Vervaardiging van de bovenste helft van de Multifunctional Fuselage Demonstrator (MFFD)
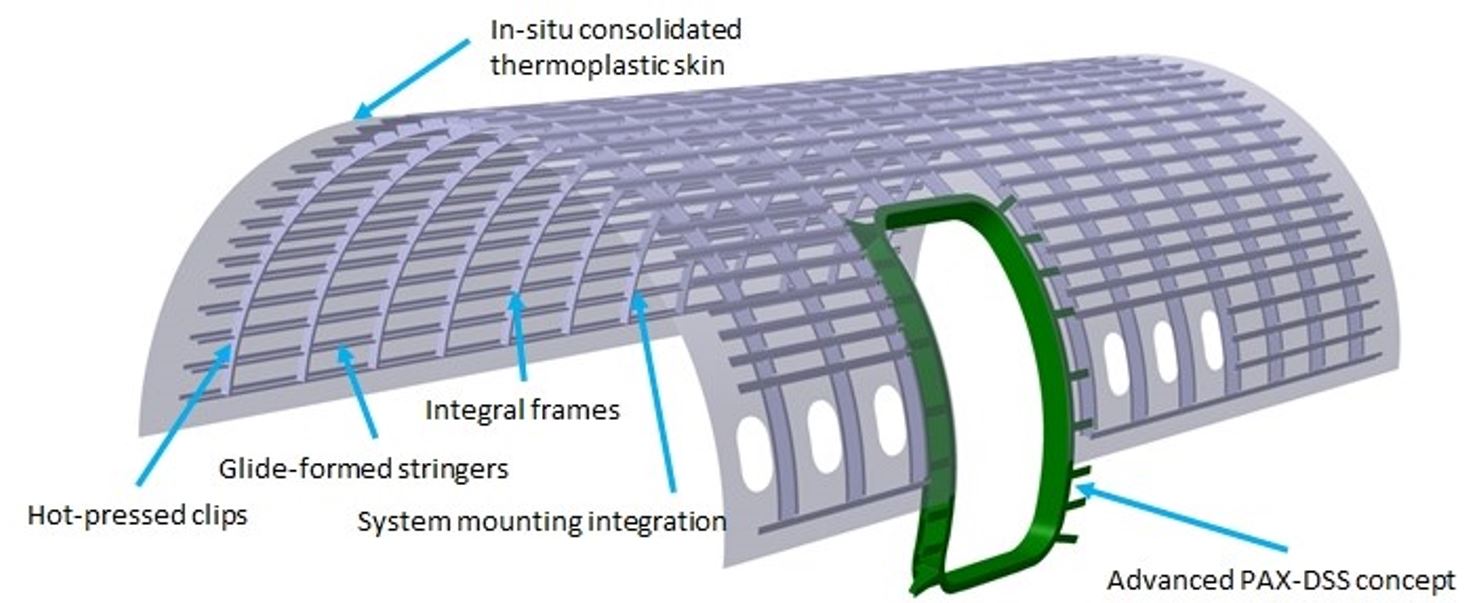
Deze blog is een vervolg op een presentatie gegeven door het German Aerospace Center (DLR, Stuttgart en Augsburg) op het TU München-symposium afgelopen najaar en CW ’s samenvatting gepubliceerd in dezelfde periode, “Moving forward on the Multifunctional Fuselage Demonstrator (MFFD)”. Het project werd ook beschreven in een presentatie gegeven door Lars Larsen om 9.35 uur op dag 3 van ITHEC 2020:"Process data-driven Advancement of robot-based, continuous ultrasonic Welding for the Dust-free Assembly of Future Fuselage Structures".
Larsen legt uit:"De grote uitdaging is om aan te tonen dat de productiekosten aanzienlijk kunnen worden verlaagd door gebruik te maken van automatisering." Voor de bovenste helft van de MFFD omvat dit in-situ consolidatie via geautomatiseerde tape-legging/vezelplaatsing (ATL/AFP) om autoclaaf en stof-/stofvrij lassen voor montage te vermijden. "Dit moet het mogelijk maken om in de toekomst de volgorde van component- en eindassemblagelijnen te veranderen", zegt Larsen, "waardoor systemen voor kunnen worden geïntegreerd bijeenkomst." Dit komt omdat, in tegenstelling tot het bewerken van bevestigingsgaten, lassen geen spanen of vuil produceert die vooraf geïnstalleerde systemen kunnen beschadigen, zoals gedistribueerde elektrische stroom, binneninrichting, enz.
