De OOA-geïnfundeerde vleugeldoos verbeteren
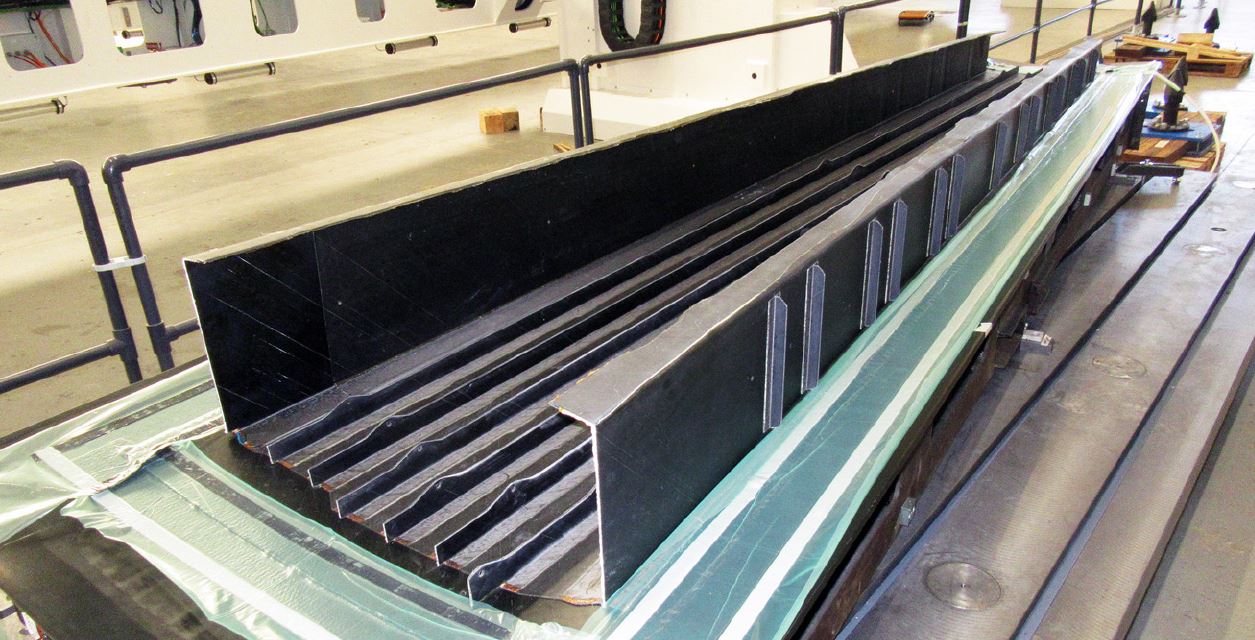
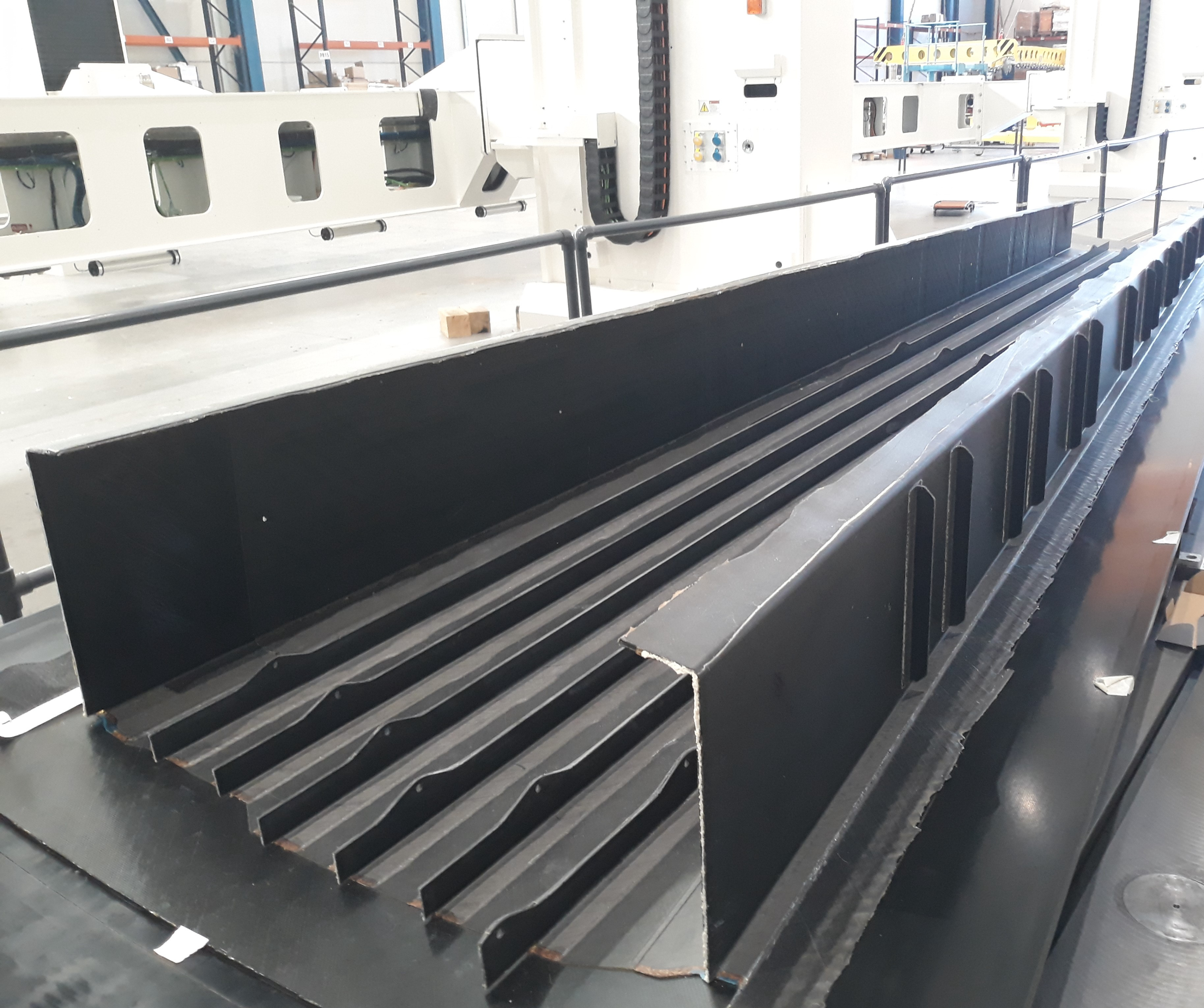
Terwijl de lucht- en ruimtevaartindustrie anticipeert op herstel van de COVID-19-pandemie, is het eerdere streven naar productie met hoge snelheid veranderd in een dringende actie om de milieubedreigingen voor de planeet en de mensen te verminderen. Deze inspanning omvat limieten voor de uitstoot van broeikasgassen (BKG), het energie- en waterverbruik en het creëren van afval dat niet kan worden gerecycled. Hoewel deze initiatieven pre-COVID aan de gang waren, wordt er nu meer nadruk op gelegd, net als de behoefte aan veel lagere kosten om composietstructuren te produceren. Het pan-Europese luchtvaartprogramma Clean Sky 2 heeft onderzoek en ontwikkeling op al deze gebieden gefinancierd en heeft een aantal vezelversterkte composiettechnologieën aanzienlijk verbeterd.
In de zevende oproep tot het indienen van voorstellen van Clean Sky 2 (CFP07, oktober 2017) is het verzoek van Airbus Defence and Space (Airbus DS, Cadiz, Spanje) opgenomen voor een innovatieve en flexibele proeffabriek om een sterk geïntegreerde wingbox-vliegdemonstrator te produceren met behulp van geautomatiseerde glasvezel plaatsing (AFP) en vloeibare harsinfusie.
Er zijn andere met hars doordrenkte en/of out-of-autoclave (OOA) vleugeldoosdemonstraties geweest, waaronder een OOA "gemengde" vleugeldoos die in 2013 werd onthuld door GKN Aerospace (Redditch, VK); de Airbus A220-vleugel geproduceerd door Spirit AeroSystems Belfast in Noord-Ierland met behulp van harsoverdracht in een autoclaaf; en de OOA-vleugel geproduceerd door AeroComposit (Moskou, Rusland) voor de MS-21 straalvliegtuig. Deze hebben echter allemaal discrete, met composieten verstevigde huiden en rondhouten met mechanische bevestigingsmiddelen geassembleerd (zie "Het pad naar OOA-vleugels met minimale bevestigingsmiddelen").
De door Airbus DS gevraagde vleugelkast in Clean Sky 2 was om een stap voorwaarts te zetten door de verstijfde onderhuid te integreren met verstijfde voor- en achterliggers, waardoor een completere module zonder mogelijk werd. bevestigingsmiddelen die moeten worden doorgestuurd voor montage met de resterende vleugelcomponenten.
Deze vleugelkast zou ook gebruik maken van smalle (0,25 of 0,5 inch brede) droge koolstofvezeltapes en hoge temperatuur (180°C Tg ) uithardende harsen, maar met energiebesparende, goedkope verwarmingssystemen en op sensoren gebaseerde digitale besturing en simulatie om de verwerking te voorspellen en te beheren, de trial-and-error-loops tijdens de ontwikkeling te verkorten en snelle training van productiepersoneel mogelijk te maken. Deze digitalisering zou zich ontwikkelen tot een mobiele augmented reality-toepassing (app) die ook gebruikers- en onderhoudshandleidingen, procesvolgordedefinitie, papierloos volgen van processen en onderdelen en projectie van CATIA-modellen op het onderdeel biedt om te helpen bij de precieze plaatsing van voorvormen van verstijvers, inzetstukken voor gereedschappen en koolstofvezelversterkte polymeer (CFRP) caulplaten.
Dit project, misschien wel het meest veeleisend, vereiste dat alle gereedschaps- en productieapparatuur draagbaar en flexibel moest zijn, gemakkelijk te implementeren op elke productielocatie en aanpasbaar voor andere onderdeelontwerpen en upgrades naarmate meer geavanceerde gereedschaps-, verwarmings- en composieten 4.0-procesbesturingstechnologieën beschikbaar komen.
Zoals uitgelegd door de topicmanager Luis Rubio, hoofd van composietontwikkelingstechniek - technologie en proces bij Airbus DS:"Het uiteindelijke doel van het project is om aan te tonen dat een alternatieve technologie (voor prepreg en autoclaaf) met lagere kosten, kortere doorlooptijden en ecologische voetafdruk kan vergelijkbare ontwerptoleranties en kwaliteitsniveaus bereiken.”
MTorres (Torres de Elorz, Spanje) reageerde en solliciteerde zonder partners. "We hadden alle mogelijkheden in huis:AFP, infusie, droge tapematerialen en automatisering", legt Sebastian Diaz uit, senior manager composiettechnologieën bij MTorres. Het bedrijf ontving het project Innovative Infusion Airframe Manufacturing System (IIAMS), gefinancierd via het Horizon 2020-programma van de Europese Unie onder subsidieovereenkomst nr. 820845, en begon in oktober 2018.
