Interview met experts:Joseph Crabtree, CEO van Additive Manufacturing Technologies, over waarom nabewerking cruciaal is voor 3D-printen
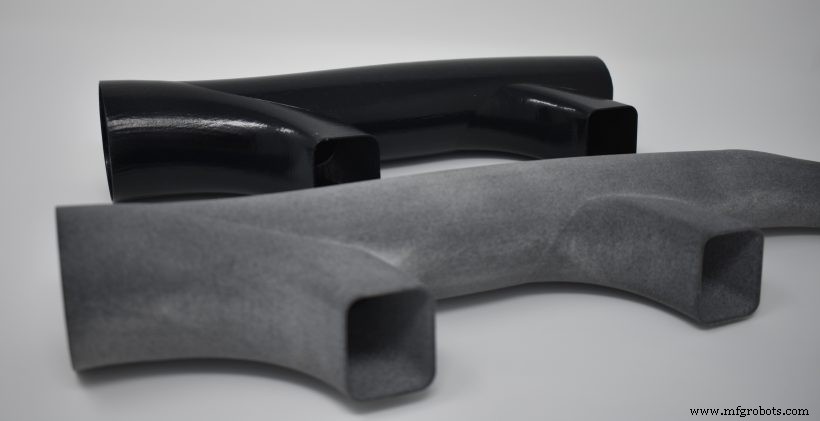
Nabewerking wordt vaak omschreven als het 'dirty little secret' van 3D-printen. Nabewerking, een noodzakelijk, maar zeer handmatig en arbeidsintensief onderdeel van het 3D-printproces, blijft een enorme uitdaging voor bedrijven die hun additive manufacturing (AM)-activiteiten willen schalen. Dit kan echter allemaal veranderen, dankzij verbeteringen in de automatisering van de nabewerking.
In het Expert Interview van deze week worden we vergezeld door Joseph Crabtree, CEO van Additive Manufacturing Technologies (AMT), een in het VK gevestigd bedrijf dat geautomatiseerde nabewerkingsoplossingen ontwikkelt. Met Joseph bespreken we waarom nabewerking belangrijk is, hoe de nabewerkingstechnologieën van AMT werken en wat de toekomst voor de industrie in petto heeft.
Kun je me iets vertellen over AMT Technologies?
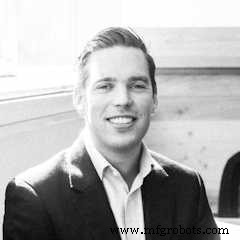
We zijn opgericht in 2017 in Sheffield in het VK, waar onze faciliteiten bestaan uit R&D-activiteiten, technische ondersteuning, verkoop en ontwikkeling van toepassingen.
We hebben een volledig eigen productiefaciliteit in Hongarije, waar we al onze engineering, ontwerpwerkzaamheden en productie doen. Dat is een vrij uniek verkoopvoorstel van ons - het feit dat we al het ontwerp en de fabricage in eigen huis doen. We hebben zojuist een faciliteit van 20.000 vierkante meter geopend in Austin, Texas, die de Amerikaanse markten gaat bedienen, en we hebben ook net onze eerste werknemer in de APAC-regio in dienst genomen. We breiden wereldwijd en zeer snel uit.
Het doel van het bedrijf is om industriële AM echt mogelijk te maken. Dus tot nu toe hebben bedrijven AM regelmatig gebruikt voor prototypes met een aantal overgangen naar toepassingen voor productie met een laag volume, maar wat we echt proberen te doen, is AM-technologie helpen opschalen van toepassingen met een laag volume naar volledige industriële mogelijkheden. We willen van 3D-printen een levensvatbaar alternatief maken voor traditionele productie.
Om eerlijk te zijn, als industrie zijn we daar nog ver van verwijderd. Er worden veel modewoorden gebruikt, maar eigenlijk is het grootste probleem tegenwoordig met 3D-printers. Iedereen heeft zich geconcentreerd op het ontwikkelen van grotere, snellere en betere printers. Dat is slechts een deel van de puzzel. Mensen beginnen zich meer te concentreren op de materialen die worden geprint, om de kosten te verlagen en de beschikbaarheid van materiaal te vergroten.
Maar de uitdaging blijft dat de onderdelen die aan het einde van het proces van de 3D-printers komen, vaak niet geschikt zijn voor eindgebruik.
