Groot denken:4 indrukwekkende toepassingen van grootschalig 3D-printen
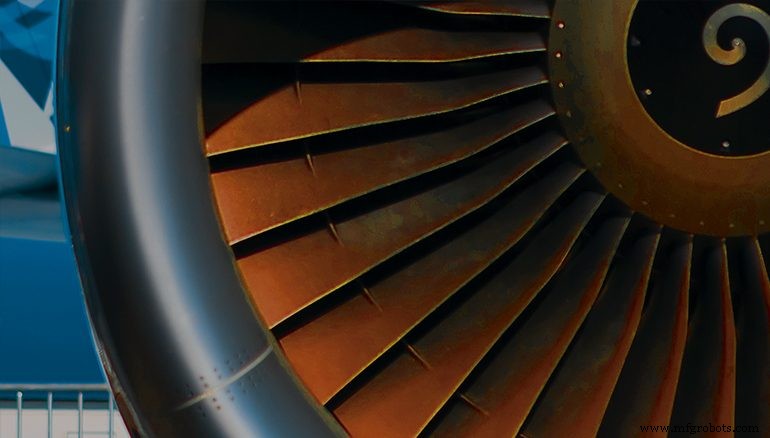
Grootschalig 3D-printen komt langzaam op de voorgrond als een kosteneffectieve en flexibele oplossing voor het vervaardigen van grote onderdelen en componenten. Dat gezegd hebbende, aangezien de meeste 3D-printers die momenteel beschikbaar zijn ontwikkeld zijn voor kleinere onderdelen, wat zijn de vooruitzichten voor 3D-printtechnologieën die grotere onderdelen kunnen printen, zoals turbinebladen en hele vliegtuigvleugels?
Het artikel van vandaag gaat in op de grootschalige 3D-printtechnologieën die momenteel beschikbaar zijn, evenals op de huidige toepassingen die de kracht van grootschalige 3D-printing laten zien.
Wat is grootschalig 3D-printen?
Als productietechnologie vindt 3D-printen steeds meer zijn plaats. De technologie wordt gebruikt in uiteenlopende toepassingen zoals gespleten lagers, auto-onderdelen, medische implantaten en schoeisel. Wat deze toepassingen echter gemeen hebben, is dat de onderdelen die worden geproduceerd allemaal relatief klein zijn.
Toegegeven, grootformaat 3D-printen is nog steeds een vrij nichetechnologie. Het heeft echter het potentieel om veel uitdagingen op te lossen waarmee fabrikanten worden geconfronteerd bij het produceren van grotere onderdelen.
Componenten van aanzienlijke omvang, zoals vliegtuigvleugels, zijn zwaar en omslachtig en vereisen langere opstellingen en grotere gereedschappen om te produceren. Dit vertaalt zich uiteindelijk in hogere productiekosten en langere doorlooptijden.
3D-printen kan fabrikanten helpen om grote onderdelen sneller en kosteneffectiever te produceren. Met de ontwerpcomplexiteit die 3D-printen biedt, kunnen dergelijke onderdelen ook profiteren van belangrijke voordelen zoals lichtgewicht en verbeterde prestaties. Ten slotte, als grote componenten in één oplage kunnen worden geprint, in plaats van in delen te worden geprint en vervolgens te worden geassembleerd, heeft dit ook het extra voordeel dat de montagetijden worden verkort.
Grootschalige 3D-printtechnologieën
Als het gaat om grootschalig 3D-printen, zijn er een aantal technologieën die daarbij passen. Hieronder vindt u enkele van de commercieel beschikbare grootschalige 3D-printtechnologieën waarvan u op de hoogte moet zijn.
Grootformaat 3D-printen voor kunststoffen
Big Area Additive Manufacturing (BAAM)
Een van de grootste 3D-printtechnologieën die momenteel beschikbaar is, is Big Area Additive Manufacturing (BAAM). Ontwikkeld door Oak Ridge National Laboratory (ORNL) in samenwerking met Cincinnati Inc., verscheen BAAM voor het eerst op IMTS 2014, waar het werd gebruikt om een volledige auto in 3D te printen.
De 3D-printer, die een extruder gebruikt die op een portaalsysteem is geplaatst, kan onderdelen tot 6 x 2,4 x 2 m maken met behulp van thermoplastische materialen zoals ABS, PPS, PC, PLA en PEI.
Sinds de introductie is BAAM in verschillende toepassingen gebruikt, van prototypes op ware grootte van een onderzeeërromp tot 3D-geprinte zelfrijdende voertuigen.
