Reboot op achterwand:One-stop, sleep naar tape naar CFRP-onderdeel
Bij het begin van de huidige opmars van koolstofvezelcomposieten in autotoepassingen, leek fabrikant BMW Group (München, Duitsland) zich te onderscheiden. Eerste werk om harstransfergieten (RTM) te versnellen voor de productie van zijn M het dak van het sportmodel leidde tot de oprichting van een complete toeleveringsketen voor onderdelen van koolstofvezelversterkte kunststof (CFRP) op de i3 en i8 voertuigen en vervolgens naar geheel nieuwe fabricage- en montagewerkcellen voor de uit meerdere materialen bestaande Carbon Core body-in-white (BIW) op zijn 7-serie .
BMW zet zich in voor de i3 in 2009 tot grote fanfare, maar datzelfde jaar richtte Audi AG (Ingolstadt, Duitsland) een technisch centrum op dat zich toelegt op vezelversterkte kunststoffen. In 2011 kondigde Audi een samenwerking aan met Voith Composites (Garching, Duitsland) om CFRP-onderdelen in hoog volume te ontwikkelen en te produceren. Het jaar daarop publiceerde het de ontwikkeling van een CFRP-versterkte stalen B-stijl, gemaakt met behulp van harstransfergieten (RTM), en haar samenwerking met SOGEFI (Guyancourt, Frankrijk) om samengestelde veren op de markt te brengen. In 2012 was Audi ook een van de oprichters van het toonaangevende MAI Carbon-cluster, waaronder BMW, Voith Composites, SGL Group (Wiesbaden, Duitsland) en anderen.
Het meest opvallende is dat Audi's eigen verhaal over de ontwikkeling van CFRP begint met de eerste generatie R8 sportwagen, uitgebracht in 2006. Het bevatte compartimentafdekkingen voor de cabriokap en zijbladen gemaakt door harsoverdrachtgieten (RTM). Het bedrijf ontwikkelde zich van esthetische buitenkanten en kleinere constructies tot het Modular Sportscar System (MSS) in de Audi R8 e-tron . Hoewel de hoofdstructuur van die elektrische supercar bestond uit geëxtrudeerde aluminium balken die waren verbonden door aluminium gietstukken, waren alle panelen en vullingen van CFRP, inclusief een kofferbakinzet met gegolfde crashstructuren waardoor de achtermodule vijf keer zoveel energie kon absorberen als het metalen frame .
De ruggengraat van de MSS is de achterwand , die van een eerste concept in 2011 evolueerde naar de module die momenteel wordt geproduceerd voor de niet-elektrische R8 door SGL Technologies (voorheen BENTELER-SGL, Ort im Innkreis, Oostenrijk; zie "Plant Tour:BENTELER SGL"). Maar Audi was al bezig met het plannen van zijn volgende stap:het herhalen van de achterwand voor gebruik in zijn grotere volume A8 luxe sedan, met Voith Composites als productiepartner.
Voith Composites is een tien jaar oude dochteronderneming van de multinational Voith GmbH &Co. KGaA, opgericht in 1867. Het moederbedrijf heeft nu 19.000 werknemers in dienst, heeft een jaarlijkse omzet van € 4,2 miljard (US$ 5,2 miljard) en levert productieapparatuur en technologieën via vier divisies:Voith Digital Solutions, Voith Hydro, Voith Paper en Voith Turbo. Voith Composites evolueerde van de productie van CFRP-rollen die worden gebruikt bij het maken van papier tot de productie van CFRP-aandrijfassen/cardanassen voor de automobielindustrie en de industrie en platte laminaten.