Deze blog is gebaseerd op mijn interview met Sebastian Nowotny, hoofd van componentontwerp- en fabricagetechnologieën bij het DLR Institute of Structures and Design (BT, Stuttgart) en Frederic Fischer, technisch leider voor de productie van thermoplastische composieten bij het DLR Center for Lightweight Production Technology ( ZLP, Augsburg). Fischer is ook de projectmanager voor de bovenste helft van de MFFD bij DLR.
OPMERKING:In de bovenstaande afbeelding verwijst glijdende stringers naar een proces dat is ontwikkeld in Clean Sky 2 door Applus+ Labaoratories (Barcelona, Spanje), zie mijn blog van 2017 over glijvormen, en heetgeperste clips verwijzen naar stempelen, zie:
- Versnellen van thermoplastische composieten in de ruimtevaart
- Thermoplastische composieten "knippen" tijd, arbeid op kleine maar cruciale onderdelen
- Binnen een broeinest van thermoplastische composieten
Structuur, cabine en systemen combineren
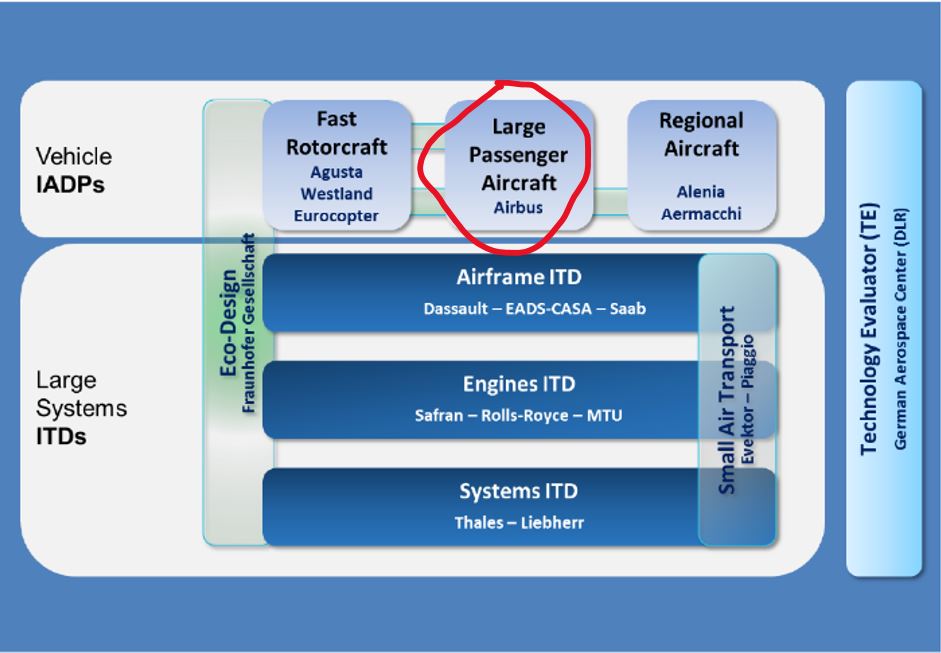
Ik vroeg Nowotny naar de geschiedenis van de bovenste helft van de MFFD. "Toen Clean Sky 2 begon, werd de eerste oproep tot het indienen van voorstellen gedaan", antwoordt hij. “Ik denk dat we in 2015 zijn begonnen en we hebben de aanbesteding gewonnen voor het project ICASUS, dat een co-partnerproject was voor het programma voor grote passagiersvliegtuigen (LPA). De belangrijkste focus lag op het ontwerp van een multifunctionele romp. In die tijd was het geen thermoplastisch composiet. Het belangrijkste doel was om de romp, de cabine, de systemen en de structuur te combineren in één ontwerpproces. Dus eigenlijk is het werk dat daar is gedaan wat nu de multifunctionele rompdemonstrator (MFFD) is geworden en het is de technologische ondersteuning voor ons werk in het bovenschilproject."
