Applicatie Spotlight:3D-geprinte beugels
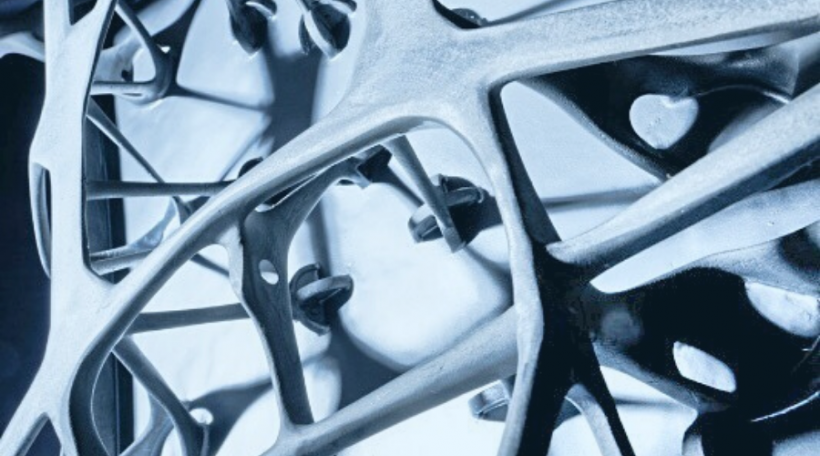
Beugels, hoewel vrij eenvoudige onderdelen, zijn een populaire keuze voor 3D-printen. Ten eerste maakt 3D-printen beugeloptimalisatie mogelijk, waardoor de prestaties van een onderdeel en een structuur waarin een beugel wordt gebruikt, worden verbeterd.
In de Application Spotlight van vandaag onderzoeken we de belangrijkste voordelen van het gebruik van 3D-printen voor beugels, en duiken we in enkele opwindende toepassingen in de lucht- en ruimtevaart- en auto-industrie.
Bekijk de andere toepassingen die in deze serie worden behandeld:
3D-printen voor warmtewisselaars
3D-printen voor lagers
3D-printen voor fietsproductie
3D-printen voor productie van digitale tandheelkunde en heldere uitlijners
3D-printen voor medische implantaten
3D-geprinte raketten en de toekomst van de fabricage van ruimtevaartuigen
3D-printen voor de productie van schoenen
3D-printen voor elektronische componenten
3D-printen in de spoorindustrie
3D-geprinte brillen
3D-printen voor productie van eindonderdelen
3D-printen voor turbineonderdelen
Hoe 3D-printen zorgt voor beter presterende hydraulische componenten
Hoe 3D-printen innovatie in de kernenergie-industrie ondersteunt
Wat is een beugel?
Een beugel is een bevestigingsmiddel, ontworpen om twee loodrechte delen bij elkaar te houden in een samenstel en om de hoek te versterken.
Beugels houden constructies overal om ons heen bij elkaar (denk aan gebouwen, vliegtuigen en auto's), en bepalen grotendeels de sterkte, veerkracht en integriteit van die constructies.
Waarom 3D-printen gebruiken voor beugels?
Beugels zijn vrij eenvoudige componenten om op traditionele wijze te vervaardigen. Met de komst van 3D-printen kunnen ingenieurs nu echter nieuwe manieren verkennen om beugelontwerpen te optimaliseren.
Dit is grotendeels mogelijk dankzij de mogelijkheid van 3D-printen om complexe geometrische vormen te creëren die met traditionele productiemiddelen onmogelijk of kostbaar en tijdrovend zouden zijn.
De belangrijkste voordelen van 3D-geprinte beugels zijn:
Snellere productie
De productie van complexe metalen beugels vereist doorgaans meerdere machineconfiguraties en kan vele uren in beslag nemen. 3D-printen kan daarentegen een snellere oplossing bieden. Een reden is dat het mogelijk is om meerdere onderdelen in een 3D-printer te nesten, waardoor de productie van meerdere beugels tegelijkertijd in dezelfde machine mogelijk is.
Voor een beugel die eerder werd gespuitgiet, is de tijdwinst nog groter omdat 3D-printen de doorlooptijd van het produceren van een matrijsgereedschap elimineert.
