De afgelopen vijf jaar vieren
Vorige maand vierden we dat het vijf jaar geleden is dat een handvol mensen in een garage de eerste 3D-printer van koolstofvezel ontwierp. We willen onze klanten bedanken voor hun bijdrage aan ons succes en het vertrouwen in ons in de afgelopen vijf jaar. Hier is het verhaal van hoe we begonnen, de early adopters die in ons geloofden, en hoe onze klanten het voor ons mogelijk maakten om door te gaan op het pad van innovatie.
The Mark One
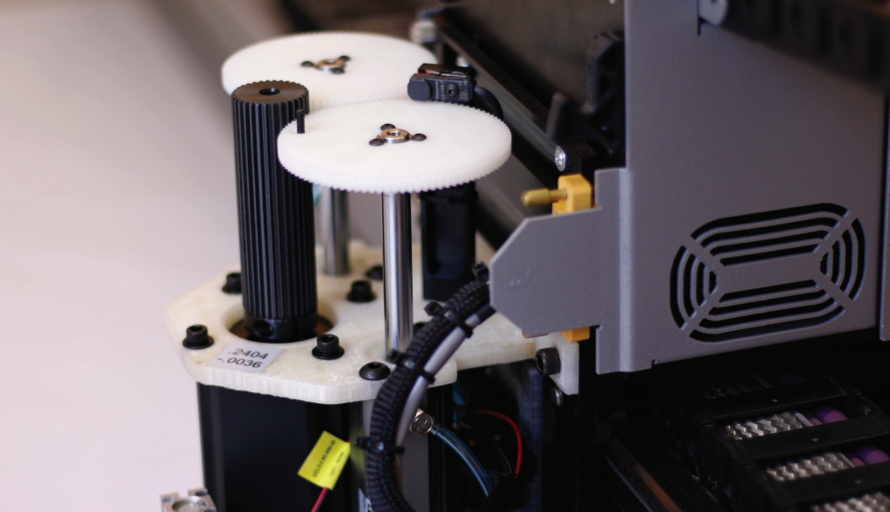
In januari 2014 debuteerden we op SolidWorks World met 's werelds eerste 3D-printer die kan printen in continue koolstofvezel:The Mark One. Autometrix geloofde in het concept en kocht een van de eerste Markforged printers.
Autometrie levert snijapparatuur en patroonsoftware voor een verscheidenheid aan industriële toepassingen, die voor alles worden gebruikt, van transport tot medische hulpmiddelen. Het bedrijf wilde prototyping in eigen huis brengen, maar ingenieurs "moesten ervoor zorgen dat de resultaten van het prototypingproces echt waren voor wat [ze] probeerden te ontwerpen", aldus Tyler Green, Electrical Engineer bij Autometrix. Nadat ze zich realiseerden dat het team een vezelversterkt onderdeel kon 3D-printen dat echt werkte op hun snijkop, werd het team verkocht op de Mark One.
Dat was nog maar het begin. Autometrix drukte vervolgens een hele snijkop af met de Mark One, en ingenieurs ontdekten dat de bedrukte snijkop een halve pond minder woog dan zijn aluminium tegenhanger. De lichtgewicht onderdelen die op de Mark One zijn gemaakt, waren bestand tegen alle impact die hun metalen tegenhangers en meer hebben, waardoor Green en andere ingenieurs bij Autometrix hun mechanische systemen konden verbeteren en uitbreiden.