Buitenste vleugeldoos demonstrator
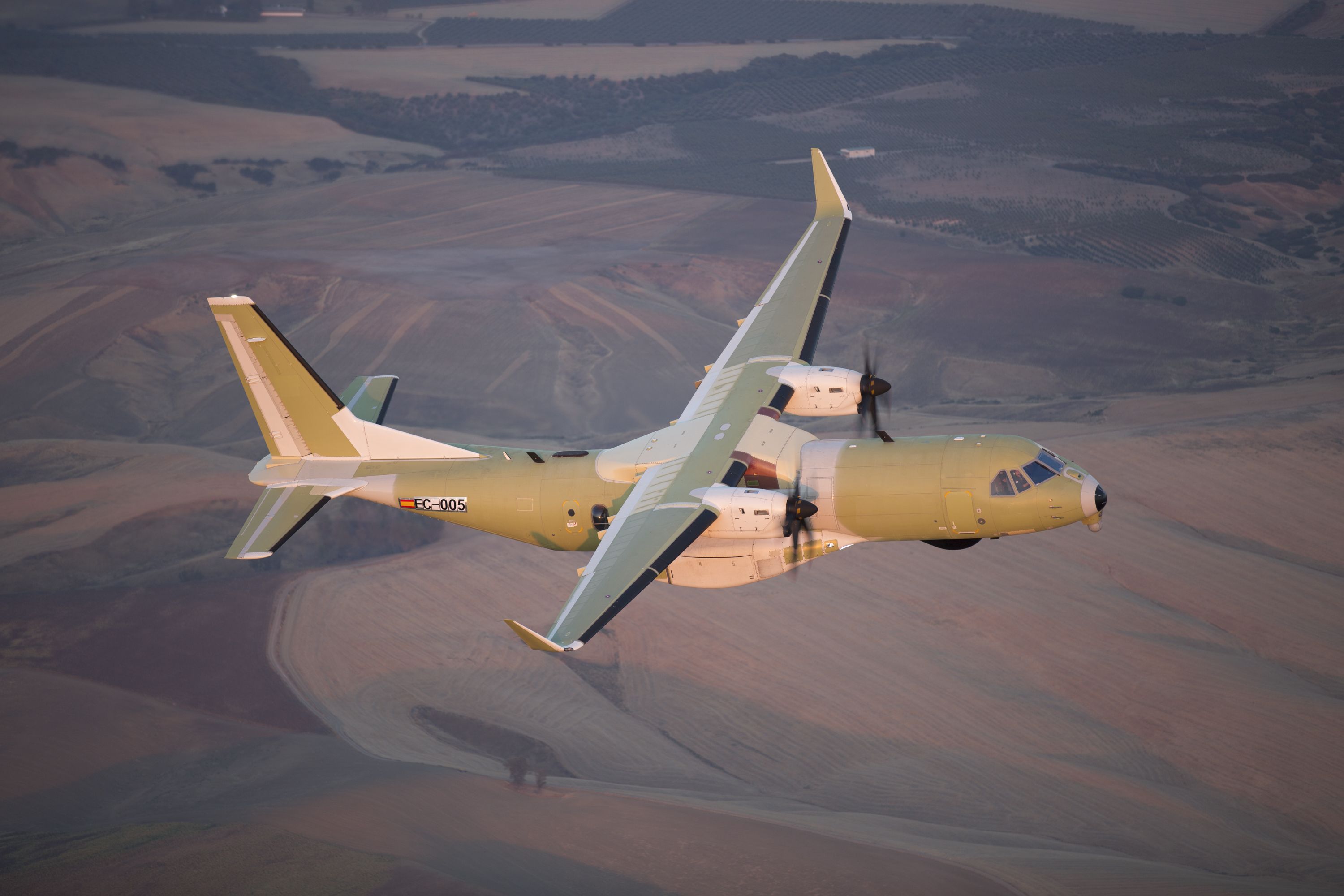
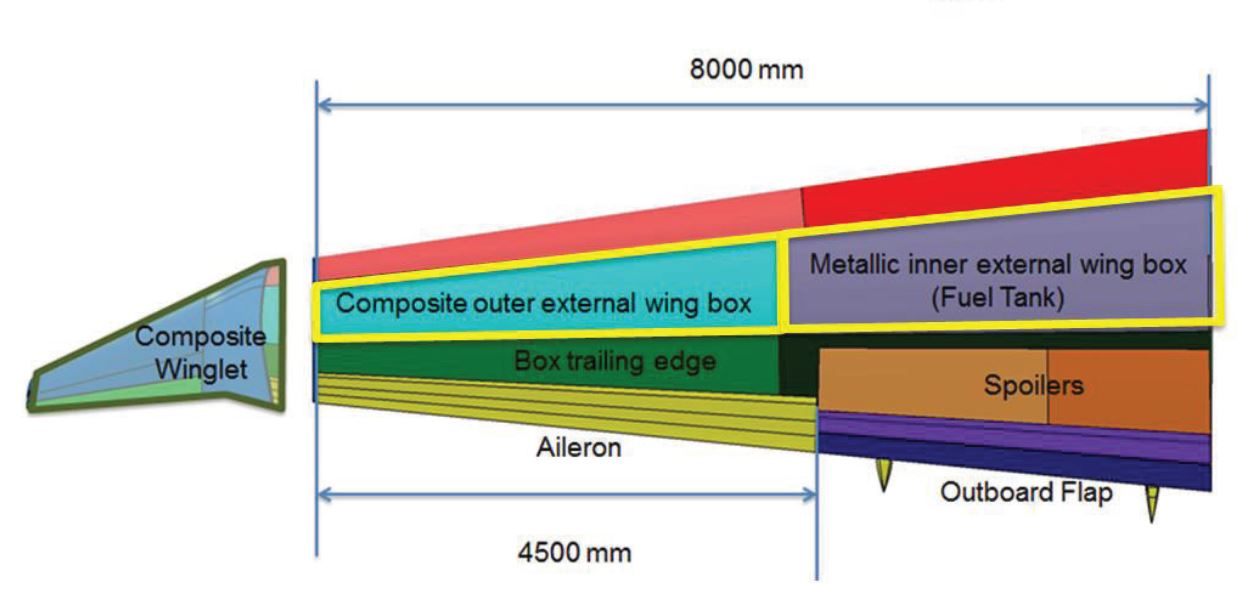
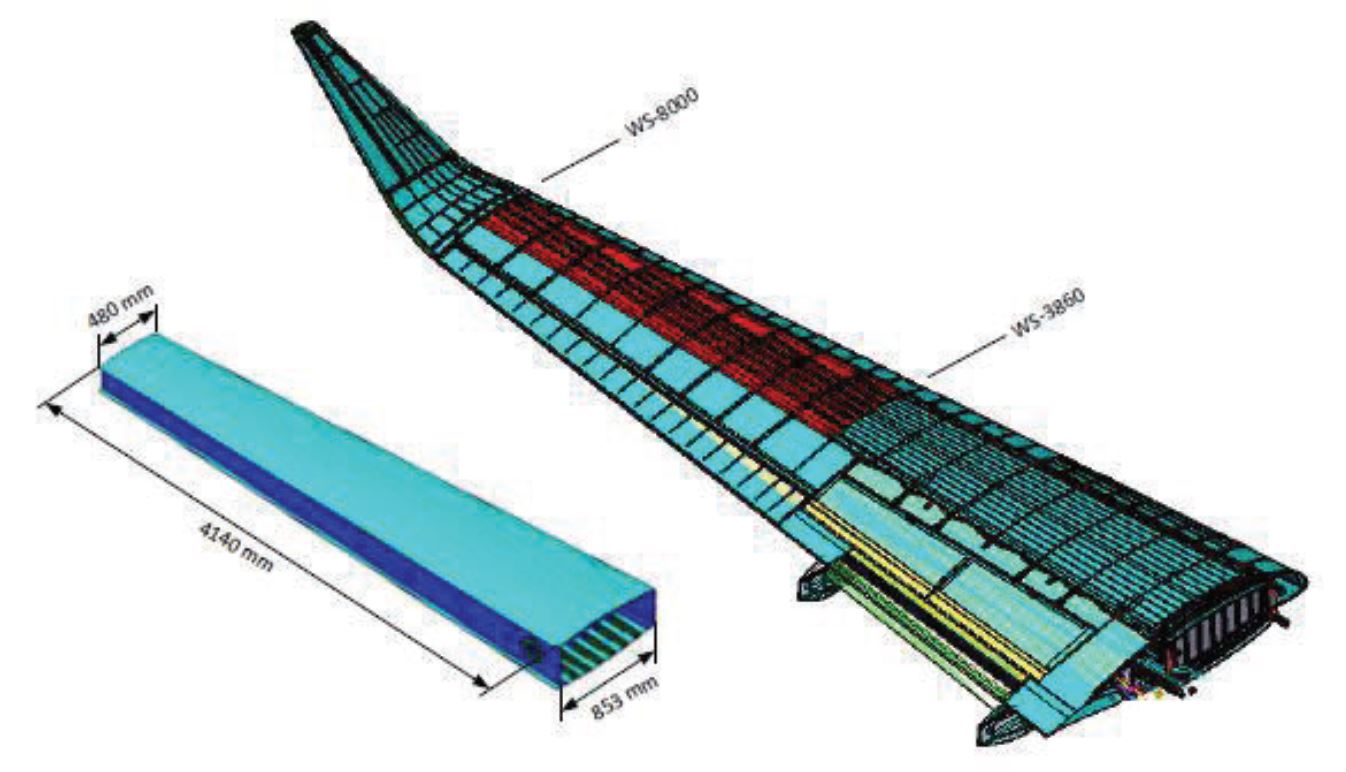
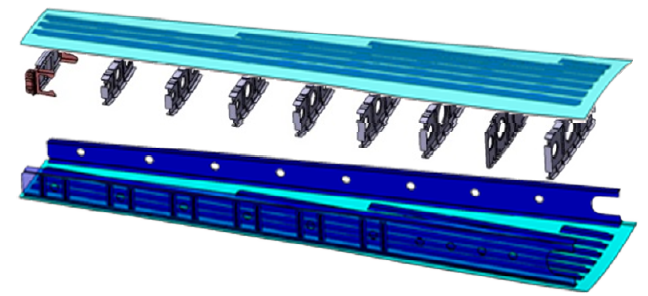
De demonstrator die Airbus DS koos, was een buitenste vleugeldoos gebaseerd op zijn C-295 twin-turboprop militair transport (Fig. 1), geproduceerd in San Pablo, Sevilla, Spanje. Deze 4,14 meter lange composiet buitenboordmotor koppelkast past op een binnenboord metaal torsie doos. De composiet wingbox wordt ook bevestigd aan een winglet, leading edge en trailing edge.
