Liftgate-ontwerp stelt aangepaste filamentwikkeling op de proef
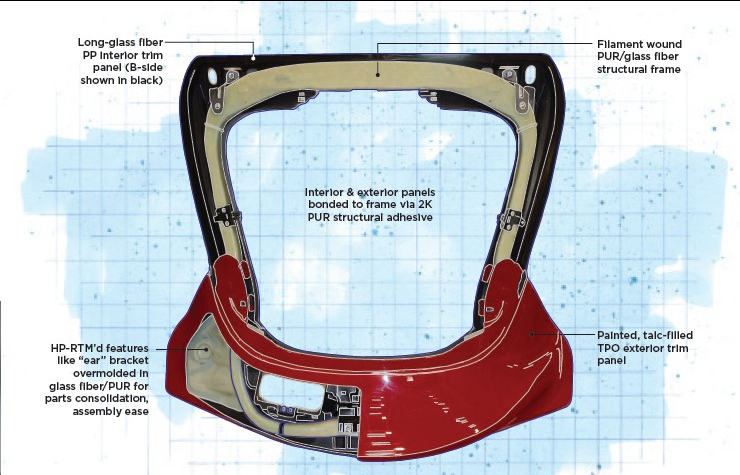
Autolaadkleppen, of achterklepdeuren, zijn decennialang langzaam overgegaan van metalen naar composieten. Hoewel het pas in 2013 was dat de eerste volledig kunststof/composiet achterklep, minus metalen steunstructuur, op de markt werd gebracht, hebben de meeste achterkleppen tegenwoordig nog steeds dit ondersteuningsonderdeel waarop de buitenhuid en binnenpanelen zijn bevestigd, met name op grotere, zwaardere sport- bedrijfsvoertuigen (SUV's) en crossover-utility-voertuigen (CUV's) met grotere achterdeuren.
Wat echter wel de volgende evolutie zou kunnen zijn in composiet achterkleppen, debuteerde in 2019 op de Toyota Supra sportwagen van Toyota Motor Corp. (Toyota City, Japan). Een met filament gewonden composietframe verving een metalen frame en zou hogere stijfheid en sterkte bieden bij een lager gewicht dan traditionele metalen constructies, met meer ontwerpflexibiliteit, vooral in krappe verpakkingsruimte. Naar verluidt is het filamentwikkelproces zodanig aangepast dat het, naarmate de belangstelling groeit en de toepassingen toenemen, kan voldoen aan de snelheids- en kostendoelstellingen van voertuigproductie met grotere volumes. Dit is hoe het ontwerp en de technologie zijn ontstaan.
Trilaterale fabricage
Magna International Inc. (Aurora, Ontario, Canada) is een Tier 1-integrator in Noord-Amerika, maar in Europa ontwerpt en assembleert haar dochteronderneming Magna Steyr AG &Co. KG (Graz, Oostenrijk) ook complete auto's voor OEM's die extra productie nodig hebben capaciteit.
Onlangs nam Magna deel aan een interessant programma waarbij autofabrikanten Toyota en BMW AG (München, Duitsland) betrokken waren, die sinds 2013 samenwerken aan ontwerp- en productieprojecten. Voor zijn laatste poging wilde Toyota zijn Supra naambord en was een samenwerking aangegaan met BMW om het voertuig en een zusterauto te ontwerpen en af te stemmen, BMW's 2-zits Z4 . De twee voertuigen delen motor, ophanging en stuursystemen. Magna Steyr zou beide auto's in Graz assembleren en de Supra . leveren met stoelen, carrosseriepanelen, deurvergrendelingen en laadkleppen. Hoewel er veel innovatie op beide auto's zit, is de achterklep in de Supra hier is de innovatie van composietontwerp het duidelijkst.
