Hitachi-poedervormmetaal omarmt robotautomatisering, verhoogt volume met 400 procent in krappe arbeidsmarkt
Poedermetallurgie (PM), of sinteren, is het proces van het samenpersen van aangepaste mengsels van elementaire of legeringspoeders in geprefabriceerde matrijzen om efficiënt machineonderdelen van verschillende complexiteit te maken. Eenmaal verdicht, worden de vormen verwarmd in een oven met gecontroleerde atmosfeer om de deeltjes te binden en de onderdelen te verharden.
Het proces, ook wel bekend als groen verdichten, levert bijna netto componenten op die doorgaans meer dan 97 procent van de oorspronkelijke grondstof in het afgewerkte onderdeel gebruiken. Aangepaste mengsels van poederlegeringen bieden de mogelijkheid om complexe, zelfs ingewikkelde onderdelen te produceren die voldoen aan de sterkte- en tolerantiespecificaties die vereist zijn voor zeer veeleisende toepassingen.
De fabriek van Hitachi Powdered Metal (VS) Inc. in Greensburg, Ind. is een van de negen van dergelijke Hitachi-vestigingen wereldwijd. Het is gespecialiseerd in het produceren van kleppentrein- en transmissiecomponenten voor autofabrikanten in de VS, met een groeiende aanwezigheid bij fabrikanten van motorfiets- en landschapsuitrusting.
Initiële motivatie
Hitachi Powdered Metals (HPM) begon in 2005 met een geleidelijke investering in industriële robots in de fabriek in Greensburg, gedreven door de opkomst van een krapper wordende arbeidsmarkt en de mogelijkheid om een uiterst kwetsbaar product te produceren.
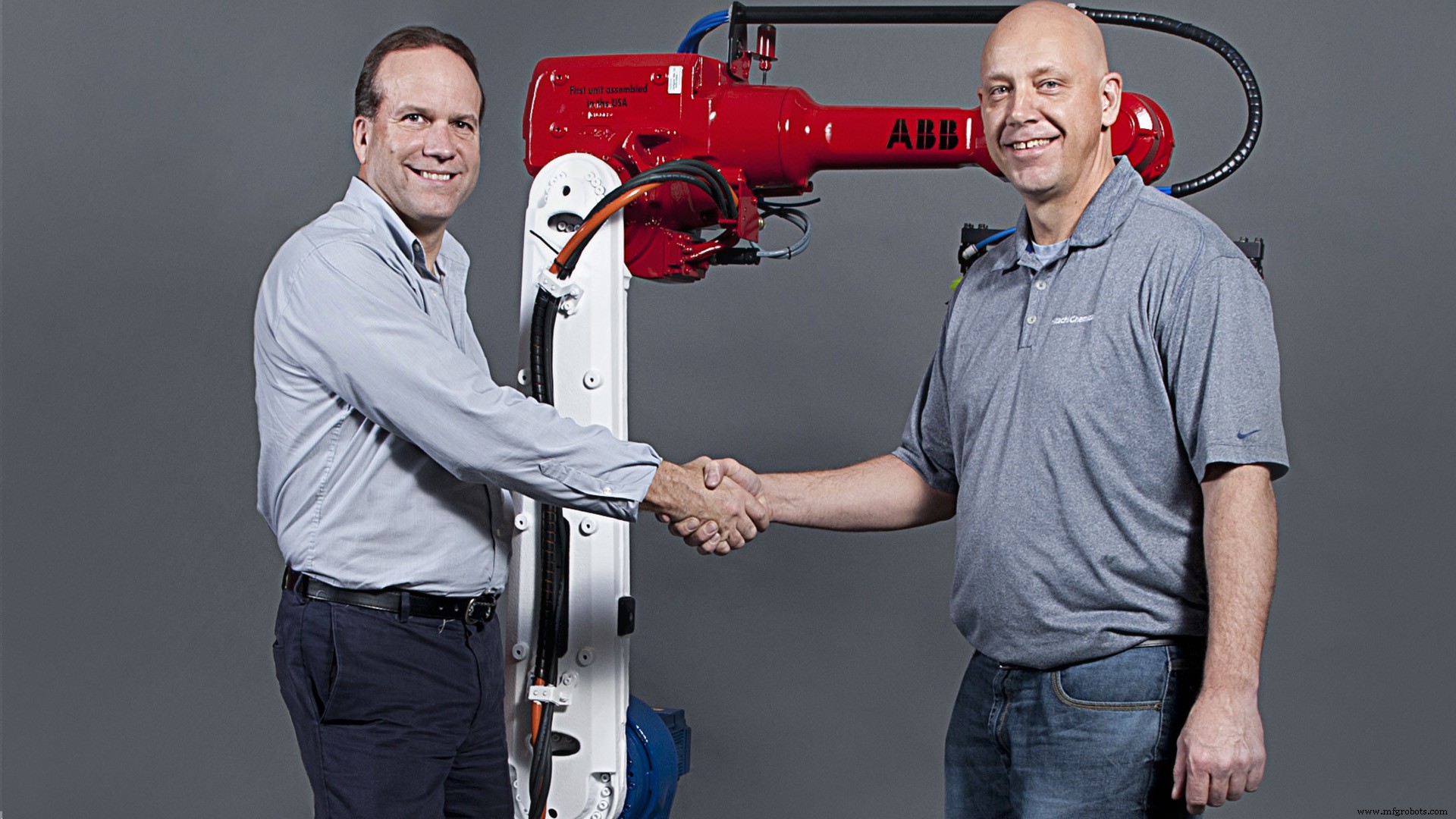
"We zijn begonnen met robots omdat we een onderdeel moesten maken voor een klant met kleine, fragiele tanden die niet handmatig konden worden gehanteerd, en op dat moment werden al onze persen met de hand onderhouden", zegt Gregory Owens, president van de HPM Greensburg-fabriek. "Het verlagen van de arbeidskosten was ook een factor, maar kort na de eerste installatie opende een grote OEM in de auto-industrie een productiefaciliteit in de stad, en ons probleem met de arbeidskosten veranderde in een probleem met de beschikbaarheid van arbeid omdat het extreem moeilijk werd om werknemers aan te nemen en te behouden."
