Een hoger kaliber van machinegereedschap QC
Machine tool QC staat aan de vooravond van een ingrijpende verandering. Volgens Steffen Hailer, een productmanager en applicatie-ingenieur voor AfM Technology in Aalen, Duitsland, zal een binnenkort te verschijnen ISO-norm (ISO 230-13) het proces definiëren waarmee een werktuigmachine kan worden gekalibreerd zodat zijn indringende metingen kunnen worden geaccepteerd door de kwaliteitsafdeling.
Dit betekent niet dat de bewerkingsmachine altijd zo nauwkeurig zal zijn als een typische CMM. Maar de productie- en QC-afdelingen spreken dezelfde taal en de machinemetingen zijn bruikbaar voor QC. Dat biedt weer voordelen in een betere procesbeheersing en lagere kwaliteitskosten.
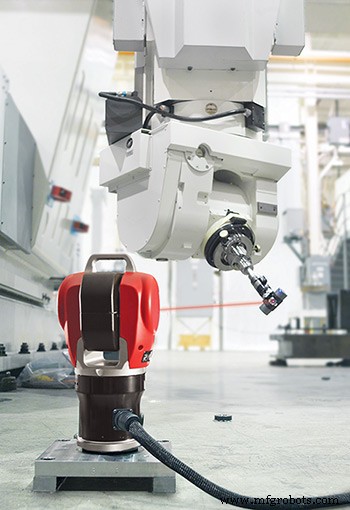
Volumetrische foutcompensatie (VEC) is misschien wel de belangrijkste factor die het voor een bewerkingsmachine mogelijk maakt om acceptabele kwaliteitscontrole uit te voeren. Maar zelfs als u nog steeds off-line apparatuur gebruikt voor eindinspectie (wat meestal het geval zal zijn), bieden de nieuwste methoden in VEC de beste manier om een hoge nauwkeurigheid te garanderen bij het produceren van complexe onderdelen.
Art Kietlinski, operations manager voor Automated Precision Inc. (API) van Rockville, Maryland, zei bijvoorbeeld dat het compensatiepakket van het bedrijf een vier- tot vijfvoudige verbetering zal opleveren in de volumetrische nauwkeurigheid van een meerassige bewerkingsmachine, en soms een nog grotere verbetering. “Normaal gesproken zien we vóór de kalibratie een machine met een maximale volumetrische fout aan de gereedschapspunt van bijvoorbeeld 0,3 tot 0,5 millimeter. En dan, na kalibratie, zitten we misschien rond de 0,075. Op een vijfassige machine bekijken en verbeteren we alle 43 mogelijke fouten.” [Zie "Machines eerlijk houden met geavanceerde kalibratie, optimalisatie", Manufacturing Engineering, juni 2019, voor een uitleg van de 43 mogelijke afwijkingen van bewerkingsmachines.]
API doet dit door een lasertracker te combineren met wat zij hun Active Target noemen, legt Ron Hicks, vice-president van productbeheer en marketing, uit. “Active Target is een kleine gemotoriseerde reflector die in de spindel is gemonteerd. Het stelt de lasertracker in staat om de positie van de gereedschapspunt van de machine nauwkeurig te meten vanaf een enkele instrumentpositie.” Dat is belangrijk, benadrukt Hicks, omdat het VEC-proces de spil tijdens het meetproces in realtime door alle assen van de machine beweegt. Dat zou niet mogelijk zijn met een standaard lasertrackerreflector, omdat de straal op verschillende punten in het volume van de machine zou worden onderbroken. Hicks voegde eraan toe dat “in tegenstelling tot conventionele laserprocessen, ons systeem niet hoeft te worden uitgelijnd op de hoofdassen van een werktuigmachine. Dit heeft enorme voordelen op het gebied van snelheid en nauwkeurigheid... We hebben twee machines op één dag kunnen compenseren.”
Het systeem van API meet "alle mogelijke machinehoudingen", voegde Kietlinski eraan toe, dus in een groot machinevolume (bijvoorbeeld 10 m) kan het wel 250 punten plotten. Van daaruit genereert de propriëtaire software coëfficiënten voor de polynomen die de nodige foutcorrecties voor elke as berekenen. Zoals Kietlinski uitlegde, is dit complexe wiskunde, omdat "de fouten niet noodzakelijk lineair zijn. Je zou kunnen eindigen met een polynoom van de tweede of derde orde waarvoor een oplossing moet worden gevonden.”
