Application Spotlight:hoe 3D-printen zorgt voor beter presterende hydraulische componenten
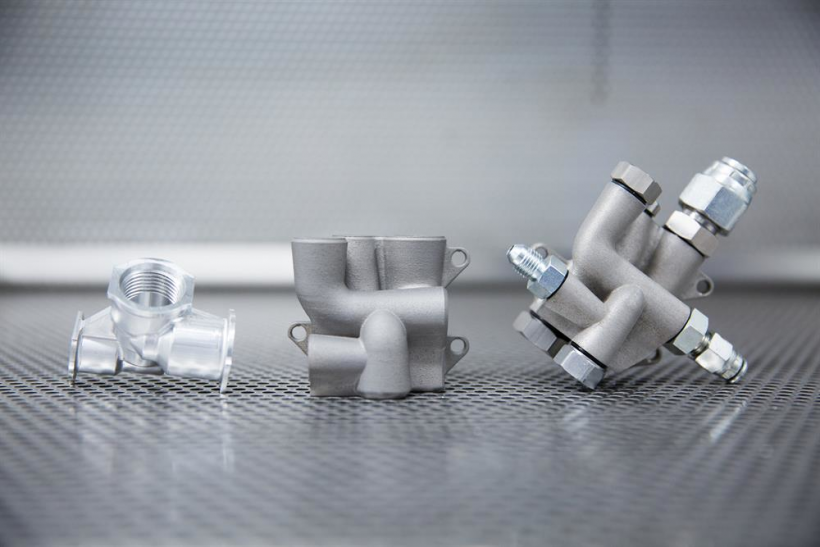
[Afbeelding tegoed:Renishaw]
De vraag naar nieuwe benaderingen in het ontwerp en de fabricage van hydraulische componenten neemt toe. Een technologie die fabrikanten in staat stelt om nieuwe mogelijkheden in de productie van hydrauliek te verkennen, is 3D-printen.
Van Liebherr en Ford tot Bosch Rexroth, bedrijven wenden zich tot 3D-printen om energiezuinigere, lichtere en goedkopere hydraulische componenten te maken.
De Application Spotlight van vandaag duikt in de voordelen van 3D-printen voor hydraulische systemen en componenten, terwijl ze de meest opwindende voorbeelden van de technologie in actie verkent.
Bekijk de andere toepassingen die in deze serie worden behandeld:
3D-printen voor warmtewisselaars
3D-printen voor lagers
3D-printen voor fietsproductie
3D-printen voor productie van digitale tandheelkunde en heldere uitlijners
3D-printen voor medische implantaten
3D-geprinte raketten en de toekomst van de fabricage van ruimtevaartuigen
3D-printen voor de productie van schoenen
3D-printen voor elektronische componenten
3D-printen in de spoorindustrie
3D-geprinte brillen
3D-printen voor productie van eindonderdelen
3D-printen voor beugels
3D-printen voor turbineonderdelen
Hoe 3D-printen innovatie in de kernenergie-industrie ondersteunt
Waarom 3D-printen gebruiken voor hydraulische componenten?
Hydrauliek is een van de meest efficiënte manieren om beweging te creëren wanneer er sprake is van zware lasten of wanneer herhaalde bewegingen nodig zijn.
Hydraulische systemen gebruiken pompen om een vloeistof onder druk te zetten, en de beweging ervan wordt vervolgens gebruikt om alles aan te drijven, van kranen tot auto's.
Hydrauliek is dagelijks overal om ons heen. Het wordt gebruikt in voertuigen, bouwmachines, gebouwen en productiefaciliteiten.
Hydraulische componenten worden traditioneel vervaardigd door middel van machinale bewerking of gieten. Veel fabrikanten van hydraulische apparatuur raken echter geïnteresseerd in het produceren van hydraulische componenten, zoals spruitstukken, servokleppen en hydraulische adapterblokken, met behulp van 3D-printen. Maar waarom overwegen ze de technologie in de eerste plaats?
