Inleiding tot 3D-printen van metaal
3D printen of CNC? Vind de beste technologie om uw metalen onderdelen te produceren
Download onze gids over het produceren van metalen onderdelen
SLM &DMLS:wat is het verschil?
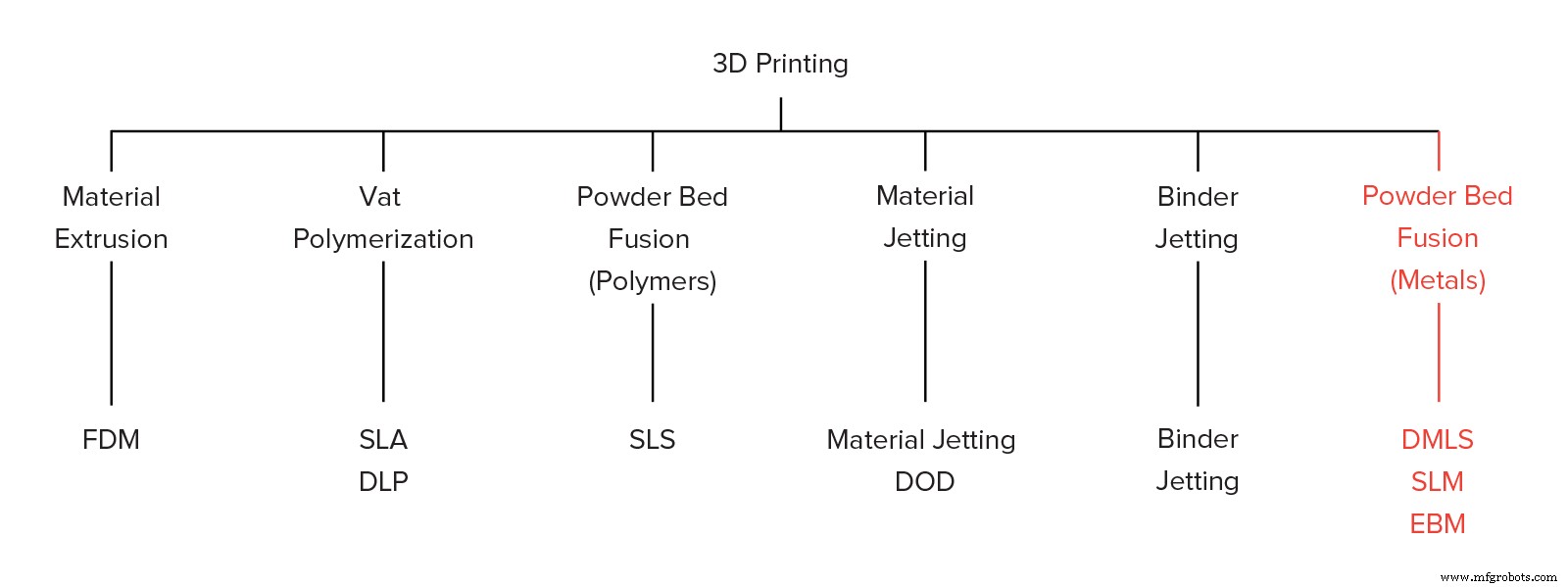
Selective Laser Melting (SLM) en Direct Metal Laser Sintering (DMLS) zijn twee additieve fabricageprocessen voor metaal die behoren tot de poederbedfusie 3D-printfamilie. De twee technologieën hebben veel overeenkomsten:beide gebruiken een laser om de metaalpoederdeeltjes te scannen en selectief samen te smelten (of te smelten), ze aan elkaar te hechten en een deel laag voor laag op te bouwen. De materialen die in beide processen worden gebruikt, zijn ook metalen die in korrelvorm voorkomen.
De verschillen tussen SLM en DMLS komen neer op de fundamenten van het deeltjesbindingsproces (en ook patenten):SLM gebruikt metaalpoeders met een enkele smelttemperatuur en smelt de deeltjes volledig, terwijl bij DMLS het poeder is samengesteld uit materialen met variabele smeltpunten die op moleculair niveau samensmelten bij verhoogde temperaturen.
In wezen:
SLM produceert onderdelen uit een enkel metaal , terwijl DMLS onderdelen produceert van metaallegeringen .
Zowel SLM als DMLS worden gebruikt in industriële toepassingen om technische eindproducten te maken. In dit artikel gebruiken we de term 3D-printen van metaal om naar beide processen in het algemeen te verwijzen en beschrijven we de basismechanismen van het fabricageproces die ingenieurs en ontwerpers nodig hebben om de voordelen en beperkingen van de technologie te begrijpen.
