Revolutie van het kostenparadigma van composieten, deel 2:Vorming
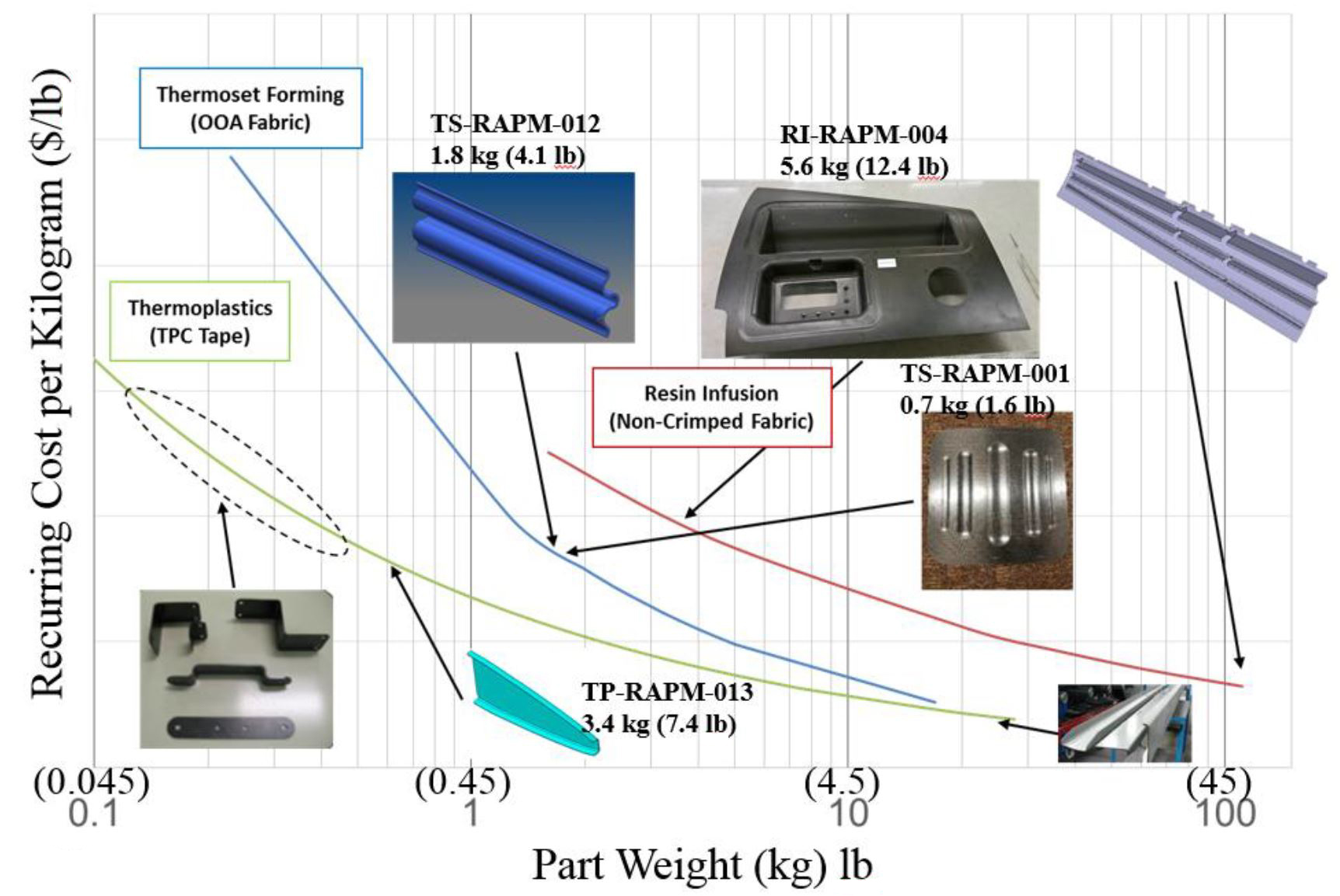
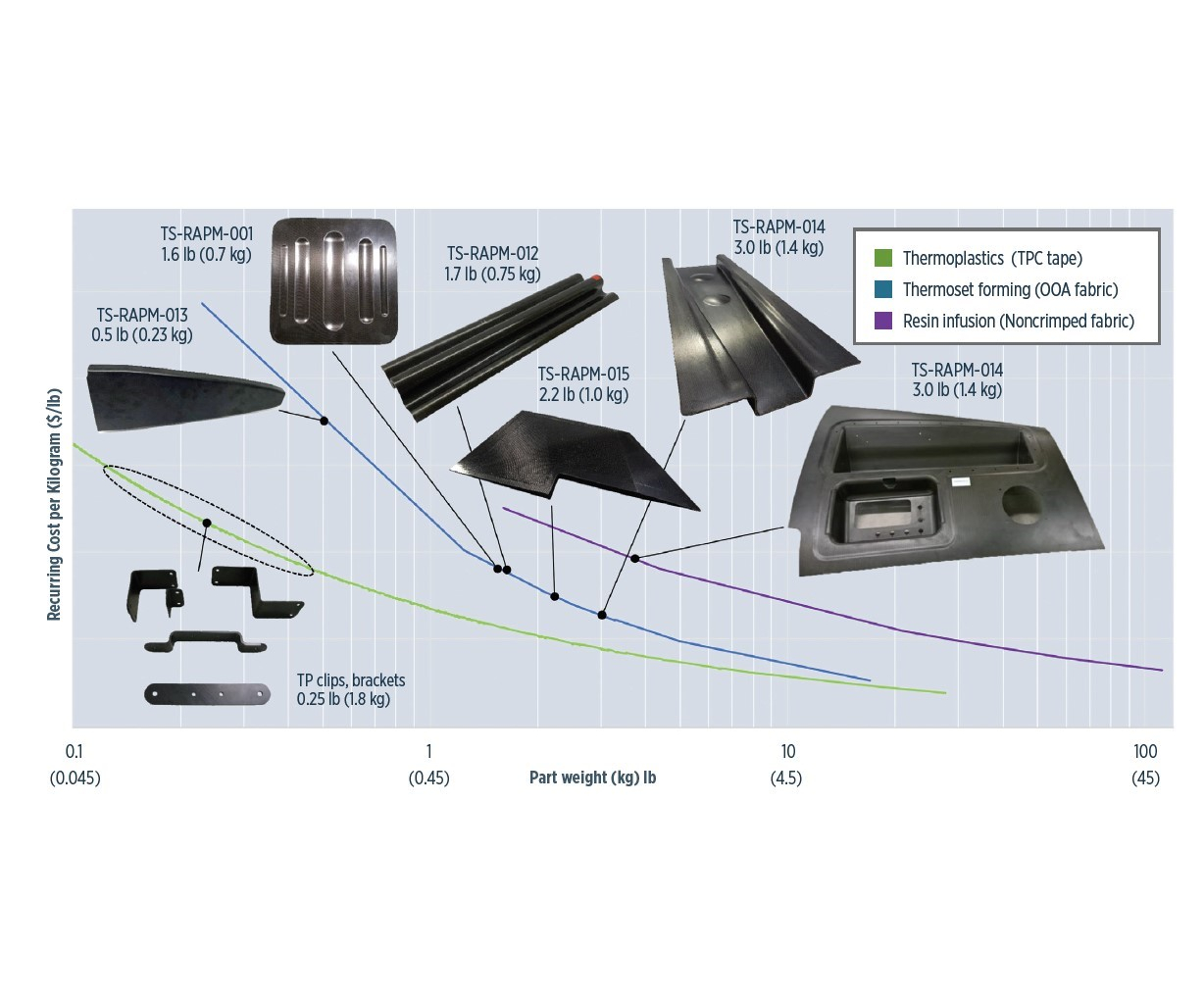
Het RAPM-subprogramma binnen DARPA's Tailorable Feedstock and Forming (TFF) -programma verzamelde analytische gegevens van huidige/verleden productie, evenals empirische gegevens van zijn eigen vormproeven voor meerdere onderdelen om deze curven te genereren. Het doel is om de handelsruimte voor composietonderdelen en -processen beter te begrijpen.
