Expertinterview:Armin Wiedenegger, voestalpine High Performance Metals GmbH
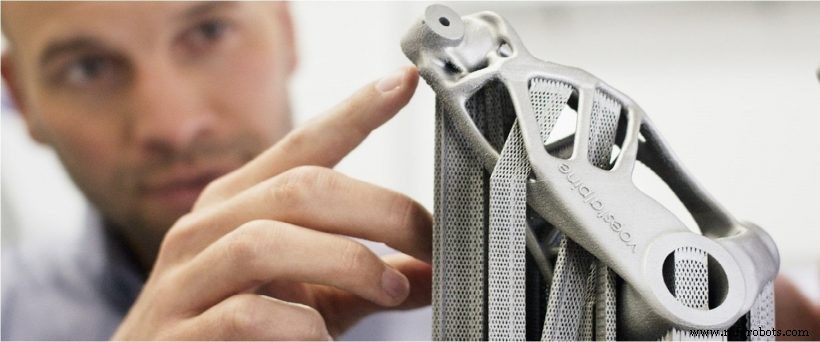
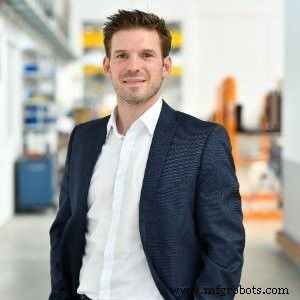
Metaal 3D-printen blijft doorgedrongen in de productie. Tegenwoordig wordt de technologie steeds meer een effectieve productieoplossing voor hoogwaardige, kleine volumes in een groot aantal industrieën. De voortdurende evolutie van 3D-printen met metaal hangt echter sterk af van de ontwikkeling van nieuwe materialen.
Een bedrijf dat de materiaalontwikkeling voor 3D-printen van metaal bevordert, is voestalpine, een van de grootste op staal gebaseerde technologiebedrijven in Europa.
Na een aantal jaren expertise in AM-materialen te hebben opgebouwd in de High Performance Metals-divisie, opende voestalpine in 2016 zijn Additive Manufacturing Centre in Düsseldorf. Sindsdien heeft het bedrijf zijn inspanningen opgevoerd met de opening van vestigingen in Taiwan, Noord-Amerika en Singapore.
In het Expert Interview van deze week is AMFG in gesprek met Armin Wiedenegger, Strategy &Business Development for Additive Manufacturing bij voestalpine High Performance Metals GmbH, om meer te weten te komen over zijn AM-metaalpoeders, geavanceerde toepassingen en succesverhalen.
Kun je me iets vertellen over voestalpine?
Voestalpine is een wereldwijde technologie- en kapitaalgoederengroep die een unieke combinatie van materiaal- en verwerkingsexpertise biedt.
Het is een toonaangevende partner voor de automobiel- en consumptiegoederenindustrie in Europa, evenals de lucht- en ruimtevaart en de olie- en gasindustrie wereldwijd, en biedt producten en systeemoplossingen waarbij staal en andere metalen worden gebruikt.
Onze Additive Manufacturing-activiteiten maken deel uit van de High Performance Metals Division van de voestalpine Group, die de wereldmarktleider is voor gereedschapsstaal en een toonaangevende leverancier van snelstaal, ventielstaal en andere producten gemaakt van speciaal staal, evenals poedermaterialen, legeringen op nikkelbasis, titanium en componenten geproduceerd met behulp van additive manufacturing-technologieën.
Wat zijn de uitdagingen bij het ontwikkelen van materialen voor 3D-printen van metaal en hoe lang duurt het proces gemiddeld?
Het ontwikkelen van poedermaterialen voor additieve fabricage van metalen is een zeer tijdrovend proces.
Het ontwikkelen van een totaal nieuwe legering kan bijvoorbeeld gemakkelijk 1 tot 3 jaar duren. Hoewel het optimaliseren van bestaande legeringen voor verbeterde 3D-printbaarheid sneller zou kunnen, vereist dit nog steeds tot een jaar van onderzoek, testen en validatie.
