Fused Deposition Modeling (FDM) Design for Manufacturing-handleiding
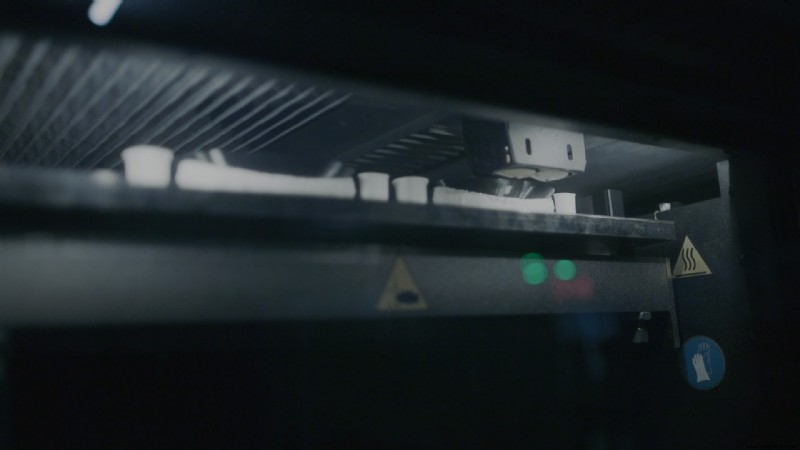
Deze geïllustreerde checklist helpt teams de basisprincipes van ontwerpen voor produceerbaarheid (DFM) met fused deposition modeling (FDM) te begrijpen.
Inleiding
Wat is FDM?
Fused Deposition Modeling (FDM) is een van de meest voorkomende vormen van additive manufacturing en waar de meeste mensen aan denken als ze '3D-printen' horen.
Fused Deposition Modeling Design for Manufacturing Guide Hoe werkt FDM? Tijdens dit proces extrudeert de FDM-machine verwarmd thermoplastisch filament door een mondstuk, waarbij het onderdeel één horizontale laag per keer wordt opgebouwd. Een belangrijk voordeel van het proces is hoe snel de machines onderdelen kunnen produceren in vergelijking met legacy-technologieën. Aangezien doorlooptijden tot 24 uur kunnen zijn, is FDM een nuttig proces voor het maken van betaalbare snelle prototypes en zelfs enkele functionele onderdelen.
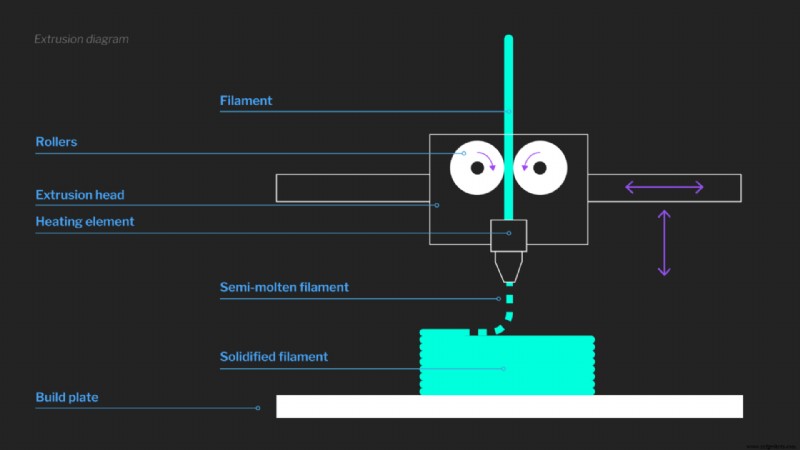
Het gemak van FDM-printen en de toegankelijkheid van FDM-materialen hebben geleid tot de populariteit van de technologie bij zowel professionele als hobbygebruikers, die de technologie kunnen gebruiken om alles te creëren, van speelgoed tot voedsel tot elektronische behuizingen. Procesinnovatie voor FDM is nog steeds aan de gang, met nieuwe mogelijkheden zoals niet-vlak printen, composiet printen en printen met meerdere materialen.
