Applicatie Spotlight:3D-printen voor vliegtuigcabines
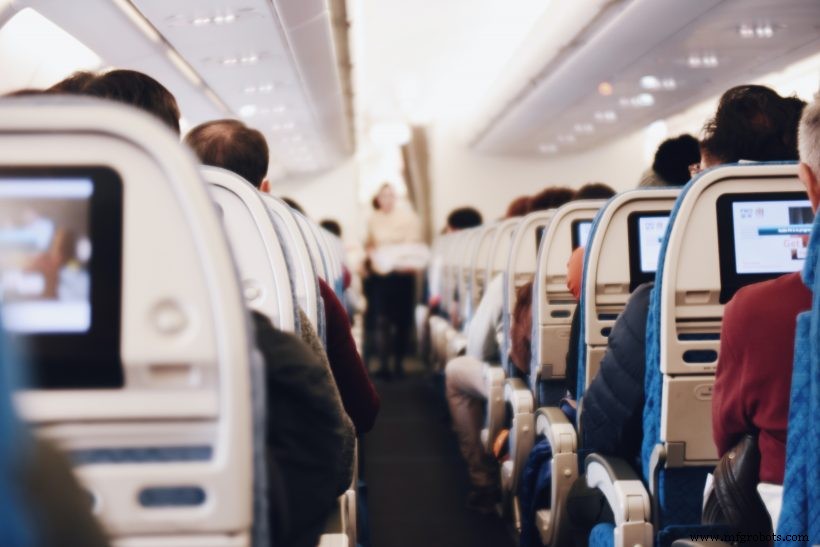
Als u in een vliegtuig vliegt, realiseert u zich waarschijnlijk niet dat uw armleuning of dienblad in 3D is geprint, maar het gebruik van deze technologie voor cabineonderdelen kan een hele nieuwe wereld aan mogelijkheden voor luchtvaartmaatschappijen openen.
Deze mogelijkheden omvatten bijvoorbeeld kosteneffectief interieur maatwerk en snellere productie en levering van reserveonderdelen.
We onderzoeken de belangrijkste drijfveren achter het gebruik van 3D-printen voor vliegtuiginterieurs en laten zien hoe toonaangevende bedrijven in de lucht- en ruimtevaartindustrie de technologie tegenwoordig toepassen.
Bekijk de andere toepassingen die in deze serie worden behandeld:
3D-printen voor warmtewisselaars
3D-printen voor lagers
3D-printen voor fietsproductie
3D-printen voor productie van digitale tandheelkunde en heldere uitlijners
3D-printen voor medische implantaten
3D-geprinte raketten en de toekomst van de fabricage van ruimtevaartuigen
3D-printen voor de productie van schoenen
3D-printen voor elektronische componenten
3D-printen in de spoorindustrie
3D-geprinte brillen
3D-printen voor productie van eindonderdelen
3D-printen voor beugels
3D-printen voor turbineonderdelen
Hoe 3D-printen zorgt voor beter presterende hydraulische componenten
Hoe 3D-printen innovatie in de kernenergie-industrie ondersteunt
Waarom 3D-printen voor cabineonderdelen?
Innovatie cabineontwerp
Luchtvaartmaatschappijen zijn altijd op zoek naar manieren om de vliegervaring van hun klanten te verbeteren, en het ontwerp van de cabine speelt daarbij een cruciale rol.
Het creëren van op maat gemaakte interieurs die voldoen aan de specifieke behoeften en functies van luchtvaartmaatschappijen is een groeiende trend en een perfecte taak voor 3D-printen.
3D-printen ontsluit nieuwe mogelijkheden voor het aanpassen van cabineonderdelen, omdat er geen dure gereedschapswijzigingen nodig zijn op basis van individuele specificaties. Het vervaardigen van custom onderdelen gaat daardoor sneller en kosteneffectiever.
Gewichtsvermindering
Omdat brandstofuitgaven een van de grootste kostenposten zijn voor luchtvaartmaatschappijen, hebben ze de neiging om te investeren in vliegtuigen met een superieure brandstofefficiëntie. Traditionele fabricagemethoden hebben echter een beperkt vermogen om het gewicht van vliegtuigonderdelen te verminderen.
Fabrikanten houden daarom de zoektocht in leven naar meer geavanceerde en alternatieve methoden om onderdelen met een lager gewicht te vervaardigen.
