Versnelde RTM met warmtestroomsensoren
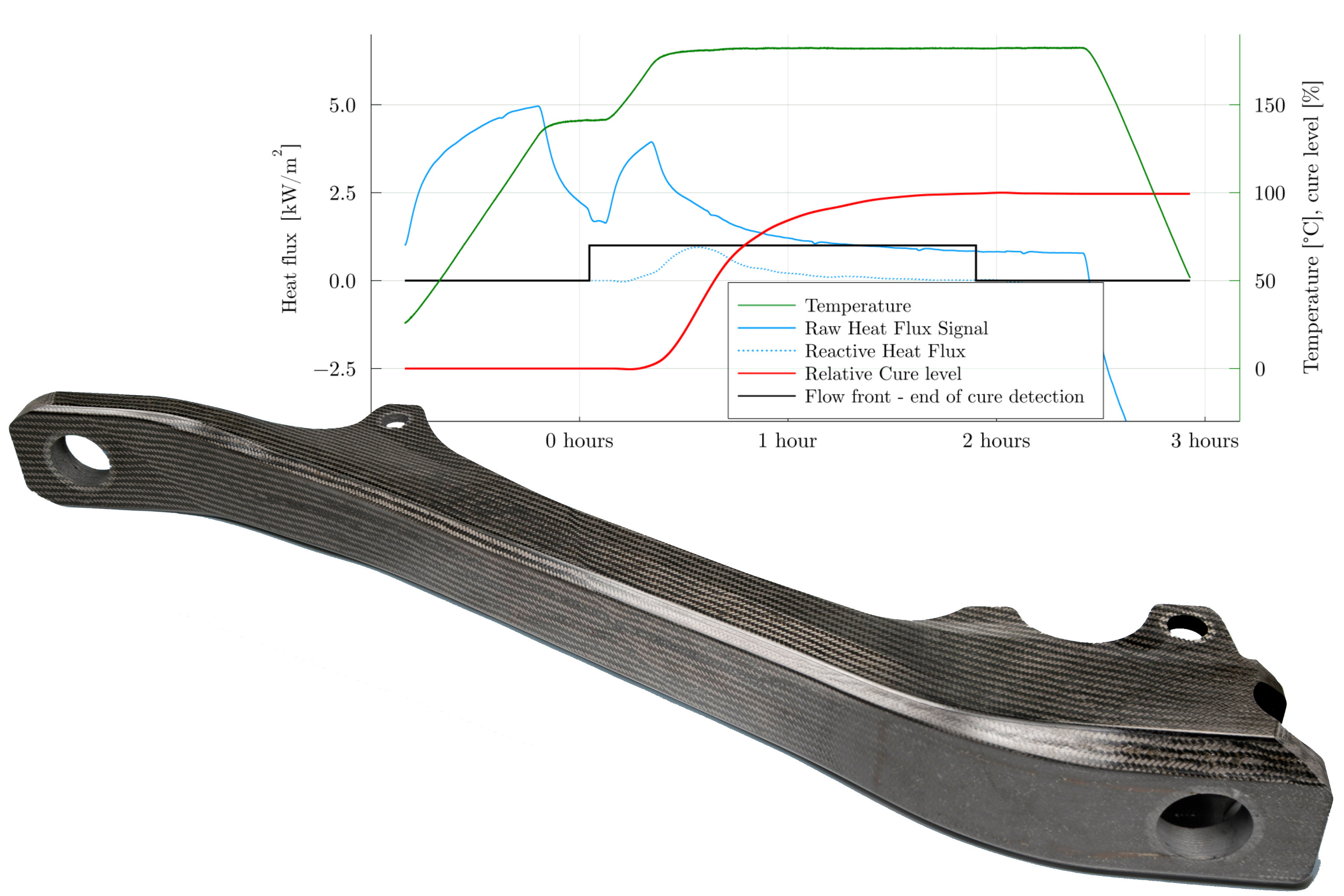
Landingsgestellen, die 3-5% van het gewicht van een vliegtuig uitmaken, zijn al lang het doelwit van gewichtsvermindering om de efficiëntie van vliegtuigen te verbeteren. Dit is nog kritischer geworden met de aanstaande overstap naar energie- en emissiereducerende elektrische aandrijfsystemen.
Safran Landing Systems (Vélizy, Frankrijk) zal bijvoorbeeld motoren-off, elektrisch taxiën mogelijk maken via elektromotoren die zijn geïntegreerd in de landingsgestellen van vliegtuigen, waardoor NOx, CO2 wordt verminderd. , CO en onverbrande koolwaterstoffen met respectievelijk 51%, 61%, 73% en 62%. Dit is een enorme overwinning voor een duurzamere luchtvaart, maar elektrische motoren hebben stroom nodig en de batterijen die nodig zijn om die stroom te leveren zijn zwaar.
De vraag naar lichtgewicht landingsgestelstructuren lijkt dus perfect te passen bij het toepassen van composieten, op één punt na. "Omdat het landingsgestel een structuur met een enkelvoudig laadpad is, kan het falen van een structureel onderdeel leiden tot een ernstige noodlanding", zegt Peet Vergouwen, technoloog bij GKN Fokker Landing Gear (Helmond, Nederland). GKN Fokker Landing Gear heeft meer dan een decennium gewerkt aan het demonstreren van de technische haalbaarheid van composiet landingsgestelstructuren, inclusief de ontwikkeling van koolstofvezelversterkte polymeer (CFRP) sleepsteunen voor de F-35 Lightning II . "Vanwege hun kritieke karakter behoren landingsgestelstructuren tot de meest conservatieve in commerciële vliegtuigen." Daarom zijn ze meestal gemaakt van metalen met een hoge sterkte.