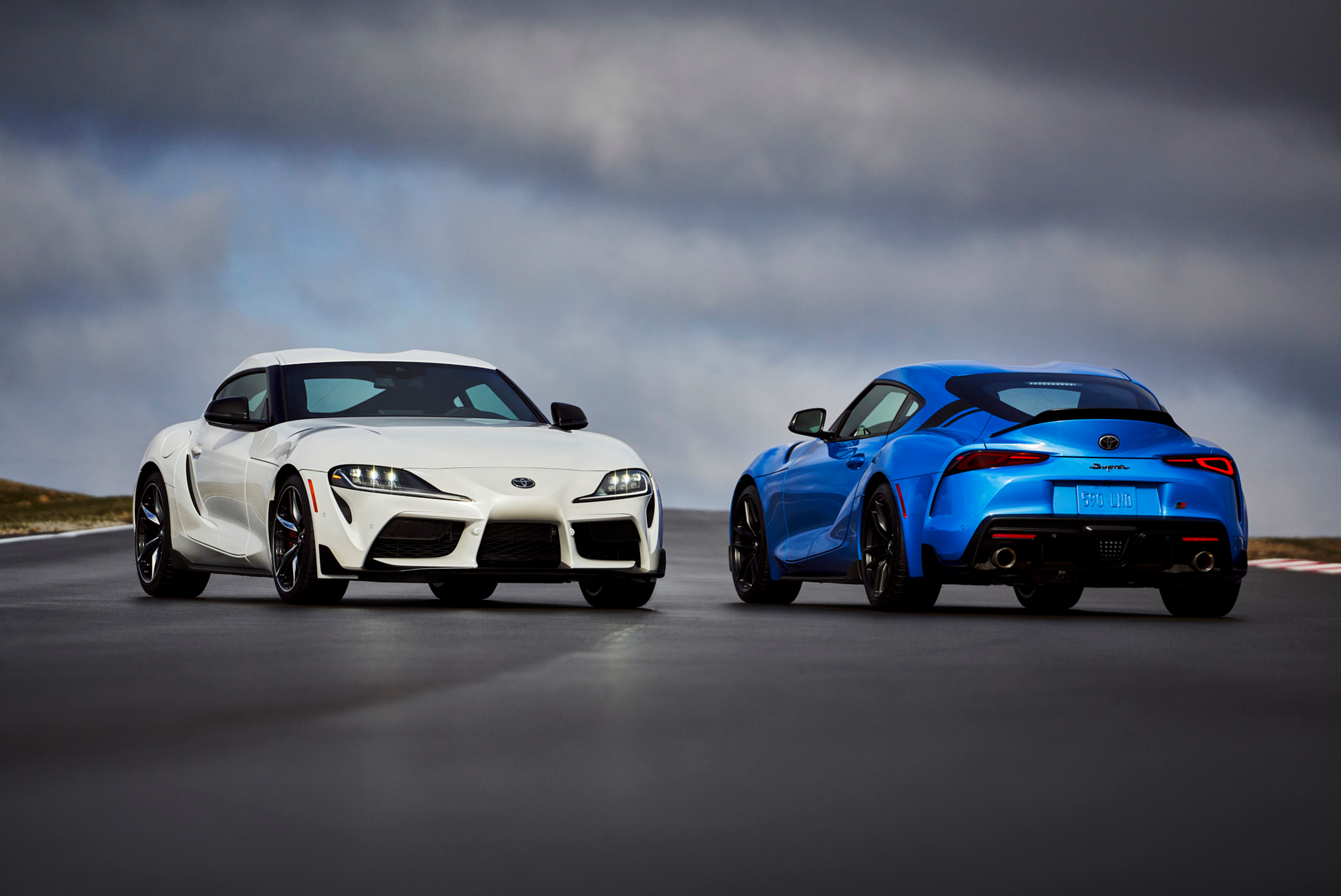
Manchester van Bohemen
Jaren voor Magna's betrokkenheid bij de 2020 modeljaar Supra, zijn bedrijf in Liberec, Tsjechië, had technologieën voor composietruimteframes voor een aantal potentiële toepassingen onderzocht. Het toeval wil dat het gebied een rijke traditie heeft als toonaangevend textielcentrum en ooit bekend stond als 'het Manchester van Bohemen'. Het Liberec-team zocht een technologische architectuur die hoge belastingen ondersteunde, de totale massa verminderde, strakke maattoleranties handhaafde en kon worden geproduceerd in een proces met hoge herhaalbaarheid en reproduceerbaarheid (R&R) om te voldoen aan de prestatie- en productie-eisen van Europese autofabrikanten.