Volgens Steffen Haack, hoofd van de Industrial Hydraulics Business Unit bij Bosch Rexroth AG, zijn er veel trends die de hydraulische industrie vormgeven, waaronder:
- Energie-efficiëntie (verminderde stromingskrachten, minder drukverlies, hogere efficiëntie)
- Ruisonderdrukking
- Verlaagde tankvolumes
- Hoger drukniveau en minder installatieruimte
- Verbeterde materiaal- en olie-eigenschappen
- Hogere beschikbaarheid en voorspellend onderhoud
- Gebruiksvriendelijkheid
- Veiligheid
3D-printen, met name met metalen en zand, speelt een belangrijke rol bij het aanjagen van sommige van deze trends, zoals verhoogde energie-efficiëntie en kleinere installatieruimte.
Hoe? Door geavanceerde ontwerpen mogelijk te maken die het mogelijk maken om nieuwe functies op te nemen, het gewicht en de afmetingen van componenten te verminderen en de algehele prestaties van het hydraulische systeem te verbeteren.
Laten we dieper ingaan op de voordelen van 3D-printen voor hydrauliek.
Het gewicht en de afmetingen van hydraulische componenten verminderen
Met 3D-printen kunnen fabrikanten van hydraulische componenten onderdelen lichter en kleiner maken.
Neem als voorbeeld een hydraulisch spruitstuk. Dit onderdeel, dat helpt om de vloeistofstroom tussen de componenten van een hydraulisch systeem te regelen, wordt meestal vervaardigd uit een massief blok metaal.
Het verwijderen van meer overtollig metaal dan nodig is, is duur, en vaak wordt het overtollige metaal niet weggefreesd, wat resulteert in een onderdeel dat meer weegt dan het mogelijk zou kunnen.
3D printen helpt dit probleem op te lossen, aangezien er bijna dezelfde hoeveelheid materiaal nodig is om een verdeelstuk te produceren.
In een metaal 3D-printproces, zoals Selective Laser Sintering, traceert een laser een microndunne doorsnede van een onderdeel, waarbij selectief een metaalpoeder laag voor laag wordt gesmolten en versmolten. Hierdoor kunnen ingenieurs de hoeveelheid materiaal regelen die in het onderdeel gaat, waarbij minder metaal wordt gebruikt dan bij CNC-bewerking nodig zou zijn.
Naast het verminderen van het gewicht van componenten, maakt 3D-printen ook compactere onderdelen mogelijk die beter passen in krappe ruimtes. Dit voordeel maakt 3D-geprinte hydraulische componenten bijzonder gewild in toepassingen die hoge precisie en een laag gewicht vereisen.
Spotlight:Aidro's 3D-geprinte spruitstuk
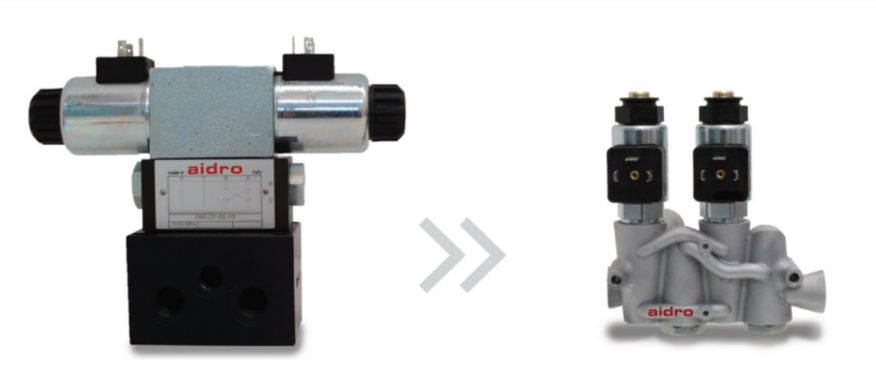
Een voorbeeld van een 3D-geprint hydraulisch onderdeel is afkomstig van de Italiaanse fabrikant Aidro.