Geëlimineerde montage
Sommige beugels zijn gemaakt van meerdere stukken, wat de tijd die nodig is om de beugel te monteren kan verlengen. 3D-printen maakt het mogelijk om een beugel als één geconsolideerd onderdeel te ontwerpen en te produceren, waardoor er minder arbeid en tijd nodig is om de beugel in elkaar te zetten. Het 3D-printen van een beugel als een enkel onderdeel zal waarschijnlijk ook de algehele sterkte van een onderdeel vergroten.
In één voorbeeld gebruikte Philips 3D-printen om een opnieuw ontworpen beugel te produceren die lampen op hun plaats houdt aan de productielijn. Het onderdeel ging vaak kapot, waarbij er elke week een of twee kapot gingen, grotendeels als gevolg van herhaalde blootstelling aan hoge temperaturen, gecombineerd met een structuur met laslijnen van een vierdelige beugel.
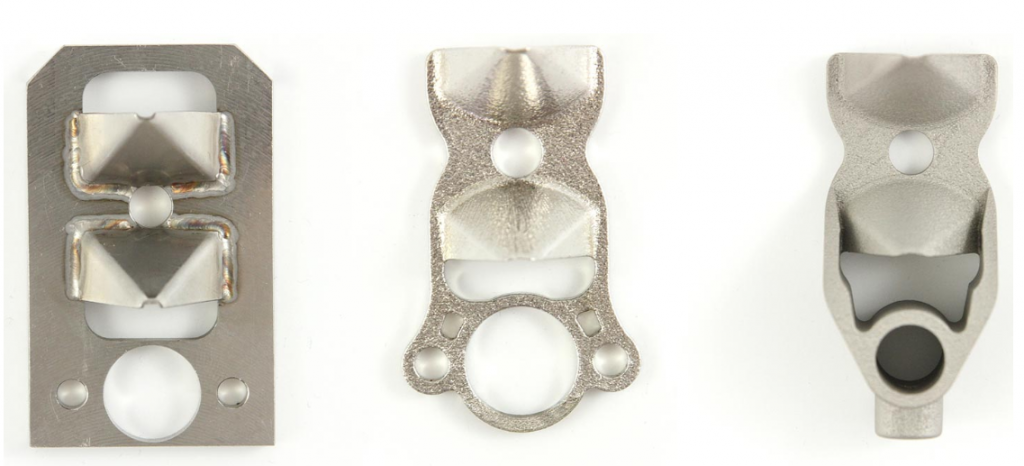
Philips was in staat om een metalen onderdeel opnieuw te ontwerpen als een beugel met één structuur, waardoor de tijdrovende montage van onderdelen werd verminderd en de drukpunten van de laslijn volledig werden verwijderd. Tijdens de eerste drie maanden van gebruik is de opnieuw ontworpen beugel niet één keer gebroken.
Minder materiaalverspilling
Het proces van het 3D printen van een beugel omdat één onderdeel vaak minder materiaal gebruikt, waardoor een lichtere beugel ontstaat.
Die gewichtsbesparing vertaalt zich in minder materiaalgebruik en kan in sommige gevallen de prestaties van een systeem verbeteren waarbij een beugel wordt gebruikt.
Neem als voorbeeld de GEnx-engines van GE. De motoren gebruikten beugels gemaakt met traditionele methoden zoals frezen. Het betekent dat de onderdelen uit een groot blok metaal zijn gefreesd, waarvan meer dan de helft als afval belandt.
Het team dat aan de beugels werkte, realiseerde zich dat ze door het 3D-printen van het onderdeel in staat zouden zijn om maar liefst 90 procent van het afval te verminderen.
Het team heeft ook kleine ontwerpverbeteringen doorgevoerd die het gewicht van de beugel met 10 procent verminderden. Volgens het team ‘als het om vliegen gaat, telt elke ons’. Het betekent dat het verminderen van het gewicht van het onderdeel een impact kan hebben op het brandstofverbruik van het vliegtuig, waardoor het lager wordt en dus tot een efficiënter vliegtuig kan leiden.
In een ander voorbeeld hebben Ford-ingenieurs onlangs een plastic elektrische parkeerrembeugel voor de Ford Mustang Shelby GT500 in 3D geprint die 60 procent lichter is dan een eerder gestempelde stalen versie.
