Ga voor prestaties zonder downtime door 'het bloed van de machine te testen'
Halverwege de jaren 2000 crashte het persluchtsysteem in de Toyota North America-fabriek in Georgetown, Kentucky, gemiddeld meer dan eens per jaar. Dat leidde ertoe dat sommigen in de fabriek zich afvroegen of het gebruik van machine learning en AI dit probleem zou kunnen aanpakken door anomaliedetectie, foutidentificatie en, belangrijker nog, voorspelling van dreigende storingen voordat ze optreden.
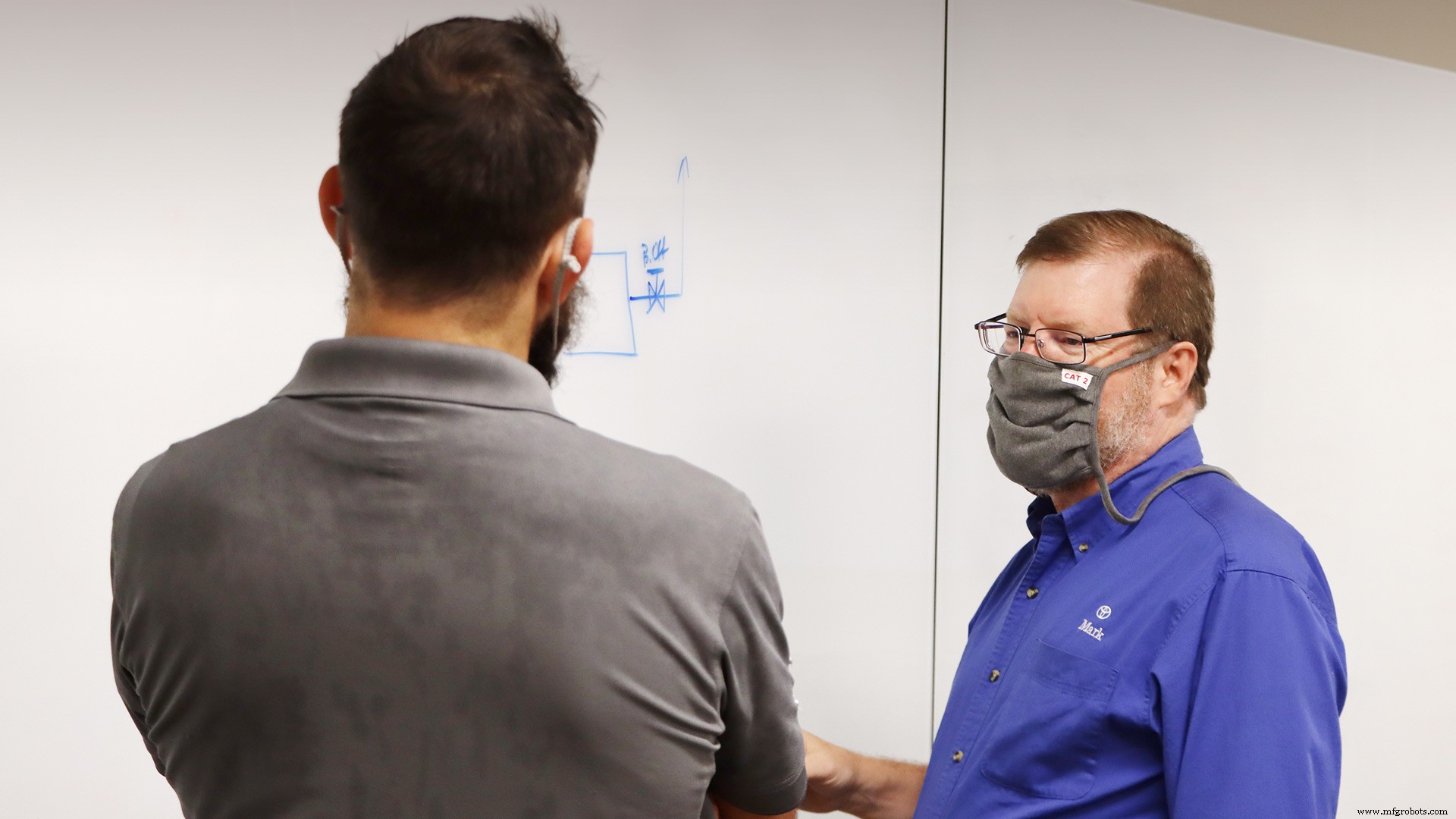
Ongeplande stilstand van het persluchtsysteem betekende natuurlijk dat de hele fabriek een probleem had. De spuiterij gebruikte perslucht om nieuwe voertuigen te spuiten. Het systeem bracht luchtgereedschap tot leven, en niets vergeleken met perslucht voor het wegblazen van schuur- en andere resten.
