Overmolded hybride onderdelen openen nieuwe composietmarkten
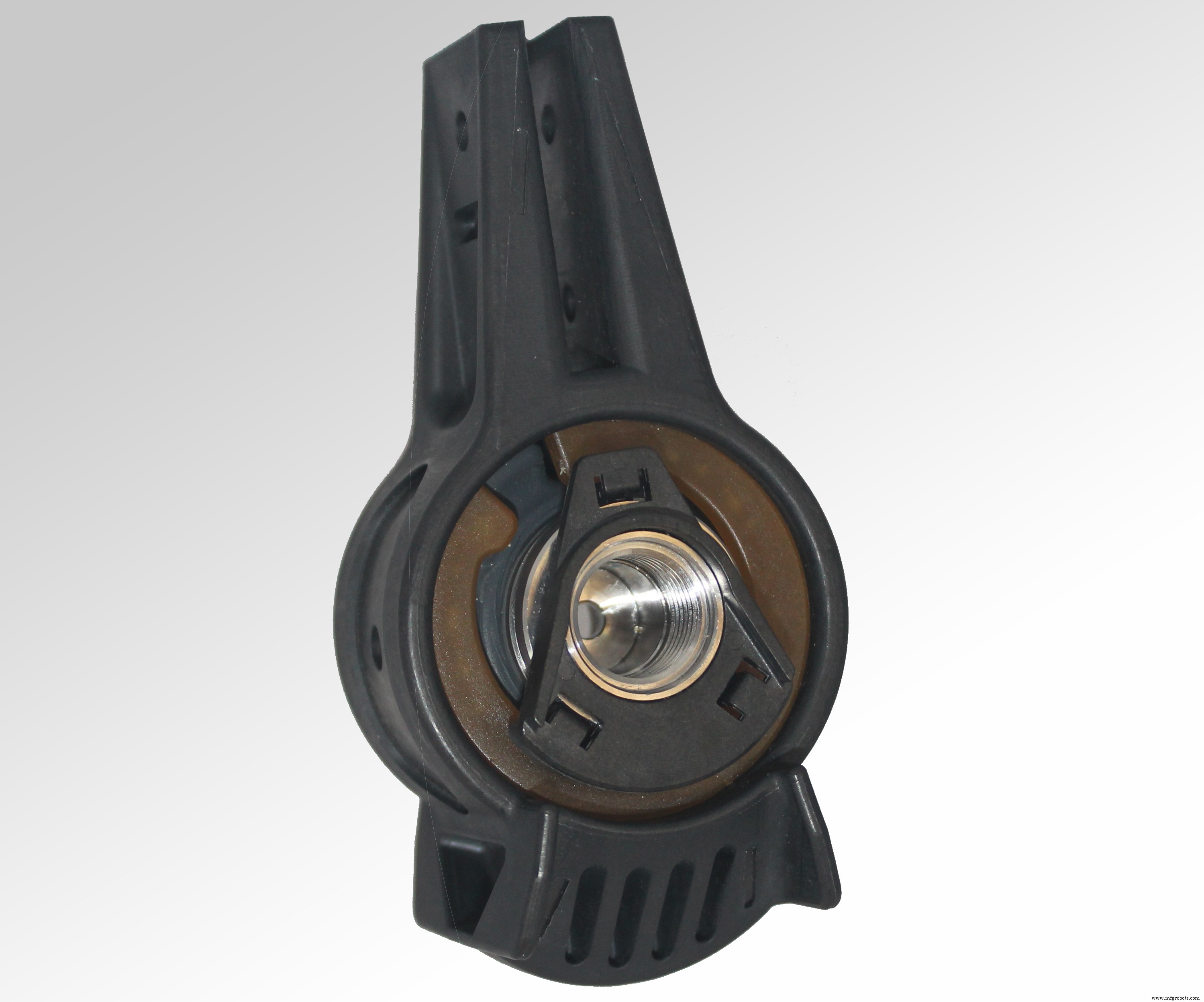
Complexiteit en kracht. Componenten zoals de B-beugel voor opslagbakken voor vliegtuigen vertonen zowel een hoge complexiteit als een vereiste voor hoge sterkte - een combinatie waarvoor de hybride overmolding-techniek bijzonder geschikt is. Bron, alle afbeeldingen | TxV Aero-composieten
In de lucht- en ruimtevaartmarkt is een OEM vaak bereid meer te betalen voor een composietcomponent, wetende dat de investering zal renderen in brandstofbesparingen vanwege het lichte gewicht van de component, een langere levensduur vanwege minder slijtage of andere verminderingen van de operationele en onderhoudskosten. Deze visie op de "productlevenscyclus" heeft vele markten en toepassingen voor composieten geopend. Bijzonderer is een composietcomponent waarvan de aanschafprijs zelf lager is dan die van de metalen versie. Maar dit is aan het veranderen. Sommige nieuwe geautomatiseerde fabricageprocessen voor composieten beginnen de schaal te kantelen ten gunste van composieten, waaronder een hybride overmolding-proces dat is ontwikkeld door TxV Aero Composites (Bristol, R.I., V.S.).
TxV, een joint venture van Tri-Mack Plastics Manufacturing (Bristol, R.I., V.S.) en Victrex (Thornton Cleveleys, V.K.), heeft zijn hybride overmolding-techniek zo ver ontwikkeld dat het de status van commerciële productie bereikt. Het bedrijf is een samenwerking aangegaan met SFS intec Aircraft Components (Althengstett, Duitsland) om een houder voor een opbergbak voor vliegtuigen te herontwerpen en commercieel te produceren die voorheen was gemaakt van aluminium van ruimtevaartkwaliteit. De beugel, een op zichzelf staand succesverhaal, demonstreert ook het potentieel van hybride overmolding en VICTREX AE 250 unidirectionele koolstofvezel/polyaryletherketon (PAEK) tape voor waardevolle gewichts- en kostenbesparingen in tal van ruimtevaarttoepassingen - voordelen bereikt door het vervangen van een subtractief metaalbewerkingsproces door een composietproces waarbij materiaal wordt toegevoegd, niet afgetrokken.
Van aftrekken tot optellen
Machinisten en machinewerkplaatsen die metalen componenten op CNC-machines produceren, hebben zichzelf de bijnaam "chipmakers" gegeven, om de voor de hand liggende reden dat hun processen onnodig materiaal van metalen blanco's wegsnijden om componenten te maken, waardoor schrootspanen ontstaan. Deze chips vormen een kostbaar aspect van metaalbewerking, of ze nu worden weggegooid, naar een recycleerder worden gestuurd of in eigen beheer worden verwerkt. In het geval van SFS intec's overhead opslagbakbeugel, wordt 60 tot 70% van het aluminium schroot tijdens de verschillende freesstappen die nodig zijn om het te bewerken.
Dit hoge uitvalpercentage maakt de grondstofkosten voor een netvormige of bijna netvormige composietversie van de beugel mogelijk lager dan de metalen materiaalkosten. “We kunnen concurreren met goedkoper (per pond) aluminium vanwege de chips; als de buy-to-fly-ratio 8:1 is, wordt het meeste gekochte aluminium schroot”, zegt Jonathan Sourkes, senior accountmanager bij TxV. “Een andere factor is de tijd die elk onderdeel kwijt is aan het frezen. We kunnen [samengestelde] onderdelen maken in minuten, niet in uren.”
