Applicatie Spotlight:3D-geprinte raketten en de toekomst van de fabricage van ruimtevaartuigen
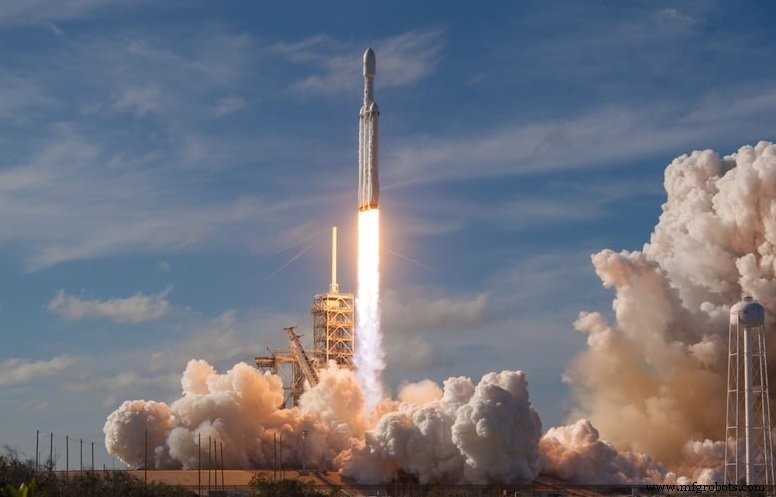
3D-printen is hard op weg een opwindende technologie te worden voor de fabricage van ruimtevaartuigen, en in het bijzonder voor raketten. Zowel startups als gevestigde fabrikanten omarmen 3D-printen om raketcomponenten te maken met verbeterd ontwerp en betere prestaties tegen lagere kosten en met snellere doorlooptijden.
Deze week gaan we verder met onze Application Spotlight-serie door te kijken naar de voordelen van 3D-printen voor raketonderdelen, en zelfs hele raketten.
Bekijk de andere toepassingen die in deze serie worden behandeld:
3D-printen voor warmtewisselaars
3D-printen voor lagers
3D-printen voor fietsproductie
3D-printen voor productie van digitale tandheelkunde en heldere uitlijners
3D-printen voor medische implantaten
3D-printen voor de productie van schoenen
3D-printen voor elektronische componenten
3D-printen in de spoorindustrie
3D-geprinte brillen
3D-printen voor productie van eindonderdelen
3D-printen voor beugels
3D-printen voor turbineonderdelen
Hoe 3D-printen zorgt voor beter presterende hydraulische componenten
Hoe 3D-printen innovatie in de kernenergie-industrie ondersteunt
Waarom wordt 3D-printen gebruikt om raketcomponenten te maken?
De race om satellieten naar de ruimte te brengen wordt steeds heviger.
Om deze reden staan ruimtevaartuigfabrikanten voor de uitdaging om de ontwikkeling en productie van raketten te versnellen, terwijl ook de kosten worden verlaagd en de efficiëntie wordt verhoogd.
Bij conventionele raketproductie maken meerdere prototypingcycli en productiestappen het proces echter lang en zeer kostbaar.
Het kan bijvoorbeeld tussen de 10 en 14 maanden duren om een conventionele verbrandingskamer te maken (een structurele raketcomponent waarbij een mengsel van brandstof en perslucht wordt ontstoken).
Om deze verbrandingskamers te produceren, moeten fabrikanten afzonderlijke componenten gieten en smeden. Koelkanalen moeten dan worden bewerkt rond de kamer — een zeer tijdrovend, arbeidsintensief en kostenintensief proces.
Gezien deze uitdagingen beginnen grote raketfabrikanten al met het produceren van verbrandingskamers met additieve fabricage. Eenmaal ontworpen, kan een 3D-geprinte verbrandingskamer binnen enkele weken worden vervaardigd, waardoor fabrikanten de productietijden en -kosten aanzienlijk kunnen verminderen.
Het vervaardigen van hardware die in de ruimte wordt gelanceerd, vereist uitzonderlijke prestaties en precisie. Voor een succesvolle lancering moet elk onderdeel naadloos op elkaar aansluiten.
Bij traditionele fabricage worden ingenieurs geconfronteerd met beperkingen bij het ontwerpen van zeer complexe raketonderdelen. Met 3D-metaalprinten kunnen ingenieurs enkele van de beperkingen van traditionele processen overwinnen en sneller complexere raketcomponenten ontwikkelen.
