Robots grijpen nieuwe mogelijkheden
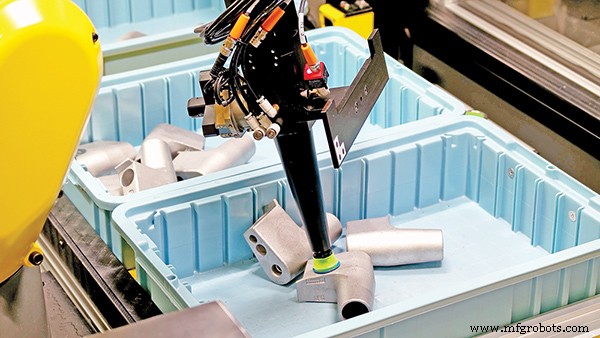
Automatisering blijft een focus in de productie - om alle voor de hand liggende redenen - en robotleveranciers blijven indrukwekkende nieuwe mogelijkheden introduceren. Velen zullen Zach Spencer, robotica-automatiseringsmanager bij Methods Machine Tools Inc., Sudbury, Massachusetts, herhalen als hij zegt dat het "grote, opwindende ding op dit moment collaboratieve robots zijn. Cobots zijn innovatieve automatiseringssystemen die nieuwe bewerkingsopties openen en uw investeringsrendement verhogen. Sommige klanten hebben in minder dan drie maanden voor cobots betaald.”
Spencer voegde eraan toe dat cobots voor een groot deel populair zijn vanwege de intuïtieve manier waarop ze kunnen worden geprogrammeerd. “In plaats van door de leerhanger te gaan om de robot te programmeren om naar een specifiek punt te gaan, kun je de robot handmatig slepen en een instelpunt in de leerhanger maken. Vervolgens sleep je de robot naar de volgende positie en wijs je setpoint twee aan. Dat is een van de betere technologieën met collaboratieve robots.”
Cobot-makers hebben ook een revolutie teweeggebracht in de automatisering door integratie met accessoires van derden te vergemakkelijken, waaronder speciale grijpers, vision-systemen, laskoppen en operationele software. Ann Arbor, in Michigan gevestigde Universal Robots is een leider op dit gebied, met meer dan 300 producten in het UR+-programma en honderden meer in de pijplijn. Senior Manager of Applications Joe Campbell noemt UR+ een “app store voor Universal Robots. We geven de ontwikkelaars diepe toegang [tot ons besturingssysteem], zodat ze software kunnen ontwikkelen. En dan valideren en testen we het en certificeren het.”
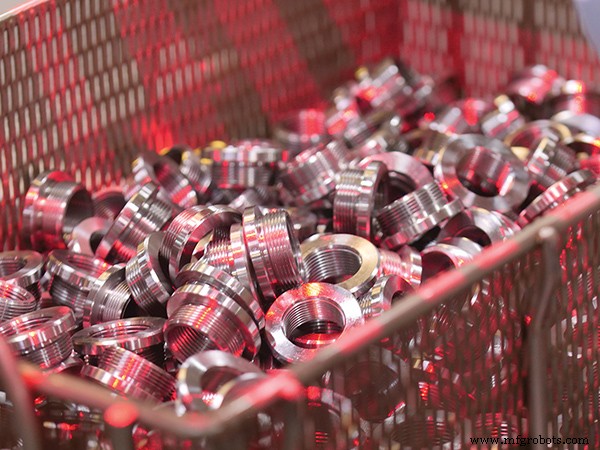
Geavanceerde bin-picking
Het vermogen van een robot om onderdelen uit een bak te halen, zelfs als ze willekeurig zijn georiënteerd, is niet nieuw. Maar leveranciers zoals Universal Robots maken dergelijke systemen eenvoudiger te implementeren. Historisch gezien, legde Campbell uit, zou je wekenlang code moeten schrijven om alle verschillende scenario's te dekken die zich in dergelijke situaties voordoen. Maar de ActiNav-oplossing van UR bevat al "een groot stuk code dat over een lange periode is ontwikkeld en dat alle programmering weghaalt die traditioneel nodig is om te bepalen hoe je van de ophaallocatie naar de neerzetlocatie gaat. … Met ActiNav leert u het het onderdeel … leert u het de plaats van inleveren, … definieert u de bak, die hem in feite op vier punten raakt, … en definieert u eventuele andere barrières in de ruimte. En dan zal het systeem zijn eigen robotpad en -traject volledig plannen om van het ophaalpunt dat het identificeert naar een plaatsingspunt te komen, zonder aangepaste programmering.”