Naast de grondstofkosten waren composietversies van componenten zoals de beugel - met een complexe geometrie en die hoge draagprestaties vereisen - economisch niet haalbaar met historisch beschikbare productieopties. Aan de ene kant, als de componenten zouden zijn gemaakt met goedkope, gehakte vezelversterking in een snel, low-touch proces zoals spuitgieten, zou het onderdeel niet voldoende draagvermogen bereiken. Aan de andere kant, als het zou worden gemaakt met een hogere belastingdragende, continue vezelversterking via een proces met lage snelheid en hoge aanraking, meestal met enige handmatige lay-up, zou de productie te traag zijn en/of productiekosten met zich meebrengen die de eindproduct te duur.
Vanwege deze belemmeringen voor nieuwe composiettoepassingen van dit type, heeft de composietindustrie als geheel aanzienlijke middelen besteed aan het ontwikkelen van geautomatiseerde processen die dergelijke componenten kunnen produceren met voldoende hoge productiesnelheden en met voldoende draagvermogen om te voldoen aan de behoeften en specificaties van de ruimtevaartklant . Met het oog op de commerciële productie van dergelijke composietcomponenten, is TxV in 2017 ontstaan, specifiek om de commerciële acceptatie van innovatieve productieprocessen voor op polyketonen gebaseerde composiettoepassingen in de lucht- en ruimtevaartindustrie te versnellen.
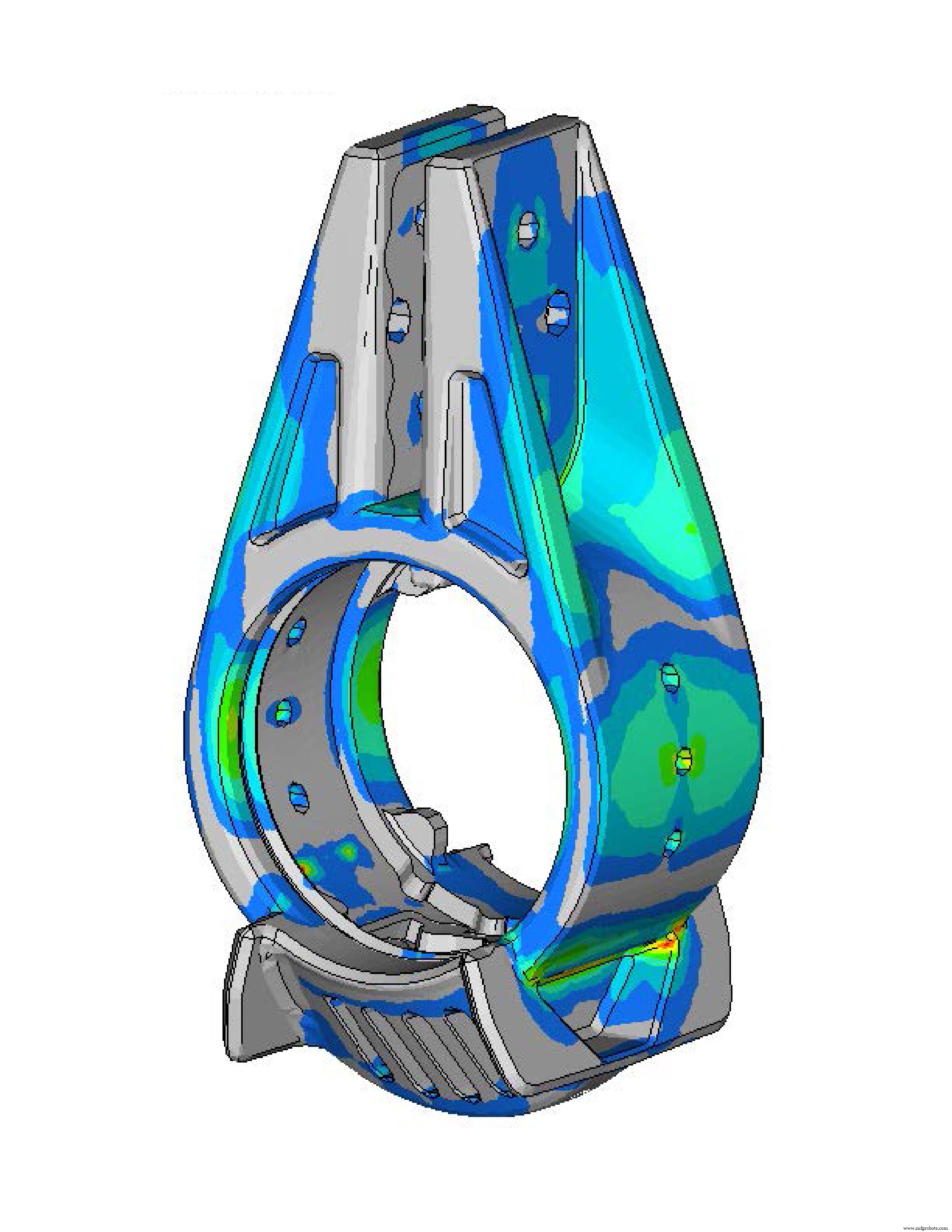
Virtuele prototyping. Met behulp van gepatenteerde gegevens die zijn ontwikkeld om de relatie tussen het laminaat en de overmold te karakteriseren, herhaalde TxV de lay-ups en laagoriëntaties zonder een fysiek prototype te hoeven vervaardigen en testen. Iteraties gaan door totdat de zichtbare spanningen, zoals hier afgebeeld, binnen het bereik van de opgegeven belastinggevallen vallen.
De overmolded hybride oplossing van TxV bevat twee belangrijke verbeteringen aan de stand van de techniek in de fabricage van composietcomponenten. Ten eerste automatiseert het de productie van die onderdelen van het onderdeel die de sterkte of stijfheid van continue vezelversterking vereisen. Ten tweede maakt het gebruik van de snelheid van spuitgieten om de complexe geometrieën van het onderdeel te voltooien. Meer specifiek produceert het een op maat gemaakt laminaat om lasten aan te kunnen, dat vervolgens wordt omgevormd om te functionaliseren en definitieve onderdeelgeometrieën te creëren. Volgens Sascha Costabel, hoofd innovatie bij SFS intec Aircraft Components, is de hybride techniek "een goede optie voor componenten die bestand moeten zijn tegen hoge niveaus van mechanische spanning en geometrieën die meerdere bewerkingsstappen vereisen waar conventionele bewerking wordt gebruikt."
Samenwerken met SFS intec is een goede keuze geweest, zegt Sourkes. “Als wereldleider op het gebied van systeembijlagen doet SFS altijd iets heel interessants. Ze zijn erg innovatief en bereid om te investeren in nieuwe technologieën”, merkt hij op. SFS intec heeft ook een sterke relatie met zijn vliegtuigklanten, voegt hij eraan toe, en ze beschikken over het vermogen om kwalificatieprocessen uit te voeren - de sleutel tot de goedkeuring van een opnieuw ontworpen onderdeel door de lucht- en ruimtevaartindustrie.
