Stratasys, Champion Motorsport-team om 3D-geprinte kerntechnologie te testen
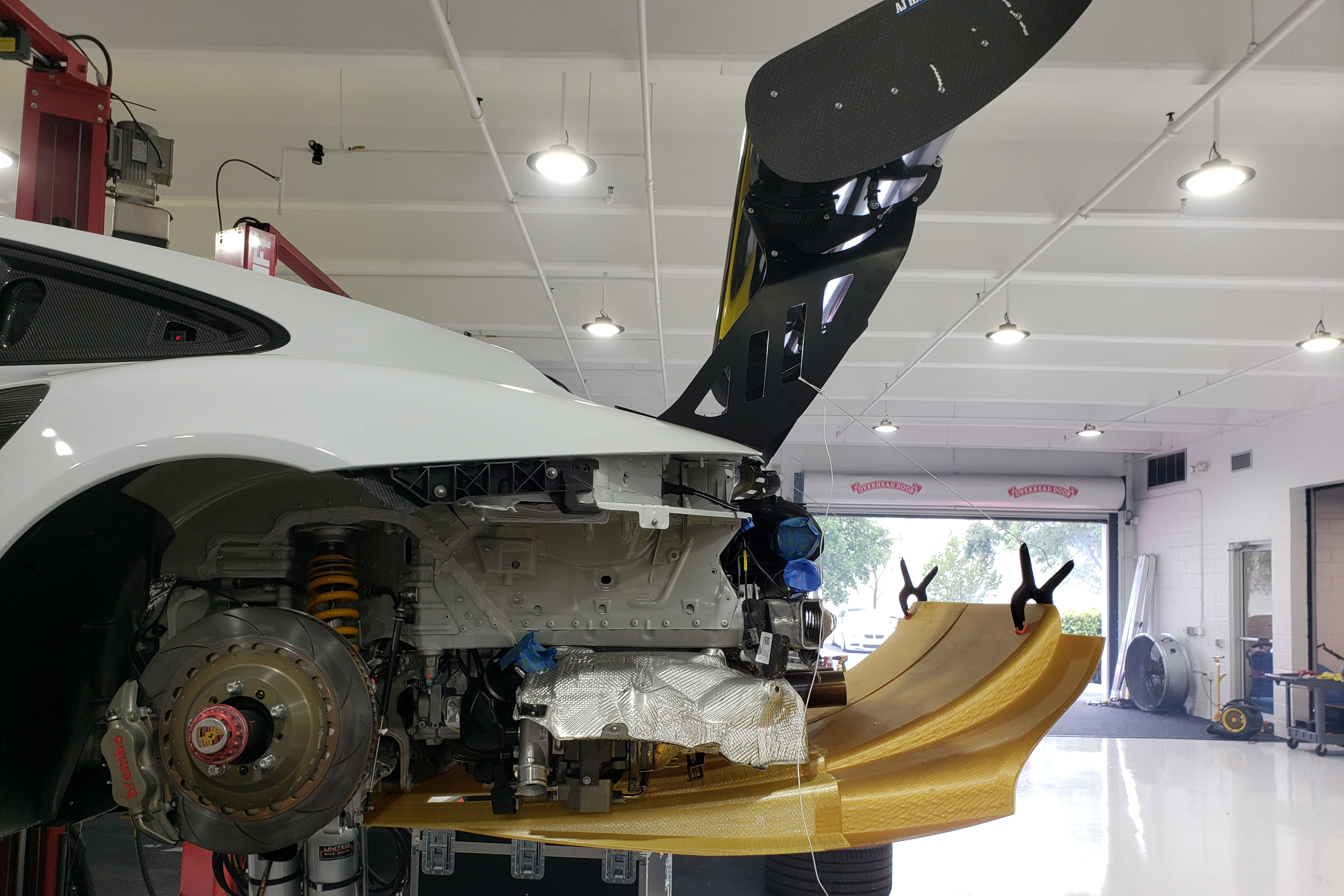
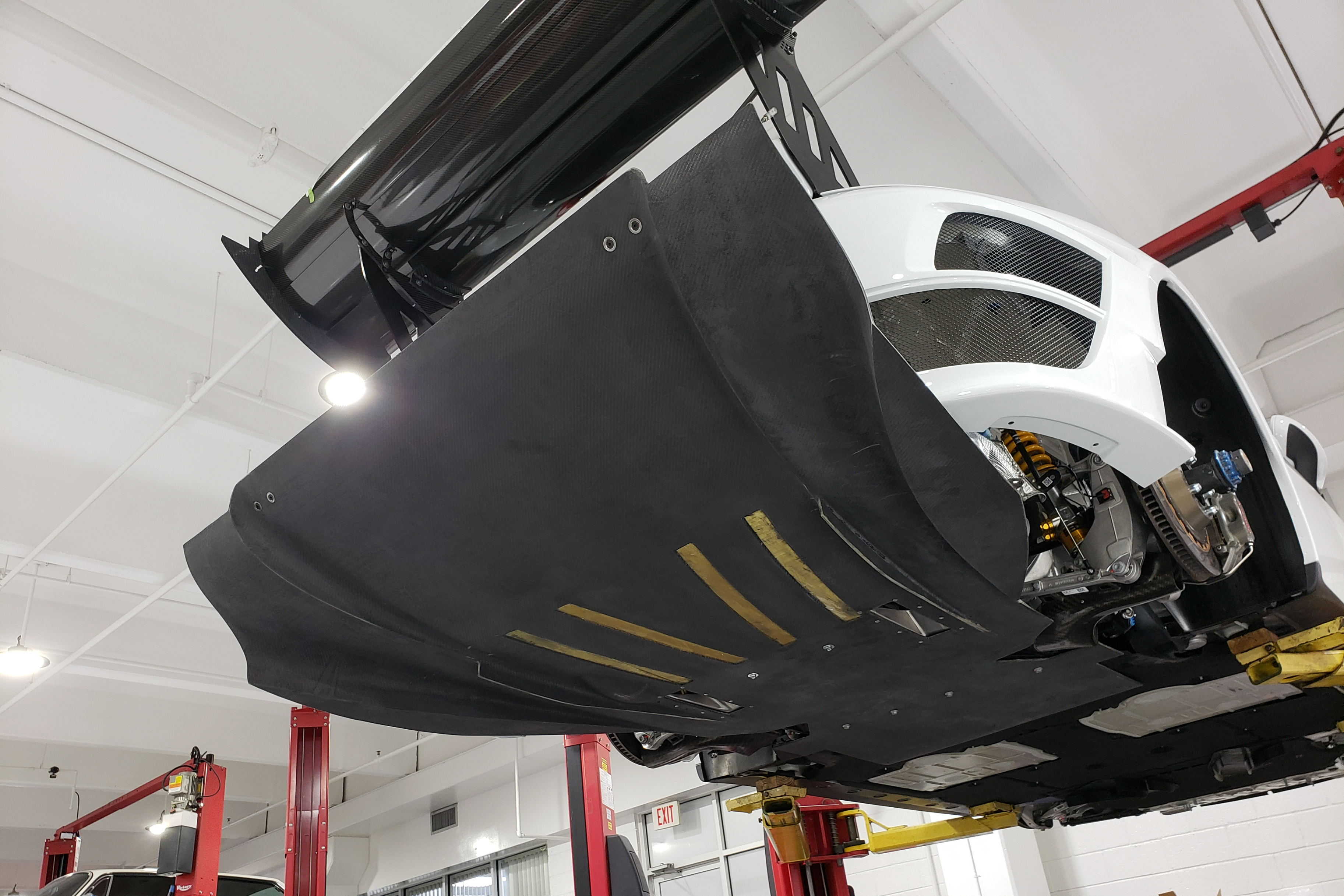
Op 27 juni eindigde een aangepaste 911 Porsche GT2 RS Clubsport-auto van Champion Motorsport (Pompano Beach, Fla., V.S.) als eerste in de Time Attack 1 Division van de 99 th Pikes Peak International Hill Climb in Colorado Springs, Colorado, VS
Een van de geheimen van het succes van het team waren de aerodynamische constructies van de auto:de vleugels, bodemplaten, diffusor en andere onderdelen van het voertuig die de lucht tijdens het rijden efficiënter door het voertuig verplaatsen. Veel van deze componenten zijn 3D-geprint door partner Stratasys (Rehovet, Israël en Eden Prairie, Minn., V.S.), waaronder de succesvolle eerste toepassing voor een nieuwe gereedschapsloze, koolstofvezel-verpakte sandwichkerntechnologie.