Bron voor alle afbeeldingen:The Boeing Co., DARPA
Het Tailorable Feedstock and Forming (TFF)-programma werd in 2015 gelanceerd door het Defense Advanced Research Projects Agency (DARPA, Arlington, Va., VS) om een snelle, goedkope en flexibele productie van kleine, complexe composietonderdelen voor defensie mogelijk te maken vliegtuigen. Dit 48 maanden durende programma was gericht op het verhogen van de kostenconcurrentie van composieten om hun gewichtsbesparing en weerstand tegen corrosie en barsten ten opzichte van bewerkt aluminium te benutten. In deel 1 van deze serie, CW onderzocht de visie van TFF en het subprogramma Tailorable Universal Feedstock for Forming (TuFF), dat een kortvezelig plaatmateriaal ontwikkelde met hoge mechanische eigenschappen en metaalachtige vervormbaarheid.
In dit artikel verschuift de focus van grondstof naar vorming met TFF's tweede subprogramma:RApid high-Performance Manufacturing (RAPM, uitgesproken als "wrap-em") onder leiding van The Boeing Co. (Chicago, Ill., V.S.). Het programma begon in juli 2016 en heeft de resultaten ervan gepresenteerd in talrijke publicaties, waaronder 6 papers en twee presentaties op SAMPE 2019. Het doel van RAPM, zoals uitgelegd door technische fellows van Boeing en hoofdonderzoekers Gail Hahn en Tom Tsotsis, is om "het kostenparadigma voor kleine composietonderdelen, waardoor wijdverbreid gebruik in defensietoepassingen mogelijk wordt.”
"We zijn begonnen met deze visie om lucht- en ruimtevaartprestaties te bereiken met auto-efficiëntie", zegt Hahn. Het programma werkte samen met fabrikanten van composietmaterialen en onderdelen voor auto's, waaronder Solvay Composite Materials (Alpharetta, Ga., V.S.) en SGL Composites (Ried en Ort im Innkreis, Oostenrijk), maar het bereiken van lucht- en ruimtevaarteigenschappen was niet altijd eenvoudig. "Hoewel lage-temperatuur, snel uithardende epoxy's gemakkelijk beschikbaar zijn voor automobieltoepassingen, komen ze niet in de buurt van de ruimtevaartvereisten", zegt Tsotsis. RAPM gebruikte wel nieuwe, snel uithardende, tweedelige epoxyharsen gericht op harsinfusieonderdelen van ruimtevaartkwaliteit. Aanvankelijk kon het gietsysteem bij SGL echter niet hoger zijn dan 130°C, waardoor het doel van 30 minuten time-on-tool niet werd bereikt.
"Ons doel was om een maximale werktijd van 30 minuten te bereiken om het gebruik van een hoogwaardige werkcel mogelijk te maken om de kosten op systeemniveau te verlagen om kostenconcurrerend te zijn met machinaal bewerkt aluminium", zegt Tsotsis. "Binnen Boeing hebben we besloten dat dit zou voldoen aan alles wat we zagen voor defensietoepassingen", voegt Hahn toe. “Waarom zou je het hier neerzetten als we 2 tot 6 minuten kunnen krijgen met thermoplasten? Omdat thermoplasten een nog hogere temperatuurverwerking vereisen met bijbehorende gereedschapsbeperkingen, en ons doel is om onze toeleveringsketen veel opties te geven. ”
Naarmate het programma vorderde, werd het toegankelijk voor ruimtevaartmaterialen en -fabrikanten en zelfs voor experimentele systemen, zoals Solvay's XEP-2750. "We dachten aanvankelijk dat we dit systeem volledig zouden kunnen evalueren, zoals we deden met CYCOM 5320-1 in ons werk met het DARPA-programma 'Non-Autoclave Manufacturing Technology' van 2007 tot 2012", zegt Hahn. Hoewel dezelfde mate van evaluatie niet mogelijk was, is XEP-2750 nu door Solvay op de markt gebracht als CYCOM EP-2750 (zie online zijbalk "Nieuwe prepreg voor compressievormen in RAPM ”) en profiteerde van de talrijke RAPM-deelproeven en geleerde lessen.
"Het enige dat ik wil, zijn een paar processen voor kleine composietonderdelen die het kunnen winnen van aluminium in een handelsstudie", zegt Jeff Hendrix, adviseur van de composietindustrie en TFF-programma over zijn doelen voor RAPM. Dus, is RAPM geslaagd? CW onderzoekt de inspanningen van het programma om honderden onderdelen te vervaardigen, waarbij meer dan een dozijn configuraties van lucht- en ruimtevaartonderdelen worden vergeleken door middel van meerdere materialen en processen, terwijl methoden worden nagestreefd om tijd en kosten te verminderen.
Programmakader
In samenwerking met belangrijke industriepartners heeft RAPM onderdelen uitgeprobeerd in drie hoofdtracks:
- Harsinfusie met HITCO Carbon Composites (Gardena, Californië, V.S.) en SGL Composites
- Thermoset prepreg vormen met Solvay Composite Materials (Heanor, V.K. en Anaheim, Californië, V.S.), Fiber Dynamics (Wichita, Kan., V.S.) en Reinhold Industries (Santa Fe Springs, Californië, V.S.)
- Thermoplastische vorming met ATC Manufacturing Inc. (Post Falls, Idaho, V.S.) en TxV Aero (Bristol, R.I., V.S.)
De vormingsproeven werden in twee fasen voltooid:een eerste fase van "Productieontwikkeling" (Fig. 1), gevolgd door daaropvolgende "Challenge and Transition" (C&T) onderdelen (Fig. 2) tot uitdaging eerste ontwikkelingen en overgang kandidaten met potentieel om te winnen tegen bewerkt aluminium.
