Rethinking control systems for Multi-Well Pads
Gegevens, besturingsvereisten stimuleren de behoefte aan modulaire, schaalbare besturingsarchitectuur.
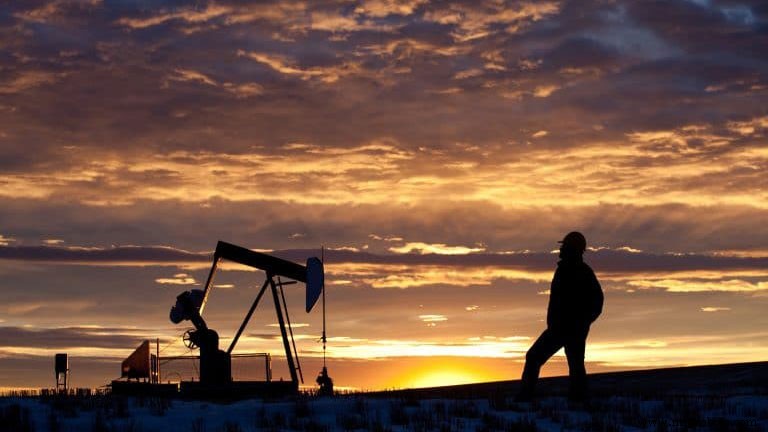
Verbeteringen op het gebied van boren hebben de evolutie van olie- en gasactiviteiten gestimuleerd van simplistische velden met enkelvoudige putjes naar complexere pads met meerdere putjes.
Tegenwoordig gebruiken veel producenten fracking- en laterale boortechnieken om 10 of meer putten op één pad te plaatsen. Sommige operators duwen hun activiteiten zelfs naar maar liefst 52 putten op één enkele pad.
Deze verbeteringen hebben niet alleen de productieterugwinning uit putten vergroot, maar ook geheel nieuwe productiemogelijkheden gecreëerd in onconventionele gebieden. Ze hebben olie- en gasproducenten ook in staat gesteld hun operationele voetafdruk te verkleinen.
Ondanks alle voordelen van pads met meerdere putten, heeft hun grote toename in omvang en reikwijdte echter een nieuwe uitdaging gecreëerd. De hogere dichtheid van meerdere putten op een enkele pad verhoogt de benodigde apparatuur ter plaatse en resulteert in veel grotere gegevens- en controlevereisten.
De traditionele besturingsarchitecturen die al tientallen jaren worden gebruikt, worden tot het uiterste gedreven en zijn misschien niet langer houdbaar. In plaats daarvan zijn meer geavanceerde besturingssystemen nodig om de schaalbare architecturen aan te kunnen die nodig zijn voor moderne putkussens.
Als gevolg hiervan moeten zowel operators als de apparatuurbouwers die hen ondersteunen nu hun benadering van besturingssystemen voor deze multi-well pads aanpassen, zo niet radicaal veranderen.
Evolutie van RTU-technologie
Stroomopwaartse olie- en gasproducenten vertrouwen al tientallen jaren op remote terminal unit (RTU)-technologie voor het regelen van boorputten. Aanvankelijk beperkten de kosten van het implementeren van RTU's en de uitdagingen bij het programmeren ervan de apparaten tot eenvoudige gegevensverwerving en controle.
Na verloop van tijd kregen RTU's echter meer functies, waaronder I/O, communicatie en IEC-61131-programmering. Deze mogelijkheden stelden olie- en gasbedrijven in staat om meer datapunten te bewaken, geschiedenis en alarmen te loggen en complexere berekeningen toe te voegen aan de RTU's. Apparatuurbouwers en ingenieursbureaus zijn ook begonnen met het ontwikkelen van speciale toepassingen voor kunstmatige-liftregelingen van putmonden met gepatenteerde microprocessorcontrollers.