Dat tij begint echter te keren. Clean Sky 2 streeft naar een gewichtsreductie van 30%, maar via CFRP-componenten in het HECOLAG-project (High Efficiency Composites LAnding Gear), voor twee toepassingen. In de eerste toepassing werd een CFRP-alternatief ontwikkeld voor de bestaande aluminium bovenste sleepstang voor het A350-1000 neuslandingsgestel, oorspronkelijk ontwikkeld en vervaardigd door Liebherr-Aerospace (Lindenberg, Duitsland). HECOLAG-partners Koninklijk Nederlands Lucht- en Ruimtevaartcentrum (NLR, Marknesse) en GKN Fokker Landing Gear hebben deze CFRP-sleepstang ontworpen volgens de Liebherr-vereisten. Met behulp van in-house ontwikkelde geautomatiseerde preforming-technologie heeft het NLR functionele prototypes gebouwd van de CFRP-sleepstang, die zijn getest door GKN Fokker Landing Gear.
In de tweede applicatie die wordt geëvalueerd door HECOLAG, hebben NLR en GKN Fokker Landing Gear ook een CFRP onderste zijsteun ontwikkeld in combinatie met Safran Landing Systems voor het geëlektrificeerde hoofdlandingsgestel. CW zal later in 2021 specifiek rapporteren over de algemene resultaten van het HECOLAG-project, maar hier ligt de nadruk op het INNOTOOL 4.0-subproject, geleid door topicmanager GKN Fokker Landing Gear om de sterk geautomatiseerde productie van CFRP-landingsgestelstructuren te bevorderen met behulp van resin transfer molding (RTM) . INNOTOOL 4.0 wil met name sensorgeïntegreerde tooling demonstreren die de weg zal banen naar kleinere tools met minder massa voor snellere productiecycli, eenvoudigere hantering en lager energieverbruik, evenals verhoogde automatisering voor lagere kosten en composiet 4.0-intelligente procescontrole. Het INNOTOOL 4.0-project wordt gefinancierd door de gemeenschappelijke onderneming Clean Sky 2 in het kader van het onderzoeks- en innovatieprogramma Horizon van de EU onder GAP-nr. 821261.
INNOTOOL 4.0-doelen
De demonstrator voor dit tweede deel van HECOLAG (zie openingsafbeelding) is meer een generiek deel, legt Vergouwen uit. "Het is bedoeld voor het demonstreren van ontwerp-, simulatie- en fabricagemethoden voor onderdelen die de prestaties, productiesnelheid en kosten zullen bieden die nodig zijn voor vliegtuigen met één gangpad." Tegen het einde van 2017 had het HECOLAG-consortium het eerste CFRP-demonstratieonderdeel en productiegereedschap gedefinieerd, het thermisch gedrag van het gereedschap geanalyseerd en prestatietests uitgevoerd. Dit grote en complexe product doorstond de voorlopige ontwerpbeoordeling en bereikte later dat jaar een technologiegereedheidsniveau (TRL) van 4. “Op basis van de problemen en lessen die we uit die eerste demonstrator leerden, waren we op zoek naar partners om RTM-toolingtechnologie te ontwikkelen om de uithardingscyclus te optimaliseren en te verkorten”, zegt Vergouwen. Een Clean Sky 2 Call for Partners werd in 2018 uitgegeven en werd toegekend aan het INNOTOOL 4.0-consortium, bestaande uit apparatuur- en automatiseringsleverancier Techni-Modul Engineering (TME, Coudes, Frankrijk) en harsinjectiespecialist Isojet Equipements (Corbas, Frankrijk). Ze begonnen te werken in april 2019 en voltooiden de eerste mijlpalen in maart 2021.
“Het composietdeel moet kostenconcurrerend zijn met gesmeed staal en aluminium”, merkt Vergouwen op bij GKN Fokker Landing Gear. "Dat is alleen mogelijk met automatisering, waardoor een zeer laag aantal arbeidsuren en goedkopere materialen mogelijk zijn dan het huidige autoclaaf-uitgeharde CFRP van luchtvaartkwaliteit."
Daarom probeerde INNOTOOL 4.0 sensoren te integreren in de RTM-tooling die de injectie- en uithardingsprocessen zullen bewaken en beheren, inclusief detectie van de harsstroomfront. "Het doel is om volledig geautomatiseerd te zijn - laad de voorvorm, druk op een knop en de vormapparatuur regelt de temperatuur, druk, vacuüm en uitharding", zegt Stéphane Besson, commercieel directeur bij TME. Dit is echter de eerste keer dat GKN Fokker Landing Gear en TME werken met cure-monitoring. "We hebben eerder met temperatuur- en druksensoren gewerkt", zegt Besson, "maar niet met sensoren voor harsstroom en polymerisatie."