3D-printen biedt een van de oplossingen voor het bereiken van gewichtsvermindering door geoptimaliseerde onderdeelgeometrie die materiaalbesparingen mogelijk maakt.
Met 3D-printen kunnen fabrikanten cabineonderdelen bouwen in lichtgewicht materialen, met dunnere wanden dan spuitgieten.
Bovendien maakt de technologie functionele integratie mogelijk, terwijl verschillende afzonderlijke onderdelen van een component als één geheel kunnen worden ontworpen en geprint, waardoor het gewicht van een onderdeel verder wordt verminderd.
On-demand 3D-printen van reserveonderdelen voor vliegtuiginterieurs
Het voorspellen van de vraag naar reserveonderdelen is een uitdaging en soms wordt een reserveonderdeel niet meer geproduceerd. Deze factoren maken de aftermarketservice voor vliegtuigen moeilijk en leiden tot inefficiënties in de toeleveringsketen. Hoewel hoge voorraadniveaus de uitvaltijd van vliegtuigen kunnen verminderen, leiden ze tot astronomisch hoge kosten voor het onderhouden van een dergelijke voorraad.
Bovendien is het vaak problematisch om tijdige MRO-diensten te verlenen. De noodzaak om in korte tijd hoogwaardige vervangende onderdelen te produceren met dure materialen, zet de fabrikanten onder druk, aangezien de doorlooptijden vaak oplopen tot enkele maanden, met behulp van traditionele productieprocessen.
Bovendien is het mogelijk dat bij het repareren of vervangen van legacy vliegtuigonderdelen de bijbehorende gereedschappen niet langer verkrijgbaar zijn bij de OEM's.
Er is een enorme kans voor 3D-printen om een aantal van deze uitdagingen te overwinnen, door een snellere doorlooptijd mogelijk te maken en de voorraad te verminderen door middel van on-demand productie.
3D-printen stelt bedrijven in staat om onderdelen rechtstreeks vanuit een digitaal ontwerpbestand te produceren, zonder gebruik te maken van gereedschap, zoals matrijzen. Het betekent dat sommige reserveonderdelen, met name onderdelen met een lagere vraag zoals verouderde componenten, opnieuw kunnen worden ontworpen voor 3D-printen en worden opgeslagen in een virtuele inventaris, waardoor er ruimte vrijkomt in een magazijn en de voorraadkosten worden verlaagd.
Als er een vervanging nodig is, kan een ontwerp gewoon uit de virtuele onderdelencatalogus worden gehaald en worden verzonden om te worden afgedrukt.
Dankzij het vermogen om kleine hoeveelheden onderdelen economisch te produceren, stelt 3D-printen bedrijven ook in staat om slechts zoveel onderdelen te maken als nodig is, waardoor het probleem van overproductie, typisch voor traditionele productiemethoden, wordt opgelost.
4 voorbeelden van het gebruik van 3D-printen voor cabineonderdelen
Veel interieurcomponenten van vliegtuigen, van ventilatieopeningen en elektrische behuizing tot afstandspanelen en armleuningen, kunnen profiteren van 3D-printen. Hieronder onderzoeken we hoe OEM's en luchtvaartmaatschappijen profiteren van de technologie voor cabineonderdelen.
1. Etihad Airways ziet een aanzienlijke meerwaarde in 3D-printen
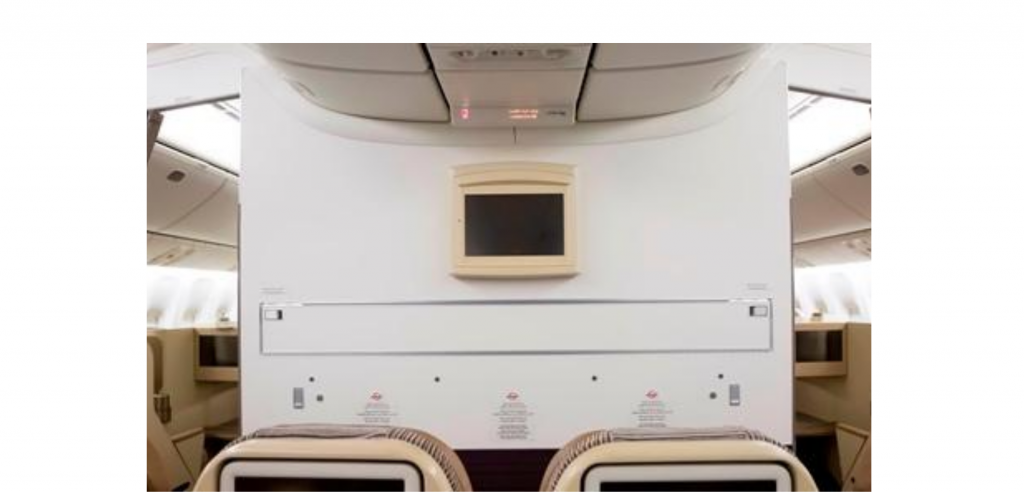
Etihad Airways, de op één na grootste luchtvaartmaatschappij in de Verenigde Arabische Emiraten, was een van de eerste luchtvaartmaatschappijen die de mogelijkheden van 3D-printen voor cabineonderdelen onderzocht.
