Nabewerking voor industrieel 3D-printen:de weg naar automatisering
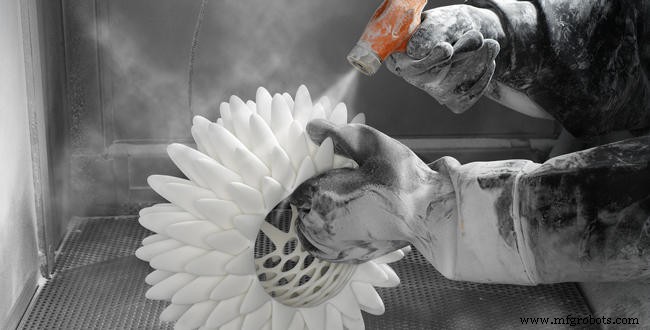
Lange tijd werd nabewerking het 'dirty little secret' van 3D-printen genoemd. Met zoveel focus op de eerste twee fasen van het additieve fabricageproces - ontwerp en productie - is de nabewerkingsfase vaak onder de radar gebleven.
Hoewel additieve fabricage vaak wordt geprezen vanwege de omarming van digitale, geautomatiseerde processen, met name in de context van Industrie 4.0, is het bijna ironisch dat de nabewerkingsfase overwegend handmatig blijft. Dit heeft belangrijke implicaties voor een bedrijf dat AM wil gaan gebruiken - nabewerking is een onvermijdelijke stap die echter tijd en kosten zal toevoegen aan het totale productieproces. Voor bedrijven die hun activiteiten willen uitbreiden en schalen, is dit vaak een nogal frustrerend knelpunt.
Bij het ontwikkelen van een routekaart voor additive manufacturing heeft de Additive Manufacturing Association in de German Engineering Federation (VDMA) onlangs naverwerking geïdentificeerd als omdat het de fase is die het meest moet worden ontwikkeld om serieproductie mogelijk te maken.
Maar in 2018 is er een toenemende focus op nabewerking voor 3D-prints, waarbij bedrijven steeds meer op zoek zijn naar automatisering van deze fase. Nu de industrie geleidelijk in de richting van productie gaat, zal het ontwikkelen van een schaalbare nabewerkingsfase een essentieel element zijn in deze overgang, die ook zal moeten evolueren om herhaalbare, schaalbare en geautomatiseerde oplossingen mogelijk te maken.
In het artikel van vandaag kijken we naar de uitdagingen en recente ontwikkelingen rond nabewerking in AM. Maar laten we eerst eens nader kijken naar de typische nabewerkingstaken waarmee AM-gebruikers te maken hebben.
Nabewerking voor 3D-printen:een overzicht
De realiteit van 3D-printen is dat vrijwel alle 3D-geprinte onderdelen enige vorm van nabewerking vereisen om de mechanische eigenschappen, nauwkeurigheid en esthetiek van een onderdeel te verbeteren. Het bepalen van de omvang en het type nabewerking hangt onder andere sterk af van zowel het materiaal als de gebruikte technologie.
Ondersteuning verwijderen
Het verwijderen van ondersteuningen is meestal de eerste nabewerkingsstap voor elk 3D-geprint onderdeel dat met ondersteuningen is geproduceerd. Deze kunnen met de hand worden verwijderd of, in het geval van FDM-onderdelen, bijvoorbeeld door een onderdeel in een oplosmiddel te plaatsen.
Als ze bijvoorbeeld van de bouwplaat zijn gescheiden, moeten FDM-onderdelen eerst worden verwijderd, terwijl SLA-onderdelen eerst moeten worden ontdaan van overtollig harsmateriaal voordat de steunen kunnen worden verwijderd.

Poederverwijdering
Met 3D-printtechnologieën die gebruik maken van materialen in poedervorm, zoals Binder Jetting en SLS, begint de nabewerkingsfase door eerst ongebruikt poeder te verwijderen. Dit wordt dan gevolgd door oppervlaktebehandelingen (SLS) of infiltratie met superlijm (Binder Jetting).
