Wat is destructief testen en wat zijn de toepassingen ervan
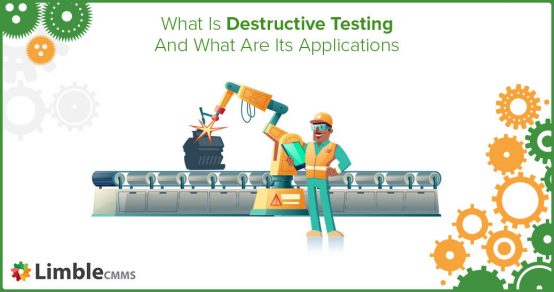
Er wordt veel nagedacht over het bouwen van betrouwbare activa. Uitgebreide tests maken deel uit van het proces dat moet worden uitgevoerd om de duurzaamheid van machines, materialen en componenten in te schatten. Het testen kan destructief of niet-destructief worden uitgevoerd.
In dit artikel gaan we dieper in op de verschillende aspecten van destructief testen en de gebruiksscenario's ervan.
Wat is destructief testen?
Destructief testen (vaak afgekort als DT) is een testmethode die wordt uitgevoerd om het exacte faalpunt van materialen, componenten of machines te vinden. Tijdens het proces ondergaat het geteste item spanning die uiteindelijk het materiaal vervormt of vernietigt. Uiteraard kunnen geteste onderdelen en materialen niet opnieuw worden gebruikt bij normaal gebruik na het ondergaan van destructieve testprocedures.
Destructief testen wordt over het algemeen uitgevoerd voordat een onderdeel in massaproductie gaat. OEM's moeten de limieten van hun producten kennen om de juiste onderhouds- en bedrijfsaanbevelingen voor hun machines te kunnen geven.
Industriële ketels staan bijvoorbeeld bekend om hun vermogen om hoge druk en hoge temperaturen te weerstaan. De materialen die zijn gekozen om de ketels te bouwen, spelen een grote rol bij het bepalen van de druk- en temperatuurclassificaties van de ketel. Het falen van industriële ketels kan een catastrofe in de fabriek veroorzaken. De materialen die worden gebruikt om ketels te bouwen, worden tot het uiterste getest om de maximale druk te bepalen die het kan weerstaan. Op deze manier worden alleen materialen met een ruime veiligheidsmarge gebruikt om elke ketel te bouwen.
Wie voert destructieve testen uit?
Destructief testen kan intern of met behulp van externe testdiensten worden uitgevoerd.
Een gespecialiseerde organisatie zoals NASA zal destructieve tests uitvoeren binnen hun faciliteiten. Andere bedrijven kunnen externe materiaaltestfaciliteiten inhuren. Serviceproviders voor materiaaltesten kunnen namens OEM's destructieve tests uitvoeren om te controleren of de componenten binnen de vereiste parameters kunnen werken.
De expertise van dergelijke faciliteiten kan ook worden gebruikt om de materialen in de eerste plaats te selecteren. Laboratoria voor materiaaltesten hebben een reeks materialen waarvan de fysieke eigenschappen worden getest en geregistreerd. Uit hun collecties kunnen materialen met de gewenste fysieke eigenschappen worden gekozen. In de VS kunnen door Nadcap gecertificeerde laboratoria voor materiaaltesten worden gebruikt om destructieve tests uit te voeren.
Destructief testen wordt uitgevoerd door gespecialiseerde onderzoekers, wetenschappers en technici. Wie het uitvoert, wordt bepaald door het type destructieve tests dat moet worden uitgevoerd . Over het algemeen wordt destructief onderzoek gedaan door:
- materiaalwetenschappers
- metallurgische en polymeeringenieurs
- experts op het gebied van scheikunde en elektrochemische processen
- experts op het gebied van storingsanalyse
- kwaliteitscontroleanalisten
- experts op het gebied van naleving van regelgeving
Dit is geen definitieve lijst, maar het geeft een goed beeld van de benodigde expertise om het proces uit te voeren, evenals het testdoel.
Het verschil tussen destructief en niet-destructief testen
Destructief testen wordt uitgevoerd door het monster dat wordt getest te beschadigen. Daarentegen loopt het geteste item tijdens niet-destructief testen (NDT) geen fysieke schade op en kan het na het testen in actieve werking worden gebruikt.
De volgende tabel toont de belangrijkste verschillen tussen de twee testmethoden.
Verschillen tussen destructief en niet-destructief testen
Houd er rekening mee dat DT en NDT over het algemeen voor verschillende doeleinden worden gebruikt. Hoewel destructieve tests kunnen worden gebruikt voor storingsanalyse, is het gericht op het waarborgen van de kwaliteit van het artikel vóór massaproductie.