In 2017 presenteerde het bedrijf het eerste gecertificeerde 3D-geprinte vliegtuiginterieur in de regio, een plastic monitorframe, en sindsdien heeft Etihad zijn inspanningen op het gebied van 3D-printen opgevoerd.
Het aangaan van strategische partnerschappen met 3D-printbedrijven, EOS en BigRep, was een onderdeel van deze inspanningen.
De resultaten van de samenwerking met toonaangevende 3D-hardwarefabrikanten lieten niet lang op zich wachten. Vorig jaar opende Etihad een faciliteit voor additieve productie (AM) in Abu Dhabi, die ontwerp- en productiegoedkeuring had gekregen van het European Aviation Safety Agency (EASA), om vliegtuigonderdelen te produceren met behulp van poederbedfusietechnologie van EOS.
Etihad Engineering, een divisie van de Etihad Aviation Group, gaat de EOS 3D-printer nu gebruiken voor het ontwerpen, produceren en certificeren van AM-componenten voor hoogwaardige vliegtuigtoepassingen en cabineonderdelen.
Het bedrijf is van mening dat het gebruik van 3D-printen veel verder gaat dan het vervangen van eenvoudige, niet-kritieke onderdelen.
Het additief produceren van cabineonderdelen biedt een substantiële toegevoegde waarde in termen van geoptimaliseerde reparatie, lichtgewicht ontwerp, kortere doorlooptijden en maatwerk. Zo zou Etihads nieuwe 'Greenliner', een gezamenlijk project met Boeing dat is ontworpen om duurzaamheid in de luchtvaartindustrie te bevorderen, veel 3D-geprinte componenten bevatten.
Als we verder in de toekomst kijken, ziet Etihad een volledige retrofit van een vliegtuig in slechts 30 dagen door middel van 3D-printen, wat resulteert in 30 procent snellere upgrades.
2. De 3D-geprinte gordijnkopbehuizing van Diehl Aviation
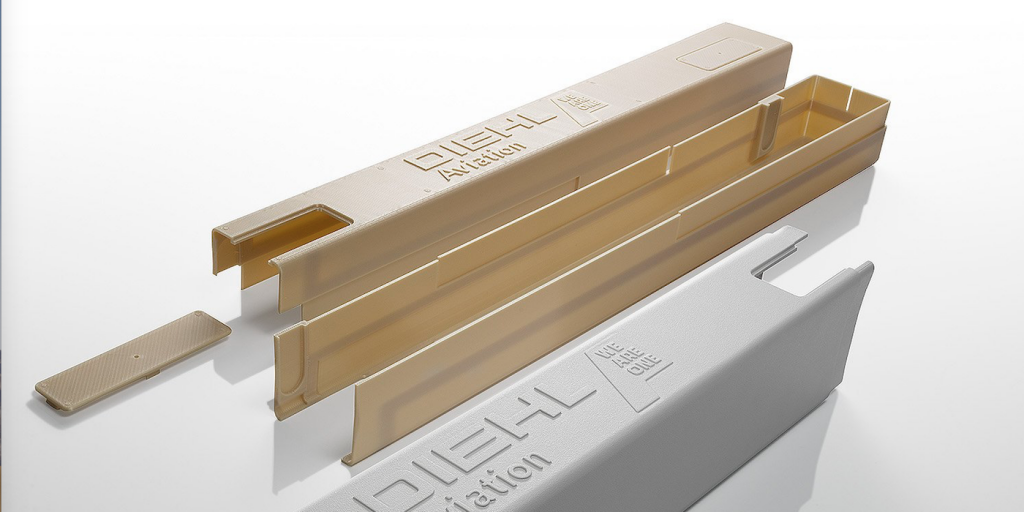
De lucht- en ruimtevaartfabrikant die gespecialiseerd is in cabine- en luchtvaartelektronica, Diehl Aviation, toonde een ander voorbeeld van 3D-printen voor interieuronderdelen.
