Application Spotlight:hoe 3D-printen innovatie in de kernenergie-industrie ondersteunt
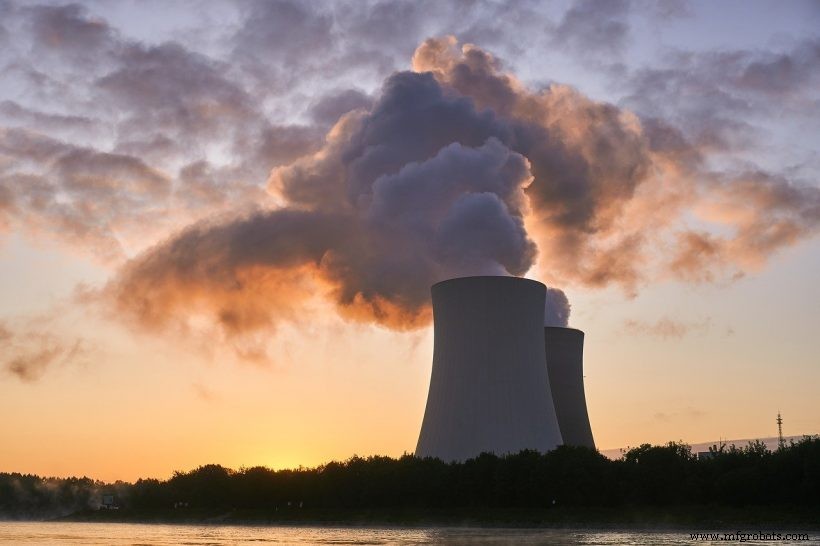
3D-printen is een opwindende technologie die belangrijke innovaties kan introduceren voor zowel huidige als toekomstige kerncentrales.
Hoewel de nucleaire industrie de reputatie heeft ongelooflijk conservatief te zijn, begint ze geleidelijk aan 3D-printen over te nemen om de mogelijkheden voor reserveonderdelen en geavanceerde onderdelen van kerncentrales te verkennen.
Dit artikel gaat dieper in op de drijfveren achter de adoptie van 3D-printen in de nucleaire industrie en onderzoekt de meest opwindende ontwikkelingen die op dit gebied plaatsvinden.
Bekijk de andere toepassingen die in deze serie worden behandeld:
3D-printen voor warmtewisselaars
3D-printen voor lagers
3D-printen voor fietsproductie
3D-printen voor productie van digitale tandheelkunde en heldere uitlijners
3D-printen voor medische implantaten
3D-geprinte raketten en de toekomst van de fabricage van ruimtevaartuigen
3D-printen voor de productie van schoenen
3D-printen voor elektronische componenten
3D-printen in de spoorindustrie
3D-geprinte brillen
3D-printen voor productie van eindonderdelen
3D-printen voor beugels
3D-printen voor turbineonderdelen
Hoe 3D-printen zorgt voor beter presterende hydraulische componenten
Waarom 3D-printen voor onderdelen van kerncentrales?
De nucleaire industrie maakt moeilijke tijden door. De markt voor nieuwbouw van grote reactoren komt tot stilstand, aangezien de kosten die met deze investeringen gepaard gaan blijven stijgen, terwijl de kosten van andere energiebronnen dalen.
Bovendien hebben grote reactoren verschillende problemen vanwege hun complexe constructie en installatie, veiligheidsvoorschriften, reparatie en andere hoge kostenrisico's.
Tegelijkertijd is er een golf van nucleaire ontmanteling. Een groot aantal nucleaire installaties is gestaakt en de verwachting is dat dit aantal de komende jaren aanzienlijk zal toenemen.
Een weg vooruit voor kernenergie kan liggen in kleinschalige kernreactoren, die veel van de nadelen van traditionele, grotere reactoren overwinnen. Deze systemen worden Small Modular Reactors (SMR) genoemd en zullen naar verwachting de bouwtijdlijnen drastisch verkorten en kernenergie betaalbaarder maken om te bouwen en te gebruiken.