In een poging om de kosten laag te houden en blootstelling tijdens de eerste proefperiode tot een minimum te beperken, kocht HPM een gebruikte, vintage 1993 ABB S3-robot van CIM Systems Inc. in het nabijgelegen Noblesville, Ind. James Adams, die enkele jaren eerder bij HPM was gekomen als een ingenieur voor productieontwikkeling, kende CIM, de langstlopende ABB Robotics Value Provider (d.w.z. systeemintegrator) in de VS, van zijn werk met robots bij zijn vorige werkgever.
"CIM had een gebruikte robot waarmee we onze weg naar robotautomatisering konden vergemakkelijken, waardoor onze initiële blootstelling zou worden beperkt voor het geval het niet zou presteren zoals bedoeld", zei Adams. "Ze hebben ons ook de broodnodige ondersteuning geboden bij het programmeren en integreren van het systeem in de bestaande operatie."
Minder afval, betere arbeidsverdeling
Wanneer de verpoederde metalen onderdelen uit de pers komen, voordat ze in de oven worden uitgehard, kunnen ze gemakkelijk afbrokkelen, zelfs bij de lichtste aanraking. Met de nieuw geïnstalleerde robot, met een elektrische magnetische grijper om het onderdeel te hanteren, ging het afvalpercentage van het nieuwe product van 11 procent terwijl het handmatig naar 0,5 procent ging.
“Toen de onderdelen met de hand uit de pers werden getrokken, was er behoorlijke handelingsschade. Het onderdeel kan onmerkbaar vervormd zijn, maar je zou het pas weten als het vijf uur later uit de oven kwam. Goed geprogrammeerd en uitgerust, zijn robots veel zachter in het omgaan met de onderdelen”, zegt Adams.
Het nieuwe systeem stelde HPM in staat om verschillende handmatige machinehandlers naar minder alledaagse posities in de fabriek te verplaatsen, waardoor de stress van een repetitieve taak werd verminderd en de arbeid op een efficiëntere manier kon worden toegewezen.
Productie stijgt met 400 procent
In het volgende jaar voegde HPM nog vijf gebruikte S3-robots toe en paste wat het van het oorspronkelijke systeem had geleerd toe om andere compacte persen te automatiseren. Na 18 maanden had HPM genoeg op schroot en arbeid bespaard om te investeren in zijn eerste nieuwe robot.