De beugel van de opbergbak voor vliegtuigen, specifiek aangeduid als een "B-beugel", werd gekozen als het eerste bevestigingsonderdeel voor het herontwerp van composieten, omdat het representatief is voor onderdelen die moeilijk te ontwerpen en te produceren zijn. Na collaboratieve engineering, gedeeltelijke conceptualisering en ontwerp, en modellering van prestaties via een Altair (Troy, Mich., V.S.) eindige-elementenanalyse (FEA)-tool, herhaalde het projectteam het eerste artikel om het model te valideren, testen en bewijzen. Ontwerp voor fabricage stond centraal bij de ontwikkeling van de composietbeugel, die gebruikmaakt van de productievoordelen van geautomatiseerde tape-legging voor de continue vezelversterkte elementen en hogesnelheidsspuitgieten voor de gehakte vezelversterkte elementen.
Beugels Gebouw B
Een belangrijk aspect van het hybride overmolding-proces is het gebruik van verschillende polymeren van dezelfde klasse. PAEK dient als de matrixhars voor de ononderbroken vezelcomposietdelen van de beugel, terwijl polyetheretherketon (PEEK) wordt gebruikt in de overgegoten gebieden. VICTREX PAEK en PEEK bieden superieure weerstand tegen vermoeidheid, chemicaliën en corrosie; uitstekende weerstand tegen rook, vlammen en giftigheid; snelle vervormbaarheid; en lasbaarheid. VICTREX AE 250, een lager smeltend PAEK (LM PAEK), biedt een smelttemperatuur van 40 graden C lager dan PEEK's. "Wanneer gesmolten PEEK over het oppervlak van de LM PAEK-composiet stroomt, zorgt de lagere smelttemperatuur voor een sterke hechting", legt Sourkes uit.
Specifieke grondstoffen voor de B-beugel zijn VICTREX AE 250 unidirectionele koolstofvezelversterkte PAEK-tape (58% koolstofvezel) in breedtes van twee inch; en korte met koolstofvezel gevulde VICTREX PEEK 150CA30 (30% koolstofvezel). Deze materialen voeden de hybride overmolding-productiewerkcellen, die de beugels maken via het volgende meerstapsproces.
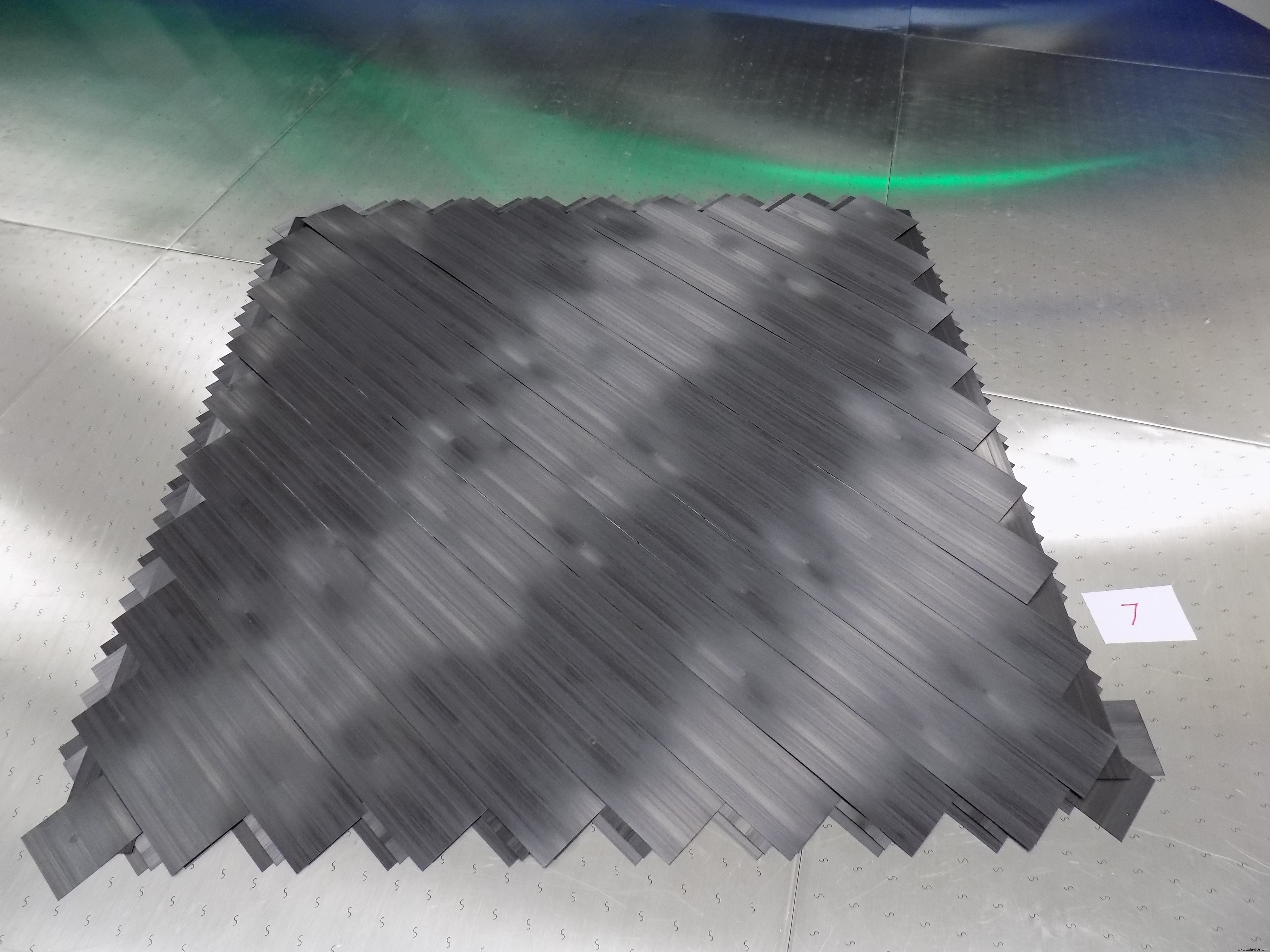
Stap 1. Een geautomatiseerd Dieffenbacher Fiberforge 2000-tapelegsysteem produceert op maat gemaakte laminaatplano's.