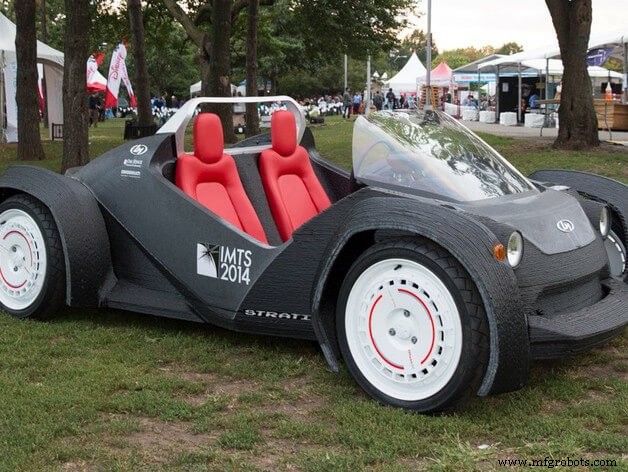
Large Scale Additive Manufacturing (LSAM)
Large Scale Additive Manufacturing (LSAM)-technologie, ontwikkeld door het Amerikaanse bedrijf Thermwood, is een andere technologie die zich exclusief richt op industriële productie.
Voor het eerst onthuld in 2016, heeft een LSAM 3D-printer een build-envelop van 10 x 40 ft (ongeveer 37 m²) en kan objecten zowel horizontaal als verticaal printen.
Een van de unieke kenmerken van de LSAM 3D-printer is de hybride benadering van het produceren van onderdelen, waarbij additieve en subtractieve technologieën worden gecombineerd.
Het bestaat uit een 3D-printportaal en een tweede trimportaal - de laatste is in feite een vijfassige CNC-router. Door deze combinatie kunnen alle stappen voor de productie van onderdelen op dezelfde machine worden uitgevoerd, wat het fabricageproces versnelt.
De LSAM 3D-printer heeft ook een extruderschroefontwerp dat is gemaakt van speciale staallegeringen. Met dit ontwerp kan de printkop printen met temperaturen tot wel 450 °C, waardoor het mogelijk is om grote onderdelen te vervaardigen waarvoor composiet thermoplasten op hoge temperatuur nodig zijn.
De LSAM-machine van Thermwood is ontwikkeld voor de productie van industriële gereedschappen, zoals matrijzen en productie-inrichtingen voor onder meer de automobiel- en luchtvaartindustrie.
BigRep's grootschalige 3D-printers
BigRep, een bekende naam in de wereld van grootformaat 3D-printen, is in 2014 opgericht met als doel grootschalig 3D-printen zo gemakkelijk en betaalbaar mogelijk te maken.
Het bedrijf introduceerde zijn eerste machine — de BigRep ONE v1 — in hetzelfde jaar, en de machine heeft een vrij groot bouwvolume van 1 kubieke meter en heeft een prijs van ongeveer $ 40.000.
Vijf jaar sinds de originele BigRep ONE 3D printer werd gelanceerd, is de BigRep ONE (nu in zijn derde iteratie) nog steeds een van de machines met de laagste prijs-per-volume beschikbaar.
BigRep's lijn van 3D-printers vult de marktkloof tussen kleine desktop 3D printers en grotere, duurdere industriële printers, en is gericht op kleine en middelgrote ontwerp- en productiebedrijven.
Grootschalige 3D-printen van metaal
Electron Beam Additive Manufacturing (EBAM)
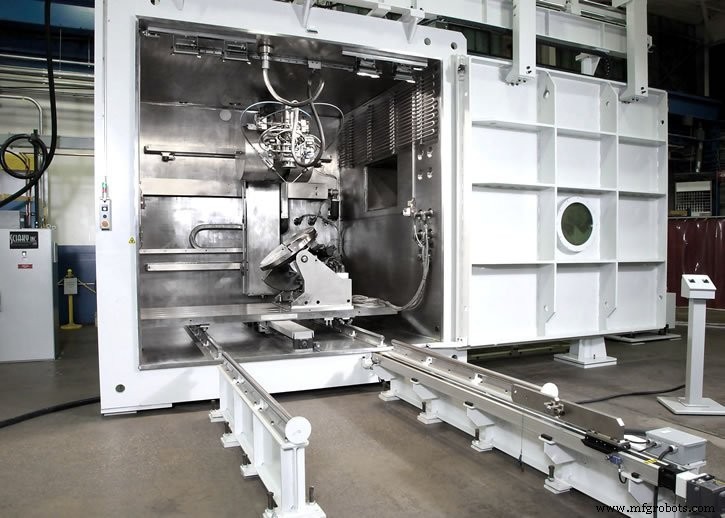
In de wereld van 3D-metaalprinten biedt Sciaky enkele van de grootste metalen 3D-printers die er zijn, aangedreven door zijn Electron Beam Additive Manufacturing (EBAM)-technologie. Het EBAM 150-systeem heeft bijvoorbeeld een indrukwekkend bouwvolume van 3708 x 1575 x 1575 mm.
