5 manieren waarop 3D-printen de traditionele productie aanvult
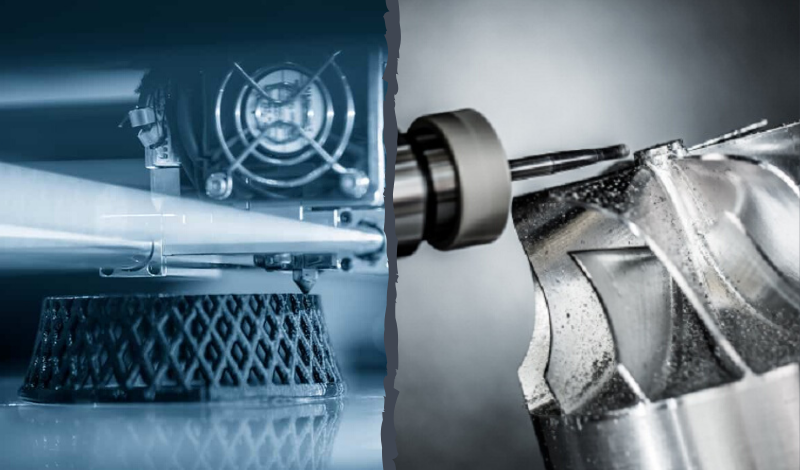
Er is voorspeld dat 3D-printen de traditionele productietechnologieën zal vervangen. De echte kracht van de technologie ligt misschien niet in het concurreren met, maar in het aanvullen en verbeteren van conventionele productiemethoden.
Om deze bewering kracht bij te zetten, onderzoeken we hieronder 5 belangrijke manieren waarop 3D-printen traditionele productie kan ondersteunen.
1. 3D-printen van beter presterende spuitgietmatrijzen
Spuitgieten omvat het proces van het smelten en injecteren van plastic materiaal in een speciaal vormgereedschap, gevormd als het gewenste object. Wanneer kunststof uithardt, neemt het de vorm aan van de vormholte. Spuitgieten is de beste manier om zeer nauwkeurige en complexe producten en onderdelen in massa te produceren.
Het proces kent echter ook enkele uitdagingen. Spuitgegoten onderdelen worden bijvoorbeeld gekoeld door kanalen te bouwen - in wezen doorgangen die zich dicht bij het oppervlak van de mal bevinden - door de mallen heen. Die kanalen zijn meestal rechte lijnen, wat soms kan leiden tot ongelijkmatige koeling, waardoor het risico op vervorming van het onderdeel toeneemt.
Efficiënte koeling kan worden bereikt met conforme koelkanalen, die zich aanpassen aan de vorm van het onderdeel. Dit soort kanalen zijn echter moeilijk te maken met conventionele methoden, waardoor 3D-printen een aantrekkelijk alternatief is voor het maken van spuitgietmatrijzen.
Het maken van mallen met conforme koelkanalen helpt niet alleen om de kwaliteit van de vormdelen te verhogen, maar helpt ook om de koeltijd aanzienlijk te verkorten.
3D-printen helpt bij het optimaliseren van de spuitgietlijn
Een voorbeeld hiervan is Alfred Kärcher GmbH &Co. KG, een bedrijf dat jaarlijks miljoenen van zijn K2-hogedrukreinigers wereldwijd verkoopt. Bij het proberen aan een dergelijke vraag te voldoen, kreeg het bedrijf te maken met een productief bottleneck, waardoor de productie van de wasmachinebehuizingen moest worden verhoogd.
In plaats van meer spuitgietmachines aan te schaffen, ging Kärcher op zoek naar manieren om de productiviteit van de bestaande machines te verhogen. Het bedrijf vond de oplossing in 3D-printen van metaal.
Kärcher wendde zich tot LBC Engineering, onderdeel van Renishaw GmbH, die ontdekte dat de gietcyclustijd werd beïnvloed door de inefficiëntie van het koelproces. De behuizingsmallen waren voorzien van traditionele koelsystemen, geboord in rechte lijnen, waardoor hotspots werden gecreëerd die de cyclustijd verlengt.