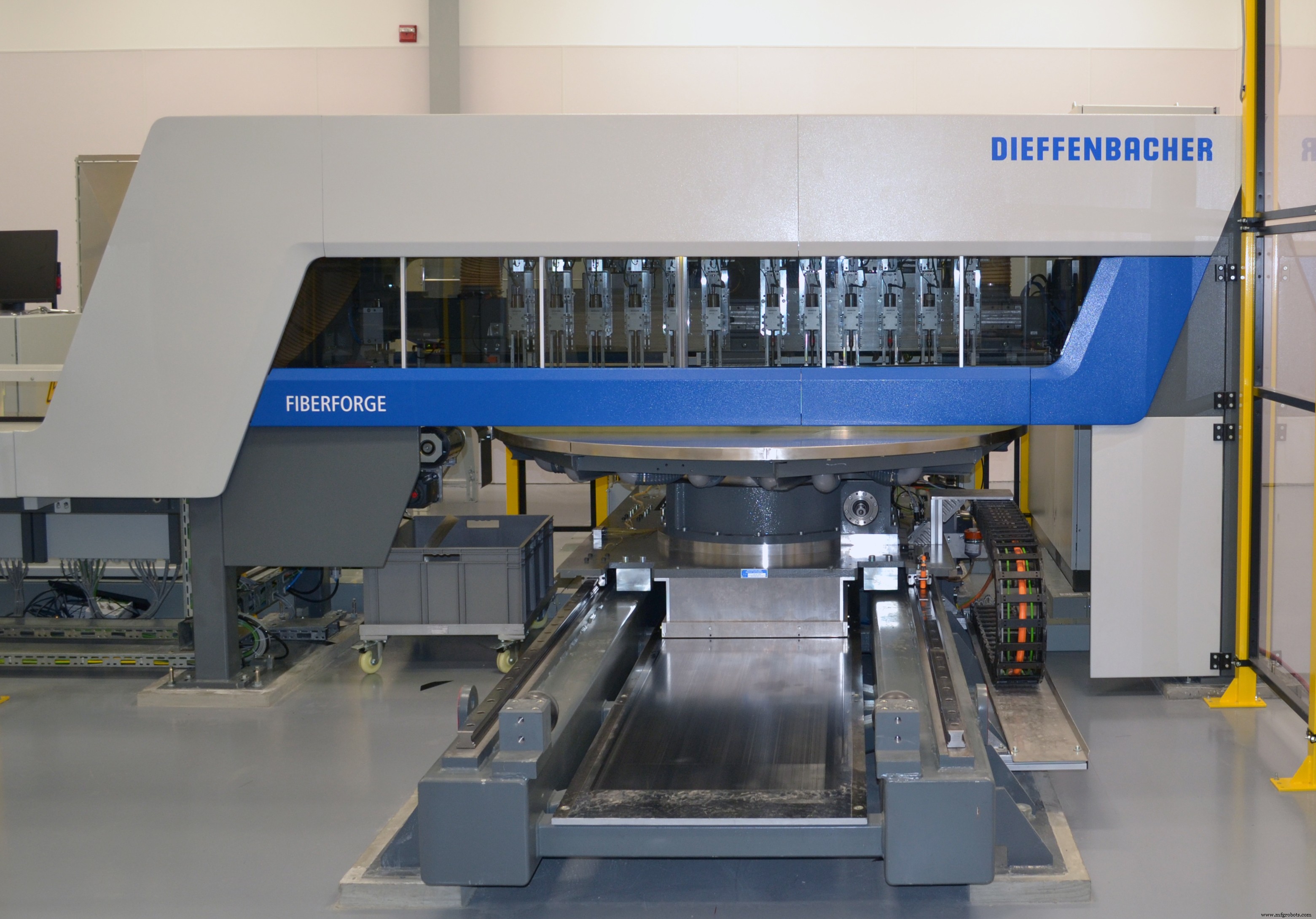
Eerst worden de koolstofvezel/PAEK-tapes in een op maat gemaakte blank gelegd met behulp van een Dieffenbacher (Eppingen, Duitsland) Fiberforge 2000-tapelegsysteem. "Deze machine is momenteel een van de snelste tape-legsystemen ter wereld", getuigt Sourkes. Het is uitgerust met robots om tapespoelen te laden en opnieuw te laden, zodat het ononderbroken kan werken, waardoor de handmatige aanraaktijd tot een minimum wordt beperkt. Layup is zo ontworpen dat openingen tussen tapes worden geminimaliseerd. Elke laag van de B-beugel op maat gemaakte blank wordt geïnspecteerd voordat de volgende laag wordt gelegd. Het proces wordt uitgevoerd in een omgeving met gecontroleerde omgeving om de kans op vreemde voorwerpen en puin (FOD) te minimaliseren.
De op maat gemaakte blanco's worden vervolgens geconsolideerd in een geautomatiseerde, op maat gemaakte cel die minimale handmatige handelingen vereist om de laminaten te laden en te lossen. In de cel consolideren op elkaar afgestemde verwarmde platen een paneel, waardoor holtes worden geëlimineerd. Bijpassende koude platen koelen vervolgens het paneel. De twee sets degels, die op temperatuur worden gehouden, zijn veel efficiënter dan een statische pers met één set degels. "Het resultaat is een drastisch kortere cyclustijd, gemeten in minuten versus uren", zegt Sourkes.
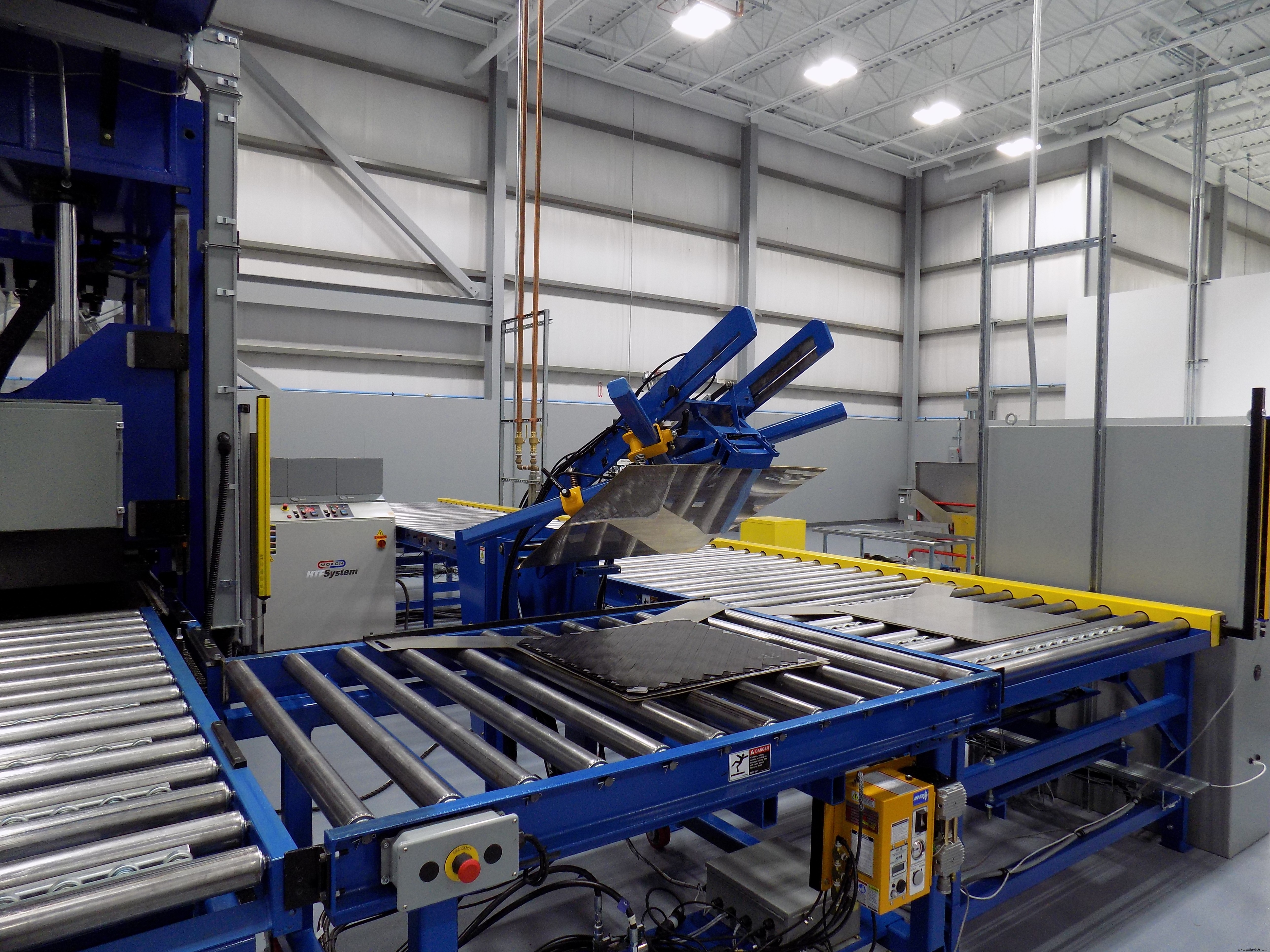
Stap 2. Op maat gemaakte blanco's worden geconsolideerd in een geautomatiseerde, op maat gemaakte consolidatiecel, die is voorzien van twee sets platen die op temperatuur worden gehouden (een warm, een koud) om deze stap te versnellen.