"We kwamen tot de conclusie dat we een thermohardend product nodig hadden met een hoge thermische en dimensionale stabiliteit", herinnert Riad Chaaya zich, Magna Global Product Line Director - Composite Liftgates. "We wisten ook dat we een gesloten vorm nodig hadden met de mogelijkheid om doorsneden met variabele vormen en diktes te produceren - die nodig zijn om mechanische prestaties, verpakkingsruimte, massa en kosten te optimaliseren - die kunnen worden geproduceerd in een proces dat in staat is om jaarlijks 150.000 onderdelen te maken. We hebben naar veel technologieën gekeken, waaronder blaasvormen, vlechten en filamentwikkelen, maar geen enkele voldeed helemaal aan onze behoeften. Na vele proeven hebben we filamentwikkeling gekozen als de beste match voor wat we wilden, omdat het ons controle gaf over oriëntaties en aantallen filamenten om de hoogste modulus bij het laagste gewicht te extraheren."
Ondanks de vele voordelen was er bezorgdheid dat het opwinden van filamenten te traag zou zijn voor conventionele autoproductie. Bovendien had het team een methode nodig om het wikkelproces te beginnen en te beëindigen om een frame met een gesloten vorm te creëren. Gelukkig had het team geen geschiedenis met het opwinden van filamenten, maar de erfenis van Liberec op het gebied van textielproductie betekende dat de lokale gemeenschap vol was met experts op het gebied van rovings en het opwinden van filamenten.
"Gelukkig voor ons hadden deze experts de passie om hun traditionele knowhow nieuw leven in te blazen om ons te helpen deze op nieuwe manieren toe te passen om te voldoen aan grootschalige automobielbehoeften", voegt Dr.-Ing toe. Josef Půta, technologieleider Magna Exteriors - Tsjechië.
