De ruimtevaart naar nieuwe hoogten brengen met 3D-printen (2020)
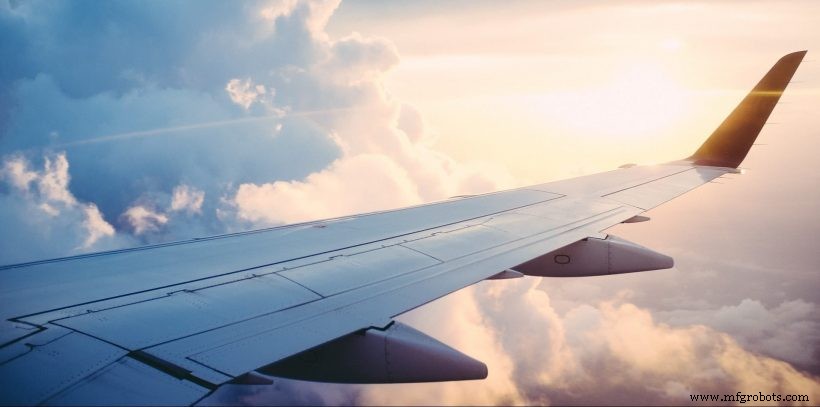
Lucht- en ruimtevaart heeft lange tijd een voortrekkersrol gespeeld op het gebied van innovatie op het gebied van 3D-printen, met het eerste gebruik van de technologie in 1989. Nu, drie decennia later, vormt de ruimtevaart een 16,8 procent aandeel van de markt voor additieve fabricage (AM) van $10,4 miljard en draagt in hoge mate bij aan de lopende onderzoeksinspanningen binnen de industrie.
Met de mogelijkheid om complexe ontwerpen, lichtgewicht onderdelen te maken en de productiekosten te verlagen, biedt 3D-printen veel voordelen voor de lucht- en ruimtevaartindustrie. Belangrijke spelers, zoals GE, Airbus, MOOG, Safran en GKN, maken echter niet alleen gebruik van de voordelen van de technologie, maar bevorderen deze ook door voortdurend onderzoek en ontwikkeling.
Terwijl we doorgaan met het onderzoeken van het gebruik van 3D-printen in verschillende industrieën, zullen we ons concentreren op hoe de lucht- en ruimtevaart de voordelen van 3D-printen benut om innovatie in het ontwerp en de productie van vliegtuigonderdelen te stimuleren .
De voordelen van 3D-printen voor de ruimtevaart
Lage productie
Voor industrieën, zoals de lucht- en ruimtevaart, waar zeer complexe onderdelen doorgaans in lage volumes worden geproduceerd, kan 3D-printen een ideale oplossing bieden. Met behulp van deze technologie kunnen complexe geometrieën worden gecreëerd zonder te hoeven investeren in dure gereedschapsapparatuur. Dit biedt ruimtevaart-OEM's (Original Equipment Manufacturers) en leveranciers een kosteneffectieve manier om kleine batches onderdelen te produceren.
Gewichtsvermindering
Naast aerodynamica en motorprestaties is gewicht een van de belangrijkste factoren waarmee rekening moet worden gehouden als het gaat om vliegtuigontwerp. Het verminderen van het gewicht van een vliegtuig kan de uitstoot van kooldioxide, het brandstofverbruik en het laadvermogen (voor ruimtevaartuigen) aanzienlijk verminderen.
Hier komt 3D-printen om de hoek kijken:de technologie is een ideale oplossing voor het maken van lichtgewicht onderdelen, wat resulteert in een aanzienlijke brandstofbesparing. In combinatie met tools voor ontwerpoptimalisatie, zoals software voor generatief ontwerp en topologie-optimalisatie, is het potentieel om de complexiteit van een onderdeel te vergroten bijna onbeperkt.
Materiaalefficiëntie
Voor lucht- en ruimtevaarttoepassingen helpt 3D-printen vaak om de buy-to-fly-ratio voor metalen onderdelen te verlagen. De term verwijst naar de correlatie tussen het gewicht van de oorspronkelijk gekochte hoeveelheid materiaal en het gewicht van het voltooide onderdeel.