ICASUS
Het ICASUS-project heeft tot doel multifunctionele en sterk geïntegreerde oplossingen te ontwikkelen voor de volgende generatie multifunctionele romp, cabine en systeemgeïntegreerde romp. Tegenwoordig wordt het fabricage- en assemblageproces voor vliegtuigen met één gangpad aangedreven door dure en tijdrovende opeenvolgende stappen. Vooral de assemblage van de belangrijkste componenten (MCA) en de eindassemblagelijn (FAL) zijn knelpunten die snellere en versnelde processen in de weg staan. Om deze reden zal ICASUS een nieuw concept ontwikkelen voor de productie en assemblage van toekomstige vliegtuigen met één gangpad die gericht zijn op:
- Hoge productie van 60 vliegtuigen/maand;
- Krompen terugkerende kostenbesparing van € 1 miljoen in vergelijking met de referentie A321 ACF ("Advanced Cabin Flex");
- Fuselage gewichtsvermindering van 1 metrische ton ten opzichte van de A321 ACF.
De aanpak zal zijn om de oorspronkelijk autarkische disciplines cabine/vracht, systemen en structuur te combineren om te komen tot de meest veelbelovende combinatie en integratie van de respectieve functies en vereisten. Dit moet worden bereikt door het gebruik van geavanceerde materialen en het toepassen van innovatieve ontwerpprincipes in combinatie met de meest geavanceerde systeemarchitectuur in combinatie met de volgende generatie cabine.
De belangrijkste drijfveer is om het brandstofverbruik aanzienlijk te verminderen door lichtgewicht systemen en systeemarchitectuur/-integratie toe te passen. Dit vereist een multidisciplinaire algemene optimalisatieprocedure, evenals de ontwikkeling en toepassing van een holistische Industry 4.0-aanpak. Ontwerp voor geautomatiseerde productie, automatisering, sensorisatie, gegevensanalyse en veilige gegevensuitwisseling moet worden gebruikt. Belangrijke doelstellingen van de fabricage van de MFFD zijn onder meer verificatie van kosteneffectieve en grootschalige productie van multifunctionele composietstructuren en bijdragen aan certificeringsconcepten voor thermoplastische CFRP-verbindingen (bijv. lassen).
Hoe combineer je de romp, de systemen en de structuur in één? “Je zou nog steeds die disciplines hebben met hun respectievelijke eisen, maar ik denk dat het belangrijkste doel de aanpak is om al in een vroeg stadium samen te werken”, legt Nowotny uit. “Er zijn strikte regels geweest voor het ontwerpproces van de vliegtuigromp die beperkingen hebben gecreëerd en een volledig geoptimaliseerd vliegtuigontwerp hebben verhinderd. Het oorspronkelijke idee om structuur, cabine en systemen te combineren, was om een ontwerpproces te hebben dat deze drie aspecten samenbrengt en vervolgens probeert het globale optimum te vinden, niet eerst één voor de cabine en dan één voor de structuur en vervolgens één voor de systemen . Maar er zijn natuurlijk veel regels en dit is geen eenvoudig proces omdat er ook certificering bij komt kijken.”
"Het is een continu proces, in die zin dat er een digitaal platform is opgezet en alle Europese partners input leveren voor dat ene digitale ontwerp", zegt Fischer. “Het bevorderen van dit geïntegreerde ontwerp voor de MFFD is wat er de afgelopen jaren is gebeurd. Ons team levert de bovenste helft met voorzieningen voor cabine en systeembevestiging. De visie is om een revolutie teweeg te brengen in de eindmontage door volledig uitgeruste belangrijke componenten te leveren.”
Hoewel DLR al deel uitmaakte van het ontwerpproject voor MFFD, kreeg het pas in 2019 definitief groen licht voor het productieproject. Het consortium om de bovenste helft te bouwen bestaat uit Airbus als de algehele MFFD-projectleider, Premium Aerotec (Augsburg, Duitsland ) als leider in industrieel en structureel ontwerp en leverancier van de frames, Aernnova (Vitoria-Gasteiz, Spanje) om de stringers te produceren en DLR als lead voor de huidlay-up en de ontwikkeling van lastechnologie. Het afgelopen jaar, zegt Fischer, "hebben we het ontwerp van de bovenste helft verfijnd om ervoor te zorgen dat het kan worden vervaardigd met de geselecteerde technologieën."
