Interview met expert:Arevo mede-oprichter Wiener Mondesir over de productie van 's werelds eerste 3D-geprinte carbon fietsframe

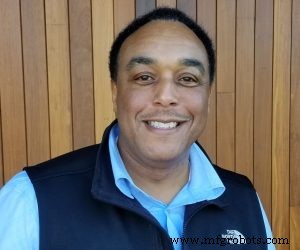
Het in Silicon Valley gevestigde bedrijf Arevo haalde in 2018 de krantenkoppen na de onthulling van wat het 's werelds eerste 3D-geprinte fietsframe van koolstofvezel noemde. De use case demonstreerde de unieke mogelijkheden van Arevo's gepatenteerde composiet 3D-printtechnologie, die robotica en software combineert om lichtgewicht, op maat gemaakte composietonderdelen te produceren.
Sindsdien werkt Arevo samen met fietsfabrikant Franco Bicycles om 3D-geprinte unibodyframes van koolstofvezel te leveren voor een nieuw merk eBikes.
Deze week praten we graag met Wiener Mondesir, medeoprichter en Chief Technology Officer van Arevo, over Arevo's gepatenteerde technologie, de voordelen van composiet 3D-printen en wat de toekomst in petto heeft voor composietproductie.
Kun je ons iets over Arevo vertellen?
Bij Arevo streven we ernaar om de fabricage van composietonderdelen op grote schaal mogelijk te maken. Dit doen we met een samenvloeiing van robotica, materialen en software.
Als je kijkt naar de composietindustrie, biedt de fabricage van composietonderdelen een zeer grote kans. Koolstofvezel kan sterker zijn dan sommige metalen en is licht van gewicht, dus het heeft een brede aantrekkingskracht in veel industrieën.
Maar om een aantal redenen is de acceptatie van composietproductie verstikt, dus de kans wordt niet benut. Een reden hiervoor is vanwege inefficiënte productieprocessen.
Composietproductie is momenteel erg arbeids-, hulpbronnen- en kapitaalintensief, wat betekent dat het niet echt kan worden opgeschaald naar grote volumes. De industrieën die echt hebben kunnen profiteren van composietproductie, waren diegene die de businesscase konden betalen, zoals de lucht- en ruimtevaart en de zeer hoogwaardige auto-industrie.
Bovendien zijn er lange ontwerpcycli vanwege gebrekkige software en inefficiënte simulatie. Een andere vaak over het hoofd geziene reden is het gebrek aan begrip van composieten in andere industrieën.
Arevo pakt al deze problemen aan. We herdenken composietproductie door gebruik te maken van wat we de digitalisering van composieten noemen.
We hebben ervoor gekozen om dit probleem op te lossen door software te ontwikkelen die de kenniskloof opvult.
Je begint met een 3D-model en onze software doet de analyse, komt met de optimale eindoriëntatie, de juiste hoeveelheid materiaal en maakt instructies om het onderdeel te fabriceren met behulp van onze fabricagetechnologie.
Laten we als voorbeeld een spinnenweb nemen. Als je naar een spinnenweb kijkt, is het een 3D-structuur met de juiste hoeveelheid materiaal voor zijn doel.
De vezel, of de zijde in het geval van het spinnenweb, gebruikt alleen de juiste hoeveelheid materiaal en is perfect geplaatst waar het moet zijn. Daar putten we inspiratie uit bij het bedenken van een geoptimaliseerde manier om composietdelen in 3D te printen.
Dus dat is onze missie als bedrijf:composietproductie op grote schaal mogelijk maken.
Wat zijn de voordelen van composiet 3D-printen?
Koolstofvezelcomposieten bieden een geweldige sterkte-gewichtsverhouding, dus je krijgt een echt sterk maar lichtgewicht materiaal.
Als je kijkt naar de trend in 3D-printen, gebruiken veel verschillende technieken roosterstructuren voor lichtgewicht metaal, dat van nature dicht en zwaar is.
Maar als je vanaf het begin begint met een lichtgewicht, sterk materiaal zoals koolstofvezel, bereik je veel sneller het eindresultaat. Dus composieten zijn veel beter geschikt voor bepaalde toepassingen dan zelfs producten met een metalen roosterstructuur, die er geweldig uitzien maar niet per se het doel dienen.