Er zijn andere additieve fabricageprocessen die kunnen worden gebruikt om dichte metalen onderdelen te produceren, zoals Electron Beam Melting (EBM) en Ultrasonic Additive Manufacturing (UAM). Hun beschikbaarheid en toepassingen zijn echter beperkt, dus ze zullen hier niet worden gepresenteerd. Klik hier voor meer informatie over Metal Binder Jetting.
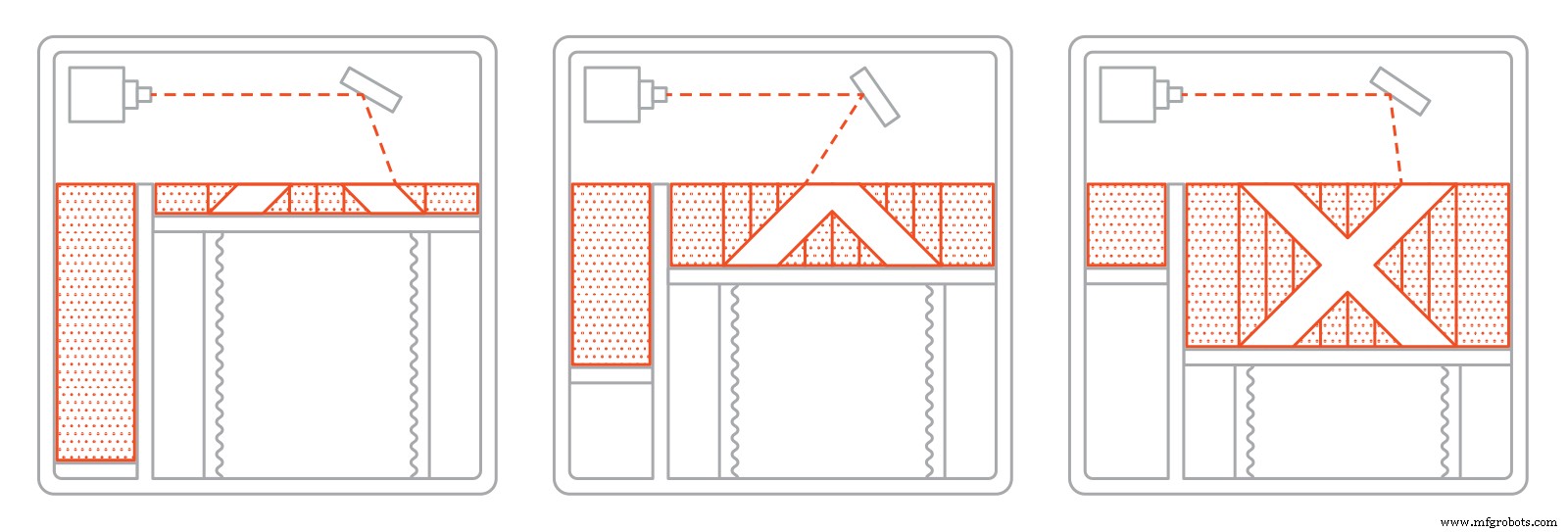
Hoe werkt 3D-printen van metaal?
Het basisfabricageproces voor SLM en DMLS lijkt erg op elkaar. Zo werkt het:
- De bouwkamer wordt eerst gevuld met inert gas (bijvoorbeeld argon) om de oxidatie van het metaalpoeder te minimaliseren en wordt vervolgens verwarmd tot de optimale bouwtemperatuur.
- Een dunne laag metaalpoeder wordt over het bouwplatform verspreid en een krachtige laser scant de dwarsdoorsnede van het onderdeel, waarbij de metaaldeeltjes samensmelten (of versmelten) en de volgende laag ontstaat. Het hele gebied van het model wordt gescand, dus het onderdeel is volledig solide gebouwd.
- Wanneer het scanproces is voltooid, beweegt het bouwplatform één laagdikte naar beneden en verspreidt de recoater nog een dunne laag metaalpoeder. Het proces wordt herhaald totdat het hele deel voltooid is.
Wanneer het bouwproces is voltooid, zijn de onderdelen volledig ingekapseld in het metaalpoeder. In tegenstelling tot het smeltproces van een polymeerpoederbed (zoals SLS), worden de onderdelen door middel van ondersteuningsstructuren aan het bouwplatform bevestigd. . Ondersteuning bij 3D-metaalprinten is gemaakt met hetzelfde materiaal als het onderdeel en is altijd nodig om kromtrekken en vervorming te verminderen die kunnen optreden als gevolg van de hoge verwerkingstemperaturen.
