Verouderde machines kunnen worden gedolven voor moderne operaties
Nog maar twee jaar geleden, toen Brad Klippstein van Okuma America wat operationele gegevens uit een verouderde bewerkingsmachine wilde persen, moest hij tientallen draden aansluiten op de schakelkast en een PLC toevoegen. Toen hij klaar was, stroomden de gegevens van de bewerkingsmachine naar de PLC en vervolgens naar een hub of server waar ze worden opgeslagen.
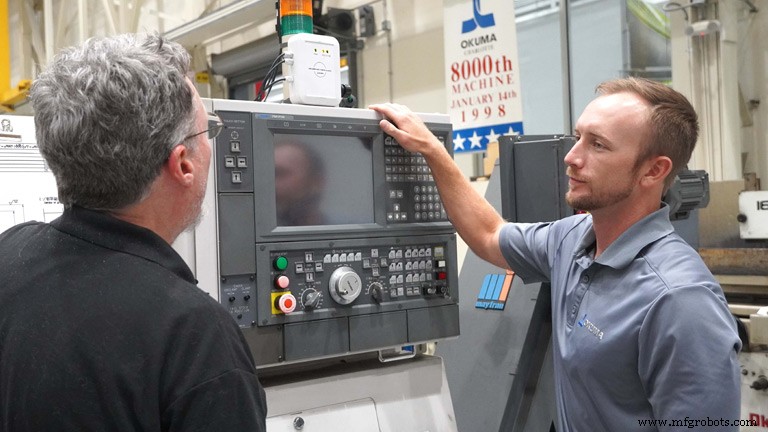
"We hebben dingen als Ethernet en Wi-Fi en al deze technologie die we tegenwoordig kunnen gebruiken", zegt Klippstein, supervisor productspecialist. “Maar apparatuur van meer dan 30 jaar geleden had die mogelijkheid niet, dus je moest fysiek een apparaat aansluiten op de schakelkast om al die gegevens eruit te halen. Nu hoeven we niet eens een harde verbinding te hebben [met nieuwe machines]. Je kunt dingen draadloos doen. Dat is de transitie van de afgelopen 30-40 jaar.”
Een deel van de taak van Klippstein is om klanten te helpen discrete stappen te zetten in de verbonden, gedigitaliseerde en gegevensgestuurde wereld van Industrie 4.0, voor nieuwe en oudere bewerkingsmachines.
Deze voordelen kunnen zijn:
- Realtime bewaking van bewerkingsmachines, in de fabriek of vanaf een externe locatie
- Verhoogde productiviteit en kwaliteit
- Bias-free rapportage
- Acquisitierechtvaardiging
- Voorspellend onderhoud
- Toptalent aantrekken en behouden dat enthousiast is over het vooruitzicht om nieuwe dingen te leren en voorop te lopen in moderne processen.
Of ze nu via kabels of door de lucht worden verzonden, gegevens die zijn verzameld van fabrieksapparaten kunnen een winkeleigenaar helpen slimmere zakelijke beslissingen te nemen.
Met analyse van de beschikbare gegevens hebben werknemers een beter zicht op de activiteiten op de werkvloer, wat hen kan helpen problemen op te lossen, processen te verbeteren en de productiviteit te verhogen.
Met een recente vooruitgang heeft die winkeleigenaar misschien niet eens meer iemand als Klippstein nodig voor zijn oude werktuigmachines.
In 2019 kwam Okuma met NET BOX suite-C Quick als een goedkoper alternatief voor een technische oplossing om gegevens van oudere machines te verzamelen. De NET BOX CQ, kortweg, wordt rechtstreeks aangesloten op een signaaltoren en vervolgens op een hub of apparaat dat wordt gebruikt om signalen binnen te halen.