EBAM gebruikt een proces vergelijkbaar met lassen, waarbij een elektronenstraal wordt gebruikt om metaal in draadvorm te smelten. Dit betekent dat de technologie zeer geschikt is voor het verwerken van een breed scala aan lasbare materialen, van titanium tot Inconel en roestvrij staal.
Sciaky positioneert zijn AM-systeem als een sneller, betaalbaarder alternatief voor grootschalige smeed- en gietstukken. Het gepatenteerde Closed-Loop Control-systeem van het bedrijf maakt de fabricage mogelijk van metalen onderdelen met verbeterde eigenschappen en microstructuren voor toepassingen in het leger, de marine en de ruimtevaart.
Wire Arc Additive Manufacturing (WAAM)
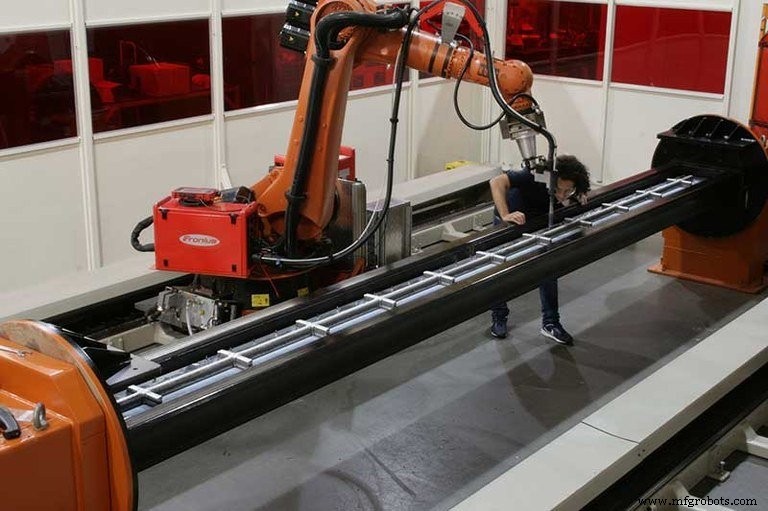
Net als EBAM gebruikt Wire Arc Additive Manufacturing (WAAM) ook draadgrondstoffen, maar smelt materialen met behulp van een elektrische boog. WAAM kan onderdelen tot 10 m lang maken met behulp van metaallegeringen zoals titanium, nikkel, roestvrij staal, aluminium en bronslegeringen.
WAAM kan worden gebruikt om grote metalen onderdelen te produceren, zoals drukvaten en panelen voor vliegtuigrompen. Naast de productie van eindonderdelen is de technologie een ideale keuze voor reparatie- en onderhoudswerkzaamheden aan specifieke componenten zoals turbinebladen, maar ook matrijzen en matrijzen.
Grootformaat 3D-zandprinten
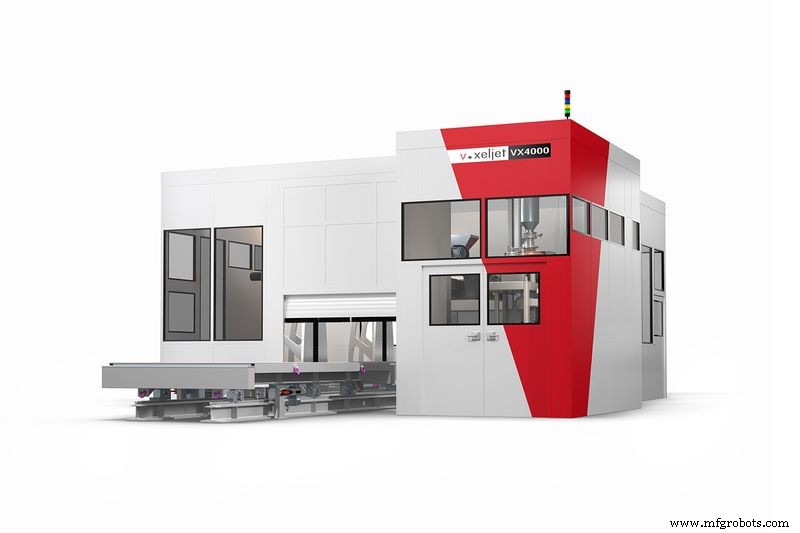
Misschien wel de bekendste fabrikant van grootformaat 3D-zandprinters is voxeljet, die sinds 2002 op dit gebied actief is.