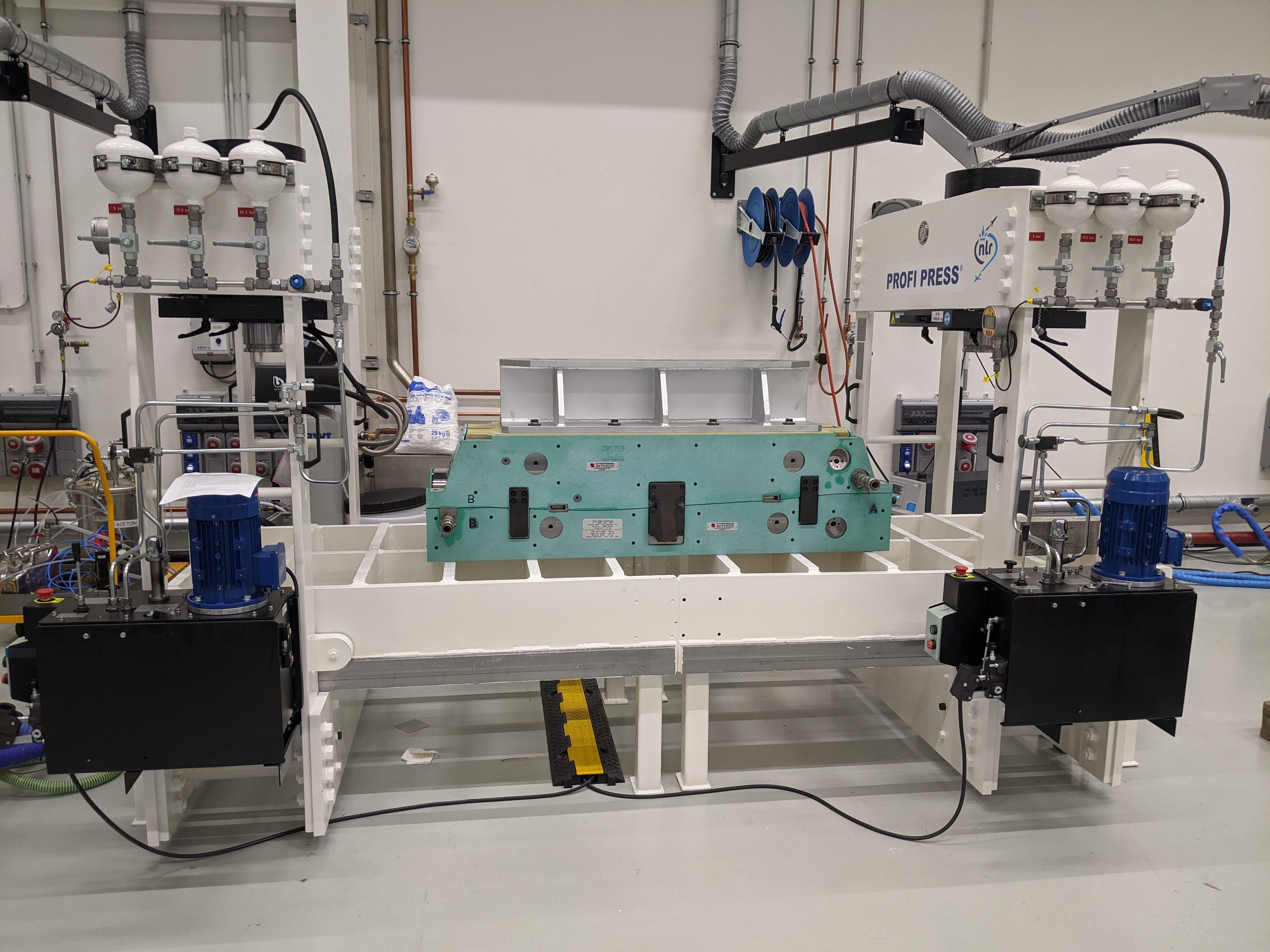
De eerste mijlpalen van het INNOTOOL 4.0-project vereisten dat TME en Isojet een met sensoren uitgerust spuitgietgereedschap en injectiesysteem aan het NLR leverden dat in maart en april 2021 zou worden gebruikt om demonstratieonderdelen te produceren. Tegelijkertijd zou TME een bestaand gereedschap gebruiken voor de productie van CFRP-platen - formaat 600 x 600 millimeter met een dikte van 1-8 millimeter - aangepast met dezelfde sensoren voor procescontroleproeven in hun fabriek. “Dit doe je liever de eerste keer op kleine schaal dan direct op een groot stuk gereedschap met een kostbaar onderdeel”, zegt Vergouwen. TME gebruikte dus een andere tool, maar dezelfde sensoren om hun mogelijkheden en diepte te tonen. Als deze tests zijn voltooid, zou het NLR de belangrijkste HECOLAG-tool opnieuw gebruiken om een nieuwe ronde CFRP-demonstrators te produceren om de procescontrole op de daadwerkelijke onderdelen verder te optimaliseren.
Ontwerp RTM-productietool
TME begon met de productie van het RTM-toolontwerp met behulp van CATIA V5-software van Dassault Systèmes (Vélizy-Villacoublay, Frankrijk) voor mechanisch en elektrisch ontwerp, en ANSYS (Canonsburg, Pa., VS) voor thermische en mechanische simulatie. Deze tool zou worden gecombineerd met Isojet's op zuigers gebaseerde 1K-2K (voor een- en tweedelige harsen) systeem om Hexcel (Stamford, Conn., VS) HexFlow 2K RTM 6 en Solvay (Alpharetta, Ga., VS) 1K te injecteren PRISM EP 2400 ééncomponent epoxyhars van ruimtevaartkwaliteit met een injectiedruk tot 20 bar.