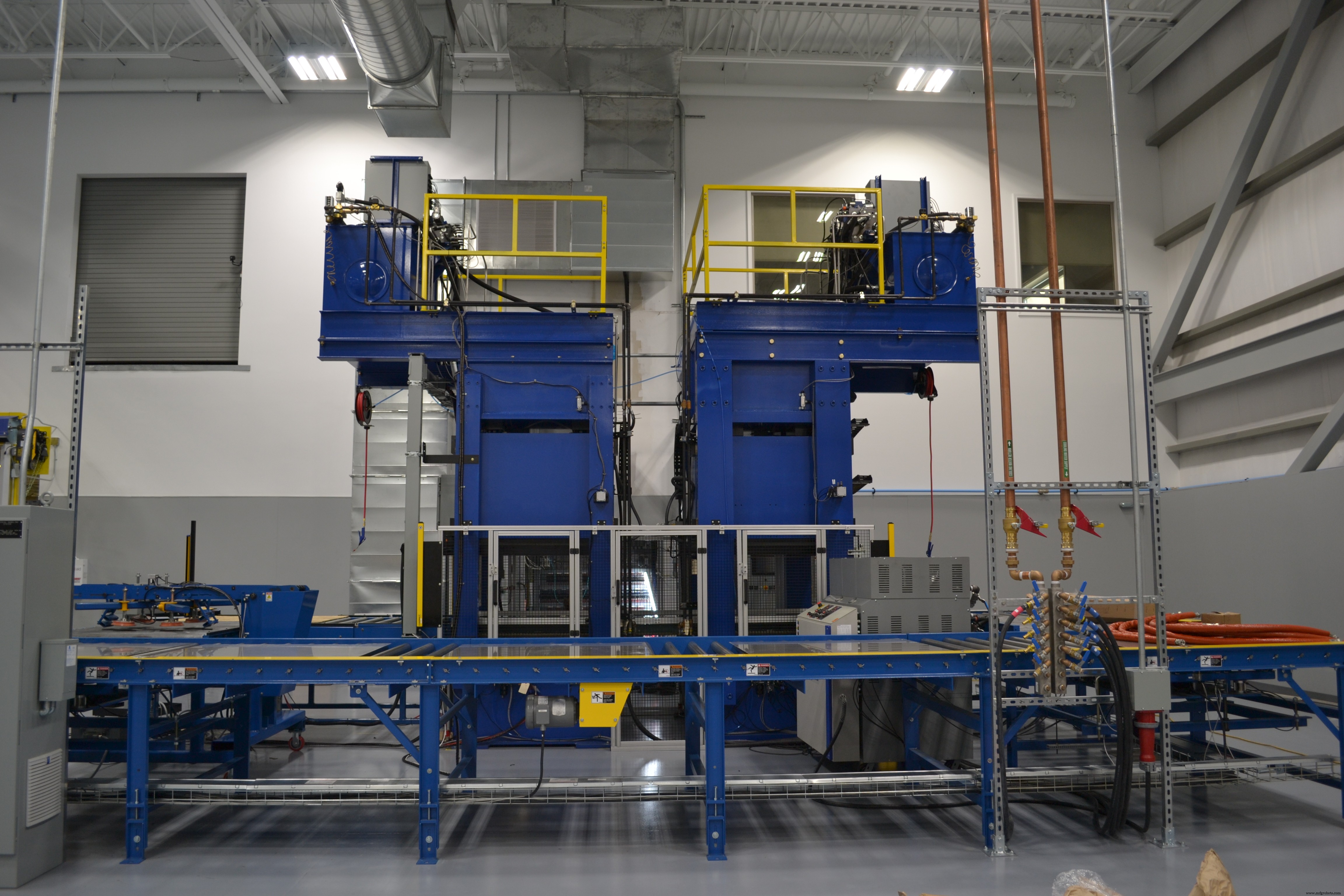
De geconsolideerde laminaatvoorvormen worden vervolgens verder verwerkt in een gepatenteerde werkcel om de primaire vorm van de beugel te vormen (stap 3). De uiteindelijke koolstofvezel/PAEK-inzetstukken worden vervolgens uit de gevormde blanks gesneden met behulp van een Flow International (Kent, Wash., U.S.) waterstraalsnijder (stap 4)
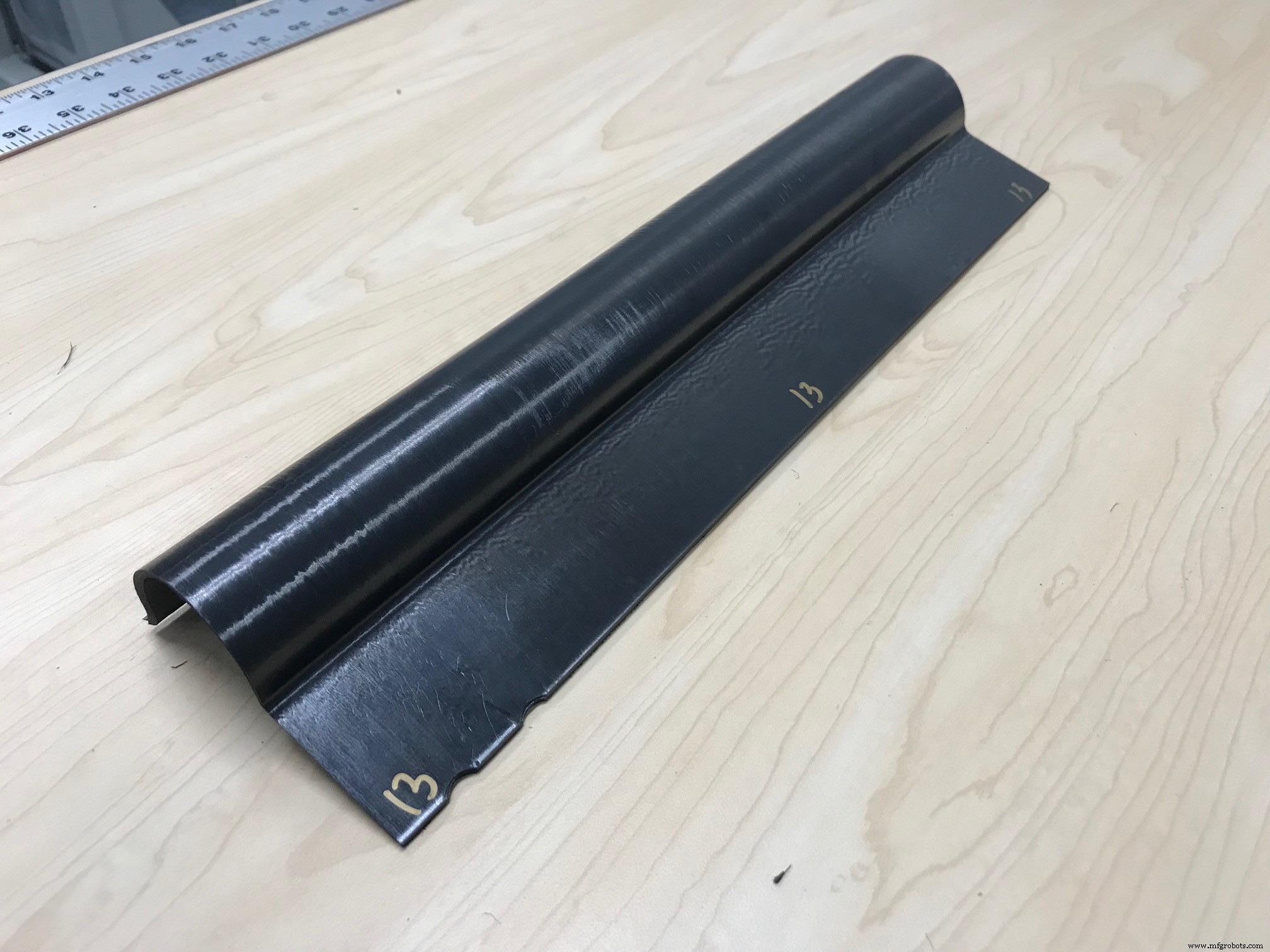
Stap 3. Een gepatenteerde werkcel vormt de primaire vorm van de beugel.
Bij het bepalen van de maat van de op maat gemaakte blank wijst Sourkes erop dat er voor elk project een afweging moet worden gemaakt. “We kunnen het laminaat zo op maat maken dat we drie of vier rechthoeken uit een enkele vierkante blanco kunnen ritsen. Door een zo groot mogelijke blanco op te leggen en deze vervolgens in preforms te snijden, maximaliseert u de buy-to-fly-ratio; maar het snijden van de preforms betekent meer tijd voor waterstraalsnijden.” In het B-beugelproject wordt elk geconsolideerd laminaat in meerdere voorvormen gesneden