Snel vooruit naar 2019. Nu met meer dan 200 robots geïnstalleerd, heeft de Greensburg-faciliteit hetzelfde aantal werknemers als 10 jaar geleden, maar produceert vier keer zoveel volume, waardoor gemakkelijk meer onderdelen kunnen worden geleverd met minder mensen dan alle wereldwijde Hitachi PM-fabrieken .
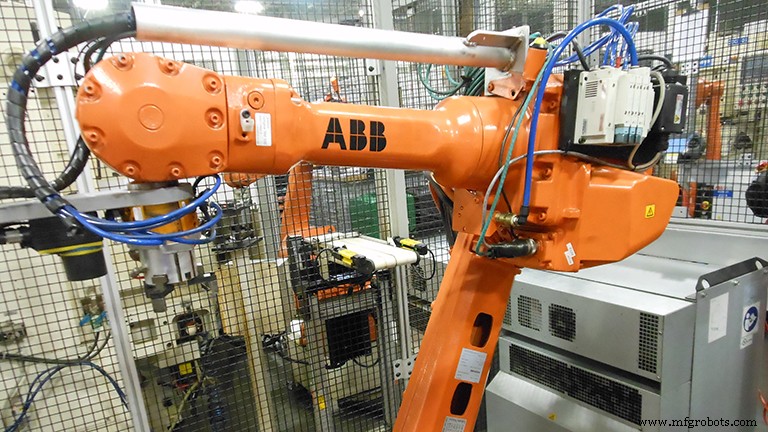
"Toen de eerste robot voor het fragiele onderdeel was geïnstalleerd, werd het heel duidelijk dat we echt konden profiteren van verdere robotautomatisering", zei Owens. "Robots hebben onze aanvankelijke verwachtingen ver overtroffen, en met de arbeidstekorten waarmee we nog steeds worden geconfronteerd, geloof ik eerlijk gezegd dat robots ons hebben gered van mogelijk niet bestaand."
Met het succes van de eerste robot was het tempo van de volgende installaties stabiel. Het duurde tien jaar om 100 geïnstalleerde robots te bereiken, en toen het bedrijfsleven en de economie bleven verbeteren, waren er nog maar vier jaar om de onlangs geïnstalleerde 200 e te bereiken robot.
Toen de kansen zich voordeden, bleef HPM gebruikte ABB-robots in goede staat kopen, hoewel er steeds meer nieuwe robots aan de vloot werden toegevoegd. In feite is elke robot die sinds #147 in 2015 is toegevoegd, nieuw.
De installatiebasis van HPM omvat een reeks ABB kleine en middelgrote zesassige robots, een Delta-robot en verschillende recent toegevoegde SCARA-modellen. Samen met 350 medewerkers wordt de automatiseringsinvestering goed benut, met drie ploegen van vijf tot zes dagen per week.
"Ons hoofdkantoor bevindt zich in Japan", zegt Adams. "Toen ze zagen hoe de robots presteerden en de snelle return-on-investment, waren ze een groot voorstander van onze robotica-agenda."
Sommige van de robots, zowel nieuw als gebruikt, zijn ABB Foundry Prime van ABB Robotics, Auburn Hills, Michigan. Het zijn IP67-geclassificeerde modellen met goed afgedichte verbindingen die de binnenkant van de robot beschermen tegen het fijne, scherpe metaal poeders die door de plantenatmosfeer zweven. De vele standaard robotmodellen met IP65-classificatie op de HPM-vloer zijn robuust en bestand tegen de stoffige omgeving.
Voortdurende uitbreiding
De verspreiding van robots bij HPM werd ondersteund door bestaande applicaties te repliceren en de automatisering uit te breiden naar andere functies in de faciliteit.
Na de installatie van de eerste robot die de compactpers voor het meest kwetsbare product verzorgde, automatiseerden Adams en zijn team achtereenvolgens de verwijdering van de compacts van andere persen. Onderdeel van dit proces was om elk onderdeel op een schaal te plaatsen om de integriteit ervan te verifiëren. Eenmaal geverifieerd, werd het onderdeel op een transportband geplaatst die naar de oven leidde.
Het resultaat was extra arbeidsefficiëntie en met de behendige aanraking van de robot ging het uitvalpercentage van de minder kwetsbare onderdelen van 7 procent naar dezelfde 0,5 procent van het oorspronkelijke onderdeel.
