De evolutie van SLS:nieuwe technologieën, materialen en toepassingen
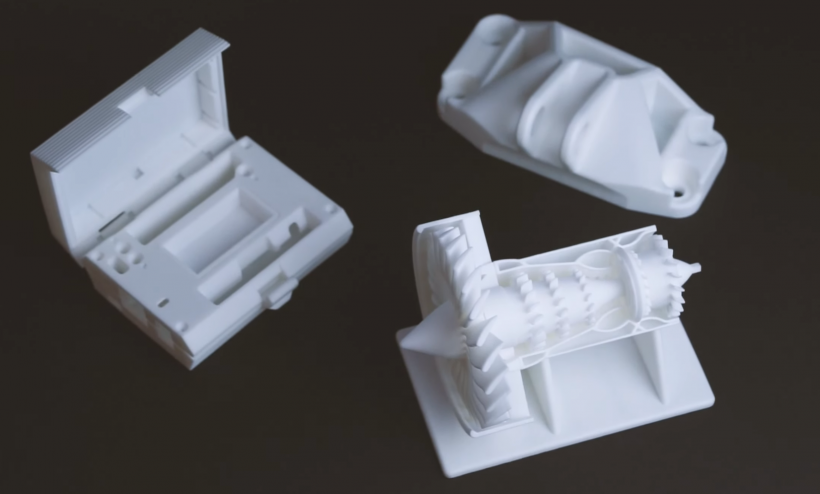
[Afbeelding tegoed:3D Hubs]
Selective Laser Sintering (SLS) is een van de meest populaire polymeer 3D-printtechnologieën voor industriële toepassingen. Sinds de opkomst, meer dan 30 jaar geleden, is SLS geleidelijk uitgegroeid tot een technologie die in staat is tot functionele prototyping en, meer recentelijk, ook tot productie.
De drijvende kracht achter deze evolutie is de voortdurende innovatie op het gebied van hardware en materialen, evenals de bereidheid van technologiegebruikers om nieuwe SLS-toepassingen te ontwikkelen.
In het artikel van vandaag zullen we de recente ontwikkelingen in SLS bekijken om meer te weten te komen over de huidige mogelijkheden en toekomstige kansen van de technologie.
Bekijk andere artikelen over de evolutie van 3D-printtechnologieën:
Metaal 3D-printen:waar zijn we vandaag?
Stereolithografie en digitale lichtverwerking:waar staan we vandaag?
Hoe desktop industrieel 3D-printen transformeert
FDM 3D-printen:waar staan we vandaag?
Alles wat u moet weten over Metal Binder Jetting (2019)
Een korte geschiedenis van SLS
Lasersinteren maakt gebruik van een krachtige laser om poedervormige materialen laag voor laag te smelten. Een van de belangrijkste voordelen van het gebruik van SLS-afdrukken is dat de ontwerpen geen ondersteunende structuur nodig hebben. Terwijl de print wordt opgebouwd, worden alle holle ruimtes automatisch gevuld met ongebruikt poeder, waardoor SLS-prints zelfdragend zijn.
Hoewel het concept van SLS-printen oorspronkelijk werd bedacht in het begin van de jaren tachtig, duurde het tot 1992 voordat de eerste industriële SLS-printer op de markt kwam:Sinterstation 2000 van DTM (later samengevoegd met 3D Systems). Dit werd in 1994 gevolgd door de EOSINT P350 van EOS.
Sindsdien kwam er een breed (en groeiend) assortiment machines op de markt, wat het begin markeerde van het tijdperk van sneller en groter printen in een industriële context.
Opmerkelijke ontwikkelingen in SLS-hardware
De evolutie van EOS' SLS-technologie
Het Duitse polymeer- en metaal 3D-printbedrijf EOS is misschien wel de grootste SLS-specialist op de markt. In 2016 beweerde het bedrijf ongeveer 3000 eenheden wereldwijd te hebben geïnstalleerd, waarvan 51 procent SLS-systemen.
Gedurende zijn 30-jarige geschiedenis heeft EOS SLS naar het niveau van een volwassen technologie, geschikt voor verschillende toepassingen, zowel in prototyping als productie.