"We zouden twee 4 meter lange demonstrators maken, de rechter- en linkervleugel, die zullen worden geïnstalleerd voor tests tijdens de vlucht", zegt Diaz. “De fabricage moest een eenmalig proces zijn, geen secundaire binding. We hebben alleen de "U" gemaakt, bestaande uit de onderhuid met zes geïntegreerde stringers en de rondhouten aan elke kant. De huid, stringers en rondhouten variëren allemaal in dikte. De J-vorm van de rondhouten en de integratie van hun verstijvers was een hele uitdaging om te vervaardigen. We stonden ook voor de uitdaging om met dit fabricageproces nauwe toleranties en nauwkeurige geometrie te behouden. Deze nauwkeurigheid is van cruciaal belang, vooral bij de wortel voor montage aan de binnenste vleugelkast en dan ook bij de vleugel."
Het ontwerp van de innovatieve, industriële productie werd ontwikkeld bij MTorres, terwijl Airbus DS de specificaties voor het onderdeelontwerp leverde. "We werkten gemakkelijk samen om het beste fabricageproces te ontwerpen, waarbij we verifieerden dat dit ontwerp door ons proces kon worden geproduceerd en vice versa", zegt Diaz.
Geautomatiseerd centrum voor thermo-infusie (ACTI)
Volgens de Airbus DS-specificatie moeten alle gereedschappen en productieapparatuur die worden gebruikt om de vleugelkast te produceren draagbaar zijn, met standaardvoertuigen naar andere faciliteiten kunnen worden vervoerd en snel en zonder speciale maatregelen kunnen worden opgesteld. Dit leidde tot de ontwikkeling van het geautomatiseerde centrum voor thermo-infusie (ACTI), dat het warm draperen van de stringers en rondhouten uitvoert; infusie van de stringers, rondhouten en huid; en genezingscycli. Hot drapeforming (HDF) — ontwikkeld als verwarmde debulking in aerostructuren en als verwarmde preforming buiten de ruimtevaart — verwijdert holtes in lay-ups en zet 2D-blanco's voor de stringers en rondhouten om in gevormde preforms (zie "Hot drapering").
De ACTI heeft een nuttig binnenoppervlak van ongeveer 5,5 x 2,2 meter en lijkt op een traditioneel HDF-systeem, met een stalen frame en een bovenste helft die elektronisch omhoog en omlaag wordt gebracht, compleet met vergrendeling en andere veiligheidsvoorzieningen. De uithardingstool en meerdere hot drape-vormgereedschappen zijn in de ACTI geplaatst. "Er wordt geen druk uitgeoefend, alleen vacuüm", merkt Diaz op. "ACTI maakt gebruik van verwarmde lucht met een luchtstroom die is gedefinieerd om een snelle warmteoverdracht te bieden, zowel bij de vorming van het hete laken als bij de infusieprocessen."
Hij merkt ook op dat het systeem zelfnivellerend is. "De stijfheid van de ACTI-structuur (en het uithardingsgereedschap) is ontworpen om te voldoen aan toleranties onder operationele belastingen in een eenvoudig ondersteunde toestand op slechts twee ondersteuningssecties", legt Diaz uit. “Dit betekent dat de maatnauwkeurigheid behouden blijft wanneer u op de vloer rust, zonder dat verdere nivellering of andere geometrische afstemming vereist is. ACTI heeft ook een laag energieverbruik en lage productiekosten.”
Dit laatste is grotendeels te wijten aan de vervanging van de assemblage van meerdere uitgeharde onderdelen door de assemblage van meerdere voorvormen, die vervolgens worden geïnfuseerd en uitgehard tot een enkele geïntegreerde structuur. “De uithardingstool is ook de montagetool”, zegt Diaz. "Alle elementen zijn droge preforms die in de uithardingstool zijn geassembleerd en vervolgens in een enkelvoudig proces samen zijn geïnfuseerd." Er is geen montagemal nodig en door innovatieve elementen in de tooling worden strikte toleranties bereikt.
Een ander belangrijk aspect van deze aanpak is het verwijderen van destructieve en niet-destructieve tests (NDT), in plaats daarvan te vertrouwen op procesgegevens die tijdens de verschillende fabricagestappen zijn verzameld om de proceskwaliteit te verifiëren en parameters die buiten de specificaties vallen te markeren. Sensoren die met de ACTI worden gebruikt, verzamelen temperatuur, vacuüm, harsstroom en uithardingstoestand. "Zowel de luchttemperatuur als de onderdeeltemperaturen worden gecontroleerd", zegt Diaz. "De tooling heeft geïntegreerde thermokoppels die de temperatuur voor de mallen en de onderdeeloppervlakken volgen." Alle gegevens worden geregistreerd, geanalyseerd en gebruikt om grafieken af te drukken en te helpen bij het nemen van productiebeslissingen.
"Zowel in IIAMS als in toekomstige projecten helpen de gegevens om de procesconfiguratie in de vroege stadia te verbeteren", legt Diaz uit. De harsstroom en de uithardingstoestand worden gecontroleerd met behulp van Netzsch (Selb, Duitsland) diëlektrische sensoren, die rechtstreeks in de CFRP-uithardingstools zijn geïnstalleerd. "We hadden contactloze sensoren voor de huid nodig omdat er geen direct contact is tussen hars en schimmel", zegt Diaz. "De sensoren bewaken de verandering van het diëlektrische veld wanneer de hars arriveert en vervolgens vast wordt tijdens het uitharden. We hebben deze gegevens gebruikt om de uithardingscyclus te verkorten.”
Later in het project werden de sensoren en ACTI gecombineerd met een door MTorres ontwikkelde mens-machine-interface (HMI), die echte procesbesturing vanaf een computer mogelijk maakt, inclusief vacuüm en temperatuur, evenals harsstroom via een toevoerklep. Volgens Airbus DS is het doel om de massaproductie van geïntegreerde primaire composietstructuren te bevorderen door het proces gestroomlijnder en intelligenter te maken.
Lichtgewicht gereedschap en draagbaarheid
MTorres produceerde twee sets mallen:een voor de rechtervleugel en een voor de linkervleugel. "Onderdelen met identieke geometrie, zoals verstijvers, hadden maar één set", merkt Diaz op. "Andere tools werden waar mogelijk gedeeld."
Een enkel uithardingsinstrument uit één stuk werd gebruikt om de 3D-vorm van de huid te vormen, waarop alle andere preforms zich bevonden. Met een lengte van ongeveer 4,5 meter zijn de rechter- en linkerversie van dit gereedschap gemaakt met CFRP, zegt Diaz. “Dit maakt het gemakkelijker om toleranties te handhaven omdat we de tooling hebben ontworpen met dezelfde lay-out en verwerking als de onderdelen, dus de CTE ligt heel dicht bij die van het uiteindelijke onderdeel. Deze CFRP-uithardingsgereedschappen zijn ook lichtgewicht, ongeveer 200 kilogram, en dus verplaatsbaar met een kleine elektrische vorkheftruck. Dit zou onmogelijk zijn als we metaal zouden gebruiken voor een 4,5 meter lang stuk gereedschap.”
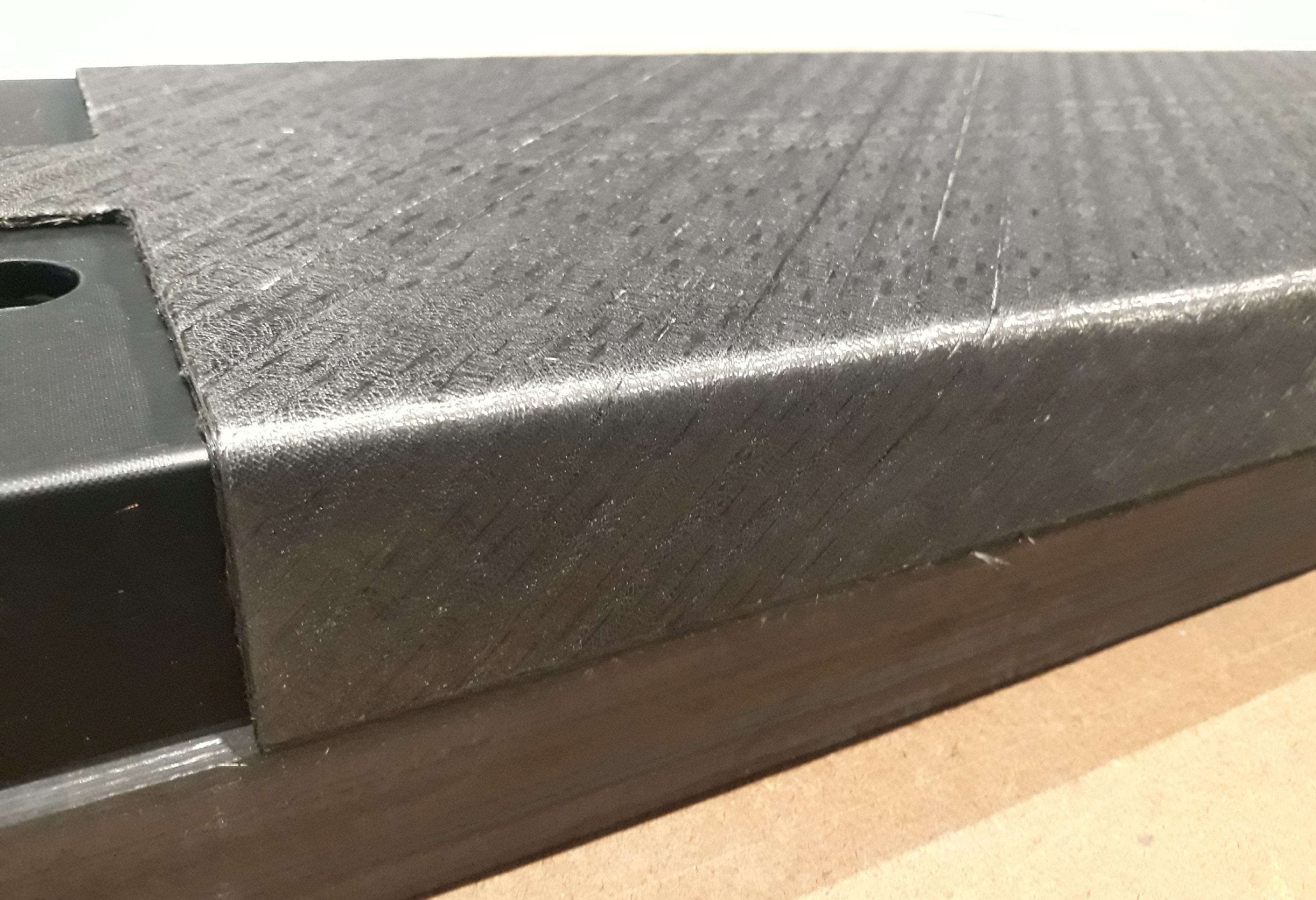
De rest van het gereedschap - cauls, positioners en HDF-gereedschappen - kon gemakkelijk met de hand worden beheerd. HDF van de stringers, rondhouten en rondhoutverstevigingsvoorvormen gebruikte mannelijke (IML) gereedschappen, ook gemaakt van CFRP. Tijdens gebruik werden deze op een aluminium tafel gemonteerd en in de ACTI geplaatst.