De volgende stap is de overgietstap, die wordt uitgevoerd met een Engel (Schwertberg, Oostenrijk) hoge-temperatuur spuitgietmachine (stap 5). De inzetstukken worden in een spuitgietholte geplaatst die vervolgens wordt gevuld met gesmolten PEEK. De inzetstukken worden in een spuitgietholte geplaatst die is gevuld met gesmolten PEEK, dat de toplaag van de VICTREX AE 250-laminaten smelt om een sterk smeltgebonden onderdeel te creëren.
Indien nodig wordt een onderdeel via machinale bewerking tot netvorm afgewerkt. "Hoewel het ons doel is om onderdelen te vormen die bijna net zijn,", geeft Sourkes toe, "is vaak achteraf een minimale mate van bewerking vereist om de procesgeometrie op te schonen." De bewerking kan worden uitgevoerd met een waterjet- of CNC-bewerking.
Baanbrekende resultaten
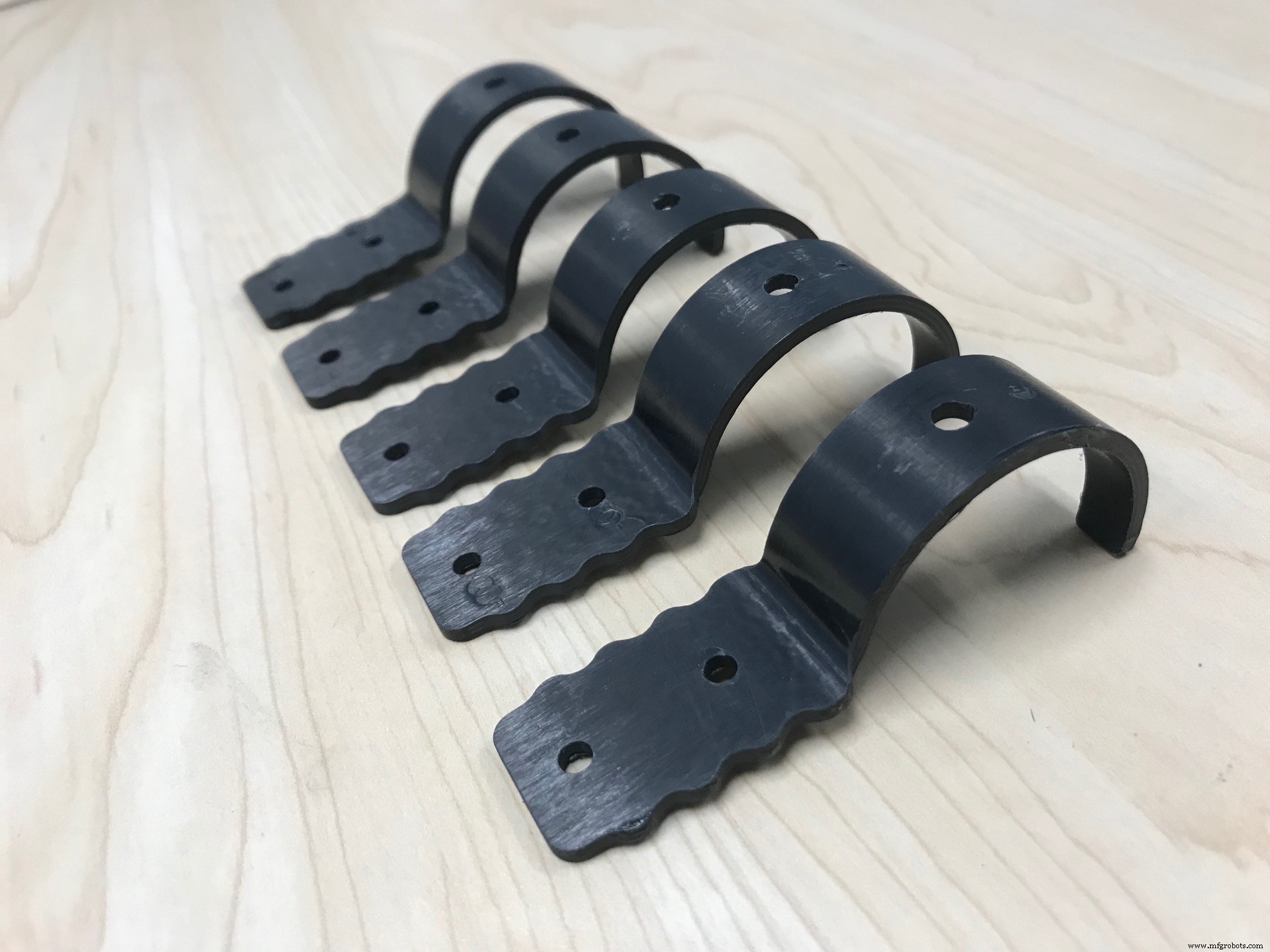
Stap 4. Een Flow International waterstraalsnijder snijdt de koolstofvezel/PAEK-inzetstukken uit de gevormde blanks. In elke beugel worden twee van deze inzetstukken gebruikt.