"Omdat traditionele filamentwikkeling te traag was voor onze behoeften, hebben wij en onze partners naar veel manieren gekeken om het sneller te laten werken", herinnert Lukáš Strouhal, hoofd industrialisatie, Magna Liberec zich. “We hebben manieren overwogen om elke stap in het proces te versnellen en dingen heel anders te doen. Hoewel we niet te veel kunnen zeggen over hoe we hebben dat gedaan, we kunnen zeggen dat we enorme snelheidsverbeteringen hebben bereikt, zodat ons aangepaste proces 'automotive waardig' kon worden. ”
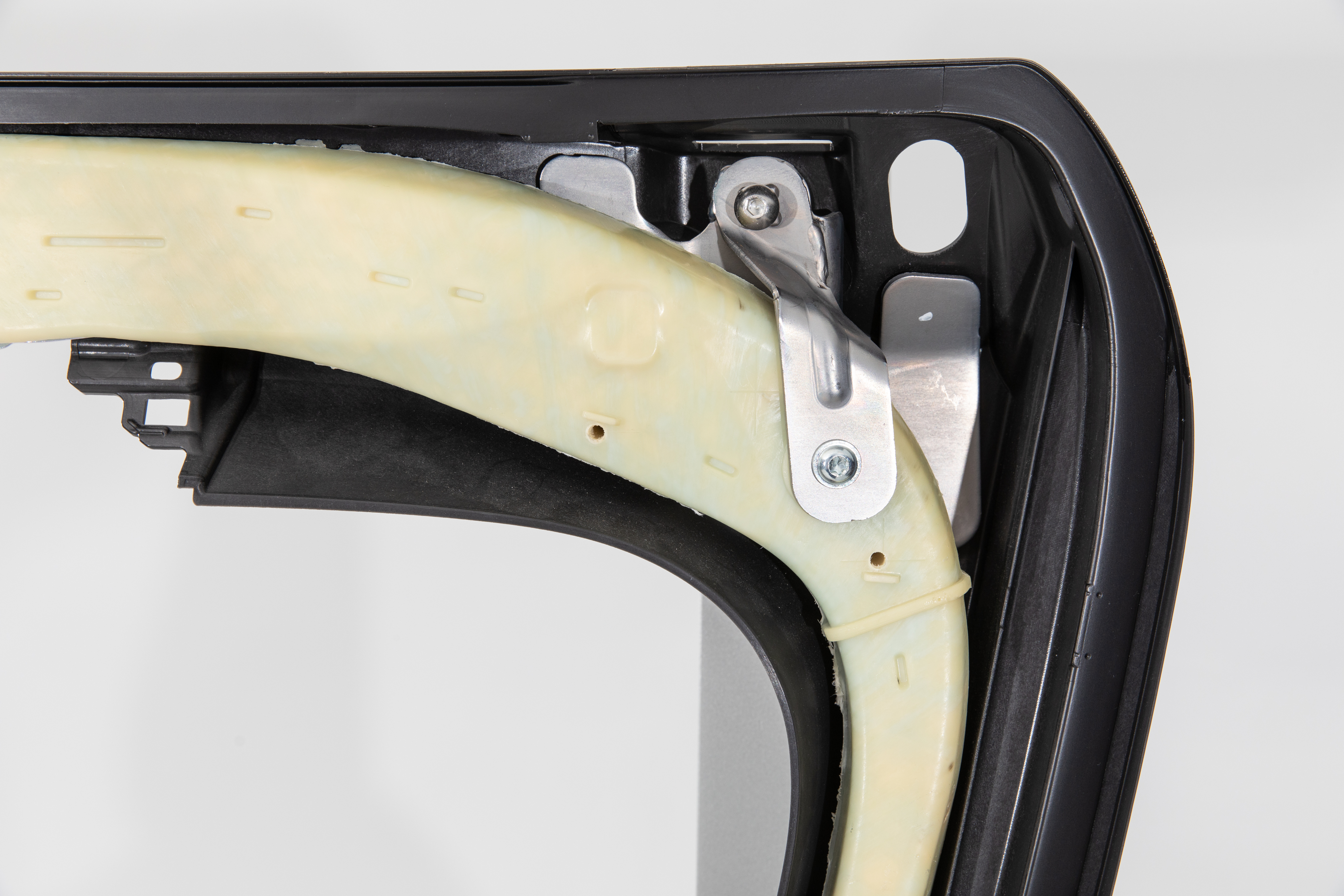
Magna en haar partners hebben veel harssystemen onderzocht, waaronder epoxy, polyurethaan (PUR) en een PUR/vinylester-mengsel, plus een verscheidenheid aan versterkingen, van glas tot koolstof tot basaltvezels. Het uiteindelijke systeem bevat PUR en glasvezels, die de beste balans bieden tussen vezelefficiëntie, prestaties, kosten en productiesnelheid.
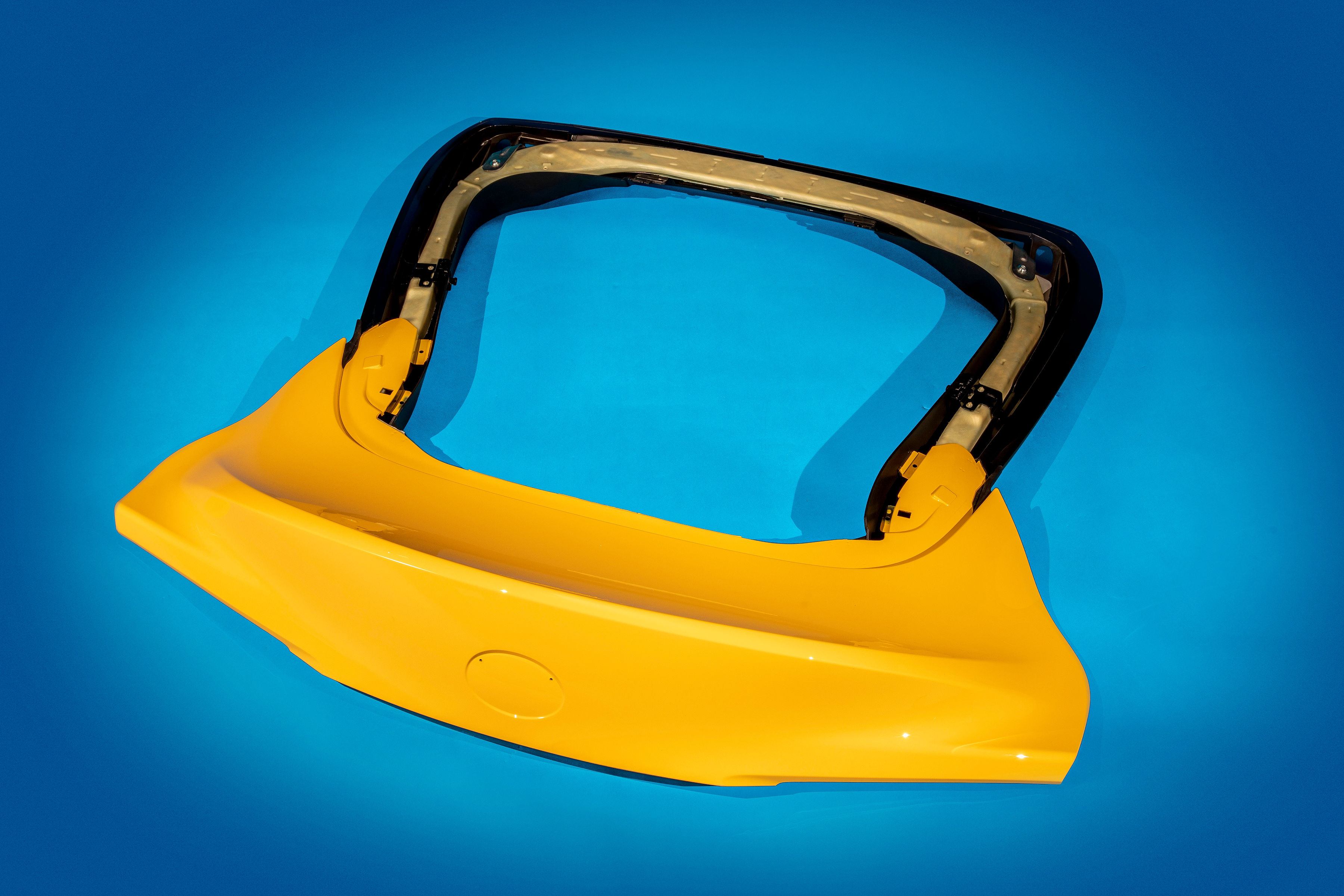
Magna's generieke filament wondruimteframe wordt geproduceerd in drie stappen, elk zorgvuldig geoptimaliseerd voor snelheid. Eerst wordt een stijve, cellulaire PUR-kern geproduceerd via reactie-injectiegieten (RIM); ten tweede is die kern, die als doorn fungeert, omwonden met glasvezel; en ten derde wordt die wondstructuur vervolgens doordrenkt met PUR en geconsolideerd in het hogedrukharsoverdrachtgietproces (HP-RTM). Er wordt voor gezorgd dat de kern niet instort tijdens infusie/consolidatie. Půta legt uit dat