In-situ consolidatie
Terwijl de onderste helft van de MFFD wordt geproduceerd met ATL en AFP gevolgd door autoclaafconsolidatie, zal de bovenste helft in-situ consolidatie gebruiken tijdens ATL/AFP. Waarom? "Om maximale output van het onderzoeksproject te hebben, hebben we ervoor gekozen om de baseline uit te dagen", zegt Fischer, "en gebruik te maken van de mogelijkheid om een technologie te gebruiken als aanvulling op de onderste helft." Nowotny voegt toe:“We hebben laten zien dat het een veelbelovende productiemethode is die zich richt op een slanke productie die de productiestappen vermindert. Maar ik denk dat het duidelijk is dat er niet één enkele productiemethode is die alle doelen dient. Je moet nog steeds per geval beslissen wat het optimale productieproces is voor elk onderdeel.”
Twee soorten lassen
Een andere keuze voor de bovenste helft was het gebruik van twee verschillende lastechnologieën. "We gebruiken robotgebaseerd continu ultrasoon lassen voor de stringers, omdat dat naar onze mening de meest geschikte technologie is voor echt lange verbindingen, en vooral voor de stringerconfiguratie", legt Fischer uit. Voor de integratie van de rompframes is gekozen voor weerstandslassen. “Deze keuzes zijn het resultaat van intensieve analyses die we in het begin van het project hebben gehad, samen met Premium Aerotec. We hebben gekeken naar de verschillende lasscenario's, wat er moest worden samengevoegd en waar.”
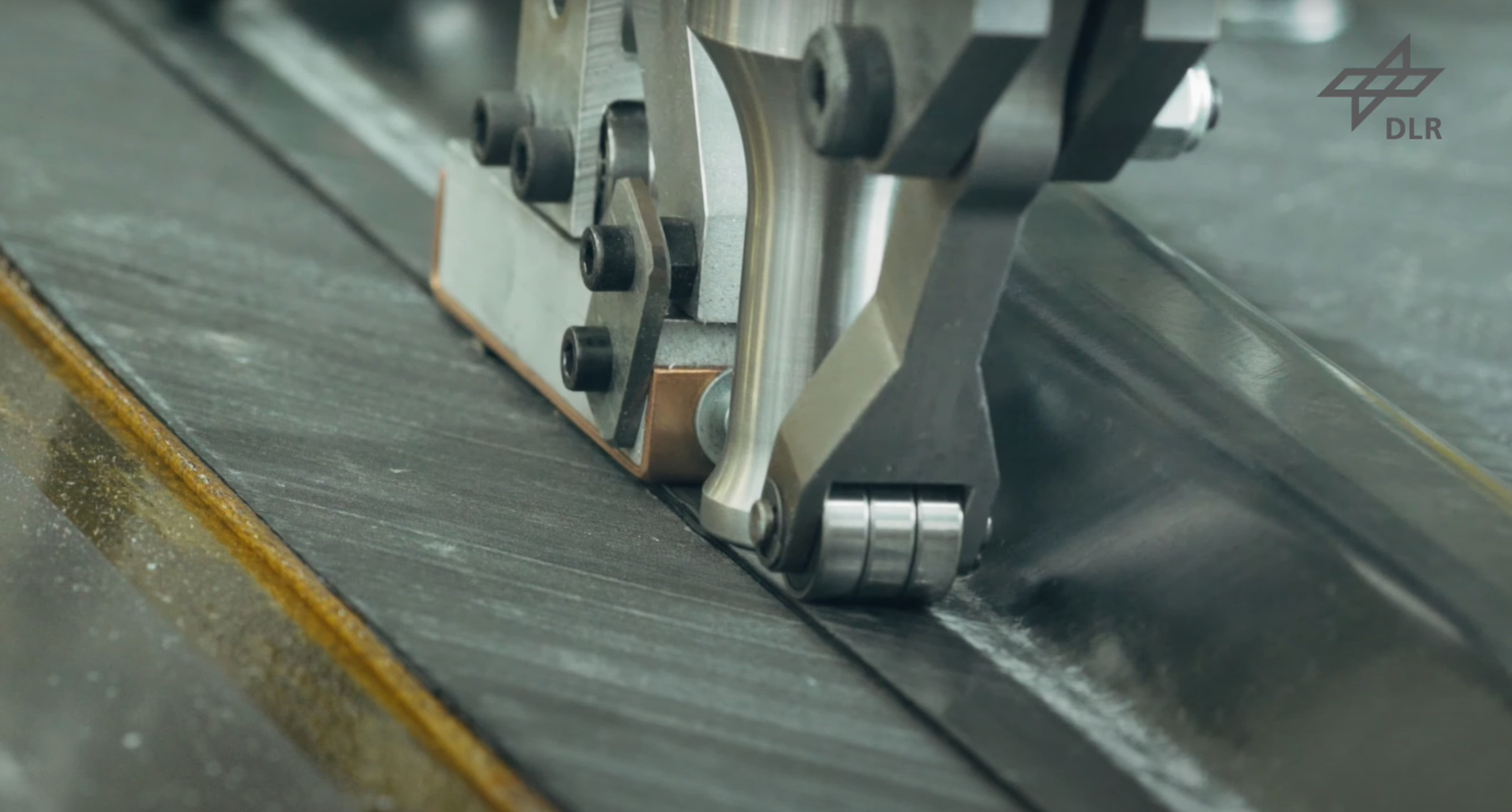
Het door DLR ontwikkelde continu ultrasoon lassen maakt gebruik van een standaard industriële robot. De laseindeffector bestaat uit een voorlopende rol, een sonotrode met een diameter van 25 millimeter en een volgende verdichtingseenheid. De eindeffector is uitgerust met meerdere sensoren, wat inline procesbewaking mogelijk maakt. Door de robot als manipulator te gebruiken, zoals te zien is in onderstaande video, kunnen verschillende geometrieën worden gelast, zoals een gebogen achterste drukschot of omega-stringers op een huid.