AFP met nieuwe droge vezeltape
Alle structurele elementen van de vleugelkast - huid, langsliggers, rondhouten, rondhouten verstijvers - werden geproduceerd met behulp van MTorres AFP-technologie voor droge vezeltapes. "In de voorsteloproep stond het gebruik van snelle en goedkope materialen", zegt Diaz. “Maar commercieel verkrijgbare droge vezeltapes, vooral van de grotere leveranciers, waren niet zo gemakkelijk te kopen en we hadden de expertise om ons eigen materiaal te maken (zie “Nieuwe droge tape voor vloeibaar gegoten composieten”). Dus gebruikten we onze 0,5-inch brede, 300 gram per vierkante meter (gsm) droge koolstofvezeltape gemaakt van Mitsubishi Rayon (Tokyo, Japan) 50K zeer sterke (HS) vezel. Onze tape is ontworpen om het tijdens de infusie te vergemakkelijken en goed te presteren, maar ook tijdens het leggen met onze AFP-koppen. We kennen alle parameters voor AFP-lay-up, hot drape-vorming en harsinfusie, en als we kleine wijzigingen moesten aanbrengen, konden we dat omdat we de tapeproductielijn beschikbaar hadden."
MTorres testte ook het fabricageproces van de vleugelkast met 200 g/m² tape van Hexcel (Les Avenières, Frankrijk) gemaakt van de IM-vezel (Intermediate Modulus). "Hoewel ons proces goed kan werken met beide soorten tapes", zegt Diaz, "was het tijdens de ontwikkelingsfase gemakkelijker en goedkoper om met ons materiaal te leggen dan met het in de handel verkrijgbare materiaal - de breedte en stijfheid werden zo ontworpen dat het gedrag van spoelen naar tafel verliep soepel en snel. Het was ook direct beschikbaar.”

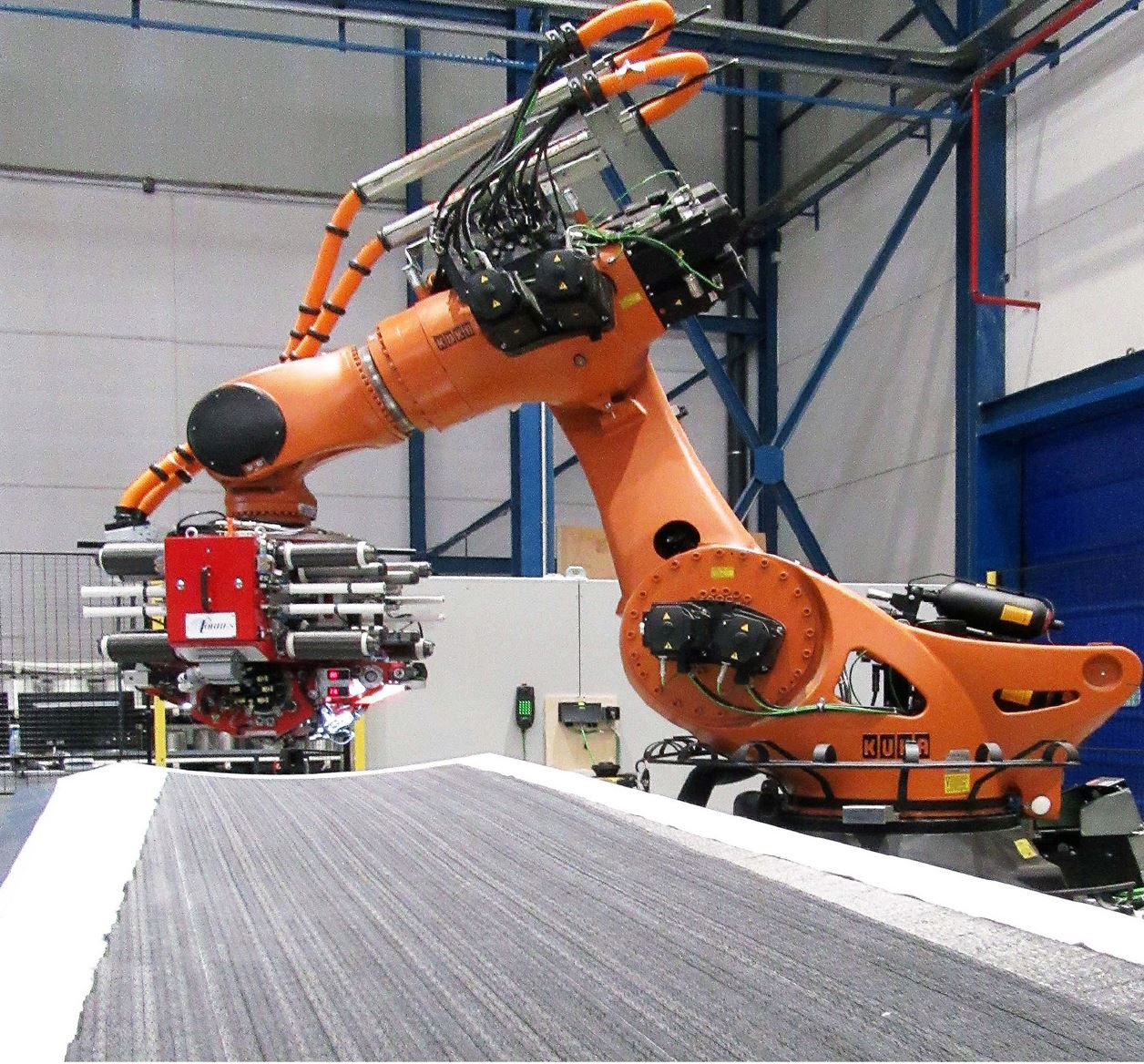
Stap 1. AFP werd gebruikt om de huid van de vleugelkast (hier weergegeven) en 2D-blanks voor stringers, rondhouten en rondhoutverstijvingen op te leggen. Photo Credit, alle stappen: IIAMS-project, Airbus Defense and Space, MTorres.
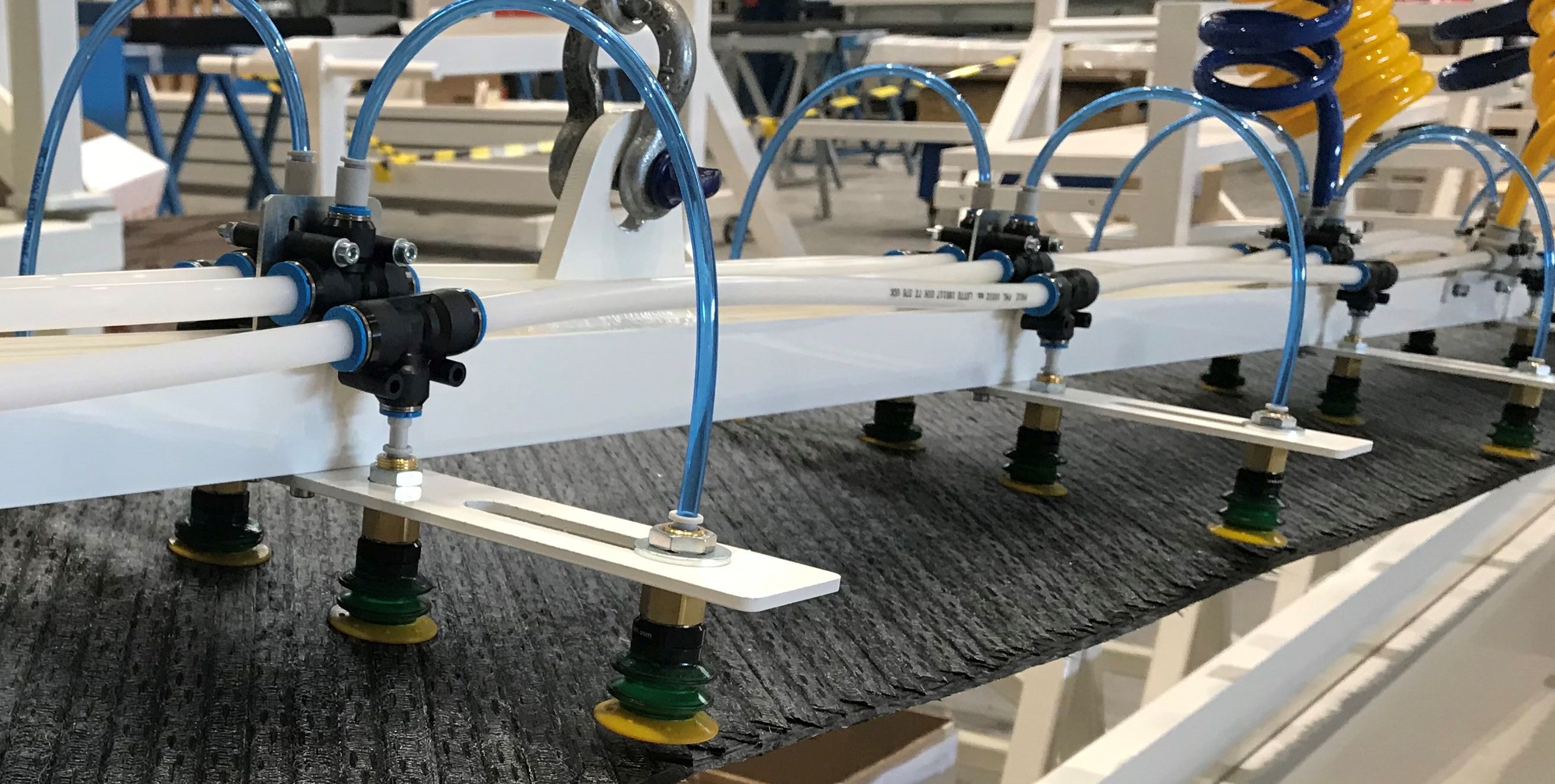
Stap 2. Platte plakband werd van de oplegtafel naar gereedschappen voor het vormen van hete laken getransporteerd.
Hij merkt op dat er voor AFP twee strategieën werden gevolgd:één voor de onderhuid en een andere voor de stringers, rondhouten en rondhoutverstijvingen. De huid (3-6 millimeter dik) werd met behulp van in de uiteindelijke 3D-vorm bovenop de uithardingstool gelegd (stap 1). een semipermeabel membraan - gepatenteerd door Airbus in zijn Vacuüm Assisted Process (VAP) infusie. De langsliggers, rondhouten en rondhouten verstijvers werden als platte plano's (2D) op een vacuümtafel gelegd en vervolgens naar de HDF-gereedschappen verplaatst om hun uiteindelijke 3D-vorm te bereiken (stap 2).
