Je gebruikt het dagelijks. Maar wat IS polyethyleen plastic?
De 101 op dit alomtegenwoordige moderne materiaal
Polyethyleen is verreweg het meest voorkomende type consumentenplastic en wordt in veel alledaagse materialen gebruikt. Het is een thermoplastisch product, wat betekent dat het kan worden gesmolten tot een vloeistof en vervolgens vele malen kan worden afgekoeld tot een vaste stof. Verschillende verwerkingsomstandigheden leiden tot verschillende soorten polyethyleen die voor zeer verschillende doeleinden kunnen worden gebruikt:van flexibele huishoudfolie aan de ene kant van het spectrum tot harde afdekkingen voor bolderpalen aan de andere kant.
Een van de meest aantrekkelijke eigenschappen van polyethyleen is de duurzaamheid. Het is bestand tegen verbleken en afbrokkelen, terwijl het ook ongevoelig is voor veel chemische stoffen, zoals zuren en bijtende oplossingen. Polyethyleen is een uitstekende elektrische isolator. Het behoudt zijn eigenschappen in extreem koude omstandigheden, maar kan bij hoge temperaturen worden gesmolten.
Polyethyleen plastic:een koolstof-waterstof molecuul
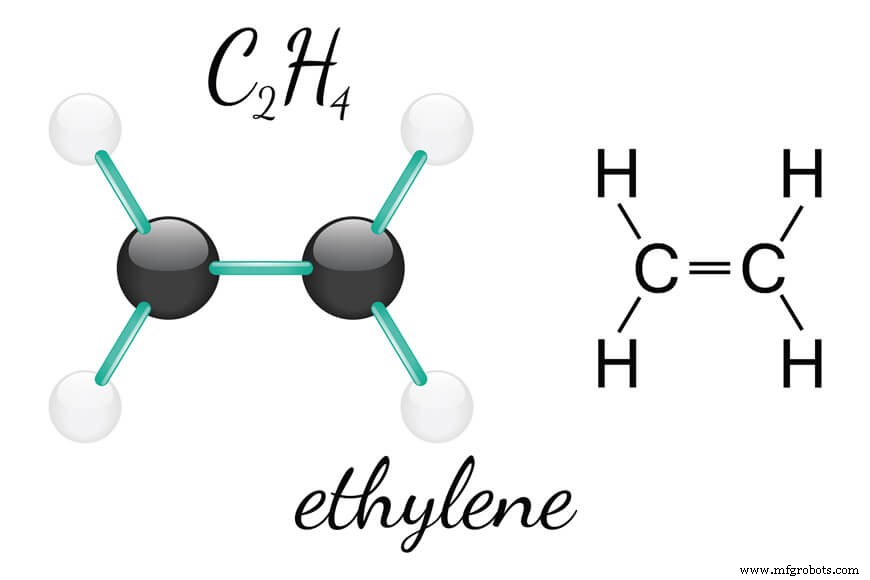
Moleculaire structuur en algemene eigenschappen
Polyethyleen bestaat uit koolwaterstofketens met als meest elementaire component het ethyleenmolecuul, bestaande uit 2 koolstofatomen en 4 waterstofatomen. Wanneer ethyleenmoleculen worden gecombineerd in rechte of vertakte ketens, wordt polyethyleen gevormd. Dit proces omvat het splitsen van de dubbele binding tussen de 2 koolstofatomen en het creëren van een vrije radicaal om zich aan te sluiten bij het volgende ethyleenmolecuul. De macromoleculen zijn niet covalent verbonden, maar worden door intermoleculaire krachten bijeengehouden in een kristallijne structuur. Hoe lager het aantal zijtakken, hoe lager de kristalliniteit en dus hoe hoger de dichtheid, zoals blijkt uit de verschillende eigenschappen voor verschillende soorten polyethyleen.