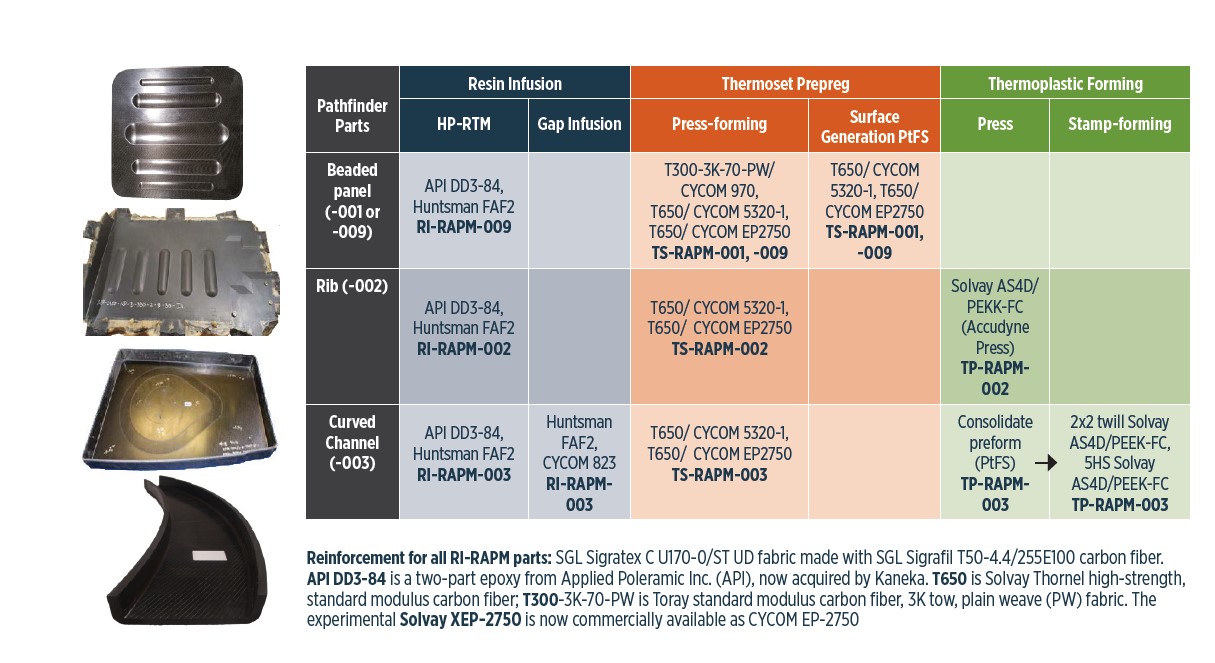
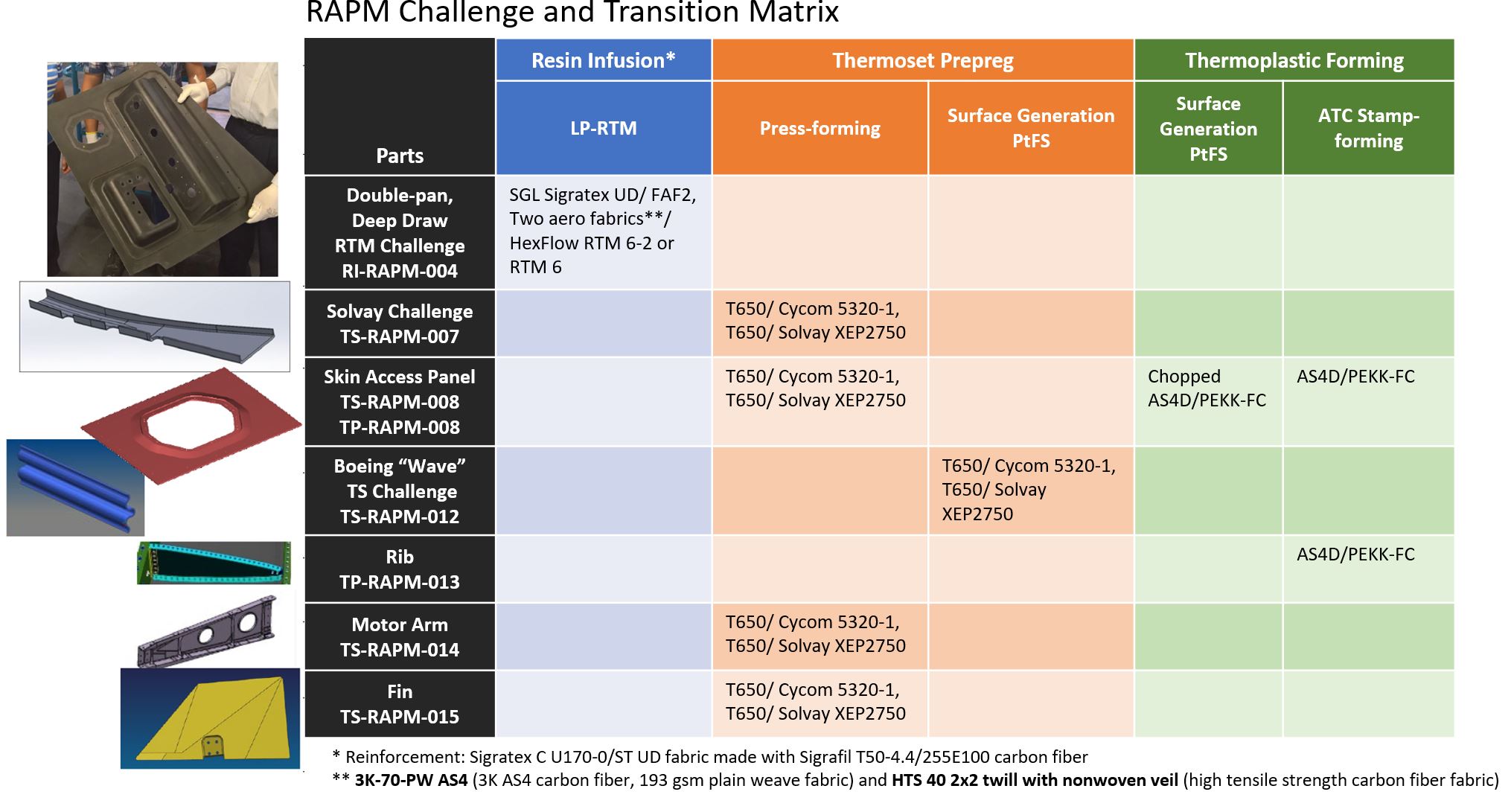
Productie-ontwikkeling proeven gebruikten drie primaire onderdeelconfiguraties:kralenpanelen (er waren twee typen), een ribbe met pad-ups (laagopbouw) en een gebogen C-kanaal. Deze ingebouwde kenmerken die gemeenschappelijk zijn voor lucht- en ruimtevaartonderdelen die fabricageproblemen kunnen veroorzaken:het kralenpaneel had meerdere buiten het vlak vallende kenmerken plus opvullingen, opvullingen en een verticale rand; het ribpaneel had een opvulling met meerdere hoeken van 90 graden en een joggle in een van de randen; en het C-kanaal had een verschillende binnen- en buitenradius, variërende kromming in de flenzen en significante laagdalingen in het web.
Het doel was om ontwerp- en fabricagerichtlijnen te ontwikkelen voor elk van de drie sporen. "Het zag er niet sexy uit tijdens deze eerste proeven", herinnert Hahn zich. "Maar ze hielpen bij het bepalen van acceptabele radii en onderdeelgeometrieën die onderdelen zouden produceren zonder ongewenste vezelvervorming en optimale combinaties van parameters zoals toegepaste spanning, temperatuur, druk en tijd op het gereedschap."
Alle drie de materiaal- en procestracks van RAPM omvatten proeven met behulp van een Surface Generation (Rutland, U.K.) Production to Functional Specification (PtFS) pixelated-heating control and tooling-systeem (zie online zijbalk "RAPM-ontwikkeling met PtFS ”), gevestigd bij Boeing R&T in St. Louis, Mo., V.S. “Dit kwam tot stand omdat we op zoek waren naar een werkcel die alle drie de soorten materialen/processen kon accommoderen in een flexibele tariefomgeving”, zegt Hahn. "We waren in staat om verschillende benaderingen en kosten van temperatuurregeling te onderzoeken." De Boeing PtFS-cel heeft een maximale temperatuur van 440 °C, een sluitkracht van 150 ton en een effectief deelvolume van 750 bij 750 bij 100 millimeter.
Hoewel de oorspronkelijke visie was om TuFF kortvezelige plaatmaterialen te gebruiken, omdat deze in het begin niet beschikbaar waren, ging RAPM door met surrogaatmaterialen. Dit is juist gunstig voor de composietenindustrie, omdat de surrogaten materialen omvatten die meer weerspiegelen wat er buiten dit project wordt gebruikt en ontwikkeld:organoplaten voor auto's en voor de ruimtevaart gekwalificeerde prepregs, experimentele epoxy's, semi-kristallijne thermoplasten en gehakte prepreg-verbindingen. De resultaten en bevindingen hebben dus betrekking op alle soorten composietfabrikanten, niet alleen op defensie.