In 2011 introduceerde voxeljet de VX4000, een van de grootste zandprinters 3D-printers tot nu toe, met een bouwvolume van 4 x 2 x 1 m.
Naast voxeljet biedt ExOne professionele zandprintsystemen, met een maximaal bouwvolume van 2,2 x 1,2 x 0,7 m.
Zowel de 3D-printers van Voxeljet als ExOne gebruiken een proces dat Binder Jetting wordt genoemd, waarbij een vloeibaar bindmiddel selectief wordt afgezet op een laag zand om zanddeeltjes samen te voegen.
Zand 3D-printen is met name gunstig voor de gieterij-industrie, omdat het een snellere en meer kosteneffectieve manier biedt om grote en complexe zandvormen en kernen voor metaalgieten te maken.
3 industrieën die kunnen profiteren van grootschalig 3D-printen
Zoals we hebben gezien, biedt het 3D-printen van grote onderdelen bedrijven een scala aan voordelen. Hieronder bekijken we hoe drie verschillende industrieën gebruik kunnen maken van grootschalig 3D-printen om de productie te versnellen, de levering te versnellen, materiaalverspilling te verminderen en nieuwe geometrieën te creëren die niet haalbaar zijn met traditionele productie.
Lucht- en ruimtevaart
Voor de lucht- en ruimtevaartindustrie wordt 3D-printen over het algemeen gebruikt om kleine en middelgrote onderdelen en gereedschappen te produceren, waardoor fabrikanten tijd kunnen besparen en kosten kunnen verlagen.
Grootformaat 3D-printen kan echter ook biedt enkele unieke kansen voor de sector. Voordelen hiervan zijn onder meer het verminderen van lange doorlooptijden en materiaalverspilling.
Normaal gesproken kan het produceren van grote structurele onderdelen met traditionele methoden zoals smeden en machinaal bewerken tot een jaar duren. Naast lange doorlooptijden kunnen traditionele subtractieve methoden ook veel materiaalverspilling opleveren - in sommige gevallen tot 80%.
Grootschalig 3D-printen daarentegen kan worden gebruikt om onderdelen te produceren in een fractie van de tijd en met minder materiaalverspilling. Wat nog belangrijker is, is dat de technologie meerdelige componenten als een enkel onderdeel kan printen - een techniek die bekend staat als onderdeelconsolidatie. Met deze aanpak kunnen montagetijden aanzienlijk worden verkort.
Spotlight:Lockheed Martin 3D print ruimtevaartonderdelen
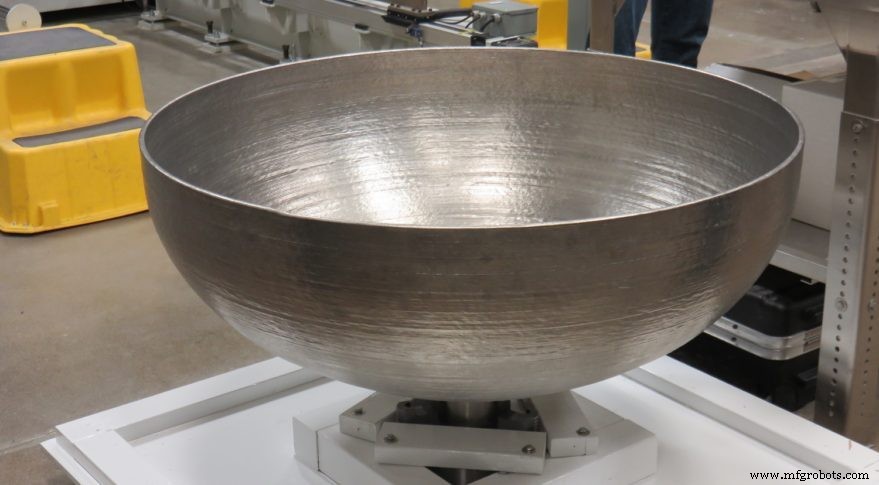
Een van de meest gebruikte grootformaat 3D-printtechnologieën binnen de lucht- en ruimtevaartindustrie is Sciaky's EBAM-technologie. Een belangrijke reden voor het gebruik in lucht- en ruimtevaarttoepassingen is het vermogen om hoogwaardige onderdelen tot 6 m hoog en 1,2 m veel sneller te produceren dan anders mogelijk zou zijn met traditionele productietechnieken.