De 3D-printtechnologieën die worden gebruikt om raketcomponenten te vervaardigen
Vanaf vandaag hebben ruimtevaartbedrijven over het algemeen op laser gebaseerde 3D-printtechnologieën voor metaal gebruikt, zoals Selective Laser Melting (SLM) om onderdelen voor raketmotoren te produceren, zoals verbrandingskamers, injectoren, mondstukken, pompen en kleppen. SLM past een krachtige, nauwkeurig afgestelde laser toe op een laag metaalpoeder, waarbij metaaldeeltjes samensmelten. Het proces wordt honderden lagen herhaald totdat een onderdeel is gemaakt.
SLM biedt hoge precisie (kan lagen tot 20 micron printen) en is geoptimaliseerd om te werken met een breed scala aan hoogwaardige metalen , van titanium tot nikkellegeringen. Deze technologie wordt meestal gebruikt voor kleinere onderdelen.
Naast SLM gebruiken sommige ruimtevaartuigbedrijven Direct Energy Deposition (DED)-technologie om grote componenten te maken. DED 3D-printers werken door metaalmateriaal te smelten met een laser of een elektronenstraal terwijl het via een mondstuk op het bouwplatform wordt afgezet.
Normaal gesproken hebben DED-machines een hoge materiaaldepositiesnelheid en kunnen ze werken met metalen materialen in poeder- of draadvorm, waardoor zeer dichte onderdelen worden gemaakt met bijna netvormen.
De voordelen van 3D-printen voor raketten
Het vermogen om te herhalen snel
Een van de grootste voordelen van 3D-printen voor raketonderdelen is de mogelijkheid om ontwerpen zeer snel te herhalen.
“Met additief kun je vijf iteraties van een ontwerp doorlopen voordat je de eerste zelfs maar op een traditionele manier krijgt, en die vijf samen zullen waarschijnlijk minder dan één kosten traditionele iteratie ”, zegt Scott Killian, Aerospace Business Development Manager voor EOS Noord-Amerika in een interview met engineering.com.
Een 3D-printer kan raketonderdelen rechtstreeks vanuit een ontwerpbestand maken zonder dat daarvoor gereedschap nodig is. Als een onderdeel moet worden aangepast, kunnen technici eenvoudig wijzigingen aanbrengen in een origineel CAD-bestand en veel sneller een nieuw, aangepast ontwerp maken dan met traditionele processen mogelijk is.
Ontwerpflexibiliteit
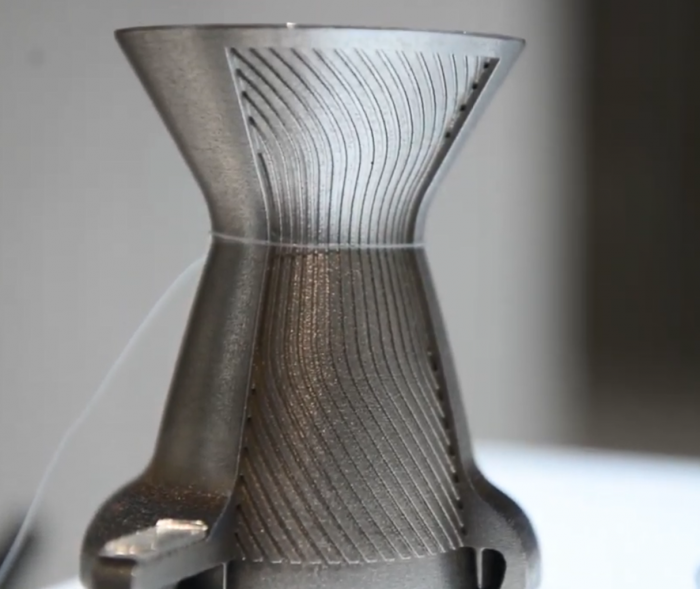
Zonder de afhankelijkheid van gereedschap, biedt 3D-printen ruimtevaartuigingenieurs de flexibiliteit om complexe vormen en geometrieën te creëren die met conventionele processen niet haalbaar zijn.
Denk aan verbrandingskamers. Een cruciale component in alle raketmotoren, een verbrandingskamer moet bestand zijn tegen een omgeving onder hoge druk en temperaturen tot 5.000 ° F (2760 ° C), aangezien drijfgassen zich vermengen en binnenin ontbranden.
Om efficiënt te kunnen presteren, heeft dit onderdeel complexe, interne koelkanalen nodig die gevuld zijn met gassen die zijn gekoeld tot minder dan 100°F (38°C) boven het absolute nulpunt.