De productie van SMR's vereist nieuwe benaderingen voor het ontwerp en de productie van reactoronderdelen , zoals verbeterde prestaties van onderdelen, compacter formaat, beter warmtebeheer en kortere doorlooptijden.
En hier komt 3D-printen in beeld.
3D-printen, of additive manufacturing (AM), staat bekend om zijn ontwerpflexibiliteit, wat veel mogelijkheden biedt voor fabrikanten van nucleaire onderdelen.
De ontwerpflexibiliteit en de geëlimineerde behoefte aan gereedschap zorgen voor consolidatie van onderdelen, een proces waarbij verschillende componenten als één kunnen worden ontworpen en afgedrukt.
Bovendien zijn de meer complexe geometrieën mogelijk met 3D-printen, compactere afmetingen van onderdelen mogelijk maken en hun daaruit voortvloeiende betere prestaties.
Een voorbeeld hiervan zijn 3D-geprinte warmtewisselaars, die kunnen worden ontworpen met wanden zo dun als 200 micron en kleine, ingewikkelde stroomkanalen in het onderdeel, wat resulteert in een groter warmteoverdrachtsoppervlak binnenin. Hoe groter het oppervlak, hoe meer warmte kan worden afgevoerd, waardoor de prestaties van een warmtewisselaar toenemen.
3D-printtechnologieën voor de kernenergie-industrie
Er zijn verschillende AM-technologieën die geschikt zijn voor toepassingen in de kernenergie-industrie, waaronder Powder Bed Fusion (PBF), metaal- en zandbindmiddelstralen en Direct Energy Deposition (DED).
Met poederbedfusie, een proces waarbij een materiaal wordt gesmolten met behulp van krachtige lasers, kunnen fabrikanten complexere componenten maken met verbeterde prestaties.
Het gebruik van bindmiddelstralen, met name met zand, kan helpen om kosten en tijd te besparen door zandvormen in 3D te printen, waardoor het niet meer nodig is om deze vormen handmatig te maken.
DED-technologie – die werkt door metaalmateriaal te smelten met een laser of een elektronenstraal, terwijl het via een mondstuk op het bouwplatform wordt afgezet – kan worden gebruikt als alternatief voor grote giet- en smeedstukken, of als aanvulling daarop. Dit proces kan de doorlooptijd, bewerking en materiaalverspilling verminderen.
Bepaalde DED-processen bieden ook verbeterde materiaaleigenschappen in vergelijking met traditionele methoden. Ze kunnen bijvoorbeeld worden gebruikt voor het plaatselijk aanpassen van materialen, zoals hard-facing voor corrosie en slijtvastheid.
De technologie is ook geschikt voor reparatie van hoogwaardige componenten, gereedschappen en lageroppervlakken.
Belangrijke toepassingen voor 3D-printen in de kernenergiesector
Vervangende onderdelen
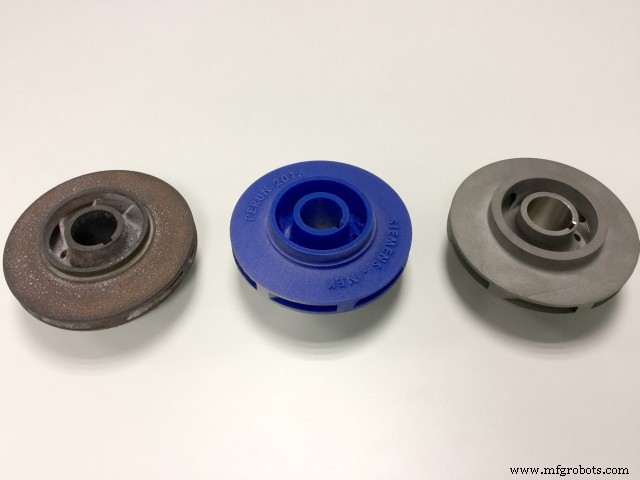
Naarmate kerncentrales ouder worden, wordt het steeds moeilijker om vervangende onderdelen te vinden, niet in de laatste plaats omdat hun ontwerpen vrijwel onmogelijk te verkrijgen zijn. In de VS zijn bijvoorbeeld veel kerncentrales meer dan 40 jaar oud, en veel van de bedrijven die de originele onderdelen maakten, bestaan niet meer.
