Applicatie Spotlight:3D-printen voor fietsproductie
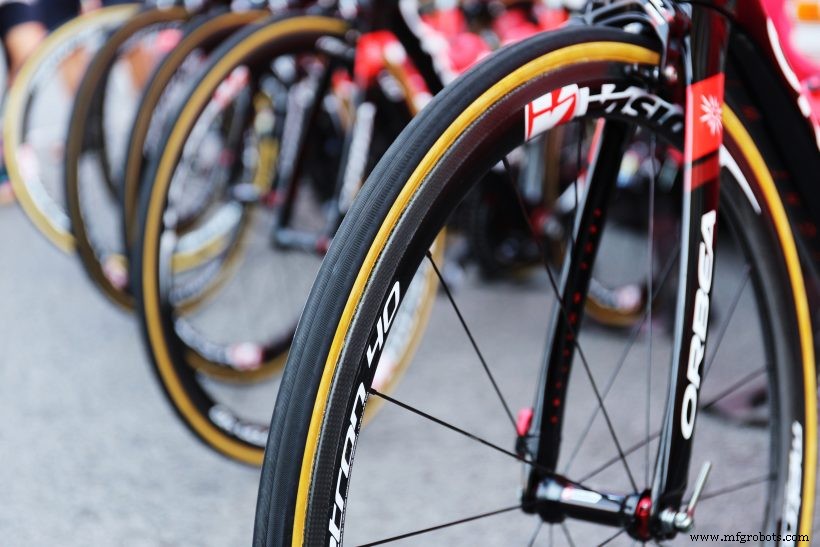
3D-printen voegt een nieuwe dimensie toe aan de fietsproductiesector, door lichtgewicht fietsen te creëren en tegelijkertijd snellere productie van op maat gemaakte fietsonderdelen mogelijk te maken.
Deze week gaan we verder met onze 3D Printing Application Spotlight-serie door te kijken naar het gebruik van 3D-printen in de productie van fietsen, evenals de voordelen en huidige toepassingen ervan.
Bekijk de andere toepassingen die in deze serie worden behandeld:
3D-printen voor warmtewisselaars
3D-printen voor lagers
3D-printen voor productie van digitale tandheelkunde en heldere uitlijners
3D-printen voor medische implantaten
3D-geprinte raketten en de toekomst van de fabricage van ruimtevaartuigen
3D-printen voor de productie van schoenen
3D-printen voor elektronische componenten
3D-printen in de spoorindustrie
3D-geprinte brillen
3D-printen voor productie van eindonderdelen
3D-printen voor beugels
3D-printen voor turbineonderdelen
Hoe 3D-printen zorgt voor beter presterende hydraulische componenten
Applicatie Spotlight:hoe 3D-printen innovatie in de kernenergie-industrie ondersteunt
Wat maakt 3D-printen geschikt voor de productie van fietsen?
Staal is van oudsher het materiaal bij uitstek voor de productie van fietsen. In de afgelopen jaren heeft dit echter plaatsgemaakt voor lichtgewicht materialen zoals titanium en koolstofvezel, die onder andere kunnen helpen om het totale gewicht van een fietsframe te verminderen.
Het hebben van een lichtgewicht fiets biedt een aantal voordelen voor een fietser. Ten eerste stelt het fietsers in staat hogere snelheden te bereiken en gemakkelijker bergop te rijden. Ten tweede, hoe lager het gewicht van een fiets, hoe gemakkelijker hij te vervoeren en te dragen is. Ten slotte kan een lichtere fiets gemakkelijker te besturen zijn tijdens het rijden en sneller reageren op de bewegingen van een rijder - wat belangrijke voordelen biedt voor competitieve fietsers.
Terwijl het maken van titanium- of koolstofvezelfietsen echter met traditionele productiemethoden is een uitdaging, niet in de laatste plaats vanwege tijdrovende en vaak arbeidsintensieve productieprocessen. Fietsframes van koolstofvezel zijn bijvoorbeeld gemaakt van meerdere stukken en vereisen een vakman om elk stuk handmatig te vervaardigen. De productie van titanium frames kan niet minder handmatig zijn, met uren besteed aan het lassen en het vastzetten van framecomponenten aan elkaar.