Wanneer de bak afkoelt tot kamertemperatuur, wordt het overtollige poeder handmatig verwijderd en worden de onderdelen doorgaans met warmte behandeld terwijl ze nog aan het bouwplatform zijn bevestigd om eventuele resterende spanningen te verlichten. Vervolgens worden de componenten via knippen, machinale bewerking of draadvonken losgemaakt van de bouwplaat en zijn ze klaar voor gebruik of verdere nabewerking.
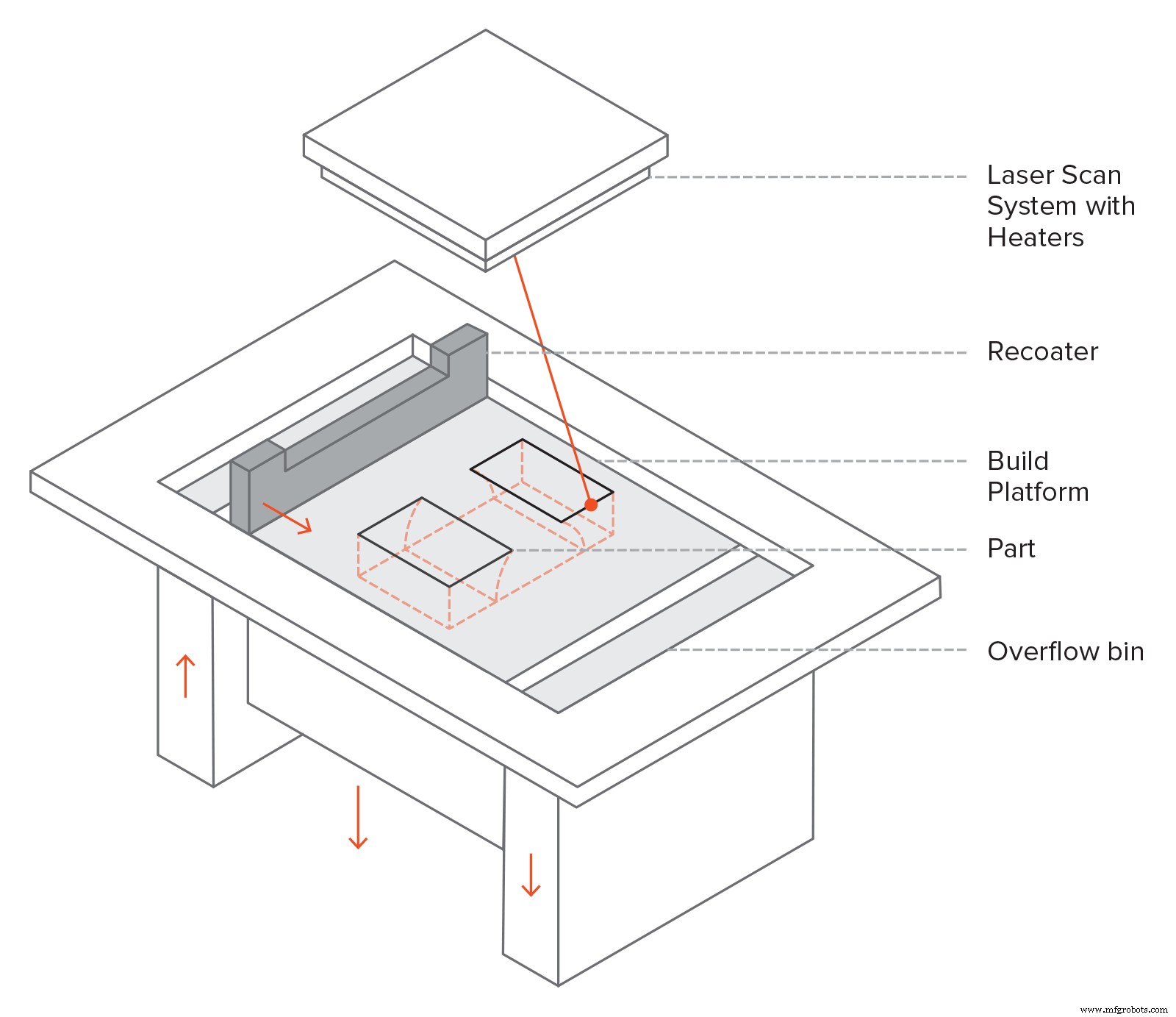
Verbeter uw ontwerpvaardigheden voor 3D-printen
Ontvang een gratis poster met 3D-printontwerpregels
Kenmerken van SLM &DMLS
Printerparameters
In SLM en DMLS worden bijna alle procesparameters ingesteld door de machinefabrikant. De laaghoogte gebruikt in metaal 3D-printen varieert tussen 20 en 50 micron en is afhankelijk van de eigenschappen van het metaalpoeder (vloeibaarheid, deeltjesgrootteverdeling, vorm enz.).