En als we het hebben over onderdelen voor eindgebruik, hebben we het over onderdelen die kunnen worden gebruikt bij chirurgische ingrepen in de medische industrie, of in schoenen, interieurtoepassingen in de ruimtevaart, auto's onder de motorkap toepassingen, of bijvoorbeeld in ruimtetoepassingen. Geen van deze voorbeelden kan rechtstreeks vanuit een 3D-printer worden gebruikt, tenzij u ze nabewerkt of afwerkt.
En dat is tot nu toe over het hoofd gezien omdat de focus op de 3D-printers lag. Het was niet zozeer een probleem om kleine hoeveelheden onderdelen te produceren. De wisselwerking hier was dat terwijl het handmatig afwerken van de onderdelen de kosten verhoogde, de marges op deze onderdelen hoger waren.
Nu bedrijven AM beoordelen voor productietoepassingen, bij hogere volumes, is de marge absoluut kritiek. Wanneer nabewerking tot 60 procent van de kosten van het onderdeel kan uitmaken, kan dit onbetaalbaar worden en moet er iets aan gedaan worden.
Ons bedrijf richt zich op de nabewerkingsketen, en wat daarmee bedoelen we alles na de afdruk. Dus, in het geval van AM op poederbasis, omvat dit de ontpoederingsfase en oppervlaktemodificatie van het onderdeel, wat betekent dat het onderdeel wordt gladgemaakt, afgedicht, ingekleurd en anderszins wordt verbeterd.
De laatste stap is inspectie en kwaliteitscontrole. AMT brengt al deze stappen in de procesketen samen met een geautomatiseerde end-to-end oplossing. Het is een technologie-agnostische benadering, in die zin dat we met alle 3D-printtechnologieën werken.
We zijn ook gericht op polymeren en in het bijzonder thermoplastische polymeren, wat in wezen op poederbed en extrusie gebaseerde technologieën is. Meer dan 95 polymeren zijn gevalideerd voor onze systemen. En in feite is ons doel om dat end-to-end automatiseringssysteem aan het onderdeel te leveren.
Nu met de investering van DSM Venturing and Foresight Group, Williams Advanced Engineering, kunnen we echt voltooien wat we noemen 'het polymeer om het ecosysteem te scheiden'. Dus in wezen beschouwen we voor het eerst het hele ecosysteem. We kijken naar de materialen, we kijken hoe we de materialen kunnen ontwerpen voor 3D-printen en vervolgens optimaliseren we het printproces op basis van materiaalkeuze.
In wezen doen we materiaalkunde, gecombineerd met werktuigbouwkunde en automatisering. De nabewerkingsfase maakt het mogelijk om de mechanische eigenschappen van het geprinte onderdeel op maat te maken, zodat de algehele mechanische eigenschappen worden verbeterd in vergelijking met het onderdeel dat rechtstreeks van de machine komt.
Het combineren van dit alles is absoluut cruciaal voor ons, en daarom zijn al onze systemen industrieel, specifiek gericht op de industriële eindgebruiker.
Wat zijn enkele van de huidige uitdagingen waarmee bedrijven worden geconfronteerd als het specifiek gaat om nabewerking?
Het grootste probleem is een gebrek aan bewustzijn. Dus tot voor kort begrepen bedrijven niet alleen niets van 3D-printen, maar ze hadden ook geen idee dat als je eenmaal een 3D-printer hebt, je wat nabewerking aan het onderdeel moet doen.
Het is een zeer moeilijke situatie omdat de fabrikanten van 3D-printers u nooit een printer zullen verkopen en zeggen dat de eerste uitvoer van slechte kwaliteit is en dat u daarom een extra stuk zult moeten kopen van de apparatuur.
Ze spraken nooit over nabewerking, maar de tijd en kosten van nabewerking overschaduwen alle voordelen die worden behaald door hogere afdruksnelheden. Wat we hopen te realiseren, is dat de printerfabrikanten een verdere marktpenetratie krijgen, zodat ze hun klanten een complete oplossing kunnen bieden.
Het is iets waar niemand ooit echt over wil praten. Dit betekent dat onderwijs in dit opzicht een uitdaging is, vooral voor die klanten die nu op de markt komen.