Metalen onderdelen
Bij 3D-metaalprinten is de nabewerkingsstap aanzienlijk ingewikkelder. Bedrukte metalen onderdelen moeten eerst worden ontpoederd, een proces dat doorgaans met de hand wordt gedaan. Zodra het poeder is verwijderd, moeten onderdelen van de bouwplaat worden weggesneden met behulp van draadvonken of een lintzaag.
Bovendien zijn voor metalen onderdelen spanningsverlichtings- en warmtebehandelingsprocessen nodig om restspanningen te verminderen en de mechanische eigenschappen van het onderdeel te verbeteren. Vervolgens worden onderdelen machinaal bewerkt om ondersteunende structuren te verwijderen en maatnauwkeurigheid te garanderen.
Inspectie
Testen en inspectie zijn een andere cruciale nabewerkingsstap voor 3D-geprinte onderdelen, met name metaal. Momenteel is inspectie van additief vervaardigde onderdelen grotendeels een vergelijkbaar proces als gesmede en gegoten onderdelen en omvat visuele, dimensionale, externe en interne tests.
Er zijn echter ook enkele verschillen, aangezien veel 3D-geprinte onderdelen worden geconsolideerd en opnieuw ontworpen. Om niet-destructieve inspectie mogelijk te maken, kiezen bedrijven steeds vaker voor CT-scanning om interne geometrieën te evalueren en ervoor te zorgen dat er geen verborgen gebreken in onderdelen zijn.
3D-geprinte onderdelen kunnen ook een oppervlaktebehandeling ondergaan om de geometrische nauwkeurigheid en esthetiek te verbeteren. Dergelijke secundaire nabewerkingsstappen omvatten schuren, vullen en schilderen van kunststof onderdelen, evenals machinale bewerking van metalen onderdelen - dit alles is typisch een handmatig proces.
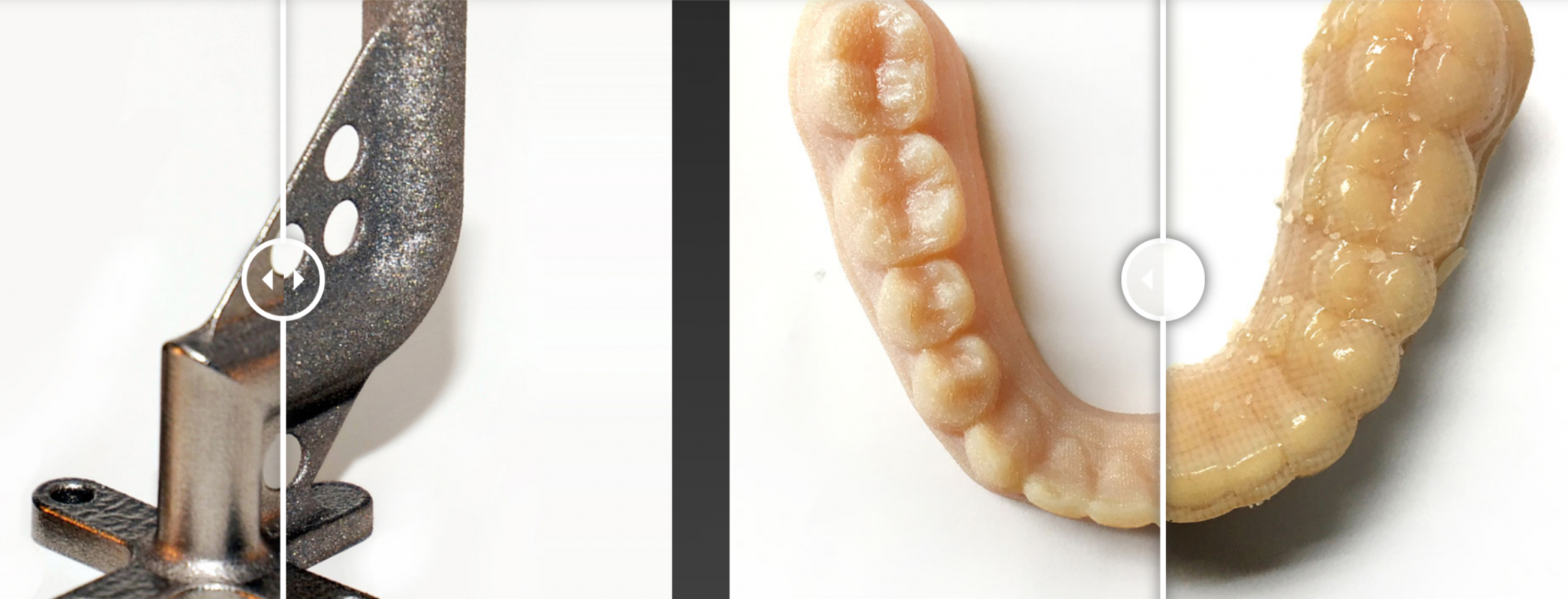
Nabewerking voor kunststoffen
ontpoederen
(schuren, polijsten, schilderen)
Nabewerking van metalen
Het knelpunt na de verwerking
De meeste nabewerkingen zijn nog steeds een zwaar handmatig proces, waarbij bekwame operators belangrijke taken moeten uitvoeren. Het gebruik van handmatige methoden om de nabewerkingsfase te beheren, kan echter de doorlooptijden en productiekosten aanzienlijk verhogen. Het is daarom geen verrassing dat nabewerking vaak wordt beschouwd als een belangrijk knelpunt voor bedrijven die hun AM-activiteiten willen schalen.