Bij conventionele fabricage kunnen titanium vliegtuigonderdelen bijvoorbeeld een buy-to-fly-verhouding hebben tussen 12:1 en 25:1. Dit betekent dat er 12 tot 25 kg grondstof nodig is om 1 kg onderdelen te produceren. In dit scenario wordt tot 90 procent van het materiaal weggefreesd.
Metaal 3D-printen kan deze verhouding voor titaniumcomponenten terugbrengen tot tussen 3:1 en 12:1. Dit komt omdat metalen 3D-printers doorgaans alleen de benodigde hoeveelheid materiaal gebruiken die nodig is om een onderdeel te maken, waardoor er slechts weinig afval wordt gegenereerd door ondersteunende structuren. Voor dure metalen, zoals titanium en nikkellegeringen, kunnen de kostenbesparingen door deze verminderde koop-tot-vliegverhouding behoorlijk aanzienlijk zijn.
Gedeeltelijke consolidatie
Een van de belangrijkste voordelen van 3D-printen is de consolidatie van onderdelen:de mogelijkheid om meerdere onderdelen in een enkel onderdeel te integreren. Het verminderen van het aantal benodigde onderdelen kan het montage- en onderhoudsproces aanzienlijk vereenvoudigen door de hoeveelheid tijd die nodig is voor de montage te verminderen.
GE bijvoorbeeld produceert nu brandstofsproeiers voor straalmotoren met behulp van AM. Dankzij Design for AM heeft het bedrijf het aantal benodigde componenten teruggebracht van 20 naar slechts 1.
Onderhoud en reparatie
De gemiddelde levensduur van een vliegtuig kan variëren van 20 tot 30 jaar, waardoor onderhoud, reparatie en revisie (MRO) een belangrijke functie in de industrie is. Metaal 3D-printtechnologieën, zoals Direct Energy Deposition, worden vaak gebruikt om ruimtevaart- en militaire uitrusting te repareren. Turbinebladen en andere hoogwaardige apparatuur kunnen ook worden hersteld en gerepareerd door materiaal toe te voegen aan versleten oppervlakken.
Baanbrekende 3D-printtechnologieën in de ruimtevaart
Lucht- en ruimtevaartbedrijven gebruiken al een breed scala aan AM-technologieën. Fused Deposition Modeling (FDM) wordt bijvoorbeeld vaak gebruikt om prototypes en tools te maken. De Franse lucht- en ruimtevaartfabrikant Latécoère gebruikt FDM voor prototyping en de productie van gereedschap, waardoor de doorlooptijden tot 95 procent worden verkort. Daarnaast kan FDM ook worden gebruikt om einddelen voor vliegtuiginterieurs te produceren.
Als het gaat om metaal 3D-printen, kunnen poederbedfusie (PBF)-technologieën, zoals Selective Laser Melting (SLM) en Electron Beam Melting (EBM), kan dichte metalen onderdelen met sterke mechanische eigenschappen leveren. Met vooruitgang in grootschalige additieve fabricage, komen innovaties in methoden, zoals WAAM voor ruimtevaarttoepassingen.
Als pionier op het gebied van 3D-printtechnologie draagt de lucht- en ruimtevaartindustrie aanzienlijk bij aan de ontwikkeling van AM-technieken en -apparatuur . Zo werkt 3D-printerfabrikant Sciaky samen met Airbus en Aubert &Duval aan de ontwikkeling van nieuwe productiemethoden voor het produceren van vliegtuigonderdelen gemaakt van titaniumlegeringen.
In de tussentijd ontwikkelt GE een metaal binder jetting machine om massaproductie met AM mogelijk te maken.
3D-printmaterialen voor ruimtevaart
Terwijl prototypes voor lucht- en ruimtevaartcomponenten gemaakt kunnen worden van een reeks plastic materialen, moeten eindstukken voor lucht- en ruimtevaarttoepassingen aan strenge eisen voldoen. Voor het 3D-printen van functionele onderdelen zijn dan ook hoogwaardige flight-grade materialen nodig.