Ontwerpen voor maakbaarheid is belangrijk voor alle ontwerpers en productteams, ongeacht de productietechnologie. Onderdeelontwerpen moeten niet alleen voldoen aan de gewenste functionele en materiaaleisen die van het prototype of het uiteindelijke onderdeel worden verwacht, maar ze moeten ook rekening houden met het fabricageproces zelf.
Deze gids bevat vijf tips om ervoor te zorgen dat uw FDM-geprinte onderdelen van hoge kwaliteit en efficiënt te produceren zijn. Door uw ontwerpen nogmaals te vergelijken met deze lijst voordat u ze voor fabricage indient, kunt u uw onderdeel verbeteren, tijd en middelen besparen en de productietijd versnellen.
1. Houdt uw ontwerp rekening met anisotroop gedrag?
Vanwege de manier waarop FDM-printers lijnen van thermoplastisch materiaal laag voor laag extruderen, is het proces inherent anisotroop, wat betekent dat de mechanische eigenschappen van het onderdeel in verschillende richtingen variëren. Dit komt voort uit het feit dat de hechtsterkte tussen lagen anders is dan de sterkte in het vlak. FDM-geprinte onderdelen bieden de hoogste treksterkte parallel aan het pad van de printkop (binnen het X-Y- of plakvlak). De hechtsterkte tussen lagen heeft invloed op de treksterkte van de Z-richting, die doorgaans minder is dan de treksterkte in het X-Y-vlak.
FDM wordt niet aanbevolen voor het produceren van kritische mechanische componenten, aangezien thermoplasten gevoelig zijn voor materiaalkruip als ze gedurende lange tijd onder hoge spanning worden geplaatst. De bouworiëntatie en geometrie van een onderdeel kunnen worden aangepast om hiermee rekening te houden of dit te verminderen. Evenzo zal het opnemen van afgeschuinde en afgeronde randen in uw onderdelen en gereedschappen hun levensduur verbeteren en spanningsconcentraties verminderen.
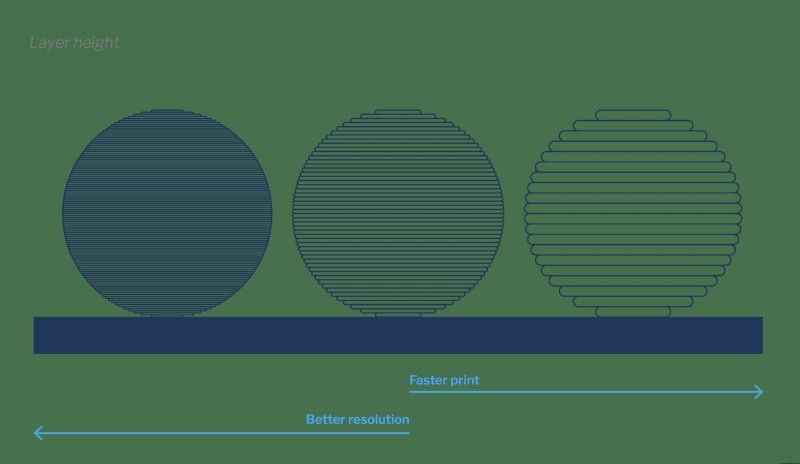
2. Zijn uw tolerantieverwachtingen redelijk?
Productteams moeten weten dat het FDM-proces geen extreem krappe toleranties kan bereiken.
De meeste industriële FDM-machines kunnen een maatnauwkeurigheid bieden van ± 0,15% (ondergrens ± 0,2 mm) en desktopprinters kunnen toleranties bereiken van ± 0,5% (ondergrens ± 0,5 mm). Omdat FDM echter grote hoeveelheden warmte met zich meebrengt, zullen andere factoren, zoals geometrie, invloed hebben op de nauwkeurigheid van het afgedrukte stuk als het afkoelt. Als een onderdeel kritische oppervlakken of gaten met hoge tolerantie vereist met een grotere nauwkeurigheid dan de FDM-printer direct kan bereiken, overweeg dan nabewerkingen of het toevoegen van componenten zoals bussen en inzetstukken met schroefdraad. Vaak kunnen FDM-tolerantieproblemen worden verminderd door verdere nabewerking.