Verwarmde voorvormen
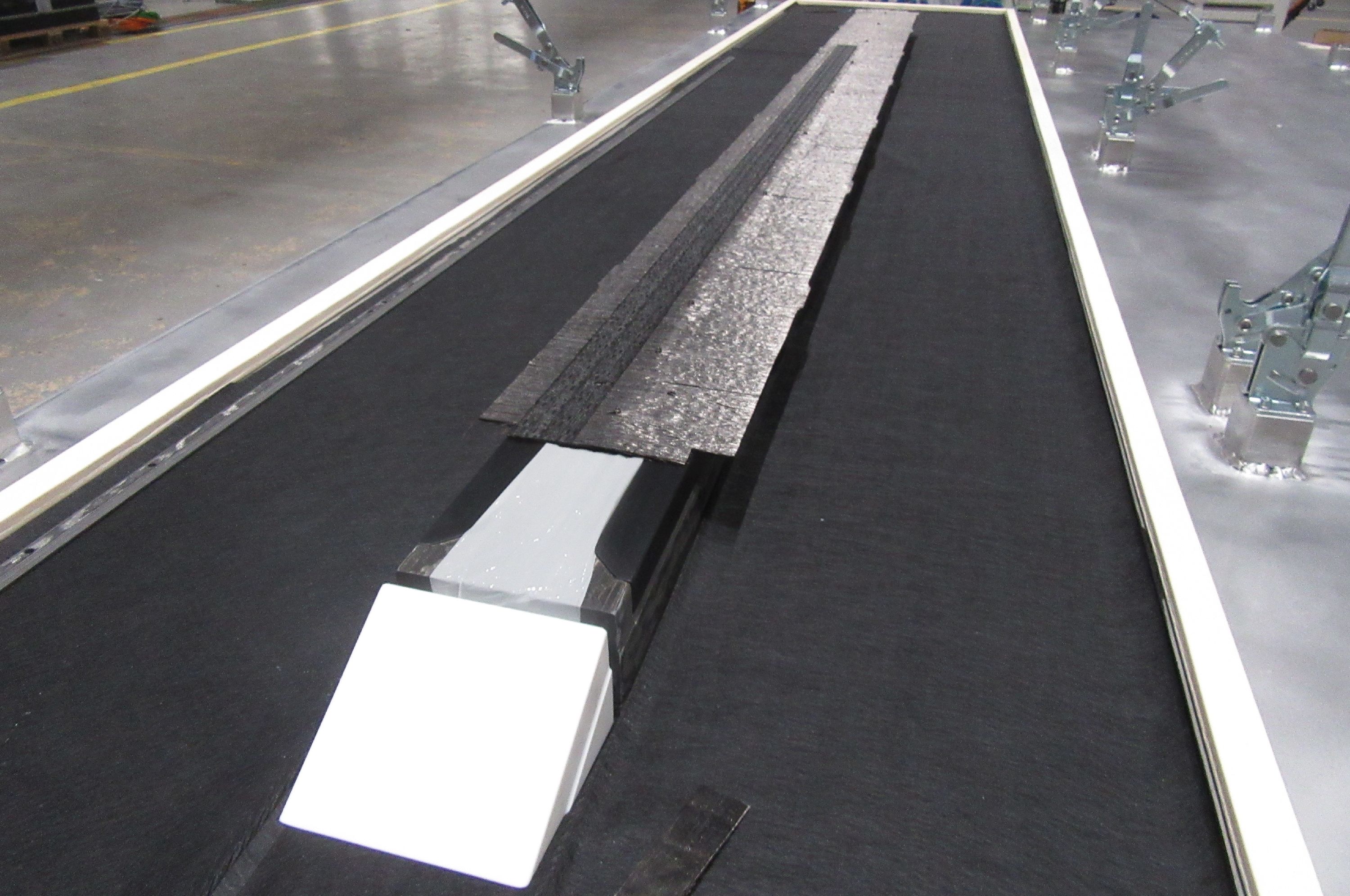
Stap 3. Stringer blank wordt bovenop mannelijke HDF-tool geplaatst.
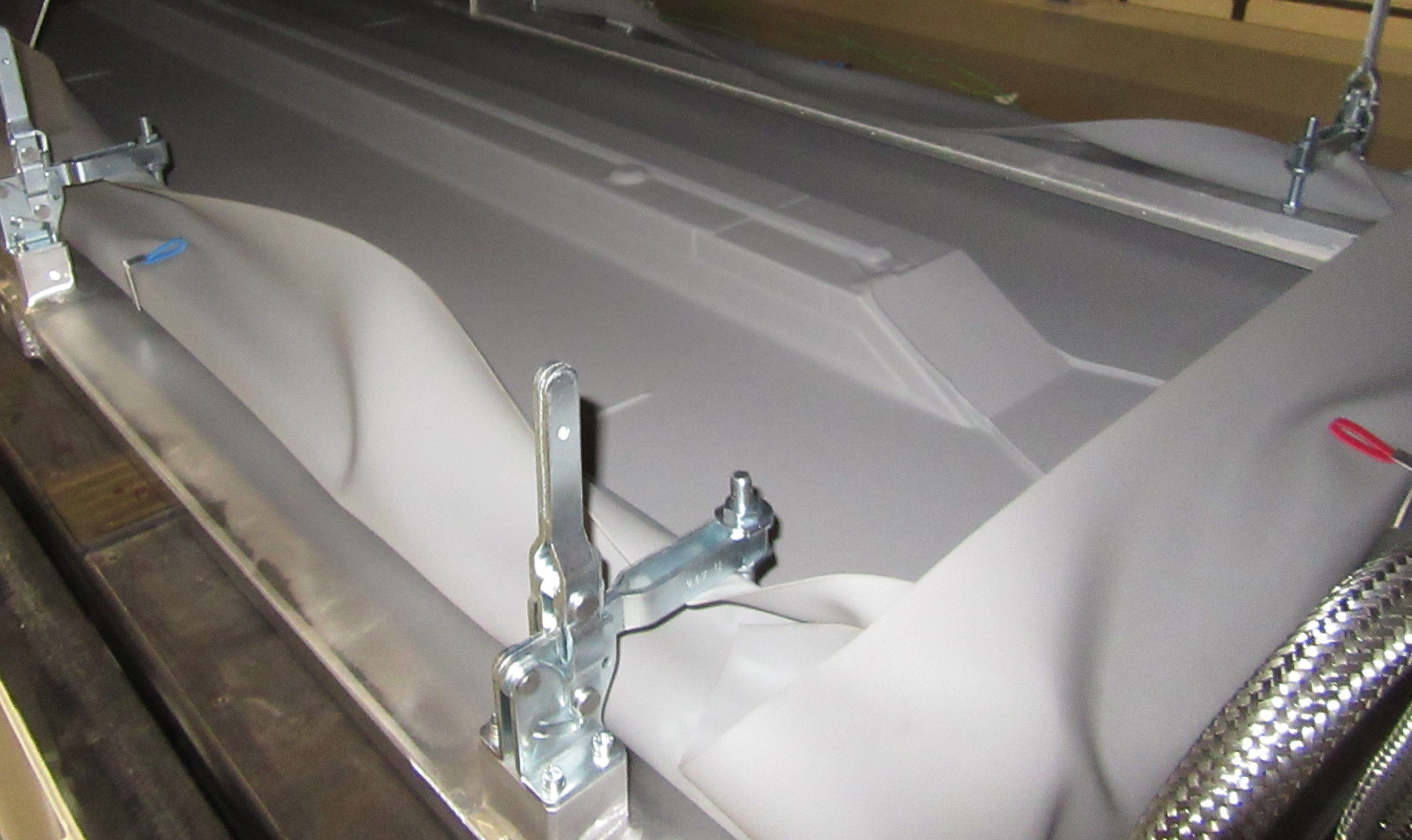
"We hebben de platte plano's voor de langsliggers, rondhouten en rondhoutverstijvingen van de oplegtafel naar het warmvormstation verplaatst met behulp van een portaal met vacuümgrijpers", legt Diaz uit. "Het geautomatiseerde systeem kan de plano's in een vlakke staat verplaatsen en op de mannelijke vormgereedschappen plaatsen [Stap 3] zonder rimpels te veroorzaken." De vormgereedschappen werden geïnstalleerd op een aluminium vormtafel, die in de ACTI werd geplaatst. Een herbruikbare siliconen vacuümzak (Mosites Rubber Co., Fort Worth, Texas, V.S.) werd bovenop de plano's geplaatst, die vervolgens in de ACTI werden verwarmd tot 130°C en gevormd met behulp van vacuümdruk (stap 4). "Vacuüm werd soepel toegepast volgens een vooraf gedefinieerde helling door middel van een regelklep wanneer het temperatuursetpoint werd bereikt", zegt Diaz.
Hij merkt op dat droge tapes gemakkelijker te voorvormen/heet draperen zijn, "omdat de hechting tussen de lagen zachter is dan bij prepregs. Ondanks dat het droog materiaal is, is het is een HDF/heated debulking waarbij de resulterende preform zijn vorm behoudt dankzij de bindmiddelen die in de tapes zitten.”
Voor de stringers en liggerverstijvers werden blanks gevormd tot twee L's, die vervolgens rug aan rug op het uithardingsgereedschap werden geplaatst om T-stringers/verstijvers te vormen. Elk van de zes huidstringers is anders en vereist verschillende gevormde blanks om de voorvormen te maken. Elk van de 24 liggerverstijvers heeft ook een andere lengte.
De voorste en achterste J-liggers bestaan uit een plano gevormd tot een C, die naar de binnenkant van de vleugelkast is gericht, en een ander plano gevormd tot een Z die naar buiten is gericht - de twee zijn rug aan rug geplaatst. De rondhouten hebben ook sinusvormige voeten aan de buitenkant van de vleugelkast (pijl in stap 7). "We sneden de vorm voor de spar-voeten op de vlakke oplegtafel voordat we de plano naar het vormstation verplaatsten", zegt Diaz. “In dit gebied mocht achteraf niets worden gesnoeid of gefreesd. De plano's werden recht op het mannelijke vormgereedschap geplaatst met de rondhoutvoeten aan de linkerkant van het gereedschap en de bovenflens aan de rechterkant."