Een van de mijlpalen op deze reis was de lancering van de FORMIGA P 100 in 2006. Het systeem zette de maatstaf voor de kwaliteit van industrieel 3D-printen in de kunststofsector, vele jaren na de introductie.
In 2012 lanceerde EOS een opvolger van de FORMIGA 100, de FORMIGA P 110, die door 3D Hubs werd uitgeroepen tot de beste lasersintermachine in de Printer Guide 2018-enquête.
Met een totale bouwgrootte van 200 × 250 × 330 mm, maakte de P 110 kosteneffectiever afdrukken van kleine volumes mogelijk en werd hij gebruikt voor middelgrote prototypebouw en onderdelen met zeer complexe geometrieën.
Snel vooruit naar 2018, de P 110 werd verbeterd tot de FORMIGA 110 Velocis. Het beschikt over een verbeterd, versneld verwarmingssysteem en hercoatingsproces, en maakt gebruik van softwarecontrole om de polymeermaterialen met een hogere snelheid voor te verwarmen met een 30-watt laserstraal.
Nu, met aanvullende technische verbeteringen en enige verfijning bereikt de Velocis een productiviteitsverhoging van 20 procent en een betere temperatuurverdeling voor het bouwgebied, wat resulteert in een meer homogene onderdeelkwaliteit.
SLS bij hoge temperaturen
Hoewel nylon het meest gebruikte materiaal in SLS blijft, wilde EOS ook de verwerking van meer geavanceerde materialen mogelijk maken, zoals PEEK, waarvoor doorgaans hoge temperaturen nodig zijn om ze te printen.
Dit resulteerde in het eerste hoge-temperatuur SLS-platform, de EOSINT P 800, onthuld in 2008. Het is in staat om polymeren te verwerken tot een temperatuur van ongeveer 385 ° C, wat de SLS-technologie heeft uitgebreid tot een nieuwe reeks thermoplasten, namelijk PEEK.
10 jaar later voegde EOS de EOS P 810 toe aan zijn 3D-printerreeks voor hoge temperaturen. Er wordt beweerd dat het nieuwe systeem 's werelds eerste lasersintersysteem voor hoge temperaturen is dat is geoptimaliseerd voor een met koolstofvezel versterkt PEKK-materiaal.
Voortdurende innovatie:FDR en LaserProFusion Technologies
De verbeteringen en innovaties van EOS op het gebied van SLS-technologie zijn aan de gang. Op Formnext van dit jaar toonde EOS bijvoorbeeld zijn Fine Detail Resolution (FDR)-polymeergebaseerde 3D-printtechnologie. Het nieuwe proces maakt gebruik van een CO-laser om delicate, maar robuuste, polymeercomponenten in 3D te printen met fijne detailresolutie-oppervlakken en een minimale wanddikte van 0,22 mm.
EOS claimt de eerste fabrikant te zijn die een CO-laseroplossing heeft ontwikkeld voor industrieel 3D-printen op poederbasis. De meeste huidige SLS-machines gebruiken één of enkele CO₂-lasers.
Het type CO-laser creëert een ultrafijne laserstraal met een focusdiameter die naar verluidt half zo groot is als de huidige SLS-technologieën. Een belangrijk gevolg van deze toegevoegde precisie zijn nieuwe belichtingsparameters die kunnen resulteren in onderdelen met extreem fijne oppervlakken.
De nieuwe technologie zou kunnen worden gebruikt om filtereenheden en vloeistofkanalen, pluggen en andere elektronische componenten in 3D te printen, evenals consumptiegoederen, zoals brillen.
Terwijl FDR-technologie is gericht op delicate componenten, is een andere – nog te commercialiseren – oplossing van EOS, LaserProFusion-technologie, ontworpen voor maximale productiviteit.
EOS gaat het LaserProFusion-systeem uitrusten met maximaal 1 miljoen diodelasers, die meer dan 5 kilowatt aan geaccumuleerd laservermogen kunnen produceren. Deze technologie is primair gericht op het voldoen aan de eisen van serieproductie en EOS stelt dat deze in veel toepassingen als alternatief voor spuitgieten kan worden gebruikt.
Sinds de lancering van de eerste SLS 3D-printer 26 jaar geleden, is EOS een van de belangrijkste drijvende krachten achter de opmerkelijke vooruitgang in SLS-technologie. Het heeft voortdurend de visie van SLS als een serieproductieoplossing nagestreefd, die uiteindelijk werkelijkheid wordt.