De typische bouwgrootte van een metalen 3D-printsysteem is 250 x 150 x 150 mm, maar er zijn ook grotere machines beschikbaar (tot 500 x 280 x 360 mm). De dimensionale nauwkeurigheid dat een metalen 3D-printer kan bereiken is ongeveer ± 0,1 mm.
Metaalprinters kunnen worden gebruikt voor productie in kleine batches , maar de mogelijkheden van metalen 3D-printsystemen lijken meer op de batchproductiemogelijkheden van FDM- of SLA-machines dan die van SLS-printers:ze worden beperkt door het beschikbare afdrukgebied (XY-richting), omdat de onderdelen aan de build moeten worden bevestigd platform.
Het metaalpoeder in SLM en DMLS is zeer recyclebaar :doorgaans wordt minder dan 5% verspild. Na elke afdruk wordt het ongebruikte poeder verzameld, gezeefd en vervolgens aangevuld met vers materiaal tot het niveau dat nodig is voor de volgende build.
Afval bij het printen van metaal komt echter in de vorm van een ondersteuningsstructuur , die cruciaal zijn voor de succesvolle voltooiing van een build, maar de hoeveelheid benodigde materiaal (en de kosten) drastisch kunnen verhogen.
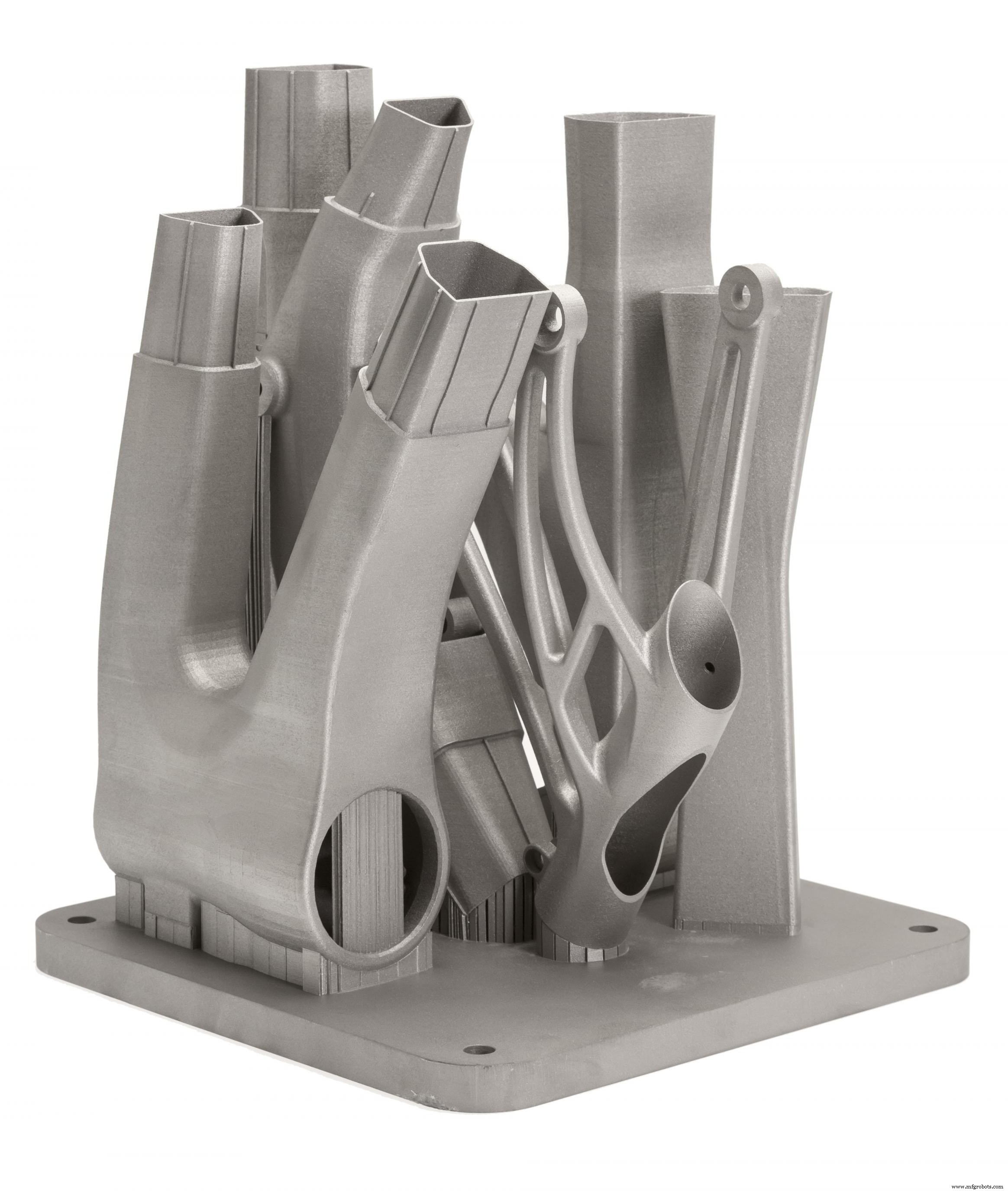
Laaghechting
Metalen SLM- en DMLS-onderdelen hebben bijna isotroop mechanische en thermische eigenschappen. Ze zijn solide met zeer weinig interne porositeit (minder dan 0,2 - 0,5% in afgedrukte staat en bijna geen na thermische verwerking).
Met metaal bedrukte onderdelen hebben hogere sterkte en hardheid en zijn vaak flexibeler dan onderdelen die op traditionele wijze zijn vervaardigd. Ze zijn echter vatbaarder voor vermoeidheid.
Kijk bijvoorbeeld eens naar de mechanische eigenschappen van de AlSi10Mg EOS metalen 3D-printlegering en de A360 gegoten legering . Deze twee materialen hebben een zeer vergelijkbare chemische samenstelling, rijk aan silicium en magnesium. De bedrukte delen hebben superieure mechanische eigenschappen en een hogere hardheid in vergelijking met het bewerkte materiaal.