Met een voltooid voertuig dat elke 25 seconden tijdens twee ploegen van een van de drie lijnen in de fabriek rolt, waren de gevolgen aanzienlijk als de persluchtvoorziening zou uitvallen.
"De kosten, als de lijn uitvalt, zijn enorm", zegt Mark Rucker, projectmanager en expert op het gebied van elektrische materie bij de fabriek. "Dus er is een goede stimulans om een goed, betrouwbaar en stabiel hulpprogramma te hebben."
Het miljoenen dollars kostende persluchtsysteem bestaat uit een tiental Ingersoll Rand centrifugale luchtcompressoren, elk ter grootte van een kleine semi-vrachtwagen. De eindtrapbladen van elke compressor draaien met 20.000 tpm op een fractie van een inch van hun behuizing. Als een mes het minste beetje buiten de specificaties werkt en de behuizing raakt, is het een goner. De hele machine moet worden herbouwd voor ongeveer $ 100.000.
Het wiebelen van het blad is echter niet de oorzaak van een crash; het is het resultaat.
De crash - ook bekend als een stroomstoot of omgekeerde stroom - dit gebeurt wanneer iets ervoor zorgt dat de normale luchtstroom van de compressor naar een leiding zichzelf probeert om te keren en de lucht in de leiding terugdringt.
De frequentie, kosten en gevolgen van crashes waren voor Toyota aanleiding om Jay Lee, oprichter en directeur van Intelligent Maintenance Systems, om hulp te vragen.
Jay Lee liep voor op de Industry 4.0-curve
Aan het begin van het nieuwe millennium, voorafgaand aan het telefoontje van Toyota, was Lee een technische professor aan de Universiteit van Cincinnati, die zich alle machines in een fabriek voorstelde die verbonden waren en gegevens leverden voor intelligent onderhoud. In die tijd bestond echter nog veel van de technologie die nodig was om Lee's visie te realiseren.
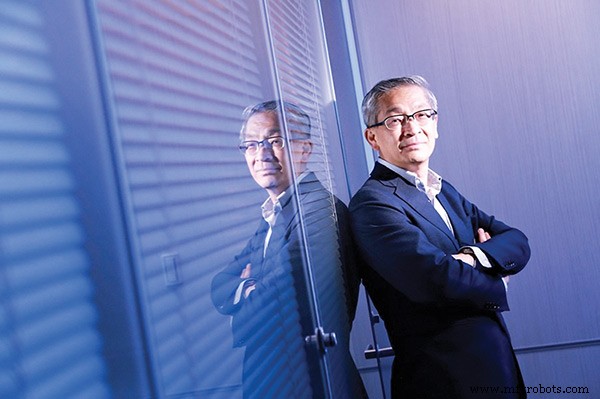
"Twintig jaar geleden geloofden maar heel weinig mensen dat het mogelijk was", zegt Lee, die momenteel met verlof is van het lesgeven en vice-voorzitter en bestuurslid is van Foxconn Technology Group in Wisconsin.
In zijn industriële visie zijn machines als patiënten en gegevens verzameld van sensoren die machines bewaken, geven informatie over hun gezondheid. Experts leiden prognoses af door de gegevens die ze verzamelen en analyseren te interpreteren.
"Ik zei:'Waarom test je het bloed van de machine niet?' En wat is het bloed van de machine?" zei Lee. "Gegevens. De vraag is:'Welke gegevens wil je krijgen?' Het hangt af van wat je wilt analyseren. We moeten de context en inhoud begrijpen en een relatiemodel tussen de onzichtbare onbekenden verder formuleren.”
Verborgen in de data zit betekenis over afwijkend gedrag van een machine of een proces. Het ontsluiten van die betekenis leidt tot het voorspellen van kwaliteit, het bepalen van de stabiliteit van de machine of het proces en het voorkomen van mogelijke storingen. "Dat is precies waar Industrie 4.0 vandaag de dag over gaat", zei Lee.
De term 'Industrie 4.0' werd natuurlijk pas populair rond de tijd van het initiatief van de Duitse regering in 2013.