Polyethyleen is weerbestendig, maar kan broos worden bij langdurige blootstelling aan zonlicht. Deze beperking kan worden overwonnen door toevoeging van UV-stabilisatoren. Het kan worden ontstoken en zal blijven branden nadat de ontstekingsbron is verwijderd met een gele getipte blauwe vlam, waardoor het plastic zal druppelen. De oppervlakte-eigenschappen van polyethyleen voorkomen dat het zonder voorbehandeling aan elkaar wordt geplakt of bedrukt. Polyethyleen kan transparant, melkachtig dekkend of dekkend zijn, afhankelijk van de materiaalkwaliteit, de dikte van het product en de aanwezigheid van additieven.
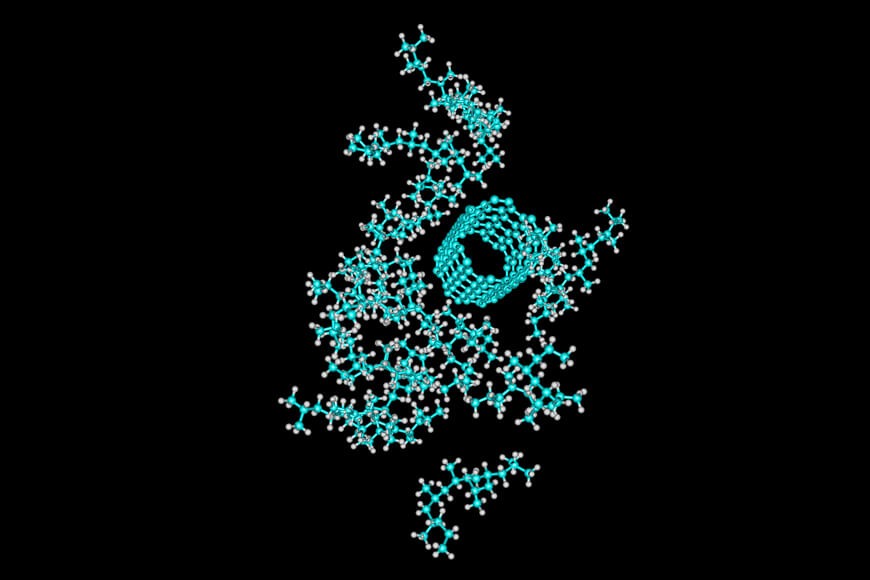
Classificaties van polyethyleen
Low-density polyethyleen (LDPE) wordt gevormd met zowel lange als korte vertakkingen in de polymeerketens. De aanwezigheid van deze vertakkingen zorgt ervoor dat de kettingen niet te strak op elkaar worden gepakt, waardoor LDPE een flexibiliteit heeft die het geschikt maakt voor toepassingen zoals plastic zakken, draadisolatie en plasticfolie. LDPE is zeer goed bestand tegen de meeste chemicaliën, waaronder zuren, basen, alcoholen, aldehyden, ketonen en plantaardige oliën. Het heeft ook een zeer lage wateropname.
Lineair polyethyleen met lage dichtheid (LLDPE) lijkt op LDPE, maar bestaat grotendeels uit lineaire ketens met veel korte zijtakken. Het wordt vaak geproduceerd met behulp van copolymerisatie van ethyleen met alfa-olefinen zoals 1-buteen, 1-hexeen en 1-octeen. De kenmerken van het eindproduct kunnen worden gemanipuleerd door de samenstellende formule aan te passen.
Hoge dichtheid polyethyleen (HDPE) bestaat meestal uit rechte keten moleculen die bij elkaar worden gehouden door intermoleculaire krachten. De afwezigheid van zijtakken zorgt ervoor dat de kettingen strak tegen elkaar worden aangedrukt. Deze hoge dichtheid resulteert in een product dat matig stijf is, waardoor het geschikt is voor toepassingen zoals snijplanken, sapcontainers, plastic hout en speelgoed. HDPE heeft een goede chemische bestendigheid en blijft taai bij zeer lage temperaturen (-76 graden Fahrenheit). Het heeft een wasachtige oppervlaktestructuur die weerbestendig is.
Polyethyleen met ultrahoog moleculair gewicht (UWMPE) heeft extreem lange kettingen en kan worden gesponnen tot draden met een hogere treksterkte dan staal. De sterkte van de intermoleculaire krachten tussen de lange rechte kettingen zorgt voor een stevig materiaal met een zeer hoge slagvastheid. Het wordt gebruikt in toepassingen zoals kogelvrije vesten. Net als andere polyethyleensoorten is UHMWPE bestand tegen de meeste chemicaliën, met uitzondering van oxiderende zuren. Het heeft ook een lage vochtopname, maar dankzij de zelfsmerende eigenschappen is het zeer goed bestand tegen slijtage.
