Consumentenelektronica:hybride composiet hoezen
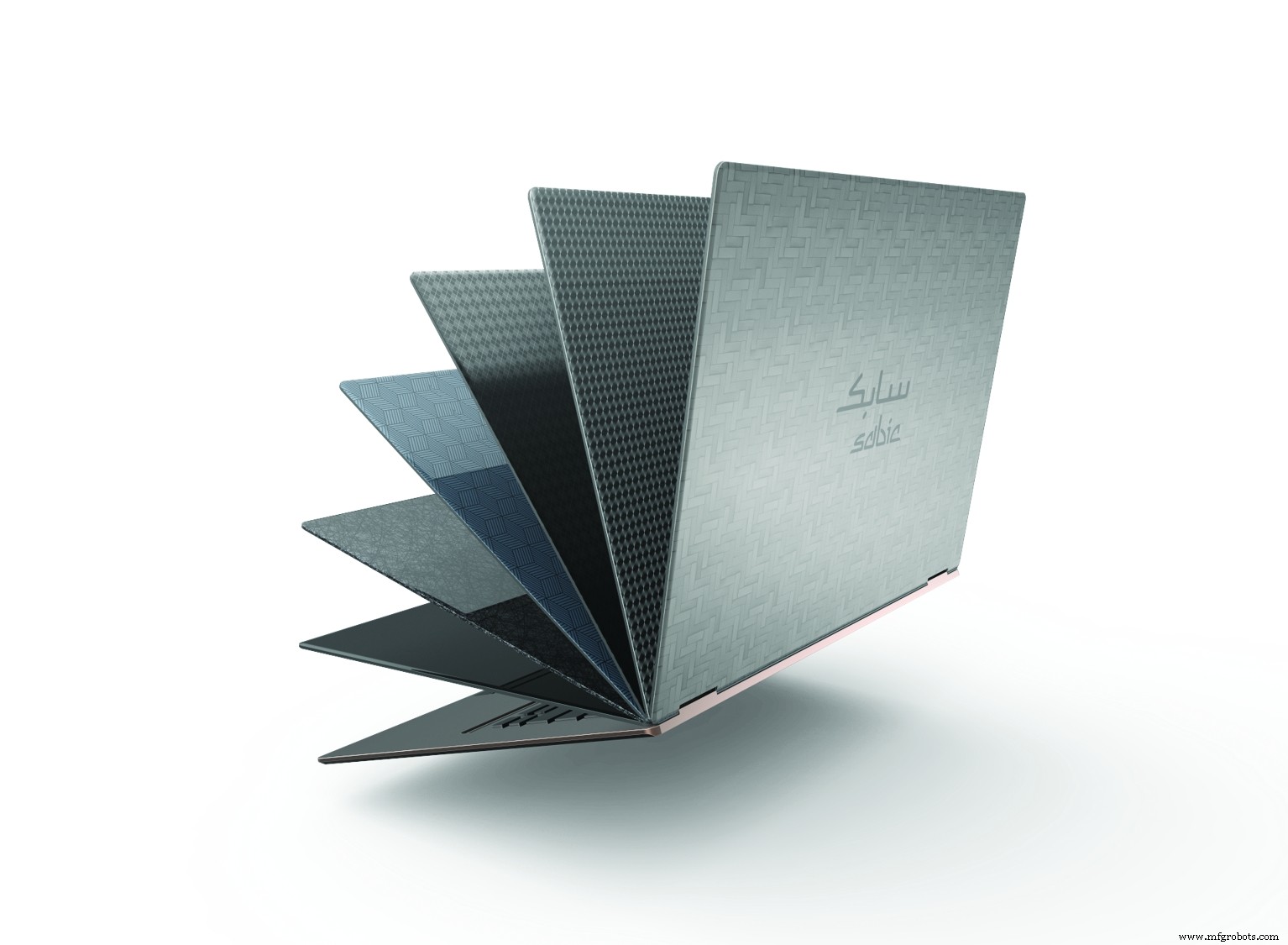
SABIC heeft in een recent onderzoek aangetoond dat een 1 millimeter dikke hoes zou kunnen voldoen aan alle relevante industriële prestatiespecificaties voor zeer dunne notebooks of tablets. Bron, alle afbeeldingen | SABIC
Consumentenelektronica is een dynamische markt met vrij korte cyclustijden tussen productgeneraties. Van hun smartphones, smartwatches, tablets en notebooks/laptops willen consumenten hogere werksnelheden, batterijen die langer meegaan, meer duurzaamheid en meer functies tegen lagere kosten en minder gewicht. Om aan de vraag van de consument te voldoen, vragen OEM's leveranciers om materialen met een hoge esthetiek en ontwerpvrijheid, uitstekende slagvastheid en hoge stijfheid - wat kwaliteit in deze markt impliceert - bij een laag gewicht en dunne wandsecties. Ze willen ook kosteneffectieve, zeer herhaalbare verwerkingsmethoden die jaarlijks in de tientallen miljoenen eenheden aan de wereldwijde productievraag voldoen. Deze druk heeft de markt eerst naar lichtgewicht metalen voor afdekkingen/koffers en frames geduwd, en nu naar metaal/composiet en volledig composietoplossingen.