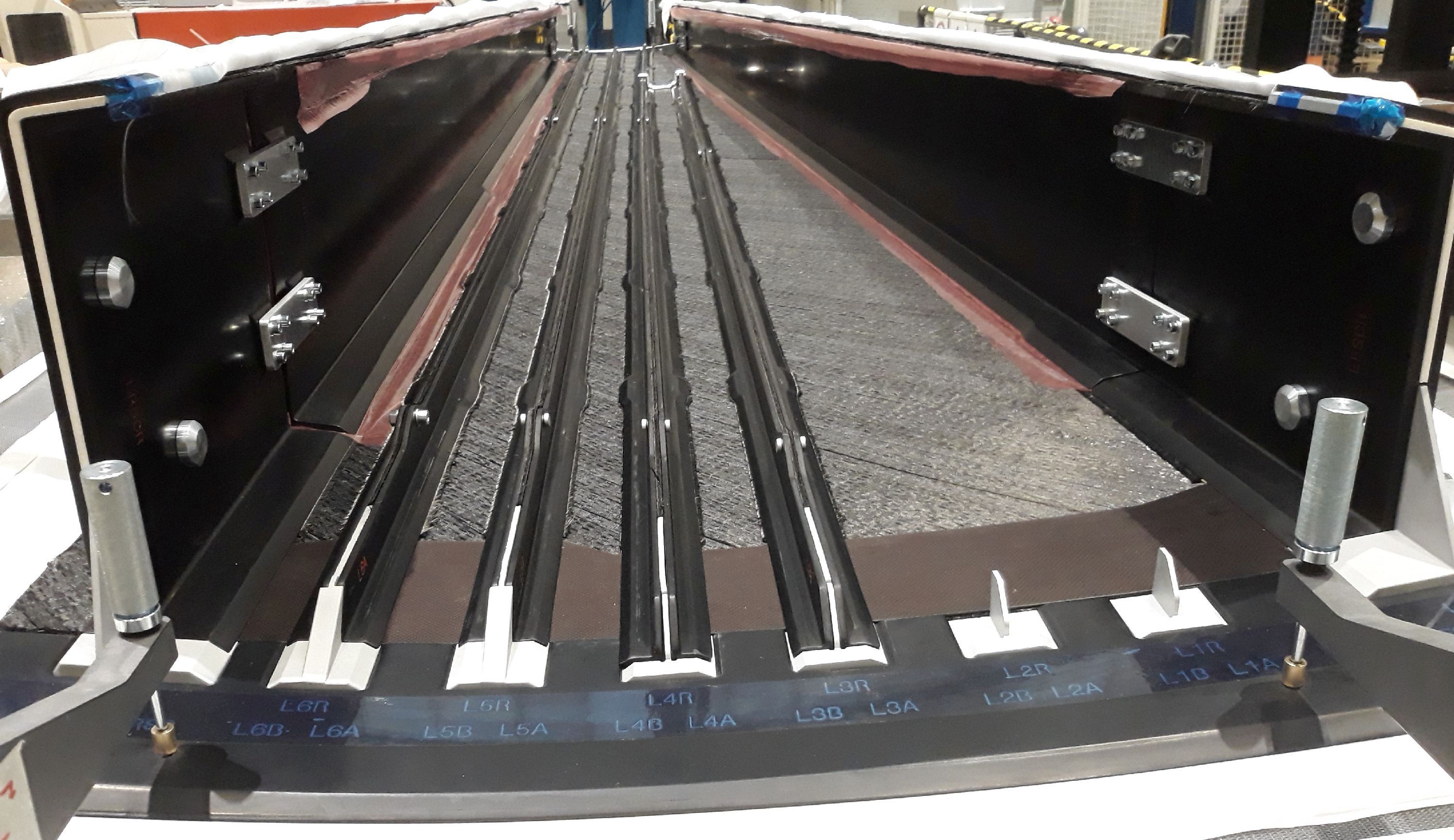
Afb. 3. Nauwkeurige plaatsing van de preforms. Preforms voor J-liggers en stringers werden gepositioneerd met behulp van dubbele metalen cilinders (uiterst links en rechts te zien), witte positioners en een CFRP-kabel met uitsparingen voor de stringers/positioners. Fotocredit: IIAMS-project, Airbus Defense and Space, MTorres.
Eenmalige infusie
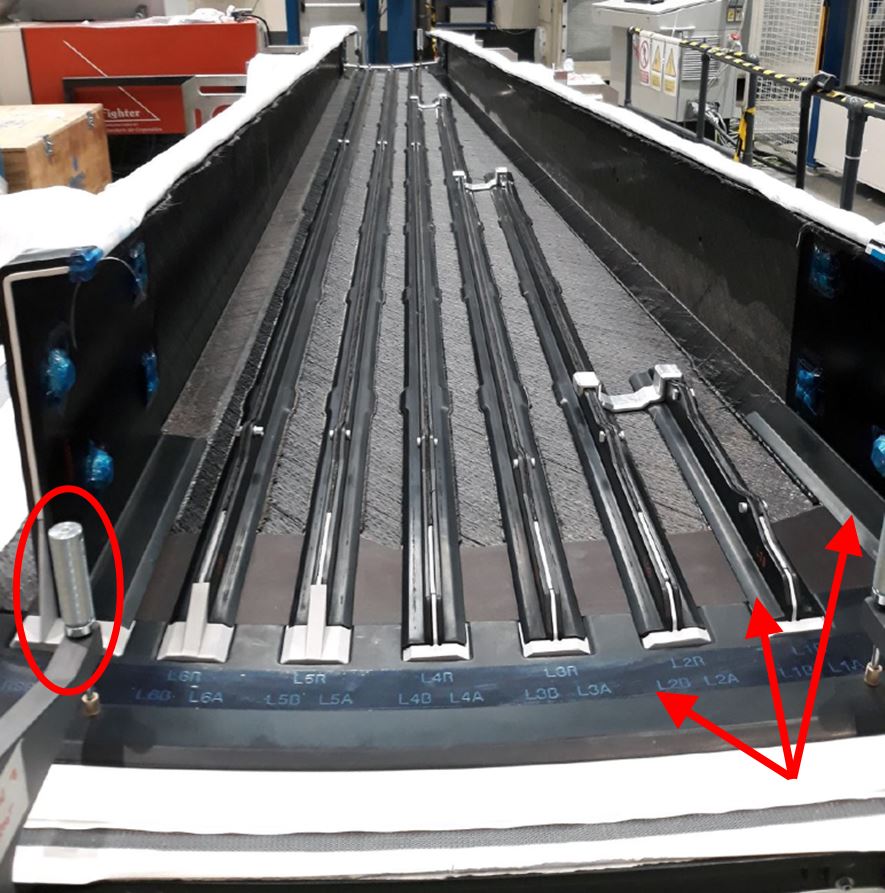
Stap 5. Stringer- en spar-voorvormen werden op de onderhuid geplaatst, geholpen door cilindrische (omcirkelde ) en witte positioneringselementen. Zwarte CFRP cauls (pijlen ) werden ook gebruikt om stringers te helpen positioneren en geplaatst bovenop stringers en J-spars.
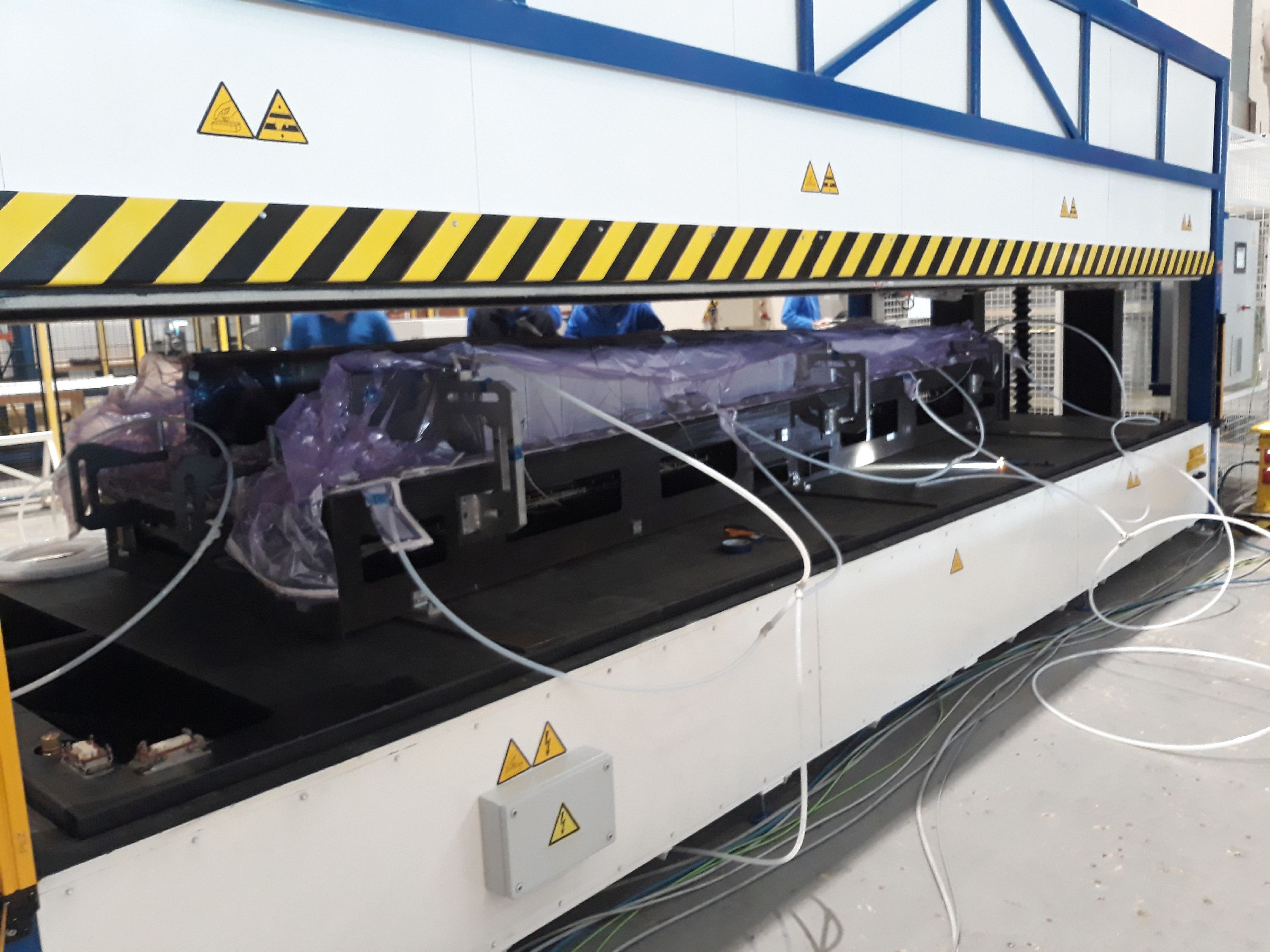
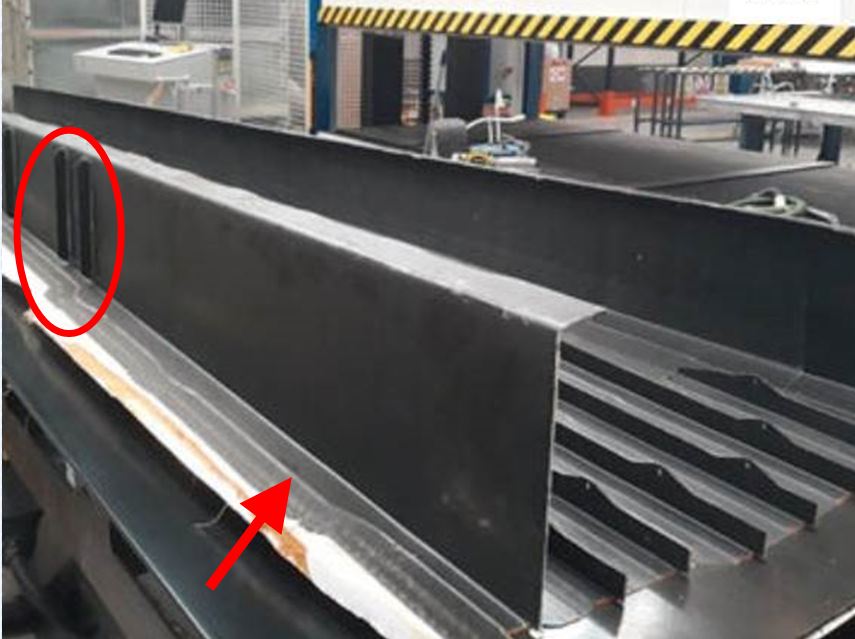
Stap 7. Eerste demonstrator voltooid bij MTorres toont de J-spar met twee ribverstevigers (omcirkeld ) en zijn sinusvormige voeten (pijl ).
