Elektrische ontladingsbewerking:constructie, toepassing, voor- en nadelen
Verspanen met elektrische ontlading, ook wel vonkbewerking genoemd, is een proces dat heel anders is dan de meeste conventionele bewerkingsprocessen zoals CNC-draaien en frezen. Bij laatstgenoemde processen zijn scherpe snijgereedschappen nodig om materiaal van het te bewerken werkstuk af te kunnen trekken. In tegenstelling tot draaien en frezen, maakt het EDM-proces gebruik van de erosie van metaal door een reeks elektrische ontladingen.
Lees hieronder verder en leer meer over de fundamentele concepten die betrokken zijn bij EDM-productie.
Hoe werkt EDM?
Bij machinale bewerking met elektrische ontlading worden elektrische vonken op de edm-machine gebruikt om sommige delen van het werkstuk te eroderen. Deze "elektrische vonken" zijn eigenlijk elektrische bogen gevormd tussen twee stroomvoerende geleiders die dicht bij elkaar zijn gebracht. De elektrische bogen zijn degenen die verantwoordelijk zijn voor het genereren van extreme hitte waardoor de elektrisch geleidende materialen smelten en verdampen. Binnen het systeem van een EDM-proces is het werkstuk verbonden met de positieve pool of de anode, terwijl het gereedschap dat verantwoordelijk is voor het eroderen van materialen is verbonden met de negatieve pool of de kathode.
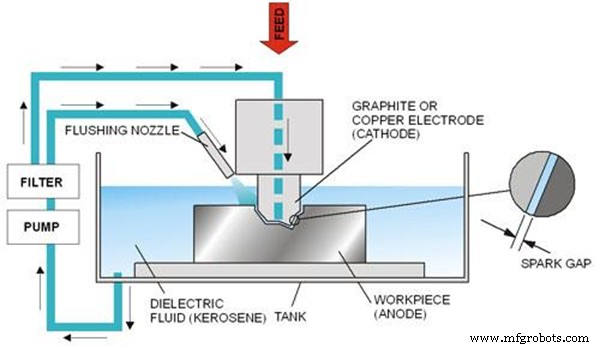
Basisconstructie van een EDM-systeem
Om het werkingsprincipe verder uit te werken, vindt u hieronder een overzicht van de basisconstructie van een elektrisch ontladingsbewerkingssysteem (EDM).
Dit onderdeel zet de AC-voeding om in een pulserende DC-voeding die hoog genoeg is om een vonk te genereren tussen het eroderingsgereedschap en het werkstuk.
Dit deel van het systeem is verbonden met de kathode van de voeding terwijl het op een gereedschapspaal is gemonteerd. Het profiel van uw gereedschap is exact hetzelfde profiel als op uw werkgedeelte. Tijdens het proces wordt een zeer kleine opening, de boogopening genoemd (geïdentificeerd door productie-ingenieurs), gehandhaafd tussen het elektrodegereedschap en het werkonderdeel. De meest gebruikte materialen voor elektroden zijn koper, wolfraamlegering, grafiet, staal en gietijzer.
Dit mechanisme regelt de voeding en beweging van het gereedschap in de EDM-machine. De boogopening, hierboven vermeld, wordt kritisch gecontroleerd door een geprogrammeerd servomotormechanisme.
Dit onderdeel levert de juiste hoeveelheid spanning die nodig is voor het genereren van vonken en het onderhoud van de ontlading. De generatie van honderdduizend vonken per seconde maakt het mogelijk om een aanzienlijke materiaalafname van het werkgedeelte te creëren.
Zowel het elektrodegereedschap als het werkdeel zijn ondergedompeld in een diëlektrische vloeistof terwijl de vloeistof wordt toegevoerd bij de opening tussen het gereedschap en het werkdeel. Bovendien moet de diëlektrische vloeistof zo worden ingesteld dat deze met een constante druk circuleert om metalen onderdelen die van het werkgedeelte zijn geërodeerd weg te flitsen. Te veel vloeistofdruk kan ertoe leiden dat de metaalspanen snel worden verwijderd, wat resulteert in een langzamere snijwerking. Een te lage vloeistofdruk kan een kortsluiting in het systeem veroorzaken door de niet-geëvacueerde spanen tijdens het erosieproces.