er veel werk is gestoken in het specificeren van de soorten rovings, maten en harsen die worden gebruikt - waarvoor nauw overleg met leveranciers nodig is voor materiaalaanpassingen - en het bepalen van het aantal windingen en de oriëntatie van de filamenten in elke laag. Het is niet verrassend dat het bedrijf talloze patenten heeft gekregen die alles omvatten, van ontwerp en kernproductie tot de filamentwikkelmachine, plus aanvullende handelsgeheimen die ze goed bewaren.
"We hebben meerdere innovaties doorgevoerd in elke processtap en elk product", legt Strouhal uit. "Je zou een van onze frames uit elkaar kunnen halen, de gebruikte vormen en geometrieën kunnen zien, en je zou je nog steeds afvragen waarom en hoe we dat hebben gedaan."
Hoewel het Magna Liberec-team zijn space-frame-technologie niet voor een bepaalde toepassing had ontwikkeld, stonden ze op het punt een interessante kans te krijgen om het te gebruiken.
Uitdagende achterklep
Magna heeft een lange geschiedenis in het produceren van laadkleppen voor passagiersvoertuigen. Het bedrijf bouwde naar verluidt de eerste all-olefin laadkleppen in Noord-Amerika en Europa voor de 2013 BMW i3 elektrische stadsauto, en ontwierp en bouwde een all-olefin achterklep van de volgende generatie voor FCA NA LLC's (Auburn Hills, Mich., V.S.) 2019 Jeep Cherokee SUV's. Aangezien de productie van de laadklep een levering was voor de Supra programma maakte Magna niet alleen gebruik van het werk dat in Liberec is gedaan, maar ook van de lange geschiedenis van het omzetten van metalen achterklepconstructies in composieten en kunststoffen.