3D-printen maakt het mogelijk om een deel van de ontbrekende reserveonderdelen te produceren met behulp van reverse engineering, dus het is niet nodig om helemaal opnieuw mallen te maken.
Bijvoorbeeld, Hydro Inc., het pomptechniek- en servicebedrijf, gebruikte reverse engineering om een zandvorm te ontwerpen en in 3D te printen voor een waaier die in een nucleaire faciliteit wordt gebruikt. De mal werd vervolgens naar een gieterij gestuurd, waar het metaal werd gegoten om het onderdeel te maken.
In een ander voorbeeld gebruikte Hydro de combinatie om een veiligheidsgerelateerde pomp in een kerncentrale te repareren. Het onderdeel kon niet binnen het door de klant gewenste tijdsbestek van de OEM worden gekocht, aangezien het traditionele gietproces negen maanden tot een jaar in beslag kon nemen. Door gebruik te maken van 3D-printen, gekoppeld aan reverse engineering, leverde het bedrijf de pomp binnen 12 weken.
Naast 3D-geprinte matrijzen, kan de technologie ook worden gebruikt om direct reserveonderdelen te produceren.
In 2017 had Siemens een belangrijke mijlpaal bereikt door met succes een eerste 3D-geprint reserveonderdeel te installeren voor de kerncentrale van Krško in Slovenië. Het vervangende onderdeel, een metalen waaier met een diameter van 108 mm voor een brandbeveiligingspomp die constant in bedrijf is, voldoet aan de strenge veiligheids- en betrouwbaarheidseisen van de nucleaire sector.
Het gebruik van 3D-printen voor vervangende onderdelen in kerncentrales zorgt ervoor dat volwassen werkende centrales kunnen blijven werken en hun volledige levensverwachting kunnen bereiken.
Geavanceerde componenten
Er is ook meer aandacht voor het ontwikkelen van geavanceerde componenten voor kernenergiesystemen, met behulp van 3D-printen.
Zo gebruikt NovaTech, een bedrijf dat productie- en engineeringdiensten levert aan de nucleaire industrie, 3D-printen om delen van de splijtstofassemblage te ontwikkelen en te produceren die het basiselement vormt van de kernreactorkern.
Sommige onderdelen van de brandstofassemblage, mogelijk met 3D-printen, omvatten ondersproeiers, neerhoudveren, bovensproeiers, kokendwaterreactor (BWR) onderste verbindingsplaten.
NovaTech's onderzoek toont aan dat bijvoorbeeld het 3D-printen van de onderste verbindingsplaat van een BWR-brandstofassemblage, die de positie van het onderste uiteinde van de brandstofstaven fixeert, met behulp van Inconel-718, de vuilfilterprestaties kan verbeteren.
De prestatieverbetering wordt bereikt dankzij het ontwerpen van kronkelige stroomdoorgangen die alleen met 3D-printen kunnen worden vervaardigd.
Met behulp van de technologie is het ook mogelijk om kanaalafdichtingen toe te voegen aan het ontwerp van de onderste verbindingsplaat, waardoor het aantal onderdelen kan worden verminderd.
Het minimaliseren van het aantal componenten in een montage is bijzonder voordelig, omdat het de fabricagekosten verlaagt en het montageproces vereenvoudigt.
Een 3D-geprinte kernreactorkern
In een ander voorbeeld gebruikt Oak Ridge National Laboratory (ORNL) 3D-printen om een kernreactorkern te ontwikkelen als onderdeel van zijn Transformational Challenge Reactor (TCR)-programma.
ORNL streeft ernaar de kern van de kernreactor tegen 2023 te bouwen en nieuwe methoden vast te stellen voor het ontwerp, de fabricage, de vergunningverlening en de exploitatie van reactoren, waarbij 3D-printen een sleutelrol speelt bij het bereiken van deze doelstelling.