De meest voorkomende diëlektrische vloeistoffen die in dit proces worden gebruikt, zijn gedeïoniseerd water, glycol en siliconenolie.
Dit maakt het ecosysteem van de EDM-machine compleet omdat het werkgedeelte is verbonden met de anode. Om het proces mogelijk te maken, moet het werkgedeelte een goede elektrische geleider zijn.
Type EDM-processen
Het EDM-proces wordt ingedeeld in verschillende typen, afhankelijk van de vorm en benadering van het gebruikte gereedschap. De drie meest voorkomende vormen van elektrische ontlading in de industrie zijn draadvonken, zinkvonken en boorvonken.
1. Draadvonken
Zoals de naam al aangeeft, gebruikt EDM-draadsnijden een zeer dunne draad (een koper- of messinglegering, meestal variërend van 0,004 inch tot 0,0006 inch dun) die wordt vastgehouden door diamantgeleiders om nauwkeurig een tweedimensionale vorm op een 3D-werkstuk te snijden. Het pad wordt bestuurd door een CNC-programma waarmee complexe vormen eenvoudig kunnen worden gesneden. Het snijden kan worden vergeleken met het snijden van een lintzaag en een kaassnijder. Dit proces wordt meestal gebruikt voor het snijden van metalen extrusiematrijzen, ponsen en platen.
2. Zink EDM
Dit type EDM-proces, ook wel ram-EDM genoemd, maakt gebruik van grafiet- of koperelektroden die in een omgekeerde vorm zijn gevormd om een holte in het werkgedeelte te snijden. Het te gebruiken gereedschap wordt machinaal bewerkt in een omgekeerde vorm van de gewenste vorm die op het werkstuk moet worden achtergelaten.
Sinker EDM maakt het perfect voor het machinaal bewerken van matrijzen die worden gebruikt voor gieten en spuitgieten waar complexe holtevormen nodig zijn.
3. Gatenboren EDM
Bij dit type EDM-proces wordt het elektrodegereedschap gebruikt om extreem dunne en diepe gaten te maken waar een conventionele boormachine misschien niet toe in staat is. Het gereedschap voor dit proces is zo ontworpen dat de diëlektrische vloeistof direct door het gat wordt geleid, dus een holle elektrode. Aangezien het boren van gaten EDM niet wordt gemaakt door middel van de conventionele bewerkingsmethode, worden er geen bramen gevormd in het werkgedeelte. Gatenboren EDM wordt gebruikt voor het bewerken van kleine reliëfgaatjes op verschillende turbinebladen, matrijzen en mallen.
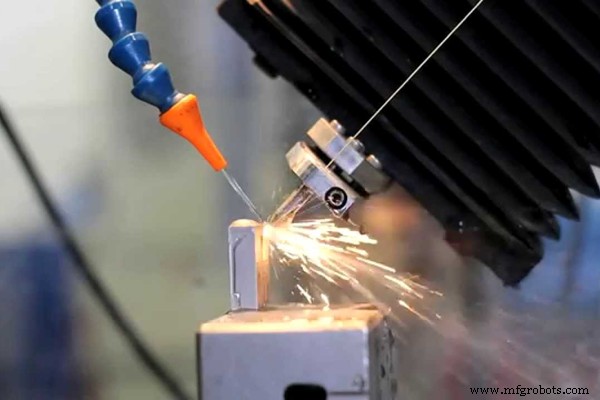
Wat zijn de toepassingen van EDM-bewerking?
EDM-bewerking is zeer goed in staat om ingewikkelde vormen en geometrieën te produceren.
