Grote composiet hoezen beschermen veel water
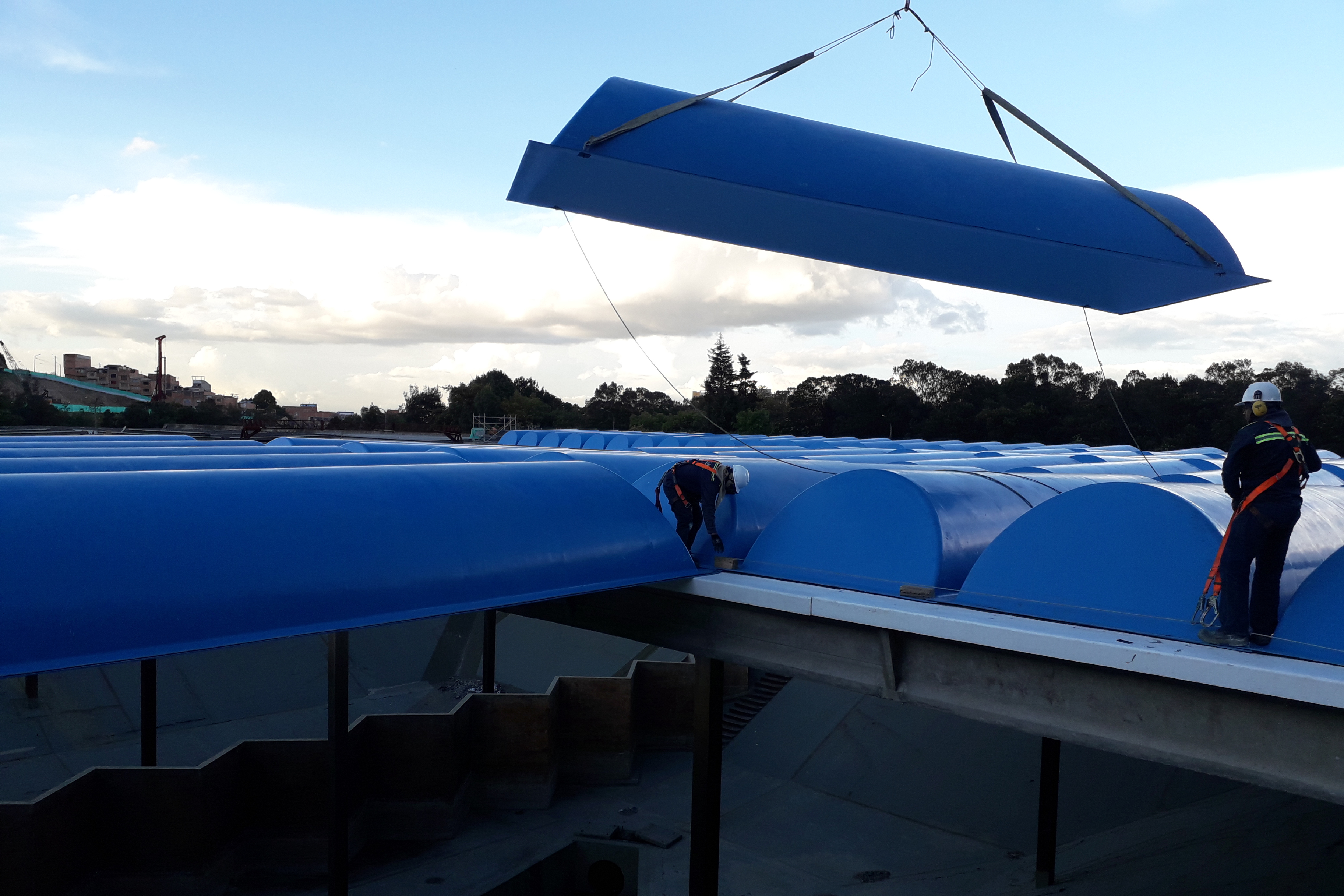
Wateropslag en -levering in Bogotá, Colombia, is, zoals in elk groot stedelijk gebied, ingewikkeld. De uitdaging is niet een van de aanbod, want de stad met zo'n 9 miljoen mensen krijgt elk jaar 32 inch (824 millimeter) regen, plus de rivier de Bogotá stroomt door de stad. De uitdaging is om dat water op te vangen, te behandelen en vervolgens op te slaan zodat het drinkbaar blijft en beschikbaar blijft voor bewoners en bedrijven. Om dit te doen, heeft Empresa de Acueductos y Alcantarillados (Bedrijf van Aquaducten en Riolen, EAAB, Bogotá) in de loop der jaren een reeks van 59 tanks door de hele stad gebouwd om behandeld water op te slaan en de levering aan klanten te verzekeren.