Knelpunt #1:Langere doorlooptijden
Langere doorlooptijden zijn een aspect waar veel bedrijven niet vanaf het begin op zijn voorbereid. Eén statistiek suggereert zelfs dat de nabewerkingsfase de totale procestijd met 17% tot 100% kan verlengen.
Bovendien, aangezien nabewerkingen vaak worden uitgevoerd op basis van een achterstand, kan ook dit de doorlooptijd van 3D-geprinte onderdelen verlengen. Onderdelen die de nabewerkingsfase binnenkomen, zullen vaker wel dan niet in een wachtrij belanden vanwege een gebrek aan beschikbaarheid van arbeidsmiddelen of toegang tot apparatuur.
Knelpunt #2:extra kosten
Van arbeid tot nabewerkingsapparatuur, nabewerking zal extra kosten met zich meebrengen die in het totale productiebudget moeten worden verrekend.
Het minimaliseren van arbeidsinput zou de arbeidskosten drastisch kunnen verlagen en tegelijkertijd de mogelijkheid bieden om de productie uit te breiden door meer 3D-printers toe te voegen of het nabewerkingspersoneel opnieuw toe te wijzen aan andere taken.
Met metalen 3D printen, zijn de kosten vaak aanzienlijk hoger. Of het nu gaat om het verwijderen van het onderdeel van een bouwplaat, warmtebehandeling of inspectie, de kosten kunnen gemakkelijk oplopen. Het gebruik van draadvonken om onderdelen van een bouwplaat te verwijderen, kan naar verluidt bijvoorbeeld tot $ 300 per plaat kosten wanneer het wordt uitbesteed en het kan enkele uren duren voordat het klaar is, afhankelijk van het aantal en de grootte van de onderdelen.
Stressverlichting en warmtebehandeling kunnen ook erg tijdrovend en duur zijn, waarbij ofwel dure nabewerkingsapparatuur moet worden aangeschaft voor intern gebruik of de taak moet worden uitbesteed, waarvan de kosten gemakkelijk kunnen oplopen tot enkele honderden dollars per onderdeel .
Knelpunt #3:vaardigheidskloof
Om nabewerking van hoge kwaliteit te bereiken, hebben bedrijven behoefte aan, maar hebben ze vaak moeite om gekwalificeerde technici te vinden. Deze uitdagingen worden nog verergerd door kwesties rond veiligheid, zoals de correcte verwijdering van afval dat vrijkomt tijdens de nabewerking.
Belangrijke ontwikkelingen
Naarmate meer bedrijven additieve productie voor productie gebruiken, wordt de behoefte aan automatisering in elke fase op schaal steeds nijpender.
In dit kader zijn al verschillende bedrijven begonnen met het ontwikkelen van slimme oplossingen om de knelpunten in de nabewerkingsfase aan te pakken.