De fabriek van Northrop Grumman in Palmdale, Californië, is een van de vele succesverhalen, zei Hicks. De fabriek gebruikt grote vijfassige portaalmachines om alle trim- en gatenboringen voor de hele F-35-romp uit te voeren, en API-bezoeken per jaar om VEC op elke machine uit te voeren. Ondertussen zeiden Kietlinski, Lockheed Martin en Israeli Aerospace de vleugelsecties op horizontalen, die API ook bedient.
Er zijn grenzen. Een recent bezoek aan een bedrijf in Michigan dat hoogwaardige gereedschappen, prototypes en kleine productiecomponenten produceert, introduceert een waarschuwing.
Begrijpen van beperkingen
Kietlinski vertelde dat het bedrijf uit Michigan API had uitgenodigd om hun apparatuur te demonstreren op een vijfassige machine die al VEC had ondergaan op basis van een 21-foutkaart, "wat de norm is voor de meeste machines en CMM's." Zoals Kietlinski uitlegde:"al deze kalibraties gaan ervan uit dat de machine een star lichaam heeft, wat betekent dat alle hoekfouten hetzelfde zouden zijn tijdens de verplaatsing van die as door het volume. Dus ongeacht waar ik de X-as door het volume laat lopen, als ik pitch-, yaw- en roll-fouten zou meten, zou ik dezelfde hoekgegevens krijgen. Maar dat is niet altijd het geval op deze grotere machines.” Dat komt meestal doordat de rails niet evenwijdig zijn, zei hij. Dit veroorzaakt stress op de machine en het aandrijfsysteem, waardoor de "belastingsstromen stijgen en een aantal andere problemen".
Dus het eerste dat Kietlinski controleerde, was de rechtheid van de lineaire assen, wat minder dan een uur duurt met de lasertracker. Hij voegde eraan toe dat er meestal een directe relatie is tussen rechtheid en andere geometrische fouten, zoals pitch-, yaw-, roll- en haaksheidsfouten, "omdat je de haaksheid niet eens kunt beoordelen als je niet recht bent." In dit geval vond hij fouten tot 200 tot 250 micron (0,010”). API voerde een volledige uitlijning uit op de machine, "zelfs de brug losbrekend en mechanisch rechtzetten. Vervolgens hebben we de 21 foutencorrectiekaart toegepast. Op dit punt... waren de hoekfouten over de hele machine hetzelfde, en we waren in staat om de machine tienvoudig te verbeteren ten opzichte van de vorige kalibratie.”
Dat komt grotendeels door de verbeterde mechanische uitlijning, benadrukte Kietlinski. “Hoe beter je de machine mechanisch hebt uitgelijnd, hoe beter de resultaten van de kalibratie.” Omgekeerd:"je kunt niet een machine nemen die niet mechanisch is uitgelijnd en proberen alles met software te repareren."
Correctie van fouten tijdens het proces
Binnen de zojuist besproken limieten kan VEC een opmerkelijke verbetering aanbrengen in de geometrische onnauwkeurigheden van een machine. Maar hoe zit het met "werkonnauwkeurigheden", de extra fouten die optreden tijdens het bewerken, als gevolg van operationele spanningen, thermische instabiliteit en andere factoren? Bill Malanche, chief operating officer voor Mitsui Seiki (VS), Franklin Lakes, N.J., noemde de belangrijkste oorzaken van onnauwkeurigheid als "verloren beweging, hitte en ontwerp. Verloren beweging werkt zichzelf in vele aspecten, maar het kan worden samengevat door geometrische uitlijning en pasvorm." Nu VEC de andere factoren aanpakt, komt thermische instabiliteit naar voren als misschien wel de belangrijkste bron van fouten tijdens het proces. En hoe groter de machine, hoe meer variatie men kan zien in de werkelijke versus nominale gereedschapspositie.