Sommige van deze tanks zijn echte tanks - volledig omsloten om het water te beschermen tegen de elementen van buitenaf. Anderen, velen van hen ouder, zijn massieve betonnen bassins die worden beschermd tegen de elementen met een reeks verwijderbare afdekkingen. Een dergelijke tank, Casablanca genaamd, bevindt zich in de wijk Ciudad Bolivar in het zuidelijke deel van Bogotá en bedient een bevolking van ongeveer 3 miljoen mensen. Casablanca, de grootste wateropslagtank in het EAAB-netwerk en de grootste wateropslagtank in Colombia, meet 144 meter (472 voet) lang x 110 meter (361 voet) breed x 9 meter diep en heeft een opslagcapaciteit van 143.000 kubieke meter ( 38 miljoen gallons) water. De tank wordt in tweeën gedeeld door een betonnen scheidingswand die in het midden loopt, zodat het water in twee gelijke delen wordt opgeslagen.
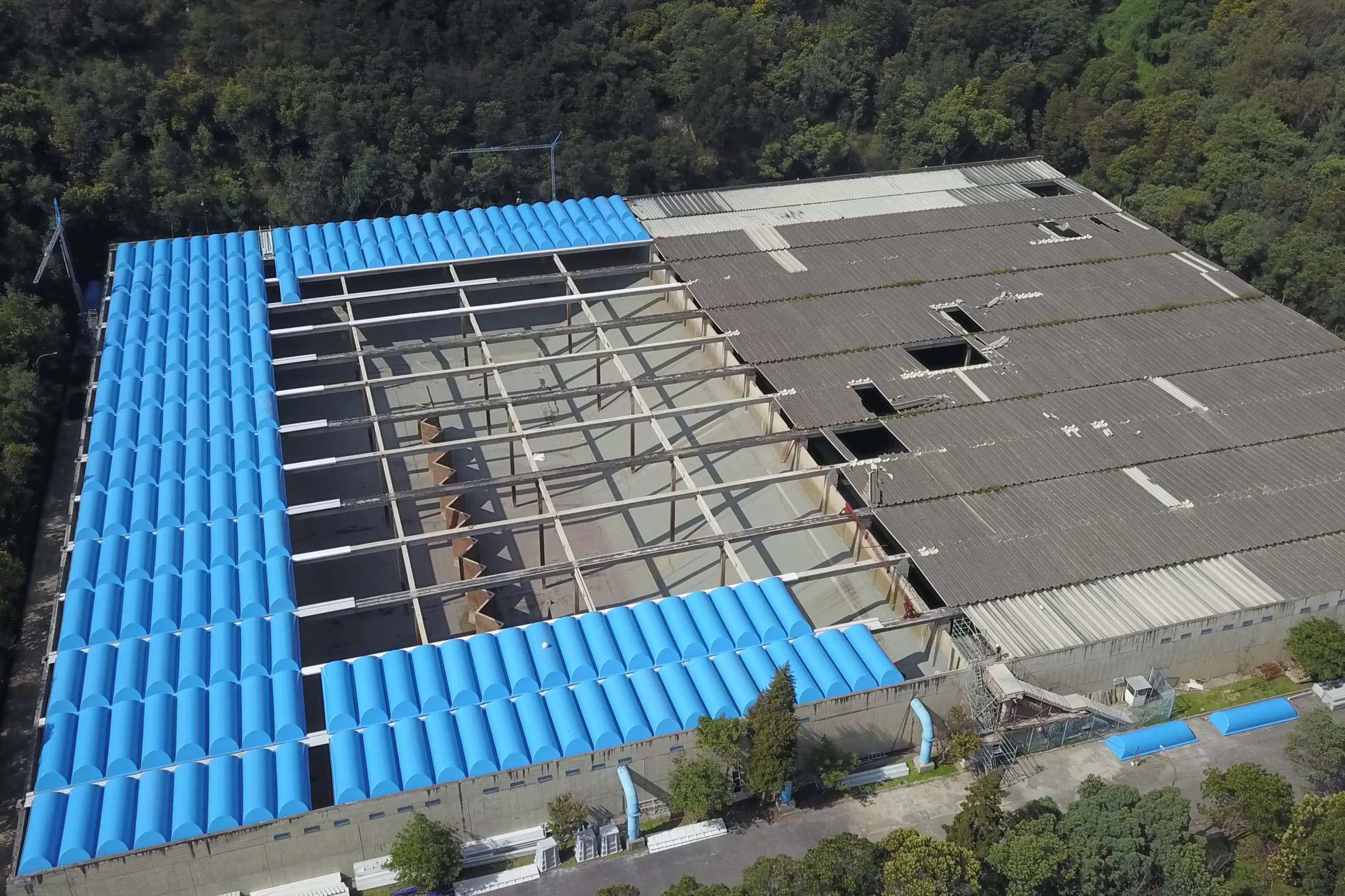
Het onderhouden van de 66-jarige Casablanca is geen gemakkelijke opgave. In 2009 werd ontdekt dat scheuren in de betonnen vloer van de tank elk uur 360.000 liter (95.000 gallons) water lieten ontsnappen. . Reparaties aan het beton met een polyurea coating reduceerden lekkage tot nul. Casablanca had echter nog een probleem boven het beton. Het water in de tank werd beschermd door een reeks afdekkingen die bestonden uit een mengsel van beton en asbest, wat een aanzienlijke bedreiging vormde voor de waterkwaliteit en de menselijke gezondheid. De oude covers waren ook gevoelig voor storingen en waren duur in onderhoud. EAAB moest de oude hoezen vervangen door een veiliger, lichter en duurzamer alternatief.