Door de korrelvorm van het onbewerkte materiaal is de as-built oppervlakteruwheid (Ra) van een metalen 3D-geprint onderdeel is ongeveer 6 - 10 m. Deze relatief hoge oppervlakteruwheid kan de lagere vermoeiingssterkte gedeeltelijk verklaren .
* :Thermisch behandeld:gegloeid bij 300℃ gedurende 2 uur
** :Getest op as-built samples
Ondersteuningsstructuur en onderdeeloriëntatie
Door de zeer hoge verwerkingstemperatuur zijn bij het printen van metaal altijd draagstructuren nodig en worden ze meestal met een rasterpatroon gebouwd.
Ondersteuning bij 3D-printen van metaal heeft 3 verschillende functies:
- Ze bieden een geschikt platform voor de volgende laag om op te bouwen.
- Ze verankeren het onderdeel aan de bouwplaat en ze voorkomen kromtrekken.
- Ze fungeren als een koellichaam warmte wegtrekken van het onderdeel en het met een meer gecontroleerde snelheid laten afkoelen.
Onderdelen zijn vaak onder een hoek georiënteerd om de kans op kromtrekken te minimaliseren en de sterkte van het onderdeel in kritieke richtingen te maximaliseren. Dit verhoogt echter de hoeveelheid benodigde ondersteuning, de bouwtijd, de materiaalverspilling en (uiteindelijk) de totale kosten.
Kromtrekken kan ook worden geminimaliseerd met behulp van gerandomiseerde scanpatronen . Deze scanstrategie voorkomt de opbouw van restspanningen in een bepaalde richting en voegt een karakteristieke oppervlaktetextuur toe aan het onderdeel.
Omdat de kosten van metaalprinten erg hoog zijn, worden vaak simulaties gebruikt om het gedrag van het onderdeel tijdens de bewerking te voorspellen. Algoritmen voor topologie-optimalisatie worden ook niet alleen gebruikt om de mechanische prestaties te maximaliseren en lichtgewicht onderdelen te maken, maar ook om de noodzaak van een ondersteunende structuur en de kans op kromtrekken te minimaliseren.