Aan het einde van de transportband worden de onderdelen op sinterbakken geplaatst die, wanneer ze gevuld zijn, in ovens worden geplaatst voor het uithardingsproces. Dit ovenlaadproces werd de tweede belangrijke functie die geautomatiseerd werd.
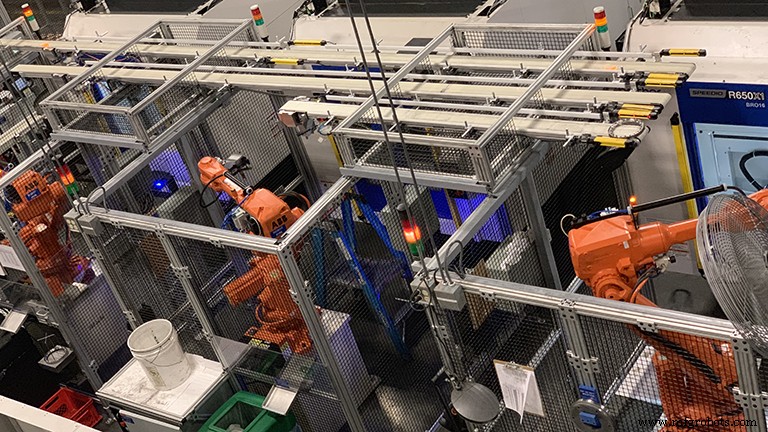
Vervolgens werden in een afgemeten tempo robots geïnstalleerd om de onderdelen van de trays te halen en op pallets te plaatsen, terwijl er ook tussenschotten tussen elke palletlaag werden aangebracht.
"Naarmate we meer vertrouwd raakten met robots, namen we wat we leerden en dupliceerden applicaties in de hele faciliteit", zegt Adams. "Programmeren werd veel eenvoudiger, en op de laatste dag van de installatie van de regel pasten we bestaande programma's aan, kopieerden en plakten we en binnen een paar uur waren we aan de slag."
RobotStudio, ABB's offline simulatie- en programmeersoftware, werd een waardevol hulpmiddel bij het versnellen van HPM's toenemende acceptatie van robottechnologie. Gebouwd op de ABB VirtualController, een exacte kopie van de echte software die robots in productie laat draaien, voert RobotStudio realistische simulaties uit, met behulp van robotprogramma's en configuratiebestanden die identiek zijn aan die op de werkvloer. Met RobotStudio was Adams in staat om de optimale cellay-out te ontwerpen en de prestaties ervan te verifiëren voordat de robots in een bepaalde operatie werden geïntegreerd.
"Het is de beste software die ooit is ontwikkeld", zegt Adams. "Het bespaart tijd en geld, zowel bij het maken van systemen voor nieuwe toepassingen als bij het repliceren van systemen die we al in andere delen van de fabriek hadden geïnstalleerd."
Introductie van visie
De relatieve eenvoud van replicatie bestaat pas nadat een bepaalde toepassing op de fabrieksvloer is geïnstalleerd en verfijnd. Nieuwe toepassingen zijn vaak uitdagender. Na 18 maanden en de succesvolle integratie van zes robots voor het verzorgen van de pers, had HPM het vertrouwen om vision-enabled technologie toe te passen, in de kinderschoenen van die tijd (2006), om de complexe muntbewerking, of onderdrukking, robotisch te automatiseren.
Nadat onderdelen uit de oven komen, kunnen ze vaak kromtrekken, waardoor ze in een pers moeten worden geplaatst die ze weer recht of plat maakt. Veel onderdelen hebben spiebanen of tanden die in de mal moeten worden geplaatst met alle aspecten precies op één lijn. Vóór de komst van de robots werden de onderdelen die werden bedacht verwerkt door een hard automatiseringssysteem dat, met veel verschillende productvariaties, frequente, tijdrovende omschakelingen vereiste. De omschakelingen duurden zo lang dat back-ups van 250 productpartijen, elk met ongeveer 100 onderdelen, gebruikelijk waren.