Het wereldwijde lucht- en ruimtevaart- en defensiebedrijf Lockheed Martin was een van de eersten die EBAM gebruikte en gebruikte de technologie sinds 2014. Met deze grootformaat 3D-printmogelijkheid is het bedrijf in staat om gigantisch titanium in 3D te printen. koepels, elk met een diameter van 116 cm, voor zijn satellietbrandstoftanks.
De afgelopen zomer gekwalificeerd, werden de 3D-geprinte koepels ontwikkeld als onderdeel van een meerjarig ontwikkelingsprogramma om hogedruktanks te maken om brandstof aan boord van satellieten te vervoeren. De satellietbrandstoftank bestaat uit een traditioneel vervaardigde titanium cilinder die het lichaam vormt en twee 3D-geprinte koepels die als doppen dienen. De drie delen zijn aan elkaar gelast om het uiteindelijke tankschip te vormen.
Door gebruik te maken van het vermogen van EBAM om de exacte hoeveelheid materiaal die nodig is te deponeren, was Lockheed Martin in staat materiaalverspilling met 80% te verminderen. Bovendien stelde de hoge depositiesnelheid van het EBAM-systeem, die kan oplopen tot 11 kg per uur, de fabrikant in staat om de domes in drie maanden te leveren in plaats van twee jaar - een maar liefst 87% kortere doorlooptijd.
Lockheed Martin gelooft dat dergelijke tanks een stap zijn in de richting van een transformatie van de manier waarop het bedrijf ruimtetechnologie ontwerpt en levert. En grootformaat 3D-printen speelt een sleutelrol om het bedrijf in die richting te helpen.
Spotlight:Bell Helicopters gebruikt 3D-printen om gereedschap voor grote bladen te maken
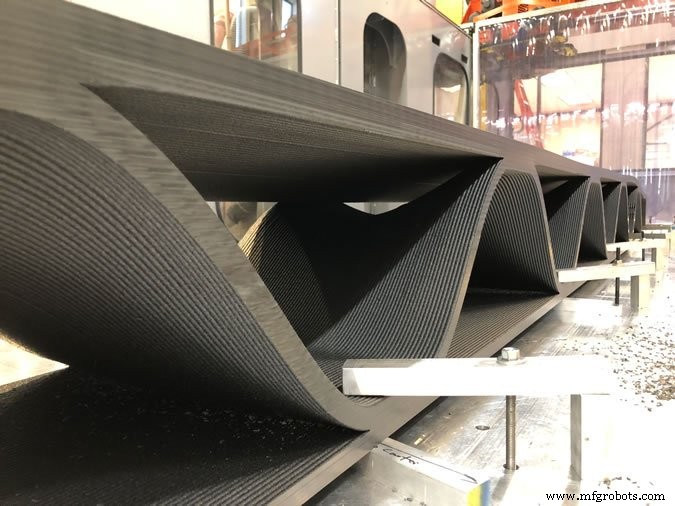
Terwijl Lockheed Martin use cases heeft gevonden voor grootschalige 3D-printing van metaal in de productie van eindonderdelen, verandert 3D-printen met polymeren het spel voor de productie van gereedschappen bij Bell.
In de lucht- en ruimtevaartindustrie kan het produceren van gereedschap een lang en duur proces zijn. Om deze uitdagingen het hoofd te bieden, wendde Bell zich tot de LSAM-technologie van Thermwood om grote mallen voor helikopterbladen te produceren.
De belangrijkste vereisten voor het gereedschap waren een goede oppervlakteafwerking, nauwe toleranties en het vermogen om autoclaafverwerking te weerstaan - een techniek die helpt bij het versterken van composietonderdelen die worden blootgesteld aan verhoogde druk en temperatuur.
LSAM was om twee belangrijke redenen ideaal voor een dergelijke toepassing. Ten eerste kon het 6 m lange gereedschap worden vervaardigd uit een hoogwaardig koolstofversterkt PESU-materiaal, dat bestand is tegen hoge drukken en temperaturen. Ten tweede, aangezien LSAM een hybride technologie is, kan een onderdeel in 3D worden geprint en afgewerkt zonder dat er een tweede machine nodig is, wat het productieproces verder helpt versnellen.
Deze voordelen stelden Thermwood in staat het gereedschap in slechts een paar dagen te vervaardigen, in tegenstelling tot de maanden die het bij traditionele processen zou kosten.
Bovendien maakte additieve technologie het mogelijk om interne ondersteuningsstructuren zo te ontwerpen dat ze de achterkant van de vormholte niet raken. Als gevolg hiervan kon de lucht vrij onder het gehele gevormde onderdeel in de autoclaaf stromen - wat helpt om het onderdeel consistenter uit te harden.