Uiteindelijk had vrijwel elke fabrikant van kunstmatige liften zijn eigen RTU ontwikkeld om zijn respectieve oplossingen te controleren en te optimaliseren. Ingenieursbureaus ontwikkelden ook hun eigen methoden met iets andere RTU-toepassingen, terwijl instrumentatiefabrikanten nieuwe instrumenten introduceerden om zowat elk vereist procespunt te meten.
De laatste tijd zijn de toegenomen eisen die worden gesteld aan operaties met meerdere putten echter de mogelijkheden van de RTU-technologie gaan overtreffen.
Apparaten tot het uiterste gedreven
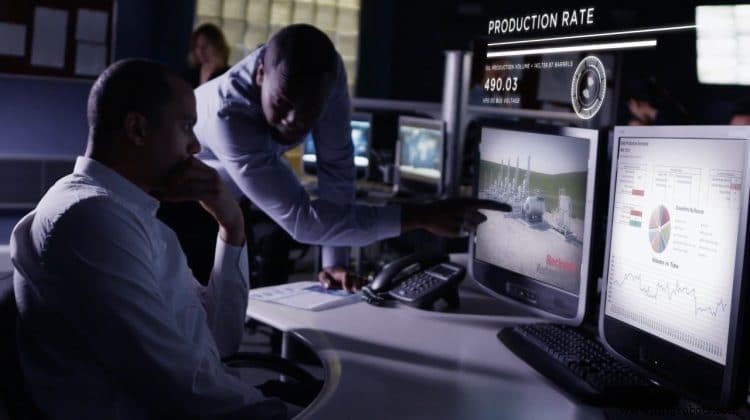
Elke put in een pad met meerdere putjes vereist een kunstmatige lift, stroommeting, apparatuurcontrole en niveaumeting. Dit creëert meer I/O- en besturingsvraag dan een enkele RTU aankan. Als gevolg hiervan zijn olie- en gasproducenten genoodzaakt om extra RTU's aan te schaffen en de applicatie- en locatiecontrole over meerdere units te spreiden.
Olie- en gasproducenten hebben met succes meerdere RTU-controllers op een putpad geïmplementeerd, maar ze lopen tegen een aantal veelvoorkomende problemen aan met deze architecturen. Enkele van deze problemen zijn:
- Verander het beheer van meerdere configuraties of programma's op elke well pad.
- Communicatiebeheer van de vele RTU's ter plaatse (bijv. peer-to-peer-communicatie).
- SCADA-communicatie met hardware van meerdere leveranciers.
- Onbetrouwbare uitvoering van aangepaste programma's in de RTU's.
De ultieme vraag naar RTU-apparaten komt wanneer een veel grotere padbesturing met meerdere wells nodig is. Dit kan een operatie omvatten met 10 of zelfs enkele tientallen putten op een enkel putkussen. De hogere dichtheid van putten op een pad verhoogt ook de benodigde apparatuur ter plaatse. Veel van deze putkussens hebben bijvoorbeeld hun eigen afscheider.
Het wordt ook zuiniger om pijpleidingcompressie, dampterugwinningseenheden (VRU's) en VRU-torens te installeren vanwege de hoge hoeveelheid aardgas die uit de pad wordt geproduceerd. Lease automatische bewaringsoverdracht (LACT) -eenheden, wateroverdracht en chemische injectiemachines worden ook vaak gezien op deze putkussens.
Bovendien investeren veel olie- en gasproducenten in elektrische gebouwen die bekend staan als E-houses. In deze gebouwen bevinden zich de hoofdstroomdistributie, motorcontrolecentra (MCC), netwerkschakelaars en ononderbroken stroomvoorzieningen (UPS), en ze worden vaak gecontroleerd door de omgeving.
Al deze toenames - in apparatuur, veldinstrumentatie en toepassingen - verergeren alleen de veelvoorkomende problemen met RTU-architecturen.
Ze creëren ook nieuwe uitdagingen op het gebied van service en ondersteuning. Het gebruik van meerdere RTU's heeft geleid tot meerdere applicatieconfiguraties en programma's om ze te onderhouden. Het dwingt olie- en gasbedrijven ook om met meerdere leveranciers samen te werken.
