder normale belastingen van respectievelijk 17 N en 25 μN. Het is duidelijk dat de stapeling aan de rechterkant van het nanokanaal groter is dan aan de linkerkant. De roterende beweging van het monster tijdens het nanofreesproces is tegen de klok in en de snijhoek van de hoofdsnijkant verandert met de rotatie. De ongesneden chipdikte is te klein om chips te vormen aan het begin en einde van een cyclus van nanofreesprocessen. De ongesneden chipdikte in het midden van een cyclus van nanofreesprocessen is relatief groot; de kleine aanvalshoek draagt echter bij aan de vorming van de pile-ups. Zo worden meer materialen naar de rechterkant van het kanaal geduwd en zijn de ophopingen dus asymmetrisch. De details voor de vorming van asymmetrische stapelingen zijn te vinden in onze eerdere studie [54].
Uit Fig. 4b en d is te zien dat de diepte van het nanokanaal begon toe te nemen met de toenemende stuurspanningen bij 1500 Hz onder normale belastingen van 17 N en 25 N. Figuur 4d laat zien dat de diepte van het nanokanaal sterk toenam van 60 V (~-2,64 mm/s) tot 90 V (~-4,10 mm/s) onder een normale belasting van 25 μN. Volgens Geng et al. [55], wordt de materiaalverwijderingsstatus aanzienlijk beïnvloed door de snijsnelheid. Materialen werden tijdens het machinaal bewerken met een snelheid van 2,64 mm/s uit het nanokanaal verdreven in stapelvorm, terwijl de toestand van de materiaalverwijdering met 4,10 mm/s werd veranderd van opstapelen naar chip (aanvullend bestand 1:figuur S4(b)) . Daarom kan de toename van de bewerkingsdiepte bij 90 V (~ 4,10 mm/s) worden toegeschreven aan de verandering in de staat van materiaalverwijdering. De breedte van het gefabriceerde nanokanaal begon toe te nemen met de toenemende stuurspanningen. Figuur 6 geeft het schematische diagram weer van het AFM-tiptraject tijdens nanofrezen, de gestippelde ellipsen, de zwarte effen ellipsen en de blauwe pijlen vertegenwoordigen respectievelijk het voltooide bewerkingsproces, het lopende bewerkingsproces en de bewegingsrichting van de AFM-tip. De breedte (B 2 ) van het bewerkte kanaal in Fig. 6(b) was groter dan dat (W 1 ) in Fig. 6(a). AS1 en AS2 (rode ononderbroken lijnen) vertegenwoordigen de contactlengte tussen de doorsnede van de AFM-tip en het monstermateriaal. De waarde van AS1 bleek groter te zijn dan die van AS2 wanneer de bewerkingsbreedte “L 1 ” was gelijk aan “L 2. ”
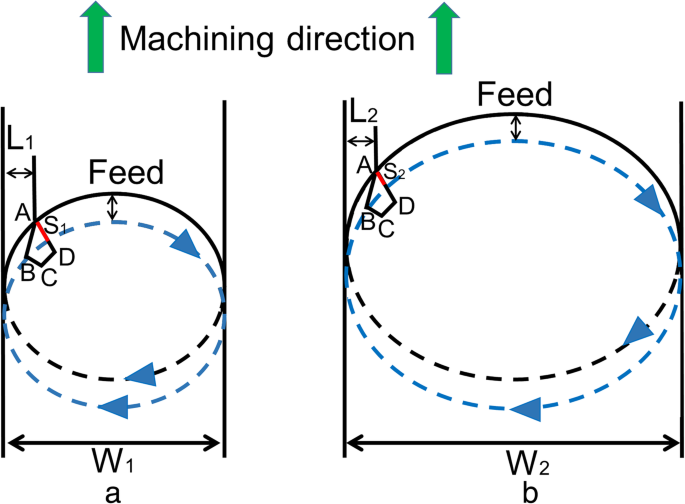
Schematische weergave van het AFM-tiptraject tijdens het nanofreesproces:de bewerkte breedte van nanokanaal (a ) is kleiner dan nanokanaal (b ), en de gestippelde ellipsen, de zwarte effen ellipsen en de blauwe pijlen vertegenwoordigen respectievelijk het voltooide bewerkingsproces, het lopende bewerkingsproces en de bewegingsrichting van de AFM-punt.
