Robotbedrijf maakt industrie 4.0-vriendelijke software
FANUC heeft een van de beloften van Industrie 4.0, die van voorspellend onderhoud voor fabrieksapparatuur, waargemaakt met zijn Zero Down Time IoT-oplossing. ZDT kan worden toegepast op alle robotarmen van FANUC en hun randapparatuur.
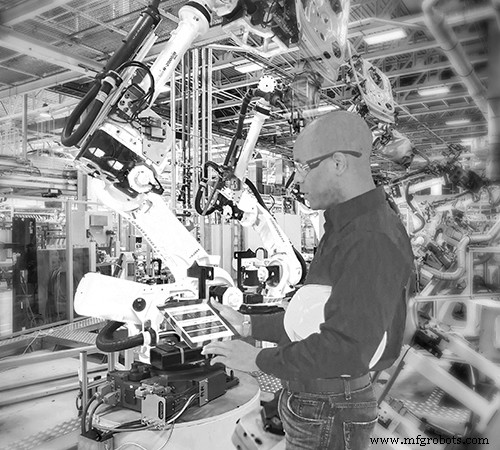
Om te helpen met de rest van de automatisering in een fabriek, zal het roboticabedrijf later dit jaar FANUC's Intelligent Edge Link and Drive (FIELD)-systeem beschikbaar stellen, een gratis en open-sourceplatform dat externe ontwikkelaars kunnen gebruiken om applicaties te schrijven die verzamelt en analyseert gegevens van andere geautomatiseerde apparatuur.
Slim produceren ging zitten met Joe Gazzarato, technisch directeur van ZDT bij FANUC America, om meer te weten te komen.
Joe, waar gaat ZDT allemaal over?
"ZDT" staat voor "Zero Down Time". Met fabrikanten die nu constant, 24/7/365, proberen aan de vraag te voldoen, kan elke onverwachte uitvaltijd hen productie kosten. Met ZDT bewaken we de mechanische, systeem- en procesgezondheid van onze robots om onverwachte uitvaltijd te voorkomen.
We hebben meer dan 21.000 robots verbonden met ZDT op meer dan 100 klantlocaties in 16 verschillende landen.
We monitoren die robots en als een probleem wordt voorspeld door onze analyses, zal ons ZDT-systeem de klant en ons serviceteam op de hoogte stellen, zodat we het probleem kunnen aanpakken voordat er onverwachte uitvaltijd optreedt. We hebben klanten al meer dan $ 85 miljoen bespaard door problemen te identificeren die volgens ons tot onverwachte uitvaltijd zouden hebben geleid.
Hoe heb je dit bereikt?
We werken nu iets meer dan vier jaar aan ZDT. We begonnen met slechts 500 robots, met 50 robots op elk van de 10 locaties.
We hebben software gemaakt voor onze robots die berichten produceren met belangrijke gegevens. Die robots sturen hun berichten naar een dataverzamelaar die zich in de fabriek van de klant bevindt. De ZDT-gegevens
Het is de taak van Collector om de berichten te coderen en uitgaand naar ons datacenter in de cloud te sturen, waar ze worden opgeslagen en automatisch worden geanalyseerd met behulp van programma's die zijn geschreven door onze technici.
Als een van de analyses vaststelt dat er een probleem is, gaan er e-mails naar de klant en ons serviceteam en een van onze servicetechnici belt de klant om ervoor te zorgen dat ze begrijpen wat de waarschuwing betekent, hoe deze moet worden bevestigd en hoe deze moet worden opgelost. Als de klant hulp nodig heeft, kan de technicus ervoor zorgen dat onderdelen of ondersteuning naar de site worden gestuurd, zodat we het probleem kunnen oplossen voordat er uitvaltijd optreedt.
Welke specifieke technologieën maken ZDT mogelijk?
De ZDT Data Collector heeft zeer lage bandbreedtevereisten. Sommige andere implementaties rond big data zullen gegevens constant streamen met een snelheid van milliseconden. ZDT is niet zo ontworpen. We verzamelen in een jaar minder dan 500 megabyte aan data van de robot. Ook kan de datacollector op een kleine computer draaien. Er zijn niet veel computerbronnen voor nodig.