Een haalbaarheidsstudie uitgevoerd door SABIC (Bergen op Zoom, Nederland) omvatte het gebruik van twee soorten thermoplastische composieten om een 1 millimeter dikke notebook-computer/tablethoes te produceren. Het onderzoek toonde aan dat het hybride thermoplastische composietontwerp een haalbare oplossing zou kunnen zijn voor de uitdagende markt voor consumentenelektronica.
Testcase
Sinds 2012 heeft SABIC een reeks investeringen gedaan om zijn eigen unidirectionele (UD)-vezelversterkte thermoplastische composiettapes te ontwikkelen (zie "Evolueren naar continue vezelversterking"), waardoor de kerncompetentie van het bedrijf op het gebied van injectie met korte vezels en lange vezels is uitgebreid. vezelthermoplastische (LFT) materialen, en stelde SABIC in staat om uit te breiden naar hoogwaardigere thermoplastische composieten. In 2015 kocht het bedrijf een meerderheidsaandeel in tapemaker Fiber Reinforced Thermoplastics BV (FRT, Lelystad, Nederland) en in 2017 ging het een partnerschap aan met en werd een minderheidsinvesteerder in Airborne (Den Haag, Nederland), een machinemaker en ontwikkelaar van composietverwerking lijnen.
Als SABIC en Airborne technologie hebben ontworpen en gebouwd om snel en kosteneffectief netvormige, hoogwaardige thermoplastische tape-gebaseerde laminaten te produceren voor echt grote volumes (zie "Hoge snelheid, high-rate thermoplastische composieten productie"), het team ging op zoek naar een testcase. Deze demonstrator zou een belangrijk marketinginstrument zijn om ontwerpconcepten te bewijzen voor thermoplastische composietlaminaten die zijn gemaakt van composiettapes die zijn overgoten met discontinue vezelversterkte verbindingen. Het zou ook belangrijk zijn om voorspellende engineeringtools te testen die het team had ontwikkeld voor zowel materiaaltechnologieën als om het snelle productieproces dat zich in Nederland ontwikkelt te demonstreren.
"We hebben besloten ons te specialiseren in toepassingen voor consumentenelektronica", legt Gino Francato, wereldwijd leider op het gebied van composieten van SABIC, uit. “Die markt is erg interessant omdat er een echte ambitie is om over te stappen op lichtgewicht materialen om onze mobiele telefoons en notebooks lichter en dunner te maken. En aangezien ze er miljoenen en miljoenen van maken, hebben we besloten de uitdaging aan te gaan die deze markt bood.”
“We besloten te beginnen met iets dat redelijk complex was, maar niet te complex”, legt Scott Davis uit, SABIC-stafwetenschapper voor wereldwijde toepassingstechnologie. De bovenklep van een zeer dunne notebookcomputer of zelfs een tablet - waarvan het team hoopte dat deze uiteindelijk zou worden vertaald naar smartphonecomponenten - leek een goede plek om te beginnen. "We werkten met een eenvoudige algemene geometrie, een rechthoek, die nog steeds een hoge esthetiek moest behouden en veel complexiteit moest bieden aan de B-kant, inclusief bevestigingsfuncties", vervolgt Davis. “We moesten de hoes erg dun houden, maar toch voldoen aan de uitdagende doorbuigingseisen die in de branche gebruikelijk zijn. En natuurlijk moesten we een zeer consistent product leveren via een complex nieuw productieproces.”