Geen crashes sinds 2006
Eenmaal bij Toyota werkten Lee en zijn team van data-analisten samen met Rucker en een groep bekwame onderhoudsmedewerkers en fabrieksingenieurs om het probleem met het persluchtsysteem aan te pakken.
De eenvoud van hun vragen logenstraft de complexiteit van de taak die voor ons ligt.
"Kunnen we een reverse-flow-probleem voorspellen voordat het een crash veroorzaakt?" zei Rucker. "Kunnen we op tijd iets zien ontwikkelen om er iets aan te doen?"
Na maanden van vallen en opstaan in 2005 verzamelde en analyseerde het team high-fidelity-gegevens van een van de compressoren en zocht naar afwijkingen. Soms creëerde het team een piek- of naderings-tot-piekconditie zodat ze de machine konden dwingen afwijkend gedrag te vertonen en te zien hoe dat eruit zag in de dataset.
Uiteindelijk wierp het werk van het team zijn vruchten af. De leden zagen dat de beste voorspeller van een beginnende piektoestand plaatsvond in fase twee (van de vier fasen die de compressor doorloopt die voortgang van normale druk naar 120 pond druk per vierkante inch of PSI).
"Wat is de fysica daarachter, waarom is dit de voorspeller?" zei Rucker. “Weet niet, maakt niet uit. We hebben zojuist gezien dat dit betrouwbaar een toekomstige stijging voorspelt, en het voorspelt dit met seconden waarschuwing.”
De volgende stap was om een differentiële sensor op elke compressor te plaatsen en een machine-learning algoritme voor de centrale besturingseenheid te creëren. Tests bevestigden dat zodra fase twee begon te "wankelen", de compressor achteruit zou gaan.
"Elke keer dat we het testten, hield het ons uit de problemen", zei hij. "We hebben sinds 2006 geen crashes meer gehad."
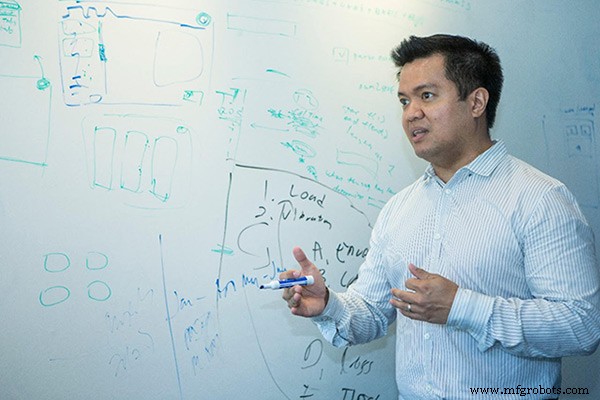
Hoewel het compressor-surge-project een succes was, faalde een ander dat zich richtte op het voorspellen van de levensduur van lagers in de persluchtreuzen. Het team kon niet genoeg betrouwbare onderhoudsgegevens vinden en deze koppelen aan de operationele gegevens van de machine om bruikbare correlaties te trekken, zei Rucker.
"Dat is waarschijnlijk ongeveer de juiste mix van R&D", zei hij. “Je probeert dingen, en je weet niet of het gaat werken of niet. En als je de helft van de tijd je geld terugkrijgt, is dat een overwinning. En zo nu en dan vind je diegene die voor al het andere betaalt, zoals de overspanningsregeling.'
Flexibiliteit is de sleutel
Lee publiceerde vervolgens een paper over het Toyota-project en hielp in 2013 bij de oprichting van Predictronics met Patrick Brown, een medewerker van Intelligent Maintenance Systems, en twee van zijn universiteitsstudenten, David Siegel en Edzel Lapira. Bruin. Lapira en Siegel vormen de Predictronics C-suite.
Zoals Toyota's Rucker Lee inschakelde voor AI-hulp, komen bedrijven naar Predictronics voor hulp bij hun ambities zonder downtime.
"Verschillende klanten hebben meestal verschillende niveaus van volwassenheid", zegt Lapira, die CEO is. “We hebben een aantal klanten die al een dataverzamelingsstructuur hebben:ze hebben een datameer, maar ze weten niet wat ze met de data moeten doen. We hebben ook een aantal klanten die helemaal opnieuw moeten beginnen.”
Klanten met activa van 50 of 60 jaar oud moeten in een nog vroeger stadium beginnen.
Steeds vaker wordt Predictronics benaderd door klanten met legacy machines. Lapira en zijn collega's sturen ze op zoek naar componenten zoals versnellingsmeters en transducers.