Track 1:Harsinfusie/RTM-productie
De productie-ontwikkelingsproeven in dit traject begonnen met materialen en processen van het autotype. Onderdelen zijn gemaakt door SGL Composites met behulp van hogedruk-harstransfergieten (HP-RTM, 300 bar) en C T50 standaardmodulus, 50K koolstofvezel non-crimp weefsels (SGL Carbon in Wackersdorf, Duitsland) in driedelige configuraties:RI-RAPM-009 , RI-RAPM-002, RI-RAPM-003 (afb. 1). Deze werden gebruikt om preform-parameters te identificeren die nodig zijn voor hoogwaardige afgewerkte onderdelen. Gap-infusie (compressie-RTM of C-RTM) werd ook getest voor RI-RAPM-003 door Boeing St. Louis met behulp van zijn PtFS-systeem.
Computationele stroommodellering werd gebruikt om beter te begrijpen hoe deze onderdelen te infuseren, het procesgedrag te analyseren om materialen en procesparameters te optimaliseren en om injectiescenario's te evalueren.
Tooling-benaderingen werden geëvalueerd voor hoe en wanneer spanning moet worden toegepast op verschillende soorten voorvormgeometrieën om vezelvervorming te minimaliseren. Deze ontwerpwijzigingen werden gevalideerd voor een aangepaste C-kanaalgeometrie, gevolgd door computertomografie (CT) analyses. De geleerde lessen werden toegepast in de daaropvolgende C&T-fase, waarbij werd overgegaan op lagedruk-RTM (LP-RTM) om de kosten te verlagen.
Bij deze proeven met pathfinder-onderdelen werden delaminaties gevonden in verschillende dieptrekstralen. Tsotsis is van mening dat deze werden veroorzaakt door een combinatie van onvoldoende initiële uitharding van de hars in het gereedschap - omdat het stoomverwarmingssysteem van SGL de temperatuur in het gereedschap beperkte tot 130°C - en thermische/mechanische spanningen buiten het vlak tijdens het verwijderen van onderdelen. "Omdat de harssterkte nog niet voldoende ontwikkeld was, hadden deze anomalieën waarschijnlijk geëlimineerd kunnen worden met volledige uitharding van het gereedschap, suggereert hij. “SGL kon de tijd op tool en . niet halen lucht- en ruimtevaarteigenschappen totdat olieverwarming (in plaats van alleen stoom) aan het gereedschap werd toegevoegd, waardoor uitharding boven 130°C mogelijk werd”, merkt Hahn op. Dit is toegevoegd na de productie-ontwikkelingsproeven.
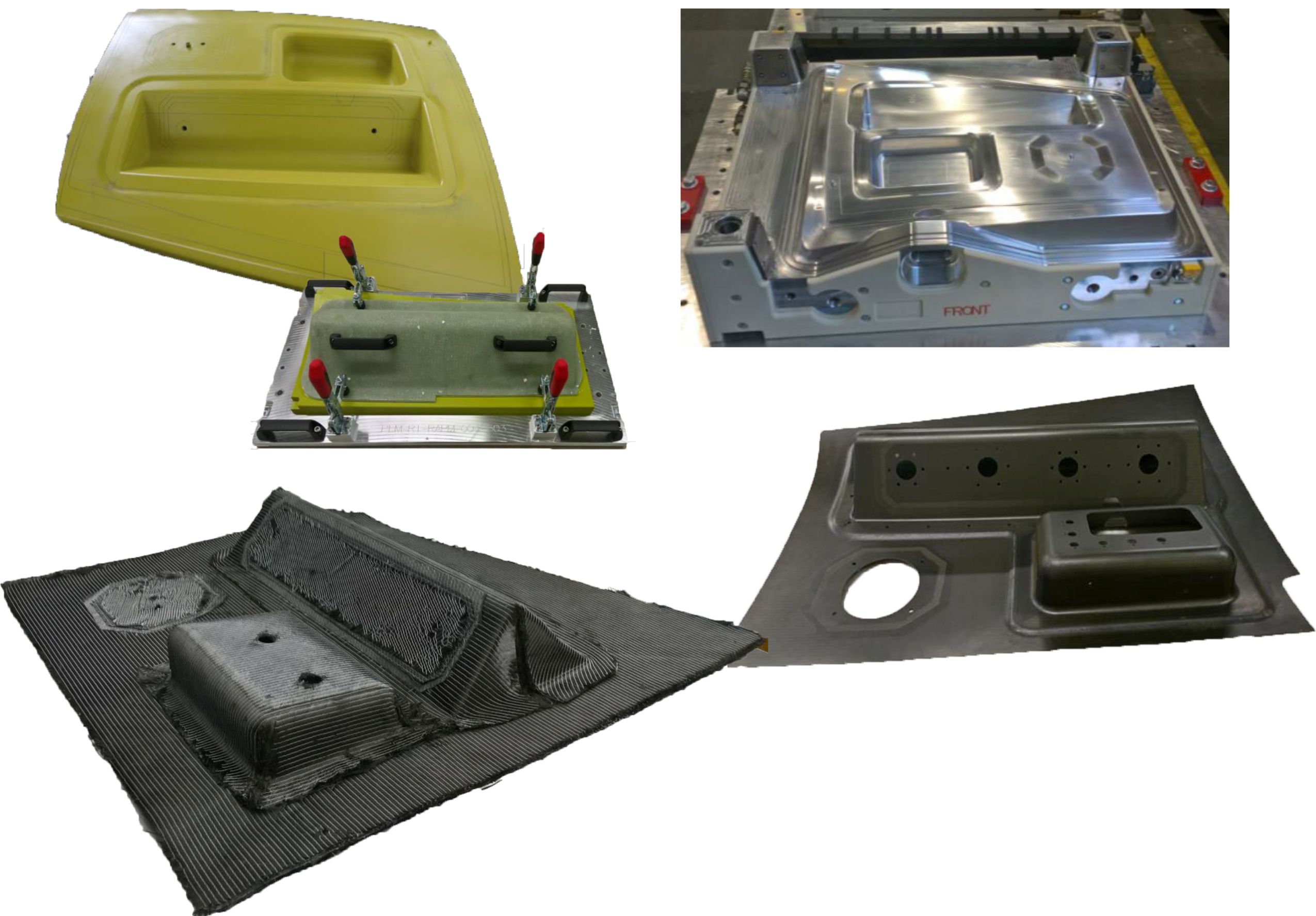
Deep-draw-uitdagingsgedeelte
De resultaten van de fabricage-ontwikkelingsproeven werden vervolgens gebruikt om uitdagings- en overgangsproeven te ontwikkelen. De modellering werd ook voltooid voor het RI-RAPM-004 dieptrekuitdagingsgedeelte (Fig. 3), dat twee diepe tekeningen bevat:een rechthoekig gebied van 5 centimeter en een gebied van 10 centimeter dat overgaat van rechthoekig naar een V-vorm. Geïnspireerd door een productiepan, zorgde de complexe geometrie voor een niet-uniform harsstroompad. Huntsman (Basel, Zwitserland) voerde de stroommodellering uit met PAM RTM-software (ESI Group, Parijs, Frankrijk) voor een LP-RTM-proces met FAF2 tweecomponenten epoxy (Huntsman, The Woodlands, Tex., VS) en SGL Carbon NCF 150 -gram per vierkante meter biaxiaal en 190 gram per vierkante meter unidirectionele (UD) versterkingen.
