Koolstofvezel/epoxy voor massavermindering in auto's, massaproductie
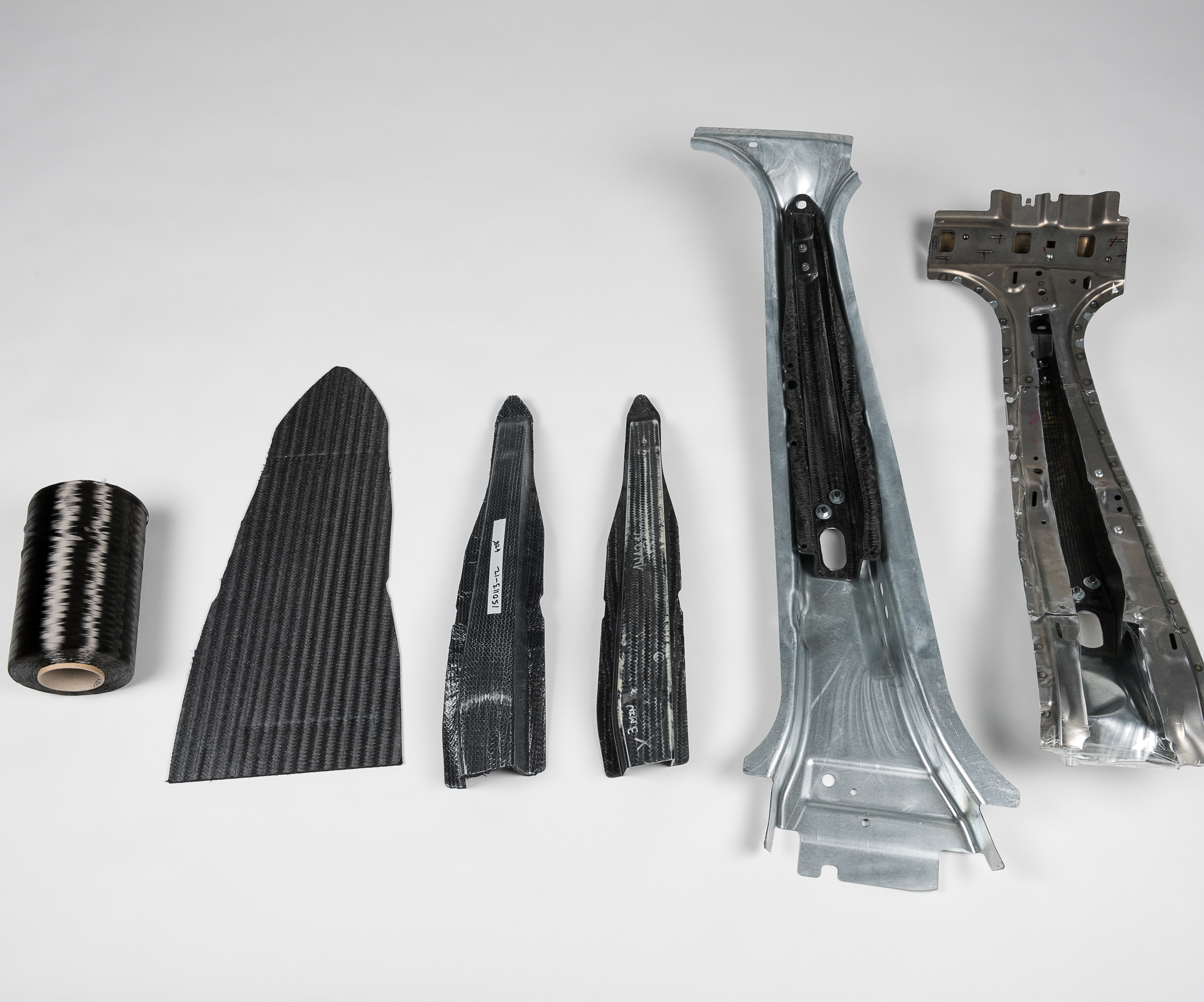
IACMI Project 3.2 evalueerde koolstofvezelversterkte composieten doordrenkt met een nieuw epoxyharssysteem om structurele composietonderdelen met complexe geometrie te ontwikkelen om metalen te vervangen in zwaarbelaste, veiligheidskritieke toepassingen op primaire carrosseriestructuren van passagiers met een groot volume voertuigen. Een van de eerste geëvalueerde toepassingen was het gebruik van een koolstofvezel/epoxy prepreg op de B-stijl van een testvoertuig. Het hoogwaardige prepreg-materiaal verminderde de massa direct met 3 kilogram en maakte een down-gauging van het omringende plaatwerk mogelijk, dat vervolgens in goedkopere legeringen kon worden gespecificeerd, wat extra gewicht en kostenbesparingen opleverde. Bron | Ford Motor Co.