De complicatie met koolstofvezel is dat het anisotroop is, wat betekent dat het sterk is in één richting. Dat maakt het een beetje moeilijker om mee om te gaan zonder gespecialiseerde tools.
Bij Arevo hebben we de toolset voor ontwerpers ontwikkeld, dus je hoeft geen doctoraat te hebben om te produceren met koolstofvezelcomposieten. Onze software zorgt daarvoor.
Je 3D-geprinte fietsframe van koolstofvezel kreeg veel publiciteit toen het werd onthuld. Wat was het proces van het maken van het fietsframe, van ontwerp tot productie?
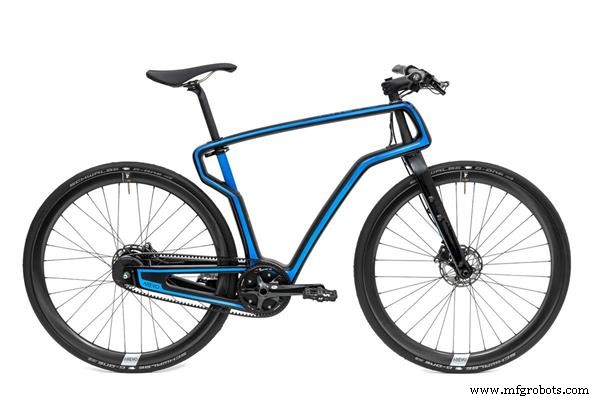
Die specifieke toepassing begon als een manier om te laten zien wat er mogelijk is met de technologie.
Een fietsframe is zeer toegankelijk, maar heeft een zeer complexe vorm en is een grote constructie die belasting, torsie en het vermogen om gewicht te dragen vereist. Het was dus de perfecte toepassing om onze technologie te demonstreren.
Als je een stap terug doet en kijkt naar traditionele composietfietsen van vandaag, doorlopen ze een ontwerp, prototype-iteratie en dan helemaal tot productie. Dat proces duurt bijna een jaar.
Bovendien worden traditionele composietfietsen vervaardigd volgens een zeer handmatig proces. Frames worden aan elkaar gelijmd van 20 tot 30 delen en maar liefst 40 mensen raken elk frame aan. Het is een zeer arbeidsintensief proces en je krijgt een zeer kostbaar product dat niet per se schaalbaar is.
De ontwerpen lijken ook erg op elkaar, dus je kunt niet veel maatwerk krijgen.
Met onze technologie hebben we dit proces verkort van bijna een jaar naar slechts enkele dagen. De software van Arevo neemt een CAD-ontwerp en maakt een isotroop generatief ontwerp op het frame dat een ontwerper bedenkt. Het optimaliseert ook de oriëntatie en doet een voorspellende analyse.
De volgende stap vindt plaats in onze productiefaciliteit. We hebben een productiefaciliteit gebouwd in Californië die op aanvraag aangepaste fietsframes kan produceren met behulp van onze robotica en depositietechnologie.
Toen we de fiets lanceerden, werden we benaderd door alle grote fietsfabrikanten omdat ze geïnteresseerd waren in de ontwerpvrijheid die de technologie bood.
Als je kijkt naar het ontwerp van het Arevo-fietsframe, dan wijkt het eigenlijk af van het conventionele fietsontwerp. Hij heeft bijvoorbeeld geen staande achtervork en ziet er heel anders uit dan een traditionele fiets.
De fiets van Arevo is een unibody-fiets gemaakt met zeer sterke koolstofvezels die in de optimale oriëntatie in de 3D-ruimte zijn georiënteerd. We zijn in staat om het ontwerp te realiseren in een unibody-structuur die het zeer solide en lichtgewicht maakt.
We kunnen de daadwerkelijke rit van de fiets afstemmen met behulp van softwaretools. We kunnen de stijfheid in bepaalde delen van de fiets afstemmen en op aanvraag een nog springerige rit mogelijk maken. Met traditionele fietsen probeer je eigenlijk altijd hetzelfde frame steeds weer opnieuw te maken.
