Expertinterview:Altair's Ravi Kunju over simulatiesoftware voor 3D-printen
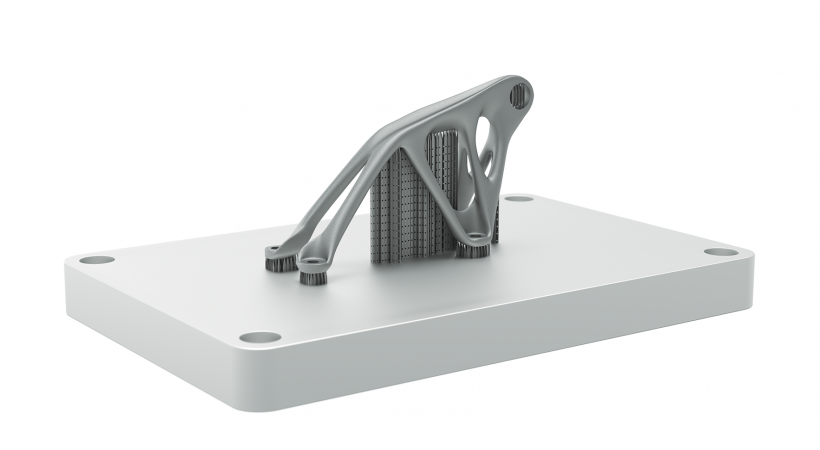
Het bereiken van een eenvoudigere en snellere workflow voor ontwerpvoorbereiding was een voortdurende zoektocht binnen de 3D-printindustrie. Ontwerpen voor Additive Manufacturing is een complex proces, met zijn unieke uitdagingen en kansen.
Daarom zijn relevante tools nodig om ingenieurs in staat te stellen ten volle te profiteren van de ontwerpflexibiliteit van AM. Altair is zo'n bedrijf dat deze oplossingen ontwikkelt. Altair is een wereldwijd technologiebedrijf dat software en cloudoplossingen levert op het gebied van productontwikkeling, high-performance computing en data-analyse.
In het Expert Interview van deze week spreken we met Ravi Kunju, Sr. VP Business Development &Strategy, Simulation-Driven Design, bij Altair. Met Ravi leren we meer over de onlangs gelanceerde Altair Inspire Print3D-softwaretool, de huidige stand van simulatiesoftware voor 3D-printen en verkennen we enkele van de opwindende AM-toepassingen die mogelijk worden gemaakt door Altair-oplossingen.
Kun je ons iets vertellen over Altair en de uitdagingen die je oplost?
We zijn een wereldwijd technologiebedrijf dat software en cloudoplossingen levert op het gebied van productontwerp, productontwikkeling, high-performance computing en ook data-analyse.
Onze visie, en wat we hebben gedaan in de meer dan 30 jaar dat we actief zijn, is om de besluitvorming over producten en bedrijven te transformeren door middel van onze simulatietechnologie, onze oplossingen voor gegevensanalyse en ook onze toonaangevende oplossingen voor ontwerpoptimalisatie .
Ik ben verantwoordelijk voor de simulatie-gedreven ontwerpproducten voor Altair.
U hebt onlangs de Altair Inspire Print3D-software gelanceerd. Kunt u de verschillende softwareoplossingen die u levert uitleggen?
Altair Inspire Print3D is slechts een van de vele oplossingen die we aanbieden.
Altair is al jaren toonaangevend op het gebied van optimalisatie. We hebben klanten die onze optimalisatietechnologie gebruiken om hun ontwerpen te maken voor allerlei productiemethoden - of het nu gaat om het vormen van plaatstaal, gieten, extrusie of spuitgieten. Ze gebruiken onze technologie ook om de prestatie-eisen beter te begrijpen en generatieve ontwerpen te maken die specifiek zijn voor een productieproces.
In die context is het belangrijk om de twee uiteinden van het spectrum te begrijpen. De ene drijft het ontwerp en de andere is wat er gebeurt als je eenmaal een ontwerp hebt dat je wilt maken. Deze elementen komen samen op ons platform.