De American Society for Testing and Measurement (ASTM) bepaalt specificaties voor verschillende soorten polyethyleen, inclusief specificaties voor verschillende toepassingen. De belangrijkste eigenschappen van de verschillende kwaliteiten polyethyleen zijn weergegeven in de volgende tabel:
LDPE
HDPE
UHMWPE
Dichtheid (lb/in3)
.035
.035
.034
Wateropname, 24 uur (%)
<0,01
0
0
Treksterkte
1.800 – 2.200
4.600
3.100
Inslagvastheid
Geen pauze
3
Geen pauze
Coëfficiënt van lineaire thermische uitzetting (x10^-5 in/in/deg F)
3
3
3
Maximale gebruikstemperatuur (def F)
160
180
180
Ongeveer. smelttemperatuur (°F)
230
260
280
Diëlektrische sterkte (V/mil) korte tijd, 1/8″ dik
460-700
450-500
900
LDPE
Dichtheid (lb/in3)
.035
Wateropname, 24 uur (%)
<0,01
Treksterkte
1.800 – 2.200
Inslagvastheid
Geen pauze
Coëfficiënt van lineaire thermische uitzetting (x10^-5 in/in/deg F)
3
Maximale gebruikstemperatuur (def F)
160
Ongeveer. smelttemperatuur (°F)
230
Diëlektrische sterkte (V/mil) korte tijd, 1/8″ dik
460-700
HDPE
Dichtheid (lb/in3)
.035
Wateropname, 24 uur (%)
0
Treksterkte
4.600
Inslagvastheid
3
Coëfficiënt van lineaire thermische uitzetting (x10^-5 in/in/deg F)
3
Maximale gebruikstemperatuur (def F)
180
Ongeveer. smelttemperatuur (°F)
260
Diëlektrische sterkte (V/mil) korte tijd, 1/8″ dik
450-500
UHMWPE
Dichtheid (lb/in3)
.034
Wateropname, 24 uur (%)
0
Treksterkte
3.100
Inslagvastheid
Geen pauze
Coëfficiënt van lineaire thermische uitzetting (x10^-5 in/in/deg F)
3
Maximale gebruikstemperatuur (def F)
180
Ongeveer. smelttemperatuur (°F)
280
Diëlektrische sterkte (V/mil) korte tijd, 1/8″ dik
900
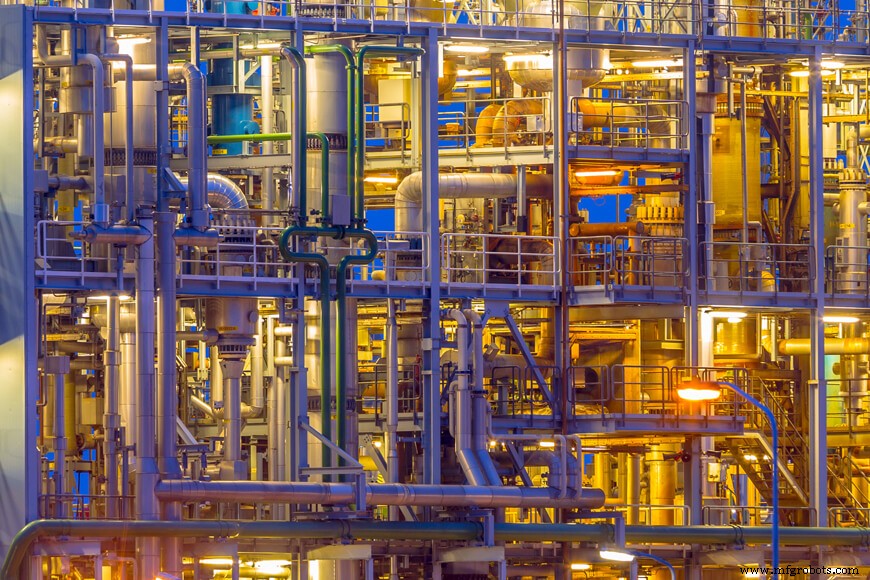
Hoe wordt polyethyleen plastic gemaakt?