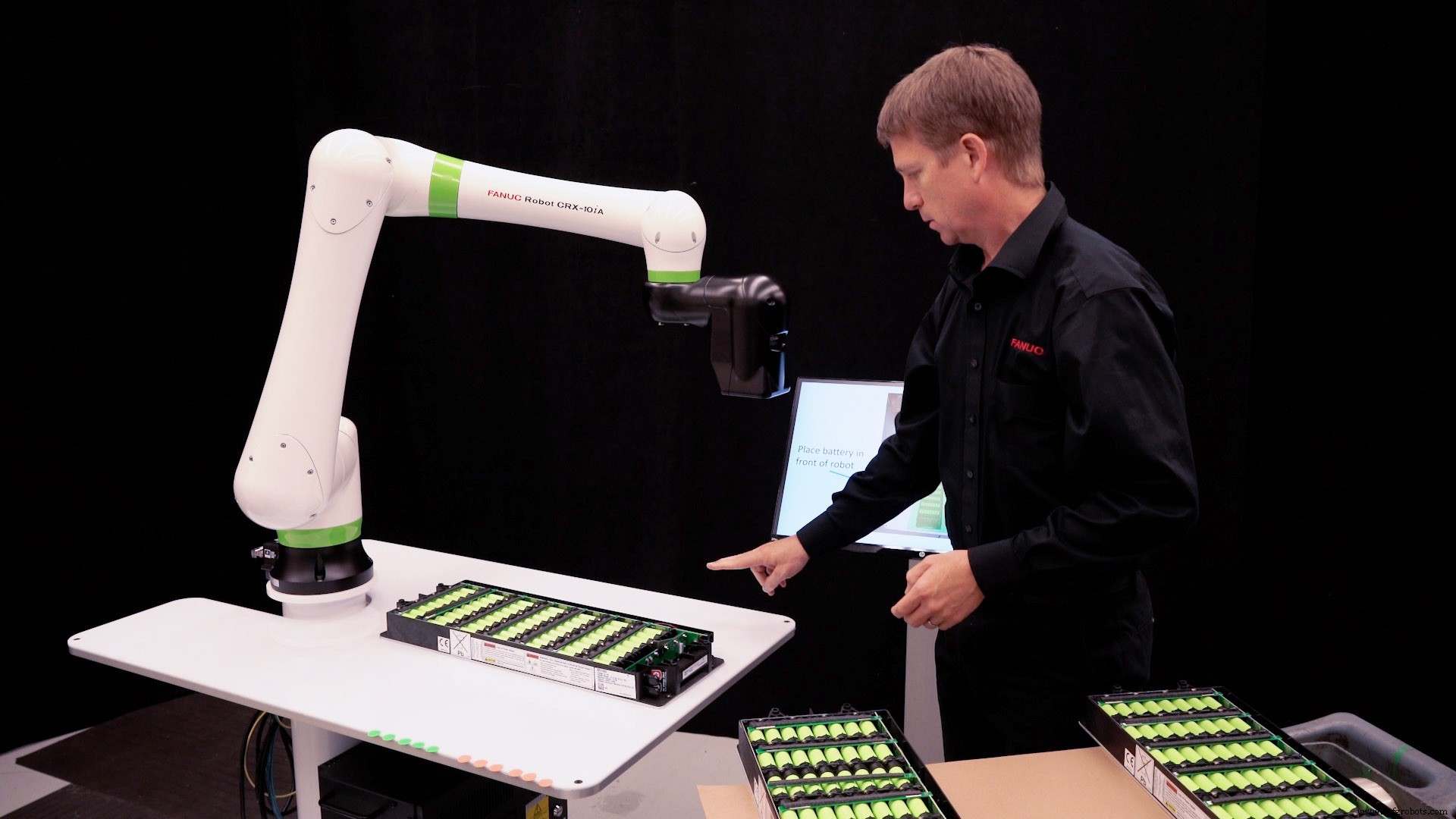
"Dit zijn de verschillende analoog-naar-digitaal-converters die we nodig hebben om die gegevens eruit te krijgen," zei hij.
Sinds de oprichting in 2013 heeft Predictronics meer dan 70 fabrieken geholpen met AI-oplossingen, waaronder veel Fortune 500-bedrijven.
Predictronics werkte samen met één klant, een fabrikant van halfgeleiders, om een voorspellende oplossing voor virtuele metrologie te ontwikkelen die de relatie tussen sensor- en meetvariabelen kon leren.