De waarde van Sh in verg. (5) werd verkregen door Vgl. (8), waarbij D en AS respectievelijk de diepte van het bewerkte kanaal en de contactlengte tussen de doorsnede van de AFM-tip en het monstermateriaal zijn.
$$ {S}_h=\frac{1}{2}\cdot \left|D\left|\cdot \right|\; AS\rechts| $$ (8)Vandaar, vgl. (5) werd verder herschreven in de vorm van Vgl. (9).
$$ {F}_{\mathrm{N}}=\frac{1}{2}\cdot \left(p\cdot \frac{\cos \beta }{\cos \alpha }-\tau \right) \cdot \left|D\left|\cdot \right| AS\rechts| $$ (9)De waarden van α en β werden tijdens het gehele bewerkingsproces constant gehouden. De waarden van de reksnelheid bij 1500 Hz werden gevonden in het bereik van 2,03 × 10 5 ~3,66 × 10 5 s -1 ; daarom kan worden aangenomen dat lokale normale druk (p ) bereikte zijn grenswaarde bij 1500 Hz. Verder vertoonde de bewerkingssnelheid geen effect op het herstel van het monster tijdens bewerking bij 30-150 V (~-2,03-3,66 mm/s) [53]; dus werden de uiteindelijke dimensionale afmetingen van het nanokanaal alleen bepaald door machinale afmetingen. De waarden van AS2 (Fig. 6(b)) bleken kleiner te zijn dan die van AS1 (Fig. 6(a)) voor grotere machinaal bewerkte breedtes, en volgens Vgl. (9) was de waarde van D groter voor een kleinere waarde van AS. Daarom namen de waarden van de bewerkingsdiepte toe met de toenemende aandrijfspanningen. Een typisch AFM-beeld van het nanokanaal vervaardigd onder een normale belasting van 25 μN, een stuurspanning van 120 V en een frequentie van 1500 Hz wordt gepresenteerd in aanvullend bestand 1:figuur S4(b). Het is opvallend dat materialen werden verwijderd in zowel chip- als stapelvorming, en de verdreven materialen verzamelden zich slechts aan één kant van het nanokanaal. Bovendien hoopten de uitgestoten materialen zich op in chipvorming aan de onderkant van het nanokanaal tijdens machinale bewerking bij 150 V onder een normale belasting van 25 μN. Daarom waren de groottegegevens van het gefabriceerde nanokanaal tijdens bewerking bij een spanning van 150 V en een frequentie van 1500 Hz (onder een normale belasting van 25 μN) leeg in Fig. 4d.
Uit figuur 4c blijkt duidelijk dat de breedte van het nanokanaal begon toe te nemen met de toenemende stuurspanningen. Bovendien, toen de waarden van normale belasting en stuurspanning constant werden gehouden, was de breedte van het nanokanaal vervaardigd met een frequentie van 1500 Hz groter dan die van 100 Hz. Bovendien was de bewerkingsdiepte van het nanokanaal vervaardigd bij 1500 Hz dieper dan die van 100 Hz, en de dwarsdoorsnede van de punt bleek groter te zijn tijdens het bewerken van een dieper nanokanaal. Daarom werden de nanokanalen breder gefabriceerd bij diepere bewerking.