Autofabrikanten in de meeste regio's worden geconfronteerd met uitdagende 2025-mandaten met betrekking tot verminderde uitlaatemissies en/of een lager brandstofverbruik voor personenauto's. Het ontwikkelen van fundamenteel nieuwe autotechnologie om aan deze vereisten te voldoen, is echter kostbaar, dus in veel landen worden consortia gebruikt om leden van de toeleveringsketen de kosten voor preconcurrentieel onderzoek te laten delen.
In de V.S. is een dergelijke organisatie het Institute for Advanced Composites Manufacturing Innovation (IACMI—The Composites Institute, Knoxville, Tenn., V.S.). Onder de initiatieven van de organisatie werken IACMI-leden uit de industrie, de academische wereld en de overheid aan meervoudige projecten - met geïntegreerde materiaal-/procesontwikkeling, modellering/simulatie, samenvoeging van meerdere materialen en recycling - om technische problemen op te lossen, de voertuigmassa te verbeteren en energie te verminderen verbruik en uitstoot, en nieuwe banen in de VS creëren.
Project 3.2 en het onmogelijke harssysteem
Project 3.2 was een van de eerste projecten die IACMI op zich nam toen het in juni 2015 werd opgericht, hoewel de technologie die in het project werd gebruikt, al een paar jaar vóór de oprichting van IACMI was begonnen, met een samenwerking tussen Ford Motor Co. (Dearborn, Mich. , VS) en wat toen Dow Automotive was (nu The Dow Chemical Co., Midland, Mich., VS). Toen IACMI werd opgericht en Project 3.2 begon, namen Ford en Dow hun eerdere werk aan een nieuw epoxyharssysteem in het programma op. Toen het eenmaal was aangesloten bij IACMI, werd het programma uitgebreid en omvatte het uiteindelijk verschillende fasen die nieuwe toepassingen voor deze innovatieve hars vertegenwoordigen:een prepreg B-stijl, een volledig plaatvormig dekdeksel (SMC) en een SMC/aluminium achterklep.
De harsfamilie, VORAFUSE genaamd, die door Dow voor Ford is ontwikkeld, is ontworpen voor gebruik in prepreg en SMC en voor verwerking op persgietapparatuur, die algemeen verkrijgbaar is in de Noord-Amerikaanse auto-industrie. Volgens de vereisten van Ford moet de glasovergangstemperatuur van de hars (Tg ) is 150-160°C, vormt het bij 145-155°C en hardt uit in minder dan 2 minuten bij 150°C (hoewel een uitharding van minder dan 1 minuut beschikbaar is), waardoor het snel genoeg is voor grote volumes ( 100.000-plus/jaar) voertuigproductie. Het bereikt een post-mold uitharding van meer dan 95%. Het systeem is vrij van oplosmiddelen en vluchtig-organische verbindingen (VOS).
"De CTQ's [critical-to-quality requirements] die door Ford zijn gedefinieerd, zijn uniek en zijn nog nooit eerder bereikt in een enkel commercieel product", legt Dave Bank, fellow, Dow Polyurethanes R&D uit. "Om deze reden waren nieuwe chemie en een groot aantal zeer niet-traditionele producten nodig om aan deze veeleisende specificaties te voldoen."
"De thermodynamische scheiding van houdbaarheid en polymerisatie in het hars / curatieve mengsel levert een droge pasta op die in koolstofvezel kan worden gegoten zonder de uitharding te bevorderen en een droge, niet-kleverige vormmassa oplevert", voegt Bank eraan toe. "Toch, wanneer de vormomstandigheden 150°C bereiken, is de chemie 'heet' en gaat de uitharding snel vooruit." Dow heeft 21 octrooiaanvragen ingediend en heeft tot nu toe vier voor de technologie gekregen.