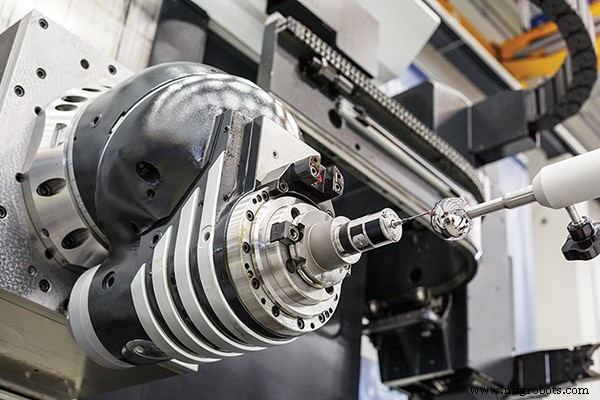
Een manier om met dit probleem om te gaan, is om de interne sonde van een machine te gebruiken om die afwijking te berekenen en deze vervolgens te compenseren. Doug Schulte, business development manager voor Select Machining Technologies, Windsor, Conn., zei dat hun Soraluce-machines "een kwalificatiegebied onderzoeken op een aantal vooraf ingestelde punten. Het doet dit voor veel hoofd- en asposities. Software vergelijkt vervolgens de gemeten punten met het kinematische model van de machine en maakt eventuele compensatie die nodig is om het middelpunt van het gereedschap in de geometrie van de machine te verzekeren.” Soraluce noemt deze functie Dynamic Head Calibration (DHC), en Schulte zei dat het een veelvoorkomend kenmerk is in vijfassige machines. [Manufacturing Engineering heeft de versie van Okuma behandeld in het artikel van juni 2019.]
Soraluce-machines zijn over het algemeen uitgerust met meerdere koppen met twee assen en DHC duurt 25 tot 30 minuten voor de hele meetcyclus. Het is ontworpen voor periodieke voorbewerkingscompensatie, zoals VEC. Maar Soraluce heeft een toegevoegde functie genaamd Accura Heads die mogelijke fouten tijdens het proces aanpakt, en het duurt slechts een minuut of twee om dit te doen. Deze optie gebruikt dezelfde taster en meetbol, maar loopt binnen het bewerkingsprogramma, legt Schulte uit.
“Als je een onderdeel wilt aanpakken dat zich in een specifieke hoek bevindt en die hoek is erg kritisch, dan kun je de Accura Heads-routine gebruiken om de hoek en de gereedschapspuntpositie van die specifieke oriëntatie te verifiëren. Dan maakt het die offset voor dat ene gereedschap. U doet die sondecyclus onmiddellijk voordat u die bewerking uitvoert."
Schulte gaf ook aan dat voor nauwere toleranties in bepaalde machineontwerpen, de gebruiker de bol dichter bij het gebied moet monteren waar ze gaan snijden, afhankelijk van de grootte van de machine. "Soraluce heeft machines gebouwd met een langsverplaatsing van meer dan 60 meter", voegde hij eraan toe. Men kan zich gemakkelijk voorstellen dat invloeden van buitenaf een afwijking kunnen veroorzaken tussen de werkelijke en nominale positionering zo ver weg.
De bewerkings-/QC-handdruk
Door een "gecompenseerde machine" als een gegeven te beschouwen, kunnen operators de mogelijkheid overwegen om de taster van een bewerkingsmachine te gebruiken om QC-functies uit te voeren. De nieuwe ISO 230-13-norm zal de vereisten definiëren, en zal dit doen onder verwijzing naar ISO 10360, de norm voor CMM's. De belangrijkste specificatie waarmee CMM's worden beoordeeld, is hun maximaal toelaatbare fout (MPE) waarde. Een acceptatietest zou zeven oriëntaties meten (vier lichaamsdiagonalen, plus één langs X, Y en Z) met ofwel een stappenmeter of een laser in combinatie met een meetbol. Om de test te doorstaan, mag de maximale afwijking (E0) niet groter zijn dan de MPE.