Het project was een uitdaging vanwege de honderden gemeten signalen die door de halfgeleiderapparatuur werden weggeslingerd.
Maar er zijn bekende statistische methoden om het aantal mogelijkheden te beperken, zei Siegel.
"Naast die methoden, is het de afgelopen jaren meer van de machine learning-gemeenschap geweest die methoden heeft ontwikkeld die een classificatieregressie-algoritme bevatten met een ingebouwd onderdeel voor variabele selectie," zei hij. "Dus dat beperkt het tot de top 10, of 20 of 30 variabelen. Vervolgens werk je samen met de klant of gebruik je je eigen kennis om te bepalen wat het meest zinvol is om op te nemen in de software en het analysemodel.”
Of Predictronics nu kennis uit eerdere ervaring toepast in zijn op sjablonen gebaseerde aanpak, die helpt de kosten laag te houden, of een oplossing die is geformuleerd in een deel van een bedrijf dat vervolgens in-house kan worden opgeschaald, "het vinden van een oplossing die direct de meest kritieke problemen, maar is ook flexibel genoeg om op andere problemen te worden toegepast, is de sleutel, "zei Brown.
Due diligence AI
Fabrieken die op zoek zijn naar een leverancier van AI-oplossingen zoals Toyota deed voor zijn persluchtprobleem, moeten hun uiterste best doen om de juiste oplossing te vinden.
Het helpt om de juiste vragen te weten te stellen, zeiden de experts van Predictronics:
Waar zijn uw services eerder gebruikt?
Heeft uw oplossing een duidelijke verbetering van de bedrijfsvoering aangetoond in termen van verminderde uitvaltijd of verhoogde kwaliteit?
Is uw oplossing in mijn branche gebruikt?
Heeft uw team kennis van industriële domeinen?
Werkt uw oplossing met oudere apparatuur?
Werkt uw oplossing met verschillende sensoren?
Maakt uw oplossing gebruik van machine learning?
Hoeveel gegevens zijn er nodig om het model te trainen?
Heeft het alleen gegevens van een gezonde machine of gegevens van een defecte of defecte machine nodig om van te leren?
Robots willen ook AI
Hoewel de werktuigmachines in een werkplaats beter presteren onder invloed van AI, is er geen reden waarom robots niet hetzelfde kunnen doen.
Fanuc America heeft onlangs "AI Error Proofing" toegevoegd aan zijn robotcontroller en de vision-functie van de robots, iRVision, die machine learning (ML) gebruikt voor onderdeelinspectie.
Met de foutbestendige mogelijkheid gebruikt een operator afbeeldingen om de ML te trainen om te controleren op twee verschillende situaties (bijvoorbeeld of er een gelaste moer aanwezig of afwezig is) en om een onderdeel te accepteren of af te wijzen.
Omdat iRVision maar liefst 27 camera's kan ondersteunen, kan de foutbeveiligingsfunctie op evenveel punten in het productieproces optreden.
"Je wilt afkeuringen of fouten identificeren voordat je waarde blijft toevoegen aan een slecht onderdeel", zegt Josh Person, stafingenieur bij Fanuc's machine vision-groep.
"Vaak zie je een fout in het ene stadium en de volgende fase zou het verdoezelen," voegde hij eraan toe.
Tijdens het instellen kan de operator meerdere voorbeelden van werkstukken presenteren en deze in twee categorieën indelen:goed en slecht. Als het voorbeeld niet in een van beide klassen valt, wordt "onbepaald" weergegeven. Onbepaalde voorbeelden kunnen dan worden toegevoegd om het geleerde model te verbeteren.
Automatisering Besturingssysteem
- SIGHT:For the Blind
- De voordelen van DevOps beoordelen voor het testen van IoT-prestaties
- Automatisering:wat het betekent voor de toekomst van het bedrijfsleven
- De toekomst voor contactloze bezorging
- Bedankt voor de herinneringen!
- De voordelen van automatisering voor uw bedrijf
- Hoe u het juiste filter kiest voor uw toepassing
- Vijf manieren om de juiste compressor voor de thuishobbyist te vinden
- Richtlijnen voor het selecteren van de juiste leverancier van persluchtdiensten
- Verwelkoming van Dorothy Parnell als blogauteur voor The Compressed Air Blog
- Het prestatieverificatieprogramma van CAGI voor roterende compressoren