Aidro's hydraulische spruitstuk, dat wordt gebruikt in landbouwmachines, is opnieuw ontworpen om gewicht en ruimte te besparen in een systeem waarin het wordt gebruikt. Het 3D-geprinte aluminium spruitstuk vervult dezelfde functies als de eenheid die het vervangt, maar is de helft minder formaat en 75 procent lichter dan het vorige spruitstuk.
Gedeeltelijke consolidatie
Met 3D-printen kunnen componenten ook kleiner worden gemaakt door meerdere onderdelen in één te integreren - een benadering die bekend staat als onderdeelconsolidatie.
Hierdoor kunnen fabrikanten complexe samenstellingen van componenten elimineren en de structurele integriteit van een onderdeel verbeteren, aangezien er minder zwakke verbindingspunten zijn die lekkage kunnen veroorzaken.
Efficiëntie optimaliseren
3D-printen maakt het mogelijk om de interne geometrie van een hydraulisch onderdeel opnieuw te ontwerpen om de vloeistofstroom te optimaliseren en de drukval te verminderen.
Als we bijvoorbeeld verdeelstukken nemen, kunnen ingenieurs vloeistofstroomkanalen in een verdeelstuk precies daar plaatsen waar ze zich bevinden nodig en in verschillende soorten en maten. Dit betekent dat stroomkanalen gebogen vormen kunnen hebben en dichter bij elkaar kunnen worden geplaatst dan bij conventionele verdeelstukken, wat het eindproduct compacter en lichter maakt.
Gebogen stroompaden kunnen naar verluidt de stroomefficiëntie met 30 tot 70 procent verbeteren.
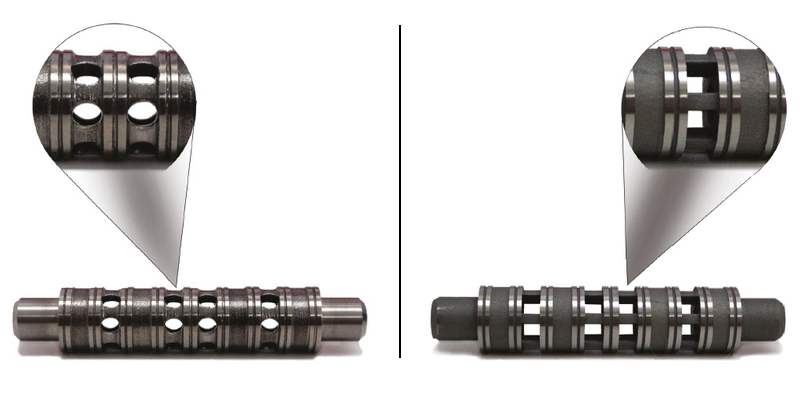
Het opnieuw ontwerpen van een vorm van de doorsnede van stroomkanalen kan ook een verschil maken. Stroompaden in klepspoelen hebben bijvoorbeeld typisch een ronde vorm, omdat ze zijn bewerkt met roterende messen.
Met 3D-printen kunnen ingenieurs dwarsdoorsneden van stroompaden ontwerpen die vierkant zijn in plaats van rond, wat de stroomcapaciteit tot 20 procent kan verhogen en de drukval kan verminderen.
Bovendien vereisen traditionele hydraulische componenten, zoals spruitstukken, vaak de machinale bewerking van dwarsgeboorde doorgangen die vervolgens moeten worden afgesloten om olielekkage te voorkomen. Deze verstopte kanalen creëren echter potentiële lekpaden die een systeemstoring kunnen veroorzaken. 3D-printen elimineert dit probleem door de noodzaak om in de eerste plaats geperforeerde passages te maken, weg te nemen.