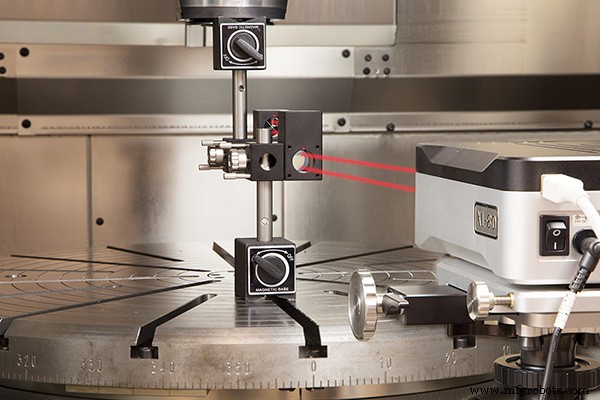
Zoals Hailer uitlegde, definieert de nieuwe ISO-norm de acceptatietestprocedure en de benodigde waarden net zo duidelijk voor werktuigmachines, maar het is een nieuw concept voor machinebouwers. “Op dit moment weet geen enkele machinebouwer hoe groot zijn MPE is. Ze moeten de procedure leren om zo'n waarde te bepalen, en dan uitzoeken wat het is. Dit is een van de diensten die we OEM's bieden.” Zodra een bouwer deze waarde voor een bepaalde machine heeft bepaald - en deze waarde ter plaatse is geverifieerd, net zoals u zou doen voor een CMM-installatie - kan een gebruiker een laatste onderdeelinspectie op de machine uitvoeren, deze nooit op een CMM plaatsen en het onderdeel afleveren aan een klant met een rapport dat de nauwkeurigheid van de metingen documenteert.
Of de MPE van een bewerkingsmachine acceptabel is voor de eindgebruiker, is een andere vraag. Maar het lijkt waarschijnlijk dat machines met een hogere precisie voor ten minste enkele toepassingen bevredigende QC zullen vervullen. Dat geldt met name voor zeer grote onderdelen, constateert Béat Ries, manager slijpproducten voor Mitsui Seiki. “Je betaalt veel geld voor een grote CMM, zeker als je naar ultrahoge nauwkeurigheid wilt gaan. De cijfers zijn astronomisch. Het lijkt erop dat niemand een economische oplossing kan bieden.”
Er is meer, zei Ries. Het kennen van alleen de MPE van een CMM of werktuigmachine is niet voldoende om te voldoen aan de lucht- en ruimtevaart- of automobielnormen. Dat komt omdat ze ook "een onzekerheidswaarde vereisen naast elke meting of validatie van onderdelen." Dus hoewel veel mensen de MPE alleen beschouwen als de "nauwkeurigheid" van een machine, geeft het cijfer niet de meetvariaties - en aanvullende onnauwkeurigheden - weer die in de echte wereld voorkomen. Ries legde bijvoorbeeld uit:"temperatuurschommelingen in een winkel zouden verschillende metingen opleveren. Dus als een CMM een MPE heeft van 1,9 plus L/250 micron, kan de berekende onzekerheid 3 micron per meter zijn. Als u meer dan één meter meet, suggereert de MPE-waarde dat u tot op 5,9 micron nauwkeurig bent. Maar als je de onzekerheidswaarde optelt, zie je dat je daadwerkelijk meet tot binnen plus of minus 8,9 micron.”
De micron splitsen
Een winkel die metingen uiterst serieus neemt, is de toepasselijke naam Precision Grinding Solutions (PGS) in Hamden, Conn. Eigenaar Curt Reed vindt het essentieel dat ze hun QC goed onder de knie hebben, inclusief onzekerheidsmetingen, omdat ze roterende onderdelen van straalmotoren slijpen. voor grote OEM's zoals Pratt &Whitney, plus Tier 1 en 2 lucht- en ruimtevaartleveranciers. PGS heeft zelfs een contract om meters te kalibreren voor meerdere Pratt-locaties.