De mogelijkheid om metaal te vervangen door plastic of composiet
Voor sommige toepassingen kan 3D-printen worden gebruikt om beugels van plastic te maken in plaats van metaal. Plastic beugels zijn wellicht beter geschikt voor toepassingen zoals consumentenproducten met een beperkte levensduur of producten met gevoelige elektronische componenten waar metalen beugels niet werken.
Een voorbeeld komt van een fabrikant van communicatieapparatuur, Boyce Technologieën. Het bedrijf gebruikte 3D-printen om plastic onderdelen te bouwen voor de NYC Transit-totems. Elk van deze systemen heeft een groene acrylkap aan de bovenkant met een LED-strip voor verlichting en een gevoelig antenne-instrument.
Om verstoring van het antennesignaal te voorkomen, mag er geen metalen materiaal ervoor. Dat betekent dat het bedrijf de beugels voor de ledstrip en de behuizing voor de antenne van kunststof moest maken. Het Boyce-team had slechts een korte tijd voor ontwerp, engineering en productie, waardoor 3D-printen een geschikte oplossing was.
Met behulp van het BigRep Studio-systeem kon Boyce een prototype maken van gebogen montagebeugels voor de LED-lampen om de kap te verlichten en vervolgens direct over te gaan tot de productie van deze onderdelen op hetzelfde platform.
Door deze beugels door 3D te printen, konden ze snel en kosteneffectiever worden gemaakt dan spuitgieten of machinale bewerking, terwijl ze ook voldeden aan de eis van geen metaal boven de antenne.
Meer voorbeelden van 3D-geprinte beugels
Lucht- en ruimtevaart
3D-geprinte titanium beugels voor Boeing 787
3D-geprinte ruimtevaartbeugels, gemaakt van titaniumlegeringen, worden steeds gebruikelijker in het ontwerp van vliegtuigen. Een voorbeeld is een beugel voor een toegangsdeurvergrendeling voor de Boeing 787, geïnstalleerd door Spirit AeroSystems.
De deurvergrendeling, die eerder machinaal werd bewerkt, is nu 3D-geprint door Norsk Titanium, met behulp van zijn gepatenteerde Rapid Plasma Deposition (RPD)-technologie. De naam beschrijft het proces:een plasmaboog zorgt voor gecontroleerde afzetting van titanium met snelle opbouwsnelheden. De technologie is naar verluidt 50-100 keer sneller dan op poeder gebaseerde systemen en gebruikt 25-50 procent minder titanium dan smeedprocessen.
De belangrijkste reden om over te stappen op titanium 3D-printen is de mogelijkheid om de productie te verlagen kosten. Titanium is duur en bij het machinaal bewerken van een onderdeel uit een blok titanium gaat veel van dit dure materiaal verloren. Het tweede probleem is een grote hoeveelheid machinetijd en kosten voor snijgereedschap die nodig zijn om het metaal weg te machinaal bewerken, waardoor de productiekosten stijgen.
Door een bracket in 3D te printen, kan Spirit deze kosten aanzienlijk verlagen, terwijl de time-to-market voor nieuwe onderdelen met ten minste 60 procent wordt verkort.
Liebherr-Aerospace 3D print brackets voor Airbus
In een ander voorbeeld in de lucht- en ruimtevaartindustrie is Liebherr-Aerospace begonnen met het 3D-printen van neuslandingsgestelbeugels voor de Airbus A350 XWB.
Deze beugels zijn de allereerste gekwalificeerde 3D-geprinte titanium onderdelen geïntroduceerd in het Airbus-systeem.
In tegenstelling tot Spirit AeroSystems was Liebherr in staat om een onderdeel opnieuw te ontwerpen om een gewichtsreductie van 29 procent te bereiken. Het gebruik van 3D-printen hielp ook om de stijfheid van het onderdeel met 100 procent te verhogen.
In 2019 bereikte Liebherr-Aerospace een belangrijke mijlpaal:het Duitse Federale Luchtvaartbureau gaf het bedrijf groen licht om componenten te produceren met AM. Sindsdien print Liebherr titanium seriële onderdelen, inclusief brackets, in 3D.