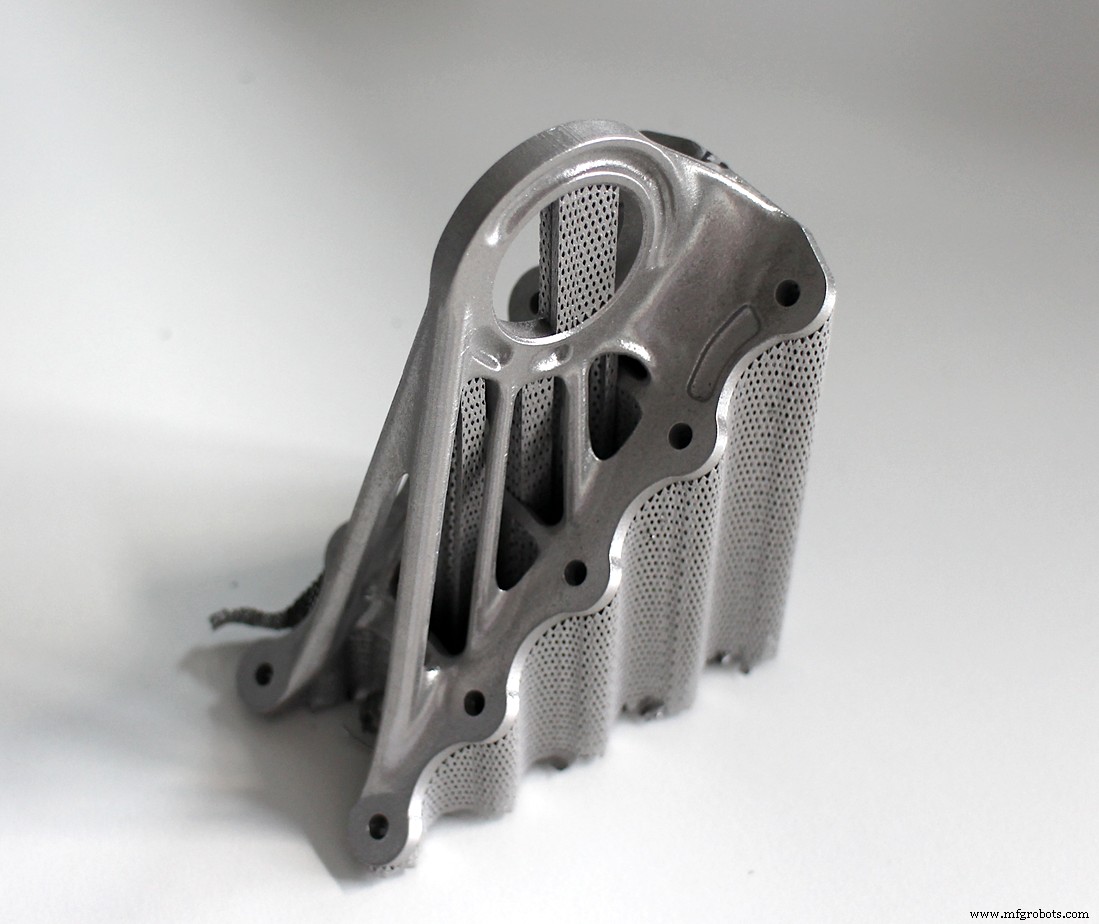
Holle secties en lichtgewicht constructies
In tegenstelling tot polymeerpoederbedfusieprocessen zoals SLS, grote holle secties worden niet vaak gebruikt bij het printen van metaal, omdat ondersteunende structuren niet gemakkelijk kunnen worden verwijderd.
Voor interne kanalen groter dan Ø 8 mm, wordt aanbevolen om in plaats van cirkelvormige doorsneden diamanten of traanvormige doorsneden te gebruiken, aangezien deze geen ondersteunende structuren vereisen. Meer ontwerprichtlijnen over SLM &DMLS zijn te vinden in dit artikel.
Als alternatief voor holle profielen kunnen onderdelen worden ontworpen met huid en kernen. Huid en kernen worden verwerkt met verschillende laserkracht en scansnelheid, wat resulteert in verschillende materiaaleigenschappen. Het gebruik van huid en kernen is erg handig bij het vervaardigen van onderdelen met een grote massieve doorsnede, omdat ze de afdruktijd en de kans op kromtrekken aanzienlijk verminderen en onderdelen produceren met een hoge stabiliteit en uitstekende oppervlaktekwaliteit.
Een roosterstructuur gebruiken is ook een veelgebruikte strategie bij het 3D-printen van metaal om het gewicht van een onderdeel te verminderen. Algoritmen voor topologie-optimalisatie kunnen ook helpen bij het ontwerpen van organische lichtgewicht vorm .