Bewijs van 3D-geprinte tooling en kerntechnologieën
Champion Motorsport is al enkele jaren klant van Stratasys, "maar de samenwerking is uitgegroeid tot meer dan de typische leverancier/klantrelatie", zegt Allen Kreemer, senior strategische applicatie-ingenieur bij Stratasys. Zo werkten Stratasys en Champion eerder samen om een nieuwe techniek te testen die Stratasys had ontwikkeld voor oplosbare tooling voor 3D-printen. Met deze technologie wordt een oplosbare plastic kern gevormd voor een kanaal of ander buisvormig onderdeel bedrukt en vervolgens omwikkeld met prepreg van koolstofvezel. Met behulp van een tank voor het verwijderen van oplosbare ondersteuning lost het bedrukte gereedschap op, waardoor een naadloos, afgewerkt, hol composietkanaal achterblijft.
"Dat was echt het begin van onze samenwerking met Champion Motorsport, waar we samenwerkten om dit zeer gecompliceerde, naadloze koolstofvezelkanaal op een niet-traditionele manier te creëren, zonder grenzen zoals bij CNC-bewerking of gieten", zegt Patrick Carey, senior VP – Amerika, producten en oplossingen bij Stratasys.
In 2019 besloten de bedrijven samen te werken aan een project om een nieuwe iteratie van dezelfde technologie te testen:een 3D-geprinte, met koolstofvezel omwikkelde kern die niet oplossen in water, dat is in plaats daarvan een structurele kern voor het voltooide onderdeel of prototype.
Kreemer legt uit dat voor sandwichcomponenten het werken met en vormgeven van kernmaterialen - of het nu gaat om flexibele aluminium honingraat, stijf structureel schuim of iets anders - moeilijk en duur kan zijn, waarbij vormgeving of machinale bewerking vereist is en vervolgens wordt gegoten met de koolstofvezelcomposiethuiden in een speciale mal. Stratasys drukt een stijve honingraatkern af met behulp van SABIC (Riyadh, Saoedi-Arabië) Ultem 1010 kunststof voor hoge temperaturen. "We printen de exacte vorm die op de auto past, en wikkelen ze vervolgens eenvoudig in koolstofvezel, in een zak en uitharden, zonder een mal te gebruiken", zegt Kreemer. "We zijn begonnen met de oplosbare kernen, die onze klanten nog steeds gebruiken, en nu zijn we overgestapt op deze sandwichkernen, die brede toepassingen zullen hebben in de lucht- en ruimtevaart en de automobielindustrie."
"We noemen het 'toolless', en dat is echt de sleutel", voegt Carey toe. "We hebben deze applicatie gemaakt om het hele proces van het bouwen van de mal over te slaan en vervolgens in de mal te leggen." Hij merkt op dat door de eliminatie van gereedschap ook de vorm gemakkelijk kan worden gewijzigd als dat nodig is.
3D-geprinte, bekroonde aerodynamica
Voor het Champion Motorsport-project zijn drie verschillende technologieën verwerkt in de 16 aerodynamische onderdelen die Stratasys in totaal heeft gebouwd voor ofwel prototyping of definitieve installatie op het racevoertuig, legt Carey uit. "We hebben de Ultem 1010 [met koolstofvezel omwikkelde] kernen geprint, we hebben sommige onderdelen 3D geprint met met koolstofvezel gevuld nylon 12 en we hebben onderdelen geprint met nylon 6 wanneer flexibiliteit en slagvastheid vereist waren."