De basisbouwsteen voor polyethyleen is het etheenmolecuul, bestaande uit 2 koolstofatomen en 4 waterstofatomen. Etheen komt voor in aardgas en wordt ook geproduceerd bij de raffinage van ruwe olie. Een van de producten van de eerste fase van olieraffinage is nafta, dat door een katalytische kraker wordt verwerkt om materiaal met een hoger octaangetal te produceren. Dit kraakproces levert ook etheen op, dat van andere producten wordt gescheiden voor verdere verwerking tot polyethyleen. Etheen is een gas.
Er zijn verschillende verwerkingsmethoden voor polyethyleen, afhankelijk van de kwaliteit van het product dat moet worden gegenereerd.
LDPE wordt gemaakt door het etheengas te comprimeren tot een druk van 50.000 psi, waarna het wordt afgekoeld en in een reactor wordt gevoerd. Aan de reactor wordt een initiator toegevoegd, waardoor de polymerisatiereactie plaatsvindt. Constant roeren van het materiaal in de reactor zorgt voor een maximale conversie. Na reactie wordt ongebruikt etheen gescheiden van het product en teruggevoerd naar de compressor. Het polymeer wordt geëxtrudeerd, in pellets gesneden en gedroogd voordat het de opslagsilo's binnengaat. Pellets worden meestal in zakken gedaan voor verzending naar klanten, waar ze worden gesmolten en verwerkt tot afgewerkte consumentenproducten.
HDPE wordt gemaakt in een katalytisch proces, waardoor het productieproces van polyethyleen bij lagere temperaturen en drukken kan plaatsvinden. Ziegler-Natta- en chroomkatalysatoren waren de eerste gebruikte katalysatoren, maar er worden voortdurend nieuwere soorten katalysatoren ontwikkeld om de productieprocessen en de kenmerken van producten te verbeteren. Sommige processen mengen zelfs verschillende soorten polyethyleen in één batch, waardoor de scheidslijnen tussen de verschillende productkwaliteiten vervagen.
LLDPE wordt ook geproduceerd in een katalytisch proces met toevoeging van copolymeren zoals alfa-olefinen (butaan, hexaan). De moleculaire structuur van LLDPE is een lange keten met veel korte vertakkingen.
UHMWPE wordt geproduceerd met behulp van metalloceenkatalysatoren, wat resulteert in extreem lange koolwaterstofketens (meer dan 100.000 moleculen van monomeercomponenten). Een secundair proces genaamd gel-spinnen neemt een verwarmde gel van UHMWPE en extrudeert deze door een spindop. Het product wordt gekoeld in een waterbad. Dit spinproces levert een vezel op met een hoge mate van moleculaire oriëntatie (95%), wat hem de extreem hoge treksterkte geeft.