Extra functies van het VORAFUSE-systeem:
- Het is meer dan 50 dagen houdbaar bij kamertemperatuur, maar kan snel worden uitgehard bij of boven 150°C. Het vereist geen vriezeropslag voorafgaand aan het snijden en vormen van de kit, zolang de opslagtemperatuur niet hoger is dan 40°C.
- De kleefvrije chemie is ideaal voor geautomatiseerde verwerking. Omdat het de plakkerigheid van traditionele prepreg mist, veroorzaakt het geen opbouw en gerelateerde problemen met robots en andere geautomatiseerde apparatuur.
- Het bevat een nieuw IMR-middel (Internal Mould Release), zodat verwerkers 1000 onderdelen kunnen vormen voordat ze externe lossingsmiddelen op gereedschapsoppervlakken moeten aanbrengen. Epoxy is normaal gesproken in tegenspraak met IMR omdat het zo'n effectieve lijm is voor metalen.
- Niet-uitgehard product kan worden gerecycled tot hoogwaardige onderdelen door materiaal te hakken en terug te voeren naar vormsystemen als een discontinue vezelversterkte verbinding die ideaal is om complexe geometrieën zoals ribben/nokken te vormen. In tegenstelling tot conventionele epoxy prepreg en SMC, kan al het niet-uitgeharde schroot worden hergebruikt, waardoor het materiaal duurzamer wordt en schrootverliezen worden bespaard die de onderdeelkosten verhogen.
Fase 1:Prepreg B-pijler
Nadat VORAFUSE in Project 3.2 was gebracht, begon IACMI te werken aan een automobieltoepassing die Fase 1 van het totale project zou worden. Tot de teamleden behoorden Ford, Dow, DowAksa US LLC (de in Tucson, Az., VS gevestigde tak van DowAksa BV, een 50/50 joint venture tussen Dow Chemical en Aksa Akrilik Kimya Sanayii A.Ş., Çiftlikköy-Yalova, Turkije); Michigan State University (East Lansing, Michigan, VS); Purdue University (West Lafayette, Ind., VS); Universiteit van Tennessee-Knoxville (Knoxville, Tennessee, VS); Continental Structural Plastics (CSP, Auburn Hills, Mich., V.S.); en Oak Ridge National Laboratory (Oak Ridge, Tenn., V.S.).
In de eerste fase ontwikkelden onderzoekers continue (gevlochten en niet-knijpstof) koolstofvezelversterkte prepreg geïmpregneerd met de epoxy. VORAFUSE P6300-hars is geformuleerd voor compatibiliteit met DowAksa A42 D012 24K koolstofvezel met standaardmodulus. Het doel van het team was om de prepreg van koolstofvezel/epoxy te gebruiken om structurele composietonderdelen met complexe geometrie te ontwikkelen ter vervanging van gestempeld metaal in zwaarbelaste, veiligheidskritieke toepassingen op primaire carrosseriestructuren van voertuigen met een groot volume.
Voor de technologiedemonstrator, de B-stijl aan één kant van een Ford Fusion testvoertuig werd gebruikt. De levensvatbaarheid werd eerst geëvalueerd via simulatie en vervolgens werden fysieke onderdelen gegoten en onderworpen aan alle vereiste tests, inclusief volledige voertuigongevallen. Onderdelen slaagden met vlag en wimpel, waardoor de massa met 3 kilogram per kant werd verminderd in vergelijking met gevestigde metalen. Niet-uitgehard schroot werd gerecycled om de complexe ribstructuren van de pilaar te vormen. Het hoogwaardige composiet maakte het mogelijk om het omringende plaatwerk te verkleinen, dat vervolgens kon worden gespecificeerd in goedkopere legeringen, wat extra gewichts- en kostenbesparingen opleverde.
Nadat het materiaal aan alle vereisten van Ford had voldaan, was het eerste commerciële gebruik van het materiaal voor een dakkop aan de voorkant en een close-outpaneel voor de vloer op de koolstofcomposiet-intensieve Ford GT superauto.