"De vorm van dit vormgereedschap is zeer complex", merkt Besson op, "waarbij verschillende diktes in de droge 3D-voorvorm worden gecombineerd met een gesloten, buisvormige vorm. Dit zorgt voor complexe dikteovergangen, met problemen rond de montage van de voorvorm, nauwkeurigheid van de laaguiteinden, interne temperatuurgradiënten en harskrimp, evenals hoe de verwarmingsmethode en verwarmingscapaciteit van de interne doorn te optimaliseren om een korte cyclustijd mogelijk te maken. Om korte cyclustijden mogelijk te maken, moeten alle onderdelen van de tool eenvoudig in gebruik en robuust zijn en snel opwarmen en afkoelen.” Hoewel het INNOTOOL 4.0-project kortstondig om niet-metalen matrijsoplossingen vroeg, werd een typische op elkaar afgestemde set van bovenste en onderste stalen mallen bedacht vanwege de druk die nodig is om rimpels te minimaliseren en te zorgen voor uitlijning van de vezels tijdens het vormen.
De op elkaar afgestemde boven- en ondermallen en doorn worden verwarmd en gekoeld. "De op elkaar afgestemde vormen gebruiken een geïntegreerd watercircuit terwijl de doorn elektrisch wordt verwarmd", legt Besson uit. "Watercirculatie zorgt voor snelle verwarming en koeling om de deelcyclustijd te verkorten en de elektrische verwarming bereikt hetzelfde in de doorn waar de ruimte beperkt is."
"Een andere uitdaging was het aantal onderdelen in de doorn", zegt Besson. “Vanwege de complexe vorm en de noodzaak om de doorn na het gieten te verwijderen, omvatte deze zes zelfverwarmende componenten en twee steunelementen waar de sensoren doorheen gaan om de interne temperatuur van de doornstukken te regelen. In gebruik worden deze elementen met de hand geassembleerd met behulp van een basissteun die de operator begeleidt.” Werken met een opblaasbare doorn als oplossing zal worden afgerond binnen het grotere HECOLAG-project, maar dat was niet opgenomen in het INNOTOOL 4.0-subproject.
Warmtefluxsensoren
TME was aanvankelijk van plan om diëlektrische sensoren te gebruiken om de harsstroom en uitharding te bewaken (zie "Combineren van AC- en DC-diëlektrische metingen voor het bewaken van de uitharding van composieten"), maar schakelde over op warmtefluxsensoren van TFX (Boncourt, Zwitserland). "Naarmate we vorderden in de ontwikkeling, wilden we sensoren waarmee metingen zonder direct contact met de polymeer- en composietmaterialen konden worden gecontroleerd", legt Jorge Lopez Torres, projectmanager bij TME, uit. "De TFX-sensoren maakten dit mogelijk omdat ze de warmteflux meten, die zich door de materialen voortplant." Hij wijst erop dat dit in feite dezelfde meting is die wordt gebruikt in differentiële scanningcalorimetrie (DSC), een laboratoriumtechniek die de uithardingstoestand van een polymeer of composiet analyseert. Met name TFX-sensoren en DSC-tests meten beide de warmte die vrijkomt tijdens polymerisatie/uitharding en resulteren in een curve van warmteflux versus temperatuur en tijd.
Voor TFX-sensoren zijn de temperatuurgegevens afkomstig van een interne temperatuursensor in de warmtefluxsensoren. Hoewel diëlektrische sensoren op dezelfde manier zijn uitgerust met een interne temperatuursensor, zijn de twee sensoren erg verschillend. "Diëlektrische sensoren meten direct de polymeereigenschappen tijdens het uitharden", legt TFX-manager Dr. Fabien Cara uit. “Warmtefluxsensoren geven niet de toestand van het materiaal op een bepaald moment. Het meten van de warmte die wordt gegenereerd tijdens de harsstroom en polymerisatie geeft echter een mooi beeld van hoe het proces zich gedraagt en hoe herhaalbaar de uithardingscyclus is voor elk geproduceerd onderdeel. En net als DSC moeten we de hele curve van het uithardingsproces zien, maar ons vermogen om de uitharding te controleren is zeer betrouwbaar.”
Tientallen jaren ervaring
Opgericht als Thermoflux in 2000, zijn TFX-sensoren gebruikt in proeven in R&D-centra en in industriële toepassingen door meer dan 100 klanten wereldwijd. "We begonnen meer dan 15 jaar geleden met RTM te werken", zegt Cara, "eerst met BMW voor auto-onderdelen en ook voor het technische centrum dat nu bekend staat als Institute de Soudure [(Saint-Avold, Frankrijk)]. In 2006 en 2012 zijn we gestart met twee grote projecten voor het monitoren van de uitharding van ventilatorbladen van vliegtuigmotoren die zijn gemaakt met RTM en 3D-geweven preforms. Safran heeft een data-acquisitiesysteem dat we voor hen hebben ontwikkeld in hun composietlab in de buurt van Parijs. Ze kunnen tot 100 signalen tegelijk opnemen [(warmteflux, temperatuur en druk]) en deze analyseren voor uitharding en monitoring van procescycli.” TFX heeft ook met Hexcel samengewerkt in zijn laboratorium in Les Avenières, Frankrijk, om de kwaliteit en verwerkingscycli te bewaken met thermohardende harsen die in droge preforms worden geïnjecteerd. TFX-sensoren werden ook gebruikt in een project met IRT-M2P (Porcelette, Frankrijk) om Compression RTM te demonstreren (Meer informatie). "Onze sensoren zijn zeer efficiënt voor snelle processen zoals persgieten, ook met SMC- en BMC-vormmassa's", merkt Cara op. "We hebben in 2016 ook een JEC Innovation Award gewonnen met Huntsman Advanced Materials [(Basel, Zwitserland)] voor een ontwikkeling met de titel 'Structurele epoxyonderdelen met autoclaafkwaliteit in minder dan 1 minuut'."