In 2011 begon Voith Composites te werken aan een sterk geautomatiseerde CFRP-procesketen, gericht op de productie van de A8 achterwand. De kern was de Voith Roving Applicator (VRA), die in een enkele lijn 35K koolstofvezelkabel uit Zoltek (St. Louis, MO, VS) verspreidt in gebonden unidirectionele (UD) tape, die vervolgens wordt gesneden en gestapeld tot een op maat gemaakte blanco vormen. De VRA werd in 2017 erkend met een JEC Innovation Award. Het legde ook een robuuste basis voor latere voorvorm- en vormbewerkingen. Op JEC World 2018 werden opnieuw de hoogste onderscheidingen in de autocategorie behaald voor Voith Composites en Audi voor de voltooide VRA-gebaseerde digitale 4.0-productielijn die werd gebruikt om de Audi A8 te vervaardigen achterwandmodule. In samenwerking met harsleverancier Dow Automotive (Auburn Hills, MI, VS) en Zoltek ontwikkelden deze partners niet alleen de materialen, het proces en de geïntegreerde inline inspectiesystemen die nodig zijn om hoogwaardige CFRP-onderdelen tegen hoge volumes te produceren, maar creëerden ze ook de volledige suite van essentiële computer-aided design/manufacturing (CAD/CAM) en simulatietools die al worden toegepast om toekomstige onderdelen te ontwikkelen.
Evolutie van het ontwerp op basis van efficiëntie
"We begonnen al vroeg met Audi samen te werken", zegt Dr. Jaromir Ufer, hoofd bedrijfsontwikkeling bij Voith Composites. De eerste prioriteit was het ontwikkelen van de nieuwe A8 achterwandontwerp, dat aangeeft hoe het onderdeel moet worden vervaardigd.
"Toen we begonnen met de engineering voor deze productie, konden we geen kant-en-klare [software]producten vinden die alles hadden wat we nodig hadden", legt Ufer uit. "Dus brachten we ontwerptools zoals ABAQUS samen, maar bouwden we onze eigen materiaalkaarten en ontwikkelden we onze eigen simulatiemethoden." Audi had al een lager BIW-gewicht en verhoogde torsiestijfheid geïdentificeerd als belangrijkste doelstellingen voor de R8 ontwerp van de achterwand (zie “Audi R8-zitwand:een opmaat naar productie”). Voor de A8 module, werd een integraal ontwerp naar voren gebracht om de uit meerdere componenten bestaande MSS te verminderen montage tot een enkel, gevormd CFRP-paneel met een klein aantal verlijmde en geklonken bevestigingen. Dit ontwerp zorgde voor de ontwikkeling van een zeer anisotroop laminaat met gelokaliseerde belastingspaden, waardoor het voltooide onderdeel 33% van de torsiestijfheid van de aandrijfcel kan leveren bij 50% van het gewicht, vergeleken met een assemblage van drie tot vijf gelaste aluminium onderdelen.
“De composiet preform voor de Audi A8 achterwandpaneel varieert van een basis van 6 lagen tot 19 lagen waar lokale versteviging is toegevoegd, bijvoorbeeld bij uitsnijdingen of puntbelastingen, zoals de bevestigingen van kinderzitjes”, legt Ufer uit (Fig 2).
Voith Roving Applicator
Ufer merkt op dat de ontwikkeling van dit ontwerp en de VRA parallel verliepen. “Alleen door de ontwerpvrijheid te hebben die de VRA biedt, waren de prestaties van de nieuwe A8 achterwand mogelijk.” Ook belangrijk was het feit dat vezelleverancier Zoltek een prijsverbintenis voor 7 jaar aan het programma was aangegaan.
Het proces van de VRA begint met een mand met Zoltek's PX 35 koolstofvezel. Meerdere klossen van 50K-kabel worden in elke VRA-lijn gevoerd en gespreid om banden van 50 mm breed te produceren. Vervolgens wordt een bindmiddel op epoxybasis aangebracht dat later zal reageren met de Dow VORAFORCE snap-cure epoxymatrixhars tijdens het harsoverdrachtgieten (RTM) van het composietdeel. Een kleine hoeveelheid infrarood (IR) warmte wordt toegepast om het bindmiddel voldoende te smelten om de tape bij elkaar te houden door middel van daaropvolgende consolidatie-, snij- en stapelstappen (stap 1).