Uiteraard zijn hoogwaardige metaalpoeders erg belangrijk voor succesvol 3D-metaalprinten. Om consistente metalen onderdelen te maken, heb je poeders nodig met dicht opeengepakte, bolvormige metaaldeeltjes van vergelijkbare grootte.
Om dit te bereiken, worden metaalpoeders zorgvuldig vervaardigd met behulp van een gasvernevelingsproces.
Bij voestalpine duurt het een paar weken om met dit verstuivingsproces metaalpoeder te maken van een bestaande legering.
De divisie High Performance Metals heeft verschillende 3D-printen centra over de hele wereld. Welke metaal 3D-printtechnologieën gebruikt u momenteel?
Er zijn twee technologieën voor additieve productie van metaal in onze centra voor additieve productie:Powder Bed Fusion en Direct Metal Deposition (DMD).
Met Powder Bed Fusion kunnen we delicatere ontwerpen produceren. Het proces is echter meestal langzamer en duurder in vergelijking met DMD.
Met betrekking tot de DMD-technologie gebruiken we metalen materialen in zowel poeder- als draadvorm. Hoewel de technologie goedkoper is dan Powder Bed Fusion, is deze minder flexibel in termen van ontwerpmogelijkheden.
Bent u gericht op specifieke branches of branches?
Onze belangrijkste doelen zijn de gereedschapsindustrie en de olie- en gasmarkten, die naar onze mening enorm kunnen profiteren van 3D-metaalprinten.
Kunt u enkele succesverhalen van voestalpine delen?
Ja, zeker.
Een van de succesvolle toepassingen van metaaladditieve fabricage bij voestalpine zijn de lichtgewicht motorkapscharnieren die we hebben ontwikkeld voor gebruik in voertuigen.
Dit onderdeel, bekend als de LightHinge+ is ontwikkeld in samenwerking met auto-engineeringbedrijf Edag en simulatiesoftwarebedrijf Simufact.
Bij traditionele fabricage is de productie van motorkapscharnieren erg duur, niet in de laatste plaats vanwege de hoge montage- en gereedschapskosten.
Bovendien weegt zo'n conventioneel vervaardigd onderdeel ongeveer 1,5 kg. Aangezien een voertuig er ongeveer 40 nodig heeft, draagt dit aanzienlijk bij aan het gewicht van het voertuig.
Dus hebben we de kracht van topologie-optimalisatie en simulatietools gebruikt om het gewicht van het onderdeel te optimaliseren. De vereiste geometrie was alleen mogelijk om te produceren met behulp van Powder Bed Fusion.
Bij het ontwerpen van onderdelen voor het PBF-proces hebben ze doorgaans veel ondersteunende structuren nodig om een succesvolle afdruk mogelijk te maken. Draagconstructies genereren echter veel materiaalafval en leiden tot moeizame nabewerking.
Dus draagconstructies was een ander gebied dat we wilden optimaliseren. De resultaten waren geweldig:
Door de simulatiesoftware van Simufact te gebruiken, konden we het volume aan ondersteuningsstructuren verminderen van meer dan de helft van het totale gewicht van het onderdeel tot minder dan 18%. Bovendien hebben optimalisatietechnieken ons in staat gesteld om de tijd en moeite die nodig is om de steunen te verwijderen tijdens de nabewerkingsfase tot een minimum te beperken.
Uiteindelijk waren we in staat om een gewichtsbesparing van 50 % te realiseren in vergelijking met een onderdeel gemaakt met plaatwerk fabricage.