RI-RAPM-004 omvat één voorvorm voor de huid, één voor elk van de dieptreksecties, plus twee opbouwzones (Fig. 3). Er werden verschillende lay-ups gebruikt voor deze preform-elementen om te voldoen aan de ontworpen paneeldiktes (zie "Het vervaardigen van de complexe geometrische onderdelen van RAPM ”).
"Lage-druk voorvormen en LP-RTM maakten het gebruik van kosteneffectieve gereedschappen mogelijk (in vergelijking met staal):het voorvormgereedschap, met handbediende klemmen, werd gemaakt met op polyurethaan gebaseerd Raku-Tool-materiaal (RAMPF Tooling Solutions, Grafenberg, Duitsland); het uithardingsgereedschap is gemaakt van 5083 aluminium.
Eerste RI-RAPM-004-proeven toonden een onverwachte anomalie in de stroming bij de uitgang die de oppervlaktelagen optilde, waardoor vezelvervorming werd veroorzaakt. Het omdraaien van de in- en uitlaat loste het probleem op. Na infusie en initiële uitharding in een stuk gereedschap van 130°C, werden de onderdelen 60 minuten nagehard bij 180°C en vervolgens machinaal tot netvorm bewerkt. Er werden tien hoogwaardige onderdelen geleverd aan Boeing voor C-scans van het geautomatiseerd ultrasoon systeem (AUSS).
De afgewerkte challenge-onderdelen vertoonden volledige consolidatie, uitstekende vezeluitlijning en goede kwaliteit. De onderdelen vertoonden een glasovergangstemperatuur van 197°C en een vezelvolumefractie (FVF) van 49,5%, typisch voor de gebruikte NCF. Het aantal onderdelen voor het leggen van onderdelen werd met meer dan tweederde verminderd in vergelijking met het huidige prepreg-proces, en de aanraakarbeid daalde met naar schatting 90%. RAPM heeft ook de uitdaging gemaakt met voor de ruimtevaart gekwalificeerde harsen en stoffen - om het aanpassingsvermogen van de gereedschappen en processen die het heeft ontwikkeld te testen - en gefabriceerde onderdelen die voldoen aan de productie-eisen voor niet-destructief testen (NDT).
Spoor 2:TS prepreg vorming

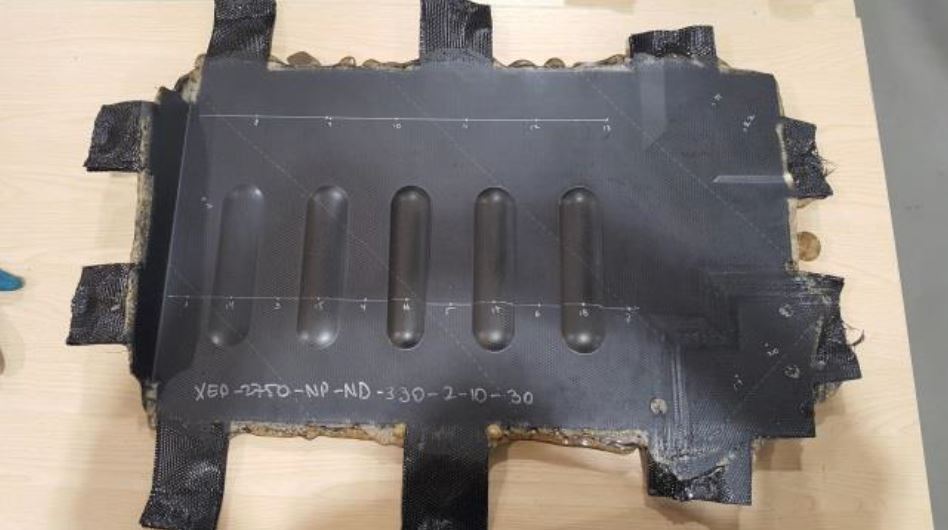
In het Solvay's Applications Center in Heanor, V.K., werden drie thermohardende (TS) prepreg-onderdelen voor fabricage-ontwikkeling vervaardigd, met gebruikmaking van stempelen met een veerframe en/of dubbele diafragmavorming (DDF). Alle drie de onderdelen zijn vervaardigd met behulp van epoxy prepregs op basis van Solvay-harsen, waaronder CYCOM 5320-1, CYCOM 970 en het CYCOM EP-2750 ruimtevaartsysteem. "CYCOM 5320-1 is onze go-to voor out-of-autoclave (OOA) onderdelen, maar het wordt ook gebruikt als een gekwalificeerd systeem voor de autoclaaf", zegt Hahn. "CYCOM 970 is een prepreg-optie met oplosmiddel versus hotmelt, en [CYCOM] EP-2750 is ons systeem voor persvormen omdat het is geoptimaliseerd voor de fysica en kinetiek van het proces, waarvan we hebben aangetoond dat het de beste onderdelen oplevert."
Stempelen met veerframes en DDF zijn isotherme compressievormprocessen waarbij thermohardende prepregs worden gesneden, verzameld en geconsolideerd tot een 2D-voorvorm. De voorvorm wordt vervolgens voorverwarmd, in bijpassende metalen gereedschappen geschoven en in vorm gegoten in een conventionele hydraulische degelpers. De voorvorm kan onder spanning worden gehouden door een veerframe (Fig. 4), waardoor de rimpels die tijdens het vormen door materiaaldrukzones worden veroorzaakt, worden verminderd. Als alternatief plaatst DDF de voorvorm tussen twee membranen, waardoor het reinigen en losmaken van de mal niet meer nodig is. De voorvorm is op een van de diafragma's geplakt, waardoor deze in wezen onder spanning wordt gehouden, maar niet zo direct of op maat gemaakt zoals bij een veerframe. In RAPM werden het veertype, de locaties en spanningen voor elk onderdeel geoptimaliseerd met behulp van simulatie, net als het veerframe. Het kralenpaneel TS-RAPM-009 gebruikte bijvoorbeeld een frame dat op en neer kan bewegen om de vorming van de lading parallel aan het sluiten van de pers aan te passen.
RAPM minimaliseerde de tijd tussen het gereedschap en het gereedschap door het verwijderen van vormstabiele onderdelen na een initiële uitharding van 15-30 minuten en vervolgens batch-uitharding om de snelheidscapaciteit te vergroten. Onderdeelfamilies werden ook onderzocht met behulp van een enkele toolset - bijvoorbeeld een C-kanaal met drie verschillende flenshoeken langs de lengte van een vleugel - om het celgebruik te maximaliseren. Andere doelen die de RAPM TS-aanpak leidden, waren onder meer:
- Geautomatiseerd sorteren en vormen om handarbeid te minimaliseren
- Mechanische prestaties in de ruimtevaart met uitharding bij 177°C
- Stalen gereedschap met een capaciteit van>1.000 onderdelen per gereedschapset.
Ontwikkeling om het uitdagingsdeel te "zwaaien"
Thermohardende prepreg-productieontwikkelingsonderdelen werden gevormd, waarbij één variabele tegelijk werd geïndexeerd, totdat voldoende onderdeelkwaliteit was bereikt. Variabelen zoals de sluitsnelheid van de pers, de sluitpositie en de sluitdruk werden beoordeeld, met als doel het materiaal op het juiste punt in de reologiecurve te consolideren om interne hydrostatische druk te creëren, harsbloeding te minimaliseren en te voorkomen dat de uitharding te ver voortgaat, om barsten te voorkomen inductie. Nadat de vormingsparameters waren ingesteld, werden drie tot vijf onderdelen gemaakt om de herhaalbaarheid van het proces te verifiëren en vervolgens op kwaliteit getest. De kralenpanelen vertoonden een porositeit van <0,5% als gevolg van hoge consolidatiedrukken (20,7 bar). Er werden ook herhaalbare ribben van hoge kwaliteit geproduceerd.