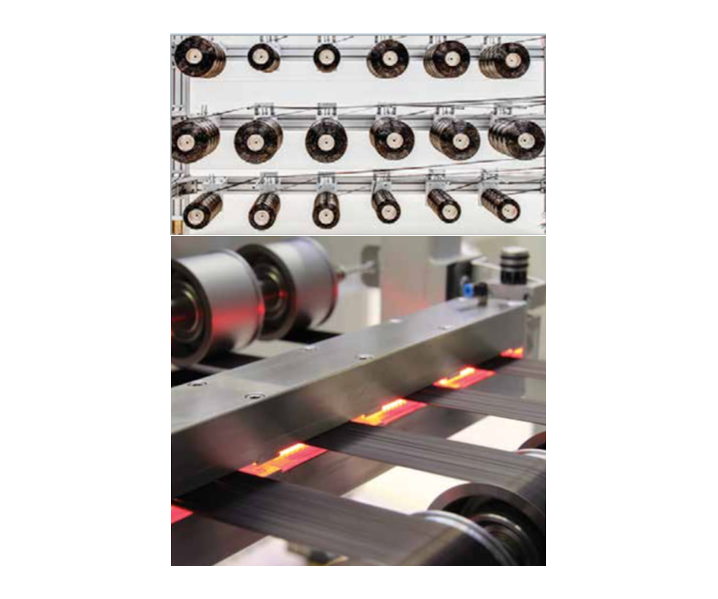
Stap 1: Zoltek 50K koolstofvezelkabel wordt in de Voith Roving Applicator (VRA) gevoerd, waar het eerst wordt uitgespreid, vervolgens bedekt met een bindmiddel op epoxybasis en daarna IR-verwarmd om het bindmiddel gedeeltelijk te smelten.
“Dit is een continu proces dat volledig geautomatiseerd is”, zegt Ufer. “Als het om wat voor reden dan ook nodig is om de lijn te stoppen, reageert de apparatuur automatisch. Zo wordt de IR heater direct uitgeschakeld en ingeschoven om beschadiging van de tape door oververhitting te voorkomen. Er zijn honderden van dergelijke details in de apparatuur en digitale besturing maakt deze technologie mogelijk.”
Stap 2: De gespreide sleepband wordt vervolgens geconsolideerd terwijl deze onder spanning door meerdere rollen gaat.
Na het aanbrengen van het bindmiddel wordt tapeconsolidatie bereikt terwijl het onder spanning door meerdere rollen gaat (stap 2). Ufer legt uit dat dit ook een buffer voor de lijn inbouwt. "We hebben een eenheid die de continue trekstroom van de vezel onderbreekt en een overgang biedt naar het pulsformaat van het tape-cut-and-place-mechanisme." Dit op portaal gebaseerde mechanisme snijdt de tapes op maat en plaatst ze onder gespecificeerde hoeken van 0-360° op een draaitafel (stap 3). Elke op maat gemaakte stapel, bestaande uit 6 tot 19 lagen tape, varieert in dikte van respectievelijk 1,5 tot 3,7 mm.
Stap 3: De VRA snijdt vervolgens de tape af en plaatst maximaal vier stukken tegelijk op een draaitafel, waarbij zowel de tapelengte als de oriëntatiehoek binnen de laminaatstapel worden aangepast (bijv. 45°/90°/30°).
Voith heeft vier VRA-lijnen geïnstalleerd (zie openingsfoto), en hoewel ze elk maximaal vier 50 mm brede tapes tegelijk kunnen aanbrengen, merkt Ufer op:"de lijnen hebben een modulaire aanpak, zodat ze 10 of meer tapes per keer kunnen aanbrengen. tijd. Het hangt af van de grootte van het onderdeel en de productiesnelheid.”
Automatisering omvat kwaliteitsinspectie. Scans van de tapes en preforms worden vergeleken met een afwijzingsalgoritme. “Het 100% scannen van de tape door de VRA zorgt voor de juiste vezeldistributie voor de hele productielijn”, legt Ufer uit. “Ook gebruiken we thermografie en lasersensoren om de preforms op aangewezen plekken te controleren.” De VRA kan dan reageren op eventuele problemen die het detecteert. "Als een band niet correct is", merkt hij op, "zal de VRA de gebrekkige lengte wegsnijden en een andere produceren om deze te vervangen." Voor traceerbaarheid wordt een QR-code op de voltooide preform geplaatst. (QR-codes hebben de voorkeur boven RFID-tags (radiofrequentie-identificatie), omdat ze naar verluidt beter bestand zijn tegen het harsinjectieproces.)