Campbell voegde eraan toe dat "het onderdeel aanleren" aan ActiNav net zo eenvoudig is als het importeren van een CAD-bestand van het werkstuk en vervolgens de oppervlakken aanwijzen waar de cobot het moet vastpakken. Het onderdeel hoeft niet eenvoudig te zijn, het moet alleen "oppervlakken hebben waarmee u een nauwkeurige keuze kunt maken. Het is heel eenvoudig. Ik heb gezien hoe jongens een gloednieuw onderdeel namen waaraan het systeem nog nooit eerder heeft gewerkt en het in ongeveer twee uur hebben opgezet. Bovendien, zei Campbell, is ActiNav, in tegenstelling tot de e-commerce-oplossingen die vaak worden geassocieerd met willekeurige bin-picking, nauwkeurig genoeg om een werktuigmachine automatisch te laden.
Zoals je misschien al geraden had, heeft ActiNav een 3D-visiesysteem nodig om de cobot voor elke pick-up te oriënteren. In dit geval is het een sensor van UR+ partner Photoneo, Bratislava, Slowakije. De unit wordt boven de bak gemonteerd en genereert vrijwel direct een gedetailleerd beeld, aldus Campbell. (Het systeem legt 3,2 miljoen 3D-punten per scan vast.) De beslissings- en laadtijd is eveneens snel, en Campbell ziet taken met een cyclustijd van ongeveer 30 seconden als de ideale oplossing voor het product. Dat is te snel voor een operator om meerdere machines te bedienen, maar binnen de verwerkingstijd van ActiNav. Als de tijd veel sneller is dan 30 seconden, zou ActiNav de machinecyclus vertragen. Natuurlijk zijn er andere situaties waarin je graag een langzamere cyclustijd zou accepteren, zoals het automatiseren van een nachtdienst die anders onproductief zou zijn.
Slim bin-picken is niet beperkt tot cobots, en Spencer van Methods Machine Tools gaf een realistisch voorbeeld waarin FANUC-robots gesmede aluminium toortslichamen uit een bak grijpen en deze in een FANUC RoboDrill laden voor bewerking. De sleutel is het iRVision-systeem van FANUC, dat een 3D-puntenwolk creëert van de objecten in de bak. "En die informatie is gerelateerd aan de robot, zodat hij weet vanuit welke hoek het onderdeel moet worden benaderd om het nauwkeurig te kunnen uitkiezen."
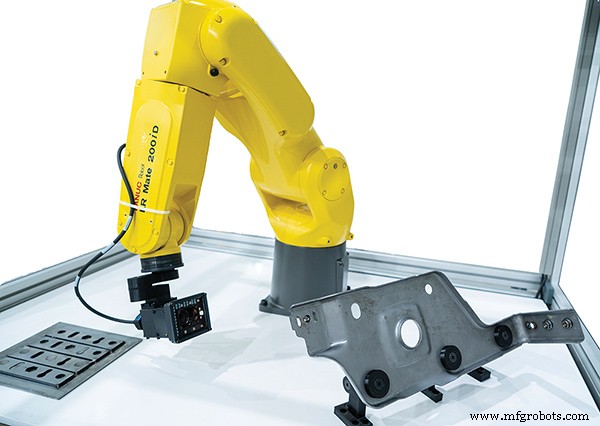
Spencer wees erop dat smeden een scheidingslijn produceert waar de twee matrijzen samenkomen, en de lijn bevindt zich niet altijd op dezelfde plek. De complexe, voorgevormde kenmerken van het onderdeel vormden een andere uitdaging. Maar net als ActiNav, "upload je een 3D-model in de software en vertel je dat dit de vorm is waarnaar we op zoek zijn", legt Spencer uit. "FANUC's software houdt rekening met variaties in grootte, en het is uitstekend in staat om je grenzen te laten stellen aan die variaties." De fabrikant uit het Midwesten van deze toortslichamen ging van met de hand ladende gigantische roterende transfermachines naar een geautomatiseerde cel van vier RoboDrills die bediend werden door twee robots. Als gevolg hiervan produceren ze nu de onderdelen "met een verbeterde doorvoer, meer uptime en een veel lager uitvalpercentage dan op de transfermachines."