Als het gaat om de tekstgrootte, is de aanbevolen minimale grootte voor tekst in het vlak 6 mm vet, maar de werkelijke waarden verschillen per printer. Tekst op verticale muren kan zo klein zijn als 3,5 mm dik.
Als uw onderdeel dunne openingen bevat, moeten deze een minimale breedte van 5 mm behouden om te garanderen dat het ondersteuningsmateriaal gemakkelijk kan worden verwijderd. Door de constructie van het onderdeel zo te oriënteren dat de openingen loodrecht op het X-Y-vlak staan, kunt u ervoor zorgen dat een goede oppervlakteafwerking behouden blijft.
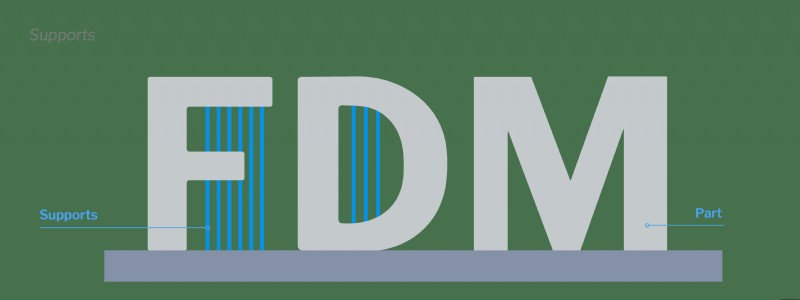
3. Heeft u rekening gehouden met wanddikte, gatafmetingen en uitsteeksels?
De optimale wanddikte voor uw onderdeel wordt bepaald door de afmeting van het filament. Kenmerken die twee keer de dikte van het filament of dunner zijn, worden over het algemeen niet goed afgedrukt. Voor muren is vier keer de filamentdikte voldoende.
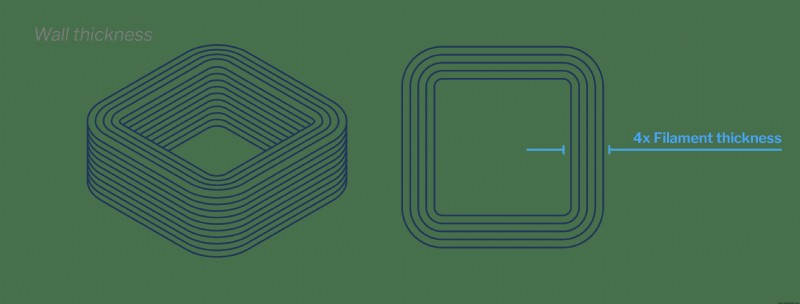
Gesloten, in-plane profielen hebben de neiging om zeer goed te printen met FDM, omdat gesloten lussen snel en naadloos printen mogelijk maken. Voorbeelden hiervan zijn vazen, kopjes en buizen, in plaats van complexe onderdelen met onderbroken zijkanten en scherpe kenmerken. Hoewel het niet nodig is om een mooi onderdeel te bereiken, kan het ontwerpen met dit in gedachten helpen om succesvolle FDM-afdrukken te garanderen.
Gaten die door FDM-printen zijn gemaakt, moeten een diameter hebben die niet kleiner is dan 1 mm om ervoor te zorgen dat de functie goed wordt opgelost. Net als bij openingen kan het oriënteren van gaten om loodrecht op het X-Y-vlak af te drukken de kwaliteit van de kenmerken verbeteren. Het uitboren of ruimen van gaten tijdens de nabewerking is een andere methode om nauwkeurigheid te garanderen.
Aangezien FDM het onderdeel laag voor laag bouwt, zal er, als de overhangen in het onderdeel groot genoeg zijn, niet genoeg ondersteuning zijn om het nieuwe materiaal van de bouwplaat af te houden. Dit materiaal moet ofwel worden ondersteund in de printsoftware met opofferingsgeometrie of het onderdeel moet worden aangepast om de uitsteeksels te elimineren.