The Mark Two
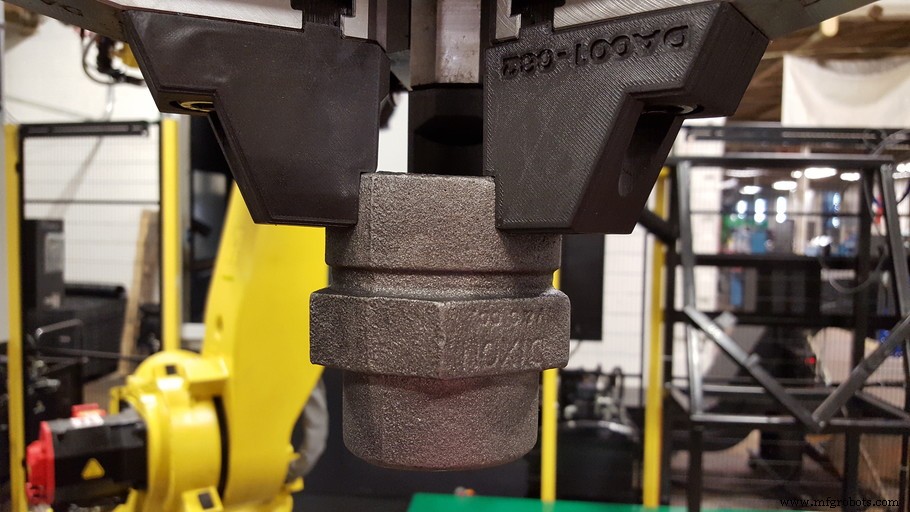
We lanceerden de Mark Two, de volgende generatie van de Mark One, in februari 2016. De Mark Two had een volledig opnieuw ontworpen composietprintsysteem dat sterkere en kwalitatief betere onderdelen mogelijk maakte dan zijn voorganger. Dixon Valve, fabrikant van fittingen en kleppen, had een printer nodig die onderdelen met een hoge sterkte kon maken, waardoor de Mark Two een groot potentieel voor het bedrijf zou kunnen zijn.
Dixon-klep was op zoek naar verbetering van zijn productielijnoplossingen. Ingenieurs Max de Arriz en J.R. Everett moesten in hun productieproces zeer sterke grijperbekken maken voor industriële robotarmen. De robotarm brengt verschillende onderdelen over tussen twee verticale draaicentra en het bedrijf wilde dat de kaken sterk, veilig en chemisch bestendig waren. Elke opstelling van een productlijn vereiste aangepaste apparatuur om specifieke onderdelen efficiënt vast te houden. Het bedrijf wist dat het een 3D-printer nodig had voor aanpasbare onderdelen, wat zijn ingenieurs naar de Mark Two leidde.
"Met de Mark Two waren we in staat om een robotarm in een productiecel in minder dan 24 uur om te bouwen", riep Everett uit. Dankzij de Mark Two kon Dixon Valve nieuwe productieoplossingen produceren met ongekende snelheid en kosten, waardoor het bedrijf een krachtig nieuw hulpmiddel in zijn gereedschapskist kreeg. Everett is van mening dat de Mark Two een cruciaal onderdeel is in het ontwerpproces van het bedrijf, en zegt:"het verandert de manier waarop we werken echt tot het punt waarop we onze procedures en plannen veranderen om dit baanbrekende product mogelijk te maken."
De introductie van Onyx
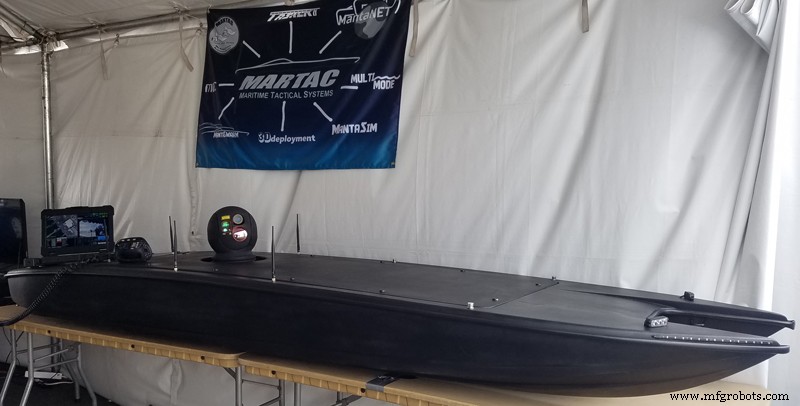
In 2016 lanceerden we Onyx, onze volgende generatie met composiet versterkte thermoplast die uniek geschikt is voor productieomgevingen. Omdat Onyx een zeer hoge thermische stabiliteit heeft, is het niet vatbaar voor kromtrekken. Het heeft superieure sterkte en stijfheid en is een zeer nauwkeurig materiaal met hoge herhaalbaarheid. Het was deze hoge precisie die MARTAC voor het eerst ertoe bracht om in Onyx te printen.