Farsoons vluchttechnologie
Een ander bedrijf dat een revolutie wil ontketenen in SLS-technologie is Farsoon. Om SLS nog sneller en nauwkeuriger te maken, maakt Farsoon gebruik van de kracht van een fiberlaser in zijn nieuwe Flight Technology.
Terwijl de huidige SLS-machines CO₂-lasers gebruiken, heeft de Chinese 3D-printerfabrikant de standaard CO₂-laser vervangen met een fiberlaser.
Een fiberlasersysteem is in staat om meer vermogen aan het poederbed te leveren en de energieverdeling naar het materiaal te verbeteren. Dit komt omdat een fiberlaserstraal een kleinere laservlekgrootte mogelijk maakt. Dit vertaalt zich in de hogere vermogensdichtheid, waardoor het poeder in een kortere tijd kan worden gesinterd.
Naast een fiberlaser heeft Farsoon ook een nieuw scansysteem ontwikkeld, wat resulteert in een scansnelheid van meer dan 20 m/s. Dit is ongeveer 4 keer zoveel als vergelijkbare technologieën. Bovendien maakt de toegevoegde kracht van een laser functiedetails zo klein als 0,3 mm mogelijk.
Ontworpen om de acceptatie van SLS 3D-printen voor productie in grote volumes te stimuleren, is Flight Technology zeker een stap voorwaarts in deze richting.
SLS 3D-printen met twee poeders
Terwijl EOS en andere gevestigde SLS-spelers vooral gericht zijn op lineaire innovatie, heeft de Belgische start-up Aerosint een radicale aanpak gekozen om een SLS-systeem te ontwikkelen dat met twee verschillende poeders kan printen. Hierdoor kan de machine een van de poeders gebruiken als goedkoop ondersteuningsmateriaal.
Normaal gesproken is het niet-gesmolten ondersteuningspoeder in een SLS-machine hetzelfde materiaal dat wordt gebruikt om een onderdeel te printen, en het is meestal duur. Dit zou natuurlijk geen probleem zijn als het poeder 100 procent hergebruikt zou kunnen worden, wat momenteel onmogelijk is.
Eén reden is dat in het SLS-proces polymeren worden blootgesteld aan hoge hitte gedurende lange tijdsperioden, waardoor chemische veranderingen ondergaan die hun sinterkenmerken veel minder voorspelbaar maken. Momenteel is de enige manier om dit probleem op te lossen door 'gebruikt-maar-niet-gefuseerd' poeder te mengen met ongeveer 50 procent nieuw poeder, zodat het opnieuw kan worden gebruikt.
Zoals geschat door een dienstverlener, van 500 kg poeder die het per maand koopt, '25% wordt een onderdeel, 25% is afval en 50% wordt hergebruikt voor het opfrissen van de volgende build'.
Introductie van een machine die goedkoop ondersteuningsmateriaal kan gebruiken en een tweede materiaal voor het printen van onderdelen, zou een aanzienlijke hoeveelheid geld kunnen besparen voor degenen die SLS-processen gebruiken.
De technologie van Aerosint, Selective Powder Deposition, bereikt dit door selectief poedermateriaal te deponeren vanuit een roterende trommel die over een bouwgebied beweegt. Eén vat deponeert één materiaal, dus er worden ten minste twee vaten gebruikt om multi-poederafzetting te bereiken.
De techniek van Aerosint is inherent lijn-voor-lijn en kan printsnelheden tot 200 mm/s bereiken. Deze snelheid is vergelijkbaar met de rijsnelheden van de huidige SLS-overcoater.
De rijping van deze technologie zal een zee van kansen voor fabrikanten ontsluiten, waaronder de voordelen van minder poederafval, besparingen op materiaalkosten en kortere nabewerkingstijd.
SLS 3D-printers naar een compact formaat brengen
In 2014 zag de SLS-markt een nieuwe lichting bedrijven profiteren van het verstrijken van het oorspronkelijke SLS-patent en probeerden de technologie betaalbaarder te maken.