Een van de dingen die we met ons Inspire-platform hebben gedaan, is om het simulatiegestuurde ontwerpproces vooraf te introduceren en het de ontwerpers heel gemakkelijk te maken om ontwerpen te begrijpen en aan te sturen, terwijl ze volledig op de hoogte zijn van de productieproces.
Omdat het niet verstandig is om het productieproces te scheiden van de ontwerpvereisten, hebben we ze allemaal in één enkele omgeving geplaatst via ons platform.
Dus, Inspire Print3D is gericht op twee dingen. Een daarvan is dat het onze gebruikers onder het Inspire-platform in staat stelt om ontwerpen te genereren die specifiek zijn voor elk AM-proces; met behulp van specifieke fabricageregels (beperkingen) die het ontwerp ertoe aanzetten om aan het fabricageproces te voldoen.
De tweede is om alle prestatie-eisen te nemen en ze te combineren, en geavanceerde numerieke methoden te gebruiken om automatisch een ontwerp te genereren voor selectief lasersmelten (SLM) of fused deposition (FDM) of binder jetting (MJF) of Wire Arc Additive Manufacturing (WAAM).
Dus met de Print 3D-module kunt u niet alleen het ontwerp genereren, maar helpt u ook bij het virtueel valideren van de prestaties van het nieuwe ontwerp dat u hebt gemaakt.
Met de eerste release van Print3D kan de gebruiker het selectieve lasersmeltproces simuleren. In deze omgeving is een geavanceerde thermomechanische simulatie ingebed om eventuele fabricageproblemen te evalueren die zich tijdens 3D-printen kunnen voordoen, zoals vervorming, hoge spanningen en breuken die daarmee gepaard gaan. De ontwerpers kunnen het ontwerp genereren en de ondersteunende structuren toevoegen, en alle problemen oplossen in één enkele omgeving voordat ze gaan printen.
Het grootste voordeel dat we zien, is dat als je tegenwoordig kijkt naar wat de klanten in AM doen, ze meestal een suboptimale benadering hebben voor het creëren van een optimaal ontwerp. Bovendien, als ze eenmaal een ontwerp hebben bedacht, zullen ze proberen ondersteunende structuren aan te brengen om ervoor te zorgen dat ze het onderdeel kunnen afdrukken en later ontdekken dat ze problemen hebben. Voor al deze stappen zijn er aparte softwareoplossingen.
Altair elimineert dat allemaal door gebruikers in staat te stellen een onderdeel te ontwerpen en te evalueren binnen één enkele omgeving.
Het is algemeen bekend dat ongeveer 45 procent van de kosten die tegenwoordig met metaal AM gepaard gaan, kan worden toegeschreven aan het verwijderen van ondersteuning. Door onze ontwerpregels (beperkingen) effectief te gebruiken, kunnen eindgebruikers ontwerpen maken met minimale of nul ondersteuningen. We stellen gebruikers ook in staat om een ondersteunende structuur te creëren, de effectiviteit ervan te begrijpen door middel van de thermomechanische simulatie; waarin we de opbouw, koeling, ondersteuningsverwijdering kunnen simuleren en de daaropvolgende terugvering en bijbehorende vervorming kunnen voorspellen en stroomafwaartse storingen kunnen voorkomen.
Dat is wat Inspire Print3D doet:het stelt eindgebruikers in staat om uw ontwerp te bedenken, evalueren en valideren in één enkele omgeving. Altair Inspire helpt onze eindgebruikers dus om lichtgewicht en hoogwaardige ontwerpen te maken en tegelijkertijd de productiviteit te verbeteren.
Hoe zou u de huidige staat van ontwerp-, simulatie- en topologie-optimalisatiesoftware voor AM omschrijven?
Altair is al een aantal jaren toonaangevend op het gebied van topologie-optimalisatie en generatief ontwerp, niet alleen voor additieve, maar voor alle productieprocessen. We hebben meer dan 5.000 klanten die onze producten dagelijks gebruiken om optimale ontwerpen te creëren.
Maar niet alle generatieve ontwerptools zijn hetzelfde. We hebben de beste numerieke methoden om belangrijke problemen op te lossen en we zijn de enigen die verschillende prestatiecriteria nemen, belastingsgevallen samenvoegen en combineren met productiebeperkingen, om ontwerpen te maken die zeer specifiek zijn voor dat ontwerpproces.