Niet-destructieve tests worden uitgevoerd op componenten die in bedrijf zijn om vroege tekenen van degradatie op te sporen en apparatuurstoringen te voorkomen. Ze helpen onderhoudsteams om op conditie gebaseerd onderhoud en voorspellend onderhoud uit te voeren.
De noodzaak van destructief testen
Materialen die destructief worden getest, worden door de testprocedures beschadigd. Toch kent destructief testen veel legitieme gebruiksscenario's. Vaak zijn destructieve tests en het gebruik van materialen met specifieke kenmerken een wettelijke vereiste .
De realiteit is dat machines en materialen fysische en chemische eigenschappen hebben die niet voor alle omstandigheden geschikt zijn. Zo zijn metalen die gemakkelijk corroderen niet geschikt voor gebruik in extreem vochtige omgevingen.
Zelfs grote consumentenbedrijven zoals Apple vallen ten prooi aan het feit dat ze weinig aandacht besteden aan het testen van de duurzaamheid van het ontwerp van hun producten. De bendgate schandaal, waarbij iPhone 6 en 6s geneigd waren te buigen in krappe zakken, werd veroorzaakt door een nogal voor de hand liggende onoplettendheid en slechte buigtests uitgevoerd door hun ingenieurs of aannemers.
De meest voorkomende destructieve testmethoden
De meeste destructieve testmethoden hebben specifieke gebruiksscenario's. Als zodanig moeten ze bepaalde normen en best practices volgen. In de meeste gevallen worden deze tests echter gedaan om de mechanische eigenschappen van de monsters en hun robuustheid te bepalen.
In sommige gevallen moeten bedrijven aangepaste testmethoden ontwikkelen om te zien hoe hun producten/items zich onder verschillende bedrijfsomstandigheden gedragen.
Meer algemeen gebruikte destructieve testmethoden worden besproken in de volgende secties.
Corrosietesten
Messingmonsters na 5 dagen zoutsproeicorrosietest ( Afbeeldingsbron )
Metalen worden op grote schaal gebruikt in veel industrieën vanwege hun treksterkte en veelzijdigheid. Ze zijn echter ook gevoelig voor corrosie. Roest op materialen op ijzerbasis, aanslag op zilver, patina op koper en koperlegeringen zijn veelvoorkomende voorbeelden van corrosie. Dit is een probleem omdat corrosie de treksterkte en levensduur van deze metalen vermindert.
Corrosietesten is een testmethode die wordt uitgevoerd om de effectiviteit van toegepaste corrosieweerstandsmaatregelen te testen. Het omvat alle experimenten en processen om corrosiegerelateerde problemen te voorkomen of te verminderen. Het meten van de eigenschappen en de mate van corrosie kan ook worden beschouwd als onderdeel van corrosietesten.
American Society for Testing and Materials (ASTM International) heeft een uitgebreide reeks normen en testmethoden voor corrosie in verschillende metalen en omgevingen. Indien nodig kunnen indien nodig aangepaste protocollen worden ontwikkeld.
Hardheidstesten (HT)
Een indenter die wordt gebruikt voor het testen van de hardheid ( Afbeeldingsbron )
De materiaalhardheid bepaalt of onderdelen door spanning blijvend vervormen. Hardheid laat zien hoe effectief een materiaal bestand is tegen indrukking. Dit geeft aan hoe lang een onderdeel in gebruik kan zijn en hoe goed het na verloop van tijd zal presteren.
De Rockwell-schaal is een veelgebruikte maatstaf om de hardheid te indexeren ten opzichte van het referentiemateriaal. Een indringer wordt gebruikt om het materiaal met een constante kracht te penetreren. De penetratiediepte wordt geïndexeerd tegen de penetratiediepte in het referentiemateriaal. Dit type mechanische testen moet niet worden verward met impacttests die worden uitgevoerd met Charpy-testen.
Nogmaals, ASTM international biedt een breed scala aan standaarden en testprocedures om de hardheid van verschillende materialen te meten.
Tests op trek (rek)
Een trekproefdemonstratie ( Afbeeldingsbron )
Trekproeven worden uitgevoerd door gecontroleerde kracht op het testmateriaal uit te oefenen totdat het faalt (scheur, breuk, enz.). Het testexemplaar wordt samengedrukt of uitgerekt volgens de kenmerken die worden gemeten. Met trekproeven wordt de sterkte van het materiaal bepaald.
De gemeten eigenschappen zijn ultieme treksterkte, breeksterkte, maximale rek of reductie. Op basis van de metingen kunnen ingenieurs fysische eigenschappen berekenen, zoals de Young's modulus, Poisson's ratio, vloeigrens en rekhardende eigenschappen.
Deze eigenschappen worden gebruikt om te bepalen welke materialen moeten worden gebruikt wanneer er een grote hoeveelheid kracht moet worden weerstaan. ASTM International heeft verschillende normen en procedures voor verschillende soorten trekproeven.
