Testmethoden van toezichthouders om prestaties te verifiëren
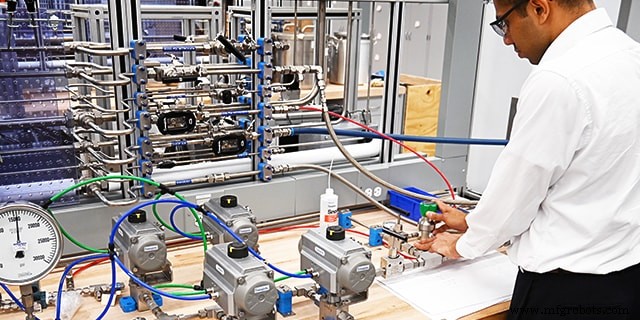
Waarom veilige prestaties van industriële drukregelaars rigoureuze tests vereisen
Tegendrukregelaars en drukreducerende regelaars worden gebruikt in een grote verscheidenheid aan industriële omgevingen over de hele wereld. Ze moeten vaak compromisloze prestaties leveren in zware omstandigheden, van hoge temperaturen nabij de evenaar tot veel koudere klimaten dichter bij de polen.
In deze omgevingen en tussenliggende omgevingen staat er veel op het spel als een regelgever faalt. Verlies van vloeistoffen in het milieu kan kostbaar zijn en door storingen veroorzaakt drukverlies kan de systeemprestaties in gevaar brengen en aanzienlijke veiligheidsrisico's veroorzaken.
Hoe kunt u vertrouwen hebben in de prestaties van de toezichthouder? Bij het selecteren en specificeren van drukregelaars voor uw industriële vloeistofsystemen kan het belangrijk zijn om uw leverancier te vragen hoe zij het bewijs van prestatie verifiëren. Regelgevers die bijvoorbeeld hoge prestaties laten zien in een reeks robuuste tests, kunnen worden vertrouwd om voor de lange termijn onder zware veldomstandigheden te werken.
Zorgvuldige engineering van regelgevers en goed doordachte, laboratoriumgebaseerde analyses kunnen tussen succes en mislukking staan. Laten we eens kijken naar de redenen waarom.
Regulator testmethoden
Niet alle leveranciers van regelgevers voeren tests uit in dezelfde hoedanigheid. Er is geen enkele standaardtest voor gemeenschappelijke prestatiekenmerken die in alle sectoren wordt erkend, en daarom is er grote variatie in de grondigheid van het testen van apparatuur tussen verschillende fabrikanten van regelaars.
Vraag uw leverancier bij het selecteren en specificeren van drukregelaars voor uw industriële vloeistofsystemen hoe deze het bewijs van prestatie verifiëren.
In plaats daarvan is een aangepaste benadering voor het testen van een reeks prestatiekenmerken nodig om er zeker van te zijn dat een regelaar zal presteren zoals beoordeeld wanneer de omstandigheden het meest extreem zijn. Een goede methode is om voorspellende modellen te gebruiken om prestatiekenmerken theoretisch te voorspellen en die theorieën vervolgens te bewijzen met behulp van praktische testmethoden. Enkele van de belangrijkste tests zijn:
Bursttesten . Een van de eerste en meest essentiële prestatiecriteria van een drukregelaar is het vermogen om zijn integriteit te behouden wanneer hij onder druk werkt. Burst-tests, die kunnen worden uitgevoerd bij drukken die de verwachte werkdruk van de regelaar ver overschrijden, kunnen ontwerpingenieurs helpen er zeker van te zijn dat hun producten zullen presteren in overeenstemming met hun drukclassificatie. De meest betrouwbare regelaars zijn vaak ontworpen om stabiele prestaties te leveren onder werkdrukken die meerdere malen hoger zijn dan de nominale druk.
De meest betrouwbare ademautomaten zijn vaak ontworpen om stabiele prestaties te leveren onder werkdruk die meerdere malen hoger is dan de nominale druk.
Vloeibare dynamische tests . Overweeg een drukverlagende regelaar die de druk moet verlagen van 6000 psi bij de inlaatstroom tot 100 psi bij de uitlaatstroom. Om een stabiele, betrouwbare uitlaatdruk te garanderen, is het belangrijk voor ontwerpers om mogelijke snelheidsvalkuilen of drukopbouwplekken in de regelaar te identificeren. Omdat de regelaar zelf de beoogde uitlaatdruk bij het membraan meet, kunnen zelfs kleine inconsistenties in het interieurontwerp drukverliezen bij de uitlaatstroom veroorzaken en tot ondermaatse prestaties leiden.