Eerste overdracht van nanokanaalmallen
Nanokanalen bewerkt door middel van een enkele krasmethode onder normale belastingen van 25 μN, 33 μN, 41 μN, 50 μN en 58 μN werden toegepast op het eerste overdrachtsproces. Bovendien werden nanokanaalmallen vervaardigd door nanofrezen met een frequentie van 100 Hz in het stuurspanningsbereik van 30-150 V (met een tussenruimte van 30 V) ook gebruikt in het overdrachtsproces. Nanokanalen (80 nm diepte en 510 nm breedte) bewerkt met een enkele krasmethode werden "nanokanaal I" genoemd, terwijl nanokanalen (50 nm diepte en 610 nm breedte, 90 nm diepte en 630 nm breedte) vervaardigd door nanofrezen werden genoemd als "nanokanaal II" en "nanokanaal III", respectievelijk. Bij het eerste overdrachtsproces werden drie verschillende PDMS-gewichtsverhoudingen (5:1, 7:1 en 9:1) gebruikt.
Figuur 7a en b onthullen de effecten van verschillende PDMS-gewichtsverhoudingen op de wandafmetingen onder een normale belasting van 25 N en een frequentie van 100 Hz, en de zwarte streepjeslijn vertegenwoordigt de oorspronkelijke nanokanaalafmeting vóór overdracht. Het typische AFM-beeld en de bijbehorende dwarsdoorsnede van de wand verkregen uit nanokanaal III met een gewichtsverhouding van 5:1 tijdens de eerste overdracht worden weergegeven in Fig. 7c en d, en deze wand werd "muur III" genoemd. De effecten van verschillende PDMS-gewichtsverhoudingen op de wandafmetingen onder een enkel krasproces met een normale belasting van 17 N en een frequentie van 100 Hz werden getoond in ESI (zie aanvullend bestand 1:Figuren. S5, S6, S7 en S8 van ESI voor details). The walls obtained from “nanochannel I” and “nanochannel II” were termed as “wall I” and “wall II,” respectively. It is evident that the heights of all walls at different PDMS weight ratios were approximately the same. The widths of the walls were larger than the original nanochannel width, and the width at the weight ratio of 5:1 was found to be the largest. Due to the thermal expansion of PC sheet, a small deviation was noticed between final wall size and original nanochannel size. It was also observed that the elasticity of PDMS increased as the PDMS weight ratio decreased from 5:1 to 7:1 [41, 42]. Hence, the wall obtained at the weight ratio of 5:1 was stiffer and its elastic recovery was smaller; thus, the width of the wall obtained at the weight ratio of 5:1 was the largest.
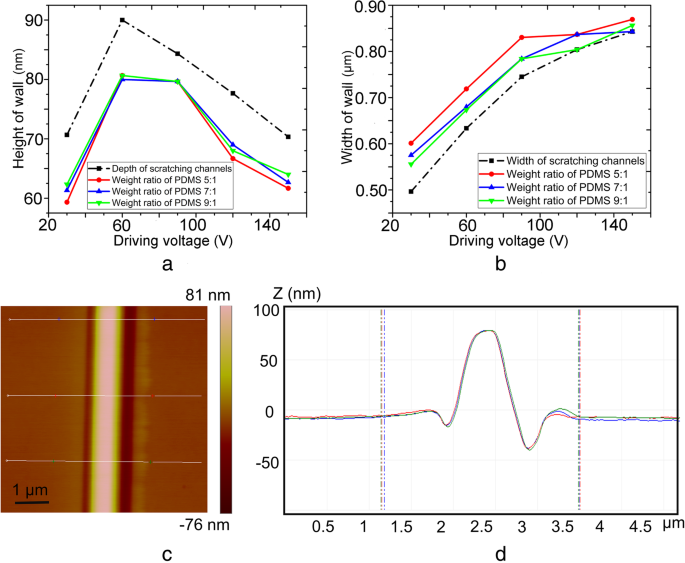
Relationship between a wall height, b wall width, and transfer parameters (various weight ratio of PDMS) during first transfer process, where the channel molds were fabricated with a normal load of 25 μN and a frequency of 100 Hz, and c typical AFM image and d corresponding cross-section of the wall obtained from nanochannel III at a weight ratio of 5:1
Second transfer of nanochannel molds
The final PDMS slabs with nanochannels were obtained during second transfer process based on the wall obtained at a weight ratio of 5:1 in the first transfer process. Three different PDMS weight ratios (10:1, 9:1, and 8:1) were used during second transfer process. Figure 8a and b present the relationship between nanochannel size obtained under a normal load of 25 μN and a frequency of 100 Hz and transfer parameters during second transfer. It is clear from Fig. 8a that the depths of the nanochannels were larger than the original machining size, moreover, the depth at 10:1 was found to be larger than other two ratios. Further, the widths of the wall were also larger than the original size, and the width at 10:1 was found to be the largest (Fig. 8b). Figure 8c and d present a typical AFM image and corresponding cross-section of the nanochannel (120 nm depth and 690 nm width) obtained from wall III at a weight ratio of 10:1 during second transfer, and it was termed as “nanochannel C.” The relationship between the nanochannel sizes obtained under single scratching process with a normal load of 25 μN and a frequency of 100 Hz and the transfer parameters during the second transfer process were shown in ESI (see Additional file 1:Figures. S9, S10, S11 and S12 of ESI for details), the nanochannels obtained from “wall I” and “wall II” were termed as “nanochannel A” and “nanochannel B”, respectively.
