Interview met experts:Pat Warner, specialist in additieve productie van Renault Formula One Team
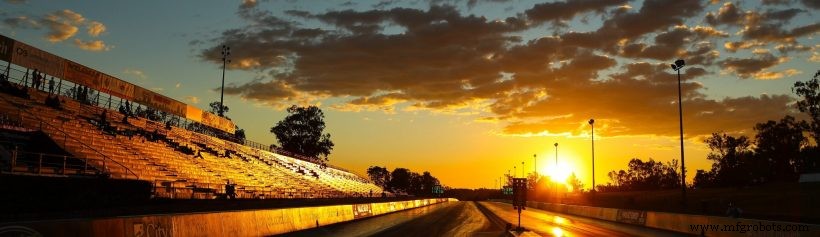
Pat Warner is ADM Manager bij Renault Sport Formula One Team — een interne specialist in additive manufacturing, die werkt aan het leveren van eersteklas geprinte componenten voor zowel prototyping als productiedoeleinden. Pat is al meer dan 19 jaar nauw betrokken bij additive manufacturing binnen de F1 en is getuige geweest van een aantal belangrijke ontwikkelingen in de technologie en de toepassingen ervan, die hij zo vriendelijk was te bespreken met AMFG in het onderstaande interview:
AMFG:Hoe ben je oorspronkelijk betrokken geraakt bij additive manufacturing?
Pat:Ik was oorspronkelijk een CNC-machinist bij het toenmalige Benetton Formula Team en verhuisde in 1997 naar de CAM-afdeling. We kochten onze eerste SLA-machine in '98, maar wisten niet echt wat we ermee moesten doen. De machine werd in een kamer naast de machinewerkplaats geplaatst en de programmeertaak werd aan de CAM-groep gegeven. Tegen 2000 hadden we genoeg toepassingen gevonden om de SLA-machine te PX voor twee nieuwere, snellere modellen. In 2002 kochten we er nog twee. In 2003 hebben we lasersinteren aan de afdeling toegevoegd en sindsdien zijn we geleidelijk uitgebreid tot de bestaande afdeling van negen machines.
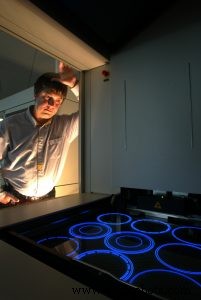
AMFG:Wat zijn enkele van de grootste AM-succesverhalen die je hebt meegemaakt tijdens je tijd bij Renault?
Pat:Er zijn er in de loop der jaren zoveel geweest.
We maken een prototype van elk nieuw onderdeel van de auto en assembleren het voor functie/geschiktheid. Dit is niets nieuws in de wereld van additieven, maar het betekent dat we onze fouten heel snel kunnen vinden. De verpakking van een moderne F1-auto is een uitdaging voor het ontwerpteam, omdat het moeilijk is om ruimte te geven aan de monteurs om toegang te krijgen tot delen van de auto als ze naar een scherm kijken.
We vervaardigen onze eigen investeringsgietpatronen voor onze structurele titaniumcomponenten, zoals de versnellingsbakbehuizing. We hebben veel tijd en moeite gestoken in het verfijnen van dit proces en eindigen meestal bij de gieterij die we gebruiken om patronen van ons te kopen (op dit moment maken we alleen componenten voor het team).
Additive manufacturing heeft ongetwijfeld het ontwikkelingstempo in de windtunnels van de F1 verhoogd. Toen we onbeperkte windtunneluren draaiden, produceerden we meer dan 600 onderdelen per week, alleen om de tunnel te voeden. De hoeveelheid conventionele productiemiddelen die nodig zijn om hetzelfde doel te bereiken, zou immens zijn.
Snelle mallen en armaturen hebben geholpen bij de productie van de auto en bij last-minute aanpassingen op het circuit. Het vinden van een probleem op vrijdag, het maken van vervangende items en het op tijd afleveren op de baan om te worden gemonteerd voor de kwalificatie, is vaak gebeurd.
Natuurlijk hebben we ook onze kleine rampen gehad, maar ze helpen allemaal bij het leerproces.
AMFG:Wat zijn de belangrijkste uitdagingen die u heeft ondervonden als het gaat om AM als hulpmiddel voor zowel prototyping als productie?
Pat:Nogmaals, er zijn er zoveel geweest.