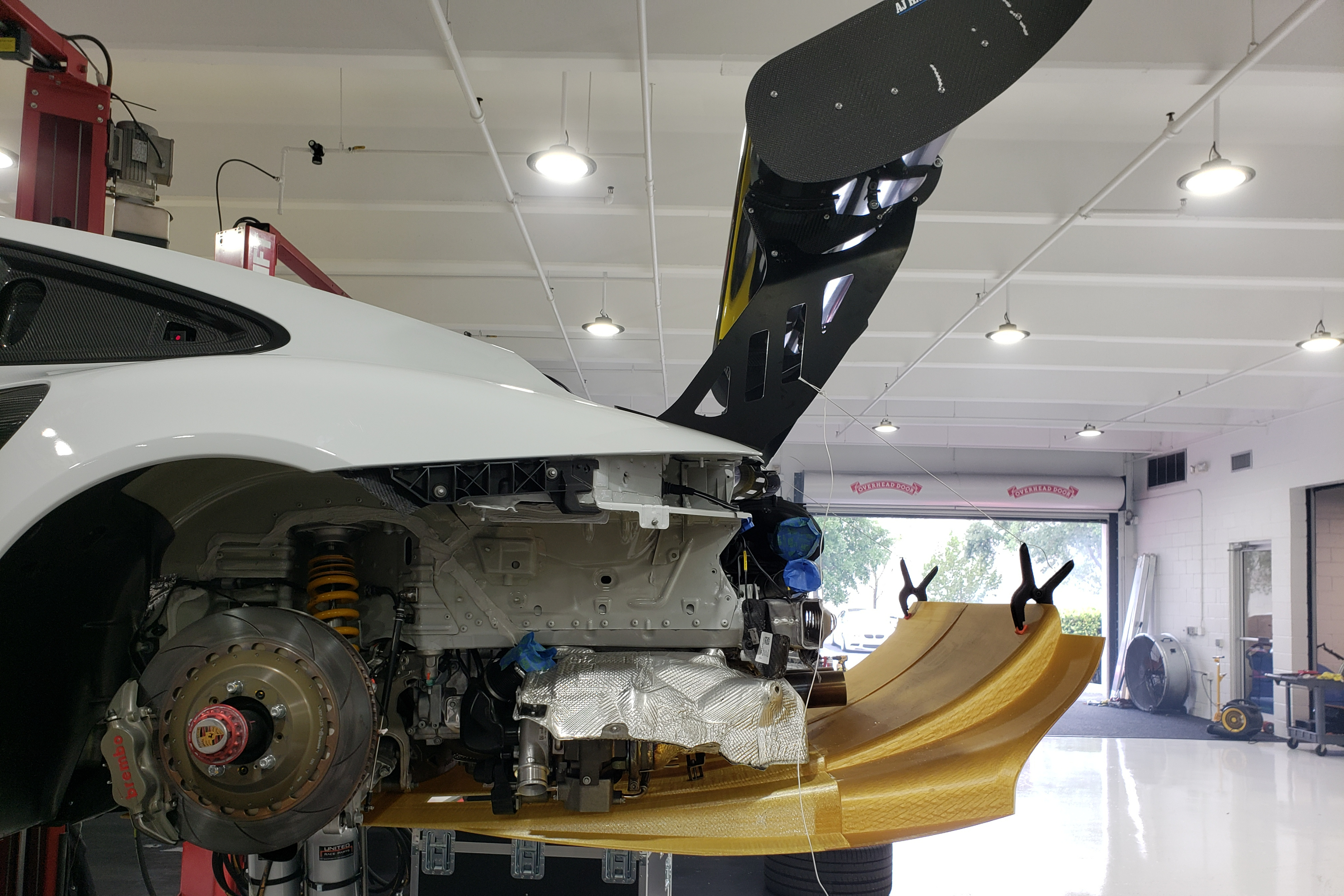
Het grootste deel was een prototype-onderdeel van een diffusor van 2 meter lang en 5 meter breed dat werd gebouwd om het uiteindelijke ontwerp van het onderdeel te testen. Het werd in zeven stukken gedrukt op een F900 fused deposition modelling (FDM) Stratasys-printer met Ultem 1010 polyetherimide (PEI) polymeer, aan elkaar gehecht, in prepreg van koolstofvezel gewikkeld, in zakken gedaan en in de oven uitgehard. De doorlooptijd van het onderdeel was ongeveer vijf dagen voor het printen en iets meer dan 24 uur voor lay-up en uitharding:"Het was extreem snel en wat we op dat moment nodig hadden", zegt Chris Lyew, werktuigbouwkundig ingenieur bij Champion Motorsport.