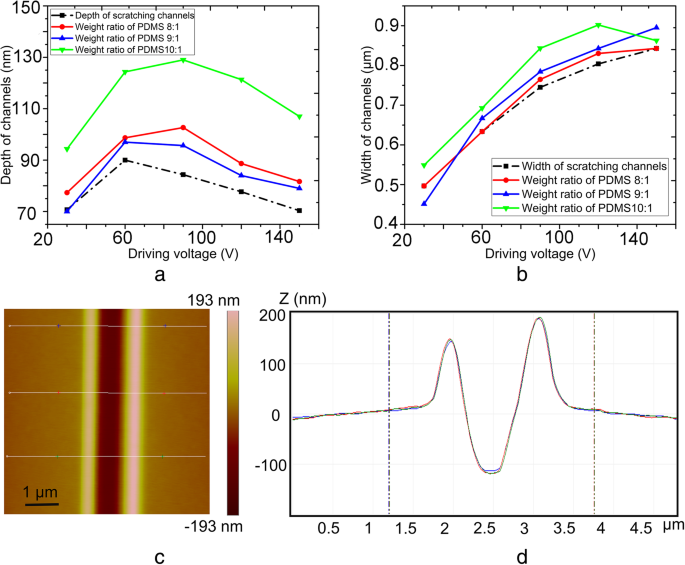
Relationship between a nanochannel height, b nanochannel width, and transfer parameters (various weight ratio of PDMS) during second transfer, where the channel molds were fabricated with a normal load of 25 μN and a frequency of 100 Hz, and c typical AFM image and d corresponding cross-section of the nanochannel obtained from wall III at a weight ratio of 10:1 during second transfer
The depths of nanochannels obtained from walls II and III were larger than the original machining size, whereas the depth obtained from wall I was smaller than the initial machining size. Furthermore, the changes in width were identical to the changes in depth. The aspect ratio of wall I was larger than those of walls II and III, thus each wall manifested different thermal expansion values. Hence, the changing trends of width and depth during second transfer were different though at the same PDMS weight ratio. The values of the depth and width of walls II and III at 9:1 and 8:1 were found to be closer to the original machining size compared with 10:1. Because the elastic recoveries of PDMS at 9:1and 8:1 are closer to 5:1 than 10:1, which indicates an almost similar recovery trend for PDMS at 9:1, 8:1, and 5:1.
Application of nanochannel devices in electric current measurement
Nanochannel devices are often used in the fields of single nanoparticle manipulation, electrokinetic transport phenomena, DNA analysis, and enzymatic reaction detection. The main working principle of nanofluidic chips depends on the variation in electric current; therefore, it is important to measure the electrical conductivities of nanochannel devices. The electrical conductance in a nanochannel can be estimated by Eq. (10) [56].