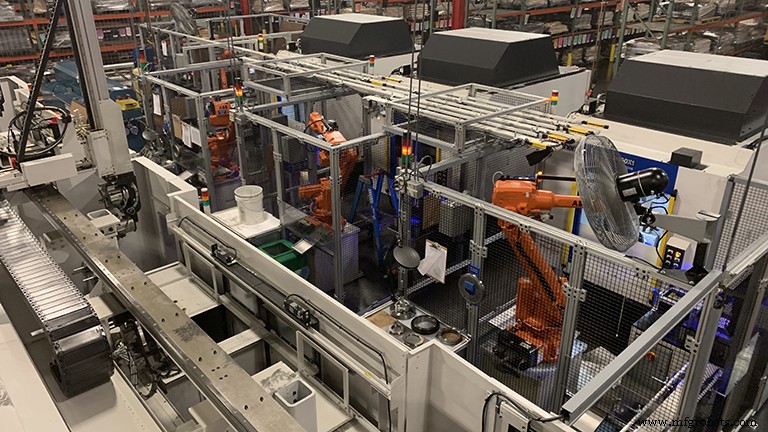
Met de vision-enabled robot is er geen uitvaltijd. De robot kan het onderdeel identificeren uit een groep van veel verschillende onderdelen, het oppakken, radiaal oriënteren en nauwkeurig positioneren in de repressie.
Omdat het vision-systeem moest aansluiten op de nieuwste robottechnologie, was dit de eerste nieuwe ABB-robot die in de fabriek in Greensburg werd geïnstalleerd. Kort nadat het operationeel was, werden nog twee nieuwe robots gekocht voor dezelfde toepassing.
"Voor de installatie van de muntstationrobot was het repressiepersoneel elke dag aan het werk", zegt Adams. "Zes maanden nadat de eerste vision-robot was geïnstalleerd, waren er geen back-ups meer en hadden de medewerkers hun weekenden vrij!"
Verdere visie
HPM gebruikte later vision opnieuw in de laatste van de belangrijkste processen die moesten worden geautomatiseerd, het depalletiseren van onderdelen die waren verzonden voor gespecialiseerde warmtebehandeling. Hoewel de onderdelen netjes op gelaagde lagen op een pallet worden verzonden, komen ze relatief wanordelijk terug en zijn ze moeilijk te ontstapelen. Een ABB-robot met geïntegreerd zicht kan de onderdelen vinden en stevig vastpakken, zodat ze veilig van de pallet kunnen worden gehaald.
"Dat is een van de unieke mogelijkheden van ABB-robots", zegt Dave Fox, president van CIM Systems, die hielp bij het integreren van de verschillende vision-systemen. "De onderdelen zijn echt gedesoriënteerd op de skids, niet in uniforme rijen, met sommige ondersteboven. Een typische robot met zes assen zou allerlei singulariteitsproblemen hebben en in een positie komen waar hij niet langer kan bewegen. Maar de ABB-robot die geavanceerde singulariteitsvermijding gebruikt, kan de onderdelen vinden, ze pakken en veilig op een transportband plaatsen zonder iets te missen.”
SCARA-robots voor kwaliteitsinspectie
Het is niet verrassend dat een recente zoektocht naar een efficiënter systeem voor het inspecteren van klepgeleiders leidde tot robots, in dit geval een groep ABB SCARA-modellen (Selective Compliance Assembly Robot Arm), die doorgaans worden gebruikt voor de assemblage van kleine onderdelen en materiaalbehandeling.
Het HPM-protocol vereist 100 procent inspectie van alle klepgeleiders, wat een hele onderneming is gezien de verscheidenheid aan onderdelen die getest moeten worden:30 verschillende maatvariaties en 16 detectiepunten voor elk onderdeel. Omdat het heersende testsysteem voor harde automatisering het volume niet voldoende kon bijhouden, ging Adams op zoek naar een beter systeem.