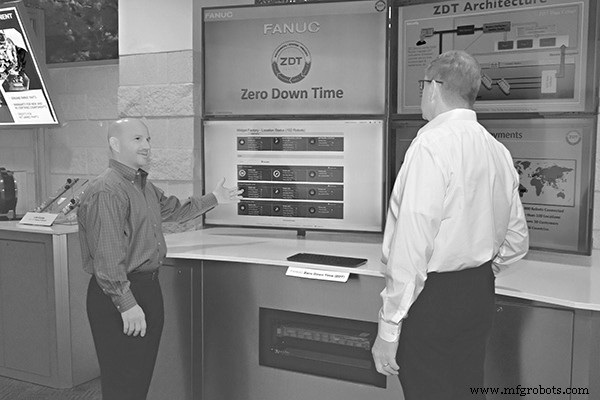
Een andere sleutel is onze cloudinfrastructuur. De tools die we gebruiken om de gegevens op te nemen en op te slaan voor analyse zijn erg belangrijk. We zorgen ervoor dat de gegevens zo worden georganiseerd dat ze veilig zijn wanneer ze worden opgeslagen en dat ze efficiënt kunnen worden gebruikt door onze analyseprogramma's.
Onze analyses zijn waarschijnlijk een van de belangrijkste onderdelen van ZDT en de sleutel tot ons succes tot nu toe. Ze zijn geschreven door dezelfde ingenieurs die onze robotbesturingssoftware hebben ontwikkeld. FANUC-ingenieurs met jarenlange robotervaring hebben de analyseprogramma's geschreven die kijken naar de gegevens die we hebben verzameld. Dankzij hun expertise in het schrijven van robotsoftware zijn ze erg goed geworden in het schrijven van analyses op basis van de gegevens die door onze robots worden geproduceerd.
Zijn er andere toepassingen voor de gegevens die u verzamelt in het ZDT-proces?
ZDT doet ook veel andere dingen. We hebben veel functies gecreëerd om klanten te helpen hun productiviteit te verhogen, hun onderhoudsbronnen te optimaliseren, hun ondersteuningsinspanningen te verminderen en de levensduur van hun robots te verlengen.
Een goed voorbeeld is onze procesveranderingsanalyse. Een veel voorkomende ervaring voor velen van ons die met automatiseringsapparatuur hebben gewerkt, is om op de werklocatie te verschijnen en te ontdekken dat uw systeem geen snelheid maakt of dat het iets anders doet dan de dag ervoor. En je vraagt wat rond en krijgt hetzelfde antwoord. 'Ik heb het niet aangeraakt' of 'Niemand heeft iets veranderd.' Zonder ZDT moeten mensen hun eigen analyse uitvoeren om erachter te komen wat er is veranderd.
Met ZDT weten onze klanten zeker of hun robots zijn gewijzigd, omdat we elke dag allerlei soorten gegevens van de robots loggen. Wanneer een robot wordt gewijzigd, weten ze precies welk programma of welke instelling is gewijzigd, samen met de datum en tijd waarop het is gebeurd, zodat ze waarschijnlijk kunnen bepalen wie de wijziging heeft aangebracht en ook de oorspronkelijke waarde kennen. Dit alles maakt het voor de klant heel gemakkelijk om dingen heel snel terug te zetten.
Zijn mijn gegevens veilig?
De ZDT-gegevensverzamelaar, die kan worden geblokkeerd door de firewall van de klant, versleutelt de gegevens terwijl ze naar ons datacenter worden verzonden en is alleen een uitgaande service.
Beschouw ZDT ook als alleen-lezen. We kunnen alleen informatie zien die door de robots is verzameld. We kunnen niets veranderen.
Als FANUC zegt dat ZDT-gebruikers toegang hebben tot diagnostische informatie in de hele onderneming, verwijst dat dan naar robots en niet naar andere apparatuur in de fabriek?
Typisch, maar we hebben ZDT zo ontworpen dat klanten sommige van hun randapparatuur kunnen volgen.
Laten we zeggen dat het kledingpakket van een robot externe luchtleidingen en elektrische kabels bevat die stroom naar het uiteinde van de arm brengen. U kunt de slijtage van de kledingverpakking associëren met gegevens van de robot. Nadat de robot bijvoorbeeld zoveel duizenden graden heeft bewogen of zijn pols zo vele duizenden keren heeft gedraaid, kan ZDT de klant informeren dat aan de voorwaarde is voldaan en kan hij iemand sturen om het jurkpakket te inspecteren.