$$ G={10}^3N\;{}_Ae\frac{wh}{l}\sum {\mu}_i{c}_i+2{\mu}_e\frac{w}{l}{\delta}_n $$ (10)waar μ ik is the mobility of ion i , c ik is the concentration of ion i , δ n is the effective surface charge inside the nanochannel, and NA and e signify Avogadro constant and electron charge, besides, w , h en l are the nanochannel width, height and length, respectively. It is obvious that the electrical conductance of a nanochannel is affected by the nanochannel feature dimensions and the solution concentration. The electric double layer (EDL) plays an important role in the nanochannel when the ratio of DEL thickness to the nanochannel height increases. The diffuse layer thickness of EDL is 3~5 times of the Debye length (λ D ), which can be expressed by Eq. (11) [57].
$$ {\lambda}_D=\sqrt{\frac{\varepsilon_0{\varepsilon}_r{k}_bT}{2{n}_{i\infty }{(ze)}^2}} $$ (11)waar n ik ∞ denotes ion density in the solution, ε o is the permittivity of vacuum, ε r is the dielectric constant of electrolyte solution, z is the valency of buffer solution (z = z + − z − = 1 for KCl), and kb en T are the Boltzmann constant and temperature, respectively. In the present study, three different nanofluidic chips were obtained after the completion of transfer process. Nanofluidic chips consisted of nanochannels A, B, and C were termed as nanofluidic chips A, B, and C, respectively. Each nanofluidic chip contained four nanochannels. The widths and the depths of nanofluidic chips A, B, and C were measured as 60 nm and 500 nm, 80 nm and 680 nm, and 120 nm and 690 nm, respectively. The effective length of nanochannels in all chips was calculated as 50 μm. As shown in Fig. 8, pile-ups distribute on the sides of the nanochannels A, B, and C. The pile-ups may fill into the nanochannels and lead to a failure of the preparation for the nanofluidic chips. Thus, in order to verify the reliability of the fabricated nanochannel devices, electrical conductivity measurement test was conducted. KCl with 1 mM concentration was as the electrolyte solution in our study, and the values of electrical current were measured by an electrometer (Model 6430, Keithley, USA). The schematic sketches of the measurements for electric current in microchannel and nanochannel are presented as the inset figures in Fig. 9a and b, respectively. The experiments were carried out under DC power (applied by an Ag electrode) with an increment of 2 V for 3-s duration. Figure 9a presents the measured I -V curves of microchannels in three different nanofluidic chips, and a linear relationship between current and voltage was observed. Moreover, as the effect of EDL in microchannels was negligible and the dimensional sizes of microchannels in different nanofluidic devices were identical, the values of current in different chips were nearly the same. It is evident from Fig. 9b that the values of current in different nanofluidic devices were distinct due to different nanochannel sizes. For KCl solution of 1 mM concentration, the value of λ D was about 10 nm, thus the diffuse layer thickness of EDL was found as 30~50 nm [57]. Consequently, EDL got overlapped along the depth (60 nm) of nanofluidic chip A; however, no overlapping was observed in nanofluidic chip C (depth of 120 nm). However, it was difficult to determine whether EDL got overlapped or not in nanofluidic chip B (depth of 80 nm). It assumes that the effective surface charges (δ n ) in all nanochannels are identical as the charge density of a surface is material property [58, 59]. The concentration of the ions in a nanochannel depends on the EDL field, the stronger the EDL field, the higher the ion concentration in the nanochanel [44]. In the present study, the EDL field in nanofluidic chip A is the strongest as the highest ratio of the DEL thickness to the nanochannel height, which signifies that the ion concentration in the nanochannel of nanofluidic chip A is the highest. Volgens vgl. (10), the nanochannel of nanofluidic chip A is more conductive due to the higher ion concentration. Hence, the value of electrical current in nanofluidic chip A was the largest, whereas nanofluidic chip C yielded the smallest value. In addition, at larger width sizes, EDLs did not overlap along the width directions of nanochannels. In nanofluidic chip B, when the value of applied electric field was lower than 25 V, a linear relationship was noticed between current and applied voltage; however, a limiting region appeared as the value of applied voltage increased and finally, became liner again as the electrical field increased further, this phenomenon belongs to ohmic-limiting-overlimiting current characteristic [60, 61]. The results of electrical current measurement revealed that the nanofluidic devices fabricated by the proposed method were effective, the pile-ups of the nanochannels A, B, and C had almost no influence on the performance of the nanofluidic devices.