TFX heeft sensoren voor elk type composiet-gietproces, gebaseerd op de methode van warmteoverdracht naar de sensor:geleiding (RTM, compressie- en spuitgieten), convectie (autoclaaf, oven) en straling (filamentwikkeling, AFP). De sensoren die in het INNOTOOL 4.0-project werden gebruikt, waren geleidend, ontworpen om te worden ingebed in metalen RTM-mallen. "Ze geven een uitzonderlijk herhaalbaar signaal op een afstand van maximaal 1 millimeter van het gereedschapsoppervlak en het composietmateriaal", merkt Cara op.
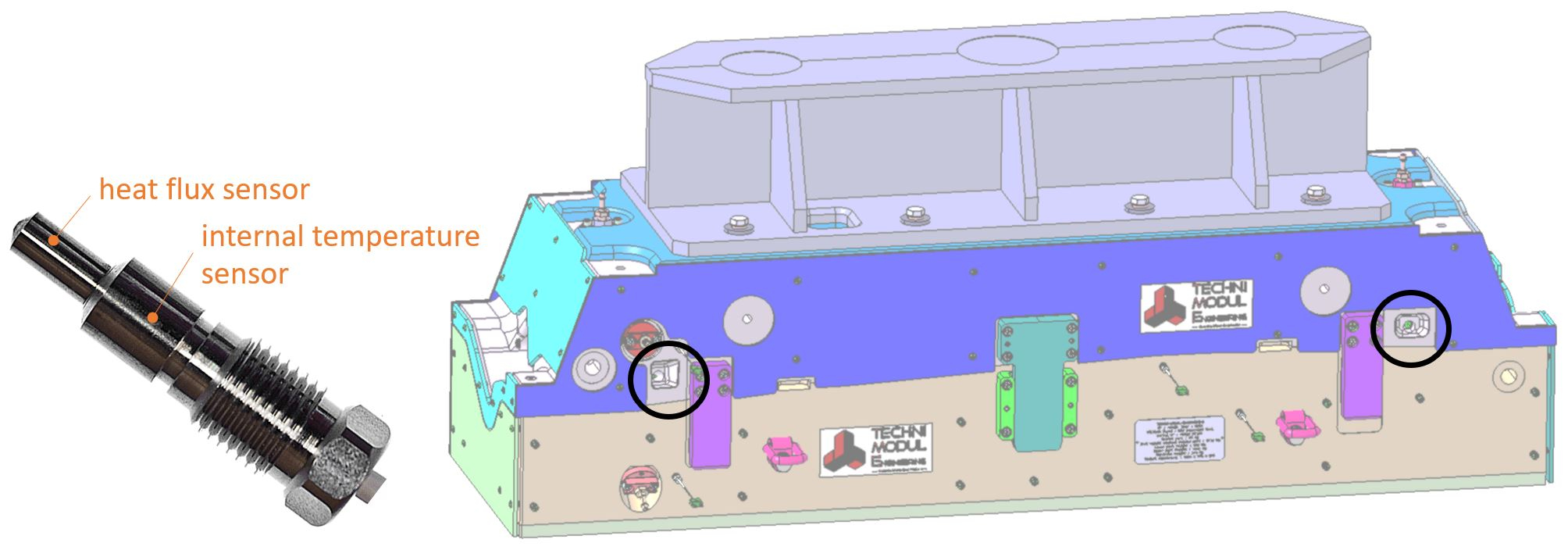
TME installeerde twee TFX-191-sensoren — één bij de harsinvoer en één bij de harsuitvoer — in de bovenste mal van de bijpassende productietoolset die het vervolgens naar het NLR stuurde (Fig. 1, 2). Het NLR gebruikte dit productiegereedschap om in maart en april 2021 HECOLAG demonstratieonderdelen te maken. De TFX-191 sensoren zijn voor dik metalen gereedschap.
Tegelijkertijd nam TME een kleiner, intern gereedschap dat werd gebruikt voor het maken van CFRP-voorbeeldplaten en wijzigde het met twee TFX-224-sensoren, die korter zijn, voor dunnere gereedschappen (Fig. 3). Deze RTM-plaattoolset werd vervolgens gebruikt om sensordemonstratieproeven uit te voeren volgens de hierboven beschreven INNOTOOL 4.0-doelstellingen. "Deze sensoren zijn vergelijkbaar met wat we voor Safran hebben gebruikt", zegt Cara, "maar zijn nu verbeterd om veel compacter en gevoeliger te zijn." De sensoren werden nabij het midden van het onderdeel en de harsuitgang geplaatst. Naast warmtefluxsensoren heeft TFX twee data-acquisitiesystemen ontwikkeld en geleverd:één geleverd aan Isojet en één gebruikt door TME voor de CFRP-plaatproeven.