Een recenter voorbeeld dat Spencer aanhaalt, is het automatisch laden van grote assen voor bouwmachines van houten sledes naar warmtebehandeling en vervolgens naar een machine. De assen verschillen in lengte, diameter en gewicht (van ongeveer 200 tot 500 lb), en de kavelgroottes zijn klein. Zelfs de hoogte van de houten sledes varieert, voegde Spencer eraan toe. Methoden creëerden een systeem waarmee de machinist eenvoudig een 4 × 4' (1,22 × 1,22 m) pallet met verschillende assen - allemaal verticaal staand, met de flens naar beneden - in de cel kon verplaatsen met een vorkheftruck. Vervolgens bepalen FANUC-software en 2D vision-camera's, gericht op een zijaanzicht, hoe ver de grijpers naar beneden moeten worden gepositioneerd om elk onderdeel te pakken, terwijl een overheadcamera de juiste positie op de vloer bepaalt (in X en Y). Spencer zei dat de verticale positionering "de grote technologische verbetering is. … In staat zijn om een foto te maken met een robot en een meting van die foto te nemen [is een grote verbetering.]”
Andere verbeteringen aan het zichtsysteem
Vanuit het perspectief van Campbell is ActiNav een voorbeeld van hoe de hedendaagse robotica "ongelooflijk complexe" technologie voor de gebruiker verbergt. In dezelfde geest vertelde Mika Laitinen, Solution Sales Director voor Fastems Oy AB, Tampere, Finland, en West Chester, Ohio, hoe de taak om X- en Y-coördinaten vast te leggen met een camera schijnbaar eenvoudig is, maar in feite geavanceerde beeldvorming vereist. algoritmen. Hij wees bijvoorbeeld op de Amerikaanse camerafabrikant Cognex, wiens nieuwste release van slimme camera's "neurale netwerkberekening voor bepaalde beeldalgoritmen" gebruikt. Hij voegde eraan toe dat dergelijke systemen een voorheen moeilijke taak, zoals het lezen van optische tekens, veranderen in een generieke, robuuste mogelijkheid. De rekencapaciteit van deze systemen verbetert zodanig dat "kunstmatige intelligentie geen apart onderwerp is van robotica. … Tegenwoordig wordt kunstmatige intelligentie steeds meer ingebed in slimme sensoren en slimme camerasystemen.”
David Bruce, engineering manager voor het algemene industrie- en automobielsegment, FANUC America Corp., Rochester Hills, Michigan, zei dat de iRVision-systemen van het bedrijf ingebouwde kunstmatige intelligentie (AI) foutcontrole hebben "zonder extra hardware". iRVision biedt robotgeleiding op basis van 2D- of 3D-machinevisie en "FANUC's zeer betrouwbare robotcontroller" handelt zowel de robotbeweging als "de visieverwerking af, inclusief de AI Error Proofing-functie.
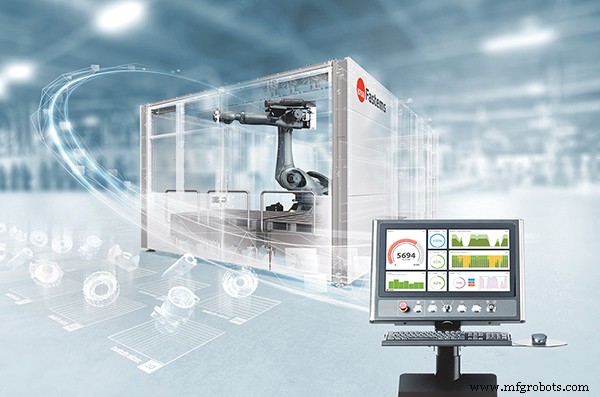
"Omdat iRVision geen pc of slimme camera gebruikt, heeft dit geen negatieve invloed op de betrouwbaarheid van een werkcel", vervolgt Bruce. “Door meerdere voorbeelden te geven van goede en slechte onderdelen, maakt de AI Error Proofing-tool onderscheid tussen de twee tijdens productieruns. Tijdens het instellen kan de operator meerdere voorbeelden van werkstukken presenteren en deze in twee categorieën indelen:goed en slecht. Zodra de operator de afbeeldingen classificeert, classificeert de AI Error Proofing-functie automatisch de onderdelen tijdens productieruns.”