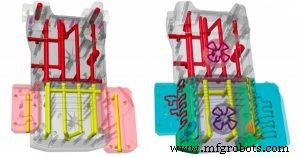
LBC Engineering heeft het ontwerp van de matrijs aangepast door twee 3D-geprinte kernen te maken om conforme koeling te bieden op de geïdentificeerde hotspots.
3D-geprinte conforme koelkanalen hielpen de wandtemperatuur in de mallen te verlagen van 100°C naar 70°C, waardoor de afkoeltijd werd verkort van 22 naar 10 seconden, een reductie van 55 procent.
Samen met enkele aanpassingen aan randcomponenten, zoals het materiaalaanvoer- en handlingsysteem, is de cyclustijd voor omhulsels gedaald van 52 naar 37 seconden. 3D-printen zorgde voor het leeuwendeel van deze reductie, waardoor Kärcher de productiviteit van zijn lijn kon verhogen en de productiedoelstellingen voor karkassen kon bereiken.
In een ander voorbeeld heeft spuitgietprofessional Pat Zaffino een meerlaagse robotdepositietechnologie ontwikkeld die conforme koelkanalen in 3D op het oppervlak van spuitgietmatrijzen print.
Eerder dit jaar lanceerde Zaffino een nieuw bedrijf, Conformal Cooling Solutions Inc. (CCS), om de voordelen van het gebruik van conforme koelkanalen te promoten.
'Creëren van conforme koelkanalen die de vorm van de holte en de kern volgen, bevordert de temperatuuruniformiteit in de kunststofmaterialen die worden gegoten, en vormers die deze technologie gebruiken, zien opvallende resultaten:kortere cyclustijden, verbeterde kwaliteit van kunststof onderdelen en - vooral - kostenbesparingen', zei hij. in een interview met canplastics.com.
Naarmate de technologie goedkoper en gemakkelijker te gebruiken wordt, kunnen matrijzen met 3D-geprinte conforme koelkanalen uiteindelijk een nieuwe standaard in de industrie worden.
2. 3D-printpatronen voor investeringscasting
Investment casting maakt gebruik van vervangbare waspatronen en keramische schalen om complexe en gedetailleerde onderdeelontwerpen te creëren. Traditioneel worden deze patronen spuitgegoten. De kosten van spuitgietmatrijzen kunnen echter oplopen tot enkele duizenden dollars, met doorlooptijden variërend van één tot vier weken. Dit maakt het proces onbetaalbaar voor mensen die misschien niet zoveel kapitaal hebben of korte deadlines hebben om onderdelen te leveren.
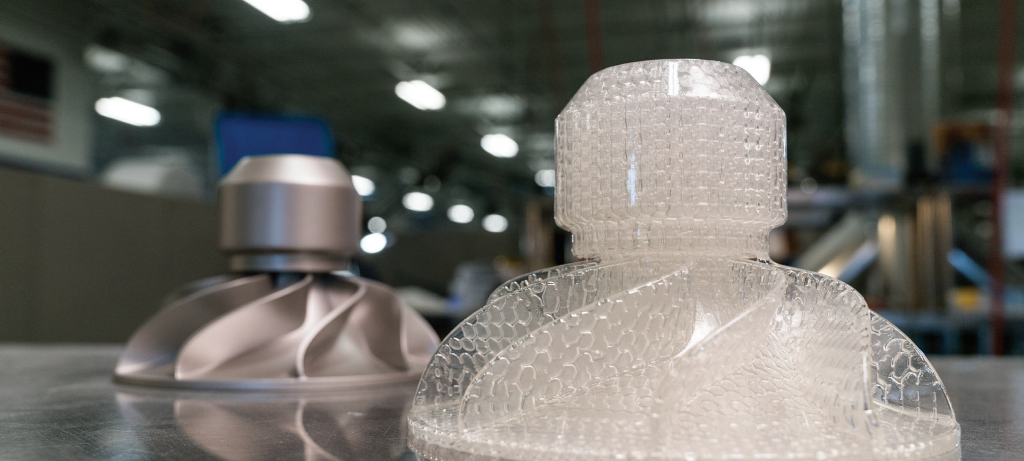
Om deze reden kunnen bedrijven ervoor kiezen om patronen in 3D te printen in een materiaal dat geschikt is voor investeringsgieten. Veel fabrikanten van 3D-printers hebben speciaal voor het gieten 3D-afdrukbare materialen ontwikkeld, waaronder was, gietbare harsen en sommige thermoplasten, op basis van PLA en ABS.