Als gevolg hiervan weten bedrijven die voor het eerst een 3D-printer kopen misschien heel weinig over 3D-printen en staan ze nu voor de uitdaging van nabewerking. Daarom gaat het om het opleiden van eindgebruikers en hen te laten zien dat het niet een reeks discrete onafhankelijke machine-items is die je moet kopen om van dit proces, laten we zeggen, een oplossing met één druk op de knop te maken, zoals misschien sommige van de promotievideo's je zouden hebben denken.
Het tweede grote aspect is dat er behalve de onze geen andere technologie op de markt is die echt geautomatiseerd is. Ja, er zijn nabewerkingstechnologieën, maar meestal zijn het herhalingen van zeer bekende technologieën. Geen van hen is digitaal.
Momenteel moet je bedreven zijn in al die genuanceerde operaties die deze 'zwarte kunst' vereisen. Dus dat is echt een grote uitdaging. En op dit moment zijn er geen opties voor nabewerking die echt innovatief zijn, evenals een digitale stimulans.
De grootste uitdaging, in termen van technologie die we hebben gezien, is ontpoederend. Niemand heeft een echt geautomatiseerde oplossing voor uitpakken en ontpoederen bedacht die geen menselijke tussenkomst vereist. Dat is een echte uitdaging. Het is niet alleen een uitdaging voor ontpoedering en automatisering, het is een uitdaging op het gebied van machinaal leren, machinaal sorteren, en dat zijn de veelvoorkomende uitdagingen die we aanpakken.
Denk je dat we het punt zullen bereiken waarop we een volledig geautomatiseerde oplossing voor het ontpoederen zullen hebben?
We hebben partners waarmee we samenwerken om hiervoor echte oplossingen te ontwikkelen. Het is een grote ontgrendeling voor hen, want nogmaals, als je je poederbed hebt en je onderdelen moet verwijderen, is er momenteel geen andere manier om dit te doen dan handmatig. Zelfs traditionele tuimeloplossingen hebben nog steeds veel handmatige tussenkomst nodig, want waar mensen erg goed in zijn, zijn delicate en moeilijke operaties:identificatie van dingen (zoals poeder op het onderdeel), het verwijderen van dat poeder zonder het onderdeel te vernietigen en onderdelen te sorteren enz. We werken aan het automatiseren van deze stappen om tijd- en kostenefficiëntie te verbeteren.
Hoe werkt uw PostPro3D-technologie?
PostPro3D is onze kerntechnologie. Het was gebaseerd op IP-licentie van de Universiteit van Sheffield en vervolgens ontwikkeld met een Innovate UK-subsidie. Het is ongeveer 8 jaar in ontwikkeling geweest op het gebied van fundamenteel onderzoek, gevolgd door industrieel onderzoek.
Het is een chemisch proces voor het gladmaken van dampen waarbij gepatenteerde chemicaliën worden gebruikt om het oppervlak van een 3D-geprint polymeeronderdeel glad te maken.
Door het oppervlak glad te maken, bedoelen we niet alleen dat het esthetisch aantrekkelijk wordt, we ontwerpen eigenlijk het oppervlak van het onderdeel. De chemische oplossing sluit het oppervlak af en verwijdert de porositeit van het onderdeel. Het voorkomt ook het binnendringen van water of gas en verbetert zelfs de mechanische eigenschappen. Het resultaat is een onderdeel met een hoge rek bij breuk en betere vermoeiingseigenschappen.
Daarnaast zijn er alle elastomere materialen die we kunnen verwerken, die bijvoorbeeld niet kunnen worden verwerkt, zelfs niet met mechanische methoden. De PostPro3D kan onderdelen nabewerken die zijn geprint met behulp van hoogtechnologische polymeren zoals ULTEM, nylons, TPU en TPE, enz.
De PostPro3D is de eerste machine met oppervlaktemodificatietechnologie die we op de markt hebben gebracht. Het is een industrieel apparaat dat is ontworpen voor industriële eindgebruikers, met een proceskamer van bijna 100 liter om grotere hoeveelheden onderdelen te verwerken.
We hebben ook de PostPro3D Mini uitgebracht. Het is fysiek een derde van de grootte van de PostPro3D, aanzienlijk goedkoper maar met dezelfde vlaggenschiptechnologie om het gebruik uit te breiden naar onderzoeksinstituten, kleinere servicebureaus en mensen die misschien maar één printer hebben. En dat is redelijk geprijsd om toegankelijk te zijn voor die mensen, zodat ze de technologie kunnen uitproberen voordat ze zich committeren aan iets groters of activiteiten uitbreiden.