De volgende stap was het plaatsen van de voorvormen van de stringer, rondhout en rondhoutversteviger op de reeds gelegde huid van de onderste vleugel (stap 5). "We indexeerden elke preform terwijl we deze op de skin and cure tool plaatsten", zegt Diaz. Cilinders die fungeren als locatie-elementen zijn te zien aan het einde van de ligger aan de linkerkant van stap 5 en aan het einde van beide liggers in Fig. 3. Deze afbeeldingen tonen ook witte positioneringsapparaten voor de stringers en J-spars. Er waren 13 van deze klepstandstellers in de uiteindelijke preform-assemblage en elk was anders.
Caul-platen waren ook een belangrijk onderdeel van het locatie- en plaatsingssysteem van de preform. Ze dienden het traditionele doel van het handhaven van uniforme druk en temperatuur in regio's met complexe lay-ups en/of geometrie, maar zouden ook van cruciaal belang zijn voor infusie, zoals hieronder wordt besproken. Een zwarte CFRP-caulplaat met uitsparingen voor de voorvormen van de stringer is te zien aan het einde van de stringers en rondhouten in stap 5 en afb. 3.
"De locatie van de voorvormen van de stringer hangt af van de locatie van die kabel", legt Diaz uit. “De digitale technologie die we hebben ontwikkeld om het productieproces te bewaken en te controleren, omvatte een augmented reality-app die de CATIA-modellen op de lay-out projecteerde. Dit werd gebruikt om de plaatsing van de caulplaten, positioneringselementen en vervolgens voorvormen te begeleiden. Het toonde ook de volgende stappen die moeten worden uitgevoerd. De app maakt zelfhulp op tabletcomputers mogelijk, zodat alle werknemers gemakkelijk toegang hebben tot alle informatie.”
Een laatste set zwarte CFRP-caulplaten werd vervolgens bovenop de L-voorvormen voor de T-stringers geplaatst en ook langs de binnen- en buitenkant van elke J-ligger, die zich uitstrekte tot op de flens en naar beneden op de voet aan de buitenkant van de vleugelkast, zoals weergegeven in stap 5 en afb. 3. "De rondhouten maken ook gebruik van een soort caulplaat aan de binnenzijde aan de uiteinden, om een grotere nauwkeurigheid in de gewrichtsgebieden te krijgen", zegt Diaz. "Al deze caulplaten werden gebruikt tijdens het HDF-proces en bleven door layup aan de preforms vastzitten."
Het voltooide droge voorvormsamenstel met caulplaten werd vervolgens bedekt met een afpellaag en een vacuümzakfilm. Het gehele samenstel van huid, stringers en rondhouten werd vervolgens in de ACTI geplaatst en het gereedschap werd verwarmd tot 120°C. Hexcel RTM6 epoxyhars werd verwarmd tot 70°C en ontgast vóór infusie via een enkele harstoevoerlocatie. "De ACTI was voorbereid om hars vanaf vier locaties toe te voeren," merkt Diaz op, "maar na uitgebreide simulatie en tests besloten we dat het gemakkelijker en goedkoper was om een enkele harsinlaat te hebben."
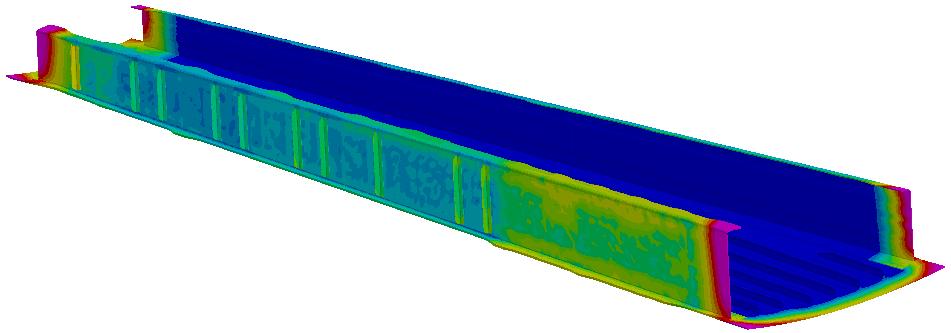
Zelfs met een enkele inlaat was het infusieproces zeer complex, met drie verschillende modi. "We hebben eerst flowsimulatie uitgevoerd met behulp van PAM-RTM-software [ESI Group, Parijs, Frankrijk]", zegt Diaz. "Er was zo'n complexe mix van stroomfronten en parameters die nodig waren voor volledige bevochtiging. De harsstroom was bijvoorbeeld sneller in het midden van de vleugelkast, maar het was een uitdaging om alle verstijvers nat te maken."
VAP, met een semi-permeabel membraan, werkte goed voor de onderhuid, maar dit werd verwisseld voor hoge temperatuur stroomgaas langs de stringers en aan de binnenkant van de rondhouten. "De hoeken waren de meest uitdagende gebieden om te bevochtigen", merkt Diaz op, "maar ze waren ook het meest kritisch voor het behouden van toleranties voor montage, evenals langs de randen." Dit is te zien aan de rode gebieden van de stromingssimulatie in Fig. 4. "In deze gebieden is een aanpak op maat ontwikkeld om de exacte benodigde afmetingen te bereiken", legt hij uit. We gebruikten ook vacuümpoorten langs de omtrek en bovenop de rondhouten.”
De infusie was relatief snel, zoals voorspeld door simulaties, gevolgd door een uitharding van twee uur bij 180°C, met alleen hete lucht en niet verwarmd gereedschap. Nadat ze uit de vorm waren gehaald, werd elke demonstrator van de vleugelkast geïnspecteerd met behulp van ultrasoon testen (UT). Dit werd gedaan als onderdeel van de opleveringen van het IIAMS-project, om de kwaliteit van de demonstrators te analyseren. Industriële toepassing van dit proces zal echter traditionele NDO verminderen ten gunste van digitale sensoren en snellere inline inspectietools zoals vision-systemen.
Volgens Diaz, hoewel de infusie-uithardingscyclus vergelijkbaar was met die voor een autoclaaf-uitgeharde prepreg-vleugeldoos, zou de totale cyclustijd korter moeten zijn. "We hebben het grootste deel van de montage achteraf geëlimineerd en we hoeven ook niets zoals met prepreg te vullen, maar onze kwaliteit is hetzelfde. Zo heeft de hechting tussen de laatste laag van de huid en de eerste laag van een stringer geen plakfolie in het midden nodig om de mechanische eigenschappen te verbeteren en toleranties op te vangen.” Dit is natuurlijk efficiënter, maar hij merkt op dat de productiesnelheid van onderdelen aanvankelijk niet de drijvende factor was. "Deze methode concurreert niet met de fabricage van afzonderlijke onderdelen, maar met een voltooide montage van de vleugelkast."
Complete demonstrators, pad naar certificering
"We hadden slechts 18 maanden om dit project te voltooien, inclusief het ontwerpen van het proces en de gereedschappen en de fabricage van de gereedschappen en demonstrators", zegt Diaz. “In maand 14 hadden we de eerste demonstrator klaar voor weergave bij JEC eind februari 2020 [stap 3], maar toen werd JEC geannuleerd vanwege de pandemie. Hoewel het project eind september 2020 eindigde, als je de maanden aftrekt dat we niet konden werken vanwege COVID-19, waren we eigenlijk in maand 16 klaar. We waren in staat om dit zeer strakke schema aan te houden dankzij onze interne ontwerpcapaciteit en bekwaamheid om de tooling-prototypes te vervaardigen met behulp van onze AFP- en CNC-freesmachines.”
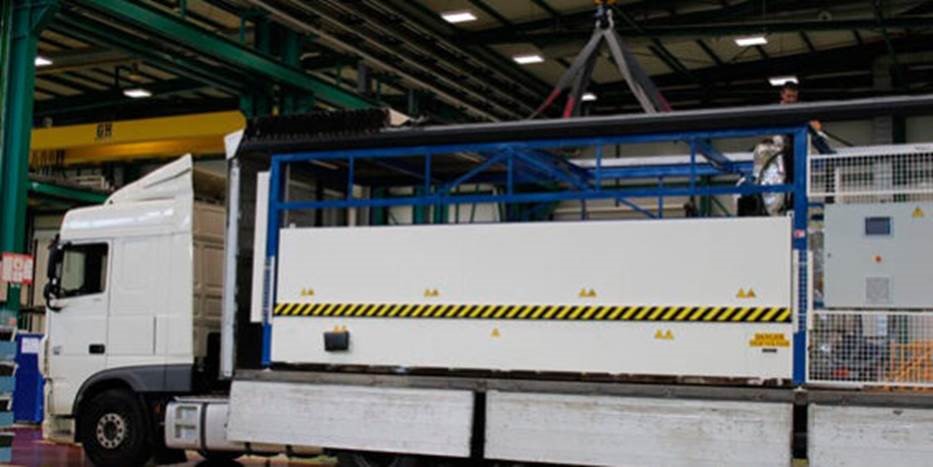
Stap 8. ACTI-vorm-/uithardingsapparatuur en vleugelkastgereedschap werden op een standaard verhuiswagen gehesen en verplaatst naar Airbus DS in Cadiz, Spanje.