Deze verschuiving leidde tot benchtop SLS 3D-printers, niet klein genoeg om 'desktop' te heten, maar compact genoeg om op een winkelwerkbank te passen. De opkomst van benchtop 3D-printers maakte de technologie toegankelijk voor prosumenten en kleine bedrijven die misschien niet het geld of de ruimte hebben voor een industrieel SLS-systeem.
De start-ups, zoals Sinterit, Sharebot, Sintratec en, meer recentelijk, Formlabs deed mee aan de race voor SLS 3D-printen in compacte vorm.
Sharebot was het eerste bedrijf dat een tafelmodel SLS-machine op de markt bracht met SnowWhite, die in 2016 voor het eerst naar klanten werd verzonden. In tegenstelling tot de systemen van Sintratec en Sinterit, die zijn uitgerust met diodelasers, beschikt SnowWhite over een krachtigere CO2-laser, die gewoonlijk wordt geïnstalleerd op de high-end professionele machines.
De laser en een klein volume van 100 x 100 x 100 mm bouwen een volume, dat afdrukken met slechts 300 g mogelijk maakt , maakt het SnowWhite-systeem bijzonder geschikt voor materiaalontwikkelingstoepassingen.
Een andere grote speler op dit gebied is het Poolse bedrijf Sinterit, met zijn Sinterit Lisa-systeem, dat een koploper blijft in dit groeiende marktsegment. Vanaf € 6.990 heeft Sinterit Lisa een bouwvolume van 150 x 200 x 150 mm en een minimale laagresolutie van 0,075 micron, waardoor het geschikt is voor kleine bedrijven die kennis willen maken met SLS-technologie zonder al te veel kapitaal te hoeven investeren in omvangrijke apparatuur.
Vorig jaar onthulde het bedrijf ook de Sinterit Lisa Pro, de nieuwste benchtop SLS 3D-printer.
Een potentiële belangrijke innovatie in dit segment zou de Fuse 1, een aangekondigde SLS 3D-printer kunnen zijn. door Formlabs, leider op het gebied van desktop Stereolithography, in 2017. Met een printvolume van 165 x 165 x 320 mm en een fiberlaser, kost het systeem ongeveer $ 10.000 en wordt het medio 2020 commercieel uitgebracht.
De stroom van goedkopere desktop FDM- en SLA/DLP 3D-printers aan het begin van de jaren 2010 veroorzaakte ontwrichting in de industrie en droeg tegelijkertijd aanzienlijk bij aan de groei van de AM-industrie. Betaalbare SLS begint deze reis nog maar en zou een soortgelijk pad kunnen volgen. Dit zal uiteindelijk het bereik van SLS uitbreiden naar een breder scala aan industrieën en gebruikers.
De evolutie van SLS-materialen
De eerste SLS 3D-printers die het meest werden gebruikt nylon, een populaire technische thermoplast, geprezen om zijn lichtgewicht eigenschappen, sterkte en duurzaamheid. Nylon, ook bekend als polyamide (PA), is bestand tegen schokken, chemicaliën, hitte, UV-licht, water en vuil, waardoor het ideaal is voor zowel snelle prototyping als productie.
Vandaag de dag is nylon nog steeds de meest populaire SLS-materiaal. De vooruitgang in technologie en 3D-printmaterialen maakte echter de opkomst mogelijk van op nylon gebaseerde composieten - materialen gemengd met koolstofvezel, glasvezel en aluminium om de mechanische en thermische eigenschappen van polyamide nog verder te verbeteren.
Naast nylon kunnen de huidige SLS 3D-printers ook PEEK, PEKK, flexibele TPU's, vlamvertragende polymeren en antistatische polymeren verwerken. De mogelijkheid om hoogwaardige materialen te verwerken is nauw verbonden met technologische innovatie. Net als in het EOS-voorbeeld moest het bedrijf eerst een 3D-printer voor hoge temperaturen maken voordat het materialen zoals PEEK kon printen.
Nieuwe SLS-materialen
Het tempo van de ontwikkeling van nieuwe materialen voor SLS is ook bemoedigend.
Het Italiaanse 3D-printbedrijf CRP Technology is misschien wel een van de belangrijkste onafhankelijke ontwikkelaars van SLS-materialen, beroemd om zijn merk Windform . Het bedrijf biedt een reeks op nylon gebaseerde composieten en rubberachtige plastic poeders.