"Dus we hebben twee processen met één groot verschil", merkt Fischer op. “Eén is een continue proces en de andere is een discontinue werkwijze. Voor de 8 meter lange verbindingen van de Z-stringers kozen we voor continu ultrasoon lassen. En voor de zeer complexe use-case - in termen van toegankelijkheid en tolerantiebeheer - om de bevestigde flenzen van de frames aan de huid te lassen, kozen we voor weerstandslassen. We zullen het weerstandslaselement passen en vooraf uitrusten met de framegeometrie en een klemachtig lasapparaat hebben dat pneumatisch sluit, contact maakt met de laselementen en vervolgens het lasproces activeert."
Nowotny merkt op dat weerstandslassen de hoogste maturiteit en hogere sterkte heeft, wat goed overeenkomt met de hogere belasting die wordt gezien in de verbindingen tussen de frames en de schoenplaatjes. Hij wijst erop dat dit proces het frame aan de huid lassen en las de schoenplaat zowel aan het frame als aan de stringer.
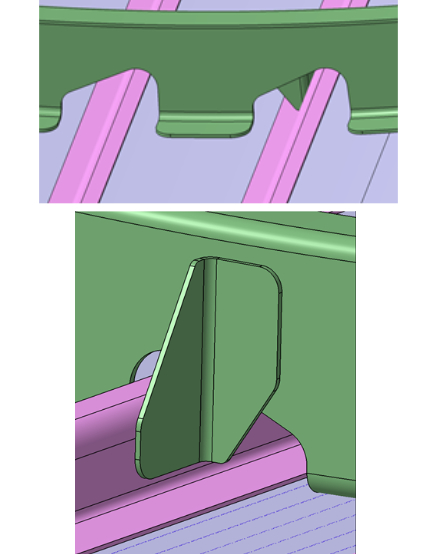
"We toonden de clipintegratie op generieke onderdelen op JEC 2017", zegt Fischer. Nowotny voegt toe:"En we hadden in 2005-2008 het project HISYS met de highlift-afdeling van Airbus Bremen voor weerstandslassen met PEEK (polyetheretherketon) thermoplast. We hebben het hele proces voor het lassen van de ribben in de huid tot TRL 5 gebracht. De basis van het proces is dus vrij goed begrepen, en we kunnen ons nu vooral concentreren op de aanpassing, automatisering en robuustheid van het proces.”