Een 3D-geprint frame daarentegen opent een nieuw bedrijfsmodel voor een industrie die gewend is aan het zeer lange proces om een nieuwe fiets op de markt te brengen. Tegenwoordig worden er ongeveer een miljoen composietframes per jaar gemaakt. En nu kunt u met onze technologie zeer aangepaste frames op aanvraag introduceren.
Ons doel is om door te gaan met het maken van nieuwe toepassingen die van deze mogelijkheid profiteren.
Is de aangepaste benadering van productie een schaalbaar bedrijfsmodel?
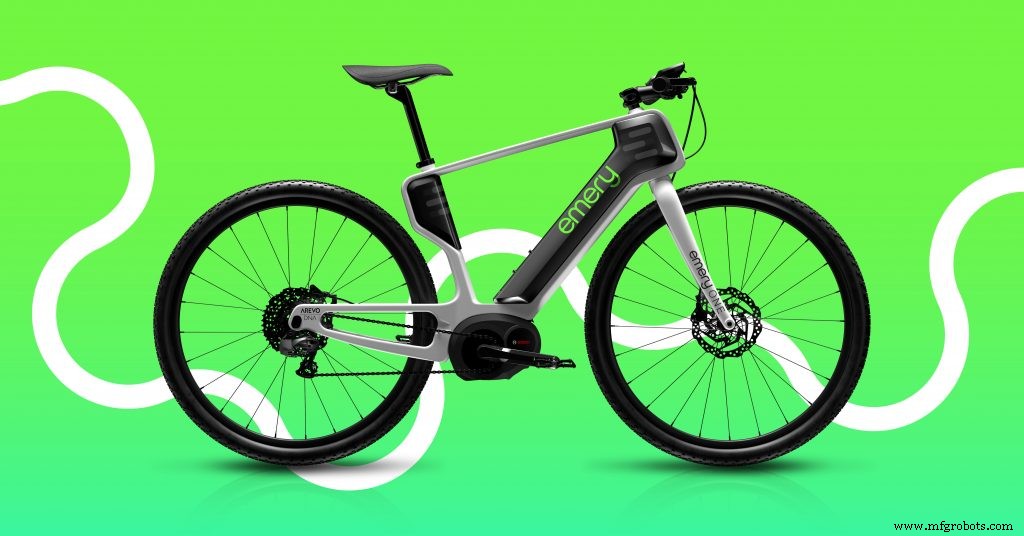
Er zit veel waarde in maatwerk als het om fietsen gaat. Ieder mens is uniek. Je wordt vermoeider als je niet op een fiets rijdt die is ontworpen, afgesteld of aangepast voor jouw frame. Een fiets is dus eigenlijk een goed voertuig om de waarde van maatwerk aan te tonen.
Er is een hele trend rond micro-mobiliteit en het kunnen rondlopen met een zeer handig voertuig. De fiets vertegenwoordigt dat. In veel verschillende landen is het een dominante vorm van transport.
Als je maatwerk voor vorm en functie nodig hebt, kun je dit niet op een massamarkt doen. Maar met onze technologie kan een consument het frame ontwerpen en onze software kan garanderen dat het frame dat hij heeft ontworpen structureel gezond is.
Dan kunnen ze dat naar onze 3D-printcellen sturen om die fiets op aanvraag te maken. Het proces van concept tot productie is dus sterk vereenvoudigd.
Welke andere toepassingen ziet u met uw technologie?
Vandaag zijn we gefocust op de fiets- en mobiliteitstoepassingen. Dit zijn toepassingen die kunnen profiteren van de waardepropositie die we bieden, namelijk een zeer lichtgewicht, hoge sterkte-gewichtsverhouding en op maat gemaakte producten.
Als je naar verschillende bedrijfstakken kijkt, is het erg belangrijk om de prestaties te verbeteren in de sportsector, maar ook in de automobiel-, energie- en ruimtevaartindustrie.
We hebben een heleboel verschillende toepassingen waaraan we werken waar lichtgewicht, hoge prestaties en hoge mate van maatwerk vereist zijn. En dat zijn de belangrijkste gebieden waar onze technologie kan worden gebruikt.
Hoe past robotica in uw technologie?