Dat is de reden waarom over het algemeen machinale bewerking met elektrische ontlading wordt gebruikt voor zeer nauwkeurige toepassingen waar conventionele bewerking niet in staat is. Hieronder staan de meest voorkomende toepassingen van EDM-bewerking:
Klein gat boren
Veel fabrikanten kiezen ervoor om EDM-bewerking te gebruiken bij het boren van extreem kleine gaatjes, omdat dit het risico op verbogen en beschadigd gereedschap verkleint. EDM-gefreesde gaten kunnen erg klein van structuur zijn en zijn te zien aan de randen van turbinebladen, microscopisch kleine openingen voor brandstofsysteemcomponenten en nog veel meer.
Mold and Die Making
EDM-bewerking wordt vaak gebruikt als een aanvullend proces naast conventionele bewerking bij de fabricage van matrijzen en matrijzen. Zoals hierboven vermeld, wordt het draadgesneden type meestal gebruikt voor het vormen van plano's voor de mallen, het zinktype kan worden gebruikt om complexe vormen van de holtes te vormen en het gatboren kan worden gebruikt voor het maken van drukontlastingsgaten.
Desintegratie van componenten
De EDM-machine wordt ook gebruikt om vastzittende metalen in een werkonderdeel te verwijderen die niet op een gewone manier kunnen worden verwijderd. Het desintegreren van de vastzittende componenten betekent het vernietigen of verwijderen van het materiaal. Sommige omstandigheden zijn onder meer breekbouten op draadgaten, zuiggereedschap op een bewerkt onderdeel of een pen die op een zeer kostbaar onderdeel wordt geplakt. Door de componenten te desintegreren, kunt u het vastzittende metaal verwijderen zonder het terug te vorderen onderdeel te beschadigen.
Medische componenten
EDM-bewerkte producten vormen geen bramen tijdens de fabricage, daarom zijn deze perfect voor het maken van verschillende medische implantaatcomponenten.
Lucht- en ruimtevaartcomponenten
Er zijn veel functies op een ruimtevaartonderdeel die niet kunnen worden gemaakt door sommige standaard snijgereedschappen, en dat is waar de EDM-bewerking van pas komt. EDM-bewerking is in staat om uitdagende functies te produceren met als belangrijkste turbinerotorschijf, dunne sleuven, scherp vierkant gaten en zeer krappe vereisten voor diepe gaten.
Waarom heeft EDM de voorkeur?
Zeer geschikt voor het bewerken van complexe profielen
De snijvrijheid voor EDM is minder beperkt dan die van conventionele machinale bewerkingen. In dit proces kunnen verschillende functies die bijna onmogelijk zijn te bereiken door het gebruik van vingerfrezen en boren gemakkelijk worden gesneden. Deze kenmerken omvatten ingewikkelde holtes, fijne diepe gaten, dunne wanden en andere onregelmatig gevormde geometrieën.
Hoge nauwkeurigheid
Met EDM-technologie bewerkte onderdelen kunnen nauwkeurig zijn tot de kleinste toleranties die worden gebruikt in de metaalverwerkende industrie. Dit is mogelijk omdat het ecosysteem van EDM-bewerking geen hoge spanning op het werkdeel introduceert en geen agressieve trillingen heeft. Afgezien hiervan kan er ook een skimming-proces worden uitgevoerd om de precisie en nauwkeurigheid te vergroten.
Braamvrije oppervlakteafwerking
Het door EDM-bewerking geproduceerde werkstuk komt er braamvrij uit vanwege de aard van het proces waarbij het geërodeerde metaal van het werkstuk bijna uiteenvalt in microdeeltjes die vervolgens worden weggespoeld. Het belangrijkste is dat bij EDM-snijden geen scherpe snijgereedschappen zoals vingerfrezen, zagen en boren nodig zijn, daarom veroorzaakt dit proces geen bramen op het werkgedeelte.