De geleerde lessen werden vervolgens toegepast op het gegolfde "golf"-uitdagingsdeel, TS-RAPM-012, om compressievormen van dikke (6,3 millimeter nominale dikte) UD-laminaten te demonstreren in vormen met een kromming met een kleine straal (12,7 millimeter). Om aan de vereisten te voldoen, gebruikte het onderdeel een quasi-isotrope lay-out van UD-tape van koolstofvezel (IM7; Hexcel; Stamford, Conn., VS). Buitenlagen van stijl 108 glasvezelweefsel en Solvay THORNEL T650 standaard modulus koolstofvezel in een satijnen stof met 8 harnassen beschermen de UD-vezels en voorkomen galvanische corrosie aan de kant die past bij een metalen onderdeel. Het gebruik van Solvay CYCOM 5320-1 epoxyhars maakte kortere (≤ 30 minuten) isotherme uithardingscycli mogelijk met een vrijstaande naharding van 2 uur bij 177°C.
Het golfuitdagingsgedeelte werd gevormd met behulp van Boeing's PtFS-werkcel en P20-stalen matrijsvlakken met geïntegreerde vacuüm- en harsafdichtingen. De gereedschapsholte was dunner dan de nominale laminaatdikte om rekening te houden met variatie in het harsgehalte van het materiaal, waardoor de interne hydrostatische druk behouden bleef voor onderdelen van hoge kwaliteit.
Er werden drie procesparameters getest, waaronder koudvervormen (voorvormen van lagen zonder warmte), hete debulk voorverdichten en voorverwarmen van de voorvorm. Koudvormen werd afgewezen als tijdrovend en niet nuttig. Voor preconsolidatie werden de laminaten in vacuümzakken op een plaat met een geweven fiberglas ontluchter verpakt en gedurende 40 minuten onder volledig vacuüm in een oven van 116°C uitgepakt. Hoewel een geautomatiseerde infraroodvoorverwarming standaard is voor industriële productie, bestond het voorverwarmen in deze proeven uit het plaatsen van de voorvorm in de hete mal (179°C) en het zoveel mogelijk sluiten zonder aanraken gedurende 3 minuten. Het onderdeel werd vervolgens geperst.
Proef 8 van de negen voltooide (#0-8) leverde het onderdeel van de hoogste kwaliteit op, voornamelijk toegeschreven aan pre-consolidatie. De monsters die eruit werden genomen, voldeden aan de dikte (een probleem met andere onderdelen) en laminaatkwaliteit met een vezelvolume van 59-63% en een leegtegehalte van 0-0,6%.
Track 3:blaasvormige TP-rib en C-kanaal
RAPM koos de TP-RAPM-002-rib uit de productie-ontwikkelingsproeven om eenstaps persgieten van grondstof tot afgewerkt complex onderdeel te demonstreren, en het TP-RAPM-003 gebogen kanaal voor een benadering in twee stappen. Boeing St. Louis vormde de -002 rib met behulp van een Accudyne Systems (Del., V.S.) pers en consolideerde blanks voor het -003 C-kanaal met behulp van de PtFS-apparatuur. In een tweede stap stampte ATC Manufacturing de C-channel blanks in onderdelen.
Voor de -002 rib gebruikte RAPM 12-inch brede UD-tape geleverd door Solvay:12K AS4D koolstofvezel (Hexcel, Stamford, Conn., V.S.) versterkt polyetherketonketon (PEKK). De -003 C-kanaal gebruikte stof van Cramer Fabrics Inc. (Dover, N.H., V.S.):3K AS4 (Hexcel) un-sized koolstofvezel in een 2x2 twill, gepoedercoat met polyetheretherketon (PEEK); vezel oppervlaktegewicht is 250 gram/vierkante meter; harsgehalte is 42%.
Thermoplastische (TP) vormingsproblemen
TP-composieten verwerken bij hogere temperaturen dan thermoharders - bijvoorbeeld 390 ° C voor PEEK en 375 ° C voor PEKK - wat een aantal problemen met zich meebrengt. Gereedschapsmaterialen die deze hoge procestemperaturen aankunnen, zijn beperkt. Verder maakt het grote temperatuurverschil tussen het verwerken en verwijderen van onderdelen het moeilijk om een uniforme gereedschapstemperatuur te handhaven. De remedie is dat warmte doordringt en/of langzamer op en neer gaat, wat de cyclustijden verlengt.
De hoge temperaturen vormen ook een uitdaging voor de thermische uitzettingscoëfficiënt (CTE). De CTE van het gereedschapsmateriaal is vaak anders dan die van het TP-laminaat, waardoor het TP-laminaat van het gereedschap kan krimpen, waardoor de uitgeoefende druk wordt verminderd en volledige consolidatie wordt voorkomen. Ook is het TP-laminaat CTE constant langs de koolstofvezel, maar een bi-lineaire curve loodrecht op de vezel. Dit resulteert in verschillende krimp in-plane vs. out-of-plane als het TP-laminaat verwarmt en afkoelt en moet ook worden aangepakt in het ontwerp van gereedschappen.
TP-laminaten kunnen ook krimpen door gereedschap, aangezien het harsvolume afneemt met de verandering van vloeibaar naar vast. Het is tijdens deze afkoelfase, wanneer kritische harsmatrixkristallisatie optreedt, dat nauwkeurige controle over temperatuuruniformiteit en laminaatdruk vereist is om hoogwaardige eigenschappen in het voltooide onderdeel te garanderen.
Een ander probleem is dat gereedschappen volledig moeten worden afgedicht om de gesmolten TP-vloeistof tijdens het vormen vast te houden. “Het afdichten van een gereedschap bij 375 °C tot 390 °C is moeilijk omdat er maar heel weinig vervormbare pakkingen zijn die deze temperatuur aankunnen en TP-vormende drukken van 300 tot 500 psi of meer”, zegt Hahn. "We zijn beperkt tot metalen pakkingen of bijpassende metalen gereedschappen om de afdichtingsfuncties te bieden. Elastomeer gereedschap zou ongelooflijk voordelig zijn, maar alle huidige elastomeren zullen afbreken bij TP-vormingstemperaturen."
Boeing St. Louis had nieuwe gereedschappen nodig om horizontale druk uit te oefenen op de verticale elementen van de ribbe tijdens consolidatie in een hydraulische pers die alleen verticale bediening had. De oplossing was een dunne aluminium blaas (een soortgelijk systeem werd gebruikt om TP-RAPM-003 te vormen, Fig. 5). Onder druk gezet met inert argongas bij hoge temperaturen, zette de blaas uit om tijdens consolidatie gelijkmatige druk uit te oefenen op alle onderdeeloppervlakken.
Boven- en ondergereedschappen zijn gemaakt van 410 roestvrij staal, wat overeenkomt met de in-plane CTE van het UD-koolstofvezel/PEKK-laminaat. Tijdens de perscyclus kwam het bovenste gereedschap met de aluminium blaas naar beneden en drukte de layup langzaam in de vrouwelijke holte van het onderste gereedschap. De blaas was 30% ondermaats ten opzichte van de uiteindelijke dikte van het onderdeel om het grootste deel van de niet-geconsolideerde tape-voorvorm in dit eenstapsproces op te nemen. Dit gereedschap was gemonteerd in een conventionele pers met elektrische verwarmingspatronen, bedraad in 12 onafhankelijk geregelde zones — plus de zes hoofdzones van de persplaat — om de oppervlaktetemperatuur van het gereedschap in de flenzen en het lijf van de ribbe te regelen.