Omdat ze niet met een echt klantontwerp werkten en alleen de beschermhoes voor een scherm creëerden, gebruikten ze generieke geometrie. Davis merkt zelfs op dat toen ze begonnen met het snijden van injectiegereedschap voor interne ontwikkeling, ze niet eens zeker wisten of ze een hoes voor een tablet of een notebook zouden maken, dus de hoes was ontworpen om voor beide te werken. "Er waren veel uitdagingen om een composietoplossing klaar te maken voor grootschalige productie", voegt Davis toe. "In feite gebeurde er veel tegelijkertijd - tape-ontwikkeling, laminaatontwikkeling en procesontwikkeling - en we konden niet wachten tot al die dingen waren afgerond om met onze tooling te beginnen, en zo kwamen we bij dat ontwerp terecht." Toen het basisontwerp voltooid was, concentreerde het team zich op andere details, zoals de beste manier om de poort te openen, welke soorten overlappingen nodig waren tussen het laminaatinzetstuk en de overmolding compound, hoe om te gaan met geautomatiseerde plaatsing in het gereedschap, hoe om te gaan met de coëfficiënt van ( lineaire) thermische uitzetting (CLTE of CTE) mismatch tussen de twee composieten en hoe u een gemakkelijk herhaalbaar onderdeel kunt maken.
Voldoen aan uitdagende vereisten
Het doel was om een bovenlaag van 1 millimeter dik te ontwikkelen die een hoge stijfheid biedt en aan alle prestatie- en esthetische eisen voldoet — met name de doorbuigingstest op het middelpunt regelmatig toegepast op laptophoezen om de belasting te evalueren die nodig is om het onderliggende scherm te beschadigen. De vereisten voor belasting/doorbuiging verschillen per OEM, apparaat en model, maar doorgaans is er niet meer dan 3-5 millimeter doorbuiging toegestaan bij een druk van 40-120 Newton — een situatie die de belasting simuleert die wordt uitgeoefend door een vinger of elleboog die in de hoes wordt gedrukt als een menselijke gebruiker staat op. In veel industrieën zou de strategie om voor dergelijke tests te slagen zijn om de sectiedikte te vergroten, maar deze markt hecht waarde aan dunnere ontwerpen die ruimte vrijmaken voor grotere batterijen en andere componenten zonder de grootte of het gewicht van het apparaat te vergroten. Daarom moest het team een andere ontwerpstrategie gebruiken om schermschade te voorkomen, namelijk het selecteren van stijvere materialen (via een laminaatinzet) en het gebruik van geometrie (bijvoorbeeld ribbels via spuitgieten). Maar eerst moesten ze materialen specificeren.
Een van deze materialen, polycarbonaat (PC), wordt in deze industrie al veel gebruikt voor afdekkingen en andere componenten, vanwege de uitstekende esthetiek en hoge slagvastheid. De grootste zwakheden van het polymeer zijn de chemische resistentie en het krassen op het oppervlak, maar de coating, verf of combinaties van beide die op de meeste bekledingen worden aangebracht, overwinnen deze potentiële problemen over het algemeen.
"Omdat ultralichte computers zo dun zijn, is de verpakkingsruimte binnenin een echte premium, dus doorbuigingen en mechanica worden echt cruciaal", merkt Francato op. "Terwijl je vanuit kostenoogpunt glas [versterking] zou willen gebruiken, moesten we koolstof [vezel] gebruiken om de stijfheid te krijgen die we nodig hadden." Als gevolg hiervan waren alle geëvalueerde op tape gebaseerde laminaten variaties van met koolstofvezel versterkt polycarbonaat - kwaliteiten die toen in ontwikkeling waren met SABIC-dochteronderneming FRT.