3D-printen daarentegen biedt een betere manier om onderdelen van titanium en koolstofvezel te maken.
Ten eerste is 3D-printen een digitaal fabricageproces dat gebruikmaakt van 3D CAD-modellen, wat inhoudt dat een onderdeel direct kan worden geproduceerd, zonder dat er speciaal gereedschap nodig is.
Bovendien kan 3D-printen fietsfabrikanten mogelijk helpen tijd te besparen en de time-to-market te versnellen. Bovendien kunnen fietsontwerpers veel meer ontwerpopties verkennen die ze niet zouden kunnen bereiken met traditionele productiemethoden.
Naast frames kan 3D-printen worden gebruikt om functionele fietsonderdelen te maken, zoals sturen, kettinghouders, dropouts (kleine lipjes in een frame of vork waar de as van het wiel is bevestigd) en nokken ( onderdelen die worden gebruikt om een frame aan verschillende onderdelen van de fiets te bevestigen).
De voordelen van 3D-printen voor de productie van fietsen
Ontwerpflexibiliteit
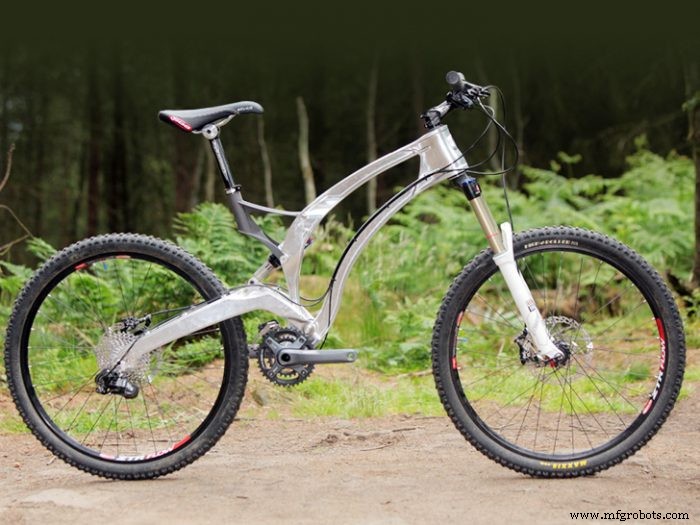
Een van de grootste voordelen van 3D-printen is de ontwerpflexibiliteit die het biedt, wat het bijzonder aantrekkelijk maakt voor fietsfabrikanten. Met 3D-printen kunnen fietsfabrikanten onderdelen ontwerpen met complexe vormen, die anders onmogelijk te produceren zouden zijn. Dit geeft hen de mogelijkheid om de fietsprestaties te optimaliseren door lichtgewicht onderdelen te ontwerpen. Dit kan worden bereikt dankzij software voor topologie-optimalisatie en roosterstructuren.
Topologie-optimalisatiesoftware gebruikt complexe algoritmen om de materiaalverdeling van een onderdeel te optimaliseren. Dit betekent dat de software op basis van specifieke parameters bepaalt waar het materiaal kan worden verwijderd zonder de sterkte van het onderdeel in gevaar te brengen.
Bijvoorbeeld, het Britse fietsfabrikant Empire Cycles, werkte samen met de fabrikant van 3D-printers, Renishaw, om een topologisch geoptimaliseerd titanium fietsframe te creëren. Renishaw ontwikkelde een nieuw frameontwerp dat 33% lichter was dan het origineel. Het geoptimaliseerde ontwerp is voorzien van holle structuren en op maat gemaakte elementen die met conventionele processen onbetaalbaar en vrijwel onmogelijk te realiseren zouden zijn.
Betaalbare aanpassingen
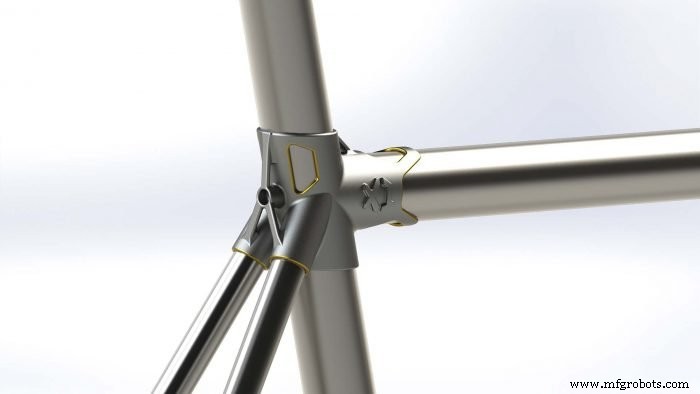
Als het gaat om de productie van fietsen, hecht maatwerk veel waarde. Aanpassing helpt niet alleen om een uniek tintje aan het ontwerp van een fiets toe te voegen, maar wat nog belangrijker is, het kan ook de prestaties van de fiets zelf verbeteren.