Bij de productie van de SFS intec-beugel bereikt het TxV hybride overmolding-proces cyclustijden van drie minuten en een buy-to-fly-ratio van 1,06:1. "Het is het efficiënte gebruik van materialen en het snelle fabricageproces dat ons in staat stelt om thermoplastische composietonderdelen met toegevoegde waarde te produceren, en dat maakt systeemkostenverlagingen mogelijk ten opzichte van de bestaande metalen ontwerpen", benadrukt Sourkes. "In feite vervangen we een goedkopere grondstof met een hoge buy-to-fly-ratio en een aanzienlijke verwerkingstijd door een hoogtechnologische materiaaloplossing." Het resultaat is een gewichtsbesparing in het bereik van 30 tot 40% en kostenbesparingen in het bereik van 20 tot 30% bij een vergelijkbare vervanging, dat wil zeggen een vervangend onderdeel dat dezelfde geometrische en operationele specificaties volgt als het bestaande onderdeel. "Met name gewichtsbesparingen kunnen oplopen tot 60% als we de mogelijkheid krijgen om een onderdelensysteem volledig opnieuw te ontwerpen", merkt hij op.
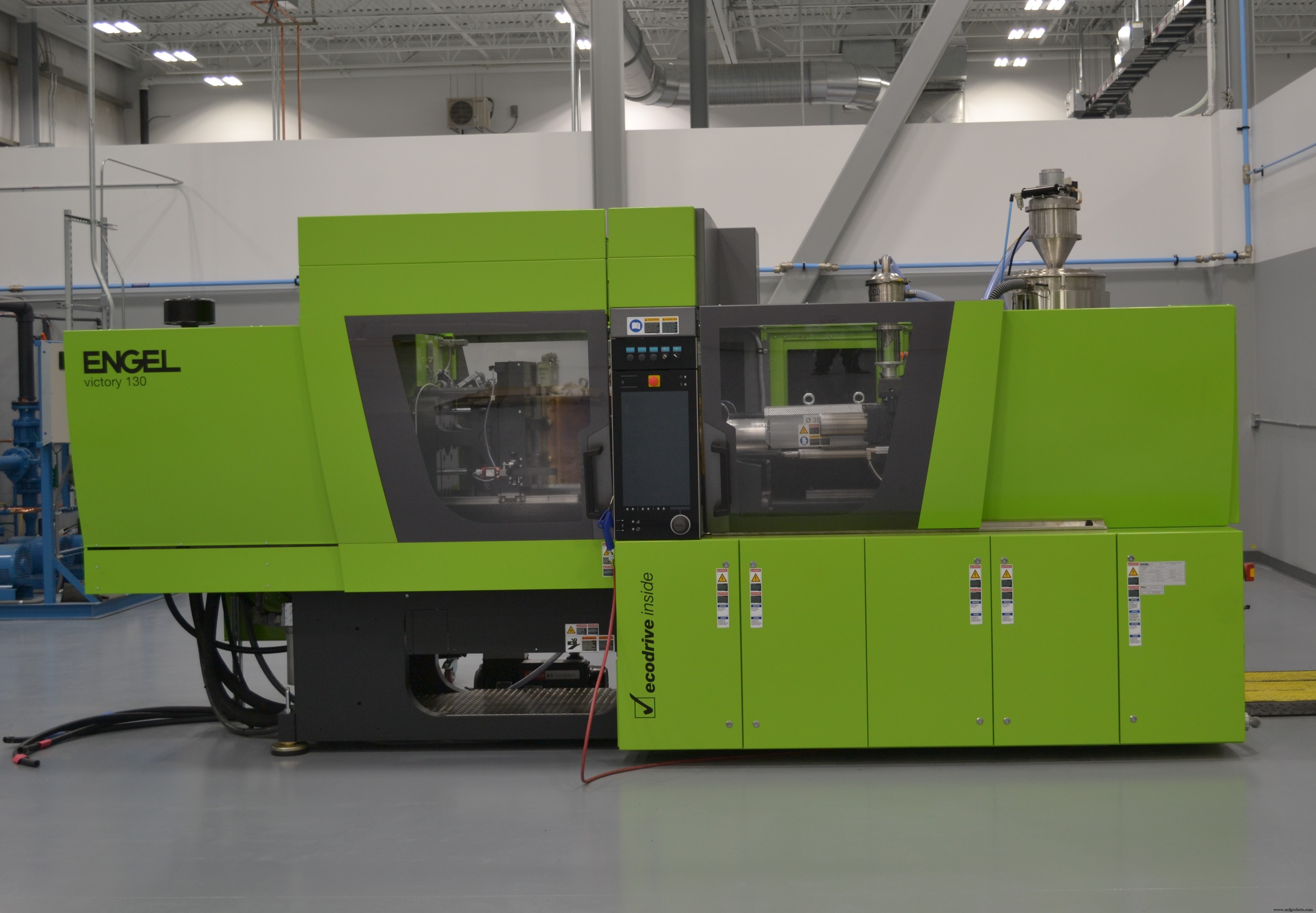
Stap 5. Een Engel-spuitgietmachine die is geoptimaliseerd voor PEEK hybride overmolding voltooit het composietdeel door de inzetstukken te overgieten.
De koolstofvezel / PAEK / PEEK-beugel heeft ook het aantal onderdelen geconsolideerd:TxV en SFS kwamen overeen om een spreidneus op de onderkant van het onderdeel te spuitgieten in dezelfde bewerking die werd gebruikt om te functionaliseren en andere functies toe te voegen. Voorheen werd de spreiderneus gemaakt van PEEK en vervolgens op zijn plaats gehouden door twee klinknagels. Zo resulteert de consolidatie zowel in een verminderd aantal onderdelen als in de eliminatie van een montagestap.
De expertise van de twee bedrijven die TxV hebben gelanceerd, heeft ongetwijfeld het succes van hybride overmolding mogelijk gemaakt. Sourkes legt uit dat Victrex, na de ontwikkeling van het PAEK-materiaal en de verwerkingstechnologie, eerst de mogelijkheden heeft verkend met bestaande zakenpartners. "Bedrijven met spuitgietexpertise hadden echter niet de expertise om met continu vezelversterkte composieten te werken en vice versa." Victrex en Tri-Mack werkten een aantal jaren samen voordat ze in 2017 TxV vormden en het speciaal gebouwde polyketon-composietcentrum van uitmuntendheid van de onderneming bouwden, dat sterk geautomatiseerd is en ontworpen voor serieproductie met hoge snelheid.