De selectie van vliegwaardige materialen varieert, van thermoplasten van technische kwaliteit (ULTEM 9085, ULTEM 1010, Nylon 12 FR) tot metaalpoeders (high-performance legeringen, titanium, aluminium, roestvrij staal).
Titanium is een van de meest populaire materialen voor het 3D-printen van lucht- en ruimtevaartcomponenten, omdat het de lichtheid van aluminium combineert met de sterkte van staal. Hoewel titaniumpoeders vrij duur zijn, kunnen de kosten gedeeltelijk worden gecompenseerd door ongebruikt materiaal te recyclen en afval te minimaliseren door betere ontwerpen die mogelijk zijn met AM.
Aerospace 3D-printtoepassingen
Gereedschap
OEM's en leveranciers in de lucht- en ruimtevaart hebben 3D-printen omarmd als een alternatieve methode voor het produceren van productiehulpmiddelen, waaronder mallen en armaturen.
De Moog Aircraft Group gebruikt bijvoorbeeld FDM 3D-printen om in eigen huis tools zoals coördinatenmeetmachines (CMM) te produceren.
In het verleden heeft het bedrijf dit armatuur uitbesteed, waarbij het proces tussen de 4 en 6 weken in beslag nam. Nu gebruikt Moog 3D-printen in eigen huis, waardoor CMM-armaturen in ongeveer 20 uur worden gemaakt. Armaturen die voorheen meer dan £ 2.000 hadden gekost, kunnen nu worden gemaakt voor een paar honderd pond.
Reserve- en vervangingsonderdelen
Vanwege de moeilijkheid om de vraag te voorspellen, moeten reserveonderdelen doorgaans op voorraad worden gehouden om op korte termijn beschikbaar te zijn. 3D-printen is een ideale oplossing voor het produceren van reserve- en vervangingsonderdelen, omdat ze op het moment van behoefte kunnen worden geproduceerd.
On-demand, laagvolume 3D-printen kan de doorlooptijd voor onderhoudswerkzaamheden aanzienlijk verbeteren, de verzendkosten verlagen en de noodzaak van een fysieke inventaris van onderdelen vrijwel elimineren.
3D-printen is bijvoorbeeld gebruikt om reserveonderdelen te produceren, zoals pakkinghandvatten en langsliggers, voor verouderde militaire vliegtuigen. In dezelfde geest heeft Lufthansa Technik, de MRO-divisie van Lufthansa, een AM-centrum opgericht om 3D-geprinte onderdelen te ontwikkelen, inclusief vervangende componenten.
Eindgebruiksonderdelen
Een toenemend aantal lucht- en ruimtevaartfabrikanten wenden zich tot AM om structurele onderdelen van vliegtuigen te produceren, van interieuronderdelen voor vliegtuigen tot complexe motoronderdelen.
Een voorbeeld van een interieurcomponent is afkomstig van Aerospace Tier 1 leverancier, Diehl Aviation. Het bedrijf heeft onlangs FDM-technologie gebruikt om een gordijnkop te produceren - een behuizing die boven de gordijnrail zit en klassen aan boord van elkaar scheidt.
De behuizing werd eerder geconstrueerd met behulp van verschillende lagen gelamineerd glasvezel en vereiste gespecialiseerde aluminium gereedschappen, wat tijdrovend en kostbaar was.
Diehl was in staat om dit onderdeel te assembleren uit 12 3D-geprinte thermoplastische componenten, waardoor de gereedschapskosten drastisch werden verlaagd en er uren aan arbeidskrachten werden bespaard. Dit stuk is naar verluidt het grootste volledig 3D-geprinte onderdeel van een passagiersvliegtuig dat ooit is geproduceerd en wordt in een lijn gemonteerd in A350's.
Het produceren van motorcomponenten is een ander gebruiksscenario voor 3D-printen, dankzij de mogelijkheid om maak lichtgewicht, complexe onderdelen. Ruimtevaartuigfabrikant Rocket Lab haalde bijvoorbeeld de krantenkoppen na de productie van zijn 100e Rutherford-raketmotor vorig jaar.