Vormen, gieten en assembleren
De 2D-stack verlaat de VRA en wordt naar de vorm-, vorm- en assemblagesectie van de productielijn gebracht. De eerste pers waarin het wordt geplaatst, geleverd door composietautomatiseringsspecialist FILL (Gurten, Oostenrijk), gebruikt warmte en druk om de 2D-tapestapel tot een 3D-voorvorm te vormen (stap 4). Ufer legt uit dat, omdat de voorvorm varieert in dikte en vorm, de pers de uitgeoefende druk kan aanpassen terwijl deze afzonderlijke gebieden van de voorvorm die in het vormgereedschap is geklemd, stempelt. ALPEX Technologies (Mils bei Hall, Oostenrijk) maakte de matched-steel RTM-mallen, gebaseerd op een ontwerp van Voith Composites. “We hebben het tooling- en persproces virtueel ontwikkeld”, zegt Ufer. "Hoewel er geen daadwerkelijke testlus nodig was, hebben we de simulatiemodellen op andere vormen en onderdelen gevalideerd en geverifieerd voordat we de A8 machinaal bewerkten. productiegereedschappen voor de achterwand. Deze simulatie van het vormproces liep rechtstreeks in de echte productie en hielp de optimalisatie te versnellen.”
Stap 4 :De tapestapel wordt in een pers geschoven, waar deze wordt gevormd tot de uiteindelijke 3D-onderdeelvorm.
De pers houdt een paar seconden vast om het poederbindmiddel te laten reageren en de vorm in te stellen, wat resulteert in een stabiele voorvorm die bestand is tegen vezelwas tijdens harsinjectie. "De bindmiddeldeeltjes werken ook om de vezels uit elkaar te houden voor een betere harsstroom tijdens RTM", merkt Ufer op. "Dit is handig omdat er geen stiksels in de voorvorm zijn om de harsstroom te bevorderen, dus deze bindmiddeldeeltjes fungeren als microstroomkanalen."
De gevormde voorvorm wordt vervolgens door een robot overgebracht naar een EiMa Maschinenbau GmbH (Frickenhausen, Duitsland) CNC-cel, waar een ultrasoon mes de buitenste definitieve contour afsnijdt. Het wordt vervolgens robotisch in een RTM-pers geplaatst (stap 5), geleverd door ENGEL (Schwertberg, Oostenrijk). Alle robots in de lijn worden geleverd door KUKA Robotics (Augsburg, Duitsland).
Stap 5: De gevormde voorvorm wordt in een pers van 350 kN geplaatst en gegoten met behulp van ultra-RTM.
Het RTM-proces dat wordt gebruikt om de A8 . te vormen achterwand is hetzelfde ontwikkeld in het Audi Lightweight Center voor de vorige R8 achterwand, ook wel ultra-RTM genoemd. Het maakt het vormen van grote onderdelen mogelijk met behulp van snelle injectie maar lage druk. Vergeleken met de 140 bar die typisch is voor HP-RTM, is de in-mold harsinjectiedruk tijdens ultra-RTM van de Audi A8 achterwand is <15 bar, zelfs minder dan die voor de R8 . Hierdoor is in plaats van 2500 kN perskracht slechts 350 kN nodig. Daarom kan een kleinere, goedkopere pers worden gebruikt om onderdelen van hoge kwaliteit met een hoog vezelvolume te produceren.
De VORAFORCE 5300 epoxyhars, een driecomponentensysteem met vormlossing, hardt uit in 90-120 seconden bij 120 °C en heeft een verwerkingsviscositeit van 20 cps. Voor de A8 achterwand wordt een harsspuit van 1,3 kg in de voorvorm gespoten, gevolgd door een uitharding van 120 seconden.
Het uitgeharde onderdeel wordt robotisch uit de vorm gehaald en in een gesloten CNC-freescel geladen voor het bewerken van uitsnijdingen. Vervolgens wordt het gefreesde onderdeel in een geautomatiseerde wasmachine geplaatst om achtergebleven CFRP-stof te verwijderen.