De ontwerpflexibiliteit die wordt geboden door 3D-printen gaat hand in hand met de mogelijkheid om fietsonderdelen kosteneffectief aan te passen, mede dankzij de productie zonder gereedschap.
In één case study gebruikte ideeën2cycles, een fietstechniekbedrijf, de metalen 3D-printer van ExOne om een set stalen 3D-geprinte aangepaste fietsonderdelen te maken. Deze onderdelen omvatten uitsteeksels, beugels, uitvaleinden en vorkkronen.
Het produceren van gepersonaliseerde fietscomponenten vereist veel handwerk, aangezien elk ontwerp uniek is en speciaal gereedschap duur is. Voor een klein bedrijf als ideas2cycles zouden de kosten onbetaalbaar zijn als traditionele methoden zouden worden gebruikt.
Dankzij ExOne's metal binder jetting-technologie werden de onderdelen echter in 4 dagen vervaardigd in plaats van 3 tot 4 weken die traditioneel vereist waren om investeringsgietpatronen te creëren en de onderdelen handmatig aan te passen. Bovendien verlaagde 3D-printen de productiekosten met meer dan 50%, van $ 1.000 (inclusief arbeid) tot $ 425 USD per assemblage.
Het gebruik van 3D-metaalprinten om onderdelen direct te produceren, bespaarde niet alleen tijd en geld, maar, belangrijker nog, stelde ontwerpers bij ideas2cycles in staat zich te concentreren op het creatieve aspect van ontwerp zonder traditionele productiebeperkingen.
Sneller time-to-market
Als het gaat om fietsen gemaakt met koolstofvezel, kan 3D-printen de doorlooptijden aanzienlijk versnellen.
Het proces van het ontwerpen, prototypen en vervaardigen van traditionele fietsframes van composiet kan bijvoorbeeld bijna een jaar duren. Bovendien is het fabricageproces zeer handmatig en tijdrovend. Frames kunnen uit 20 tot 30 delen bestaan die worden gemaakt door vellen van het composietmateriaal met de hand in lagen te leggen. Dit meerstaps- en arbeidsintensieve proces wordt vaak weerspiegeld in de hoge kosten van het product.
Een 3D-geprint koolstofvezelframe daarentegen stelt fietsfabrikanten in staat om een zeer lang proces van het op de markt brengen van een nieuwe fiets.
Arevo is een bedrijf dat een composiet 3D-printtechnologie heeft ontwikkeld om fietsframes van koolstofvezel te produceren.
Arevo verkort de ontwerp- en productietijd voor een eBike van koolstofvezel van maanden tot dagen
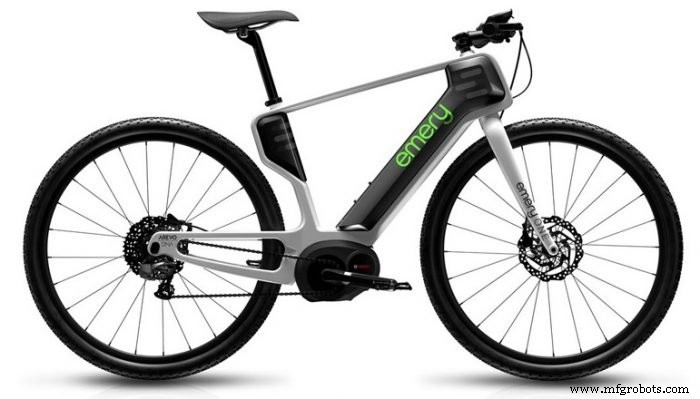
Boutique-fietsfabrikant Franco Bicycles heeft een nieuwe lijn eBikes gelanceerd met een 3D-geprint composietframe, vervaardigd door de in Californië gevestigde startup Arevo. Het frame maakt deel uit van het Emery-fietsassortiment en wordt gebruikt in de Emery ONE eBike, waardoor het 's werelds eerste fiets is met een 3D-geprint frame.