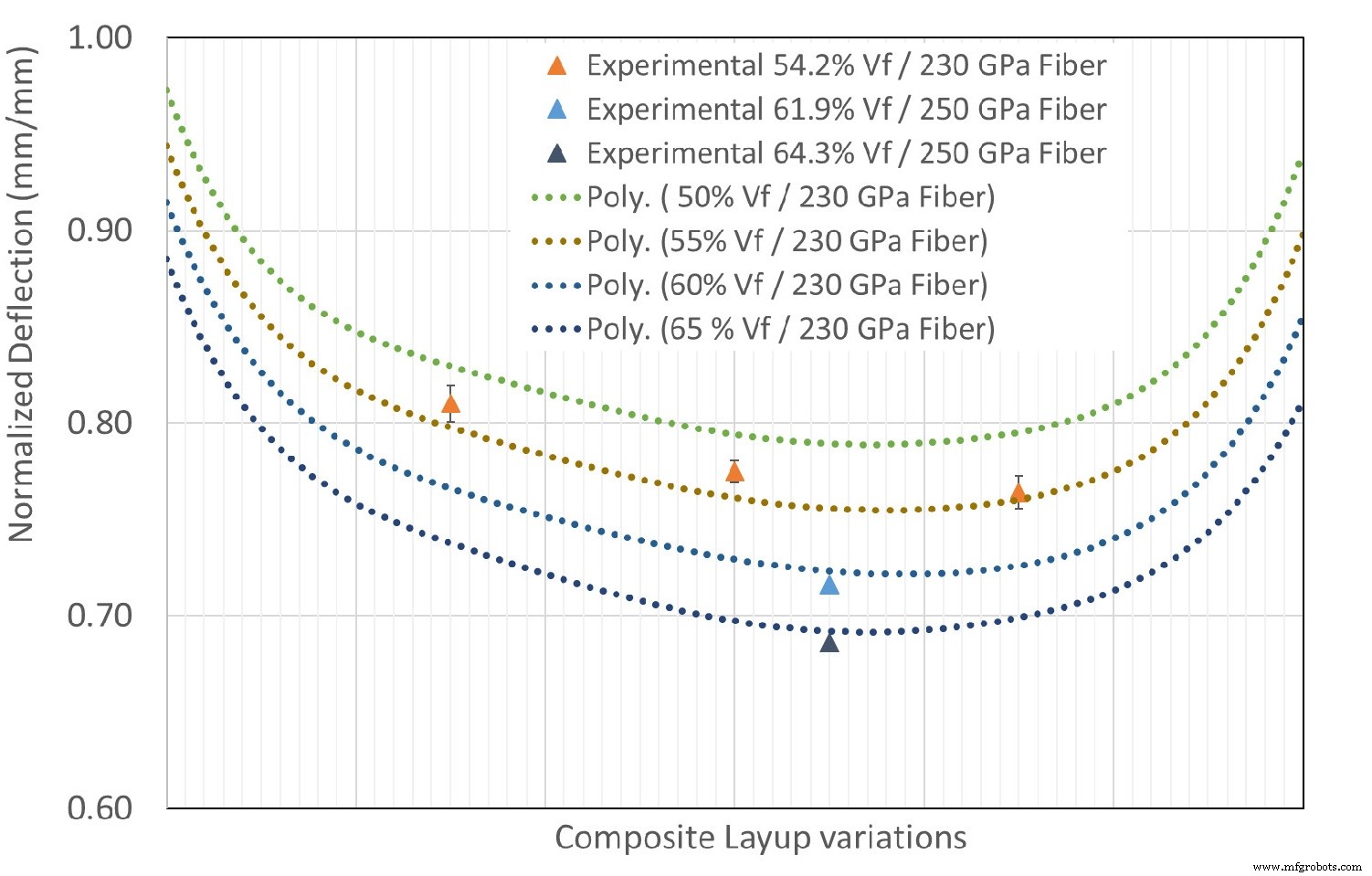
SABIC heeft voorspellende modellen ontwikkeld om het laminaattype en de architectuur (met en zonder overmolding-verbindingen) versus de prestaties van gegoten onderdelen te simuleren en rapporteert dat er een sterke correlatie is tussen voorspellingen en experimentele resultaten. De voorspellende engineeringtools zouden de materiaalontwikkeling versnellen.
De overmolding compound vereiste een andere aanpak. Aanvankelijk was de strategie om een LFT-verbinding met langere vezels te gebruiken, maar om een aantal redenen - waaronder hoge esthetische vereisten, onderdeelgrootte en poortstrategie - voldeden korte-vezelverbindingen beter aan de projectvereisten. Een ander probleem was het type vezel dat moest worden gebruikt. "Korte koolstofinjectieverbindingen zijn erg moeilijk om mee te werken en hebben nog steeds een hoge esthetiek", vervolgt Francato, "dus voor ons overmolding-materiaal hebben we gekeken naar met korte glas versterkte soorten." SABIC-dochteronderneming LNP Engineering Plastics, Inc. (Exton, Pa., V.S.) biedt veel glasvezel/PC-kwaliteiten met een goede esthetiek en stijfheid die populair zijn bij OEM's van apparaten, dus het team richtte zich daarop.