Meer voorbeelden van 3D-geprinte hydraulische componenten
3D-printen van een hydraulisch adapterblok
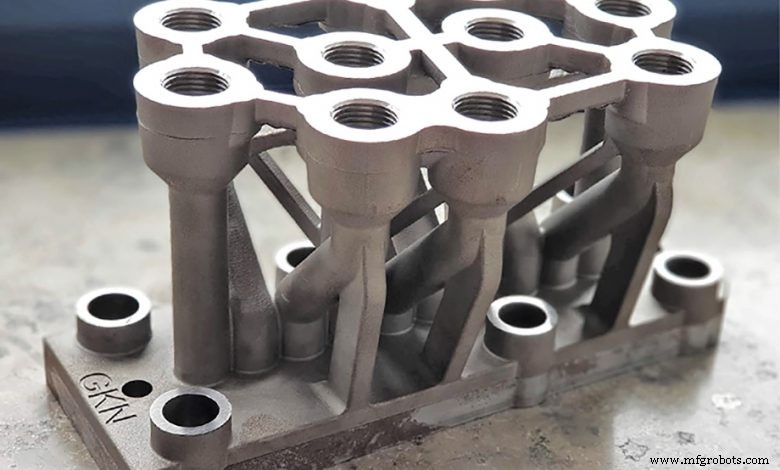
GKN Additive heeft een hydraulisch adapterblok in 3D geprint, een verdeelstuk dat de vloeistofstroom in een hydraulisch systeem stuurt en kleppen, pompen en actuatoren met elkaar verbindt.
Traditioneel gebruikte hydraulische blokken hebben meestal een blokvormig ontwerp met een reeks interne kanalen erin geboord. Het productieproces van hydraulische blokken begint met het boren van gaten van boven en onder.
De verticale gaten worden vervolgens verbonden door horizontale kanalen en de draden worden erin gesneden. Om olielekkage uit de open horizontale kanalen te voorkomen, worden ze afgedicht met stelschroeven en afgedicht.
Dit proces is echter om verschillende redenen zeer inefficiënt. Ten eerste zorgen de geboorde en gefreesde randen voor scherpe bramen die in de nabewerking moeilijk te bereiken zijn. Deze kunnen tijdens het gebruik soms afbreken en een systeemstoring veroorzaken.
Ten tweede genereren de scherpe hoekverbindingspunten turbulente stroming, wat resulteert in energie-inefficiënties. Ten derde kunnen ongebruikte horizontale kanalen vuil ophopen, waardoor de levensduur van het hydraulische systeem wordt verkort.
3D-printen heeft GKN Additive geholpen de bovenstaande uitdagingen te overwinnen om een beter presterend hydraulisch blok te creëren.
Het gewicht van het hydraulisch blok is teruggebracht van 30 kg naar 5,5 kg, zonder in te boeten aan functionaliteit. Met een nieuw ontwerp was het mogelijk om het overtollige materiaal te verwijderen en ervoor te zorgen dat er geen overlappende gaten in het onderdeel waren.
Bovendien laat het nieuwe ontwerp de ongebruikte horizontale kanalen helemaal weg, zodat vuil zich nergens kan ophopen. Ten slotte hebben ingenieurs, om de turbulente stroming in het systeem te verminderen, scherpe interne hoeken vervangen door gladde pijpleidingen.
Als we de voordelen van 3D-printen voor deze toepassing opsommen, stelde 3D-printen de fabrikant in staat om de functionaliteit van het onderdeel te verbeteren, terwijl er minder materiaal werd gebruikt. Dit vertaalde zich in een lager gewicht van het onderdeel en lagere productiekosten.