Het voordeel van ons proces is dat al onze onderdelen en bewerkingen het heeft cyclustoxiciteitstests ondergaan en het gaat momenteel door de medische goedkeuring van de FDA, enz. Dus dat is echt belangrijk als we het hebben over gereguleerde, industriële eindgebruikstoepassingen.
Bovendien complementair aan die technologie zijn onze kleurtechnologieën. We hebben onze unieke, gepatenteerde technologie voor kleuren, waarmee we een onderdeel tegelijkertijd kunnen kleuren en gladmaken, zodat u kleur kunt toevoegen terwijl u het gladstrijkt. Dat opent dan ook een hele reeks andere toepassingen.
Aan de andere kant hebben we onze ontpoederingssystemen, die we, zoals ik al zei, momenteel aan het testen zijn met enkele van onze productiepartnerbedrijven. Hiermee kunnen we het poederbed automatisch uitpakken, ontpoederen en de onderdelen uit poederbed AM-systemen verwijderen.
Uiteindelijk moeten we het allemaal met elkaar verbinden. We hebben metrologie- of inspectiesystemen die zijn ontwikkeld in samenwerking met de Universiteit van Nottingham, en de slimme stukjes zitten eigenlijk in de algoritmen en machine learning, niet in de hardware. Ze zijn dus goedkoop, wat betekent dat we ze kunnen gebruiken in overeenstemming met onze systemen en onderdelen voor kwaliteitscontrole terwijl we onze processen doorlopen.
En dan het laatste deel is de end-to-end automatisering, die we ons digitale productiesysteem — of DMS — noemen, waarmee we het hele proces kunnen automatiseren.
Je zei dat je 95 polymeren hebt gevalideerd met je oplossingen. Overweegt u in de toekomst metalen onderdelen?
Grote vraag. Mijn achtergrond ligt eigenlijk in de metallurgie. Ik ben afgestudeerd aan de Universiteit van Sheffield op het gebied van additieve fabricage van metalen.
Maar hoewel metaal mijn achtergrond is, koos ik voor polymeren, omdat ze gemakkelijker te verwerken zijn. Metaal is een grote uitdaging, vanwege het vereiste industriële type processen.
We hebben IP ingediend over de nabewerking van metalen en we hebben oplossingen ontwikkeld voor quasi-metalen componenten. De technologie van Desktop Metal is bijvoorbeeld een op extrusie gebaseerd proces in een polymeerdrager, met een metalen onderdeel erin geklemd. We hebben dus eigenlijk IP en kunnen bijvoorbeeld Desktop Metal-onderdelen gladmaken voordat ze gesinterd worden, en we kunnen dan het niet-uitgeharde gedeelte gladstrijken. Tegen de tijd dat hij uitkomt, heb je een mooie gladde metalen staaf.
Wat betekent uw recente investeringsronde voor de toekomst van het bedrijf?
Het is volledig transformerend. We zijn een inkomstengenererend bedrijf vanaf het eerste jaar van ons bestaan, wat erg belangrijk is omdat het betekent dat er een geweldige product-markt-fit is. We ontwikkelen dus geen dingen die niet nodig zijn.
Met deze financiering kunnen we onze wereldwijde groei versnellen. Het stelt ons in staat om onze vestiging in Austin af te ronden en naar behoren uit te breiden naar de APAC-markt en in Europa.
Maar wat nog belangrijker is, deze financiering stelt ons in staat om agnostisch te blijven, in tegenstelling tot andere bedrijven.
Omdat we agnostisch wilden blijven, hebben we DSM als materiaalchemisch bedrijf gekozen. Dit geeft ons toegang tot alle expertise op het gebied van materialen en chemie waar ze bekend om staan op het gebied van traditionele en additieve fabricage, maar in wezen stelt het ons ook in staat om naar een compleet industrieel AM-ecosysteem te streven waar alleen wij van kunnen profiteren.