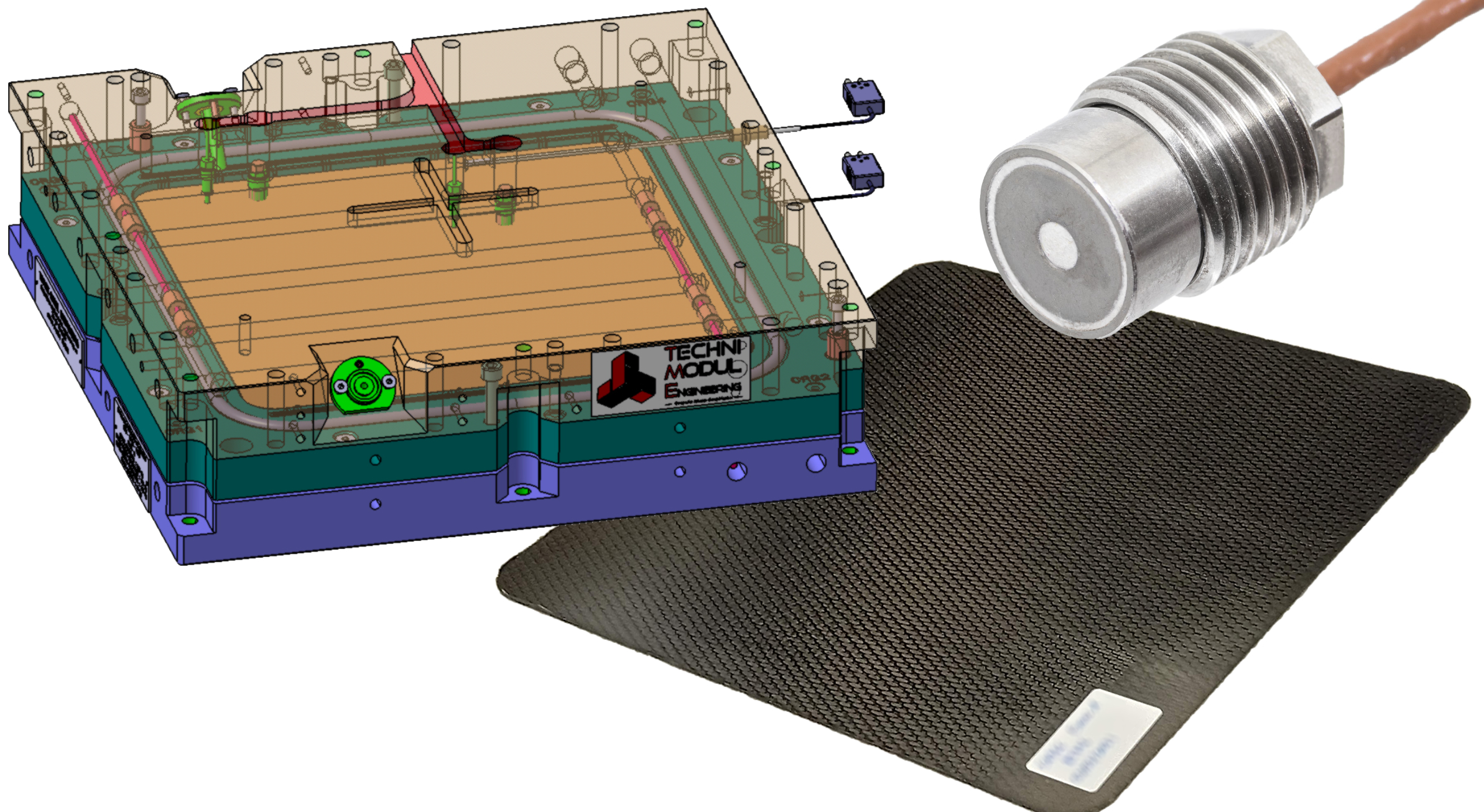
INNOTOOL 4.0-testresultaten
De proeven die TME heeft uitgevoerd met zijn plaatgereedschap dat is gemodificeerd met TFX-sensoren, testten twee verschillende harsen — HexFlow RTM 6 en PRISM EP 2400 — evenals de invloed van de dikte van het onderdeel en de algehele uithardingstijd. “De sensoren gaven mooie signalen om de uithardingscyclus te monitoren”, zegt Cara. "Het team analyseerde vervolgens de uithardingscurves en toonde aan dat de uithardingstijd voor RTM 6 met ten minste 30 minuten kon worden verkort ten opzichte van de voorgeschreven uitharding van twee uur."
Dit is te zien in de onderstaande curve, waarbij t=0 uur het begin van de injectie is. Let op, de uithardingstijd begint wanneer de temperatuur 180°C bereikt en het einde van de uitharding komt overeen met 99% van het relatieve uithardingsniveau (zie verticale as rechts). Het einde van de uitharding valt ook samen met de stabilisatie van de ruwe warmteflux.