Om een ontwerp aan te sturen en te genereren, moeten er twee dingen goed worden begrepen:prestatie-eisen en het fabricageproces.
Als u bijvoorbeeld metaal giet en geen kernen wilt hebben, die opofferend en duur zijn, of, als u een vorm wilt creëren zonder ondersnijdingen voor het efficiënt verwijderen van patronen uit de matrijsholte; de juiste fabricagebeperkingen moeten worden gecombineerd met hoogwaardige fabricage om een lichtgewicht ontwerp te genereren.
Er zijn veel tools die een organisch ontwerp kunnen genereren, en mensen hebben de neiging om te denken dat dit alles is wat nodig is. Maar in feite is dat nog maar het begin, want u wilt er zeker van zijn dat u de fabricageprocessen begrijpt en begrijpt wat het optimale ontwerp voor een bepaald proces zou moeten zijn. Alleen het genereren van een optimale vorm is niet voldoende als u de fabricagevereisten niet begrijpt.
In de generatieve ontwerpruimte zijn er veel numerieke benaderingen die u kunt gebruiken; je kunt bijvoorbeeld sommige ontwerpvariabelen verstoren en duizenden ontwerpen genereren en dan zeggen:'Ik ga al deze verschillende vormen en maten variëren en dat zal me duizend ontwerpen opleveren, elk ervan evalueren en dan de beste identificeren. ' Dit kan suboptimaal, tijdrovend en duur zijn voor bepaalde optimalisatie op componentniveau. Het kan zijn dat u geen goede oplossing krijgt.
Op het gebied van simulatie is AM tegenwoordig voornamelijk beperkt tot prototyping. Maar Altair is op zoek geweest om onze klanten te helpen het proces te transformeren om meer dan eenmalige onderdelen te maken. Kunnen we de andere methoden, zoals binder jetting, onderzoeken? Kunnen we hybride gieten onderzoeken, waarbij je zandprint en vervolgens gietstukken in een zandvorm giet? Kunnen we enkele van deze opties onderzoeken om uw capaciteit om te zetten in capaciteit?
Dat is onze zoektocht geweest om de unieke productievereisten grondig te begrijpen. Tegenwoordig zijn we toonaangevend op het gebied van het maken van hoogwaardige lichtgewicht onderdelen, evenals gereedschappen en assemblage, met behulp van het nieuwste ontwerp voor productiemethoden.
Kunt u iets vertellen over enkele van de toepassingen die zijn gerealiseerd, mede dankzij uw ontwerpsoftware?
De eerste adoptanten waren de satelliet- en ruimtevaartbedrijven, omdat ze geen grote volumes hadden, maar ze hadden sterk geoptimaliseerde en lichtgewicht ontwerpen nodig. We ontwierpen een telescoopbeugel en andere beugels met EOS voor EADS waar complexe belastingen een rol speelden.
We werken ook samen met autofabrikanten, waaronder BMW, Ford, GM en een overvloed aan andere bedrijven over de hele wereld die additive manufacturing onderzoeken als een haalbare optie voor prototyping.
Als ik het doorsnijd, zien we niet alleen direct 3D-printen, maar ook een overvloed aan hybride productie, waarbij traditionele productie wordt gecombineerd met additief. Wat ik daarmee bedoel is bijvoorbeeld zand 3D-printen van kernen en mallen voor gieten.
Het tweede gebied zijn matrijzen voor kunststof spuitgieten. Het is belangrijk dat het vormsamenstel dat de holte vormt, niet scheidt tijdens de drukverhogingscyclus die een flits veroorzaakt die moet worden verwijderd. De hele mal kan structureel worden geoptimaliseerd met behulp van generatief ontwerp om de integriteit onder de belastingen te behouden.
Naast de structurele optimalisatie, kunnen we ook optimaliseren voor warmteafvoer met conforme koellijnen die zich om gebieden wikkelen die snelle koeling vereisen. Dergelijke organische structuren zijn ideaal voor 3D-printen.
We werken met PROTIQ aan deze voorbeelden, waarbij je bijna van 9 seconden cyclustijd naar 3 seconden kunt gaan. Dus als je een miljoen onderdelen per dag maakt, kun je 3 miljoen onderdelen per dag maken. Het betekent dat u uw productiviteit kunt verdrievoudigen door de matrijs voor het spuitgietproces te optimaliseren.