Torsietesten
Een torsietestdemonstratie ( Afbeeldingsbron )
Torsietesten worden op dezelfde manier uitgevoerd als trekproeven. In plaats van compressie en rek worden torsiekrachten op het materiaal uitgeoefend. Dit helpt bij het bepalen van de schuifkrachten die het materiaal kan weerstaan voordat het vervormt.
Het punt waarop het materiaal draait en breekt, is het bezwijkpunt van het materiaal. ASTM en ISO schetsen beide normen en testprocedures voor verschillende materialen en gebruiksscenario's.
Stresstesten
Een onderdeel kan tijdens bedrijf verschillende soorten spanningen ondervinden. Stresstesten is een overkoepelende term die wordt gebruikt om een scenario te beschrijven waarin we een combinatie van verschillende testmethoden toepassen die in de vorige paragrafen zijn genoemd.
Het testen richt zich op de krachten die naar verwachting optreden tijdens reguliere operaties. Een torsietest is bijvoorbeeld geweldig voor een onderdeel dat als as van een elektromotor wordt gebruikt. Torsietests zijn echter nutteloos voor materiaal dat alleen drukbelastingen ondervindt.
Agressieve omgevingstests
Machines werken in verschillende omgevingscondities die worden beïnvloed door:
- temperatuur
- druk
- vochtigheid
- zoutgehalte
- blootstelling aan chemicaliën
- blootstelling aan andere elementen of natuurlijke krachten
Materialen worden getest op basis van de kenmerken van de omgeving waarin ze zullen werken. Bouwmaterialen die worden gebruikt om een strandhuis te bouwen, moeten bijvoorbeeld bestand zijn tegen het zoutgehalte, de vochtigheid, de wind en andere omgevingsfactoren van de kustregio.
Restspanningsmeting
Het boren van gaten als onderdeel van de restspanningsmeting ( Afbeeldingsbron )
Restspanning is de interne spanning die wordt ervaren door verschillende componenten zonder dat er externe belastingen aanwezig zijn. Het is een maatstaf die bepaalt of een onderdeel tijdens zijn levensduur bestand is tegen extreme belasting en stress.
Röntgendiffractie, neutronendiffractie en synchrotrondiffractie zijn drie complexe methoden die kunnen worden gebruikt om restspanning te meten.
Een eenvoudige techniek om een willekeurig gat in het materiaal te boren en het nieuwe spanningsevenwicht te testen, kan ook worden gebruikt om restspanning te meten (zoals te zien is in de afbeelding hierboven).
Destructief testen is essentieel voor de betrouwbaarheid van de machine
De betrouwbaarheid van de machine is sterk afhankelijk van de kwaliteit van de gebruikte componenten. Een asset is zo sterk als de zwakste schakel. Destructief testen zorgt ervoor dat alleen componenten met geschikte fysieke kenmerken in hun machines terechtkomen.
De juiste materialen en een goed productontwerp (een ontwerp met fouttolerantie en andere best practices) zijn de kenmerken van een kwaliteitsproduct, of dat nu een consumentenproduct of een industriële machine is.
Het resultaat van uitgebreide destructieve testen is belangrijk voor zowel fabrikanten van apparatuur als de onderhoudsteams die voor hen moeten zorgen. Deze resultaten worden immers ook gebruikt om zaken als bedrijfskenmerken, vervangingscyclus, onderhoudsvereisten, aanbevolen levensduur, enz. vast te stellen.
Zelfs artikelen van de beste kwaliteit ondergaan uiteindelijk regelmatig slijtage en misbruik. Onderhoudsprofessionals kunnen NDO-inspecties gebruiken om de actuele staat van hun assets in de gaten te houden.
In die zin spelen zowel niet-destructieve als destructieve testmethoden een cruciale rol bij de betrouwbaarheid van apparatuur, ook al worden ze op verschillende punten in de levenscyclus van de apparatuur gebruikt.
Onderhoud en reparatie van apparatuur
- Wat zijn de toepassingen van tantaal en zijn legeringen?
- Hafniumoxide en zijn structuur en toepassingen
- Wat is de werking van een afstandssensor en zijn toepassingen
- Wat is AD8232 ECG-sensor:werken en zijn toepassingen
- Wat is de HC-SR04 ultrasone sensor:werking en zijn toepassingen
- Werking van de spanningssensor en zijn toepassingen
- Lambdasensor – werking en toepassingen
- Wat zijn natuurlijke vezelcomposieten? Basisprincipes, toepassingen en toekomstige mogelijkheden
- Hoe IoT industrie 4.0 zal stimuleren en wat zijn de voordelen ervan?
- Wat zijn mallen en armaturen?
- 3D-printen:wat zijn de gevolgen voor bewerking en industrieel ontwerp?