Computational fluid dynamics (CFD) en praktische stromingstests zijn enkele van de belangrijkste methoden waarmee fabrikanten de drukzones in de regelaar onderzoeken om ervoor te zorgen dat het apparaat de uitlaatdruk nauwkeurig afleest en daardoor regelt volgens de systeemspecificaties. CFD gebruikt numerieke analyse en datastructuren om problemen met vloeistofstromen en -drukken te analyseren en op te lossen. Door deze potentiële invloeden op de druk te identificeren, zijn ontwerpers beter in staat om een regelaar nauwkeurig te ontwerpen om ervoor te zorgen dat de werkelijke uitlaatdruk overeenkomt met de productclassificatie, wat uiteindelijk een indicator is voor de kwaliteit van de regelaar.
Beproeving van effect van voedingsdruk . Toevoerdrukeffect (SPE), ook wel inlaatafhankelijkheid genoemd, is een verandering in uitlaatdruk als gevolg van een verandering in inlaatdruk. Als de inlaatdruk daalt, zal er een overeenkomstige toename van de uitlaatdruk zijn. Omgekeerd, als de inlaatdruk toeneemt, neemt de uitlaatdruk af.
SPE heeft tot op zekere hoogte invloed op de meeste regelgevers - en het is de verantwoordelijkheid van de fabrikant om dit adequaat te voorspellen en te minimaliseren. De meeste leveranciers zullen klanten een cijfer geven dat de verandering in uitlaatdruk per verandering in inlaatdruk beschrijft. Om de kleinst mogelijke, meest nauwkeurige waarde te bieden, is SPE-testen een essentieel onderdeel van de engineering en het ontwerp van regelaars.
Test van levenscycluselementen . Eenmaal geïnstalleerd, mogen operators verwachten dat een regelaar jaren van prestaties levert over vele bedieningscycli. Om er zeker van te zijn dat een ademautomaat dat soort prestatie-levensduur zal bereiken zoals ontworpen, kan een reeks levenscyclustests worden toegepast.
Levenscyclustesten kunnen worden uitgevoerd als een banktest waarbij technici een reeks verschillende cyclusbelastingen uitvoeren, soms tot 120 cycli per seconde. Het doel is om te bepalen wanneer en waar een ademautomaat slijtage kan gaan vertonen die de prestaties kan beïnvloeden. Gewapend met deze kennis kunnen ingenieurs regelaars robuuster ontwerpen tegen voorspelbare slijtagepatronen.
Beheerders mogen verwachten dat een regelaar jaren van prestatie levert over miljoenen bedieningscycli.
Thermische tests . Aangezien van drukregelaars wordt verwacht dat ze presteren onder een reeks verschillende omgevingsomstandigheden, is het testen van de prestaties van de volledige regelaar onder verschillende thermische omstandigheden een essentieel onderdeel van een goede productontwikkeling en ontwerp.
Roestvrijstalen drukregelaars worden bijvoorbeeld vaak gebruikt in een reeks algemene industriële toepassingen en bieden onder de meeste omstandigheden voorspelbare prestaties. Extreem hoge en lage temperaturen kunnen echter de afdichtingsprestaties beïnvloeden. Zeer hoge temperaturen kunnen ervoor zorgen dat bepaalde elastomere materialen opzwellen; zeer lage temperaturen kunnen ervoor zorgen dat materialen verstijven en krimpen. Elke omstandigheid kan een betrouwbare afdichting en dus betrouwbare prestaties van de regelaar in gevaar brengen.
Wat het testen van robuuste regelaars voor u betekent
Real-world prestaties zijn de ultieme maatstaf voor succes voor elk onderdeel van een industrieel vloeistofsysteem. Drukregelaars moeten dus optimale resultaten kunnen leveren voor operators, zodat de systeemdruk precies zo nodig, veilig en betrouwbaar kan worden geregeld.
Het productontwerp en de testprotocollen van een fabrikant dicteren het vermogen van een regelgever om precies dat te doen. Bij het selecteren en specificeren van regelaars voor uw systeem, is het de moeite waard om uw leverancier van regelaars te raadplegen om te bespreken hoe hun producten zijn ontworpen en getest om te voldoen aan de strengste real-world prestatie-uitdagingen. Het is een gesprek dat onze regulatorspecialisten bij Swagelok graag voeren. Met ervaring in een breed scala van verschillende industriële regelaartoepassingen, kunnen we u helpen uw behoeften op het gebied van drukregeling te evalueren en een oplossing te vinden die het beste bijdraagt aan uw voortdurende succes.
Industriële technologie
- SaaS- en cloudbeveiliging toevoegen met testen en automatisering
- Spanningsregelaar
- JFET-stroomregelaar
- De voordelen van DevOps beoordelen voor het testen van IoT-prestaties
- Beschadigd anker:veelbetekenende tekens en testmethoden
- Wat is niet-destructief testen (NDT)?- Methoden
- PCB-ionische verontreinigingstests
- Gids voor PCB-testmethoden
- Nieuwe diagnostische techniek voor thermische golven bevordert het testen van batterijprestaties
- Ken de verschillende testmethoden voor PCB's
- Drukregelmethoden voor persluchtsystemen