De gewassen achterwand wordt overgebracht naar een montagecel die is uitgerust met twee robots. De eerste robot plaatst het gegoten onderdeel in een geautomatiseerde klinkmachine, die de kracht documenteert die wordt uitgeoefend tijdens het installeren van de klinknagel. Dit maakt deel uit van de fabricage-intelligentie die in het algehele proces is ingebouwd en wordt toegevoegd aan het digitale verwerkingsrecord van elk onderdeel (d.w.z. digitale draad). Het onderdeel wordt vervolgens naar het verlijmingsgebied verplaatst en een tweede robot bereidt het verlijmingsgebied voor met behulp van een geautomatiseerd doekje met oplosmiddel. Dezelfde robot brengt vervolgens de snel uithardende, tweecomponenten Dow BETAFORCE 9050M polyurethaan structurele lijm aan (stap 6), die compatibel is met de driecomponenten epoxy. Het onderdeel wordt vervolgens in een oven geplaatst voor een korte lijmuithardingscyclus.
Stap 6: BETAFORCE polyurethaanlijm wordt robotisch aangebracht voor gehechte bevestigingen en vervolgens uitgehard in een korte ovencyclus.
Deze productielijn handhaaft een cyclustijd van 5 minuten voor het voltooide onderdeel en aan de huidige vraag naar onderdelen kan worden voldaan in een of twee ploegen van 8 uur. Een 3D-laserscanapparaat wordt periodiek gebruikt om de 3D-vorm en afmetingen van het onderdeel te controleren. Afgewerkte onderdelen worden vervolgens klaargemaakt voor verzending naar de Audi A8 eindassemblagelijn in Neckersalm, Duitsland, ongeveer 3 uur rijden over de weg (stap 7).
Stap 7: Het voltooide onderdeel wordt vervolgens klaargemaakt voor verzending naar de eindassemblagelijn van de Audi A8.
Directe plaatsing van glasvezel =toekomstige flexibiliteit
Met alle investeringen die zijn gedaan, is het verrassend om te horen dat Voith Composites niet verzekerd was van dit bedrijf, maar het bedrijf voltooide inderdaad de ontwikkeling en nam vervolgens deel aan een concurrerend biedingsproces om de productie binnen te halen. "We waren in staat om te voldoen aan de door Audi vastgestelde doelkosten voor onderdelen, evenals aan de kwaliteits- en onderdeelprestatie-eisen", zegt Ufer. Dit was geen geringe prestatie, aangezien nogal wat bedrijven streden om het programma.
Voith Composites heeft meerdere onderdelen van zijn proces gepatenteerd. "De VRA heeft de industrialisatie aangetoond met behulp van directe vezelplaatsing [DFP] van tapes, waardoor het schroot en het materiaalgebruik worden verminderd via een sterk geoptimaliseerde lay-out", zegt Ufer. Het maakt ook gebruik van de meest kosteneffectieve materialen - onbehandelde zware vezels en poederbindmiddel. Het proces van de tweede generatie vervangt poederbindmiddel door directe toepassing van hars, waardoor meer processtappen worden geëlimineerd. Het bedrijf heeft echter andere DFP-processen ontwikkeld, waaronder de Voith Longfiber Preformer en Voith Prepreg Winding.
"We stellen nieuwe normen voor koolstofvezelonderdelen voor grootschalige autoserieproductie", zegt Voith Composites-directeur Dr. Lars Herbeck. "De slimme fabriek die we hebben opgericht, brengt de geautomatiseerde productie van CFRP-componenten naar een nieuw niveau van efficiëntie en flexibiliteit, inclusief bijna elke vorm en individuele partijgroottes." Dit is inderdaad waar de industrie naartoe gaat.
Hars
- Waarom PEEK-materiaal aan de top van zijn klasse staat
- Koolstofvezelversterkte kunststof (CFRP)
- K 2019:Materialen zijn belangrijk op de Messe
- Arkema lanceert 'Start-Up Connect'-programma
- Polykemi investeert in eigen Amerikaanse compounderingsfabriek
- Polykemi heeft een samengestelde productie op drie continenten
- PPS-gebaseerde thermoplastische unidirectionele tape van koolstofvezel
- Uitdagingen van laserondersteunde tapewikkeling van thermoplastische composieten
- Composieten-intensief meesterwerk:2020 Corvette, Part 2
- Gesplitste koolstofvezel verbetert SMC-prestaties
- CFRP-module bespaart gewicht op raketontwerp