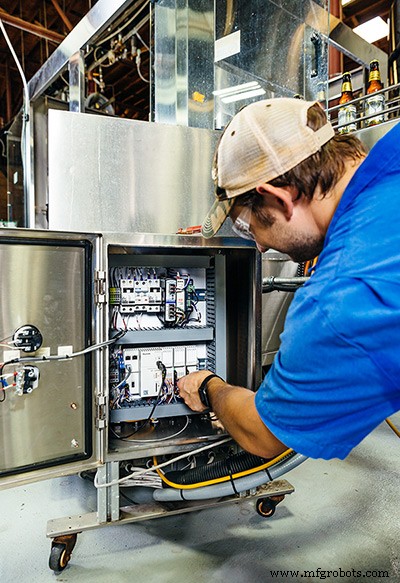
NET BOX CQ gebruikt drie optische sensoren - één voor de groene, gele en rode lichten op de toren - en zet de informatie die ze verzamelen om in een formaat dat door een computersysteem kan worden gelezen. Om gegevens die door een van zijn software worden verzameld te standaardiseren, gebruikt Okuma MT Connect, een open-source, veelgebruikt communicatieprotocol.
"Het is eenvoudig te installeren en je hebt geen Okuma-technicus nodig om het te doen", zei Klippstein over NET BOX CQ.
Om te beginnen is het vermogen om te zien of een machine draait een geweldige maatstaf om te volgen, omdat een winkeleigenaar gewoonlijk elk apparaat tot maximale productie wil pushen. Hij wil dat zijn algehele effectiviteit van apparatuur (OEE) in het bereik van 65-85 procent ligt, omdat een machine alleen geld verdient als hij draait.
"Dus, gewoon door die informatie te trekken - groen, geel, rood - kan ik dat in de loop van de tijd volgen en trenden en op zijn minst zien wanneer er stilstand is opgetreden en voor hoe lang," zei Klippstein. "En dan zou ik de volgende stap nemen en zeggen:'Waarom is dit gebeurd en waarom gebeurt het nog steeds elke dag om 2.30 uur?' Dus nu kan ik dingen trenden. Dat zet me in ieder geval een stap in de goede richting.”
Christopher Rezny, centrale regionale manager van Fastems, leverancier van fabrieksautomatisering, zei dat hoewel de software van MT Connect en Okuma zeer goede middelen zijn voor het verzamelen van gegevens, de beperkte hoeveelheid beschikbare gegevens van een legacy-machine niet hun enige nadeel is in vergelijking met moderne machines.
"Interfaces van oudere, legacy-machines terug naar andere interne software die wordt gebruikt, bijvoorbeeld een ERP-systeem, zijn ook zeer beperkt of zelfs niet aanwezig", zei hij. "Er kunnen ook problemen zijn met de feedbackmechanismen van deze oudere machines met betrekking tot veiligheidsprotocollen voor de gebruiker."
Werknemers op de werkvloer moeten klaar zijn voor verandering
Ondanks de beperkingen die Rezny beschreef, zijn er genoeg data en machines voor bedrijven als Okuma en Excellerant Manufacturing om mee te werken.
"De meeste winkels hebben oudere apparatuur", zegt John Carpenter, president van Excellerant Manufacturing. “De meeste mensen komen naar ons vanwege onze geschiedenis met verouderde apparatuur - die kasten van binnen en van buiten kennen - omdat we door de jaren heen letterlijk tienduizenden CNC-machines hebben verbonden en we hebben verzameld wat ik handelsgeheimen zou noemen over wat de beste manier om deze oudere apparatuur aan te sluiten.”
Het eerste doel wanneer een nieuwe klant wordt gebeld, is te begrijpen wat hij of zij wil. Probeert die persoon gewoon gegevens van de fabrieksvloer naar boven te halen, zodat iedereen weet wat er aan de hand is?