Kan harde metalen snijden
EDM-bewerking is in staat om harde metalen met weinig kracht en minimale inspanning te snijden, zolang ze geleidend zijn. De hardheid van het te snijden materiaal heeft geen invloed op het algehele proces.
Lage stress
De gereedschappen die in een EDM-proces worden gebruikt, raken het werkstuk niet aan, in tegenstelling tot andere bewerkingsmethoden waarbij de snijgereedschappen contact maken met het te snijden oppervlak. Dit verklaart de minimale spanning die in het werkstuk wordt geïntroduceerd.
Zeer schaalbare productie
EDM-bewerkingsprocessen zijn zeer veelzijdig als het gaat om productieschaal, het is geschikt voor productie van kleine tot grote volumes. Deze processen zijn zeer herhaalbaar, wat betekent dat meerdere onderdelen met een constante kwaliteit kunnen worden gemaakt.
Lorem ipsum dolor sit amet, consectetur adipiscing elit. Ut elit tellus, luctus nec ullamcorper mattis, pulvinar dapibus leo.
Wat zijn de beperkingen van het EDM-proces?
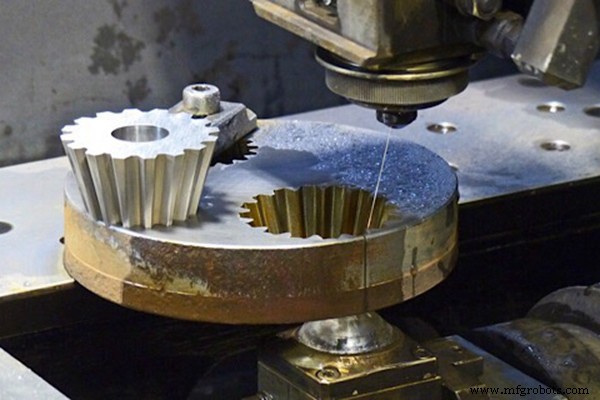
Alleen van toepassing op geleidende materialen
De warmte die verantwoordelijk is voor het eroderen van het materiaal op het werkgedeelte is afhankelijk van de introductie van elektrische ontladingen, waardoor edm-bewerking niet compatibel is met niet-geleidende materialen zoals composieten, kunststoffen en andere diëlektrische materialen.
Lage materiaalverwijderingssnelheid
Zoals vermeld, erodeert EDM-bewerking geleidelijk het materiaal. Dat maakt de materiaalverwijderingssnelheid veel lager dan die van de conventionele bewerkingsprocessen zoals frezen en draaien.
Dure productiekosten
De kosten voor het produceren van onderdelen met EDM omvatten verschillende factoren, zoals een hoog stroomverbruik, overmatige gereedschapsslijtage en een lange bewerkingstijd.
Samenvatting
Verspanen met elektrische ontlading is een zeer nuttige aanvulling op verschillende conventionele CNC-bewerkingsprocessen. Het speelt zijn kracht waar het in staat is om speciale eigenschappen te produceren die moeilijk te bereiken zijn door middel van frezen en draaien. Bovendien heeft het EDM-proces een uitzonderlijke nauwkeurigheid, zelfs bij het snijden van extreem harde elektrisch geleidende metalen, en zorgt het voor een lage spanning tijdens de verwerking.
CNC machine
- Voors en tegens van Lost-Foam Casting
- Voor- en nadelen van koudvervormende metaalbewerking
- EDM-bewerking:constructie- en werkingsprincipe besproken
- Waarom zijn elektrische ontladingsbewerkingen populairder dan andere technieken?
- Wat is Electrical Discharge Machining (EDM)?
- Typen elektrische ontladingsmachines (EDM), voor- en nadelen
- Prototypebewerking:voor- en nadelen van CNC voor prototypen
- Sinker EDM versus draadvonken:belangrijkste verschillen en toepassingen
- Voorbij de CNC:wat is elektrische ontladingsbewerking?
- De voor- en nadelen van technologie in productie
- Bewerkingsprocessen en -technieken