Samen met Airbus heeft Diehl een 3D-geprinte Curtain Comfort Header ontwikkeld - een behuizing die boven de gordijnrail zit en klassen aan boord scheidt - geïnstalleerd op een Qatar Airways Airbus A350 XWB.
De behuizing werd eerder geconstrueerd met behulp van verschillende lagen gelamineerd glasvezel en vereiste gespecialiseerde aluminium gereedschappen, wat tijdrovend en kostbaar was.
Diehl was in staat om dit onderdeel te assembleren uit 12 3D-geprinte thermoplastische componenten, waardoor de gereedschapskosten drastisch werden verlaagd en er uren aan arbeidskrachten werden bespaard.
Bovendien vergen de onderdelen minder nabewerking en kunnen ze gemakkelijk worden verwijderd voor reparatie of vervanging, wat nog kortere doorlooptijden tijdens reparatie betekent.
Dit stuk is naar verluidt het grootste volledig 3D-geprinte onderdeel van een passagiersvliegtuig dat tot nu toe voor passagiersvliegtuigen is geproduceerd.
3. British Airways voorspelt toenemende acceptatie van 3D-printen voor vliegtuiginterieurs
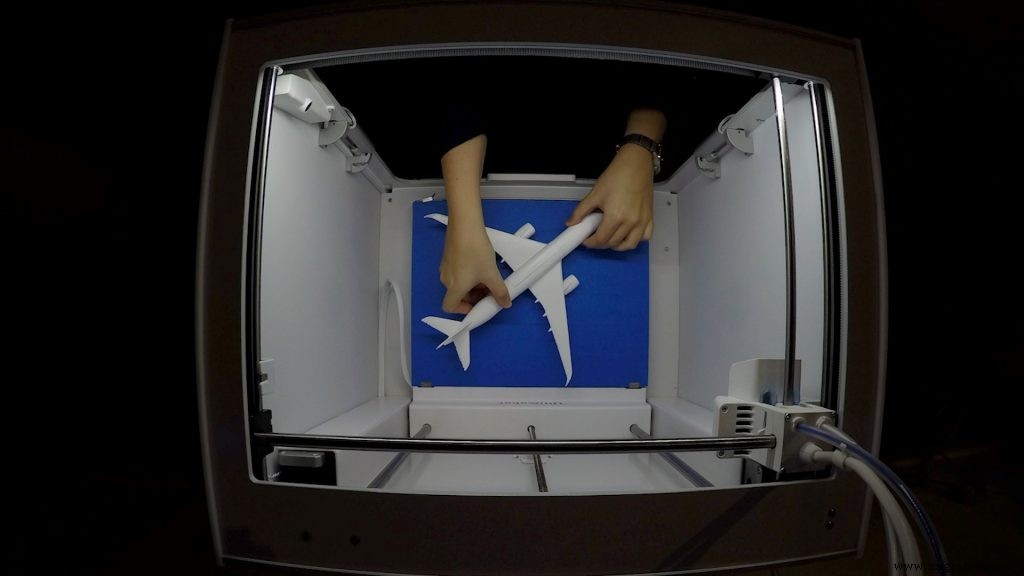
Hoewel het lijkt alsof de meeste inspanningen voor het 3D-printen van cabineonderdelen geconcentreerd zijn in de EMEA-regio, zijn Europese luchtvaartmaatschappijen bezig hun achterstand in te halen.
Bijvoorbeeld, British Airways onderzoekt de mogelijkheid om 3D-printers te gebruiken om vliegtuigonderdelen te maken, te beginnen met niet-essentiële cabineonderdelen, waaronder stukken dienblad, inflight entertainment (IFE) systemen en toiletten.