We werken ook samen met de robotica-industrie, die tal van toepassingen heeft waar ontwerpoptimalisatie en 3D-printen worden gebruikt voor robottoepassingen. -of-arm grijpers. De grijpers hebben de neiging zeer snel te slijten en moeten daarom onmiddellijk worden vervangen om onderbrekingen in de assemblagelijn te voorkomen.
Voor extreem grote constructies hebben we onlangs samengewerkt met MX3D aan een 3D-geprinte robotarm. MX3D is een 3D-printbedrijf dat gebruik maakt van gepatenteerde draadboogtechnologie om grote metalen constructies te produceren.
Onze software-enabled MX3D optimaliseert het ontwerp van de robotarm om meer dan de helft van het oorspronkelijke gewicht te verminderen, rekening houdend met printbeperkingen. Voor dit project hebben onze ingenieurs Generative Design Customization gebruikt om de meest efficiënte vorm voor de 3D-geprinte robotarm te bedenken.
Er zijn ook veel defensietoepassingen die kunnen profiteren van 3D-printen. Als bijvoorbeeld een onderdeel van een gevechtsvoertuig kapot gaat, wil je dit onderdeel direct lokaal kunnen printen, zonder te hoeven wachten op een vervangend onderdeel. Dit is met name het geval voor oudere onderdelen waarvoor u mogelijk geen tekeningen heeft.
Onze oplossingen worden ook gebruikt op het gebied van medisch 3D-printen. Andiamo, een orthesenbedrijf, gebruikt bijvoorbeeld 3D-printen om beter passende orthesen te maken. De traditionele manier om een orthese te maken is door een ledemaat van een torso in gips te wikkelen, dat vervolgens wordt afgesneden en opgestuurd voor handmatige fabricage.
Andiamo's proces elimineert de noodzaak voor gipsafgietsels, in plaats daarvan begint het met een digitale 3D-scan van het lichaam, waardoor een zeer nauwkeurig model ontstaat om rond te ontwerpen. Het proces omvat ook tal van simulaties om een perfecte pasvorm voor een kind te garanderen.
We zien ook een toegenomen interesse in 3D-printprocessen zoals binder jetting. We werken op dit gebied samen met enkele van onze partners, zoals Desktop Metal en ExOne. We presenteerden binder jetting-toepassingen op Formnext, waar we het hele proces van het maken van een fietsbeugel met FDM, SLM, Hybrid-Casting en binder jetting-proces hebben doorlopen.
Als je naar de industrie in het algemeen kijkt, wat zie je dan als enkele van de belangrijkste ontwikkelingen voor 2020?
De industrie gaat erg snel. Telkens wanneer ik naar AM-evenementen ga, is het duidelijk dat het aantal printerfabrikanten en materiaalleveranciers jaar na jaar bijna verdubbelt. Nu de concurrentie toeneemt, ben ik er zeer zeker van dat de kosten zullen worden verlaagd, wat op dit moment een groot afschrikmiddel is voor de additieve productie.
Het toenemende aantal spelers gaat de eindconsument waarschijnlijk helpen.
Kijk bijvoorbeeld naar de tandheelkundige industrie. Het is een van de meest volwassen, want als een consument een nieuwe kroon wil laten maken, neemt zijn tandarts gewoon een scan van de tand en stuurt de scan om binnen 2-3 dagen te worden afgedrukt. Die cyclus moet ook in andere sectoren worden bereikt. En dat is waar iedereen in 2020 naar zal blijven streven.
Zijn er volgens u nog uitdagingen die moeten worden overwonnen om de acceptatie van 3D-printen verder te versnellen?
Er zijn een aantal uitdagingen die met elkaar verweven zijn.
Op nummer één staan de kosten. De kosten zijn uiteraard gerelateerd aan de grootte van het onderdeel en het productievolume die bepalen welk type fabricagemethode moet worden gebruikt. Zelfs binnen additieven zou je bijvoorbeeld kunnen kiezen voor selectief lasersmelten of voor metaalbindmiddelstralen.