Gevraagd om het TxV-proces en de resultaten te vergelijken met een conventionele productiebenadering, merkt Sourkes op dat de B-beugel niet geschikt is voor standaard composietproductiebenaderingen. "Dit zou een hele uitdaging zijn zonder de beugel van een samengestelde knuppel te bewerken - wat onbetaalbaar zou zijn", zegt hij.
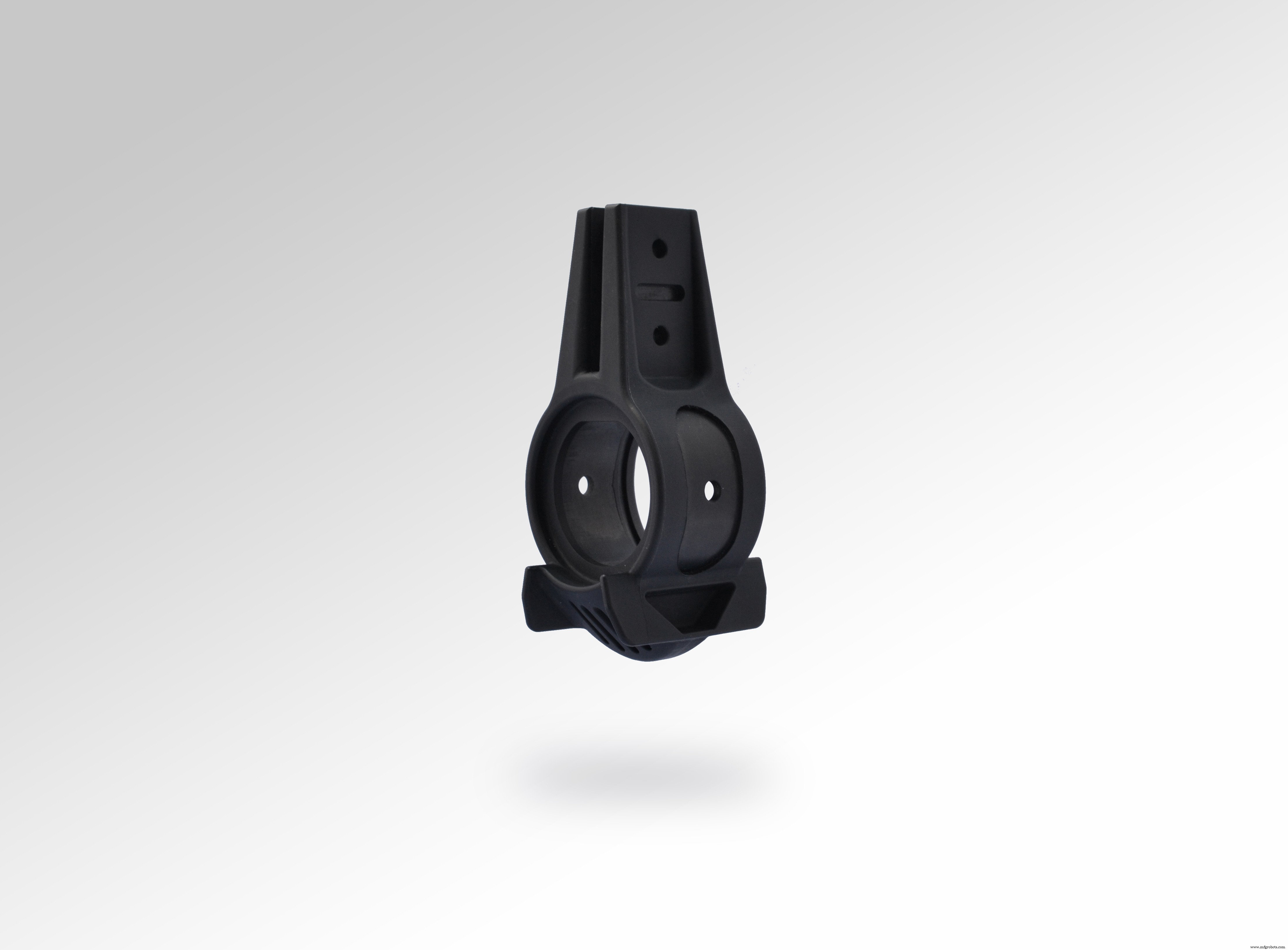
Stap 6. De laatste B-beugel wordt geproduceerd met een cyclustijd van drie minuten, een buy-to-fly-verhouding van 1,06:1 en een gewichtsbesparing van 30 tot 40%.
Kwalificeer en vlieg dan
Door gebruik te maken van het vermogen van SFS intec om kwalificatie uit te voeren, zijn de twee bedrijven doorgegaan met certificering door middel van "puntontwerp", wat betekent dat alleen deze specifieke onderdeelgeometrie vluchtgoedkeuring krijgt. Onderdelen zijn geproduceerd en onderworpen aan de tests die in het kwalificatiedocument zijn beschreven. "Aangezien het onderdeel een beugel voor een bovenliggende bak is, zijn de operationele belastingen vrij eenvoudig te bereiken", merkt Sourkes op. "De prestatie-eisen gaan echter verder dan die typische belastingen en moeten enkele extreme start- en landingsmanoeuvres dekken." Als CW gaat naar de pers, het kwalificatiepakket is ingediend en wacht op definitieve ondertekening door de specificatiebewaarder. TxV en SFS intec verwachten dat het onderdeel begin 2020 zal vliegen.
Zodra de B-beugel is gekwalificeerd, wordt TxV opgeschaald naar productievolumes. Hoewel het bedrijf zijn bestaande hybride overmolding-lijn gebruikt om deze beugels te produceren, benadrukt Sourkes dat het bedrijf een tweeledig mandaat heeft:zowel om onderdelen met de technologie te maken als om industriële fabrikanten te ondersteunen die geïnteresseerd zijn in het zelf toepassen van de technologie. Met andere woorden, composietfabrikanten kunnen deze fabricagetechniek toepassen in hun eigen faciliteiten.
Samengestelde beugels zoals het SFS intec-product hebben het potentieel om een vrij grote markt voor dit soort componenten over te nemen. Commerciële vliegtuigen gebruiken duizenden beugels en systeembevestigingen, wat verantwoordelijk is voor aanzienlijke kosten en gewichtsbijdragen aan het totale vliegtuig. “We zijn ervan overtuigd dat componenten van thermoplastisch composiet een steeds grotere rol zullen spelen bij de fabricage van vliegtuigen”, anticipeert Costabel.
vezel
- MMF #5:een gids voor het insluiten van componenten in 3D-geprinte onderdelen
- Een revolutionaire nieuwe manier om metalen onderdelen te vervaardigen
- Introductie van ons nieuwe Markforged-materiaal:Onyx
- AT&T, Tech Mahindra werken samen aan nieuw open source AI-platform
- LANXESS neemt twee nieuwe productielijnen in gebruik voor Tepex thermoplastische composieten
- Versnelling van thermoplastische composieten in de ruimtevaart
- Een nieuwe definitie van composieten?
- Nèos International vestigt nieuw hoofdkantoor, composietenfaciliteit in het VK
- Hoe precisie-mechanische componenten te vervaardigen
- Componenten met hoge precisie begrijpen
- Onderdelen en componenten Afwerking