MARTAC (Maritime Tactical Systems) ontwerpt en produceert hoogwaardige onbemande watervaartuigen. Het bedrijf was op zoek naar geometrisch complexe inlaten die zouden kunnen helpen zeewater door koelkanalen te leiden. Door dit onderdeel in Onyx 3D te printen, kon MARTAC een complexe, aangepaste geometrie creëren die niet hoefde te voldoen aan subtractieve bewerkingsbeperkingen.
Onyx is nu het belangrijkste materiaal voor MARTAC-vaten. “Het leuke van het gebruik van de Onyx is dat het niet corrodeert door constant in zout water te zijn. Deze onderdelen hebben ook bewezen redelijk veerkrachtig te zijn met puin in het water”, zegt Ian Weaver, Operations Coordinator bij MARTAC. Door deze opnames te printen, werden de fabricagekosten voor het bedrijf drastisch verlaagd voor wat een ongelooflijk moeilijk te fabriceren onderdeel zou zijn.
Industrieel gaan
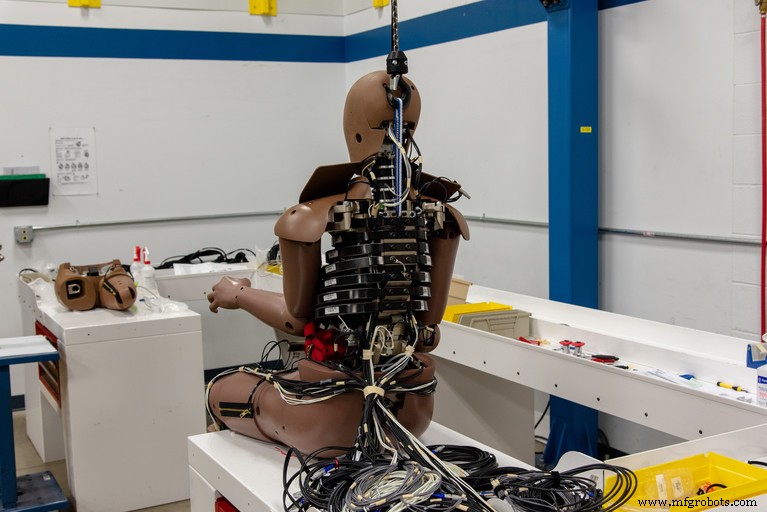
Met bijna drie keer het bouwvolume en een geavanceerde zelfcontrolesensorsuite, was de X7 onze eerste 3D-printer in industrieel formaat. Humanetics - 's werelds toonaangevende leverancier van crashtestdummies - had een nieuwe technologie nodig om het proces rond het vervangen van grote onderdelen te versnellen. De X7 was voor hen de perfecte oplossing.
Humanetiek ’ crashtestdummies worden gebruikt in de automobiel-, militaire en ruimtevaartindustrie. Geconfronteerd met het probleem dat de mallen te snel verslijten, was Humanetics op zoek naar een kosteneffectieve manier om duurzame onderdelen te maken die bestand zijn tegen hoge temperaturen. Kris Sullenberger, Design Engineer bij Humanetics, keek naar 3D-printmallen voor dummy-onderdelen voor crashtests en kwam de X7 tegen.
Humanetics heeft ergens tussen de vijf en tien mallen gedrukt en is van plan veel van de 150 mallen van het bedrijf te vervangen door Markforged-prints. Naast de voordelen op het gebied van kosten en duurzaamheid, ontdekte Kris dat bedrukte mallen betere onderdelen opleveren. Waar siliconen mallen naden en andere onvolkomenheden achterlaten, resulteert de precieze pasvorm van bedrukte mallen in een bijna perfect onderdeel. Van het printen van productie-crashtest-dummy-onderdelen voor zijn ontwerpteam tot het vervangen van massieve, verouderde armaturen voor assemblagetechnici, Humanetics laat bijna altijd de machine printen. Kris vindt het leuk hoe hij ervoor kan kiezen om "duizenden en duizenden dollars uit te geven om deze buiten te laten machinaal bewerken of produceren" of "ze in huis te doen voor letterlijk tientallen of honderden dollars."