Grote covers, en veel van hen
EAAB besloot een composietoplossing voor de afdekkingen na te streven, maar werd onmiddellijk uitgedaagd door de schaal van het project. Casablanca wordt doorkruist door een reeks betonnen pilaren die een netwerk van balken ondersteunen waarop de dekens rusten. Deze balken liggen op een onderlinge afstand van ongeveer 7,2 meter (23,6 voet), dus de nieuwe overkappingen zouden zelfdragend moeten zijn en die overspanning moeten afdekken om gebruik te kunnen maken van de bestaande infrastructuur. EAAB stelde voor om dergelijke afdekkingen te vervaardigen via light resin transfer molding (LRTM). De uitdaging? Composietconstructies van dit formaat die voor deze toepassing nodig zijn, waren nog nooit via LRTM in Colombia vervaardigd. Veel fabrikanten waren gewoon niet in staat om het project op zich te nemen.
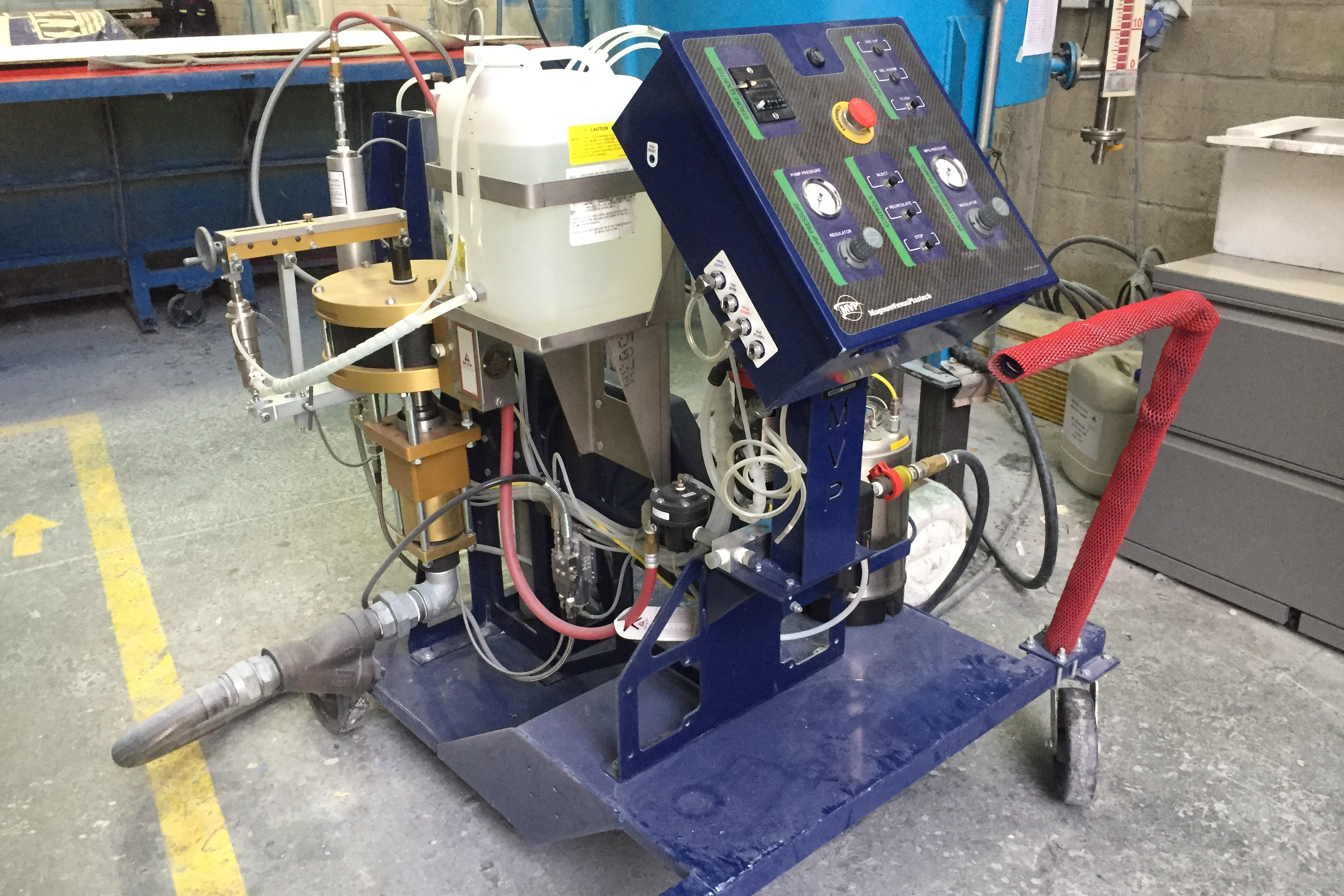
De uitzondering was Innovative Engineering Solutions, of Soling, een fabrikant van composieten in La Estrella, Antioquia, Colombia, net ten zuiden van Medellín. Soling werd in 2014 opgericht door Javiar Moreno, eigenaar en beheerder van verschillende composietproductiebedrijven in en rond Colombia. Rodrigo Vergara, engineeringcoördinator bij Soling, zegt dat de grootte van de afdekkingen voor veel fabrikanten een niet-starter was. "Niemand had hier ervaring mee in Colombia vanwege de grootte van het onderdeel", merkt