Als je naar 3D-printen kijkt, is het grootste deel van 3D-printen gebaseerd op lagen en worden de lagen afgezet in de X- en Y-vlakken. Als je kijkt naar de eigenschappen van onderdelen die met dat proces zijn gemaakt, hebben ze de neiging om in de Z-richting te lijden.
We gebruiken een volledig gelede robot met zes assen om onze koolstofvezel in de X-, Y- en Z-richtingen te deponeren. We hebben het probleem met de Z-sterkte geëlimineerd dat andere op lagen gebaseerde technologieën plaagt, omdat we in de Z-richting kunnen gaan liggen. Dat is een van de unieke mogelijkheden van onze depositietechnologie. Robotica speelt daar een grote rol in.
Het tweede aspect is de schaal van de onderdelen die kunnen worden afgedrukt. Tegenwoordig zijn de meeste systemen gedegradeerd tot een bepaalde build-envelop, wat betekent dat je alleen onderdelen van een bepaalde grootte kunt maken. Als u een bepaalde maat overschrijdt, moet het onderdeel in subassemblages worden gesneden om een grotere structuur te maken.
Onze robots bieden oneindige mogelijkheden voor het bouwen van enveloppen, omdat we onze robots op het portaal kunnen plaatsen om ruimtevaartonderdelen te maken. Tegelijkertijd kan dezelfde robot een fiets maken. Het bereik van onze robots is een volume van vier meter hoog. In wezen is het zeer schaalbaar in termen van het geven van die grote bedrukte envelop.
Hoe zou u de huidige staat van de markt voor composiet 3D-printen omschrijven? Hoe geavanceerd is de technologie?
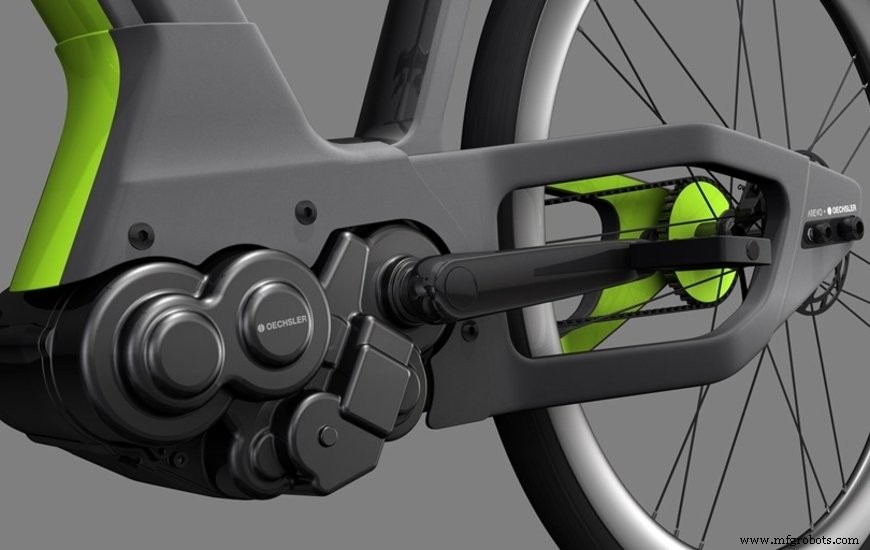
De composietindustrie doet al geruime tijd aan additieven. Alleen is de complexiteit van de geometrieën zeer beperkt gebleven tot wat je op een mal zou kunnen passen, zoals onderdelen met een zeer kleine kromming. Daarnaast worden de lagen veelal handmatig gelegd, waardoor een onderdeel vrij beperkt in complexiteit is.
Composiet 3D-printen bestaat dus al een tijdje. Maar nu maken dingen als geautomatiseerde robotica of mechatronica-systemen, die de plaatsing van de vezel automatiseren, complexere geometrieën mogelijk.
Er zijn veel bedrijven die de automatisering van composietproductie op een andere manier benaderen, van verschillende soorten harssystemen tot verschillende gebruiksscenario's.
En dat is erg nuttig.
Over het algemeen denk ik dat de sector voor composiet 3D-printen gezond is, met Arevo aan de leiding.
Wat zijn enkele van de uitdagingen waarmee de industrie wordt geconfronteerd, of het nu gaat om 3D-printen in het algemeen of om composiet 3D-printen in het bijzonder?