Automobiel
Een dakbeugel, geoptimaliseerd en in 3D geprint door BMW
In 2018 bracht BMW zijn iconische i8 Roadster-auto uit, met een bekroonde 3D-geprinte metalen daksteun.
De daksteun, een klein onderdeel dat helpt bij het opvouwen en het uitklappen van de bovenkant van de auto, vereiste een nieuw ontwerp om de prestaties van het dakvouwmechanisme te maximaliseren. Om dit doel te bereiken, combineerden de ingenieurs van BMW 3D-printen met software voor topologie-optimalisatie.
Door de software te gebruiken, konden ingenieurs parameters invoeren zoals het gewicht, de grootte van het onderdeel en de belasting die het zal dragen. De software genereerde vervolgens een ontwerp dat de materiaalverdeling van het onderdeel optimaliseerde.
Het ontwerp van het engineeringteam was onmogelijk te gieten. Het team ontdekte dat de enige manier om dit ontwerp mogelijk te maken, was door middel van 3D-printen van metaal.
Dankzij Selective Laser Melting (SLM)-technologie hebben ingenieurs een metalen dakbeugel gemaakt die 10 keer stijver en 44 procent lichter is dan het conventionele alternatief.
De lichtgewicht beugels van Bugatti
De voertuigen van Bugatti zijn ook voorzien van een aantal 3D-geprinte beugels. Een daarvan is een titanium spoilerbeugel die is vervaardigd in samenwerking met Fraunhofer IAPT. Deze spoiler zou het aerodynamische ontwerp van Bugatti-voertuigen verbeteren.
Een andere partner in het spoilerbeugelproject was Siemens, die hielp bij het optimaliseren van de beugel voor productie. Uiteindelijk vertoonde het laatste onderdeel een treksterkte van 1250 MPa, een materiaaldichtheid van meer dan 99,7 procent en een gewichtsvermindering van 53 procent.
3D-printen is ook gebruikt om een kleine motorsteun met geïntegreerde waterkoeling voor de Bugatti Chiron supercar. Het onderdeel dient als een actief hitteschild, waardoor de overgedragen warmte van de motor aanzienlijk wordt verminderd. Het innovatieve onderdeel, geprint in AlSi10Mg op een SLM280 Twin 3D-printer door SLM Solutions, is geïnstalleerd in alle serievoertuigen sinds de release van de eerste Bugatti Chiron.
3D-geprinte beugels:kleine componenten met een enorme kans
Beugels zijn kleine en nogal alledaagse onderdelen, die in het verleden moeilijk te optimaliseren waren, toen ingenieurs werden beperkt door traditionele productiemethoden. Tegenwoordig kunnen ingenieurs geoptimaliseerde beugels ontwerpen en deze ontwerpen tot leven brengen met behulp van 3D-printen.
Dankzij de technologie kunnen beugels lichter, maar toch steviger en duurzamer worden gemaakt. De bovenstaande voorbeelden laten ook zien dat door gebruik te maken van 3D-printen, de levensduur van het onderdeel en de algehele prestaties kunnen worden verbeterd.
Het is duidelijk dat we nog ver verwijderd zijn van massa-3D-geprinte haakjes. Dat gezegd hebbende, zullen gespecialiseerde toepassingen, zoals vliegtuigbeugels en beugels die in kleine volumes worden geproduceerd, een goede niche blijven voor de toekomstige technologie.
3d printen
- 3D-geprinte kunststof onderdelen lassen en lijmen
- Polyjet 3D-printen verkennen
- Wat is bioprinten?
- Applicatie Spotlight:3D-printen voor medische implantaten
- Applicatie Spotlight:3D-printen voor digitale tandheelkunde &Clear Aligner-productie
- Applicatie Spotlight:3D-printen voor fietsproductie
- Applicatie Spotlight:3D-printen voor lagers
- Applicatie Spotlight:3D-printen voor warmtewisselaars
- Applicatie Spotlight:3D-printen in de spoorwegindustrie
- COVID-19 heeft 3D-printen in de schijnwerpers geduwd
- Toepassing van 3D-printen in de auto-industrie