hij op. "Het is het grootste composietonderdeel dat in Colombia is gefabriceerd." Voor Moreno was het formaat van de hoezen echter een interessante uitdaging. "Voor onze eigenaar [Moreno]", zegt Vergara, "was het een droom die uitkwam. 'Onmogelijk' is een woord dat hij niet begrijpt. Hij zei:'We zullen dit doen!' Ik zei:'OK!'”
Soling stelde een specifieke oplossing voor voor het Casablanca-project:een reeks van 840 koepelvormige, rechthoekige composietstructuren, elk 7,6 meter lang en 2,4 meter breed (24,9 x 7,9 voet). Er is gekozen voor het halfronde koepelontwerp, zegt Vergara, omdat "de geometrische vorm met de meeste mechanische weerstand een omtrek is. Dit was de belangrijkste factor om te garanderen dat de afdekkingen zelfdragend waren. Aan de andere kant moesten we de gemakkelijkste manier vinden om ze van de productielocatie naar het installatiepunt te vervoeren, dat 460 mijl verderop was."
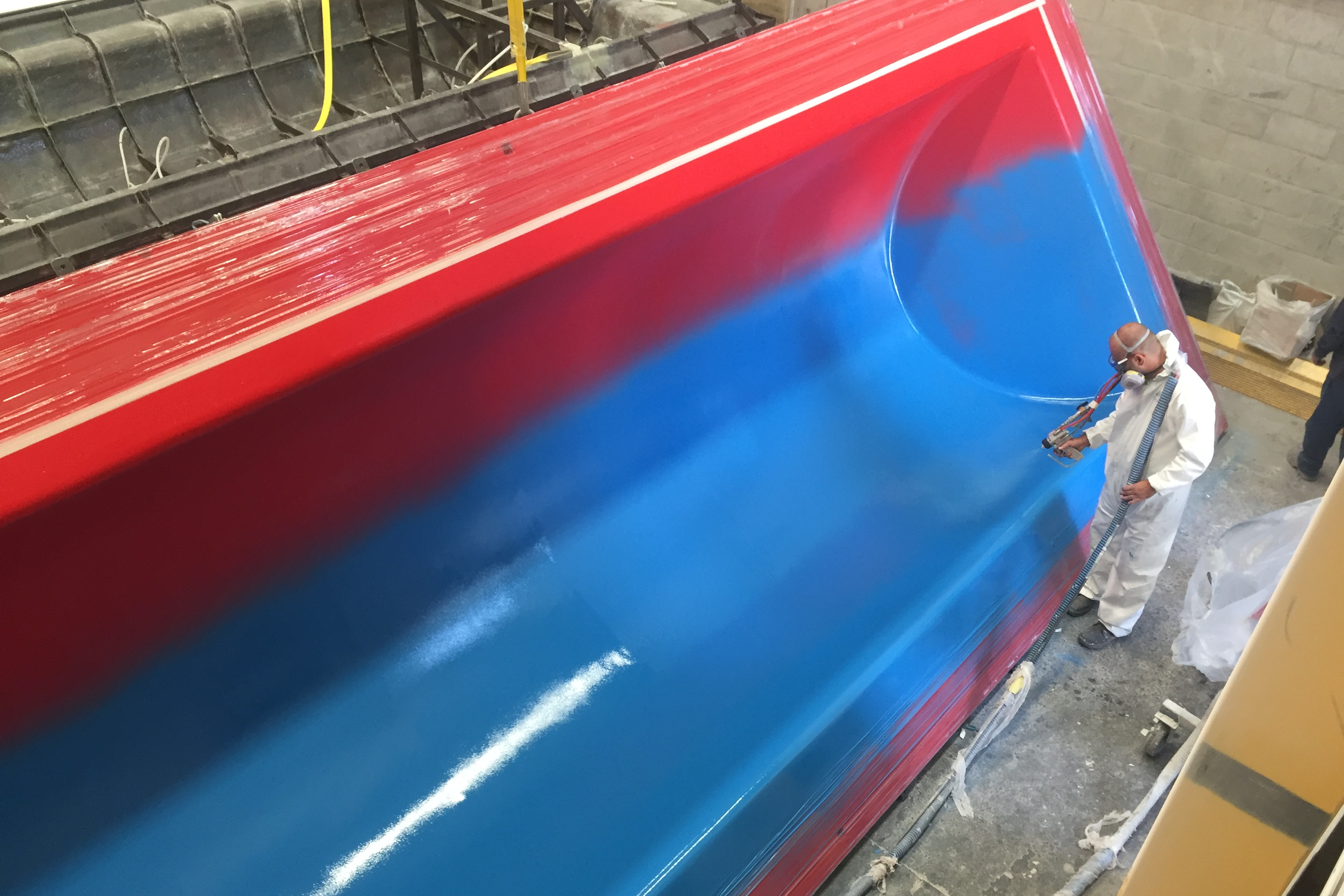
De hoezen zouden worden vervaardigd via LRTM met, volgens de EAAB-specificatie, een blauwe gelcoat aan de buitenkant en een witte gelcoat aan de binnenkant. Bestaande uit glasvezelweefsels en een polyesterhars, zou de hoes, met een oppervlakte van 28,5 vierkante meter (207 vierkante voet), 320 kilogram (705 pond) wegen, waarvan 208 kilogram hars. Met een ontwerp in de hand en een commitment om de hoezen te leveren, gingen Vergara en Soling aan de slag.