Een van de unieke aspecten achter de productie van het 3D-geprinte koolstofvezelframe is dat het als een enkel onderdeel is vervaardigd in tegenstelling tot een meerdelige montage die typisch is voor traditionele fietsframes. Dit wordt mogelijk gemaakt door Arevo's gepatenteerde robot 3D-printproces en gepatenteerde generatieve ontwerpsoftware.
Voorafgaand aan de productie optimaliseert de software van Arevo het CAD-ontwerp en kunnen de frame-eigenschappen worden aangepast.
“[Met behulp van softwaretools] kunnen we de stijfheid in bepaalde delen van de fiets afstemmen en, indien gewenst, op verzoek een nog veerkrachtiger rit mogelijk maken”, zegt Arevo's medeoprichter en CEO, Wiener Mondesir . "Een 3D-geprint frame... opent een nieuw bedrijfsmodel voor een industrie die gewend is aan het zeer lange proces van het op de markt brengen van een nieuwe fiets."
Zodra het ontwerp is goedgekeurd, wordt het geproduceerd door Arevo's robot 3D-printer met PEEK-filamenten versterkt met continue koolstofvezels. De printer heeft een printkop die is bevestigd aan een robotarm met zes assen.
Door de robotarm te bewegen, kan de printkop het materiaal continu afzetten om de verbeterde prestaties van het onderdeel te garanderen. Door deze aanpak ontstaat een frame uit één stuk dat in alle drie de dimensies even sterk is.
Dankzij dit proces is de doorlooptijd van het Emery ONE-frame teruggebracht van een cyclus van 18 maanden tot slechts een paar dagen. Bovendien was het bedrijf ook in staat de kosten voor productontwikkeling aanzienlijk te verlagen.
Revolutionaire productie van fietsen met 3D-printen
3D-printen biedt een reeks unieke voordelen voor de productie van fietsen. Daarom integreren een handvol gespecialiseerde fietsfabrikanten al 3D-geprinte componenten in hun producten.
Naast wat we al hebben genoemd, gebruikt het Britse bedrijf Reynolds 3D-metaalprinten om gepersonaliseerde frameonderdelen van roestvrij staal en titanium te produceren. Het bedrijf zegt dat het met 3D-printen onderdelen kan maken met schonere randen en nauwere toleranties, waardoor een tijdrovend montageproces wordt gestroomlijnd.
We zijn echter nog ver verwijderd van 3D-printen voor massaproductie in de fietsindustrie. Momenteel wordt 3D-printen grotendeels gebruikt in eenmalige projecten zoals op maat gemaakte, high-end fietsen, waar de voordelen voor maatwerk echt kunnen schijnen.
Dat gezegd hebbende, maakt 3D-printen de productie van veel ingewikkelder vormen mogelijk dan met gieten of smeden mogelijk is. Uiteindelijk vertaalt het gebruik van 3D-printen in de productie van fietsen zich in esthetisch aangename, lichtgewicht en beter presterende fietsen.
In ons volgende artikel zullen we kijken naar 3D-printen in de tandheelkundige industrie, en specifiek voor clear aligners. Blijf op de hoogte!
3d printen
- Virtuele inventaris en 3D-printen:de noodzaak van beveiliging
- Applicatie Spotlight:3D-printen voor medische implantaten
- Applicatie Spotlight:3D-printen voor digitale tandheelkunde &Clear Aligner-productie
- Applicatie Spotlight:3D-printen voor lagers
- Applicatie Spotlight:3D-printen voor warmtewisselaars
- Applicatie Spotlight:3D-printen in de spoorwegindustrie
- Applicatie Spotlight:5 elektronische componenten die kunnen profiteren van 3D-printen
- Applicatie Spotlight:3D-printen voor schoenen
- 3D-printen is overal
- De zaak voor 3D-printen in de productie
- VDMA ontwikkelt roadmap voor 3D-printen met manufacturing roadmap