Plastic gieten met polyethyleen
Polyethyleen komt uit de fabriek in korrelvorm en wordt gesorteerd volgens de specificaties. Klanten gebruiken deze pellets als grondstof in hun eigen productieprocessen, waarbij ze worden gesmolten door warmte en druk toe te passen en vervolgens het vloeibare plastic in zijn uiteindelijke vorm te gieten. Er zijn verschillende methoden om polyethyleen te vormen, afhankelijk van de kwaliteit van de grondstof en het type eindproduct dat nodig is:
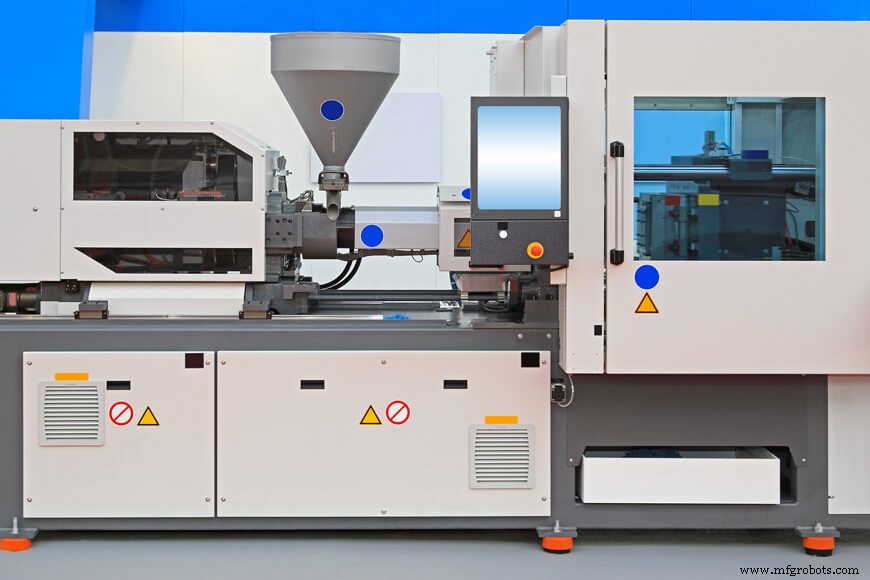
- Spuitgieten
Spuitgieten is een van de twee meest voorkomende methoden voor het maken van eindproducten van polyethyleen. Pellets worden in een verwarmde cilinder gevoerd waar een roterende vijzel het smeltende plastic door een poort in een mal duwt. Een vaste hoeveelheid polyethyleen wordt geïnjecteerd onder een hoge druk van 10.000-30.000 psi. Zodra de injectie is voltooid, wordt de mal afgekoeld voordat deze wordt geopend en het eindproduct wordt verwijderd. Dit is het typische proces dat wordt gebruikt om in massa geproduceerde artikelen zoals emmers en doppen te vervaardigen. - Blazen
Blow molding wordt gebruikt om producten zoals flessen en spuiten te maken, waarbij er een holte in het product zit. Bij het blaasvormen omvat de eerste fase het vormen van een voorvorm rond een kernpen met behulp van een standaard spuitgietmatrijs. Nadat de preform is afgekoeld, wordt deze in het midden van een tweede mal geplaatst. De voorvorm wordt opnieuw verwarmd en via de kernpen wordt perslucht toegevoerd om het gesmolten plastic tegen de binnenwanden van de uiteindelijke mal te blazen en zo de interne holte te creëren. Eenmaal afgekoeld, wordt de pin verwijderd. - Compressievormen
Compressievormen wordt voornamelijk gebruikt voor thermohardende kunststoffen, dit zijn kunststoffen die niet meerdere keren opnieuw kunnen worden verwarmd en opnieuw gevormd. Poeders en andere materialen kunnen aan de mix worden toegevoegd om speciale eigenschappen te creëren of het eindproduct te versterken. Bij dit proces wordt het plastic gevormd door verwarmde platen die druk uitoefenen op het plastic. De korte cyclustijd in dit proces maakt het aantrekkelijk voor toepassingen met grote volumes, zoals onderdelen voor de auto-industrie. - Transfergieten
Transfer molding houdt in dat het plastic wordt verwarmd tot de gesmolten toestand voordat het wordt overgebracht naar een compressiegietproces. Wanneer er veel kleine gaatjes of metalen inzetstukken zijn, vormt het gesmolten plastic zich hier gemakkelijker omheen zonder de uitlijning te verstoren. - Film insert molding
Dit proces omvat het inbrengen van een film of textielmateriaal in een spuitgietmatrijs voordat het plastic wordt geïnjecteerd, zodat de film wordt opgevangen in het eindproduct. - Extrusie