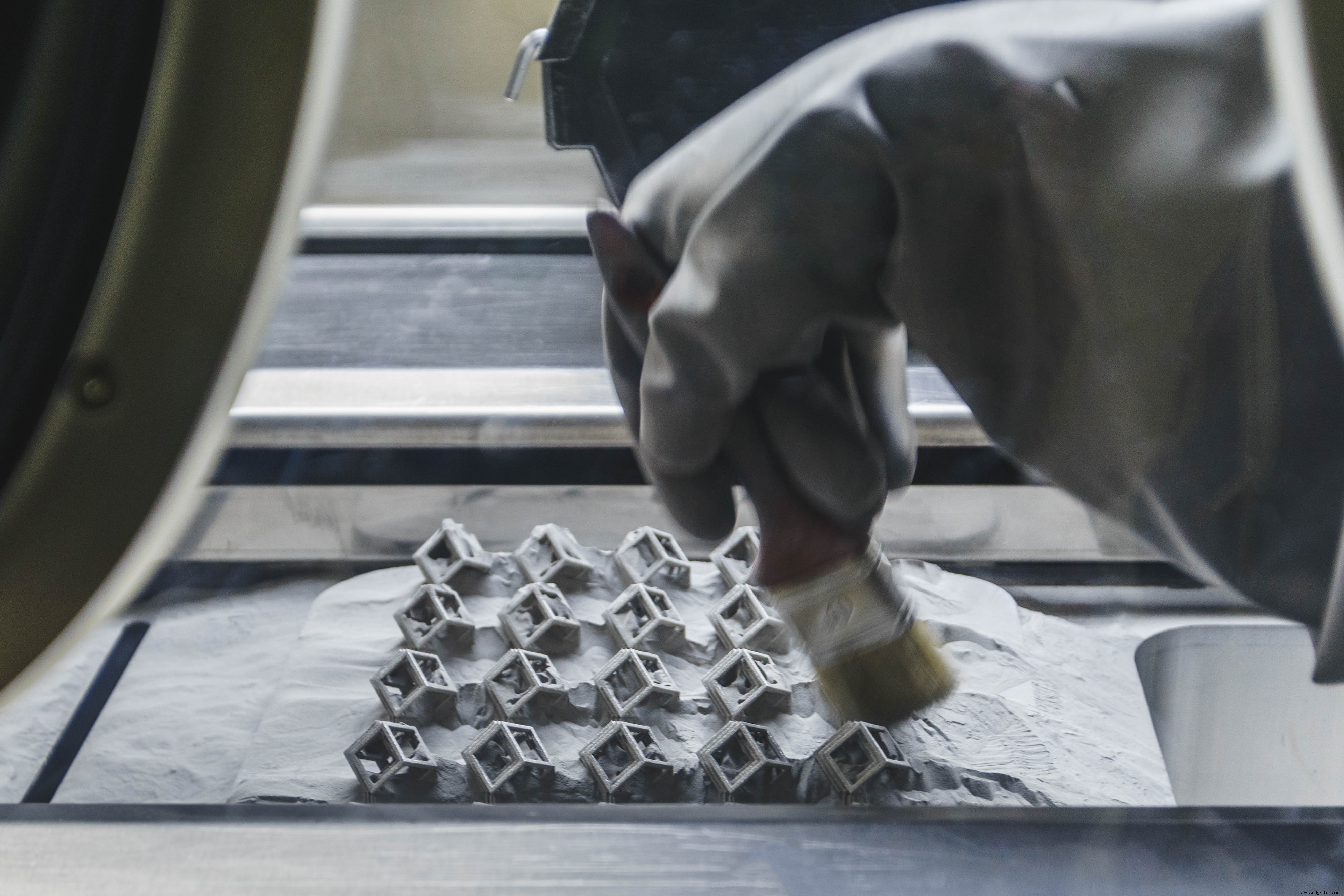
Veelgebruikte SLM- en DMLS-materialen
SLM en DMLS kunnen onderdelen produceren van een groot aantal metalen en metaallegeringen, waaronder aluminium, roestvrij staal, titanium, kobaltchroom en inconel. Deze materialen dekken de behoeften van de meeste industriële toepassingen, van ruimtevaart tot medische toepassingen. Edelmetalen, zoals goud, platina, palladium en zilver kunnen ook worden verwerkt, maar hun toepassingen zijn marginaal en voornamelijk beperkt tot het maken van sieraden.
De kosten van het metaalpoeder zijn erg hoog. Een kilo roestvrij staal 316L-poeder kost bijvoorbeeld ongeveer $ 350 - $ 450. Om deze reden is het minimaliseren van het onderdeelvolume en de behoefte aan ondersteuning essentieel om de kosten zo laag mogelijk te houden.