De meest recente toevoegingen aan de Windform-lijn zijn Windform FR1 en Windform FR2 - vlamvertragende composieten, geschikt voor vliegtuigtoepassingen (bijvoorbeeld interieuronderdelen, cockpitcomponenten, luchtkanalen en luchtuitlaatkleppen); transportonderdelen (voertuiginterieurs, behuizingen en behuizingen) en consumptiegoederen en elektronica (verlichting en apparaten).
Chemiebedrijf DSM is onlangs ook naar voren gestapt om materialen voor SLS te ontwikkelen. Dit resulteerde in een vorig jaar uitgebracht polybutyleentereftalaat (PBT) poeder. Interessant is dat DSM specificeert dat het materiaal eigenlijk het eerste PBT-poeder is dat commercieel beschikbaar wordt gemaakt voor SLS 3D-printen. PBT is een thermoplastisch technisch polymeer met toepassingen in de elektronica-industrie, dankzij de isolerende eigenschappen.
Bovendien biedt Forward AM, een dochteronderneming van een chemiereus, BASF, een reeks SLS-materialen aan onder de Ultrasint merk. Vlambestendig Ultrasint Polyamide PA6 Zwart FR-materiaal is het nieuwste in dit assortiment en heeft een hoge stijfheid en goede thermische stabiliteit. Volgens Forward AM wordt het al gebruikt om nieuwe componenten voor voertuigen te produceren die voldoen aan de vereisten voor voertuigbrandbeveiliging.
Zowel BASF als DSM hebben onlangs SLS 3D-printers overgenomen van de Franse fabrikant Prodways. Met een verhoogde SLS-capaciteit kunnen de twee chemische bedrijven hun ontwikkeling van geavanceerde materialen voor SLS 3D-printen versnellen.
Nabewerking in SLS
Hoewel de SLS-technologie de noodzaak voor het ontwerp en de verwijdering van ondersteuningsstructuren elimineert, zijn er ook uitdagingen op het gebied van nabewerking. De grootste daarvan is de noodzaak om het overtollige poeder te verwijderen dat op het oppervlak van een onderdeel is achtergebleven en soms in een onderdeel vastzit.
Momenteel worden deze uitdagingen aangepakt door handmatig wassen en reinigen, en traditionele technieken, zoals parelstralen en tuimelen.
Deze methoden vereisen echter veel handmatige tussenkomst, waardoor het risico op beschadiging van kwetsbare geometrieën en het produceren van inconsistente definitieve onderdelen toeneemt.
Als het gaat om oppervlakteafwerking, worden SLS-onderdelen vaak gladgemaakt door te schuren en met behulp van semi-automatische apparatuur die doorgaans niet is ontworpen voor 3D-printen. Deze benaderingen zijn niet praktisch om de mogelijkheden van een SLS-printer volledig te benutten en op te schalen naar grotere productievolumes.
Gelukkig ontwikkelen verschillende spelers in de sector geautomatiseerde oplossingen voor de nabewerking van SLS-onderdelen.
PostProcess Technologies, bijvoorbeeld, biedt oplossingen in poedervorm door zijn Thermal Atomized Fusillade (TAF)-technologie, waarbij twee loodrechte eenassige straalstromen, bestaande uit perslucht, detergent en zwevende vaste stoffen, zorgen voor een gerichte explosie sequenties, terwijl 360° deelrotatie wordt gebruikt voor maximale blootstelling aan het oppervlak.
Het Britse bedrijf AMT gaat later dit jaar een geautomatiseerde oplossing voor het verwijderen van poeder lanceren.
Uiteindelijk zal het overschakelen van handmatige naar geautomatiseerde depowdering de SLS 3D-printworkflow aanzienlijk helpen optimaliseren, niet alleen door handmatige arbeidstijd te verminderen, maar ook door bedrijven in staat te stellen hun SLS-productie efficiënter te schalen.
SLS-toepassingen:een groeiend gebruik in de productie
Hoewel SLS-technologie nog steeds wordt gebruikt bij het maken van prototypen, wordt het ook steeds populairder voor het testen van functionele onderdelen en voor productietoepassingen.