Zonder ZDT kunt u periodiek onderhoud uitvoeren, maar met ZDT inspecteert u het op basis van hoe de robot wordt gebruikt. Klanten optimaliseren dus het gebruik van hun onderhoudsresources en voeren onderhoud uit wanneer dat nodig is en niet alleen vanwege de verstreken kalendertijd.
En hoewel ZDT geen gegevens van andere apparatuur verzamelt, bereidt FANUC zich voor om later dit jaar technologie uit te brengen die is ontworpen om precies dat te doen.
Hoe zou u het FIELD-systeem omschrijven?
FIELD is een platform dat we dit jaar in de VS lanceren. Het is ontworpen om gegevens te verzamelen van alle netwerkcomponenten, inclusief robots, lascontrollers, PLC's en sensoren, en niet noodzakelijkerwijs FANUC-apparatuur. Elk netwerkapparaat in een faciliteit kan zijn gegevens delen met het FIELD-systeem, dat intern in de fabriek zal draaien.
FANUC stelt softwareontwikkelaarskits beschikbaar zodat derden applicaties kunnen schrijven die toegang hebben tot die gegevens en dingen kunnen doen die waarde bieden aan de klant. ZDT is een voorbeeld van de waarde die FANUC biedt door het gebruik van dit soort gegevens, maar we denken dat er miljoenen mogelijkheden zijn voor wat mensen kunnen doen met gegevens van productieapparatuur. Het FIELD-systeem is ontworpen om het voor andere bedrijven mogelijk te maken hun eigen applicaties te ontwikkelen en aan fabrikanten te verkopen.
Er zijn twee verschillende servers beschikbaar voor het FIELD-systeem. Een daarvan, de FIELD Base Pro, kan tot 30 apparaten aansluiten. We ondersteunen ook een Unified Computing Server van Cisco die tot 150 apparaatverbindingen kan ondersteunen. Ze kunnen worden samengevoegd, zodat informatie tussen de servers kan worden gedeeld.
Er zijn veel verschillende IoT-platforms, maar het FIELD-systeem van FANUC is uniek vanwege de verschillende voordelen die het biedt.
- Het draait in de fabriek. Anderen draaien in de cloud, zoals ZDT doet. Aangezien FIELD-applicaties in de fabriek zullen draaien, kunnen de applicaties veel responsiever zijn. Ze krijgen hun gegevens bijna in realtime en kunnen deze analyseren en zeer snel beslissingen nemen. Ze zijn ook niet afhankelijk van een internetverbinding.
- FANUC heeft het FIELD-platform volledig open gemaakt. Er komt een FIELD system Partner's Association waar mensen die applicaties willen schrijven of het FIELD-systeem in hun systemen of met hun apparaten willen integreren, dat kunnen doen. Lid zijn kost niets.
- Het systeem kan verbinding maken met elk netwerkapparaat. Veel van de andere bestaande platforms ondersteunen slechts een paar protocollen of een paar standaardprotocollen, maar FANUC biedt ook de mogelijkheid voor apparaatfabrikanten om hun eigen protocol te schrijven. Dus als er geen bestaand stuurprogramma is om uw apparaat op het FIELD-systeem aan te sluiten, kunt u er een maken. En die ontwikkelaarskit is gratis beschikbaar voor apparaatfabrikanten.
Het idee is om deze gemeenschap van apparaten en applicatieontwikkelaars te creëren om de productiemogelijkheden te vergroten.
Automatisering Besturingssysteem
- Industrie 4.0-softwareoplossingen:wie weet het beter dan de gebruikers?
- GE lanceert $ 1,2 miljard IIoT Company
- Sepro lanceert apps om robotsoftware te verbeteren
- Collaborative Robot Marketplace voegt monitoringsoftware toe
- De opkomst van de robot:investeren in disruptieve automatisering
- B&R-software benut het potentieel van robots beter
- Mitsubishi Electric neemt Amerikaans softwarebedrijf Iconics over
- Verizon neemt softwarebedrijf voor autonome mobiele robots over
- Moderne HMI-software stuwt industrie 4.0 voort
- Epson creëert autonome dubbelarmige robot voor hightech productie
- Het delen van kennis in het bedrijf, in de industrie