Deze materialen worden doorgaans gebruikt met stereolithografie (harsen) en FDM ( plastics) technologieën, waardoor zeer nauwkeurige patronen met uitstekende burn-out-eigenschappen worden gecreëerd.
Een ander voordeel van deze aanpak is het relatief lage risico om het te proberen. Patronen kunnen in 3D worden geprint met professionele desktop 3D-printers, die minder dan $ 5.000 kosten, een fractie van de kosten van duurdere industriële 3D-printapparatuur.
Versnelde doorlooptijden voor gietstukken met 3D-printen
3D-geprinte investeringsgietpatronen worden steeds vaker gebruikt om sieraden op maat te maken met ingewikkelde ontwerpen en kortere doorlooptijden. Zo kon het Canadese sieradenbedrijf Vowsmith, dat gespecialiseerd is in op maat gemaakte ringen, zijn productie- en levertijden met 50% verkorten door de 3D-waxprinters van 3D Systems in zijn workflow te integreren. In een enkele print produceerde het bedrijf tussen de 35 en 40 gepersonaliseerde ringpatronen, klaar om te gieten.
De technologie wordt ook steeds vaker toegepast in gieterijen, om complexe patronen te creëren voor een breed scala aan industriële toepassingen. Invest Cast, Inc. heeft bijvoorbeeld onlangs de nieuwe digitale gieterijoplossing van 3D Systems geïntegreerd in zijn patroonproductie.
De mogelijkheid om definitieve gegoten onderdelen te maken zonder een mal te bewerken, heeft de klanten van Invest Cast de vrijheid gegeven om test meerdere iteraties snel en kosteneffectief, waardoor ze uiteindelijk tot betere definitieve onderdelen kunnen komen.
Volgens Invest Cast heeft de ProJet MJP 2500 IC 3D-printer van 3D Systems veel tijd bespaard met het gietproces van de investering . De technologie stelt het bedrijf in staat om in 2-5 dagen van model naar metaal te gaan, wat lager is dan de gemiddelde doorlooptijd van ongeveer 6-12 weken met investeringsgietmatrijzen.
3. Productiviteit verhogen met 3D-geprinte snijgereedschappen
3D-printen kan worden gebruikt om snijgereedschappen te maken - kleine inzetstukken van hardmetaal die materiaal uit het geprogrammeerde gereedschapspad verwijderen.
Sommige hoogwaardige materialen, zoals ultrasterk staal, titanium en nikkellegeringen, kunnen moeilijk te bewerken zijn en kunnen ertoe leiden dat het gereedschap snel verslijt.
3D-printgereedschappen met aangepaste geometrieën, met ingebouwde koelkanalen die de overtollige warmte die tijdens het bewerken in de buurt van de snijzone wordt gegenereerd effectief kunnen verwijderen, kunnen de standtijd en prestaties verlengen.