Hoewel deze componenten geen invloed hebben op de veilige werking van een vlucht, kunnen ze, als ze kapot gaan, het aantal beschikbare stoelen of toiletten voor klanten verminderen en vertragingen veroorzaken omdat technici wachten tot de onderdelen zijn gerepareerd of vervangen .
Volgens de luchtvaartmaatschappij kunnen 3D-printers vervangende onderdelen produceren die, hoewel even sterk en duurzaam als traditionele componenten, in een veel kortere tijd beschikbaar kunnen zijn.
Gewichtsvermindering aanhalend als een andere drijfveer voor het adopteren van AM, zegt British Airways dat 3D-printen kan helpen het gewicht van een onderdeel tot 55 procent te verminderen. Zelfs met kleine componenten kunnen de effecten aanzienlijk zijn, aangezien elke kilo die wordt verwijderd, tonnen CO2-uitstoot bespaart tijdens de levensduur van een vliegtuig.
In de toekomst voorspelt de luchtvaartmaatschappij dat het mogelijk zal zijn om een 3D-print veel uitgebreider assortiment cabineonderdelen, van bestek en stoelen tot bagagecontainers en vliegtuigramen.
4. Stratasys, SIA Engineering Company en Additive Flight Solutions 3D printen duizenden cabineonderdelen
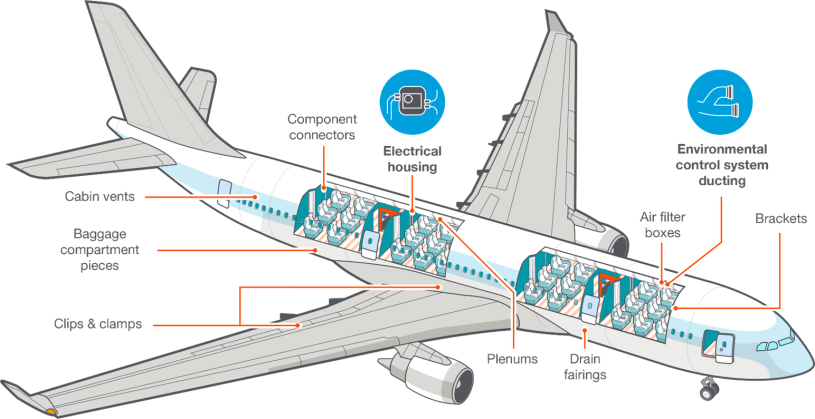
Stratasys, samen met SIA Engineering Company, dat MRO-services voor vliegtuigen levert, en een 3D-printservicebureau, Additive Flight Solutions, zien AM ook als een kritieke technologie om oplossingen te bieden aan de luchtvaartmaatschappijen.
In een joint venture, opgericht in 2018, hebben 3 partners de Stratasys FDM-technologie gebruikt om tot op heden meer dan 5.000 gecertificeerde onderdelen voor vliegtuigcabines te produceren.
Een dergelijk onderdeel is een hoes die bedoeld is om stoelcontrollers te beschermen, zodat passagiers niet per ongeluk op de knoppen kunnen drukken. Een van de belangrijkste redenen om het AM-proces te verkiezen boven een ander, meer traditioneel proces, is de mogelijkheid om deze hoezen sneller en goedkoper in een klein volume te bestellen.
In een ander voorbeeld heeft het team 3D een clip geprint om vliegtuiggordijnen tegen te houden die te vaak loskwamen. Er zijn 7 verschillende ontwerpen voor deze hoezen/gordijnen, wat betekent dat het team de eindafdekkingen van de gordijnrails moest aanpassen voor elk van de ontwerpen. 3D-printen is veel flexibeler dan andere technologieën om een dergelijk niveau van maatwerk mogelijk te maken.
Bovendien is er 3D-printing toegepast om een veiligheidspal voor de nooddeuren van de Boeing 787 te produceren. Het onderdeel is een essentieel onderdeel dat ervoor moet zorgen dat de nooddeuren niet opengaan terwijl het vliegtuig ligt op de grond, waardoor er kans op verwondingen ontstaat, omdat ontsnappingsglijbanen per ongeluk kunnen worden geactiveerd.
Andere producten die zijn gemaakt waren steunen voor de onderkant van de passagiersstoel, een 3D-geprint cocktailblad, houders voor de badkamer dispensers voor zeep en ontsmettingsmiddel.