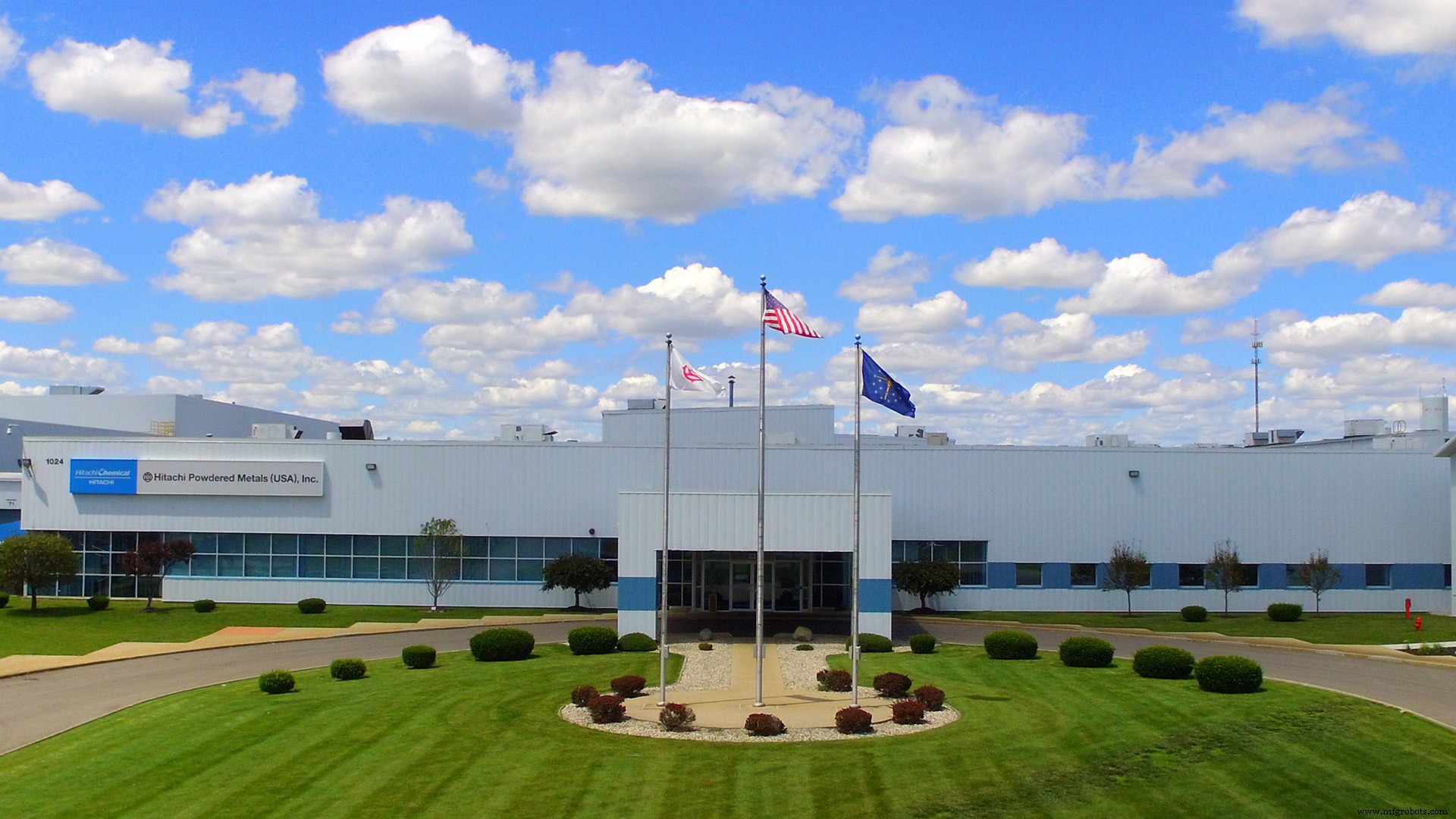
Na verschillende opties te hebben bekeken, die allemaal te veel bewegende delen hadden en complexe engineering vereisten, stelde Fox voor een systeem te ontwerpen rond de SCARA-robots, die ABB in 2016 aan zijn portfolio heeft toegevoegd. Ze waren zeker snel genoeg, met een grote herhaalbaarheid en hadden een kleine footprint en een ongehinderde vorm van montage die passen in een kleine ruimte.
Er werd een relatief eenvoudig systeem ontworpen met drie SCARA-robots die individuele klepgeleiders van een hoppertransporteur plukken en deze presenteren aan visioncamera's en een stationaire "comparator" onder de verschillende hoeken die nodig zijn om toegang te krijgen tot de 16 detectiepunten. De onderdelen die passeerden, werden op één transportband geplaatst en de onderdelen die dat niet deden, werden in uitwerpbakken geplaatst.
Met de flexibiliteit om elke verschillende onderdeelvariatie met hetzelfde gemak behendig te behandelen, kan het systeem elke twee seconden een onderdeel inspecteren, 30 procent sneller dan de vorige methode. Omdat de bewegingen beperkt zijn tot een korte afstand en de onderdelen erg licht zijn, zou een robot met zes assen niet zo effectief werken als de gestroomlijnde SCARA met beperkt bereik.