Het is niet verrassend dat de koolstofvezel/epoxy prepreg een hogere prijs met zich meebrengt, dus het is het beste voor voertuigen met aanzienlijke massaverminderingsmandaten die een premie kunnen betalen voor aanzienlijke gewichtsbesparingsmogelijkheden.
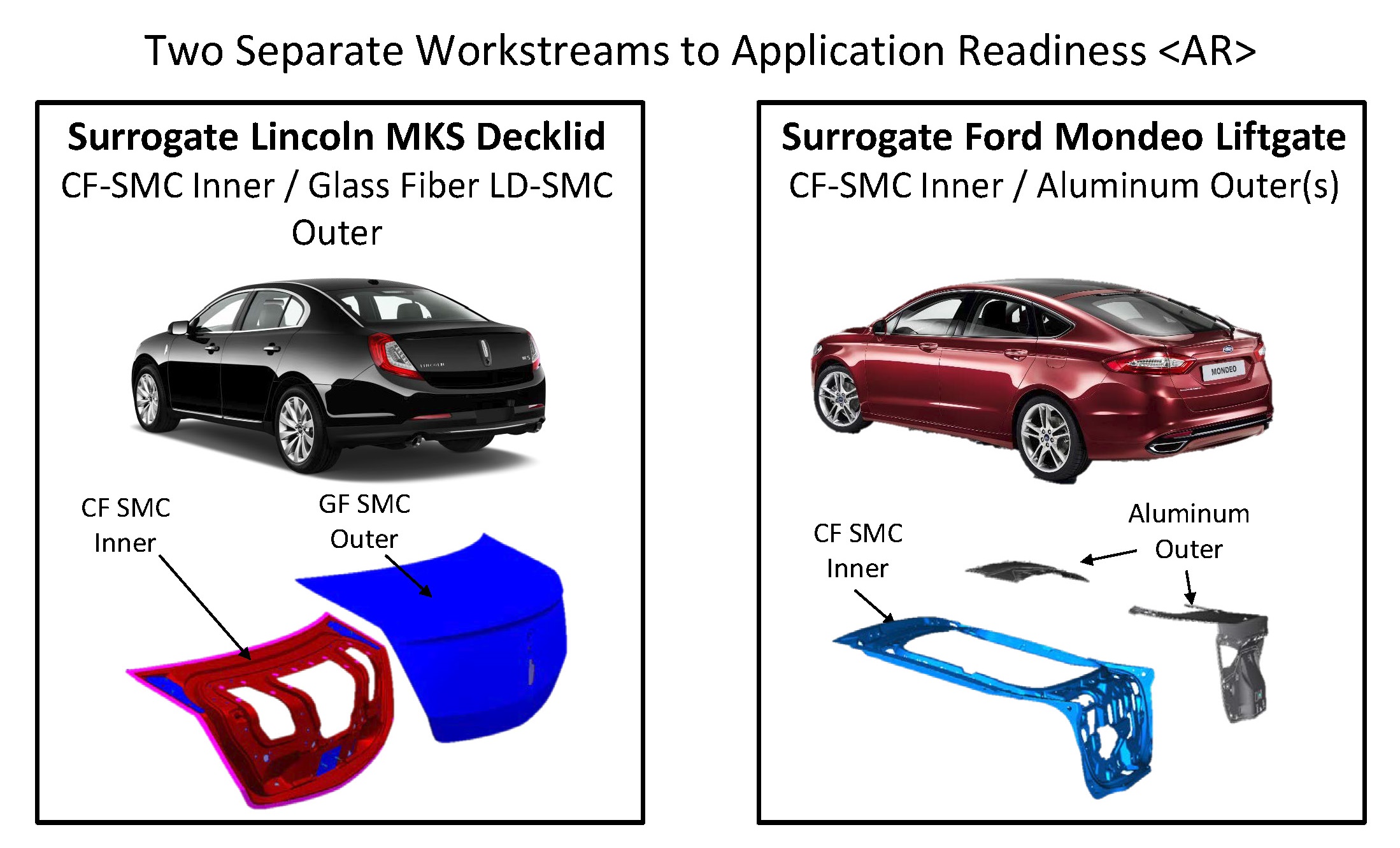
Fase 2/Workstream 1:All-SMC decklid
Voortbouwend op de prepreg-successen, onderzochten projectonderzoekers vervolgens discontinue koolstofvezelversterkte SMC met de nieuwe epoxyhars in complexe 3D-structuren met veiligheidskritieke functies. In één demonstrator werd de koolstofvezel/epoxy SMC gebruikt als het binnenste/structurele paneel van een verlijmd dekdeksel (kofferdeksel), en in een andere demonstrator werd het gebruikt voor het binnenste/structurele paneel van een veel grotere en complexere verlijmde achterklep ( achterklep/deur met ruit, ruitenwissermotoren, verlichting, enz.). In beide werkstromen bleven de oorspronkelijke ontwerpbeperkingen, hardware, verbindingstechnieken en structurele lijmen ongewijzigd. Er werden uitdagende mechanische doelen gebruikt met een treksterkte van meer dan 300 MPa en een trekstijfheid van meer dan 40 GPa - vergelijkbaar met het bestaande gegoten magnesium en aluminium. SMC had ook een hogere stroom nodig dan prepreg, dus werd een iets andere kwaliteit ontwikkeld, de VORAFUSE M6400.
Voor de decklid-demonstrator, die een stapsgewijze vooruitgang betekende ten opzichte van de huidige glas/SMC-technologie, verving de koolstofvezel/epoxy SMC conventionele structurele glasvezelversterkte onverzadigde polyester SMC voor een decklid-binnenkant op een Lincoln MKS prototype voertuig. Het koolstofvezel/epoxy SMC-binnenpaneel was gebonden aan een SMC-buitenpaneel met lage dichtheid (LD, 1,25 SG) glasvezel/polyester, dat een gevestigde SMC-glasvezel/polyester met standaarddichtheid (1,9 SG) verving. Zowel oude als nieuwe buitenpaneelmaterialen waren Klasse A-compatibel. Het originele gereedschap werd hergebruikt om zowel de koolstofvezel/epoxy SMC-binnenpanelen als de glasvezel/polyester-buitenpanelen te vormen. Krimp — hoewel enigszins verschillend tussen beide harssystemen — was dichtbij genoeg om geen problemen met de pasvorm en afwerking te veroorzaken (met andere woorden, er werden geen significante dimensionale veranderingen waargenomen).