Liebherr's 3D-geprinte hydraulische kleppenblok
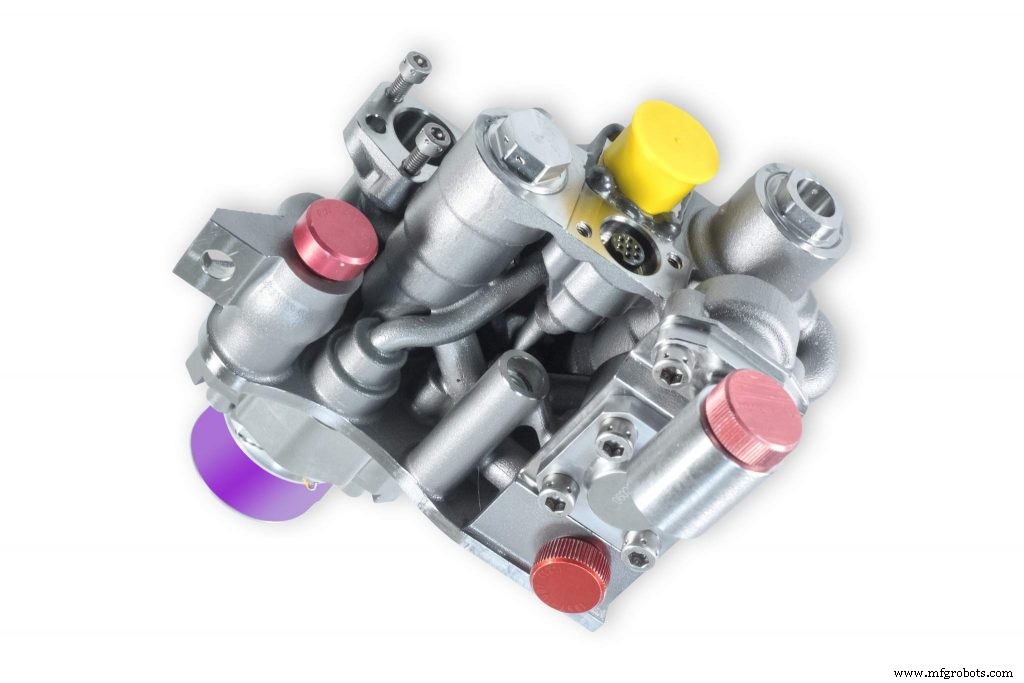
Een ander goed voorbeeld van 3D-printen voor hydrauliek komt van de Liebherr Group. Met behulp van 3D-printen kon het bedrijf een hydraulisch hogedrukventielblok, dat in vliegtuigen wordt gebruikt, opnieuw ontwerpen om het lichter en efficiënter te maken.
Het Liebherr-team integreerde 10 functionele elementen in het nieuwe kleppenblok, waardoor het complexe systeem van leidingen met veel dwarse boringen werd geëlimineerd. Het resultaat is een 35 procent lichter kleppenblok, gemaakt van minder onderdelen.
Het 3D-geprinte onderdeel is met succes getest in een testvlucht van het A380-vliegtuig.
Domin Fluid Power vernieuwt zijn vloeistofstroomsystemen met 3D-printen
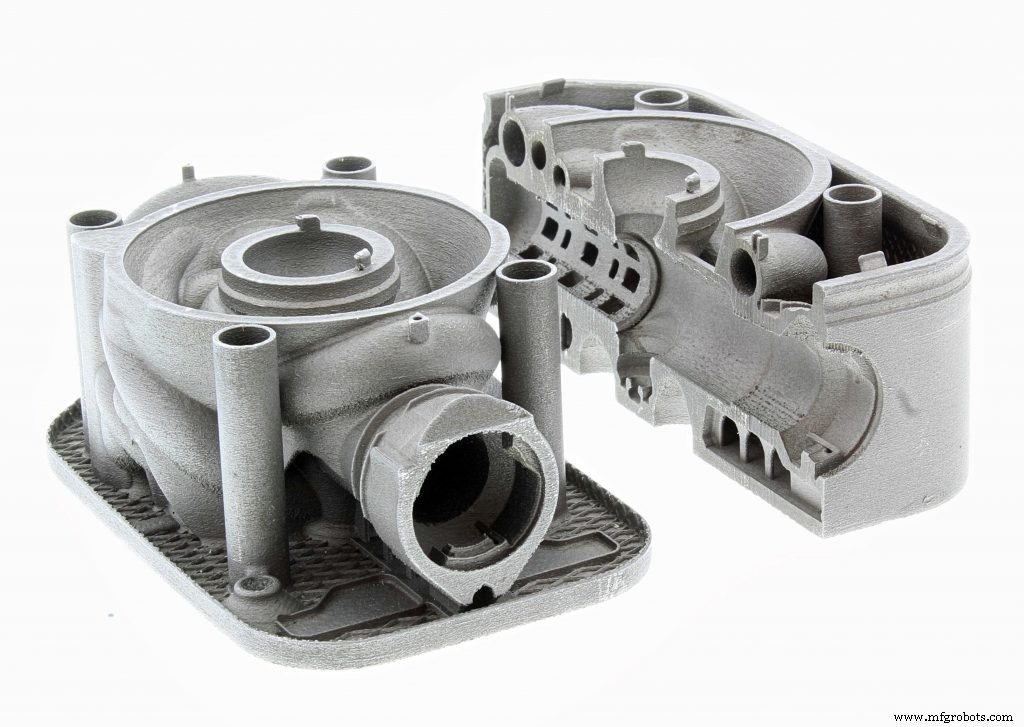
De in het VK gevestigde fabrikant van hydraulische systemen, Domin, is overgestapt op 3D-printen om zijn hoogwaardige servokleppen met directe aandrijving te herontwikkelen, die worden gebruikt voor het omzetten van signalen in druk.