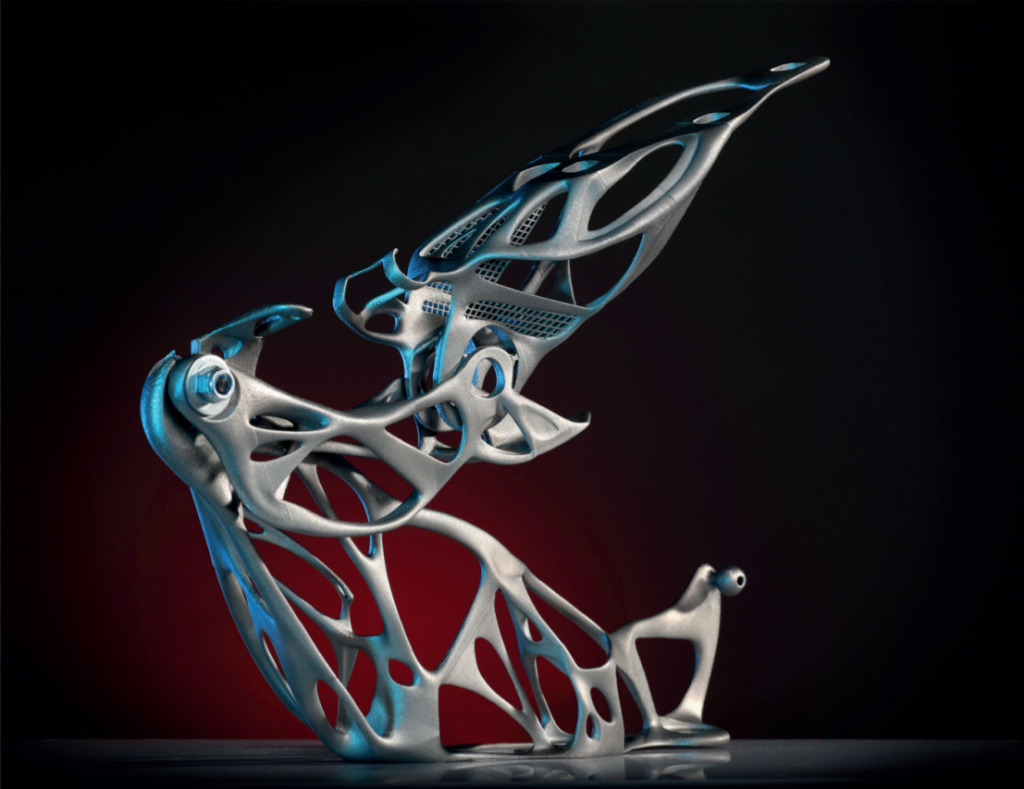
Hoe ziet u de huidige staat van de additive manufacturing-industrie en hoe ziet u deze evolueren?
In toenemende mate zien we dat additive manufacturing verschuift van enkelstuksproductie naar serieproductie. Dit wijst op de groeiende erkenning van de technologie als productieoplossing.
Welke uitdagingen moeten nog worden overwonnen om de adoptie van 3D-metaalprinten te versnellen?
AM staat voor verschillende uitdagingen op zijn weg naar een productieve technologie.
Ten eerste moeten de productiesnelheden worden verbeterd.
Ten tweede moeten de kosten van apparatuur omlaag om de technologie voor bredere markten te ontsluiten.
Ten slotte moet de AM-waardeketen meer worden geconsolideerd om een bredere acceptatie van 3D-metaalprinten te bereiken. Dit omvat de integratie van verschillende softwareoplossingen, van ontwerp tot productie tot beheer, evenals optimalisatie van de nabewerkingsfase.
Ga voor meer informatie over de High Performance Metals Division van voestalpine naar:https://www.voestalpine.com/highperformancemetals/en/
3d printen
- Metaal met hoog smeltpunt | Top 10 metalen met hoge smeltpunten
- Interview met een expert:professor Neil Hopkinson, directeur 3D Printing bij Xaar
- Interview met een expert:Philip Cotton, oprichter van 3Dfilemarket.com
- Interview met een expert:Dr. Alvaro Goyanes van FabRx
- Interview met een expert:Dr. Bastian Rapp van NeptunLab
- Expertinterview:Felix Ewald, CEO van DyeMansion
- Waar komen metalen vandaan?
- Meer over poedervormige metalen
- Draaien met hoge prestaties
- De economie van metaalbewerking
- Hoge snelheid strekmetaalmachine