Samen met spuitgieten is extrusie een van de meest populaire methoden om polyethyleen in een gewenste vorm te vormen. Pellets worden via een trechter in een verwarmde kamer gevoerd, waar een vijzel het smeltende plastic naar voren drijft. Aan het einde van de verwarmde kamer bevindt zich een matrijs, die het plastic vormt wanneer het in de atmosfeer komt. Dit proces wordt gebruikt om doorlopende platen, buizen, kabels, leidingen en meer te maken. Het eindproduct komt op een transportband terecht waar het luchtgekoeld wordt (soms met behulp van blowers). Het product kan ook in water worden geplaatst om het koelproces te versnellen. - Gassenspuitgieten
Bij gasspuitgieten wordt een standaard spuitgietproces verbeterd door een extra stap. De mal wordt gevuld tot 70% van het totale benodigde gesmolten plastic, waarna gas in de kamer wordt gepompt om het plastic in het uiteinde van de mal te duwen. Het netto-effect is dat het eindproduct door het blazen van gas een hol centrum heeft en er minder plastic wordt gebruikt. - Rotatievormen
Gepoederd plastic wordt in een holle mal geplaatst en vastgezet op een roterende naaf. De naaf draait om 2 assen in een oven, waardoor het plastic smelt en de binnenwanden van de mal bedekt. De naaf blijft door de koelcyclus draaien, waarbij vaak water op de buitenkant van de mal wordt gespoten. Ten slotte wordt het eindproduct verwijderd. Het voordeel van deze methode is de eenvoud van mallen, het ontbreken van benodigde druk en het ontbreken van lassen en verbindingen in het eindproduct. - Structuurschuimvormen
Gesmolten plastic wordt samen met gecomprimeerd gas in een accumulator geïnjecteerd om een schuimeffect in het plastic te creëren. Vanuit de accu wordt het schuimplastic in de mal gespoten. De drukval van de accumulator naar de mal zorgt ervoor dat het plastic uitzet en de mal vult. Na afkoeling is de huid glad, maar de interne kern is geschuimd, waardoor het eindproduct een hoge stijfheid krijgt. - Thermovormen
Thermovormen en vacuümvormen worden bereikt door een plastic vel te nemen, het te verwarmen tot het zacht is en het vervolgens over een mal te draperen. In sommige gevallen wordt positieve luchtdruk toegepast, terwijl in andere gevallen een vacuüm wordt gecreëerd om het plastic tegen de mal te drukken. Na afkoeling wordt het eindproduct afgevoerd. - Reactiespuitgieten
Reactiespuitgieten is een nieuwere technologie voor het vormgeven van kunststofproducten. De kunststof wordt gemengd met andere componenten op een lagere temperatuur dan bij traditioneel spuitgieten. In de mal vindt een exotherme reactie plaats om het plastic onder druk te zetten. Omdat lagere temperaturen en drukken nodig zijn, worden de productiekosten verlaagd. Glasvezel kan ook aan het mengsel worden toegevoegd om het eindproduct sterker te maken.
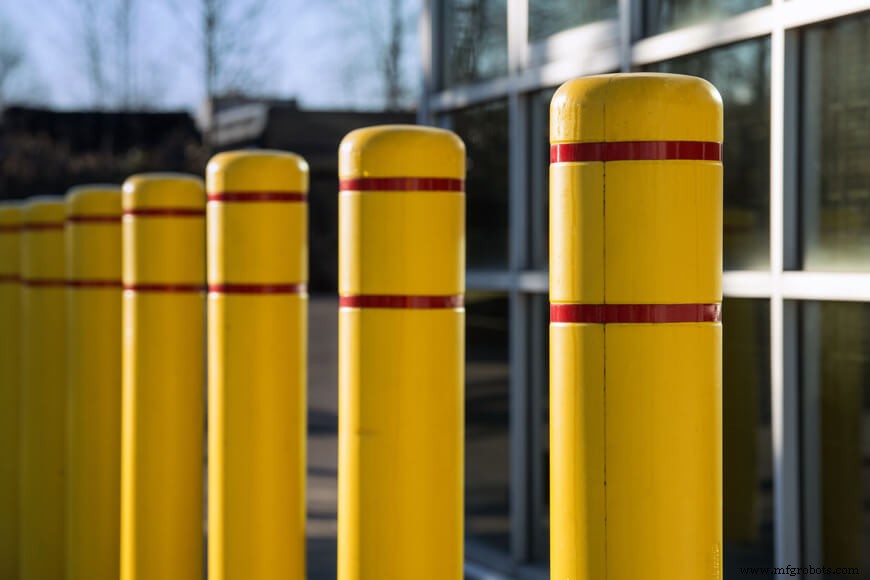
Onderhoud
Polyethyleen is een zeer duurzaam materiaal, dat niet snel slijt of verzwakt. Voortdurende blootstelling aan zonlicht kan echter na verloop van tijd brosheid van het product veroorzaken. Voor pijpleidingen of tanks die zijn blootgesteld aan de elementen, wordt een inspectiecyclus aanbevolen om spinnenwebben of scheuren als gevolg van broosheid te identificeren.