Virtuele prototyping onderwierp de gelijmde assemblage aan een aantal uitdagende belastingsgevallen, waaronder torsiestijfheid, stijfheid van de voorhoeken, watervaldoorbuiging en vergrendelingsbelastingen. Tientallen binnen- en buitenpanelen werden vervolgens gegoten, gelijmd en getest - inclusief uitdagende aanrijdingen van achteren met een snelheid van 89 kilometer per uur. Assemblies hebben zowel virtuele als fysieke tests zonder problemen doorstaan.
Deklidmassa werd met 30% verminderd (van 10,5 naar 7,33 kilogram) ten opzichte van de benchmark. Als de budgetten het echter mogelijk hadden gemaakt om het binnenpaneel opnieuw uit te werken - dat dunner had kunnen worden ontworpen gezien de hogere mechanische prestaties in vergelijking met de bestaande - dan hebben onderzoekers berekend dat de massa met minstens 35% had kunnen worden verminderd met wanden van 2 millimeter, en zelfs verder met muren van 1,5 millimeter.
De koolstofvezel/epoxy SMC voldeed aan alle Ford-vereisten en kan nu worden gebruikt op commerciële platforms, hoewel de kosten hoger zouden zijn dan bij conventionele glasvezel/polyester SMC.
Fase 2/Workstream 2:SMC/aluminium achterklep
Voor het laatste project kozen onderzoekers voor een werkelijk uitdagend scenario:het vervangen van lichtgewicht metaal door koolstofvezel/epoxy SMC om een hybride (metaal/composiet) gebonden assemblage te produceren voor grotere en complexere laadkleppen op Ford Mondeo vijfdeurs/hatchback-testvoertuigen. Om veranderingen in de bouwvolgorde van voertuigen tot een minimum te beperken, hebben onderzoekers het samenstel ontworpen om te worden toegevoegd aan de body-in-white (BIW) voorafgaand aan de elektroforetische roestcoating (e-coat) en de bijbehorende verfbakcycli.