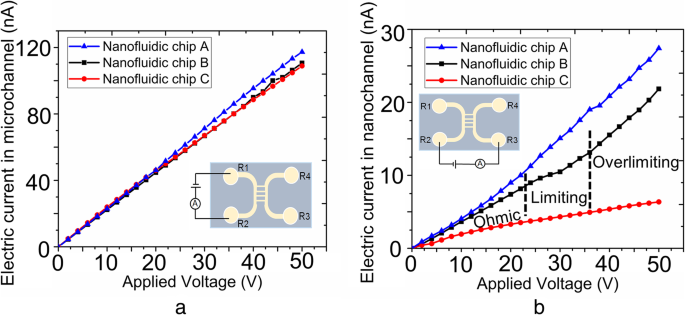
Electric current measurement results based on the fabricated nanochannel devices, the cross-section size (depth × width) of nanochannels for nanofluidic chip A, B, and C are 60 × 500 nm, 80 × 680 nm and 120 × 690 nm, respectively. een Current in microchannels. b Current in nanochannels. The insets display the schematic sketches of the measurements
Conclusies
In the present research, nanochannels with controllable sizes (sub-100-nm depth) were fabricated by AFM tip-based nanomilling, and for the first time, the machined nanochannels were applied to prepare nanofluidic devices. The multichannel nanofluidic devices were prepared in four steps:(1) fabrication of nanochannels by AFM tip and piezoelectric actuator, (2) fabrication of microchannels by lithography, (3) transfer of micro- and nanochannels, and (iv) bonding. Further, nanochannel sizes were controlled by changing the driving voltages and frequencies inputted to the actuator. The heights of the wall obtained during first transfer were smaller than the original machining size, whereas the widths were larger than the original machining size. The experiment results revealed that during second transfer process, nanochannel sizes affected PDMS weight ratios. Finally, micro-nanofluidic chips with three different nanochannel sizes were obtained by bonding a PDMS nanochannel chip on a PDMS microchannel chip. Moreover, the electrical current measurement experiment was conducted on the fabricated nanofluidic chips, and it was found that the values of current were affected by nanochannel sizes. Therefore, PDMS nanofluidic devices with multiple nanochannels of sub-100-nm depth can be efficiently and economically fabricated by the proposed method.
Compared with other fabrication approach, the proposed method for fabrication of the nanofluidic devices in the study is easy to use and low cost; besides, the nanochannels with controllable dimension size can be obtained easily. However, the commercial AFM system cannot equip with a large-scale high-precision stage due to the spatial limitation; thus, the maximum fabrication length of the nanochannel is confined as 80 μm. In addition, the tip wear cannot be neglected after long-term fabrication due to the high machining speed, which should be investigated in future work.
Afkortingen
- AFM:
-
Atoomkrachtmicroscoop
- DC:
-
Gelijkstroom
- EDL:
-
Electric double layer
- KCL:
-
Potassium chloride
- PC:
-
Polycarbonate
- PDMS:
-
Polydimethylsiloxane
- PSD:
-
Position-sensitive photodetector
Nanomaterialen
- Stansen:een spoedcursus over dit fabricageproces
- Blog:inzicht in het fabricageproces van PDMS
- De meest populaire composiet fabricagemethoden
- Wat is het fabricageproces van plaatwerk?
- De verschillende manieren waarop het afwerkingsproces functionele waarde toevoegt aan metaalproductieprojecten
- Een 3D-printer gebruiken om uw fabricageproces te verbeteren - Video
- Uw gids voor het knippen van metaalproductieprocessen
- Procesleidingfabricage vereist vindingrijke routeplanning
- Voor de fabricage van procesleidingen moet aan exacte specificaties worden voldaan
- Hoeveel tijd heeft uw fabricageproces nodig?
- De voordelen van zandstralen voor uw op maat gemaakte metaalproductieproject