Poederverwijdering en reiniging
Voor metaalpoederbedfusieprocessen is het ontpoederen en reinigen van metalen onderdelen een belangrijke stap in de nabewerkingsfase. Dit kan met name een uitdaging zijn als het gaat om zeer complexe of ingewikkelde onderdelen, zoals infusiesproeiers of koelkanalen voor spuitgietmatrijzen.
Duits bedrijf Solukon heeft een systeem ontwikkeld met een geautomatiseerd poederverwijderingsproces. Met behulp van gecontroleerde trillingen en programmeerbare asrotatie zorgt de SFM-AT800S ervoor dat metalen onderdelen grondig kunnen worden gereinigd van ongesinterd metaalpoeder en is al in gebruik door Siemens.
Metalen AM-systeemfabrikant Digital Metal is een ander bedrijf met het oog op een toekomst van slimme nabewerking, met de ontwikkeling van een computergestuurde ontpoederingsmachine. Naast een pick-and-place robot is het systeem ontworpen om belangrijke processtappen te automatiseren door automatisch ongesinterd poeder te verwijderen en groene onderdelen te verzenden voor debinding en sinteren.
Voor plastic onderdelen biedt DyeMansion een Powershot C-systeem, uitgerust met twee straalmondstukken en een roterende mand om reproduceerbare reiniging en poederverwijdering voor polymeeronderdelen mogelijk te maken.
Ondersteuning verwijderen
Ondersteuningsstructuren worden al lang als een noodzakelijk kwaad beschouwd bij 3D-printen, wat extra tijd en kosten met zich meebrengt voor zowel het printproces als de nabewerking.
“Tegenwoordig is er nog steeds een zwaar onderdeel van handenarbeid als het gaat om het verwijderen van steunen van additieve onderdelen”, zei Jeff Mize, CEO van PostProcess Technologies, in ons recente interview.
PostProcess-technologieën heeft tot doel de stap voor het verwijderen van de ondersteuning voor 3D-geprinte onderdelen te automatiseren, naast het aanbieden van oplossingen voor oppervlakteafwerking. Het bedrijf biedt al een reeks geautomatiseerde, handsfree oplossingen voor het verwijderen van ondersteuning voor onderdelen die additief zijn vervaardigd door FDM-, SLA-, PolyJet- en CLIP-technologieën.
Er zijn verschillende spannende ontwikkelingen met betrekking tot het verwijderen van ondersteuningen voor metalen onderdelen. Een voorbeeld is het Amerikaanse bedrijf Velo3D die een metalen 3D-printer met poederbed heeft ontwikkeld die kan printen met tot vijf keer minder benodigde ondersteuningen in vergelijking met andere metalen systemen met poederbed.
Een ander aanbod dat het verwijderen van ondersteuning vergemakkelijkt, is afkomstig van Materialise . De e-Stage for Metal-software genereert automatisch ondersteuningsstructuren voor metalen componenten. Gegenereerde dragers zijn dun en gemakkelijk te verwijderen, en kunnen naar verluidt de tijd die nodig is voor het verwijderen van metalen dragers met 50% verminderen.
Oppervlakteafwerking
Het bereiken van een glad, afgewerkt uiterlijk is een belangrijke vereiste voor zowel prototypes als eindonderdelen. Het handmatig voltooien van deze stap kan echter zeer inefficiënt zijn in termen van snelheid en consistentie. Het automatiseren van oppervlakteafwerking is dus weer een cruciale stap in het overbruggen van een gat in de digitale productieketen van AM.
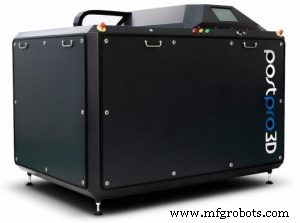
Additive Manufacturing Technologies (AMT) heeft een geautomatiseerde nabewerkingsoplossing ontwikkeld voor 3D-geprinte onderdelen, die in september van dit jaar commercieel werd gelanceerd. De PostPro3D-machine van het bedrijf maakt automatisch 3D-geprinte elastomere of nylon onderdelen glad en afwerkt die zijn gemaakt door middel van 3D-printen op poederbasis en op filamenten. Interessant is dat de PostPro3D naar verluidt porositeit, afdichting en gladde onderdelen verwijdert zonder hun mechanische eigenschappen aan te tasten, nadat het is getest door HP en Under Armour.