Hoewel volledig amorfe pc's minder vatbaar zijn voor kromtrekken dan semi-kristallijne polymeren, maakte het team zich toch zorgen over CLTE-verschillen tussen de sterk versterkte en anisotrope UD-koolstofvezeltapes en de meer isotrope, discontinue overmolding-kwaliteiten van korte glasvezels bij lagere vezelbelastingen. "In zulke dunne muren is er heel weinig ruimte voor fouten, dus de kleine verschillen in CLT waren dingen waar we goed rekening mee moesten houden", legt Davis uit. “En dat gaat nog niet eens over alle normale zaken waar je mee te maken hebt bij spuitgieten, zoals poortlocaties, vulpatronen, pakkingdruk en breilijnen. Al deze factoren zijn gesimuleerd en geverifieerd met fysieke tests.”
Nadat de materialen waren gekozen, voerden SABIC-ingenieurs meerdere iteraties uit van het vullen van de mal, structurele analyse en kromtrekkingssimulatie om de laminaatlay-out, geometrie en materiaalcombinaties te evalueren om de stijfheid voor de belasting/doorbuigingstest te optimaliseren, plus andere prestatie- en kostenvereisten. Het bedrijf zegt dat het uitgebreide en nauwkeurige tools voor het modelleren van composieten heeft ontwikkeld (beschikbaar voor klanten en die werken in gemeenschappelijke structurele en verwerkingscodes) die snel laminaatarchitectuur, overmolding compound-samenstelling en verschillende verwerkings- en tooling-opties kunnen modelleren en simuleren in vergelijking met de prestaties van het gegoten onderdeel. Van deze tools wordt gezegd dat ze een sterke correlatie tussen voorspellingen en gemeten prestaties bereiken en ideaal zijn voor het versnellen van de ontwikkeling van aangepaste materialen.