Veroorzaakt door de onzekerheid of persoonlijke evenementen deze zomer konden worden gehouden vanwege COVID-19, "kwam het project op het laatste moment online en moesten veel systemen tegelijkertijd worden aangepakt", legt Lyew uit. "Aerodynamica is er een van, en het is normaal gesproken een zeer tijdrovend proces" van het ontwerpen, testen en herhalen van de componenten, zegt hij. Conventionele methoden zouden het maken van gereedschap, het met de hand opleggen op de mal en het snijden en passen van de kern vereisen. "Zonder dit proces hadden we onze streefdata voor het testen van de auto op het circuit niet gehaald", zegt Lyew.
De frontsplitter van de auto werd ook op een vergelijkbare manier geprototypeerd en getest. Voor de onderdelen die prototypes waren, werden de uiteindelijke productieonderdelen gemaakt met traditioneel gereedschap, maar het prototypeonderdeel werd gebruikt als een patroon voor het testen van verschillende iteraties. Carey merkt op:"Met een proces zonder gereedschap kunnen we sneller itereren, het testen, dan sneller itereren en het testen. Met traditionele tools zou je nooit kunnen itereren, je maakt er gewoon een en je zit eraan vast. Hier kunnen we echt een rol spelen, testen en ervan leren.”
Een aantal kleinere productie-onderdelen werden ook geproduceerd door Stratasys. Zo waren de winglets aan weerszijden van de voorbumper van de auto bedrukt van 35% met koolstofvezel gevuld nylon 12, de zijskirts van het voertuig werden ook bedrukt in Ultem 1010 met een honingraatvulling aan de binnenkant en vervolgens omhuld met koolstofvezel.
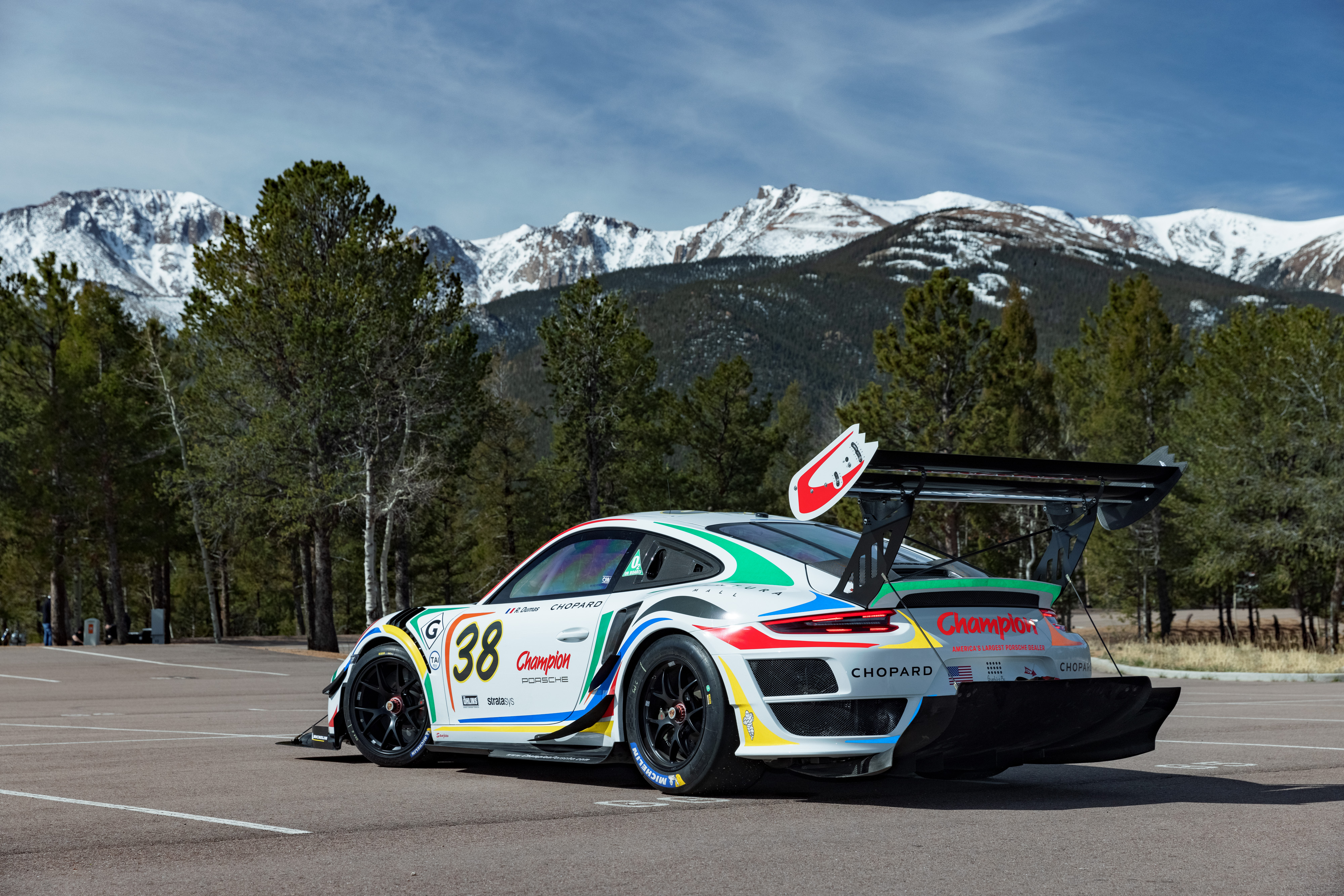
Veel van de aerodynamische "strepen" van de auto - kleine vinachtige stukken die op strategische punten aan de buitenkant van het voertuig worden vastgeschroefd om de luchtstroom rond het voertuig te helpen regelen - werden ook afgedrukt van met koolstofvezel gevuld nylon 12 of niet-versterkt nylon 6. Deze onderdelen zijn zo ontworpen dat ze gemakkelijk opnieuw kunnen worden ontworpen of vervangen als dat