Traditioneel zijn deze koelkanalen erg ingewikkeld en kostbaar om te ontwikkelen. Ze vereisen gespecialiseerd gereedschap om koelkanalen te CNC-machines en de buitenwand van de kamer te solderen. Deze afzonderlijke segmenten moeten dan tot één stuk worden gelast.
3D-printen daarentegen stroomlijnt het proces door het mogelijk te maken om de hele kamer direct te produceren. Bovendien maakt het complexe koelkanaalontwerpen mogelijk, zoals weergegeven in de afbeelding hierboven, die onmogelijk te machinaal zouden zijn.
Minder dure raketonderdelen
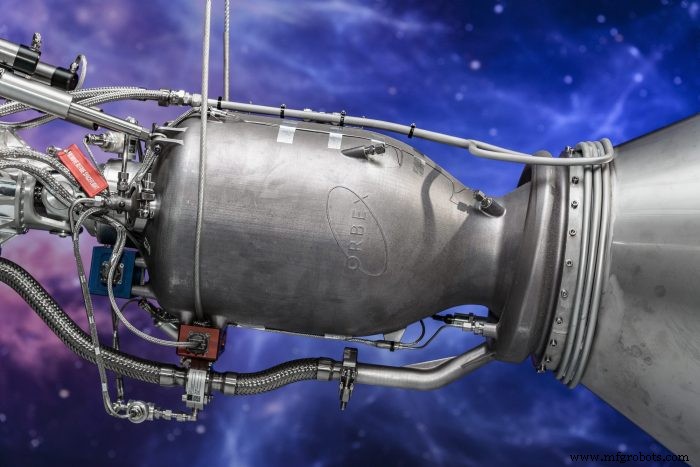
Motoren zijn het duurste onderdeel van een lanceervoertuig (een raketaangedreven voertuig dat wordt gebruikt om satellieten of andere ruimtevaartuigen de ruimte in te lanceren). De kosten van een motor kunnen oplopen tot 40% van de kosten van de gehele raket. Door 3D-printen te gebruiken om cruciale motoronderdelen te maken, kunnen raketfabrikanten de totale kosten van een ruimtevaartuig drastisch verlagen.
3D-printen stelt ingenieurs in staat om de productie van raketmotorcomponenten te stroomlijnen, waarbij een aantal productiestappen worden omzeild. Hoe minder stappen, hoe minder apparatuur en finetuning er nodig is, wat uiteindelijk resulteert in lagere productiekosten.
Bovendien betekent automatisering van het productieproces met 3D-printen dat de meeste arbeidskosten uit de vergelijking worden gehaald .
Het Britse ruimtevaartbedrijf Orbex gebruikte bijvoorbeeld SLM-technologie en een nikkellegering om een motor voor zijn Prime-draagraket in 3D te printen. Met 3D-metaalprinten kon Orbex de doorlooptijd met 90% verkorten en de kosten met 50% verlagen in vergelijking met meer traditionele productieprocessen, zoals CNC-bewerking.
Elon Musk's particuliere commerciële ruimteonderneming, SpaceX, heeft omarmde ook 3D-printen om de kosten te verlagen en meer flexibiliteit te bieden in het productieproces van zijn Draco- en SuperDraco-thrusters. Het bedrijf gebruikt een op SLM gebaseerde metalen 3D-printer om Inconel-verbrandingskamers te maken.
Volgens Musk kunnen "door 3D-printen robuuste en hoogwaardige motoronderdelen worden gemaakt tegen een fractie van de kosten en tijd van traditionele productiemethoden .”
Vereenvoudigde montage
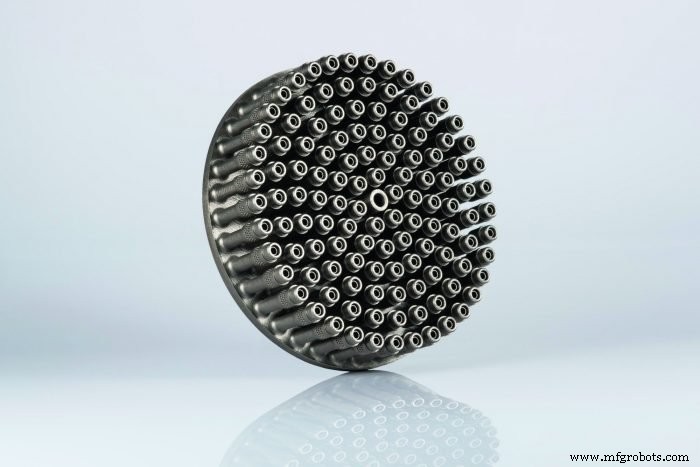
Bovendien kunnen ingenieurs ook het aantal stappen in het assemblageproces sterk verminderen. Dit kan worden bereikt door raketonderdelen die uit meerdere componenten zijn gemaakt, als één stuk in 3D te printen.