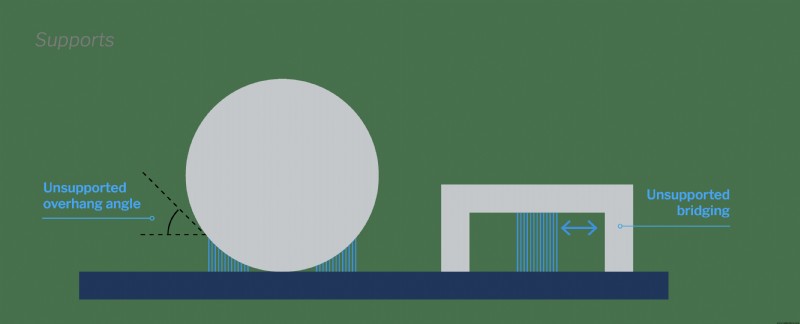
4. Zal uw ontwerp kromtrekken?
Kromtrekken treedt op tijdens het koelproces wanneer verschillende delen van het stuk stollen en krimpen met verschillende snelheden, waardoor interne spanningen ontstaan die het materiaal op een niet-uniforme manier trekken. Hoewel kromtrekken geen probleem is voor alle FDM-geprinte onderdelen, kunnen bepaalde ontwerpkenmerken zoals verticale wanden, dunne secties of kenmerken met hoge beeldverhoudingen de kans vergroten dat een onderdeel kromtrekt tijdens het koelproces.
Warp kan worden vermeden door:
- Ribben toevoegen aan verticale wanden
- Filets toevoegen aan scherpe hoeken
- Extra steunen toevoegen aan de randen van dunne of uitstekende elementen
- Onderdelen vermijden met hoge aspectverhoudingen (lengte-breedte-/dikteverhoudingen)