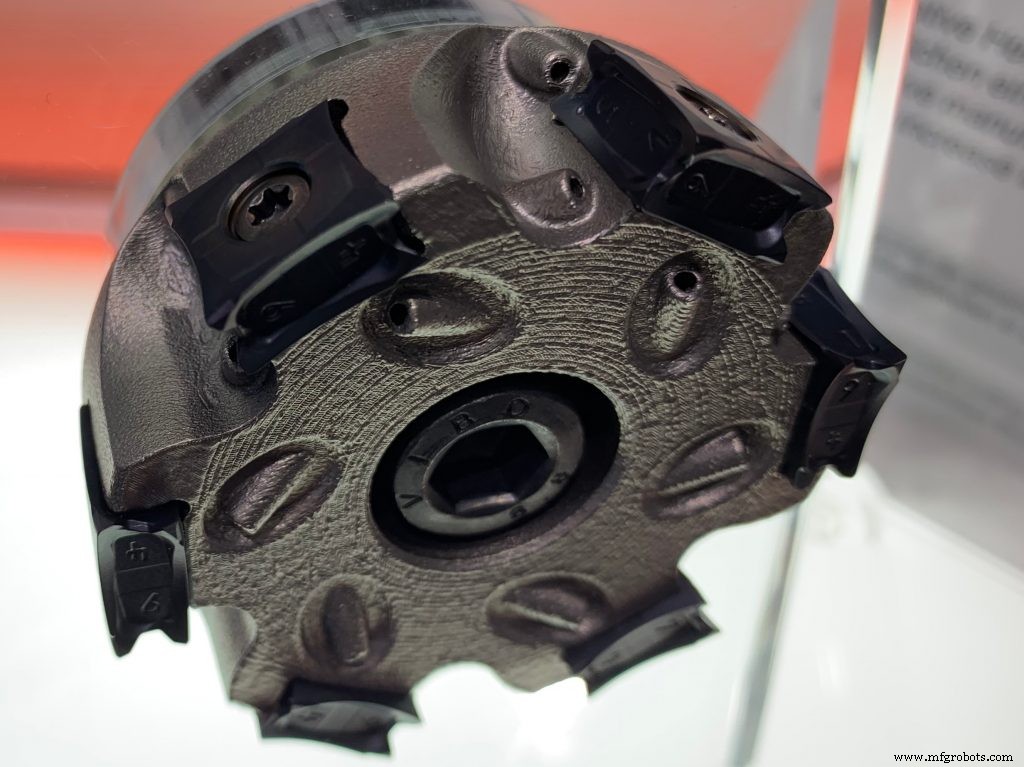
Gereedschapsspecialist LMT Tools Inc. heeft de technologie gebruikt om interne koelmiddeldoorgangen te creëren in een freeslichaam, dat voorheen rechte gaten had. Dankzij de vrijheid van 3D-printen om gebogen kanalen te bieden, kan het freesgereedschap van LMT koelmiddel precies daar leveren waar het nodig is. LMT zegt dat proefsnijden een verbetering van de standtijd van 50 procent heeft laten zien bij het frezen van titanium, dankzij deze ontwerpwijziging.
Komet Group verhoogt gereedschapsproductiviteit met 3D-printen
Een van 's werelds toonaangevende leveranciers van precisiesnijgereedschappen, Komet Group, past ook metaal 3D-printen toe voor de productie van gereedschappen.
Met behulp van aluminiumlegering en lasertechnologie van de Britse specialist Renishaw kon Komet meer snijkanten in het gereedschap introduceren en de geometrie optimaliseren om de gereedschapsproductiviteit te verhogen.
Ingenieurs hebben bijvoorbeeld de koelmiddelkanalen van het gereedschap geoptimaliseerd om ervoor te zorgen dat elke snijkant nauwkeurig wordt voorzien van koelmiddel via een afzonderlijk kanaal. Dankzij deze ontwerpverbeteringen kan de bewerkingstijd per eenheid tot 50 procent worden verminderd.
AM biedt ook de mogelijkheid om het gewicht van de componenten te verminderen, aangezien het materiaal alleen kan worden gebruikt waar dit nodig is voor een optimale functionaliteit van het component. Het is ook gemeld dat het beter presteert dan conventionele productiemethoden, in termen van levertijd, voor speciale of experimentele tools die de klanten van Komet nodig hebben.
3D-printen van een efficiëntere freeskop
Bovendien heeft de Zweedse fabrikant van gereedschapssystemen, Sandvik Coromant, onlangs een nieuwe frees geïntroduceerd met een metalen 3D-geprinte kop. Een primeur voor het bedrijf, het onderdeel markeert een stap in de richting van de betrokkenheid van het bedrijf bij 3D-printen voor productie voor eindgebruik.