Neem als voorbeeld een injectorkop. Een injectorkop is een van de kernelementen van een aandrijfmodule, die het brandstofmengsel in de verbrandingskamer dwingt.
Traditioneel worden injectorkoppen gemaakt van tientallen of zelfs honderden onderdelen, die machinaal moeten worden bewerkt en aan elkaar moeten worden gelast. Daarentegen kan 3D-printen dergelijke componenten als één stuk produceren.
Onderzoekers van het Duitse Lucht- en Ruimtevaartcentrum (DLR) gebruikten 3D-printen om een nieuw ontwerp te maken van een injectorkop voor een kleine satellietdraagraket.
Het resultaat is een monolithisch onderdeel dat 10% lichter is. Door het aantal componenten te verminderen van 30 naar slechts één, heeft het onderzoeksteam ook bekende storingspunten op bevestigingslocaties geëlimineerd. Ten slotte zou het nieuwe, geoptimaliseerde ontwerp de prestaties van het onderdeel verbeteren en de levensduur van het onderdeel verlengen.
Evenzo heeft metaal 3D-printspecialist EOS de montage van een injectorkop voor zijn Ariane 6-draagraket vereenvoudigd , ontwikkeld door ArianeGroup, een joint venture van Airbus Group en Safran.
Het gebruik van SLM-technologie stelde het team in staat een injectorkop opnieuw te ontwerpen als één onderdeel in plaats van de 248 onderdelen die nodig zijn voor een traditioneel ontwerp. Bijkomende voordelen waren een kostenreductie van 50% en een drie keer kortere doorlooptijd.
Voorbeelden van 3D-geprinte raketonderdelen
Rocket Lab's 3D-geprinte Rutherford-engine
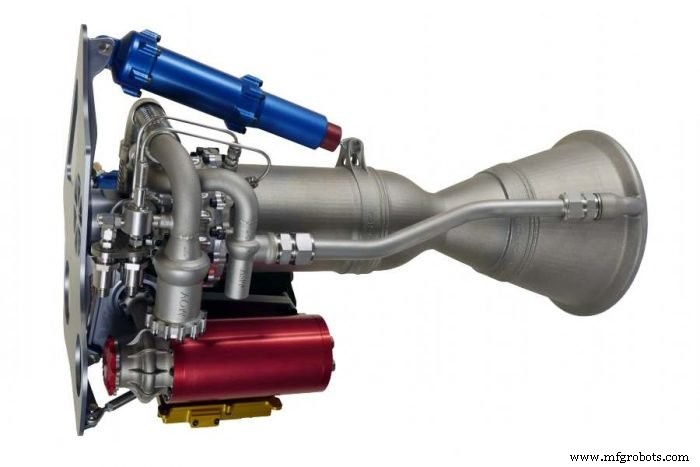
In juli voltooide Rocket Lab, een in Californië gevestigd ruimtevaartbedrijf, de 100e 3D-geprinte Rutherford-raketmotor. Het bedrijf gebruikt sinds 2013 3D-printen voor al zijn primaire motorcomponenten (inclusief verbrandingskamers, injectoren, pompen en belangrijkste drijfgaskleppen).
Negen Rutherford-motoren met vloeibare stuwstof drijven de Electron-raket van Rocket Lab aan, die is gemaakt van composieten en tot 225 kg laadvermogen kan dragen. De motoronderdelen worden 3D-geprint met behulp van Electron Beam Melting (EBM)-technologie, die naar verluidt motoronderdelen goedkoper produceert dan conventionele processen.
Onlangs bewees Rocket Lab opnieuw de betrouwbaarheid van 3D-geprinte motoren door met succes vier satellieten in een baan om de aarde te lanceren met zijn Electron launcher.
Tegen 2020 is het bedrijf van plan om twee lanceringen per maand uit te voeren. Met 3D-printen waardoor Rocket Lab in een kwestie van dagen in plaats van maanden een motor kan produceren, is het team goed gepositioneerd om dit plan uit te voeren.