De levensduur en duurzaamheid van polyethyleen producten is zo goed dat veel fabrikanten ze als onderhoudsvrij omschrijven.
Toepassingen
Polyethyleen is de meest voorkomende vorm van thermoplast die wordt gebruikt in consumentenproducten en heeft een breed scala aan toepassingen. Hier volgen enkele van de meest voorkomende toepassingen:
- Voedselverpakkingsmateriaal: Omdat polyethyleen zo goed bestand is tegen wateropname en chemische schade, is het gecertificeerd als veilig voor gebruik in voedselverpakkingen.
- Medische slangen: Het gebrek aan porositeit van polyethyleen maakt het een ideaal materiaal om te gebruiken voor katheters en andere medische producten vanwege de weerstand tegen contaminatie.
- Emmers, flessen en bakken: Vanwege de hardheid van kunststof en de duurzaamheid onder stress, is het geschikt voor consumentenproducten.
- Kogelvrije vesten: UHMWPE-vezels hebben een hoge treksterkte, maar zijn toch erg licht, waardoor ze ideaal zijn voor veiligheidstoepassingen.
- Kabels met hoge treksterkte: Ze zijn licht, dus eenvoudig te installeren, maar sterk, dus nuttig in complexe industriële toepassingen.
Recycling
Plastic producten hebben veel slechte pers gekregen vanwege hun impact op het milieu, maar zoals bij de meeste potentiële verontreinigende stoffen, is het het gedrag van mensen - niet het product zelf - dat tot milieuschade leidt. Polyethyleen is niet biologisch afbreekbaar, waardoor het een ongeschikt materiaal is om via stortplaatsen te worden afgevoerd.
De eigenschappen van polyethyleen maken het echter ideaal voor recycling, omdat het kan worden omgesmolten en omgevormd tot een ander product. Bovendien zorgt de weerstand tegen chemische verontreiniging en absorptie van vloeistoffen ervoor dat het gerecyclede product niet veel onzuiverheden bevat. Soms worden gerecycled en nieuw materiaal met elkaar vermengd in het vormingsproces van afgewerkte consumentenproducten. Recyclingnummer #2 geldt voor HDPE en #4 voor LDPE; veel recyclingbedrijven kunnen beide soorten verwerken voor hergebruik.
Veel materialen die voorheen als milieurisico's werden beschouwd (bijvoorbeeld rubber), worden nu steeds vaker gerecycled naarmate mensen een duurzamere levensstijl gaan nastreven en de recyclingtechnologie zich ontwikkelt.
Verwante artikelen
- Nog steeds nieuwsgierig? Bekijk:Wat is polyurethaanplastic?
- En het plastic is vierkant! Bekijk hoe in Flexibele paaltjes versus verkeersafbakeningen.
Bronnen
- BPF. “Kunststofprocessen”
- Kunststofindustrie. "Methoden voor het verwerken van kunststof"
- Polymeerdatabase. “Polyolefinen”
- Amerikaanse Chemieraad. "Levenscyclus van een plastic product"
- ECI. “Polyethyleen”
- Britannica. “Polyethyleen”
Metaal
- Welke metalen 3D-printpoeders kun je gebruiken in 2020? [Gids]
- Waarom moet je landbouwkleurstoffen gebruiken?
- Wat is OSGi en wat heb je eraan?
- Bluetooth Low Energy (LE) bereik:wat kun je verwachten in deze use case?
- Wat kunt u snijden met een Fiber Laser?
- Wat maakt jou een leider?
- Wat is plastic? Veelgestelde vragen
- Wat bedoel je met schilderen?
- Industriële koppelingen:wat zijn het en hoe gebruik je ze?
- Begrijpen wat Naval Brass voor u kan doen
- Bronzen gieten en wat je moet weten