Bovendien vereist het hebben van meerdere apparaten van meerdere leveranciers ook dat werknemers meer training en ervaring hebben om hen te ondersteunen. Hoewel sommige producenten volledig bemand zijn met voldoende opgeleid personeel om het onderhoud van de putcontrolesystemen af te handelen, zijn velen dat niet. Deze producenten moeten vertrouwen op ondersteuning van de fabrikant of contractengineering om hun controlesystemen te onderhouden.
Overstappen naar modulaire, schaalbare besturingssystemen
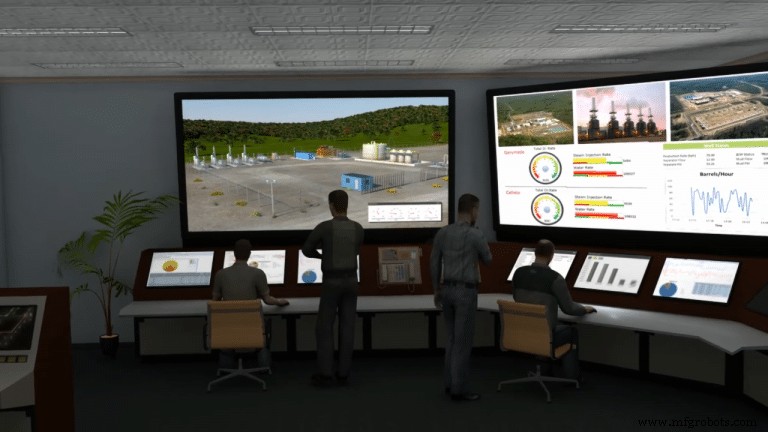
RTU's vervullen al tientallen jaren hun rol bij het omgaan met eenvoudige besturingsvereisten, eenvoudige veld-apparaatinteractie en eenvoudige communicatie. Maar ze voldoen niet langer in de complexere besturingsomgevingen van vandaag.
Veel olie- en gasproducenten die veelvoorkomende RTU-problemen hebben ondervonden, hebben een haalbare alternatieve oplossing gevonden in de vorm van een modulaire en schaalbare programmeerbare logische controller (PLC). PLC-technologie is jarenlang verfijnd in industriële procesbesturingsomgevingen die net zo robuust zijn als stroomopwaartse olie- en gasproductie.
PLC's bieden een aantal voordelen in vergelijking met RTU's:
- Modulariteit: Sommige RTU's ondersteunen wel modulaire hardware. Maar het balanceren van de modulevereisten met toepassings- en besturingsvereisten in een RTU is veel moeilijker dan in een PLC. Bovendien zijn modules van derden voor RTU's doorgaans niet beschikbaar omdat RTU's geen open architecturen zijn, terwijl PLC's dat wel zijn.
Er is een grote verscheidenheid aan modules beschikbaar voor PLC's die monitoring en besturing van een breed scala veld instrumenten. Communicatie-ondersteuning voor veel verschillende netwerktypes wordt ook ondersteund door modulaire configuratie. - Schaalbaarheid: Dit is belangrijk bij het overwegen hoe een pad met meerdere putten in elkaar wordt gezet. Een enkele put wordt vaak geïnstalleerd op een locatie met meerdere putten, en pas maanden of zelfs jaren later zullen extra putten en apparatuur online komen.
In deze gevallen willen apparatuurbouwers in staat zijn om off-site uitrustingsskids te bouwen en ze vervolgens eenvoudig aan te sluiten en te configureren op het putpad. Ze willen de noodzaak voor het graven van sleuven, het trekken van kabels, het afsluiten van kabels, het installeren van panelen en instrumenten in het veld verminderen om kosten te besparen. Schaalbaarheid in zowel programmering als hardware is in dit geval vereist, en dat is precies wat PLC-technologie biedt. - Eenvoudig programmeren: Historisch gezien werden PLC's gezien als een leeg canvas voor automatisering en besturing. Alleen ingenieursbureaus of ervaren programmeurs wisten hoe ze helemaal opnieuw moesten beginnen en de besturing moesten ontwikkelen die nodig is in een PLC.