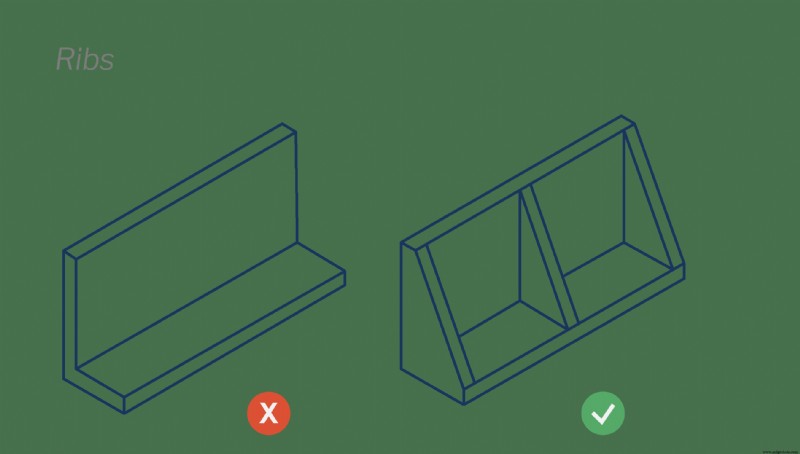
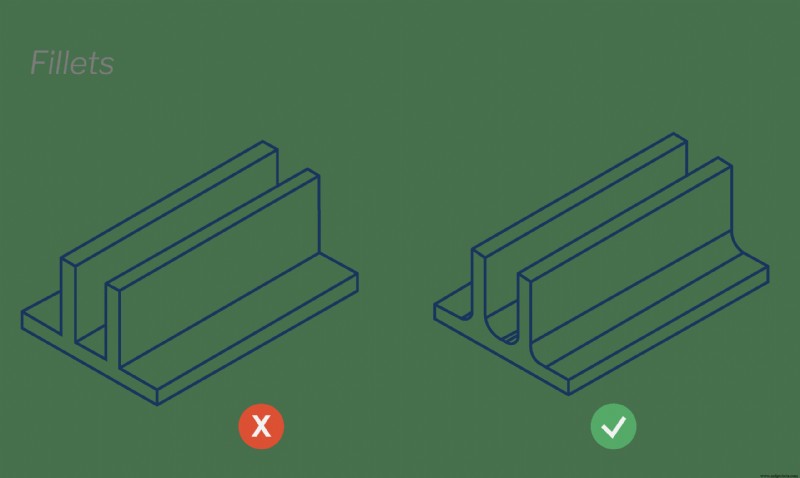
5. Heb je overwogen om onderdelen te snijden voor out-the-box probleemoplossing?
Snijden betekent eenvoudigweg het opdelen van het CAD-bestand van uw onderdeel in kleine, afzonderlijk geprinte componenten. Door te snijden is het mogelijk om onderdelen te bouwen en samen te stellen die te groot zijn voor het bouwvolume van de printer of om de behoefte aan ondersteunende structuren te verminderen. Door breekbare kenmerken afzonderlijk af te drukken, kunt u ook een beter geschikte bouworiëntatie gebruiken, waardoor een sterker, superieur onderdeel wordt geproduceerd. Het snijden van onderdelen vereist echter enige expertise en zorg, aangezien een onderdeel altijd in stukken wordt gesneden.
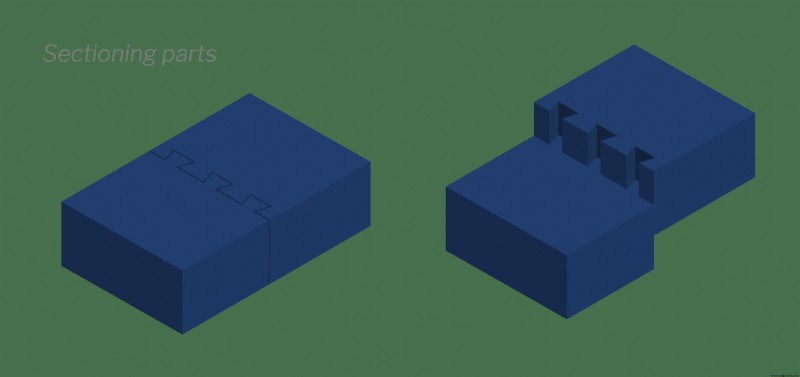
Aan de slag met een DFM-expert
FDM kan een zeer efficiënte en betaalbare methode zijn om thermoplastische prototypes en onderdelen te produceren. Tussen de korte doorlooptijden, de beschikbaarheid van de printtechnologie en de brede materiaalcompatibiliteit is het geen wonder dat zowel hobbyisten als professionals de voordelen van FDM willen benutten.
Wanneer u samenwerkt met een ervaren fabrikant als Fast Radius, kunt u er zeker van zijn dat met al deze overwegingen - en nog veel meer - rekening zal worden gehouden. Ons team van ingenieurs en productmanagers maakt gebruik van geavanceerde digitale ontwerptechnologieën en tientallen jaren ervaring om ervoor te zorgen dat elk onderdeel dat we produceren het best mogelijke onderdeel is voor de klus. Niet alleen dat, ons team werkt tijdens elke stap nauw samen met klanten, van ontwerp tot uitvoering, om ervoor te zorgen dat elk onderdeel is geoptimaliseerd voor eindgebruik en maakbaarheid.
Neem vandaag nog contact met ons op voor meer informatie over hoe we uw ideeën kunnen verwezenlijken.
Bezoek het Fast Radius resource center voor meer informatie over additive manufacturing, CNC-bewerking en onze andere productieprocessen.
Download het ontwerp voor fused deposition modeling (FDM) voor fabricagehandleiding.
Klaar om uw onderdelen te maken met Fast Radius?
Start uw offerteIndustriële technologie
- Ontwerp voor maakbaarheid:een handleiding
- Proces voor de productie van ijzercarbide
- Ontwerp voor het vervaardigen van PCB's
- Wat is FDM (Fused Deposition Modeling) 3D-printen? Uitgelegd door Hubs
- Spuitgietpoortontwerp:een ultieme gids voor kunststofproductie
- Gids voor werknemersveiligheid voor de maakindustrie
- Ultiboard – de ultieme gids voor beginners
- Fused Deposition Modeling (FDM) 3D-printontwerptips
- Fused Deposition Modeling (FDM) 3D Printing:technologieoverzicht
- Waarom is design for manufacturing belangrijk?
- 5 Snijproces voor metaal in productie