Domin stelt dat 3D-printen het de mogelijkheid geeft om complexe onderdelen sneller en zonder gereedschap te bouwen. Het bedrijf heeft bijvoorbeeld een van zijn schijven ontworpen die 25 procent van de oorspronkelijke grootte en 25 procent krachtiger is. Het onderdeel is geproduceerd voor een derde van de kosten en de fabricagetijd is teruggebracht van 5,5 uur tot slechts 1 uur.
Dergelijke resultaten zijn onmogelijk te bereiken met conventionele methoden, beweert Domin.
Ford 3D print een inlaatspruitstuk
Hoewel we voorbeelden hebben gezien van hydraulische componenten die 3D zijn geprint voor zwaar materieel en vliegtuigen, heeft Ford baanbrekend werk verricht in 3D-printen voor hydraulische systemen voor auto's.
Vorig jaar demonstreerde de autofabrikant wat hij beweert het grootste 3D-geprinte metalen inlaatspruitstuk te zijn dat ooit in een werkend voertuig is geplaatst.
Dat voertuig is de 'Hoonitruck' van Ken Block Ford pick-up.
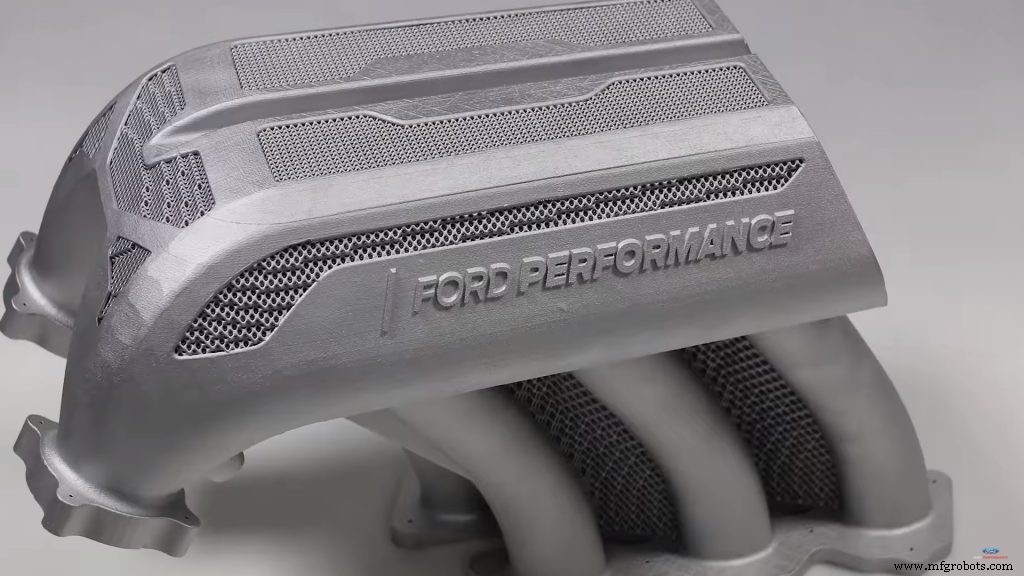
Het voertuig had een speciaal inlaatspruitstuk nodig om de cilinders van de motor te voorzien van lucht uit de turbocompressoren, en Ford besloot over te gaan op 3D-printen van metaal.