Deze prestatie wijst op de nieuwe ontwerpmogelijkheden die grootschalig 3D-printen ontsluit voor grote en technisch complexe luchtvaartcomponenten.
Bouw
Hoewel 3D-printen in de bouwsector nog in de kinderschoenen staat, biedt de technologie veelbelovend potentieel voor de sector.
Een van de opkomende trends voor 3D-printen in de bouwsector zijn bijvoorbeeld 3D-geprinte prefabbekistingen.
In de bouw verwijst bekisting naar een tijdelijke mal waarin beton wordt gestort en gevormd. Bekistingen worden gebruikt om van alles te maken, van bruggen tot funderingen en de muren van een gebouw.
Normaal gesproken kan bekisting handmatig worden gemaakt met hout. Houten bekisting is echter niet bijzonder duurzaam en begint vaak na 15 tot 20 gietstukken af te breken. Bovendien beperkt het handmatige proces onvermijdelijk de reikwijdte van de mogelijke vormen en geometrieën tot wat menselijkerwijs mogelijk is om te produceren.
In een dergelijk scenario kan grootschalig 3D-printen het proces van het maken van bekistingen aanzienlijk vereenvoudigen en tegelijkertijd grotere complexiteit en duurzaamheid voor grote matrijsconstructies mogelijk maken.
Spotlight:3D-geprinte prefab mallen transformeren de gevel van een gebouw met meerdere verdiepingen
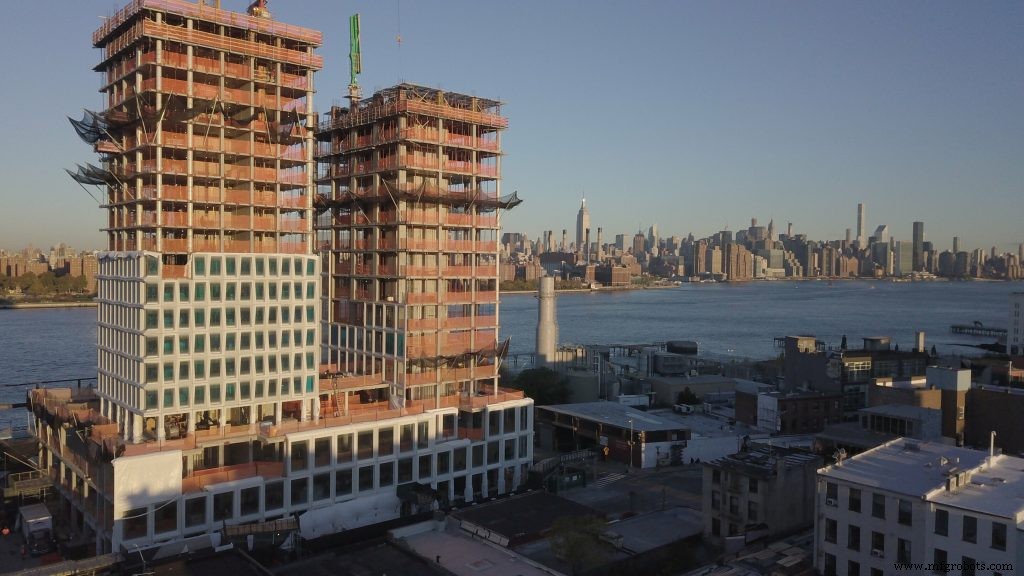
Een recent voorbeeld van het gebruik van 3D-geprinte bekisting betreft een grootschalig renovatieproject voor een woon- en bedrijfsgebouw van 42 verdiepingen in New York City.
Gate Precast, een bedrijf dat aan de nieuwe gevel van het gebouw had gewerkt, ontdekte dat het maken van houten mallen voor het project een grote onderneming zou zijn die tot 9 maanden in beslag zou kunnen nemen. De benodigde mallen waren groot - sommige met afmetingen tot 2,6 x 1,7 x 0,5 m, wat de lange productietijden nog vergroot.
Om het proces te versnellen, besloot het bedrijf te experimenteren met 3D-printen, in samenwerking met Oak Ridge National Laboratory (ORNL) om zijn BAAM-technologie te gebruiken.
Dankzij BAAM was het bedrijf in staat matrijzen te printen tussen de 8 en 11 uur per stuk, met nog eens 8 uur bewerking om de gewenste oppervlakteafwerking te bereiken. De mallen zijn gemaakt met koolstofvezelversterkt ABS, een veelgebruikte thermoplast vermengd met gehakte koolstofvezels voor extra sterkte.