“ Een van de belangrijkste factoren voor verschillende lastechnologieën - ook al bestaan ze al heel lang - is om te laten zien dat ze klaar zijn voor commerciële toepassing in de industrie", benadrukt Fischer, "inclusief de noodzakelijke automatisering, programmering en kwaliteitsborging . Een van de belangrijkste kwesties waar we naar kijken, is hoe te weten of de las goed is. We willen er zeker van zijn dat we de procesgegevens hebben om aan te tonen dat we weten dat de las op lange termijn zal presteren en dat we niet vragen om een volgende NDT-controle met ultrasoon, of een andere algehele inspectie in de voltooide assemblage. Een van onze hoofddoelen in dit project is dus het ontwikkelen van industriële kwaliteitsborging.”
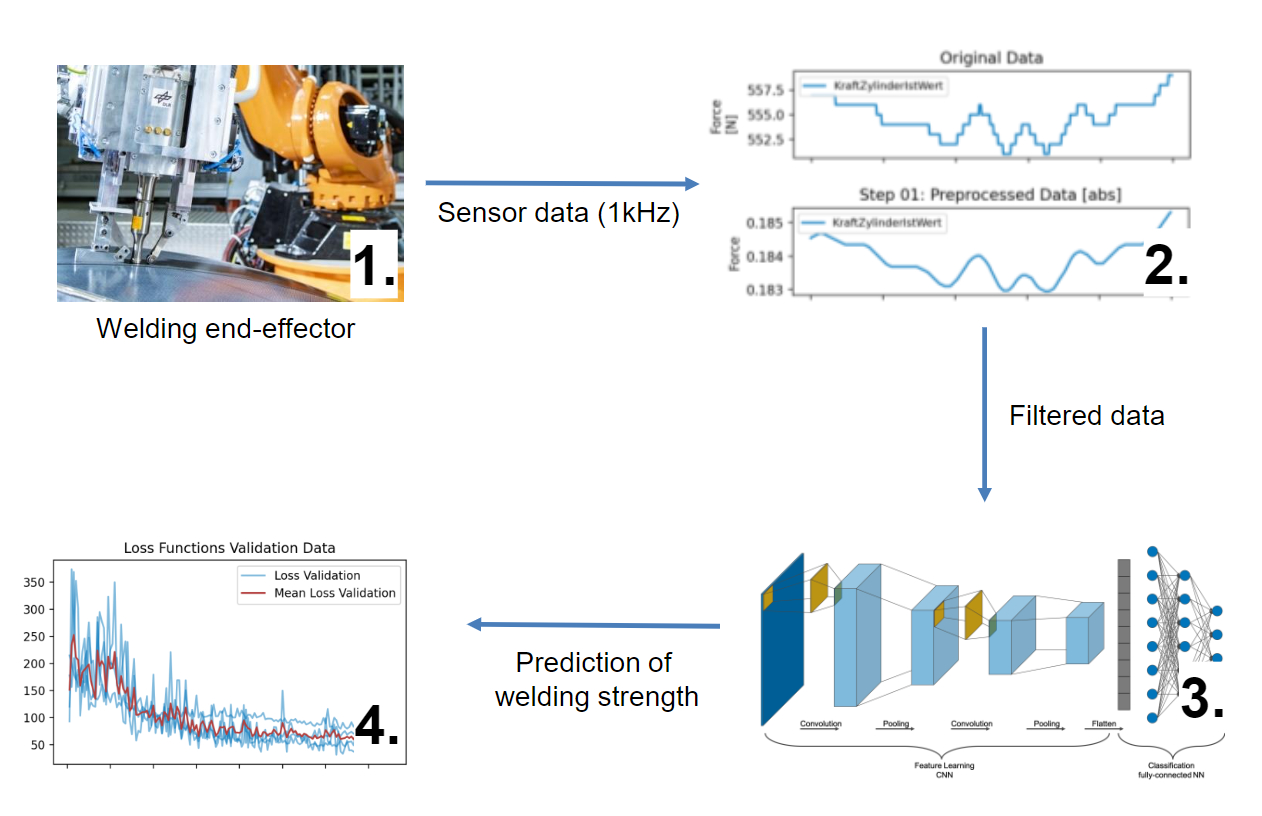
Draaien naar LM PAEK
Zoals uitgelegd in mijn blog, "Beproeving van LM PAEK-lassen voor demonstrator voor multifunctionele rompen", hoewel de MFFD begon met koolstofvezel/PEKK (polyetherketonketon), was het basismateriaal bij de 10e oproep tot het indienen van voorstellen (CFP10) in maart 2019 overgestapt op koolstofvezel/PAEK (polyaryletherketon). PAEK is de algemene familie van polymeren waarbinnen PEEK, PEKK en LM PAEK zich bevinden. Hoeveel ervaring heeft de bovenste helft van het team met LM PAEK? "We hebben het al voor een aantal productieproeven gebruikt", zegt Fischer. “De materiaalprestaties zijn veelbelovend voor zowel ultrasoon als weerstandslassen. Toch is het materiaal in ontwikkeling en is er een proces van gemeenschappelijke uitwisseling in termen van geleerde lessen en ontwikkeling van verwerkingsrichtlijnen opgezet tussen alle Europese partners en de materiaalleverancier.”