Deze vormproeven leverden samengestelde onderdelen op met redelijke NDI-resultaten. Het ontwerp van het blaasgereedschap vereist echter verdere ontwikkeling om de vorming van de lay-up in de strakke binnenradii van het onderdeel te verbeteren en ook om een uniforme oppervlaktedikte te behouden.
Consolideren van PEEK-stof blanco's
Voor het TP-RAPM-003 gebogen C-kanaal had de gepoedercoate PEEK 2x2 twill stof die gebruikt werd een relatief hoge bulkfactor. Boeing St. Louis first consolidated the layup, which dropped from 32 to 24 plies along the length of the part, into a flat blank with a tapered cross-section, and then sent the blanks to ATC Manufacturing, which stamped the final part with vertical flanges.
As with the rib, Boeing used a forming bladder and steel top and bottom tools. The bladder was changed to AZ31 magnesium, which better resists rupture versus aluminum. The C-channel tool was designed to operate within the Surface Generation PtFS forming cell to enable more rapid heating and cooling versus the conventional press with cartridge heaters used for the rib.
The C-channel tooling approach was developed to increase flexibility for multiple parts. The layup was placed onto the bottom tool, which was heated to the material’s glass transition temperature (Tg ) to maintain pliability without melting. A volume reducing frame that included a pressure-sealing gasket was placed on top of the bottom tool, leaving a cavity slightly larger than the part layup (Fig. 5). Heat and hydraulic pressure were applied from the top tool through the bladder to the layup. Once at forming temperature, argon gas was applied to the bladder, forcing it down into the frame cavity to apply pressure to the tapered blank. The tool temperature was then increased through the melt phase of the material while maintaining bladder pressure, which prevented material from flowing across the lower tool while in melt phase.
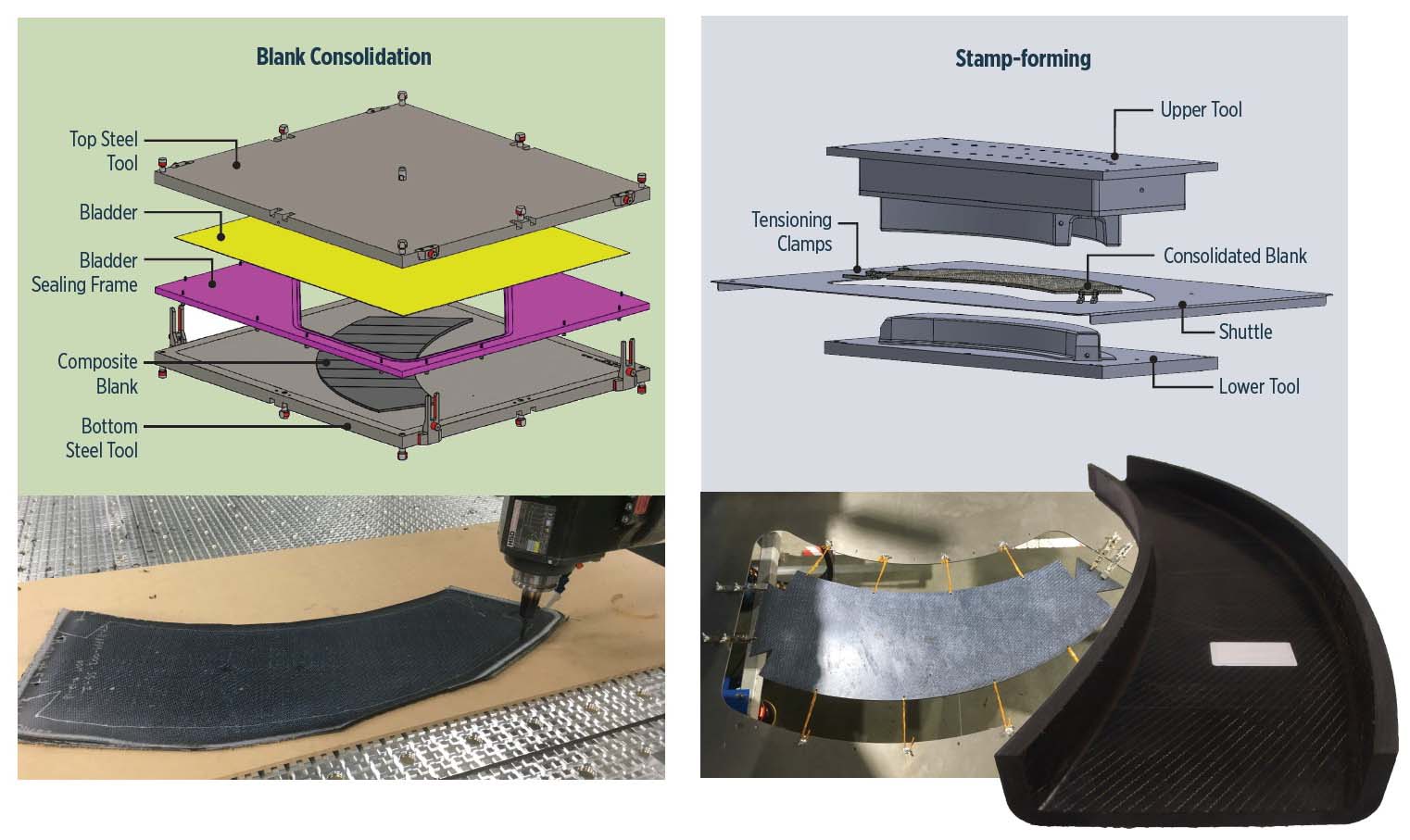
Preforming cycle time comprised 55 minutes for bladder and TP charge to reach process temperature and 30 minutes to cool below the PEEK crystallization temperature. Pressure ranged from 1.4 to 9.7 bar and was maintained manually from a high-pressure tank with a valve. With the recent incorporation of a pressclave system into the PtFS cell, autoclave-like control of vacuum and pressure (±3 psi) in the press mold cavity will be automated in the future.
TP stamp-forming
Consolidated blanks for the -003 C-channel were sent to ATC Manufacturing for stamp-forming, in which the blank is heated sufficiently above melt temperature to ensure polymer flow. It was then transferred to a rapidly closing press to form and cool the part quickly. The forming tool in the press is kept at constant temperature, enabling rapid cycle times by eliminating ramp-up and cool-down. The tool temperature must be between melt temperature and Tg to develop the required level of thermoplastic matrix crystallinity in a short time, yet ensure the part can be removed without deformation. A series of blanks with implanted thermocouples was used to validate the complete thermal cycle for stamp-forming the C-channel.
Forming simulations using Aniform software (Enschede, Netherlands) showed the highly drapable PEEK fabric blank still posed a risk of wrinkling in compression areas, namely the inner (smaller radius) flange. Thus, a tensioning system (Fig. 5) comprising shuttle plate and clips held the blank in tension as the matched metal tools closed to form it. Despite this, the flange face in compression still showed buckling as fiber was pushed inward at the inner radius. “All three RAPM tracks struggled to make this part,” Hahn contends. “Its geometry was extreme, and not so indicative of a real part, but more designed to push what we could achieve in formability.”