Toen we er voor het eerst mee begonnen, was de levensduur van het onderdeel een groot probleem, SLA-materialen waren erg kwetsbaar en konden niet goed tegen vochtigheid. Als je een onderdeel een week op je bureau zou kunnen houden zonder dat iemand het breekt, zou het vervormen omdat het vocht uit de lucht absorbeert. Materiaalontwikkeling heeft voor deze problemen gezorgd en een aantal enorme verbeteringen aangebracht.
Toen we begonnen met het inkopen van onderdelen van externe leveranciers, merkten we dat je in sommige gevallen hetzelfde onderdeel zelden twee keer zou krijgen, zelfs als het van dezelfde build kwam. Dit moedigde ons aan om meer in huis te halen, meer tijd te besteden aan het begrijpen van de apparatuur en materialen en het verfijnen van onze processen. In 2004 gingen we een partnerschap aan met Boeing. Deze samenwerking heeft ons allebei op die weg geholpen en heeft ertoe geleid dat we meer componenten op onze voertuigen kunnen plaatsen. We hebben speciaal voor onze behoeften materialen ontwikkeld, die in de handel verkrijgbaar zijn (volgens de FIA-voorschriften moet dit zijn) en die elders worden gebruikt.
Onderwijs was ook een uitdaging, hoewel de technologie al geruime tijd bestaat, is de acceptatie ervan in de reguliere productie geleidelijk gegaan, net als het onderwijs. Als gevolg hiervan krijgen we nog steeds nieuwe ontwerpers die niet zijn blootgesteld aan additive manufacturing.
AMFG:Welke nieuwe innovaties zou je het liefst zien op het gebied van zowel printplatforms als materialen?
Pat:Beide gebieden hebben een lange weg afgelegd in de 19 jaar dat ik erbij betrokken ben geweest, maar er is nog meer ruimte om de technologie te laten rijpen. We moeten nog steeds veel aandacht besteden aan onze processen om de gewenste resultaten te bereiken en we zien nog steeds inconsistenties in sommige van de componenten die we inkopen. Sommige van deze inconsistenties kunnen zitten in de apparatuur die we gebruiken, maar er zijn onlangs goede stappen gezet op dit gebied belemmeren sommigen de leveranciers de apparatuur te gebruiken en de materialen te recyclen. Het gaat echter niet alleen om de platforms en materialen; we hebben ook betere ontwerptools nodig voor AM.
We hebben allemaal de lichtgewicht holle structuren gezien met traliewerk aan de binnenkant. Dit zou perfect moeten zijn voor autosport en ruimtevaart, maar in werkelijkheid zijn we niet in staat om de sterkte, stijfheid en faalmechanismen van dergelijke componenten goed genoeg te voorspellen om ze volledig te kunnen benutten.
AMFG:Hoe ziet u het gebruik van AM de komende jaren binnen de F1 evolueren?
Pat:We vinden voortdurend nieuwe toepassingen. Naarmate de toolbox groter wordt, neemt ook het aantal applicaties toe.
Metalen maken elk jaar enorme stappen, net als polymeren op hoge temperatuur. Naarmate ze verder komen en we beter begrijpen hoe we ze moeten gebruiken, kunnen we veel meer uit AM-onderdelen halen.
Het is best een spannende tijd voor AM, het krijgt veel aandacht en geld. Dit kan alleen maar goed zijn voor de hele industrie, want er is nog een lange weg te gaan voordat we de conventionele productie volledig kunnen uitdagen.
www.renaultsport.com
3d printen
- Heroverwegen van het software-integratieproces voor additive manufacturing-activiteiten
- Expertinterview:Felix Ewald, CEO van DyeMansion
- Interview met een expert:Ibraheem Khadar van Markforged
- Interview:Dominic Parsonson van Fuji Xerox Australia
- Expertinterview:James Hinebaugh van Expanse Microtechnologies
- Interview met expert:CEO van PostProcess Technologies over het oplossen van het knelpunt in de nabewerking voor additieve productie
- Interview met experts:Sintavia President Doug hedges op het bereiken van serieproductie met 3D-metaalprinten
- Interview met experts:Brian Alexander van Solvay over de ontwikkeling van hoogwaardige polymeren voor 3D-printen
- Expert Interview:Jabil's Rush LaSelle over de toekomst van additieve productie
- Interview met expert:Nanci Hardwick, CEO van MELD Manufacturing, over het benutten van het potentieel van de productie van metaaladditieven
- Additieve productie in de lucht- en ruimtevaart