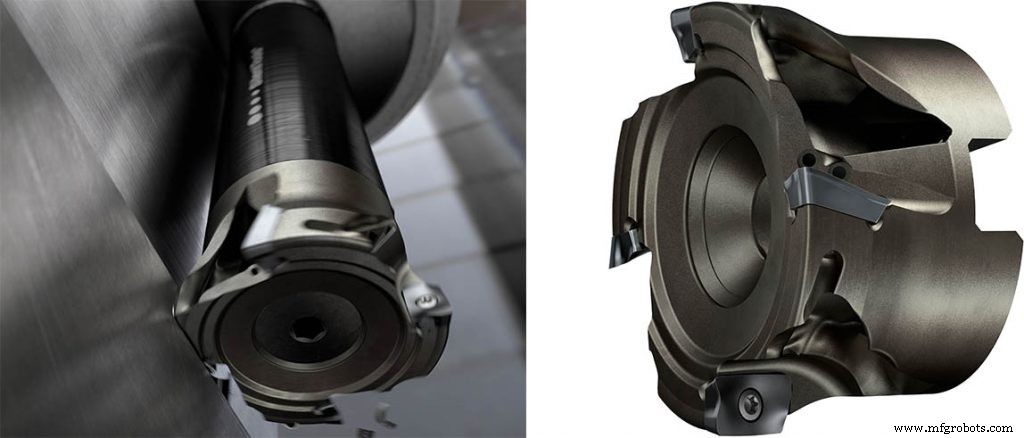
De nieuwe lichtgewicht CoroMill 390, geproduceerd door Sandvik Coromant, is een metalen freeskop gebaseerd op het CoroMill 390 ontwerp. Het gereedschap, geproduceerd met Sandvik's handelsmerk Osprey-poeder van titaniumlegering, is speciaal ontwikkeld om trillingsproblemen tijdens het frezen van metaal met lange uitsteeklengtes te overwinnen.
Dergelijke eigenschappen zijn een veelvoorkomende eis van componenten die worden gebruikt in de lucht- en ruimtevaart en de olie- en gasindustrie. Diepe holtes in een CNC-gefreesd onderdeel kunnen worden aangetast door trillingen, wat leidt tot een langzamere productie, een kortere standtijd en een slechte oppervlakteafwerking. Bij gebruik in combinatie met de Silent Tools-freesadapters van het bedrijf, meldt het bedrijf dat het 3D-geprinte gereedschap de bewerkingsproductiviteit met 50 procent kan verhogen.
4. Versleten en beschadigd gereedschap repareren
3D-printen kan niet alleen worden gebruikt om nieuwe gereedschappen en mallen te maken, maar ook om beschadigd gereedschap te repareren. Bedrijven in de lucht- en ruimtevaart, scheepsbouw en industriële goederen beginnen AM-processen, zoals Direct Energy Deposition (DED), te gebruiken om componenten terug te brengen naar hun oorspronkelijke vorm.
Ook bekend als lasercladden, gebruikt DED een laser om een lasbad op het componentoppervlak te genereren. Materiaal wordt vervolgens als poeder of draad aan het smeltbad toegevoegd. De gesmolten deeltjes smelten samen en stollen, terwijl het mondstuk wordt gemanipuleerd om de gewenste structuur aan het onderdeel toe te voegen.
Eerder dit jaar lanceerde een consortium van 7 Britse bedrijven en organisaties een project van £ 1,2 miljoen, genaamd DigiTool , om goedkope reparatie van gereedschappen en matrijzen mogelijk te maken met behulp van AM-technologieën.
Met 3D-printen kunnen bedrijven in de gereedschaps- en matrijzensector de kosten van het vervangen en repareren van matrijzen overwinnen, met het potentieel om te versnellen het onderhoudsproces op. Dit zal bedrijven helpen besparen op kosten en materialen, terwijl ze tegelijkertijd hun duurzaamheid verbeteren met minder verspilling.
Sneller reparatie van een mal-inzet
Het Duitse gereedschaps- en matrijzenbouwbedrijf HWF heeft 3D-printen gebruikt om een inzetstuk van een mal te repareren. Een van de uitdagingen waarmee HWF werd geconfronteerd, was het bouwen van een constructie van 300 x 20 x 20 mm op een typisch malmateriaal.