Ik denk dat de grootste uitdagingen voortkomen uit het gebrek aan beschikbare softwaretools om te onderzoeken wat er mogelijk is met additief. Je hebt een mentaliteit van kijken naar traditionele productietechnieken, en we zijn opgeleid met traditionele productietechnieken.
Mensen beginnen vaak met onderdelen die op traditionele wijze zijn gemaakt en willen dat onderdeel geforceerd passend maken, maar dat komt niet altijd overeen.
Maar als je echt benut wat je kunt doen met additieven, of het nu op metaal, composiet of polymeer is, in termen van uniekheid en complexiteit, dan heb je echt tools nodig om je door dat proces te leiden en ontwerpers te informeren en ingenieurs.
Hoe ziet u de branche de komende vijf jaar evolueren?
Het is erg bemoedigend. Sinds de oprichting van Arevo zijn we altijd gefocust geweest op productieonderdelen.
Als je naar de industrie van vandaag kijkt, is het echt bemoedigend om te zien dat iedereen het heeft over productie-onderdelen. Dat is het gemeenschappelijke thema.
In de toekomst verwacht ik dat de industrie ook begint te praten over kwaliteit en schaalbaarheid. Als u begint met het maken van producten, zal het produceren op schaal en met een grotere herhaalbaarheid de belangrijkste focus voor de industrie zijn.
Het waarborgen van de kwaliteit van onderdelen en processen is momenteel een belangrijk gespreksonderwerp voor additive manufacturing. Wat is Arevo's benadering hiervan?
Een van de belangrijkste doorbraken die Arevo heeft kunnen bereiken, is ons op laser gebaseerde depositieproces.
Bovendien gebruiken we machine learning-algoritmen die in situ inspecties kunnen uitvoeren. We hebben een sensorsuite en we zijn in staat om een onderdeel ter plaatse te inspecteren terwijl het wordt vervaardigd.
Hierdoor krijgen we een zeer homogeen drukwerk met minder dan 1% holtes. Je zou een dwarsdoorsnede van een onderdeel kunnen maken en als je het onder een microscoop bekijkt, kun je heel homogeen gedrukt materiaal waarnemen.
Dit vertaalt zich in onderdelen van zeer hoge kwaliteit voor veeleisende toepassingen zoals de ruimtevaart. Deze kwaliteitscontrole in situ, gecombineerd met onze closed-loop monitoring, zorgt ervoor dat we een herhaalbare en voorspelbare kwaliteit hebben.
Wat houden de komende 12 maanden in voor Arevo?
In de komende 12 maanden zullen we ons concentreren op de uitvoering van de productie. Sinds we de fiets hebben gelanceerd, hebben we eigenlijk meer vraag dan we kunnen voldoen. Ons doel voor het komende jaar is om door te gaan met het lanceren van nieuwe applicaties, maar vooral om onze capaciteit op te schalen om aan de huidige vraag te voldoen.
Ga voor meer informatie over Arevo naar: https://arevo.com/
3d printen
- Expertinterview:Nanoe CEO Guillaume de Calan over de toekomst van keramisch 3D-printen
- Expert Interview:Ultimaker President John Kawola over de toekomst van 3D-printen
- Interview met expert:Simon Fried, medeoprichter van Nano Dimension over de opkomst van 3D-printen voor elektronica
- Expertinterview:medeoprichter van Carbon, Philip DeSimone, over de overgang naar productie met hoog volume met 3D-printen
- Expert Interview:Jabil's Rush LaSelle over de toekomst van additieve productie
- Interview met expert:Xometry's Greg Paulsen over de opkomst van het productie-as-a-service-bedrijfsmodel
- Interview met expert:VELO3D's VP of Technology Partnerships over uitbreiding van de mogelijkheden van 3D-metaalprinten
- Expertinterview:John Barnes, oprichter van The Barnes Group Advisors, over de toekomst van additieve productie
- Expert Interview:Versterk CEO Josh Martin over zijn Digital Composite Manufacturing Technology
- Introductie van 's werelds eerste koolstofvezel smartphone
- Toray maakt 's werelds eerste poreuze koolstofvezel met continue poriënstructuur van nanoformaat