Moderne PLC's hebben echter bibliotheken met vooraf ontwikkelde en gedocumenteerde code die snel in een bijna drag-and-drop mode. Sommige PLC-leveranciers hebben ook vooraf ontwikkelde upstream-olie- en gasbibliotheken die ter plaatse kunnen worden geconfigureerd. Olie- en gasproducenten hoeven alleen de vereiste gegevens van de HMI in te schakelen en te configureren om een PLC op te starten, of om skid-hardware toe te voegen aan een bestaand systeem.
Dit kan iemand als een put overbodig maken technicus met gespecialiseerde expertise om de programmeeromgeving te kennen en nieuwe code te schrijven bij het toevoegen van hardware.
Bovendien kunnen programma- en configuratiewijzigingen online in een PLC worden aangebracht zonder het proces af te sluiten. RTU's kunnen dergelijke wijzigingen traditioneel niet accepteren zonder offline te worden gehaald en gedownload. Dit is een kritische onderscheidende factor in een moderne multi-well pad-omgeving, omdat het uitschakelen van het besturingssysteem leidt tot productieverlies. - Remote I/O-functionaliteit: RTU's hebben traditioneel geen native remote I/O-functionaliteit, maar PLC's wel. Dit kan de installatiekosten verlagen. Wanneer apparatuur-skids aan een site worden toegevoegd, kunnen ze ook worden geleverd met voorgemonteerde en bedrade I/O en instrumenten. Het opstarten van deze skids is net zo eenvoudig als het aansluiten van een Ethernet-kabel op een switch en het configureren van de I/O in de controller.
Levenscyclusbeheer verbeteren
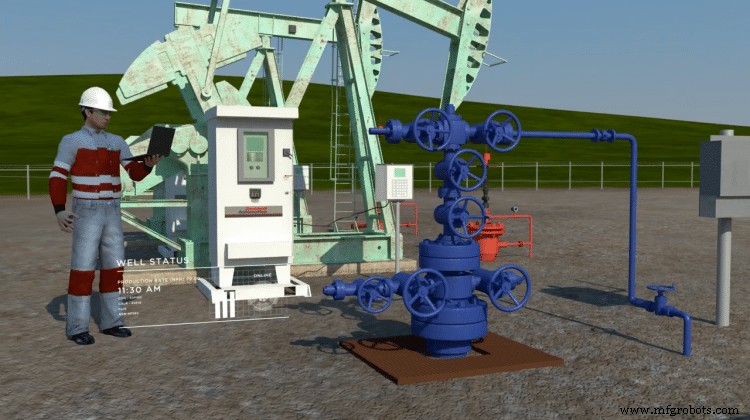
Well pad-levenscyclusbeheer kan een grote hoofdpijn zijn voor operationele teams. Putten kunnen door veel verschillende stroomtoestanden gaan, waaronder natuurlijk stromende, elektronische dompelpomp (ESP) of progressieve holtepomp (PCP) en zuigstangpomp. En het stroomtype en de levenscyclus kunnen per put verschillen.
Er worden vaak meerdere RTU's gebruikt om de verschillende levenscycli van de put te beheersen. Het wijzigen van de RTU betekent het wijzigen van communicatiestuurprogramma's naar het SCADA-systeem, omdat de fysieke RTU bij de bron hardware is van een nieuwe leverancier. En het configureren van de RTU om de applicatie te besturen en het instellen van die hardware op het systeem is vaak een moeizaam proces.
Een op PLC gebaseerde putpad kan op dit gebied aanzienlijke verlichting bieden en efficiëntie- en optimalisatievoordelen opleveren die operators misschien nooit voor mogelijk hadden gehouden.