Klaar voor primetime
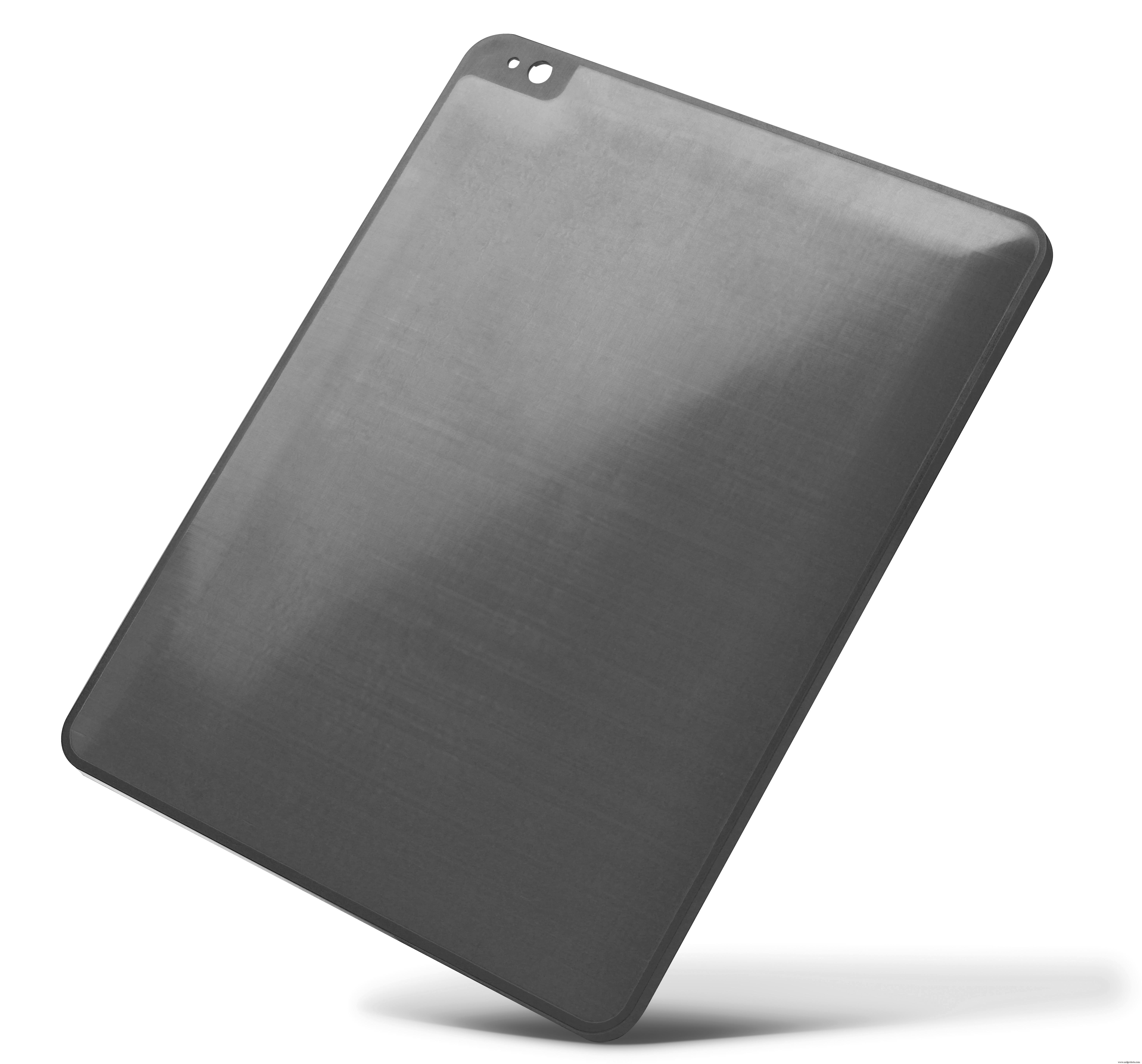
Voorkant van de uiteindelijke laptop/tablet hoes, die werd geproduceerd met behulp van een met koolstofvezel versterkt polycarbonaat tape-gebaseerd laminaat inzetstuk overgoten met korte glas/polycarbonaat-copolymeer verbinding, een combinatie die voldeed aan alle relevante mechanische en esthetische vereisten in een 1- millimeter dik onderdeel.
De laatste demonstrator is voorzien van een laminaat-inzetstuk dat is geproduceerd uit zeven lagen ontwikkelingsgerichte UDMAX-koolstofvezel/PC-tapes (55% vezelvolumefractie), vervolgens geconsolideerd, bijgesneden, voorgevormd en opnieuw bijgesneden tot de uiteindelijke netvorm, voordat het door spuitgieten wordt overgoten met 40% vezel -gewichtsfractie THERMOCOMP D452 korte glasvezel/PC-copolymeer (een kwaliteit geoptimaliseerd voor hoge vloei en hoge esthetiek en al veel gebruikt in dit segment). De combinatie levert een deksel op met een hoge stijfheid en sterkte bij een lage massa en sectiedikte, terwijl het talrijke 3D-ontwerpdetails, bevestigingsfuncties en een goede esthetiek bevat, waardoor het beste van elk materiaal wordt benut. De hoes heeft naar verluidt alle vereiste industriële tests doorstaan en wordt momenteel geëvalueerd door OEM's van apparaten.
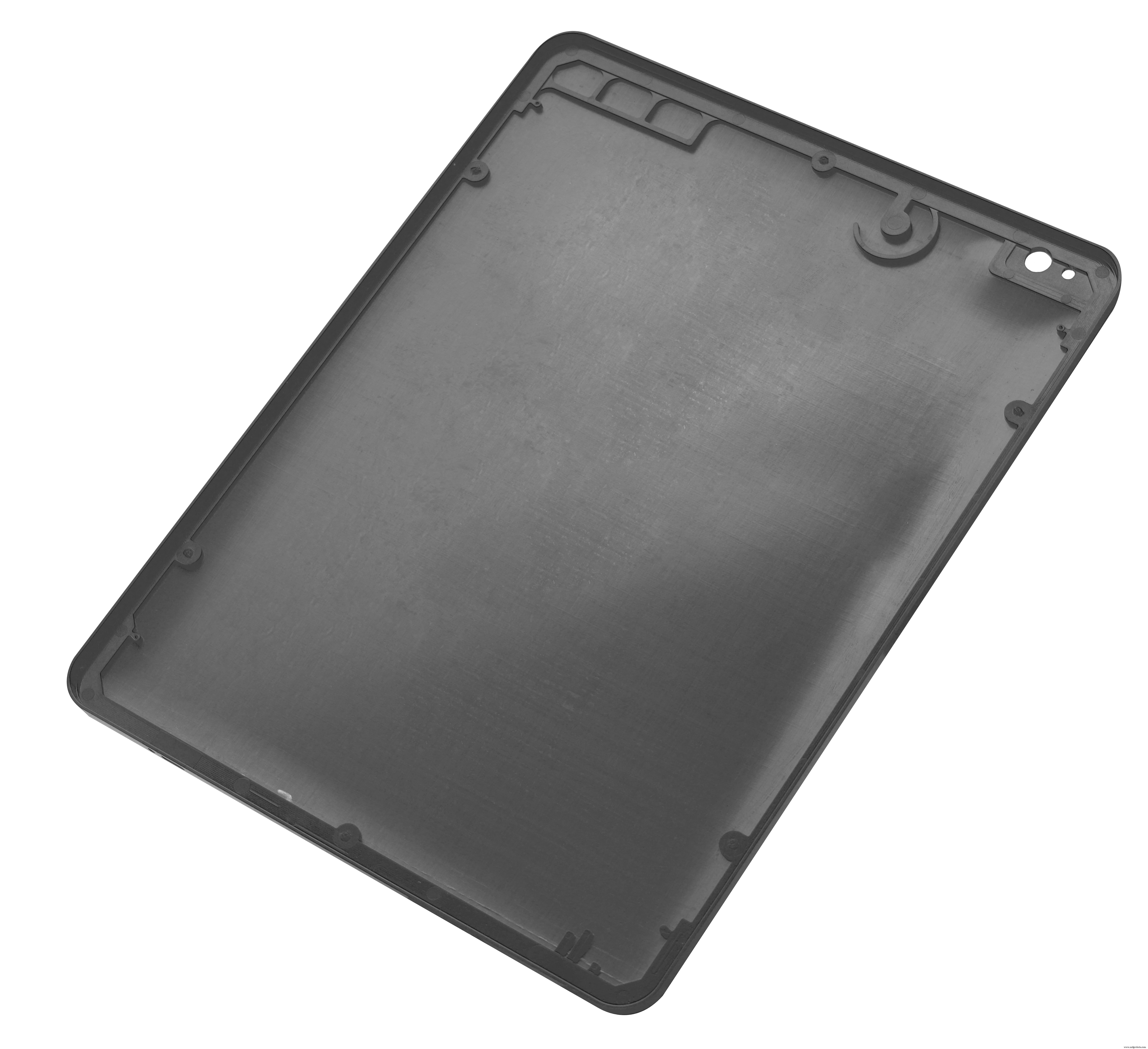
Achterkant van de afgewerkte omslag.