Hoewel het grootste deel van de reactor zal worden gemaakt van conventionele componenten, zal de kern, die verantwoordelijk is voor het vasthouden van de uraniumbrandstof en de componenten die de splijtingsreactie regelen, volledig worden 3D-geprint uit siliciumcarbide, een hittebestendig materiaal.
'Door 3D-printen te gebruiken, kunnen we technologie en materialen gebruiken waar de nucleaire gemeenschap de afgelopen decennia niet van heeft kunnen profiteren', zegt Kurt Terrani, technisch directeur van TCR. 'Dit omvat sensoren voor bijna-autonome controle en een bibliotheek met gegevens en een nieuwe en versnelde benadering van de kwalificatie waar de hele nucleaire gemeenschap van profiteert.'
Een 3D-geprint plug-in apparaat
Hoewel een 3D-geprinte reactorkern zich nog in de ontwikkelingsfase bevindt, heeft Westinghouse vorige maand met succes een 3D-geprint onderdeel geïnstalleerd dat wordt gebruikt voor de daadwerkelijke stroomopwekking. Het geïnstalleerde onderdeel is een 'vingerhoedplug-apparaat' dat wordt gebruikt om splijtstofassemblages in reactorkernen te laten zakken.
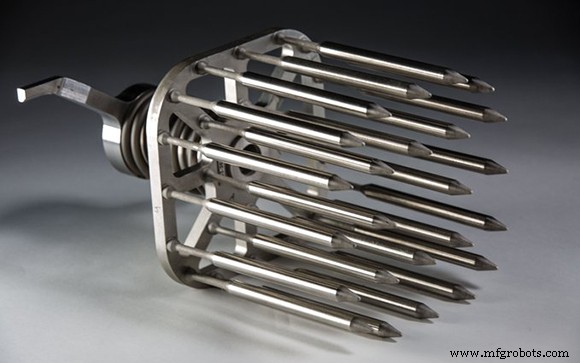
Het onderdeel was het resultaat van een driejarige samenwerking tussen Westinghouse, een leverancier van nucleaire technologie, en Exelon Generation, Amerika's toonaangevende leverancier van kernenergie.
Een stekkerapparaat is essentieel voor de productie van kernenergie, maar het werd beschouwd als een onderdeel met een laag risico, omdat er minimale gevolgen zouden zijn als het onderdeel kapot zou gaan.
3D-geprinte onderdelen voor nucleair afvalbeheer
Uiteindelijk gaat elk nucleair gesprek over radioactief afval en veiligheid.
Het vinden van effectieve oplossingen voor het langetermijnbeheer van radioactief afval is een andere uitdaging binnen de kernenergiesector.
/>3D-printen helpt deze uitdaging aan te gaan door ingenieurs in staat te stellen nieuwe ontwerpen van afvalrecyclingsystemen te ontwikkelen.
In de VS hebben wetenschappers van het Argonne National Laboratory van het Department of Energy 3D-geprinte onderdelen, wat de recycling van verbruikte splijtstof zal vergemakkelijken.
De manier waarop 3D-printen wordt gebruikt in het proces omvat het creëren van een rij van 1,25 cm centrifugale contactors - complexe vloeistofapparaten met interne kanalen. Eenmaal aangesloten, maken de contactors een continue opwerkingslus mogelijk.
Momenteel kunnen nucleaire ingenieurs 95 procent van de verbruikte splijtstof uit een kernreactor recyclen, terwijl de resterende 5 procent moet worden opgeslagen als 'langdurig term' afval. De bovengenoemde 3D-geprinte apparatuur kan worden gebruikt om een deel van de laatste te sorteren en te recyclen, wat betekent dat een extra 2 procent van het kernafval kan worden gerecycled.
Terwijl 2 procent misschien niet bijzonder indrukwekkend klinkt vooruitgang, kan het de hoeveelheid verbruikte brandstof die moet worden opgeslagen en de tijdsduur dat het gevaarlijk blijft aanzienlijk verminderen.