Door gebruik te maken van de modulaire en schaalbare I/O-hardwarearchitecturen die een PLC biedt, kunnen operators I/O-modules installeren waar de instrumentatie zich bevindt en die gegevens naar de PLC sturen. En ongeacht welke I/O-ontwerpbenadering een olie- of gasproducent gebruikt, de hardware in het besturingssysteem zal constant blijven, de communicatie met het SCADA-systeem zal dezelfde stuurprogramma's gebruiken en het systeem blijft online en beheert alle toepassingen zoals updates worden gedaan. Al die tijd blijft er slechts één PLC-programma over om te onderhouden.
Er is ook de kwestie van ondersteuning van leveranciersapplicaties. Zoals eerder vermeld, maken veel leveranciers hun eigen toepassingen voor een verscheidenheid aan upstream-productiebehoeften, en elke leverancier gebruikt doorgaans een ander type RTU. Als gevolg hiervan kunnen leveranciers meestal maar een paar specifieke applicaties ondersteunen, niet allemaal.
De ondersteuning van PLC-leveranciers op padontwerpen met meerdere putten groeit dagelijks. Dit omvat ondersteuning voor toepassingen voor apparatuurbesturing, kunstmatige lift en stromingsmeting. Automatisering van apparatuur is eenvoudig te regelen via rijke programmeeromgevingen en een breed scala aan I/O- en communicatiemodules. Flowmeting wordt ook ondersteund met AGA- en API-compliant flowmeting, kalibratieondersteuning en custody transfer rapportage naar SCADA-systemen. Toepassingen voor kunstmatige liften, hoewel ze niet zo gangbaar zijn in PLC's, worden ook snel ontwikkeld om alle soorten kunstmatige liften te ondersteunen.
Ten slotte hebben veel olie- en gasproducenten hun frustratie geuit over het feit dat RTU-toepassingen "black box" zijn. Dit betekent dat het systeem is ontworpen met specifieke ingangen die bedoeld zijn om alleen specifieke uitgangen te regelen.
Een black-boxbenadering verhindert flexibiliteit omdat olie- en gasproducenten de manier waarop het systeem functioneert niet kunnen veranderen. Als gevolg hiervan moeten ze ofwel van leverancier veranderen om in hun behoeften te voorzien of gewoon leven met de technologie die ze hebben, in de wetenschap dat deze niet zo efficiënt werkt als ze nodig hebben.
Een PLC-gebaseerd systeem kan daarentegen in het veld worden aangepast met gangbare industriële tools (IEC-61131), wat een veel grotere flexibiliteit oplevert.
Het nieuwe normaal omarmen
De PLC wordt al lang gezien als een oplossing die meer geschikt is voor productiefaciliteiten dan voor besturing van putkussens. Maar de moderne putkussens van vandaag zijn in wezen kleine fabrieken. Ze hebben gebouwen die door de omgeving worden gecontroleerd, energie voor nutsvoorzieningen of generatoren en veel grotere gegevens- en controlevereisten.
Dit maakt ze ideaal voor een PLC. Een padbesturingssysteem met meerdere putten dat gebruikmaakt van de modulaire en schaalbare mogelijkheden van een PLC, kan de kosten en installatietijden verlagen, de uptime van de productie verbeteren en het levenscyclusbeheer vereenvoudigen.
Zack Munk is onshore upstream business development manager voor olie en gas voor Rockwell Automation.
Automatisering Besturingssysteem
- Flexibele productiesystemen bouwen voor Industrie 4.0
- ASM Assembly Systems gebruikt de Sawyer-robot van Rethink Robotics voor kwaliteitscontroles
- Overwegingen voor AFD-bedieningspanelen
- Voordelen ingesloten technologieën voor modulair ontwerp
- Eenvoudige oplossingen voor oude automatiseringssystemen
- Bedrijven stellen deadlines voor intelligente systemen
- Top 10 workflows voor fabrikanten
- Lokale versus wereldwijde systemen voor productiecontrole
- Voordelen van het gebruik van VIA in pads
- Marposs kondigt BLÚ LT modulair besturingssysteem voor werktuigmachines aan
- Wat zijn hydraulische regelsystemen?