Metaal X
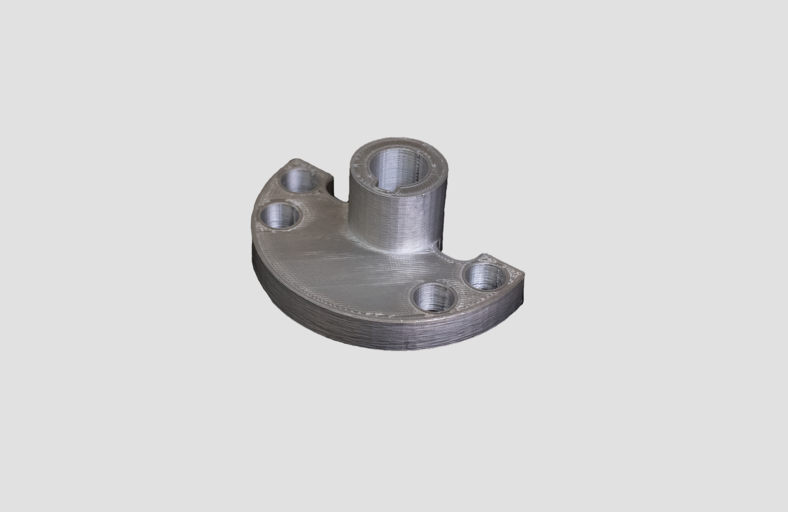
In het afgelopen jaar hebben we metaal 3D-printen aan onze productlijn toegevoegd in de vorm van de Metal X. De mogelijkheid om roestvrijstalen onderdelen te printen opent nieuwe mogelijkheden voor het printen van gelijkaardige vervangingen voor een breed scala aan productlijnen . Stanley Infrastructure nam de Metal X over om te onderzoeken hoe dure, op maat gemaakte onderdelen werden vervangen door goedkope bedrukte onderdelen.
Stanley-infrastructuur , een divisie van Stanley Black &Decker, is 's werelds grootste fabrikant van handbediend hydraulisch gereedschap. Het bedrijf had een onderdeel nodig om verstelbare geleidewielen vast te houden op een kikkermolen, die moeilijk te bewerken was. Ingenieurs kozen ervoor om wielassen uit een enkel blok staal te maken, maar door de diameter van de flens en de lengte van de as ging in elk onderdeel ~90% van het voorraadmateriaal verloren. Met de hulp van Markforged-ingenieurs heeft Stanley Infrastructure de wielas opnieuw ontworpen om een driedelige assemblage te zijn. Door een kant-en-klare as en spie aan te schaffen, kon het bedrijf de complexere flens eenvoudig op een Metal X printen. De nieuwe assemblage doorstond zowel de duurzaamheids- als de valproeven voor misbruik.
Volgens een ingenieur van Stanley Infrastructure Innovation, "is het zeer haalbaar om het Metal X-platform te gebruiken bij het additief vervaardigen van de besproken actuatorbehuizing met een zeer minimale kapitaal- en tijdinvestering." Sinds de aankoop van de printer heeft Stanley Infrastructure zich gericht op het printen van onderdelen van hoge kwaliteit, waardoor de bewerkingstijd tot een minimum is beperkt en de kosten zijn verlaagd.
Wat nu
Van Fortune 100-bedrijven tot familiebedrijven, duizenden bedrijven gebruiken Markforged-technologie om hun producten en processen te verbeteren. En net als deze bedrijven zijn we constant op zoek naar nieuwe manieren om onze producten en processen beter dan ooit te maken.
Op nog vele jaren innovatie van onze klanten!
Wilt u de kracht van onze printers testen? Vraag hier een gratis Markforged proefstuk aan .
Wilt u meer van dit soort berichten zien? Volg ons op Facebook , Twitter , Instagram , en LinkedIn voor meer updates!
3d printen
- Hoe 3D-printen zijn stempel drukt in de medische wereld
- 10 jaar Formlabs 3D Printing vieren
- Carl Calabria's gids voor het gebruik van inserts op de Mark One
- Hoe gebruik je de lijmstift op je Mark One Print Bed
- Amazon-Whole Foods:twee jaar na de deal
- Vijf manieren om een groenere laatste mijl te bereiken
- De vijf meest populaire bouwmachines
- 5G IoT-inkomsten stijgen de komende vijf jaar
- Digitale productie verdrievoudigt in twee jaar
- ProtoPompoenen door de jaren heen
- Bewerking, disruptie en de komende jaren