Maar aan de andere kant hebben we Foresight Group, Williams, een VC van een miljard pond. Dit geeft ons toegang tot al hun materiaalchemie, analyse-expertise, Formule 1-technische herkomst van de afgelopen 50 jaar, plus alle data-analyse, engineeringkosten, productoptimalisatie, ontwerpoptimalisatie, enz. Ten slotte geeft Foresight Group ons toegang tot enorme VC drijven kapitaalmarkten aan.
Bovendien geeft het ons via de verkoopkanalen een netwerk van verkoop, marketing en potentiële distributie, dat klaar is voor gebruik. Het versnelt dus echt onze reis om op te schalen.
We hebben veel gesproken over de uitdagingen met nabewerking en hoe je dat aanpakt. Even terzijde om wat meer in het algemeen over 3D-printen te praten, wat zijn enkele van de uitdagingen die je nog steeds ziet in de industrie die nog steeds potentiële toetredingsdrempels kunnen zijn?
Voor ons is het weer dezelfde uitdaging. Bedrijven die 3D-printen willen toepassen, hebben zoveel keuze. En het gaat er echt om de hype eromheen te doorbreken. Er is niet zoveel marketinghype als er was, maar er is nog steeds behoorlijk veel.
Bovendien denk ik nog steeds dat een van de grootste uitdagingen is dat voor veel bedrijven de technologie gewoon niet klaar is om op te wedden. Als u bijvoorbeeld vandaag een CNC-machine koopt, kunt u morgen onderdelen bewerken - en onderdelen van zeer hoge kwaliteit. Evenzo, als u een spuitgietmachine koopt en een gereedschap hebt, kunt u hetzelfde doen. Ik vereenvoudig een beetje, maar in grote lijnen is dit een uitdaging waar de AM-industrie voor staat.
Als je een 3D-printer koopt, het materiaal, dat alles beschouwd als apparatuur; je kunt nog steeds geen onderdelen van goede kwaliteit maken. En ik denk dat daar het probleem zit:we zijn nog ver verwijderd van een proces waar je bijvoorbeeld een miljoen onderdelen zou kunnen maken.
Een perfect voorbeeld hiervan is onze stand op Formnext. We bouwen iets meer dan zes en een half duizend afzonderlijke 3D-geprinte onderdelen, verbonden door aluminium componenten. De structuur is 4 meter bij 6 meter bij 14 meter. Dat is een enorme structuur. En je vraagt je ineens af waarom niemand het eerder heeft gedaan, en het probleem is, want voor 6000 componenten die identiek of geschikt zijn vanuit het oogpunt van herhaalbaarheid en reproduceerbaarheid, is het gewoon heel moeilijk om te doen. Het zou een maand van ontwikkeling vergen om op het punt te komen waarop je een stabiel proces hebt.
Dus echt, als we in de buurt komen van het punt waarop de processen stabiel zijn, waar we herhaalbaarheid en reproduceerbaarheid hebben, dan bereiken we industriële processen.
Een ander ding is dat we moeten ophouden te denken aan 3D-printen als een batchproces. Zie het eerder als een continu proces, met een volledige proceslijn en end-to-end automatisering.
Ik denk dat een deel van het probleem is dat veel mensen al te lang met 3D-printen bezig zijn en het zien opgroeien. We zien nu echter een nieuwe revolutie, waarbij mensen het echt zien als een industriële technologie, maar om dat echt te laten werken, is een mind-shift vereist. En daarom heeft ons bedrijf zoveel geluk, want niet iedereen is van 3D-printen. Dus we brengen een heel ander perspectief in het proces.
Kun je vertellen hoe je je stand op Formnext opbouwt?
Dit jaar hebben we een stand van 86 vierkante meter, die bijna als een roosterstructuur is opgebouwd. Elk knooppunt is een reeks onderling verbonden 3D-geprinte onderdelen, en we bouwen de structuur op uit deze individuele componenten die kubussen vormen, en de kubussen vormen de structuur, die 4 meter hoog is. Maar het punt is, het is erg licht van gewicht. De hele constructie weegt niet meer dan 120 kilogram.
We denken dat dit de eerste keer is dat iemand dit heeft geprobeerd. Zonder nabewerking zou het buitengewoon moeilijk zijn om dit te bereiken. Uiteraard gebruiken we onze schroefdraadverbindingen met tolerantie, ingewikkelde interne geometrieën, enzovoort. En wat hier belangrijk is, is dat we dit zonder de technologie die we hebben ontwikkeld niet hadden kunnen produceren. We hadden de onderdelen kunnen printen, maar we zouden ze niet hebben kunnen afmaken en ze in de juiste kwaliteit kunnen krijgen die nodig is om daadwerkelijk iets te bouwen.