3D-printen voor ingebouwde sensoren
Kernreactoren zijn zeer goed uitgerust om variabelen als temperatuur en druk te bewaken. Het is echter een uitdaging om de structurele gezondheid van een reactoronderdeel tijdens bedrijf te bewaken, wanneer het wordt blootgesteld aan extreme temperaturen en straling.
Een obstakel is de moeilijkheid om sensoren in hitte- en stralingsbestendige materialen in te bouwen. Maar 3D-printen kan een oplossing bieden.
De nieuwe ontwerpen, mogelijk gemaakt door 3D-printen, zullen ingebouwde sensoren mogelijk maken die gegevens rechtstreeks vanuit de kern leveren.
ORNL, voor gebruikt bijvoorbeeld ultrasone AM om zeer nauwkeurige, stralingsharde sensoren in constructies en componenten in te bedden.
Bovendien heeft het Amerikaanse ministerie van Energie (DoE) de University of Pittsburgh Swanson School of Engineering een subsidie verleend om AM-technieken te ontwikkelen om elektrische sensoren voor nucleaire kernen te maken.
Gestart in 2017, heeft het project al enig succes gehad bij de ontwikkeling van glasvezelsensornetwerken. Het team heeft onlangs de eerste succesvolle test gevierd van een in-core glasvezelsensor in een van de MIT-reactoren.
Nieuwe materialen voor nucleaire toepassingen
Kerncentrales van de volgende generatie zullen materiaalinnovatie nodig hebben om te voldoen aan de vraag van hun agressieve omgeving, waaronder uitdagingen op het gebied van corrosie bij hoge temperaturen en hoge stralingsdoses.
AM kan snellere materiaalinnovatie ondersteunen. Het kan bijvoorbeeld nieuwe legeringen mogelijk maken met eigenschappen die niet met traditionele methoden kunnen worden geproduceerd. Het proces kan ook materialen zoals silicium gebruiken die niet kunnen worden bewerkt met traditionele metaalbuigmethoden.
Een voorbeeld hiervan is een recente samenwerking tussen de Zweedse ontwikkelaars van 3D-printmateriaal, Additive Composite Uppsala en Add North 3D, aan de ontwikkeling van een polymeer composietmateriaal voor stralingsafschermende toepassingen.
Het materiaal, genaamd Addbor N25, combineert boorcarbide en nylon, in de vorm van een filament dat is geoptimaliseerd voor 3D-printen. De stralingsafschermende eigenschappen worden bereikt dankzij het boorcarbide-element, dat zorgt voor een effectieve absorptie tegen neutronen.
De nucleaire industrie vernieuwen met 3D-printen
Hoewel we nog maar aan het begin staan van wat er mogelijk is met 3D-printen in de nucleaire industrie, wijzen de recente ontwikkelingen op het enorme potentieel dat de technologie te bieden heeft.
Als fabrikanten de vrijheid omarmen die 3D-printen biedt, kunnen ze verbeterde componentontwerpen leveren, nieuwe materialen verkennen en op kosteneffectieve wijze reserveonderdelen produceren die niet langer beschikbaar zijn.
We zullen de komende jaren zeker meer opwindende innovaties op het gebied van 3D-printen zien, die nucleaire technologie helpen de huidige uitdagingen het hoofd te bieden en de veiligheid en duurzaamheid ervan verder te verbeteren.
3d printen
- Hoe drijft Tungsten de lucht- en ruimtevaartindustrie aan?
- Hoe verandert 3D-printen de defensie-industrie?
- Hoe verandert 3D-printen de auto-industrie? (2021)
- Hoe 3D-printen de reserveonderdelenindustrie transformeert [update 2021]
- Applicatie Spotlight:3D-printen voor medische implantaten
- Applicatie Spotlight:3D-printen voor fietsproductie
- Applicatie Spotlight:3D-printen voor lagers
- Applicatie Spotlight:3D-printen voor warmtewisselaars
- Applicatie Spotlight:3D-printen in de spoorwegindustrie
- Hoe 3D-printen wordt gebruikt in de matrijsindustrie
- Toepassing van 3D-printen in de auto-industrie