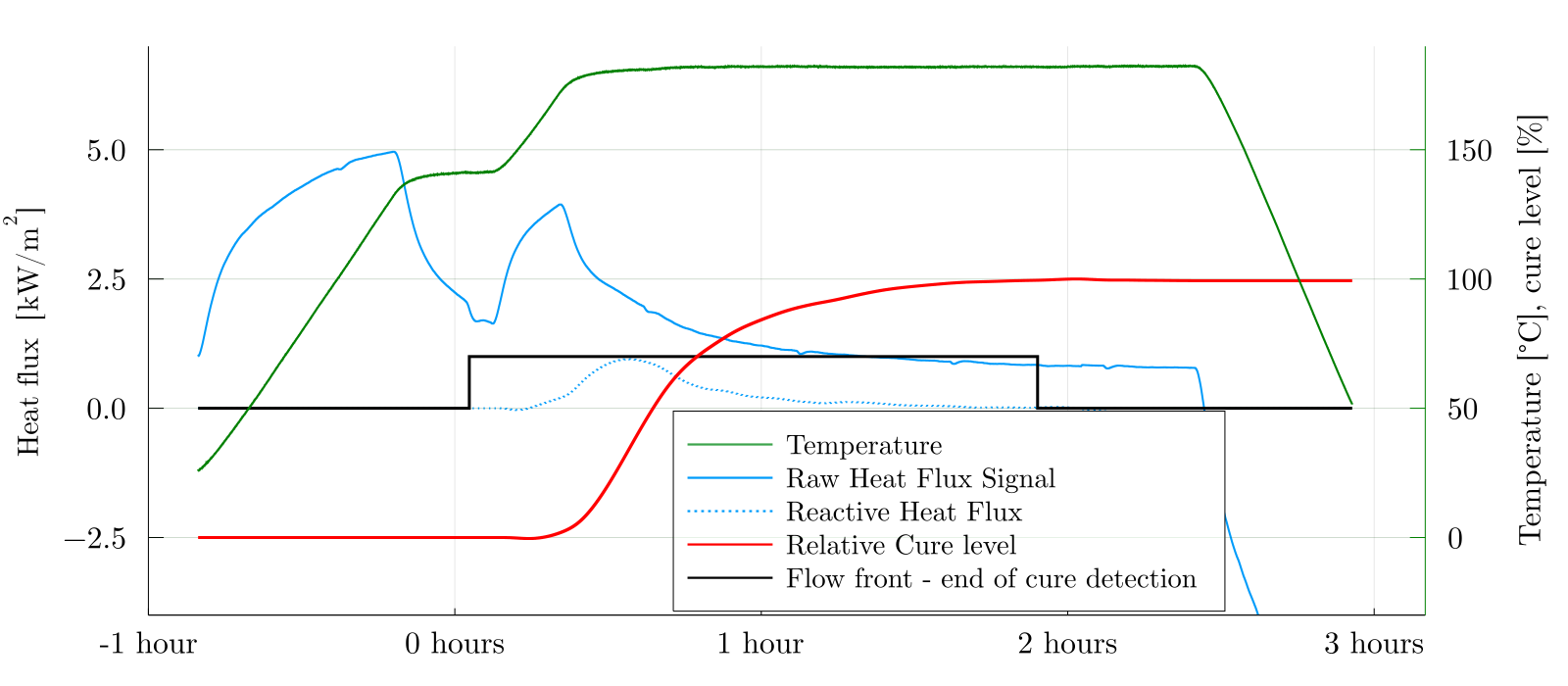
Dit werd geverifieerd door metingen van de uithardingstoestand van ontvormde onderdelen met behulp van dynamische mechanische analyse (DMA), een alternatieve laboratoriumtechniek voor DSC die de glasovergangstemperatuur meet (Tg ) voor composieten. “De DMA-resultaten bevestigden dat voor RTM 6-hars de Tg blijft onveranderd na 90 minuten uitharden bij 180°C,” voegt hij eraan toe.
Ook het effect van dikte werd onderzocht. "De eerste CFRP-platen die door TME werden getest in hun demonstratietests met sensoren, waren minder dan 2 millimeter dik", merkt Cara op. “Deze platen hadden ook een hoog vezelvolume (50-60%) en een langzame uithardingscyclus om exotherm en mogelijke problemen met thermische stress en onderdeelkwaliteit te voorkomen. Dit is allemaal heel normaal voor lucht- en ruimtevaartonderdelen, maar het betekent dat er heel weinig hars is, en dus was de hoeveelheid warmtestroom die vrijkwam door de harsreactie klein. Dus we waren in feite op zoek naar de naald van warmtestroom vanwege het uitharden van hars in een oceaan van verwarming van het gereedschap en het onderdeel. "
Met andere woorden, zoals Cara uitlegt:"De meeste RTM-uithardingscycli in de ruimtevaart omvatten het injecteren van hars bij één temperatuur en vervolgens geleidelijk uitharden om uit te harden bij een tweede, hogere temperatuur. Dus als je klaar bent met injecteren, verwarm je het gereedschap tot de uithardingstemperatuur, wat een grote warmtestroom in het totale systeem genereert.” Echter, net als bij DSC-testen, is de sleutel tot het bewaken van de uitharding met warmtefluxsensoren het meten van de warmte die vrijkomt tijdens polymerisatie/uitharding en deze metingen weer te geven in een curve van warmteflux versus temperatuur in het vormsysteem en tijd. "Dus hebben we een methode uitgevonden die ons helpt om de basislijn van het verwarmen van de mal en de geleiding van die warmte naar het onderdeel af te trekken, zodat het mogelijk is om de warmtestroom van de harsreactie te identificeren."