De combinatie van additive manufacturing met traditionele technologieën opent de weg voor geautomatiseerde oppervlakteafwerking voor metalen onderdelen. Er zijn al hybride systemen op de markt die DED-technologie en CNC-frezen integreren om een betere oppervlakteafwerking en nauwere toleranties te bereiken.
Inspectie en kwaliteitsborging
Als het om einddelen gaat, is er geen ruimte voor onzekerheid. Om deze reden is het verifiëren van grondstoffen en het identificeren van mechanische en chemische eigenschappen van additief vervaardigde componenten een integraal onderdeel van het AM-proces. Hoewel grondige kwaliteitscontroles essentieel zijn om ervoor te zorgen dat er geen defecten aan onderdelen zijn, is het optimaliseren van het proces voor kwaliteitscontroles even belangrijk.
Vandaag de dag moet een groot deel van de inspectie van 3D-geprinte onderdelen nog steeds handmatig worden uitgevoerd met behulp van speciale inspectieapparatuur, maar er komen nieuwe oplossingen aan om het beheer van deze bewerkingen te digitaliseren.
Bij AMFG bieden we bijvoorbeeld post-productiebeheeroplossingen, waaronder postverwerkingsplanning en beheeroplossingen voor digitale kwaliteitsborging. De eerste vereenvoudigt de nabewerking doordat gebruikers de middelen kunnen plannen en toewijzen die nodig zijn om aan eventuele aanvullende vereisten voor nabewerking te voldoen. Hiermee kunnen gebruikers onderdeeldocumentatie, zoals rapporten, datasheets en 3D-beelden, importeren en deze specificaties vergelijken met het fysieke, 3D-geprinte onderdeel.
Het op deze manier digitaliseren van het QA-proces zorgt voor meer efficiëntie en traceerbaarheid in de inspectiefase.
Nabewerking:de weg vooruit
Hoewel er dit jaar een reeks belangrijke ontwikkelingen zijn geweest op het gebied van nabewerkingsoplossingen voor 3D-printen, moet er nog veel gebeuren om 3D-printen echt te laten schalen.
Momenteel richten bedrijven in de industrie zich op het automatiseren van zoveel mogelijk van de nabewerkingsstappen om handmatige bewerkingen te vervangen door software of robotgestuurde systemen. Ondertussen is ontwerp voor additive manufacturing ook een sleutelfactor als het gaat om het verminderen van de behoefte aan nabewerking.
Het bevorderen van nabewerking in 3D-printen is echter niet alleen een kwestie van het ontwikkelen van nieuwe systemen, softwareoplossingen en het overbruggen van de kenniskloof. Een van de grootste struikelblokken waarmee de industrie momenteel wordt geconfronteerd, is het ontbreken van een uitgebreide reeks normen met betrekking tot nabewerking. Terwijl er op dit gebied wordt gewerkt - ASTM heeft bijvoorbeeld een standaard vrijgegeven voor thermische nabewerking van metalen AM-onderdelen - kan de ontwikkeling ervan enige tijd in beslag nemen.
Ondanks deze uitdagingen lijkt de weg voor ons echter rooskleurig; de voortdurende verbeteringen in de nabewerking die we vandaag waarnemen, zullen bijdragen aan de doorvoer, consistentie en productiviteit die de industrie nodig heeft.
3d printen
- Zal de nabewerkingsfase ooit achterhaald worden?
- Industrieel 3D-printen:6 trends om op te letten in 2018
- Emiraten adopteren 3D-printtechnologie voor vliegtuigonderdelen
- Kan 3D-printen met meerdere materialen de volgende stap zijn voor AM?
- Is de bouwsector klaar voor 3D-printen? (update 2020)
- De weg naar industriële IoT-beveiliging
- De zekering 1 afdrukken met de zekering 1
- The Economist:industrieel 3D-printen gaat van de grond
- Wat zijn de voordelen van een horizontale boormachine voor industriële onderdelen?
- 10 waterbestendige opties voor uw 3D-geprinte onderdelen:materialen en nabewerking
- De kracht van AI in industriële automatisering