nodig is vanwege schade of slijtage. "Bij Pikes Peak zijn er nogal wat ruige terreinkenmerken die mogelijk schade kunnen veroorzaken, dus de mogelijkheid om [de strakes] gemakkelijk te vervangen, was voor ons van cruciaal belang", voegt Lyew toe. Er werden ook verschillende reservesets geprint en geleverd voor gemakkelijke vervanging tijdens de race indien nodig.
Voorbij Pikes Peak
Pikes Peak bleek uiteindelijk een ideale race om deze technologie te testen, zegt Kreemer, vanwege de unieke omgeving die specifiek is voor dit evenement, dat op het hoogste punt op 14.000 voet hoogte wordt gehouden. "Alle raceauto's gebruiken downforce om de auto naar de baan te duwen om grip te krijgen, maar deze specifieke auto's op Pikes Peak zijn anders dan elke andere vorm van motorsport ter wereld, omdat ze echt overdreven aerodynamische effecten nodig hebben om de auto's op de baan te houden [ op die hoogte].” Het resultaat zijn grotere vleugels en andere aerodynamische componenten dan bij welk ander type raceauto dan ook.
In de toekomst is Stratasys van plan om zijn gereedschapsloze geprinte kerntechnologie te introduceren bij andere racebedrijven voor vergelijkbare aerodynamische onderdelen. Carey zegt dat er in de toekomst ook veel andere potentiële toepassingen zijn in auto-, recreatievaart- of zelfs interieuronderdelen in kleine hoeveelheden. "Elke applicatie die iteratie of een aangepast ontwerp vereist, we geloven dat we daar waarde kunnen toevoegen", zegt hij.
Hars
- Materialen:lichtgewicht honingraatproductietechnologie op K 2019
- Evonik vestigt nieuw 3D-printtechnologiecentrum in de VS
- Nieuwe vorm van 3D-geprint materiaal gericht op lichtere, veiligere auto-ontwerpen en meer
- Hoe de veiligheid van geavanceerde ADAS-technologie te garanderen
- EconCore thermoplastische honingraatpaneelproductietechnologie
- Composiet + metaal:holle hybride technologie
- Een zeer gespecialiseerde speler in een team van wereldklasse
- Lineaire bewegingstechnologie
- Arno Strotgen
- printplaat 101
- Wat is landbouwtechnologie?