"Het gaat erom welk probleem je probeert op te lossen," zei Carpenter. “En laten we je dan de basis geven om mee te beginnen. De meeste fabrieken hebben de gegevens die er zijn niet volledig gewaardeerd. Ze kruipen nu. Ik zal winkels binnenlopen en medelijden met ze hebben omdat ze nog niet eens het kruipstadium hebben bereikt."
Carpenter herinnerde zich een klant waar het management basistransparantie wilde:gegevens over wat er op de werkvloer gebeurde. En werknemers op de werkvloer drongen tegen het verzamelen van de gegevens terug uit angst dat Big Brother ze zou bekijken.
Carpenter liet het probleem over aan het winkelmanagement. Maar hij erkende dat de arbeiders geen keus hadden. Hij wist dat winkelleiders gegevens zochten om de productie te meten en processen te verbeteren, niet als een Big Brother-tactiek. Helaas had het management zijn medewerkers niet voorbereid op de verhuizing.
"Het opent zoveel ogen op zoveel niveaus, maar je mensen moeten klaar zijn voor de verandering", zei hij.
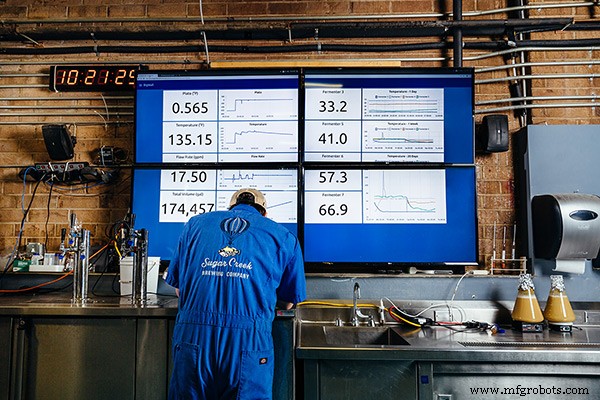
Zodra de basis wordt gevolgd:snijden we? Als we snijden, is dat dan 100 procent? En als dat niet het geval is, bevinden we ons dan in een verminderde productiemodus? En de gegevens worden ingevoerd in Excellerant's realtime machinegegevens- en communicatieplatform, het is mogelijk om talloze sensoren en transducers toe te voegen om meer gegevens te krijgen.
Er kunnen sensoren worden ingebouwd om temperatuur, trillingen, druk, stroming, concentratie en meer te meten.
"Je moet bepalen wat belangrijk is," zei Carpenter. “We kunnen allerlei data verzamelen vanaf een punt op een werkvloer. Er is een enorme hoeveelheid gegevens wanneer u zich bezighoudt met trillingsanalyse en gereedschapsonderbrekingen. De lijst gaat maar door.”
Er is altijd een manier om meer gegevens te verzamelen, maar soms wordt het onbetaalbaar, zei hij. De winkeleigenaar moet bepalen hoeveel hij aan een sensor wil uitgeven om zijn gegevens naar een hoger niveau te tillen.
"Als je dit rond een of ander OEE-project wikkelt, is het meestal een snelle ROI," zei Carpenter.
Ken de vragen die je moet stellen
"Dit is duidelijk een sectorbreed probleem, maar de vragen die we krijgen vallen meestal in twee categorieën", zegt Cory Weber, senior industrieel IoT-architect bij Bosch Rexroth. “Het is:hoe verhoog ik de kwaliteit van mijn productie met IoT of IIoT? Of het is:hoe verhoog ik mijn efficiëntie?
"De andere vraag die daarbij komt kijken is:hoe verlaag ik mijn productiekosten?"
Naast hulp bij het beantwoorden van deze productiegerelateerde vragen, schat Weber dat 90 procent van de klanten realtime visualisatie en bewaking van bewerkingsmachines wil, zowel op locatie als op afstand.
"Het is de eerste stap, toch?" hij zei. "Wat doet mijn [geautomatiseerde lijn of bewerkingsmachine]?"