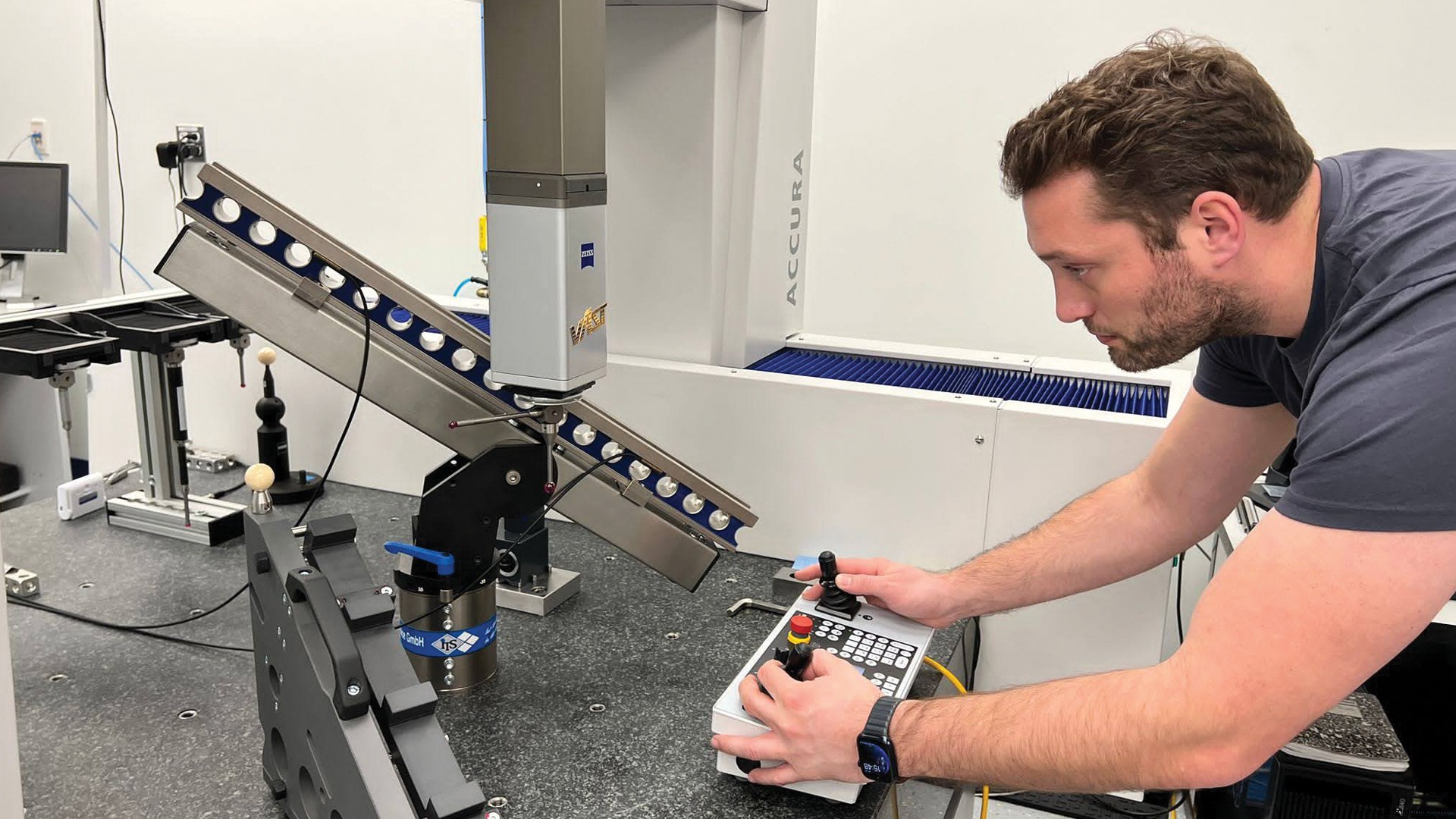
PGS heeft een Zeiss PRISMO ultra CMM, die Reed aanduidt als een “referentieklasse” machine. De CMM heeft een E0 van 0,5 + L/500 m, en PGS heeft het onzekerheidsbudget “op een van de ouderwetse manieren” bepaald. Je neemt een bekend artefact, bijvoorbeeld een van de Pratt-meters die we aan het kalibreren zijn, en meet een kritiek kenmerk ongeveer 50 keer. Vervolgens onderzoek je deze verspreiding van gegevens, houd je rekening met factoren zoals veranderingen in de kamertemperatuur, sluit je dat allemaal aan op een al lang bestaande formule en bedenk je een onzekerheidscijfer.”