“De SCARA's zijn een geweldige aanvulling op de ABB-portfolio. Als die oplossing er niet was geweest, had Hitachi waarschijnlijk een andere technologie moeten gebruiken voor de inspectie van onderdelen”, aldus Fox. “Het was fijn om een andere toepassing voor robots te kunnen vinden, ook al was dat niet de eerste optie die in me opkwam.”
CIM-systemen altijd aanwezig
Een constante die vanaf de eerste robot die bij HPM is geïnstalleerd tot op de dag van vandaag aanwezig is, zowel op de voorgrond als op de achtergrond, is CIM Systems. CIM is altijd beschikbaar wanneer dat nodig is en heeft HPM opgezet met nieuwe en gebruikte robots, geholpen bij het programmeren en oplossen van problemen, en misschien wel het allerbelangrijkste, het HPM-personeel heeft geleerd veel dingen zelf te doen.
Toen HPM robots integreerde in een nieuwe applicatie, al dan niet met visie, deed CIM de set-up en programmering, waarbij ze altijd bedachtzaam waren om hun expertise te delen, inclusief het gebruik van RobotStudio. Tijdens de incidentele stilte in HPM's tijdlijn voor het verwerven van robots, was CIM beschikbaar om programma's bij te werken, ongrijpbare reserveonderdelen voor oudere modellen te vinden of advies te geven over het werken met robots in verschillende jaren.
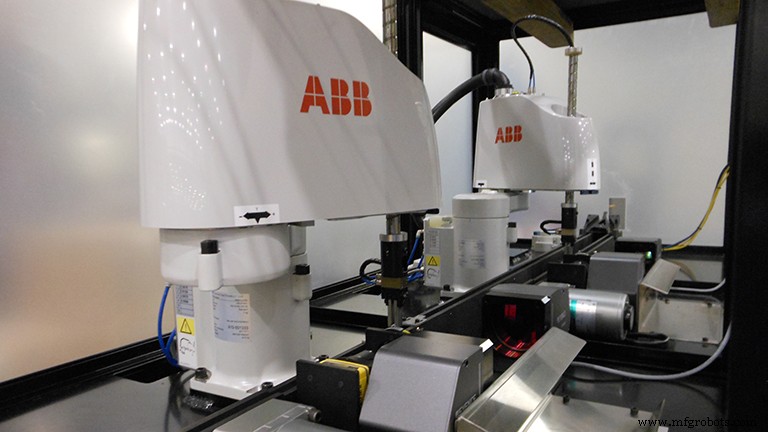
“Omdat we elk van de verschillende processen raakten, lieten we CIM de initiële integratie en programmering doen. Toen we eenmaal begonnen met het repliceren van processen in de hele fabriek, hadden we genoeg geleerd om veel zelf te doen”, aldus Adams. “Door zijn nauwe relatie met ABB weet Dave Fox altijd wanneer er nieuwe technologie op komst is en welke robots optimaal zijn voor onze verschillende toepassingen. De ondersteuning die we kregen van CIM Systems en de service van ABB was een ideale combinatie.”
Met zo'n langdurige relatie is het geen verrassing dat toen de eerste robot in 2017 van de band rolde in de Amerikaanse productiefaciliteit van ABB in Auburn Hills, deze in opdracht van CIM bij HPM werd uitgevoerd. De unieke IRB 2400-robot is in de fabriek op maat rood, wit en blauw geverfd en staat prominent op de HPM-faciliteit, waar hij inspectie- en palletiseertaken uitvoert.
"We zijn verheugd dat we de eerste in Amerika gemaakte robot voor HPM hebben kunnen aanschaffen", aldus Fox. "Het is vooral belangrijk omdat de fabriek in Indiana de meest flexibele automaat heeft van de vele wereldwijde faciliteiten van HPM."
Ondersteuning van andere HPM-faciliteiten
Het bedrijfsmanagement van HPM in Japan heeft kennis genomen van de grote productiviteitsverbeteringen die het Greensburg-team met robots heeft bereikt, en in 2017 hebben Adams en Owens de opdracht gegeven om een 'Global Robotics'-initiatief te leiden om de andere poedermetaalfabrieken van Hitachi over de hele wereld te ondersteunen, hun gebruik van robots uit te breiden .
Het tweejarige programma is voorbij het midden en de aangesloten bedrijven beginnen aanzienlijke productiviteitsverbeteringen te realiseren, zelfs met de lagere arbeidskosten in de andere landen.