De oplossing van Bosch Rexroth om gegevens uit oudere machines te persen, is een IoT-gateway genaamd PR-21, een kleine computer met één printplaat die is gehard voor industriële omgevingen. Het heeft ook een IIoT-platform, ctrlX CORE, om gegevens op te halen en te verwerken en deze naar de opslag op een lokale server of in de cloud te verplaatsen.
Een van de meest voorkomende toepassingen die Weber heeft gezien voor het gebruik van verzamelde gegevens is die van preventief onderhoud.
Slimme, gegevensgestuurde aanpassingen in een onderhoudsschema zijn een manier om werktuigmachines draaiende te houden en tegelijkertijd de productiekosten te verlagen door afval te verminderen.
"Ik weet dat we zelfs in onze eigen faciliteiten dingen hebben gedaan zoals het overschakelen naar gebruiksuren in plaats van gepland onderhoud voor [kalender]", zei Weber.
Zo heeft Bosch Rexroth een hydraulische testruimte waar arbeiders vroeger elke twee weken de vloeistof verversten. Nadat ze de machine continu hadden gecontroleerd, waren ze in staat om het vloeistofvervangingsschema te herzien naar een schema op basis van gebruikstijd versus kalendertijd.
"Als je het hebt over 50-60 gallons hydraulische vloeistof of meer, kan dat prijzig worden", zei hij.
Andere soorten vloeistoffen hebben parameters ingesteld waaraan moet worden voldaan voor optimaal gebruik, ongeacht of deze zijn gebaseerd op concentratie, blootstelling aan hitte of andere factoren.
"Als u regelmatig kunt testen, kunt u uw onderhoud naar behoefte wijzigen en kunt u veel geld besparen en uw kwaliteit beschermen", zegt Weber. "Het is een aantrekkelijk verkoopargument en relatief laaghangend fruit."
Weber heeft domeinkennis opgedaan voor productie terwijl hij opgroeide:zijn vader heeft een klein productiebedrijf. Zijn opleiding is echter in informatietechnologie. Zowel kennis van het productiedomein als datasmarts zijn nodig om te profiteren van de implementatie van Industrie 4.0, zei hij.
"Je hebt iemand nodig die het eigenlijke proces begrijpt", zei hij. "En iemand die het proces begrijpt, kan naar de gegevens kijken en zeggen:'Dit ziet er niet uit zoals het hoort'."
Als de gegevens eenmaal in de hand zijn, zijn de mogelijkheden eindeloos, afhankelijk van hoeveel de gebruiker ze wil verwerken.
Als een winkeleigenaar het geluk heeft iemand te hebben met een echte datawetenschapsachtergrond, kan hij zich zelfs wagen aan kunstmatige intelligentie.
"Het is een kwestie van voldoende gegevens verzamelen om ze waardevol te maken en dan, en ik kan dit niet genoeg benadrukken, weten welke vragen je van de gegevens wilt stellen," zei hij.
Het datagerelateerde advies van Weber is natuurlijk van toepassing op zowel nieuwe als oudere machines. Datamining voor slimme operaties geldt voor beide.
Automatisering Besturingssysteem
- Digital Twins kan de intelligente voorsprong zijn voor IoT in de productiesector – deel 2
- Het verzamelen van gegevens van verouderde systemen om de bedrijfsvoering te verbeteren
- Robotisch lassen:vindt u ROI voor kleine batchproductieactiviteiten?
- ABB test automatiseringsoplossing voor datacenters
- Arch Systems werkt samen met Flex voor transformatie van productiegegevens
- Smart Home-upgrades voor modern leven
- Legacy-apparatuur en IIoT:kunt u een oude hond nieuwe trucs leren?
- Hoe fabrikanten Analytics kunnen gebruiken voor een betere klantervaring
- Industriële automatisering maakt plaats voor informatieautomatisering
- Drie manieren waarop AI de productieprocessen verbetert
- Effectieve HR voor de moderne productieomgeving - wat is het geheim?