Het resultaat is een sterke mal die maar liefst 200 betonstortbeurten kan dragen tijdens zijn leven, vergeleken met 15-20 stortingen voor een houten mal.
Het bedrijf is van mening dat het zonder de 3D-geprinte mallen en BAAM onmogelijk zou zijn geweest om de formulieren binnen de voor dit project benodigde tijd te maken.
In dit geval bood 3D-printen waarde bij het produceren van duurzamere en complexere mallen in een korter tijdsbestek.
Dat gezegd hebbende, hoewel deze benadering voor het maken van bekistingsmallen voordelen heeft, zal 3D-printen houten bekisting niet vervangen. Toch bewijst dit project dat 3D-printen van grote onderdelen een reeks voordelen biedt voor de bouwsector, waardoor architecten een levensvatbaar alternatief voor de productie van geprefabriceerde matrijzen krijgen.
Gieterij
Grootformaat 3D-printen komt steeds meer in beeld in de gieterij-industrie. Het gieterijbedrijf omvat de productie van metalen gietstukken door metaal te smelten en te gieten in speciaal gevormde vormen en kernen.
Als het gaat om metaalgietprocessen, kan de technologie helpen om de kostbare en tijdrovende aspecten van het maken van patronen, kernen en mallen te omzeilen.
Laten we als voorbeeld conventioneel metaalgieten nemen. Het kan maanden duren om van een tekening naar het maken van precieze mallen en patronen en uiteindelijk naar het afgewerkte gietstuk te gaan. Gieterijen zullen doorgaans ook matrijzen in voorraden moeten opslaan, wat duur kan zijn in het geval van grotere of zelden gebruikte matrijzen.
Een tekort aan vakbekwame patroon- en matrijzenmakers is een andere uitdaging waar gieterijen vaak tegenaan lopen.
3D-printen kan worden gebruikt als een hulpmiddel binnen de metaalgietindustrie om de bovenstaande uitdagingen het hoofd te bieden. Een van de voordelen van de technologie ligt in het aanzienlijk vereenvoudigde matrijsbouwproces. Omdat voor 3D-printen alleen een ontwerpbestand nodig is, kan het handmatige matrijzenbouwproces en de assemblage van de complexe kernen worden geëlimineerd.
Door de productie op deze manier te stroomlijnen, kan een gieterij binnen enkele dagen mallen en patronen maken in plaats van weken en maanden. Bovendien kan 3D-printen worden gebruikt om on-demand matrijzen te produceren, waardoor een bedrijf zijn fysieke voorraad en daarmee de opslagkosten kan minimaliseren.
Spotlight:Teignbridge maakt propellers met 3D-geprinte gietpatronen
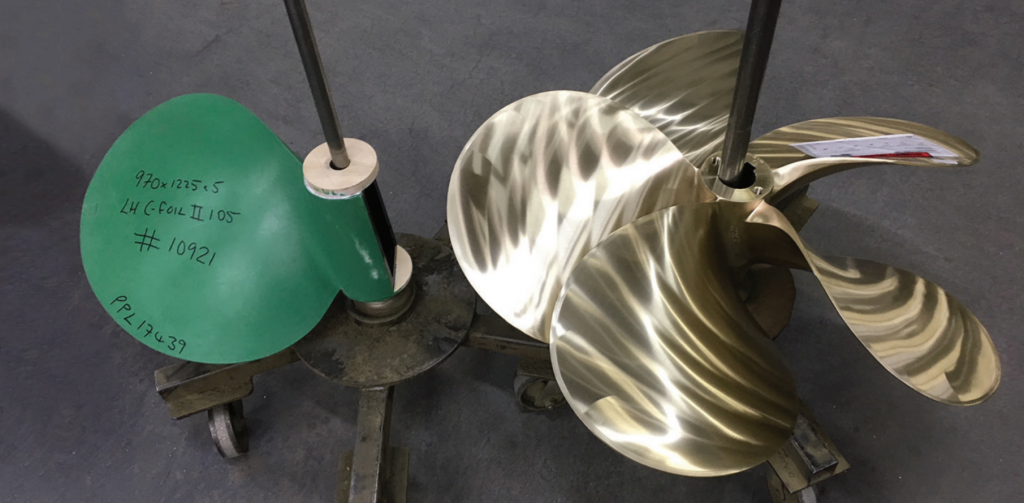
Teignbridge is gespecialiseerd in de productie van op maat gemaakte schroeven en voortstuwingssystemen voor sleepboten, luxe jachten, vistrawlers en veerboten. Sinds de oprichting 40 jaar geleden gebruikt het bedrijf het meertraps gietproces bij de productie van zijn producten.