Een belangrijk voordeel van 3D-printen met metaal is de compatibiliteit met materialen met een hoge sterkte, zoals nikkel of kobalt-chroom superlegeringen, die zeer moeilijk te verwerken zijn met traditionele productiemethoden. Aanzienlijke kosten- en tijdbesparing kan worden gemaakt door 3D-printen van metaal te gebruiken om een bijna netvormig onderdeel te creëren dat later kan worden nabewerkt tot een zeer hoge oppervlakteafwerking.
Vergelijk de kosten van 3D-printen van metaal
Ontvang direct een offerte
Nabewerking
Er worden verschillende nabewerkingstechnieken gebruikt om de mechanische eigenschappen, nauwkeurigheid en het uiterlijk van de met metaal bedrukte onderdelen te verbeteren.
Verplichte nabewerkingsstappen omvatten het verwijderen van het losse poeder en de ondersteunende structuren, terwijl warmtebehandeling (thermisch uitgloeien) vaak wordt gebruikt om de restspanningen te verlichten en de mechanische eigenschappen van het onderdeel te verbeteren.
CNC-bewerking kan worden gebruikt voor dimensioneel cruciale kenmerken (zoals gaten of schroefdraad). Het stralen van media, metaalplateren, polijsten en microbewerkingen kunnen de oppervlaktekwaliteit en vermoeiingssterkte van een met metaal bedrukt onderdeel verbeteren.

Meer informatie over CNC-bewerkingen
Download de ontwerp- en fabricagehandleiding
Voordelen en beperkingen van 3D-metaalprinten
Hier zijn de belangrijkste voor- en nadelen van metalen 3D-printprocessen:
Metalen 3D-printprocessen kunnen worden gebruikt om complexe, op maat gemaakte onderdelen te vervaardigen met geometrieën die traditionele productiemethoden niet kunnen produceren.
3D-geprinte metalen onderdelen kunnen topologisch worden geoptimaliseerd om hun prestaties te maximaliseren en tegelijkertijd hun gewicht en het totale aantal componenten in een assemblage te minimaliseren.
3D-geprinte metalen onderdelen hebben uitstekende fysieke eigenschappen en het beschikbare materiaalaanbod omvat moeilijk te verwerken materialen, zoals metalen superlegeringen.
De materiaal- en fabricagekosten in verband met 3D-printen van metaal zijn hoog, dus deze technologieën zijn niet geschikt voor onderdelen die gemakkelijk met traditionele methoden kunnen worden vervaardigd.
De bouwgrootte van de metalen 3D-printsystemen is beperkt, aangezien nauwkeurige productieomstandigheden en procescontrole vereist zijn.
Reeds bestaande ontwerpen zijn mogelijk niet geschikt voor 3D-printen van metaal en moeten mogelijk worden gewijzigd.
Gedetailleerde ontwerprichtlijnen voor metaal 3D-printen worden gegeven in dit artikel van de Knowledge Base. De belangrijkste kenmerken van SLM- en DMLS-systemen zijn samengevat in de onderstaande tabel:
Vuistregels
- Metaal 3D-printen is het meest geschikt voor complexe, op maat gemaakte onderdelen die moeilijk of zeer kostbaar zijn om met traditionele methoden te vervaardigen.
- Het minimaliseren van de behoefte aan ondersteunende structuren zal de kosten van het printen van metaal aanzienlijk verlagen.
- Topologie-optimalisatie is essentieel om de extra voordelen van het gebruik van metaalprinten te maximaliseren.
- Metalen 3D-geprinte onderdelen hebben uitstekende mechanische eigenschappen en kunnen worden vervaardigd uit een breed scala aan technische materialen, waaronder metalen superlegeringen.
Leer het verschil tussen 3D-printen van metaal en CNC
Download onze gids over het produceren van metalen onderdelen
3d printen
- Vuurvaste metaalpoeders VS 3D-afdruktechnologie
- Een inleiding tot passiveren in metaalbewerking
- 3D-microfabricage:een inleiding tot 3D-printen op microformaat
- Een inleiding tot metaalfabricage
- Een inleiding tot direct metaallaser sinteren
- Een inleiding tot 3D-printen met plastic
- Een inleiding tot 3D-printen voor zandgieten
- Een inleiding tot het smelten van elektronenstralen
- 3D-printen met harsen:een introductie
- 5 innovatieve toepassingen voor 3D-metaalprinten
- Metalen onderdelen lichter maken met 3D-printen op metaal