Laitinen van Fastems vermoedde dat LiDAR-technologie (lichtdetectie en -bereik) uiteindelijk stereovisiesystemen zal vervangen (d.w.z. het gebruik van meerdere camera's om in X, Y en Z te meten). “2D-camera's zijn klein, handig en gemakkelijk overal neer te zetten. Je kunt ze in de robotpols verbergen en alle informatie krijgen. Maar als je 3D-visie wilt gebruiken, is de apparatuur veel groter en kan het extra laserprofielscanners bevatten of welke technologie dan ook die wordt gebruikt om de derde coördinaat te meten.”
Omgekeerd, zei hij, zien LiDAR-eenheden er niet anders uit dan 2D-camera's, maar leggen ze 3D-gegevens vast. (Laitinen verwees specifiek naar sensoren van SICK AG, Waldkirch, Duitsland en Minneapolis, Minn.) "Het gebruik van LiDAR-technologie om de X-, Y- en Z-coördinaten te meten met slechts één camera zou een soort revolutie zijn", zoals Laitinen het uitdrukte . Fastems heeft een dergelijk systeem nog niet in gebruik genomen, maar heeft bij verschillende klanten haalbaarheidsstudies uitgevoerd.
Nieuwe robotische metrologiemogelijkheden
Het gebruik van een robot om een CMM of meetstation te verzorgen is niet verrassend en ook niet nieuw, maar het gebruik van de grijpers van een robot om daadwerkelijk een meting uit te voeren is dat wel. Campbell zei dat New Scale Robotics, Victor, N.Y., een UR+-leverancier, een grijper heeft ontwikkeld die naast de pick-and-place-functie ook dienst doet als een uiterst nauwkeurige remklauw. En het is tot op 2,5 µm nauwkeurig.
Campbell zei dat gebruikers "het onderdeel kunnen oppakken en de meting kunnen opnemen terwijl het onderdeel wordt vastgepakt, of ze kunnen de grijper gebruiken om over het onderdeel te microfoonen, meerdere locaties testen voordat ze het verwerven, het oppakken en verplaatsen. Het is een geweldig voorbeeld van het inbedden van het metrologieproces midden in het productieproces.”
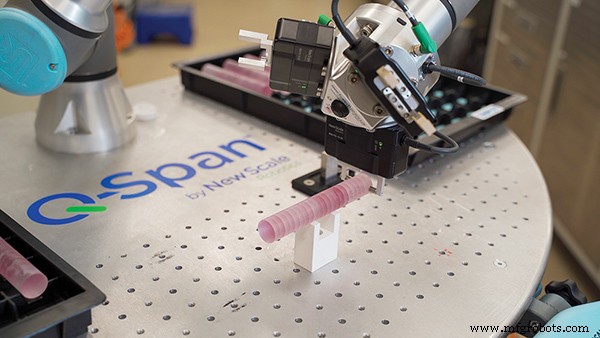
New Scale Robotics, een divisie van New Scale Technologies, koppelt de uiterst nauwkeurige grijper aan een UR3e-cobot van Universal Robots om het Q-Span-werkstation te creëren. Een klant, OptiPro Systems, Ontario, N.Y., gebruikt de Q-Span voor 100 procent in-process inspectie van de optische glazen cilinders die uit zijn OptiSonic-slijpmachine komen. Onderdelen die door de keuring komen, gaan naar een CMM voor definitieve validatie. Dit elimineert niet alleen de noodzaak voor handmatige controles die het bedrijf eerder uitvoerde, de Q-Span is ook vier keer nauwkeuriger dan handmatige remklauwen, wat volgens de fabrikant resulteert in een strakkere controle over het productieproces en minder afval. Campbell zei dat de New Scale-grijpers ook in één cyclus bereiken wat een mens zes stappen nodig heeft om te doen. Bovendien kan OptiPro verschillende onderdelen aan met dezelfde set grijpers.