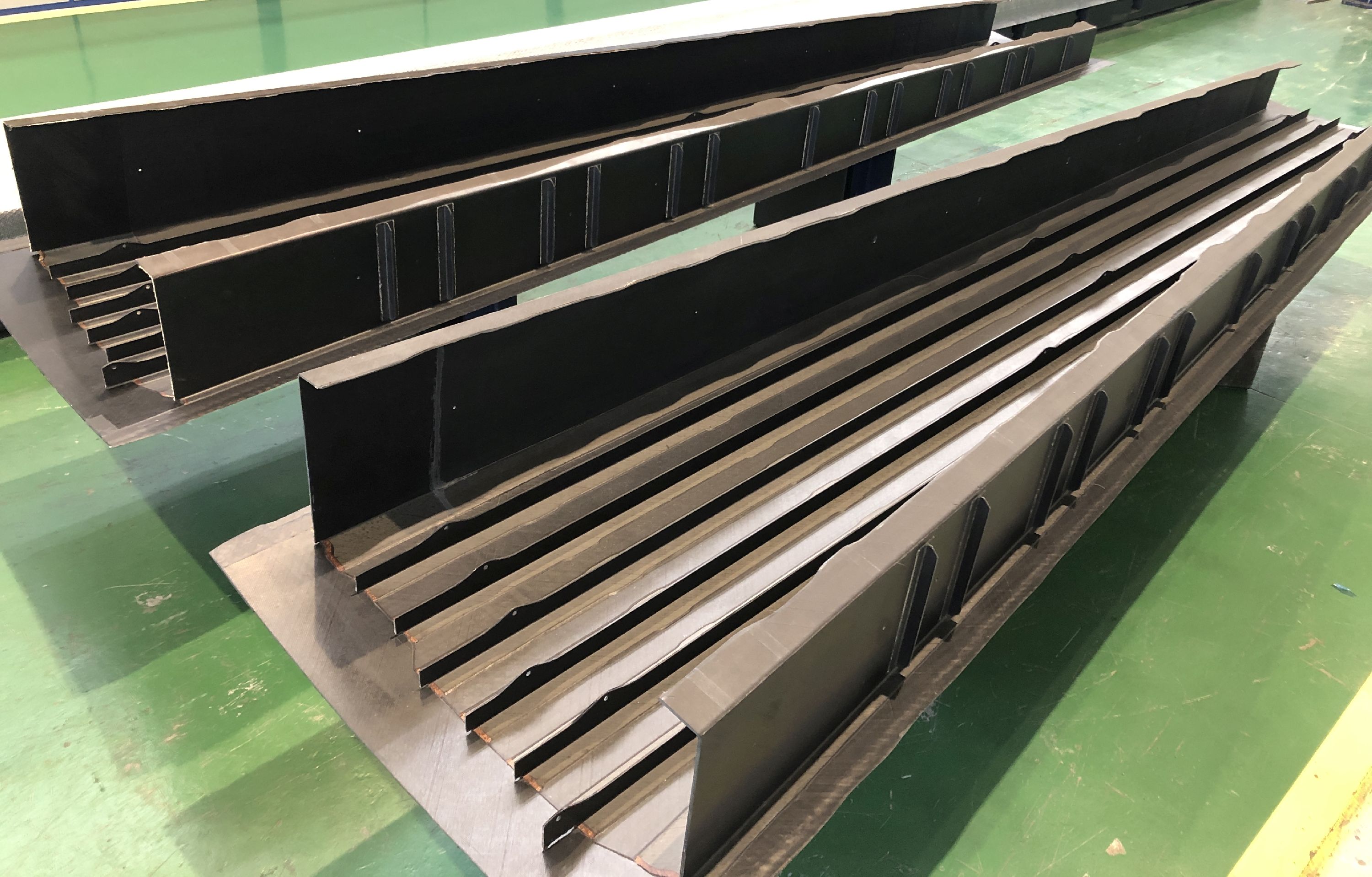
Bij MTorres is een vereenvoudigde, 1 meter lange demonstrator gemaakt om alle procesparameters te controleren. Toen werd de eerste demonstrator op ware grootte geproduceerd. Gereedschaps- en productieapparatuur werd vervolgens verplaatst naar Airbus DS in Cadiz (stap 8), waar de laatste demonstrator werd geproduceerd. Dit maakte ook deel uit van de resultaten van het project, wat aantoont dat de apparatuur gemakkelijk op meerdere locaties kon worden getransporteerd en geïnstalleerd.
Zoals uitgelegd in de zijbalk, "IIAMS-routekaart naar certificering", heeft Airbus DS een sleutelrol gespeeld in het Clean Sky-programma, en is hij geëvolueerd van co-leider van de Green Regional Aircraft (GRA) geïntegreerde technologiedemonstrator (ITD) in Clean Sky, tot mede-leider van de AIRFRAME ITD, evenals leider voor de flight testbed 2 (FTB#2) in het REGIONAL Integrated Aircraft Demonstrator Platform (IADP) binnen Clean Sky 2. De FTB#2 zal andere composieten en casco bevatten ontwikkelingen, ook in de cockpit en andere vleugelcomponenten.
Alle projecten ter voorbereiding van de FTB#2 maken in feite deel uit van een bredere langetermijnstrategie bij Airbus. Het doel is om een toekomstig turboprop-casco te ontwikkelen dat lichter en efficiënter is, en productieprocessen die goedkoper zijn en minder energie verbruiken, vloeistoffen en hulpmaterialen produceren, maar ook minder schroot genereren en meer recycleerbaarheid bieden.
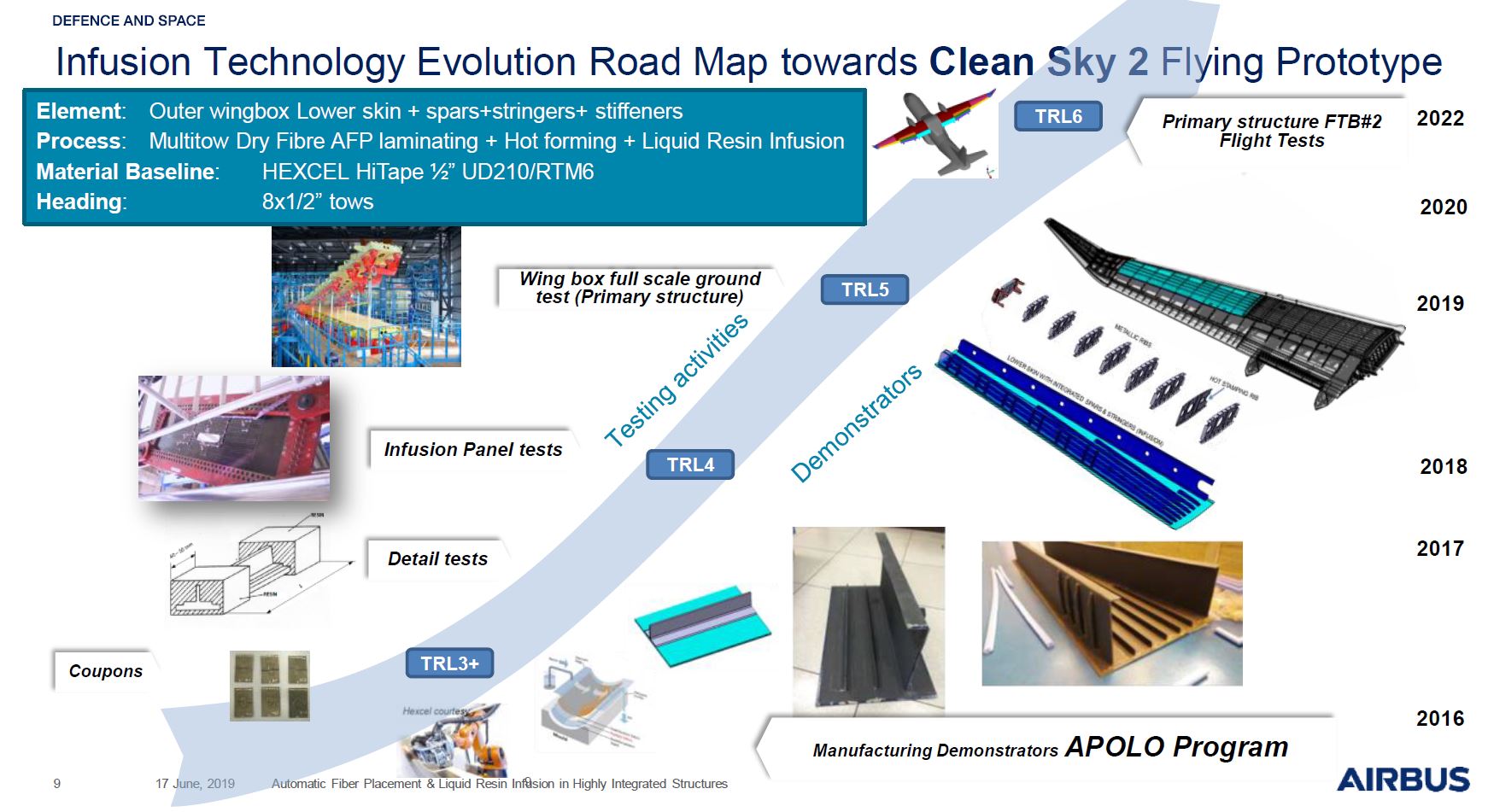
"Stap voor stap doorlopen wij [Airbus DS] de volledige testpiramide van cascostructuren, van coupons tot de volledige structurele tests van de buitenvleugel", legt A.E. Jiménez Gahete uit in een Materiales Compuestos van september 2020 artikel getiteld:"Airbus Defense and Space sterk geïntegreerde vleugelkastsectie vervaardigd door plaatsing van droge vezels en vloeibare harsinfusie." Materiaalkarakteriseringstests, een testmatrix voor ontwerpdetails en subcomponenttests voor toegestane ontwerp zijn allemaal afgerond met positieve resultaten. MTorres hielp bij deze tests, inclusief de fabricage van testcoupons en onderdelen, en demonstranten om het fabricageproces en de ontwerpdetails van de vleugelkast te valideren. Alleen de laatste volledige statische en functionele tests van de buitenste vleugel blijven over, zegt Gahete, om de FTB#2-kwalificatie voor vliegen te verkrijgen.
"Eenmalige infusie vermindert gewrichten, vermindert het gewicht en verhoogt de robuustheid", zegt Diaz. "De nieuwe droge tape die MTorres heeft ontwikkeld, heeft uitstekende resultaten opgeleverd, zowel in de verwerking - AFP, vorming van heet laken en infusie - als in de structurele eigenschappen van het onderdeel." Hij merkt op dat er historisch gezien twijfel bestond dat met hars geïnfuseerde composieten dezelfde structurele prestaties en toleranties zouden kunnen hebben als autoclaaf-uitgeharde prepreg.
"Het was onze grootste uitdaging om dezelfde toleranties te krijgen in een enkelvoudig proces met zachte [niet-metalen] gereedschappen", geeft hij toe. “Maar we hebben bewezen dat deze technologie werkt en dat het de grote primaire structuren kan produceren die nodig zijn voor toekomstige vliegtuigen. Onze volgende stap is om de digitale technologieën en de draagbaarheid van het productiesysteem verder te ontwikkelen.”
Hars
- Pigmentpoeders hebben de kunststofindustrie helderder gemaakt
- BLB Industries The BOX SMALL
- Airbus introduceert de fabriek van de toekomst
- De Edge Supply Chain Conference bijwonen? Hier leest u hoe Supply Chain Management vooruitgaat
- Een inleiding tot het ultrasoon lassen van kunststoffen
- De ontwikkeling van moderne kunststoffen
- Geschiedenis van de schroef
- Vespel®:het ruimtevaartmateriaal
- Wat is de circulaire economie?
- Vooruitgang in technologie in het nieuwe werkscenario
- De beste keuze:een Box Way CNC-draaibank