“De Supra achterklep bood een aantal directe uitdagingen”, herinnert Chaaya zich. “Ten eerste was de verpakkingsruimte zeer beperkt, wat betekent dat de toleranties erg krap waren en de lineaire thermische uitzettingscoëfficiënten zorgvuldig moeten worden beheerd om ervoor te zorgen dat de laadkleppen vrij kunnen openen en sluiten. Ten tweede was de vorm van deze deur nog uitdagender. Toyota wilde niet alleen een lichtere achterklep, maar ze hadden ook zeer specifieke stijlvereisten voor de manier waarop de achterkant van het voertuig werd gedrapeerd. Ten derde, met de verwachte bouwvolumes van het voertuig, zou gereedschap om die vorm in metalen te bereiken erg duur zijn. We kwamen zelfs tot de conclusie dat het frame van de achterklep niet uit één stuk metaal kon worden vervaardigd en toch aan de ontwerp- en prestatie-eisen van Toyota kon voldoen. Dat betekende dat het ruimteframe gemaakt moest worden van composieten en meer specifiek van thermohardende composieten.”
De buitenhuid zou een geverfd, spuitgegoten, met talk versterkt TPO-paneel zijn om de agressieve vorm aan te kunnen, terwijl het binnenpaneel van langglas polypropyleen (PP) zou zijn; beide zouden met een structurele 2K PUR-lijm aan het frame worden bevestigd. Chaaya voegt eraan toe dat er veel werk is verzet om het ruimteframe te optimaliseren en de laadklep te voltooien om te voldoen aan de vereisten voor torsiebelasting. Een vroege uitdaging was het vinden van een manier om materiaaleigenschappen nauwkeurig te simuleren om een nauwkeurige correlatie te verkrijgen tussen voorspelde en gemeten resultaten.
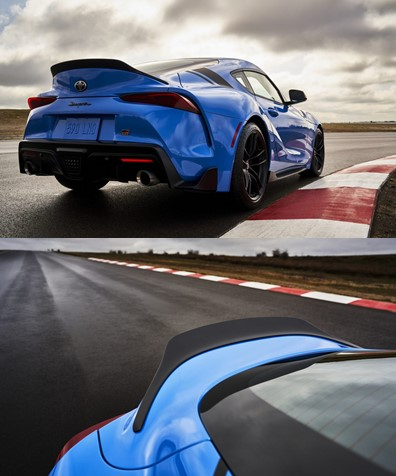
"Het was een harde strijd om een goede correlatie met onze materiaalmodellen te krijgen, omdat we elke wikkellaag moesten simuleren en vorm, radii en de wikkelvereisten zelf moesten opnemen", voegt hij eraan toe. “Hoewel we begonnen met 20% korting, waren onze uiteindelijke voorspellingen, na veel afstemming en het bepalen van de beste manier om onze stijfheid te verbeteren, heel dichtbij. Op zo'n groot frame zijn we er ook in geslaagd om maattoleranties tot 1 millimeter te houden.”
Veel voordelen
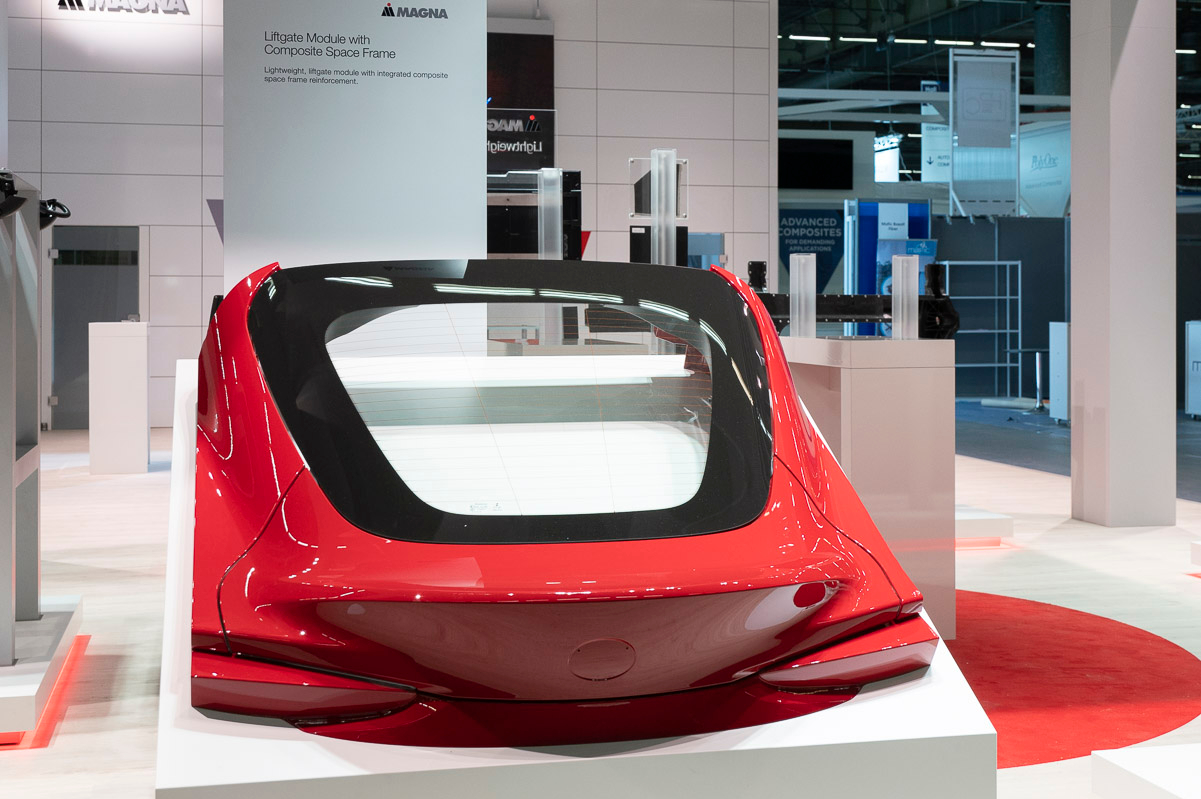