Adams heeft ABB's Remote Monitoring-functie bij HPM opgezet, zodat hij of leden van zijn team kunnen zien hoe robots werken en de meeste problemen van overal buiten de fabriek kunnen oplossen op een laptop, tablet of smartphone. Met de nieuwere robots hoopt HPM te profiteren van ABB Ability Connected Services - ABB's uniforme, sectoroverschrijdende, digitale aanbod - dat realtime gegevens biedt over de robotstatus en -prestaties vanaf elke locatie.
Toekomstplannen
De voortdurende missie van HPM omvat het verbeteren van haar activiteiten met robotautomatisering.
"We verwachten in de nabije toekomst met 10 procent per jaar te groeien en we moeten er alles aan doen om concurrerend te blijven", aldus Owens. “We bekijken welke transmissieonderdelen we kunnen maken voor elektrische voertuigen en hebben onze zinnen gezet op het doordringen van niet-automobielsegmenten zoals zwaar materieel, waar poedervormig metaal onderdelen van andere materialen tegen lagere kosten kan vervangen. .”
"Ik verwacht zeker dat het tempo van robotinstallaties stabiel zal blijven of zelfs zal toenemen", zei Owens.
Ga voor informatie over Hitachi Powdered Metals (USA) Inc. naar www.hitachi-pm.us of bel 812-663-5058. Ga voor informatie over CIM Systems Inc. naar www.cimrobotics.com of bel 317-773-5600. Ga voor informatie van ABB Robotics naar www.abb.com/robotics of bel 248-391-9000.
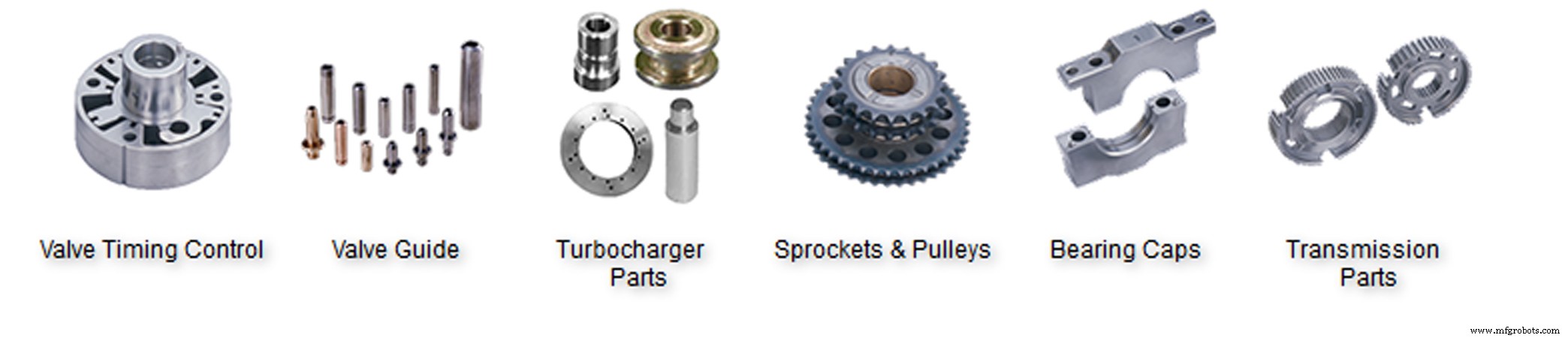
Automatisering Besturingssysteem
- Logistiek en magazijnautomatisering
- Meer automatisering =meer capabele robots
- NPE2018:Robots en automatisering pakken toenemende complexiteit aan
- Automatisering:compatibel ontbraamblad voor robots
- ABB voorspelt belangrijke trends die robotautomatisering in 2022 zullen veranderen
- Een nieuw type robotbrein kan moderne fabrieken transformeren
- Hitachi neemt robotsysteemintegrator JR Automation over voor $ 1,4 miljard
- Hitachi voltooit overname van JR Automation
- ATI Industrial Automation lanceert nieuwe vlakschuurmachine voor robots
- Robotische procesautomatiseringsmarkt om impuls te krijgen van Blue Prism's digitale personeelsbestand en zijn uitzonderlijk beveiligde automatisering
- Markt voor robotprocesautomatisering groeit met $ 750 miljoen