Zijn er opwindende trends of ontwikkelingen waar u persoonlijk enthousiast over bent?
Ik vind het geweldig dat mensen nabewerking als een probleem zien en er iets aan willen doen. Het is geweldig om te zien dat de nabewerking eindelijk serieus wordt genomen.
In het AMFG-landschap van de AM-industrie was het interessant om te zien dat er 2 of 3 nabewerkingsbedrijven zijn. Voor mij was dat een geweldige visuele weergave van het feit dat van alle 3D-printbedrijven er maar een paar zijn in nabewerking.
Maar mensen praten er zeker meer over, en onderwijs is hier echt noodzakelijk. Want als je het niet weet, weet je ook niet dat het een probleem is. We moeten ons dus informeren voordat we kunnen verkopen, en we moeten onszelf ook informeren over wat onze gebruikers nodig hebben.
De andere opwindende trend is dat we nu industriële spelers op de markt zien komen, en ik bedoel niet printerfabrikanten, ik bedoel gebruikers van de technologie. Bedrijven zijn dus echt op zoek naar 3D-printtoepassingen en overwegen nu serieus 3D-printen, en dat is een mooie trend.
Uiteindelijk moeten we ons concentreren op toepassingen in het echte leven - ze zijn misschien niet zo opwindend als PR-gerichte, spraakmakende toepassingen, maar ze laten zien dat de industrie volwassen wordt.
Ik zal je een analogie geven:wanneer was de laatste keer dat iemand naar je toe kwam en zei:'Kijk eens naar dit spuitgegoten onderdeel, kijk eens hoe geweldig het is'. Het maakt je niet uit, niemand geeft erom, het maakt gewoon niet uit. Dat is wat we uit ons hoofd moeten zetten en gewoon door moeten gaan met de nieuwe technologie. En de tijd zal komen dat niemand het verschil zal weten.
We zijn al begonnen, en we laten het mensen zien door te zeggen:'Kijk, dit is een spuitgegoten onderdeel', en ze knipperen niet eens. Dan laten we ze een 3D-geprint onderdeel zien dat we hebben nabewerkt en ze zeggen:'Oh mijn God, dat is geweldig'. We moeten daar voorbij zien te komen en het gewoon als een andere productietechnologie kunnen accepteren.
Hoe zien de komende 12 maanden eruit voor AMT?
De komende 12 maanden zullen we een zeer snelle groei zien, zowel wat betreft onze uitbreiding als onze omzet.
We zullen eind volgend jaar ook ons end-to-end DMS-systeem lanceren, dat omvatten ontpoederen, gladmaken, kleuren en inspectie - volledig geautomatiseerd. En dat is echt onze focus als we 2020 ingaan - om die elementen aan elkaar te koppelen, zodat we echt een end-to-end nabewerkingssysteem kunnen bieden in de ware zin van het woord.
Ga voor meer informatie over AMT naar:https://amtechnologies.co.uk/
3d printen
- AMFG's Keyvan Karimi:"Waarom het tijd is voor additieve productiesoftware om te evolueren"
- Additive Manufacturing Technologies:het nabewerkingsbedrijf dat de toekomst van de productie vormgeeft
- 6 redenen waarom u ontwerp voor additieve productie moet overwegen
- Expertinterview:Nanoe CEO Guillaume de Calan over de toekomst van keramisch 3D-printen
- Hoe Ford Motor Company 3D-printen voor de auto-industrie innoveert:interview met experts van Harold Sears
- Interview met expert:CEO van PostProcess Technologies over het oplossen van het knelpunt in de nabewerking voor additieve productie
- Interview met experts:Sintavia President Doug hedges op het bereiken van serieproductie met 3D-metaalprinten
- Interview met experts:Brian Alexander van Solvay over de ontwikkeling van hoogwaardige polymeren voor 3D-printen
- Expert Interview:Jabil's Rush LaSelle over de toekomst van additieve productie
- Interview met expert:AMendate over zijn geautomatiseerde topologie-optimalisatiesoftware voor 3D-printen
- De zaak voor 3D-printen in de productie