The manufacturing development trials led to challenge and transition parts that included multiple versions of the TP-RAPM-008 skin access panel, the TP-RAPM-013 rib with joggles on the flanges and a bladder study using three different geometries of the TP-RAPM-017 panel (Fig. 2). Boeing St. Louis produced all of these except for the TP-RAPM-013 rib, which ATC produced. “Even though this part was made with UD tape, which is typically more challenging to form versus fabric, we were able to form these parts very well,” says Trevor McCrae, R&D director for ATC Manufacturing. Overall, the TP forming trials showed that stamp-forming can produce complex geometries that might not be possible with conventional compression molding.
Learning to cut cost vs. aluminum
RAPM has demonstrated novel forming capability in all three tracks and amassed numerous lessons learned, ranging from how to position pad-ups to prevent slippage during compression molding to guidelines for part geometry to maximize quality and minimize tooling cost. “Understanding the effects of out-of-plane features, radius-to-thickness ratio and distance between geometric details becomes key as you move to small parts,” Hahn observes. “Standardizing features such as radii, curves and flange angles can help mitigate cost drivers, for example, reducing tooling costs, the number of forming trials during development and the need for multiple scans during NDI (nondestructive inspection) by enabling a standard AUSS shoe for a family of parts.”
Another cost driver RAPM highlighted was the time-consuming pre-consolidation step during TS prepreg compression molding. “Low-bulk and higher resin content prepregs widen the process window and increase repeatability for high-quality parts,” Hahn explains. “Solvay has developed a patent-pending ‘transformer film’ which can be applied to lower-impregnation prepregs before compression molding as a method of guaranteeing hydrostatic pressure in the mold cavity during consolidation.”
Although RAPM won’t officially end until fall 2020, followed by additional published results, findings so far for selected parts, which are based on real defense programs, show that composites can compete with machined aluminum (Fig. 6). Though the selected resin infusion and TP parts reduce recurring costs — e.g., materials, machine time, etc. calculated over total parts per family assuming non-recurring infrastructure is in place — the TS-RAPM-012 wave assembly actually shows a 7% increase vs. machined aluminum. However, it does achieve desired weight savings, and at a premium that is actually within the margin mandated by Hendrix:“No one is going to pay 2X for the weight savings composites offer; they must cost within 10 percent of aluminum.” However, he does concede, “There are still non-recurring time and cost issues to figure out, such as tooling and the development required to successfully form the shape.”
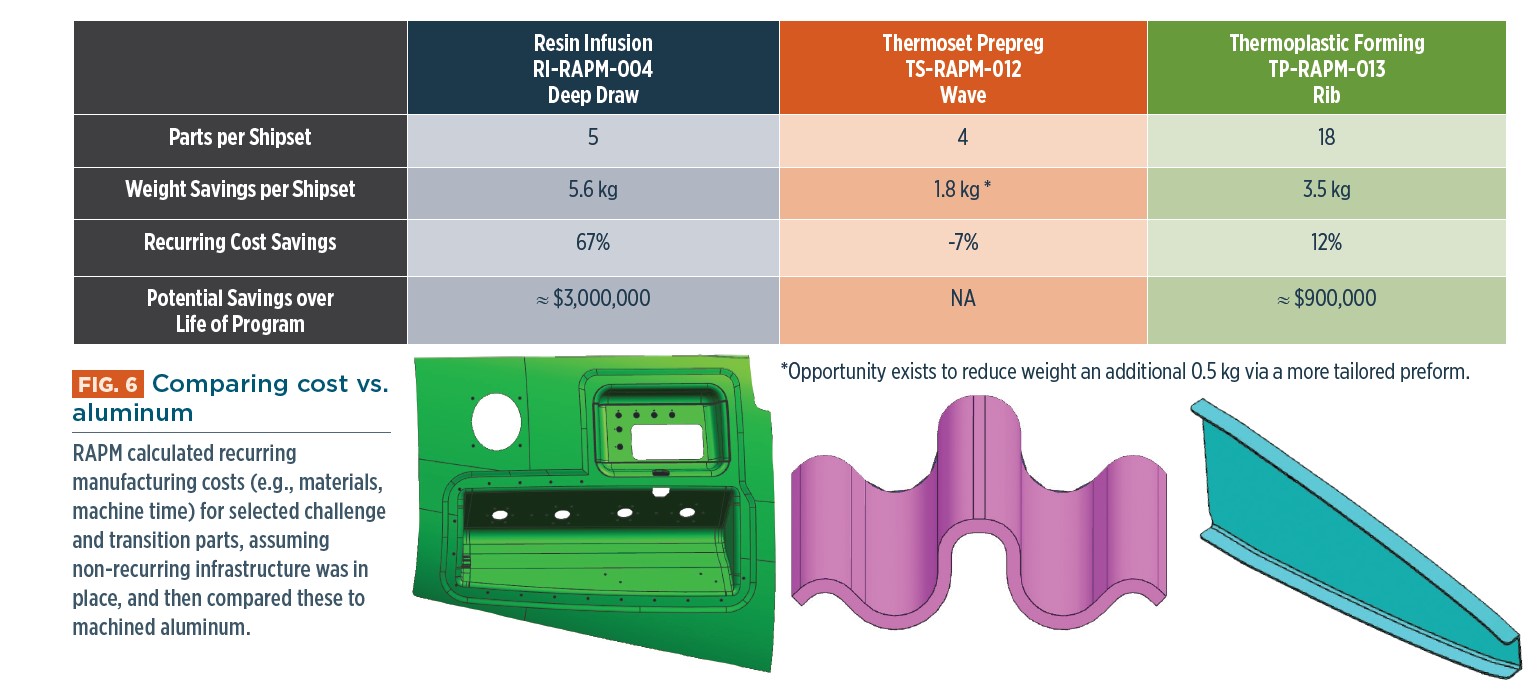
Expanding options
Although resin infusion wins for large parts, says Hahn, TS and TP stamping look pretty good for small parts. “Initial tooling cost for resin infusion is hard to overcome unless the metal parts are very complex, requiring a lot of machining,” she explains.
“Thermoplastics look good for high volume, but a subcontractor for a given program might not be set up to do thermoplastics. However, thermoset stamping might be a very good option, even for low-volume replacement parts. Because defense applications are so wide-ranging, it is important to have more than one material and process in a trade discussion.” Hahn notes that RAPM has opened up new materials and proven aerospace materials can work in automotive-type processes. “We also brought in new manufacturers.”
Hendrix agrees that RAPM’s aerospace and automotive manufacturing exchange was beneficial. Further, he was impressed with Solvay’s and SGL’s ability to form complex shapes without fiber distortion or other defects. “What it takes to make aesthetic auto parts actually has benefits,” he concedes. “You can’t have wrinkles or bad surface finish; they have to be perfect. But it still took multiple trials and significant development for them to form the RAPM parts. I’m not sure defense programs will want to invest in this non-recurring engineering if they’re dealing with small quantities. The economics will be on a case-by-case basis, but tooling and development remain issues we need to address.” Hahn adds, “We are publishing lessons learned, enabling more informed trade studies with expanded options and establishing a reasonably open basis for industry discussion.” CW will continue this discussion with an update once RAPM wraps up later this year.
Hars
- 6 manieren om de kosten van 3D-printen te verlagen
- De vraag over contractonderhoud – Deel I
- Composite fabricage:de fabricage van composietmaterialen
- De economie van 3D-printen
- Klantgedeelte van de maand
- Tracing the History of Polymeric Materials, Part 13
- De voordelen van een zakelijk palletprogramma
- ACMA lanceert Thermoplastic Composites Conference 2020-programma
- SAMPE 2018 keynote blikt op de toekomst van composieten
- De kosten van CNC-bewerking
- De waarde van investeringscasting (deel 2)