Koolstofvezel / epoxy SMC verving magnesium voor structurele / binnenpanelen die waren gebonden aan bestaande aluminium buitenpanelen. Omdat er nieuwe gereedschappen moesten worden gemaakt om het composietpaneel te produceren, werd het onderdeel opnieuw ontworpen. De dikte van het paneel werd gevarieerd op basis van de vereisten voor stijfheid/sterkte en om ribbels toe te voegen. Er werden ook metalen versterkingen gebruikt in bevestigingsgebieden met hoge belasting voor gasveren, grendels, scharnieren en sloten, die het composietpaneel allemaal wat dikker maakten - iets dat de verpakkingsruimte toestond.
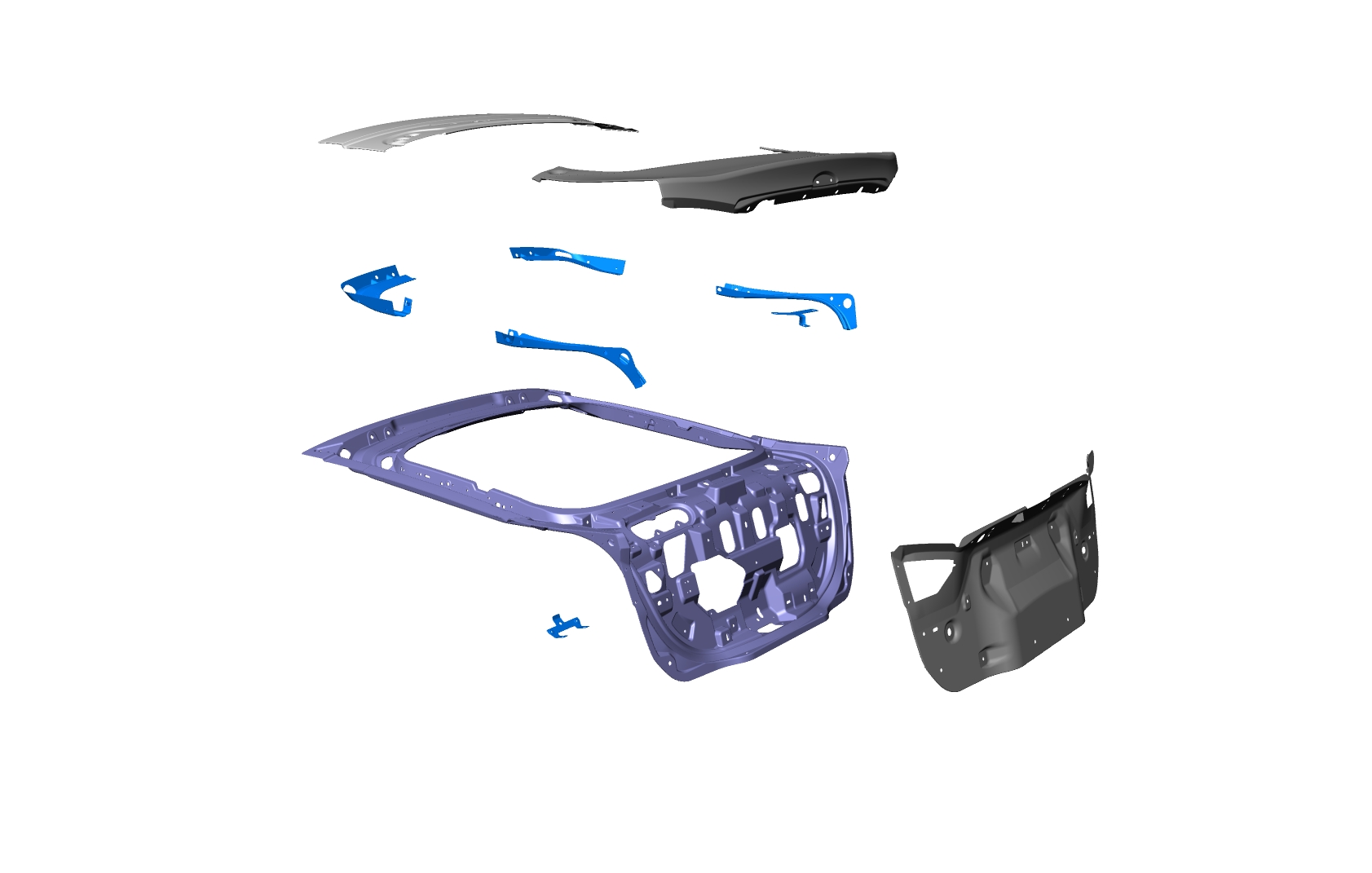
Een explosietekening van de SMC/aluminium achterklep (met metalen hardware) voor de vijfdeurs/hatchback-versie van de Ford Mondeo. Bron | Ford Motor Co.