Nu implementeert PGS een nieuwe methode om nog beter grip te krijgen op meetonzekerheid:Virtual CMM (VCMM). Reed legde uit dat VCMM een plug-inmodule is voor het Calypso executive-softwarepakket van Zeiss waarmee "u een andere kolom in uw rapporten kunt invoegen die de onzekerheid toont van elke afzonderlijke meting die u neemt." Daarnaast legt het ook alle andere fouten vast waar laserkalibratie geen rekening mee houdt, voegde Reed eraan toe.
PGS werkt samen met de AfM om de gegevens vast te leggen die nodig zijn voor deze inspanning, wat volgens Reed verder gaat dan het volgen van temperatuurschommelingen en trillingen. “Er wordt bijvoorbeeld rekening mee gehouden of je een lange stylus met een dunne schacht gebruikt, of een korte, stompe stylus. Hoe ziet de machinebuighandtekening eruit? Als je de machine meet, wat is dan de werkelijke geometrie, de schalen, de geleidingsbanen... Hoe ziet dat er allemaal uit?” De AfM zal dit allemaal bepalen door een reeks speciale metingen te doen met een reeks artefacten waarin verschillende ballen en stappen zijn verwerkt. Dan zullen foutbestanden op de achtergrond worden uitgevoerd om de onzekerheid te bepalen.
Samenvattend, zei Reed:"VCMM is een veel modernere, uitgebreidere manier om onzekerheid voor het hele systeem en het laboratorium te onderzoeken. Het is niet alleen gebaseerd op één artefact. Het kwalificeert zich door alle metingen die de AfM doet, en het kwalificeert het hele meetvolume van de CMM, niet slechts één lokaal gebied waar je een meter hebt getest."
Als het klaar is, merkte Reed op, zullen de nieuwe rapporten de kwaliteit van de foto slechter doen lijken, "omdat het functie voor functie beter werkt. Als u deze functie inschakelt, ziet u de onzekerheid van elke afzonderlijke functie die op elk programma wordt uitgevoerd. Dus als je iets meet dat 'tot op de micron' zou zijn geweest, en je voegt de onzekerheid toe, misschien is het 1,15 micron. Maar het levert een echt, waarheidsgetrouw onderzoek op van de onzekerheid van het hele systeem.”
Het systeem van Reed is al uitstekend. PGS heeft een topklasse CMM en het laboratorium is temperatuurstabiel tot op een derde van een graad F. Maar ze hebben andere investeringen gedaan om de onzekerheid te beperken:“We kochten AfM's software en meetartefacten om een betere controle te krijgen over de nauwkeurigheid van de machine. . We kochten ook een opstaprand van 700 millimeter die identiek is aan degene die door Zeiss-service wordt gebruikt. Het is onze bedoeling om te allen tijde te begrijpen waar de machine is.”
PGS vertrouwt niet langer alleen op jaarlijkse kalibraties van de OEM, deze zijn slechts een momentopname. Reed zei dat die bezoeken een aanzienlijk bedrag kosten en dat je je nog steeds afvraagt hoe de machine het hele jaar door presteert. "Als de OEM binnen een jaar terugkomt en de 'zoals gevonden'-kalibratie niet in de specificaties is, zet dit elk product dat u met de machine hebt geaccepteerd in twijfel. Dat risico willen we niet meer nemen. We proberen wekelijks of zelfs dagelijks onze CMM's te onderzoeken."
Onderhoud en reparatie van apparatuur
- Hoekbetrokkenheid:hoeken bewerken
- 10 belangrijke stappen voor het kiezen van een machineprognostisch hulpmiddel
- Draaibankmachinebewerkingen en draaibanksnijgereedschappen
- Bestellingen voor werktuigmachines nemen af in september
- Fuji introduceert multitasking-machine
- Methoden voor machinegereedschappen om Koch Machine Tool te verwerven
- Freescapaciteit van draaimolencentrum
- Draaicentrum en machinetechnologie
- 3 methoden voor het construeren van 5-assige CNC-tool
- Bewerkingsproces en werktuigmachines begrijpen
- Nieuw gereedschap toevoegen