Alle onderdelen moeten voldoen aan strenge eisen, zoals thermische weerstand en Vlam-, Rook- en Toxiciteitsclassificaties (FST) voor vliegtuiginterieurs.
Zoveel toepassingen, al ontwikkeld door het team en geïnstalleerd in commerciële vliegtuigen, geven aan dat de toekomst van vliegtuiginterieurs nauw verbonden is met volwassen wordende 3D-printtechnologieën.
Standaard AM voor cabineonderdelen
Dat gezegd hebbende, is er geen toekomst voor 3D-printen in de luchtvaartindustrie zonder standaardisatie. Het is niet verrassend dat het gebrek aan normen en certificering een enorm knelpunt blijft bij het gebruik van AM voor onderdelen van vliegtuigcabines.
'Als je in de lucht- en ruimtevaart geen standaard hebt waarmee je een onderdeel kunt certificeren tegen, of doorgaans meerdere standaarden, dan kun je het niet op een lucht- en ruimtevaartplatform zetten' , zei Matthew Donovan, nu voormalig hoofdingenieur voor additieve productie bij Oerlikon, in een interview met AMFG.
Zonder de juiste standaarden zullen lucht- en ruimtevaartbedrijven de technologie niet kunnen gebruiken met hetzelfde vertrouwen dat wordt geboden door traditionele productiemethoden.
Het ontbreken van industriebrede normen voor AM-materialen, -processen, kwaliteitsbeoordeling en ontwerp, samen met de beperkte materiaalverwerkingsgegevens, leiden tot langere certificeringsperioden.
Momenteel certificeren luchtvaartmaatschappijen en bedrijven die onderdelen voor vliegtuigen maken onderdelen per onderdeel, wat een dure en tijdrovende onderneming is.
Gelukkig is er een sterke druk om de normen, het beleid en de richtlijnen te ontwikkelen voor het toepassen van AM voor vliegtuigonderdelen.
Autoriteiten, zoals de Federal Aviation Administration (FAA) en European Aviation Safety Agency (EASA), werken samen met de AM-industrie en organisaties voor de ontwikkeling van normen, zoals ASTM, SAE en ISO, om de huidige uitdagingen op het gebied van normalisatie te overwinnen.
Een reeks specificaties voor polymeer 3D-printen in de lucht- en ruimtevaartsector, gepubliceerd door SAE International, is een van de recente ontwikkelingen op dit gebied.
De specificaties, genaamd AMS7100:Fused Filament Fabrication Process en AMS7101:Material for Fused Filament Fabrication, zijn speciaal ontwikkeld voor het FDM-proces om de adoptie van 3D-printen voor plastic cabineonderdelen aan te moedigen.
De toekomst van 3D-printen voor vliegtuiginterieurs
3D-printen is een van de belangrijkste technologieën die luchtvaartmaatschappijen helpen om vliegtuigcabines voorop te laten lopen op het gebied van innovatie. De technologie verbetert de MRO-operaties door een kleine productie van reserveonderdelen mogelijk te maken en verbetert de klantervaring door aangepaste ontwerpen van cabineonderdelen.
Honderden 3D-geprinte interieurcomponenten die al in vliegtuigen zijn geïnstalleerd, benadrukken het potentieel en de waarde die de technologie biedt voor de lucht- en ruimtevaartindustrie. Nu is het cruciaal om te focussen op het opschalen van het gebruik van 3D-printen, door middel van samenwerking en ontwikkeling van standaarden, om dit potentieel ten volle te kunnen benutten.
3d printen
- Emiraten adopteren 3D-printtechnologie voor vliegtuigonderdelen
- Applicatie Spotlight:3D-printen voor medische implantaten
- Applicatie Spotlight:3D-printen voor digitale tandheelkunde &Clear Aligner-productie
- Applicatie Spotlight:3D-printen voor fietsproductie
- Applicatie Spotlight:3D-printen voor lagers
- Applicatie Spotlight:3D-printen voor warmtewisselaars
- Applicatie Spotlight:3D-printen in de spoorwegindustrie
- Applicatie Spotlight:5 elektronische componenten die kunnen profiteren van 3D-printen
- Applicatie Spotlight:3D-printen voor schoenen
- Applicatie Spotlight:3D-geprinte raketten en de toekomst van de fabricage van ruimtevaartuigen
- 10 sterkste materialen voor 3D-printen