3D-printen van hele raketten
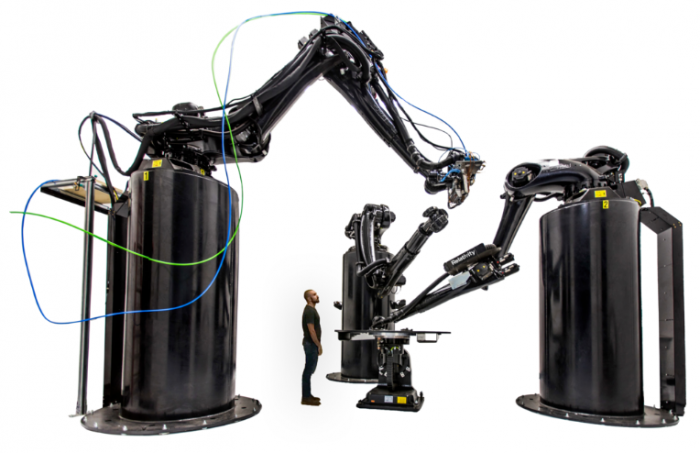
De in Californië gevestigde startup Relativity Space wil verder gaan dan 3D-geprinte raketmotoren. Het bedrijf ontwikkelt een Terran-raket, waarvan ongeveer 95% van de componenten 3D-geprint zal worden.
Om dit te bereiken heeft het bedrijf Stargate ontwikkeld, een van 's werelds grootste DED-metaal 3D-printers. Met de mogelijkheid om componenten te maken met een diameter tot 2,7 m (9 ft.) en ongeveer 4,5 m (15 ft.) hoog, zal Stargate alle brandstoftanks en andere grote raketcomponenten printen.
Door 3D-printen te gebruiken om vrijwel een hele raket te vervaardigen, hoopt Relativity Space het gewicht van de raket aanzienlijk te verminderen, wat de lanceringskosten mogelijk kan verlagen, terwijl het laadvermogen toeneemt.
3D-printen zal ook het aantal onderdelen dat moet worden geassembleerd verminderen, waardoor de sterkte en stabiliteit van de raket wordt vergroot.
Voor kleinere onderdelen gebruikt het bedrijf SLM-technologie.
Volgens Relativity Space stelt 3D-printen het in staat om ontwerpen snel te veranderen en minder gereedschap en arbeid te gebruiken dan normaal nodig zou zijn bij de ontwikkeling van raketten. Uiteindelijk zou dit Relativity Space in staat kunnen stellen om in minder dan twee maanden van onbewerkt materiaal naar een vliegklare raket te gaan.
Relativity Space is momenteel het enige bedrijf dat 3D-printtechnologieën toepast voor een volledige raket. Zal het concept van een 3D-geprinte raket succesvol zijn? Het antwoord zal uiteindelijk liggen in testen en lanceren. De testlancering van de 3D-geprinte Terran-raket staat gepland voor eind 2020.
De toekomst van 3D-printen in de ruimtevaart
3D-printen heeft een revolutie teweeggebracht in de manier waarop raketten en onderdelen van raketmotoren worden ontworpen en geproduceerd. De basisprincipes van raketontwerp zijn misschien niet veranderd, maar 3D-printen met metaal heeft nieuwe manieren ontgrendeld om de raketprestaties te verbeteren en meer ontwerpvrijheid te bieden.
De technologie kan helpen om de productiekosten van motoren, een van de duurste raketcomponenten, te verlagen. Dit wordt bereikt door het aantal productiestappen te verminderen en frequentere ontwerpiteraties mogelijk te maken.
Hoewel de mogelijkheden van 3D-printen buiten motoronderdelen nog moeten worden getest, is het potentieel van de technologie voor volledig 3D-geprint raketten in de toekomst is echt spannend.
3D-printen is een belangrijke productietechnologie geworden voor de productie van ruimtevaartuigen, waardoor ingenieurs sneller kunnen innoveren en de volgende generatie ruimtevaart tot stand kunnen brengen.
In ons volgende artikel zullen we kijken naar 3D-printen in de schoenenindustrie. Blijf op de hoogte!
3d printen
- Generatief ontwerp en 3D-printen:de productie van morgen
- Applicatie Spotlight:3D-printen voor digitale tandheelkunde &Clear Aligner-productie
- Applicatie Spotlight:3D-printen voor fietsproductie
- Robotica en de toekomst van productie en werk
- De voordelen van rapid prototyping en 3D-printen in de maakindustrie
- Industriële automatisering:een korte geschiedenis van productietoepassingen en de huidige stand van zaken en toekomstige vooruitzichten
- De toekomst van industriële machines in 2020 en daarna
- Welke rol zullen robotica en 3D-printen spelen in de toekomst van de maakindustrie?
- Automatisering en de toekomst van digitale productie?
- De toekomst van 3D-printen in de maakindustrie
- Is 3D-printen de toekomst van productie?