In het verleden werden constructies als deze opgebouwd met behulp van een handmatige draadaangedreven lasercladmethode om de risico's van scheuren, vervorming en gewijzigde metallurgische eigenschappen te voorkomen. Het kan de lasser echter tussen de 60 en 80 uur kosten om de taak te voltooien.
Vandaag de dag gebruikt HWF DED-technologie van OR Laser, waarmee het dezelfde structuur kan creëren door lagen van 250 µm dik aan te brengen, met een snelheid van 5000 mm³ per uur. De productietijd kan daardoor worden teruggebracht tot 24 uur.
Dankzij dit proces wordt het basismateriaal ook veel minder aangetast dan voorheen, waardoor het risico op scheuren en materiaalondersnijding, vaak veroorzaakt door conventionele reparatiemethoden, aanzienlijk wordt verminderd.
5. Meer flexibiliteit bereiken met hybride processen
Het combineren van additieve en subtractieve mogelijkheden in een hybride systeem is een andere manier waarop AM de traditionele productie kan aanvullen. In dit scenario kunnen additieve en subtractieve technologieën een scala aan mogelijkheden bieden voor verbeterde, one-stop-productie.
Hybride productie maakt gebruik van de meest waardevolle mogelijkheden van beide technologieën:de geometrische complexiteit van AM en de hoge precisie van subtractieve methoden. Dit betekent dat een onderdeel in één bewerking additief kan worden gemaakt en bewerkt, waardoor het productieproces wordt versneld.
Er zijn nu verschillende commerciële hybride systemen op de markt verkrijgbaar. DMG MORI combineert bijvoorbeeld DED met vijfassige CNC-capaciteit in zijn hybride productiesysteem.
Ondertussen kozen Matsuura en Sodick voor een andere aanpak, door Powder Bed Fusion (PBF)-technologie en CNC-capaciteit te combineren in hun hybride productiesystemen. Om gelijke tred te houden met de concurrentie heeft DMG MORI recentelijk gereageerd met een eigen PBF en CNC hybride systeem.
Naast een stand-alone hybride systeem is er ook een optie om een bestaand CNC-bewerkingscentrum achteraf uit te rusten met de Ambit poeder-aanvoer laserdepositiekop van Hybrid Manufacturing Technologies.
Bedrijven kunnen ook een combinatie van poeder- en draadaanvoermogelijkheden toevoegen aan een CNC-machine, met technologie van 3D Hybrid. Hierdoor kan een conventioneel subtractief systeem worden omgezet in een hybride productiesysteem met relatief minimale kosten en inspanning.
Hoewel de belofte van hybride productie boeiend is, zijn we net begonnen te leren hoe deze technologie kan worden efficiënt en levensvatbaar worden toegepast.
3D-printen omarmen als een aanvullende technologie
3D-printen kan een waardevolle aanwinst worden voor fabrikanten die hun traditionele productieprocessen willen optimaliseren.
De technologie kan worden gebruikt om beter presterende mallen en complexe gietpatronen te produceren, en om de efficiëntie van bewerkingsgereedschappen te verhogen. Bovendien kunnen hybride machines bedrijven meer vrijheid en flexibiliteit bieden bij ontwerp en fabricage.
Daarom moeten fabrikanten, in plaats van additieve fabricage als een concurrerende technologie te beschouwen, het omarmen als een ander hulpmiddel in de gereedschapskist en de voordelen ervan benutten.
3d printen
- 5 voordelen van 3D-printen in productie
- 4 manieren waarop 3D-printen de medische industrie transformeert
- 8 manieren waarop industrieel 3D-printen de productie transformeert
- 6 manieren om productiekosten te verlagen met 3D-printen
- 6 manieren om de kosten van 3D-printen te verlagen
- Applicatie Spotlight:3D-printen voor fietsproductie
- 3D-printen is overal
- 5 manieren waarop 3D-printen de auto-industrie verandert
- Additieve productie in de geneeskunde en tandheelkunde
- De toekomst van 3D-printen in de maakindustrie
- Is 3D-printen de toekomst van productie?