Het uiteindelijke donutvormige frame heeft overal variabele diameters en wanddiktes, maar heeft een nominale diameter van 50-60 millimeter. Afgezien van een kleine beugel in de hoek en harde bevestigingen zoals grendels en scharnieren, plus folie om de integrale antennes te aarden, is het hele frame - dat 104 x 111 centimeter is - volledig samengesteld. Zelfs "oor"-beugels, die worden gebruikt om het binnenbekledingspaneel met de onderste helft van de achterklep te verbinden, zijn van composiet en vervaardigd via HP-RTM. Hoewel het composietframe 10% lichter is dan een vergelijkbaar metalen frame, zorgen de massaontbindende effecten ervoor dat de complete achterklep ~20-25% lichter is dan een metalen achterklep. Lichtere laadkleppen vergen minder inspanning voor de consument om te openen/sluiten, zijn gemakkelijker te installeren voor een werknemer tijdens de montage van het voertuig, besparen brandstof tijdens het gebruik van het voertuig en bieden wat Strouhal beschrijft als "een verbazingwekkend solide geluid" wanneer de achterklep sluit. Het composietsysteem elimineerde ook stappen zoals het omzomen van randen en laspunten/verbindingen die nodig zijn bij metalen laadkleppen.
Chaaya laat doorschemeren dat zijn bedrijf nog een groot autoproject met filamentwonden heeft. Hij zegt ook dat Magna andere toepassingen voor de technologie ziet dan laadkleppen. "Deuren, dekdeksels, motorkappen, FEM's (front-end modules) en zelfs autonome voertuigen - zoals een bus die bestaat uit een met glas omhuld frame - zou zo'n ruimteframe kunnen gebruiken, "voegt hij eraan toe. “En het zou niet eens verborgen hoeven te zijn. Als we koolstofvezelweefsel zouden gebruiken, zou het een teken van prestige zijn om dat mooie oppervlak bloot te laten en het frame er niet in te verbergen."
Hars
- De beginnershandleiding voor gefuseerde filamentfabricage (FFF)
- De rol van Computer-Aided Design (CAD) bij 3D-printen
- De uitdagingen van productontwerp
- De Triode
- Wat is ingebed systeemontwerp:stappen in het ontwerpproces
- Industrieel ontwerp in het tijdperk van IoT
- Optimaliseren van de RF-feedline in PCB-ontwerp
- Nieuwe technologieën en markten op World of Filament Winding-evenement
- Roth filamentwinder om grote Ariane 6 gewichts-/kostenbesparingen te vergemakkelijken
- De voordelen van prototypen van PCB's
- Ken de betekenis van stuklijst in PCB-ontwerp