Het bedrijf gebruikt sinds 2013 3D-printen voor al zijn primaire motorcomponenten (inclusief verbrandingskamers, injectoren, pompen en belangrijkste drijfgaskleppen).
3D-printuitdagingen in de ruimtevaart
Een van de grootste uitdagingen voor OEM's in de ruimtevaart bij het implementeren van 3D-printtechnologie, is certificering. Vliegtuigonderdelen moeten voldoen aan strikte voorschriften, en regelgevers moeten ervoor zorgen dat 3D-geprinte onderdelen net zo veilig zijn als onderdelen die met traditionele methoden zijn vervaardigd.
Dat gezegd hebbende, worden normen en voorschriften voor 3D-printen in de lucht- en ruimtevaart geleidelijk ontwikkeld. In 2018 bracht SAE International haar eerste suite van Aerospace Material Specifications (AMS) uit voor metalen AM-materialen en -processen die worden gebruikt voor kritieke onderdelen van vliegtuigen en ruimtevaartuigen.
Naast AM-normen voor metaal heeft SAE International vorig jaar ook de eerste AM-polymeerspecificaties voor de lucht- en ruimtevaartindustrie vrijgegeven. De AMS7100-specificatie legt bijvoorbeeld de kritische controles en vereisten vast om betrouwbare, herhaalbare, reproduceerbare lucht- en ruimtevaartonderdelen te produceren door FDM of andere materiaalextrusieproductie.
ASTM International's AM-technologiecommissie (F42) ontwikkelt ook 4 extra normen die fabrikanten van vliegtuigonderdelen helpen om te voldoen aan veiligheids- en prestatie-eisen. De normen hebben betrekking op grondstoffen, eigenschappen van afgewerkte onderdelen, systeemprestaties en betrouwbaarheid, en kwalificatieprincipes.
Een andere uitdaging voor OEM's in de ruimtevaart is het waarborgen van de herhaalbaarheid van het proces. Naast ontwerpen en regelgeving moeten kwalificatieprocessen worden vastgesteld om ervoor te zorgen dat certificeerbare onderdelen on-demand kunnen worden gemaakt met behulp van 3D-printen. Dit kan het gebruik van software voor workflowautomatisering omvatten, zoals AMFG, om ervoor te zorgen dat alle processtappen worden vastgelegd en dat volledige traceerbaarheid wordt bereikt in elke productiefase.
De toekomst van 3D-printen in de ruimtevaart
Ondanks de uitdagingen blijft de lucht- en ruimtevaartindustrie pionieren in de ontwikkeling van AM als een levensvatbare technologie voor de productie van eindonderdelen.
Samenwerking zal een sleutelrol spelen in deze ontwikkeling, waarbij OEM's, overheidsinstanties en onderzoeksinstellingen samenwerken, bijvoorbeeld om het certificeringsproces te versnellen.
Binnen de lucht- en ruimtevaartmarkt , wordt verwacht dat de productie van eindonderdelen voor 3D-printen in 2024 $ 3 miljard zal bedragen. Naarmate 3D-printen gestaag blijft groeien, zouden we de komende jaren nog meer 3D-geprinte metalen en polymeeronderdelen in vliegtuigen en ruimteschepen kunnen zien.
3d printen
- Een inleiding tot 3D-printen met plastic
- ACEO® onthult nieuwe technologie voor 3D-printen met siliconen
- 3D-printen met siliconen — is het zover?
- Aan de slag met keramisch 3D-printen
- Een korte handleiding voor 3D-printen met Binder Jetting
- 3D-printen met harsen:een introductie
- 6 manieren om productiekosten te verlagen met 3D-printen
- De zekering 1 afdrukken met de zekering 1
- KUHMUTE herontwerpt mobiliteit met SLS 3D Printing
- 3D-printen met hoge snelheid met AION500MK3
- Solukon werkt samen met Siemens om nieuw 3D-printsysteem te onthullen