Lucht- en ruimtevaart
De lucht- en ruimtevaartindustrie gebruikt bijvoorbeeld SLS om interieuronderdelen van vliegtuigen te maken. Een voorbeeld hiervan is Emirates, de grootste luchtvaartmaatschappij in de VAE. De luchtvaartmaatschappij gebruikt 3D-printen om onderdelen van de vliegtuigcabine te produceren, waaronder videobewakingsschermen en ventilatieroosters. Deze laatste zijn al gecertificeerd en geïnstalleerd voor proeven aan boord van Emirates-vliegtuigen.
Emirates werkt samen met 3D Systems om de videobewakingsschermen te produceren, met behulp van SLS-technologie en het DuraForm ProX FR1200 Nylon-materiaal van 3D Systems, dat voldoet aan de door de lucht- en ruimtevaartindustrie vereiste vlamvertragende drempels voor interieuronderdelen.
Consumentengoederen
In de consumptiegoederenindustrie pioniert Chanel met het gebruik van SLS 3D-printen voor mascaraborstels. Het merk print nu miljoenen mascaraborstels in 3D, in samenwerking met de Franse 3D-printserviceprovider Erpro Group.
Met behulp van SLS-technologie is het ontwerp van het borsteltje geoptimaliseerd. Zo verbetert de ruwe, korrelige textuur, bereikt met SLS-technologie, de hechting van de mascara aan de wimpers.
In Naast schoonheidsproducten wordt SLS steeds vaker gebruikt in de medische sector en in de schoenensector om op maat gemaakte inlegzolen en sandalen te produceren.
Motorsport
In de autosport kan de technologie raceteams helpen auto-ontwerpen te innoveren en sneller te testen dan met traditionele technologieën zou zijn toegestaan.
Alfa Romeo's Sauber Formula One (F1)-team is een goed voorbeeld van hoe een autosportbedrijf SLS 3D-printen kan benutten.
SLS wordt voornamelijk gebruikt voor de aerodynamische ontwikkeling van de Alfa Romeo F1-auto in de windtunnel, evenals voor een breed scala aan lamineermallen, kernen en complexe serieonderdelen.
Tijdens de productie gebruiken ze een materiaal op poederbasis, ontwikkeld door Sauber Engineering, dat wordt gebruikt wanneer bijzonder lichte en stijve componenten nodig zijn, van F1-remventilatie en carrosseriecomponenten voor preproductievoertuigen en prototypes , tot een breed scala aan kant-en-klare constructie-elementen.
The sky is the limit voor SLS-toepassingen. Gezien de recente ontwikkelingen in SLS-materialen en -technologie, klinkt deze uitspraak bijzonder waar.
SLS:een van de beste keuzes voor 3D-printen met polymeren
De SLS 3D-printmarkt is continu in ontwikkeling. De technologie wordt gedemocratiseerd met de introductie van compacte en betaalbare benchtop-systemen. Ondertussen leggen de fabrikanten van industriële SLS-apparatuur meer nadruk op oplossingen die helpen om SLS als productietool te vestigen.
Als gevolg hiervan neemt het aantal projecten, gerealiseerd met SLS-technologie, gestaag toe.
Bewijs hiervan is het feit dat meer dan 75 procent van de 3D-printprojecten in 2019 SLS-methoden gebruikten, volgens het rapport van Sculpteo. Een afhaalpunt hierbij is dat SLS wordt beschouwd als een van de beste keuzes voor polymeer 3D-printen. Wij geloven dat dit in de nabije en verre toekomst zo zal blijven.
3d printen
- 4 Gebruik van Hafnium | De toepassingen van Hafnium- en Hafniumlegeringen
- 13 soorten vuurvaste materialen en hun toepassingen
- De twee fundamentele soorten SLS-materiaal begrijpen
- De synergie van cellulair IoT en Bluetooth LE
- K 2019 Slideshow:New Resins, New Applications in Materials
- Ontwerpen van draadloze IoT-toepassingen voor de opkomende nieuwe netwerken – LTE en NB-IoT
- 5G, IoT en de nieuwe supply-chain-uitdagingen
- De basis van kunststofextrusie:proces, materialen, toepassingen
- De evolutie van medische materialen
- Freesspil en de opmerkelijke toepassingen
- 9 soorten draadsnijgereedschappen en de toepassingen