Het onderdeel is 3D-geprint van aluminium, met behulp van een Concept Laser-machine, en het duurde 5 dagen om te bouwen. Door gebruik te maken van geavanceerde CAD-software was het mogelijk om een complexe webachtige structuur te creëren die niet met traditionele productiemethoden kon worden gemaakt. Het ontwerp is geoptimaliseerd voor betere prestaties en een lager gewicht - het laatste onderdeel weegt slechts 6 kg.
Bosch Rexroth gebruikt zand 3D-printen voor spruitstukken
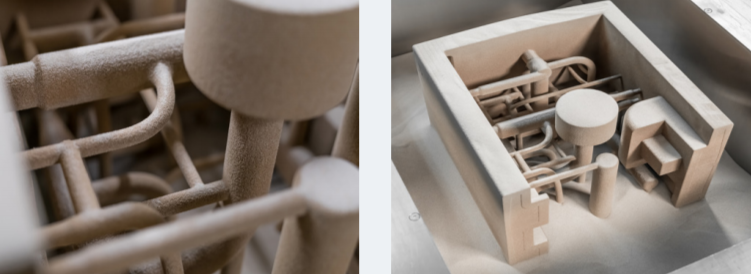
Naast het 3D-printen van metaal is het ook mogelijk om een zandkern 3D te printen waarmee vervolgens een hydraulisch onderdeel kan worden gegoten. Het proces dat voor deze toepassing wordt gebruikt, heet binderjetting, en het werkt door selectief een bindmiddel af te zetten op een laag kwartszand.
Bosch Rexroth gebruikt al enkele jaren zand 3D-printen voor het produceren van gietkernen voor stuurblokken.
Als een van de belangrijkste voordelen hiervan noemt Bosch Rexroth de mogelijkheid om machinecomponenten, zoals filters in het spruitstuk, te integreren en een gewichtsvermindering tot 30 procent.
Bijkomende voordelen zijn onder meer de eliminatie van hulpgaten die lekken kunnen veroorzaken en optimalisatie van interne stroomkanalen die de energie-efficiëntie verbeteren.
Hydraulische componenten herontdekken met 3D-printen
Omdat de hydraulische industrie streeft naar energiezuinigere en kleinere hydraulische componenten, biedt 3D-printen een mogelijkheid om beter presterende ontwerpen te ontwikkelen en te produceren.
Gezien de voordelen in doorlooptijd, gewichtsbesparing en de kosten en prestaties die mogelijk worden gemaakt door 3D-printen, beginnen veel fabrikanten van hydraulische componenten deze technologie voor hun producten te verkennen.
In de toekomst verwachten we dat de rol van 3D-printen bij de productie van hydraulische componenten zal toenemen, waardoor bedrijven in de hydraulische industrie de huidige en toekomstige trends kunnen bijhouden.
3d printen
- Applicatie Spotlight:3D-printen voor medische implantaten
- Applicatie Spotlight:3D-printen voor digitale tandheelkunde &Clear Aligner-productie
- Applicatie Spotlight:3D-printen voor fietsproductie
- Applicatie Spotlight:3D-printen voor lagers
- Applicatie Spotlight:3D-printen voor warmtewisselaars
- Applicatie Spotlight:3D-printen in de spoorwegindustrie
- Applicatie Spotlight:5 elektronische componenten die kunnen profiteren van 3D-printen
- Applicatie Spotlight:3D-printen voor schoenen
- Applicatie Spotlight:3D-geprinte raketten en de toekomst van de fabricage van ruimtevaartuigen
- Applicatie Spotlight:3D-geprinte brillen
- Applicatie Spotlight:3D-printen voor turbineonderdelen