Gegevens van de robot
Laitinen merkte op dat het verzamelen van servogegevens over de beweging en gezondheid van de robot ook twee belangrijke voordelen biedt. De eerste is de mogelijkheid om trends voor voorspellend onderhoud te bestuderen, waarvan het ZDT-programma (zero down time) van FANUC een opmerkelijk voorbeeld is. De tweede is QC-gerelateerd, "het verzamelen van toepassingsspecifieke procesgegevens en deze distribueren naar de besturingssoftware op het hoogste niveau." Dit geldt voor toepassingen waarbij de robot op het werkstuk inwerkt, in tegenstelling tot een andere machine.
Laitinen zei dat de lucht- en ruimtevaartindustrie goede voorbeelden biedt van zowel het gebruik van robots op deze manier - bijvoorbeeld het afwerken en afwerken (een afwerkingstechniek die metaal gladmaakt of vlak maakt) van turbinecomponenten - en van het gebruik van robotservogegevens om het proces te besturen. "Mensen in de lucht- en ruimtevaartindustrie begrijpen dat in plaats van onderdelen te maken en de kwaliteit achteraf te controleren, het beter is om een inspanning te leveren om het proces te beheersen", zei hij. Het leidt tot een begrip van hoe het onderdeel is vervaardigd en alle belangrijke prestatievariabelen en hoe die waarden variëren tijdens het fabricageproces. Als het goed is gedaan, gebruiken ze deze gegevens om realtime correcties aan te brengen of, indien nodig, een robot automatisch offline te halen en het werk door te sturen naar andere eenheden voordat ze slechte onderdelen produceren.
“Dat is het succesverhaal van Fastems in de lucht- en ruimtevaartindustrie. Onze besturingssoftware kan zich aanpassen aan dit soort veranderingen in de productielijn zonder de productie stil te leggen.” Hij voegde eraan toe dat de COVID-19-pandemie het bedrijf heeft gedwongen om klanten buiten de commerciële luchtvaart te zoeken, en het brengt deze filosofie over "het meten van het proces en niet het onderdeel" naar de nieuwe klanten.
Coöperatieve robots
Het is al lang zo dat sommige geautomatiseerde lijnen vereisen dat de ene robot een onderdeel aan een andere overdraagt. En bij het lassen is het soms zo dat de ene meerassige robot het onderdeel vasthoudt terwijl een andere de toorts beweegt, waarbij beide robots onder het commando staan van één enkele besturing. Maar het is relatief zeldzaam dat meerdere robots hetzelfde onderdeel verplaatsen. Fastems heeft onlangs zo'n systeem in de VS geïnstalleerd. De onderdelen zijn gigantische ringen met een diameter tot 2,4 m, met verschillende diktes en gewichten. Laitinen legde uit dat het optillen met één robot een zeer grote en dure driepuntsgrijper zou hebben gekost, om nog maar te zwijgen van een zeer grote robot, "en de toegankelijkheid zou erg moeilijk zijn geweest.
"Dus in plaats daarvan gebruiken we twee robots op dezelfde lange lineaire baan [die parallel loopt met de productielijn van werktuigmachines, wasstations, enz.]. De robots bewegen alsof ze één tweearmige robot zijn,” zei hij. “Dit wordt aangestuurd door een enkele robotcontroller en beide robots krijgen instructies vanuit één programma.” Alle pick-and-place-taken worden gedaan met eenvoudige grijpers met twee vingers die het onderdeel aan beide uiteinden pakken, het tegelijkertijd optillen en verplaatsen.
Automatisering Besturingssysteem
- Automatisering:nieuwe bron en mogelijkheden voor samenwerkende robots
- Injection Molding:nieuwe robots bij Fakuma
- Nieuwe robots:voordelig en topklasse
- Nieuwe topklasse servorobots met Industry 4.0-connectiviteit
- Injection Molding:nieuwe modellen van economische robots
- Injection Molding:New Picker, Robots &Box Packer
- Injection Molding:nieuwe robots op K 2019
- Automatisering:nieuwe hardware en software voor goedkope robots
- Een overzicht van de voordelen en mogelijkheden van verpakkingsrobots
- RIA publiceert nieuw technisch rapport over collaboratieve robots
- Universal Robots stuurt drie nieuwe lasapparaten aan bij FabTech