Dus hoewel de procesomstandigheden in de aanvankelijke dunne platen erg uitdagend waren, konden we de warmtestroom van de harsreactie nog steeds zien, zegt Cara. Door echter ook dikkere onderdelen te maken, konden we precies het verschil in warmtefluxniveaus zien op basis van de onderdeeldikte en dit valideerde onze uithardingsbewaking in de dunne onderdelen.” Let op, de bovenstaande curve (ook getoond in de openingsfoto) werd verkregen met RTM 6-hars in een 3,2 millimeter dikke plaat.
Resultaten voor detectie van harsstroomfront waren echter problematischer. "Voor de sensor bij de uitgang konden we de stroming heel goed zien, maar niet voor de sensor in de buurt van het centrum, waar hars erg laat arriveerde", zegt Cara. "Flowfrontdetectie met warmtefluxsensoren vereist dat de harsstroom een verandering in het lokale thermische veld teweegbrengt. Dit gebeurt wanneer de hars niet dezelfde temperatuur heeft als de preform.” Hij merkt op dat een ΔT groter dan 0,1°C voldoende is voor detectie. “Bij de proeven met dunne CFRP-platen was de temperatuur in de mal echter zeer gelijkmatig en kwam de hars heel langzaam aan. Het thermische contrast was dus niet voldoende om de harsaankomst te detecteren ten opzichte van de thermische ruis in het totale systeem. De hars kwam echter sneller aan bij de uitgang vanwege uitlopers [openingen tussen de voorvorm en de malrand, zie "Vervaardiging van de complexe geometrische onderdelen van RAPM"], wat helpt om een groter thermisch contrast te creëren dat gemakkelijker te detecteren en te controleren was. ”
Cara suggereert dat deze monitoring van de harsstroom aan de voorkant kan worden verbeterd met nieuwe actieve sensoren die TFX heeft ontwikkeld die een geïntegreerd verwarmingsvermogen in de sensor gebruiken. "Hierdoor kunnen de sensoren helpen om het thermische contrast te leveren dat nodig is in onderdelen en processen waar dit inherent moeilijk is", legt hij uit.
Uitbreiding van de controlemogelijkheden voor samengestelde processen
"We zijn blij met het werk dat we tot nu toe hebben voltooid", zegt Torres, "maar dit is slechts een eerste stap. Het doel is om deze warmtefluxsensoren te gebruiken voor het beheer van composietverwerking in productieomgevingen.” Dit is mogelijk, zegt Cara, door automatisch een signaal van het sensorsysteem naar de injectieapparatuur te sturen op basis van harsaankomst en naar de pers op basis van een nulhelling in de uithardingscurve. Torres voegt eraan toe dat TME procesbesturingssystemen heeft voor de injectiemachine en de RTM-pers die temperatuur en druk regelen. "De volgende stap", zegt hij, "is om de TFX-sensoren in deze besturingssystemen te integreren en het algehele proces vanaf een laptop te beheren." Cara merkt op dat TFX-sensoren en data-acquisitie ook werken met druksensoren (bijv. Kistler, Winterthur, Zwitserland) om te helpen bij deze algehele procesbeheersing, en zijn bedrijf ontwikkelt een sensor die warmteflux, temperatuur en meet. em> druk in een enkel geïntegreerd apparaat.
Maar is deze procesbeheersing betaalbaar? Cara zegt dat de initiële investering van $ 10-30.000 voor het monitoringsysteem over het algemeen een rendement oplevert in de ontwikkelingsfase, waardoor vallen en opstaan wordt verminderd door een beter begrip van processen en onderdelen. "Het systeem zorgt vervolgens voor besparingen tijdens de productie, verkort de cyclustijd, zorgt voor herhaalbaarheid en zorgt voor vroege detectie van afwijkingen of afwijkingen."
Bij GKN Fokker is Vergouwen van mening dat zodra het vermogen om de cyclustijd te verkorten en de kosten te verbeteren is bewezen, "het mogelijk is om composieten voor te stellen in niet alleen het type landingsgestelonderdeel dat wordt gedemonstreerd in de INNOTOOL 4.0- en HECOLAG-projecten, maar alle soorten onderdelen. Dat zou onze ontwerpruimte openen en ons in staat stellen de grenzen van lichtgewicht landingsgestellen nog verder te verleggen.” Besson ziet een nog bredere toepassing:“Dit type procesbeheersing kan worden ontwikkeld voor allerlei soorten matrijzen en composietdelen.”
Hars
- Soorten sensoren met hun schakelschema's
- ams om Sensors Expo 2019 te verlichten met innovatieve demonstraties
- Huishoudelijke temperatuurstroom in kaart brengen met goedkope sensoren
- Meet temperaturen met een 1-draads DS18B20-sensor en Raspberry Pi
- Een effect besturen met echte sensoren
- Analoge sensoren uitlezen met één GPIO-pin
- Analoge sensoren lezen met Raspberry Pi en Zabbix Supervisor
- Win10 IOT-irrigatiecontroller met vochtsensoren
- De monitoring van luchtvervuiling verbeteren met IoT-sensoren
- Vereenvoudiging van sensorfabricage met lijmverbindingen
- Slimme wondverbanden met ingebouwde genezingssensoren