Eén van de fasen is het maken van een patroon, een model van het uiteindelijke object. Het patroon wordt in een zandbak geplaatst om een mal te maken. Vaak is dit een arbeidsintensief en tijdrovend proces en moet eerst een patroon uit een blok hout of piepschuim worden gefreesd.
Om de tijd die nodig is om een patroon te maken te verminderen, besloot Teignbridge te kiezen voor grootformaat FDM 3D-printen met behulp van BigRep's BigRep ONE 3D-printer.
Door een 3D-printer met zo'n grote envelop in huis te hebben, kan Teignbridge het hele plastic patroon in één keer printen, wat tastbare voordelen oplevert van kortere cyclustijd en arbeidsinput.
Bij een traditionele benadering van het maken van een patroon kan een ervaren CNC-operator bijvoorbeeld tot 20 uur besteden aan frezen, sectiemontage en nabewerking. Met 3D-printen daarentegen kan Teignbridge het proces voor het maken van patronen automatiseren, waardoor de arbeidsinput met 90% wordt verminderd.
Bij het metaalgieten wordt 3D-printen steeds vaker gebruikt als alternatieve manier om patronen en mallen te maken.
Naast grootformaat FDM 3D-printen hebben bedrijven ook een 3D print optie. Zand 3D-printers elimineren de stap van het maken van patronen door direct een zandvorm te maken.
Hoewel zand 3D-printsystemen zo groot kunnen zijn als 4000 x 2000 x 1000 mm, zijn ze meestal vrij duur. Dat gezegd hebbende, beginnen bedrijven de voordelen van 3D-geprinte patronen en mallen te erkennen, omdat ze het gietproces sneller, flexibeler en kosteneffectiever maken.
Grote kansen met grootschalig 3D-printen
Grootformaat 3D-printen blijft momenteel eerder een nichetechnologie. Een van de belangrijkste redenen hiervoor kan liggen in het feit dat veel bedrijven nog steeds niet op de hoogte zijn van de voordelen en mogelijkheden van additive manufacturing in het algemeen, laat staan het grootformaat aspect ervan. Als gevolg hiervan hebben bedrijven moeite om een passende businesscase te vinden.
Complicatie is dat veel 3D-systemen op groot formaat onbetaalbaar blijven. Als gevolg hiervan kunnen bedrijven die met de technologie willen experimenteren om de juiste toepassing te vinden, het zich niet veroorloven.
Gelukkig begint dit te veranderen, aangezien de markt voor grootschalig 3D-printen voortdurend groeit, wat meer betaalbare opties biedt, zoals de 3D-printers van BigRep.
Uiteindelijk heeft de technologie voor het printen van grotere onderdelen het potentieel om uit te breiden naar andere markten en toepassingen. Automotive zou daar een van kunnen zijn.
Autofabrikanten zouden 3D-printen op groot formaat kunnen gebruiken om prototypes te maken van grotere onderdelen zoals spoilers en autopanelen, die met de huidige machines moeilijk te printen zijn.
“Elk voertuig bestaat uit een heleboel kleine componenten die goed passen binnen de bouwomhullingen van de huidige machines”, zegt Harold Sears van Ford Motor Company in een recent interview met AMFG. “Maar er zijn ook veel grotere componenten die tegenwoordig gewoon niet helemaal passen. Daarom zouden we graag zien dat fabrikanten andere systemen overwegen die een grotere bouwomhulling hebben.”
Het is duidelijk dat de vraag naar grootformaat 3D-printen er is, gedreven door de voordelen van kortere doorlooptijd en kosten. Nu moet de industrie de technologie blijven ontwikkelen om aan die behoefte te voldoen, zodat andere industrieën zich kunnen openstellen voor grotere kansen, zowel letterlijk als figuurlijk.
3d printen
- Toepassingen van 3D-afdruktechnologie van titaniumlegering
- De rol van extrusie in 3D-printtoepassingen
- 5 toepassingen die innovatie op het gebied van 3D-printen laten zien
- Drie 3D-printtoepassingen om over te lachen
- Wat biedt de toekomst voor 3D-printen – biomedische toepassingen
- Hoe integreert u 3D-printen in een groot bedrijf?
- 3D-printen gaat een grote rol spelen in de ontwikkeling van elektrische auto's
- Materialen:PEEK-filament van implantaatkwaliteit voor medische toepassingen in 3D-printen
- Wat is 3D-printen? Werkingsprincipe | Soorten | Toepassingen
- Toepassingen van 3D-printen in de tandheelkunde
- 10 meest hittebestendige 3D-afdrukmaterialen