“ Maar,” voegt Nowotny toe, “ik denk dat het een goede zaak is dat we deze materiaalkeuzes nu hebben, want vele jaren geleden was er alleen Cytec APC-2, en niets anders. Vooral in Europa kon je soms het materiaal krijgen en soms kreeg je 'nee, sorry'. Inmiddels hebben we meerdere materiaalleveranciers die actief aan de materialen werken, maar ook aan de verschillende processen. Victrex, zoals we hebben gezien tijdens het symposium van de TU München in 2020, kijkt nu naar optimalisatie voor additive manufacturing. Er is ook wat werk aan de gang met optimalisatie voor AFP in-situ consolidatie, en wat voor secundaire consolidatie met behulp van een autoclaaf en verschillende productieprocessen buiten de autoclaaf (OOA). Er gebeurt nu dus veel meer en dit vergroot de kans op een goed materiaal voor elk proces.”
Tijdlijn en volgende stappen
"We zijn in feite klaar met het ontwerpproductieproces voor een tussenliggende demonstrator - A320-diameter met twee framevakken en een breedte van 950 millimeter - en we zullen die kleinere halve schaal begin volgend jaar (2021) bouwen", zegt Fischer . “Afgezien daarvan zijn we begonnen met de aanschaf van de tooling voor de volledige bovenste helft van de schaal, en we voeren onze technologieën op om ervoor te zorgen dat we in 2022 de volledige bovenste helft op tijd kunnen produceren. .”
Wat houdt dit in? Een probleem zijn montagetoleranties. "De langsnaden langs de linker- en rechterkant van zowel de bovenste als de onderste romphelften zijn al enige tijd ontworpen", legt Fischer uit. "Hiervan hebben we bepaalde vereisten en we moeten ervoor zorgen dat onze productietoleranties aan die vereisten voldoen."
"Het basisverhaal van wat we met de bovenschaal proberen te doen, is om de meest efficiënte routes voor de productie van thermoplastische composieten te demonstreren en een manier te vinden die kan concurreren met aluminium voor toekomstige vliegtuigen", zegt Fischer. Hij merkt op dat DLR dit al heeft laten zien in zijn werk met Premium Aerotec om een gelast thermoplastisch achterdrukschot te ontwikkelen, getoond in 2018 en 2019 (zie ook "Nieuwe horizonten in het lassen van thermoplastische composieten"). Lassen en slanke productie zijn belangrijke factoren voor thermoplasten. En nu moeten we deze technologieën uit het laboratorium en in de industrie krijgen. En om industrieën te laten geloven dat ze deze lastechnologieën echt kunnen gebruiken, moeten we laten zien dat ze kunnen worden geautomatiseerd, voorspelbaar en gecontroleerd voor betrouwbaarheid in echte productietaken. En dat is wat we doen.”
Hars
- De voordelen van productie op korte termijn
- Zijn organische materialen de toekomst van de kunststofproductie?
- Hoe u de beste leverancier voor kunststofproductie kiest
- Assemblagerobots 101:het wat, waar en hoe van assemblagerobots in de productie
- Het laatste nieuws op het gebied van productie-reshoring
- 15 feiten over productie in de VS
- De rol van blockchain in productie
- De 8 verspillingen van Lean Manufacturing
- Wat zit er in het productieproces?
- De toekomst van 3D-printen in de maakindustrie
- Is 3D-printen de toekomst van productie?