Het tweede aspect is certificering. Hoe kunnen we een onderdeel certificeren, afhankelijk van of het een dragend onderdeel is of een veiligheidskritisch onderdeel? En wat is de herhaalbaarheid?
Vandaag de dag is de uitdaging dat we de kosten niet kunnen beheersen en een lage herhaalbaarheid hebben. Als een onderdeel in een bepaalde printer wordt afgedrukt, kan men dan dezelfde specificaties bereiken als dat onderdeel door een andere printer en op een andere locatie wordt afgedrukt? Hoe groot is de kans dat de onderdelen zich precies hetzelfde gedragen? Dat resulteert in een uitdaging om de fysica die op microniveau plaatsvindt nauwkeurig te kunnen modelleren.
Dit roept de vraag op of gebruikers erop kunnen vertrouwen dat het laatste deel consistent kan worden afgedrukt op verschillende platforms en locaties.
Er is zoveel werk aan de winkel als het gaat om het vaststellen van industriebrede normen en materiaalkwalificatie. Materiaalleveranciers, printerfabrikanten, softwareleveranciers - iedereen moet samenkomen om bepaalde normen vast te stellen in termen van aanvaardbare toleranties voor licht belaste of zwaar belaste veiligheidskritieke onderdelen; in termen van voldoen aan interne porositeit en/of externe oppervlaktekwaliteit.
Als je naar de geschiedenis kijkt, of het nu gieten, smeden of plaatwerk is, door de jaren heen hebben ze allemaal een associatie gehad, zoals bijvoorbeeld de American Foundry Society. Er zijn veel organisaties die zich inzetten om iedereen bij elkaar te brengen en standaarden te creëren. Tegenwoordig explodeert de AM-markt op alle gebieden, maar uiteindelijk moet alles samenkomen om gezamenlijk normen te creëren en ervoor te zorgen dat elke speler in de sector op dezelfde lijn zit.
Ten slotte, wat brengt het komende jaar voor Altair?
We zullen doorgaan met het ontwikkelen van meer simulatieoplossingen voor onze gebruikers. Wat de additieve fabricageprocessen betreft, zullen we doorgaan met het ontwikkelen van oplossingen die technologiegebruikers helpen het proces te valideren en de onzekerheden die daarmee gepaard gaan te begrijpen.
Uiteindelijk zijn we gefocust op drie hoofdpijlers:inzicht in prestaties, een ontwerp maken door twee dingen te combineren; prestaties en het productieproces zelf. Ze moeten allemaal hand in hand gaan en we zullen doorgaan met onze missie om onze klanten te helpen de prestaties en het productieproces zo nauwkeurig mogelijk te valideren om de ontwerpen aan te sturen.
We blijven natuurkunde combineren met high-performance computing en data. We moeten ze allemaal samenvoegen, want sommige problemen kun je oplossen door de natuurkunde te begrijpen en sommige moet je oplossen met machine learning. We streven ernaar om alle technologieën die we ontwikkelen te combineren om dingen efficiënter en winstgevender te maken voor onze klanten, met als einddoel hen te helpen betere beslissingen te nemen en beter presterende producten te maken.
3d printen
- Interview met een expert:professor Neil Hopkinson, directeur 3D Printing bij Xaar
- Interview met een expert:Philip Cotton, oprichter van 3Dfilemarket.com
- Interview met een expert:Dr. Alvaro Goyanes van FabRx
- 6 belangrijke ontwerpoverwegingen voor 3D-metaalprinten
- 4 belangrijke ontwerpoverwegingen voor 3D-printen
- 10 bedrijven die geavanceerde 3D-printsimulatiesoftware aanbieden
- Interview met expert:Simon Fried, medeoprichter van Nano Dimension over de opkomst van 3D-printen voor elektronica
- Interview met experts:Brian Alexander van Solvay over de ontwikkeling van hoogwaardige polymeren voor 3D-printen
- Interview met expert:hoofdtechnoloog van ANSYS over het bereiken van succesvol 3D-printen met metaal met simulatie
- Interview met expert:AMendate over zijn geautomatiseerde topologie-optimalisatiesoftware voor 3D-printen
- Ontwerptips voor Carbon DLS™ 3D-printen