Deze uit meerdere materialen bestaande assemblages werden onderworpen aan hoge eisen, waaronder torsie- en buigbelastingen, zijdelingse stabiliteit, corrosieweerstand, duurzaamheid op lange termijn en crashtests aan de achterkant. Ze moesten ook voldoen aan strenge eisen op het gebied van maatvastheid met betrekking tot marges en vlakheid.
Hoewel het hybride systeem gemakkelijk aan de meeste eisen voldeed, waren er problemen met de pasvorm en afwerking als gevolg van de coëfficiënt van lineaire thermische uitzetting (CLTE)-mismatches tussen composiet binnenpanelen en aluminium buitenpanelen, wat leidde tot restspanningsopbouw in verlijmde verbindingen en paneelvervorming na afkoeling omlaag. Daaropvolgend werk met het simulatieteam van Purdue University was gericht op het verbeteren van de voorspellingen van modulus, sterkte en uithardingskinetiek voor de 1K epoxylijm (gekozen vanwege zijn vermogen om e-coat-temperaturen te overleven) in de hoop een lijm te reverse-engineeren die beter zou werken. Warpage werd een orde van grootte verminderd, maar miste het doel enigszins. Er zijn verschillende oplossingen mogelijk:een 2K/kamertemperatuur-uithardende of inductie-uithardende lijm zou kunnen worden geprobeerd of een nieuwe hoge-temperatuurlijm zou kunnen worden ontwikkeld. Op langere termijn zou het vervangen van aluminium door koolstofvezelcomposiet op het buitenpaneel het probleem oplossen, net als het offline produceren van de achterklep en het later toevoegen in de bouwreeks van het voertuig. Beide opties brengen echter kosten met zich mee.
Project 3.2 is nu aan het afronden, maar heeft interessante technologie voortgebracht, waarvan sommige - de B-pijler prepreg en SMC-deklid - commercieel klaar zijn, en sommige wijzen op gebieden waar verder werk nodig is.
"Door samen te werken met IACMI en onze industriële en academische partners konden we veel dieper in technologie duiken vanaf het eerste hoofd, fundamentele wetenschap ontwikkelen en putten uit een veel bredere kennisbasis dan we alleen hadden kunnen doen", vat project 3.2-leider Patrick Blanchard samen, technisch leider-geavanceerde polymeersystemen, Ford onderzoek en innovatie. "We kijken ernaar uit om nieuwe commerciële kansen en R&D-activiteiten te identificeren om met onze IACMI-partners te blijven werken."
Hars
- Koolstofvezelapparatuur voor thuis
- Top 3 toepassingen voor 3D-printen van koolstofvezel in productie
- Innovatief gebruik van koolstofvezel
- Koolstofvezel in automobieltoepassingen
- 5 leuke toepassingen voor koolstofvezelplaten
- Waar wordt koolstofvezelfolie voor gebruikt?
- 8 koolstofvezel sleutelhangers voor elke stijl
- Materialen:met glas en koolstofvezel versterkte PP voor auto's
- Hexion introduceert tweecomponenten epoxyoplossing voor de productie van composieten in de ruimtevaart
- Foiling motorjacht maakt indruk in koolstofvezel/epoxy
- Serie ontworpen voor autoproductielijn