Het werk tussen Airborne en SABIC heeft ook zijn vruchten afgeworpen voor de doelstellingen van de markt voor consumentenelektronica van SABIC. De samenwerking werd aangekondigd in 2018, en dit jaar zijn er meer details gegeven over wat beide bedrijven hun Digital Composites Manufacturing Line noemen, die vier netvormige geconsolideerde laminaatinzetstukken kan produceren van thermoplastische composiettapes per minuut of 1,5 miljoen laminaten per jaar vanaf een enkele productielijn. Het systeem zou flexibel zijn (qua lay-outarchitectuur en materialen) en snel. Vanaf 2020 zal Airborne de lijn gebruiken voor de productie van laminaten voor commercieel gebruik in consumentenelektronica, waardoor het een hulpbron wordt waarvan beide bedrijven hopen dat het de penetratie van thermoplastische composieten in dit zeer competitieve en snelle segment aanzienlijk zal vergroten.
vezel
- Materialen:enkellaags flexibel grafiet voor consumentenelektronica
- Solvay breidt capaciteit thermoplastisch composiet uit
- Thermoplastisch wiel neemt de ruige weg
- Fraunhofer stelt geautomatiseerde Engel-productiecellen in gebruik voor R&D van thermoplastisch composiet
- Thermoplastische tapes blijven potentieel tonen voor composiet aerostructuren
- Avient lanceert vochtbestendig nylon lange vezel thermoplastisch composiet
- Wing of Tomorrow-ribben:One-shot, thermoplastische, OOA-consolidatie
- INEOS Styrolution gaat productielocatie bouwen voor StyLight thermoplastisch composiet
- Xenia introduceert CF/PP thermoplastische composietverbindingen
- NIAR's NCAMP kwalificeert TenCate thermoplastisch composiet
- Composiet + metaal:holle hybride technologie