De perfecte omslag bouwen
Soling nam het Casablanca-project natuurlijk niet zonder hulp op zich. De samenwerking met het bedrijf was een toeleveringsnetwerk dat een distributeur, een materiaalleverancier en een leverancier van apparatuur omvatte. De distributeur, Minepro SAS (Medellín, Colombia), bood technische ondersteuning en werkte samen met apparatuurleverancier Magnum Venus Products (MVP, Knoxville, Tenn., VS), die pompen en hulpapparatuur voor het LRTM-proces leverde. De leveranciers van materialen zijn Andercol (Medellín), die de polyesterharsmatrix, gelcoats en technische ondersteuning leverde, en Jushi (Tongxiang City, China), die de E-glasvezelstoffen leverde.
Fabricage begint natuurlijk met tooling. De vraag was hoeveel mallen het project nodig had. Om dit te bepalen, zegt Vergara dat Soling eerst het fabricagetempo moest bepalen om aan de leveringsvereisten van EAAB te voldoen. Dit werd op zijn beurt beïnvloed door de eisen op de werkplek. Om mogelijke verontreiniging van de watertoevoer tijdens de installatie van de nieuwe afdekkingen te voorkomen, stemde EAAB ermee in de helft van Casablanca, waarover afdekkingen werden geleverd, leeg te maken en op zijn plaats te laten zakken. Het halveren van de wateropslagcapaciteit van Casablanca brengt uitdagingen met zich mee, daarom moest EAAB de levering en installatie zo snel mogelijk laten plaatsvinden.
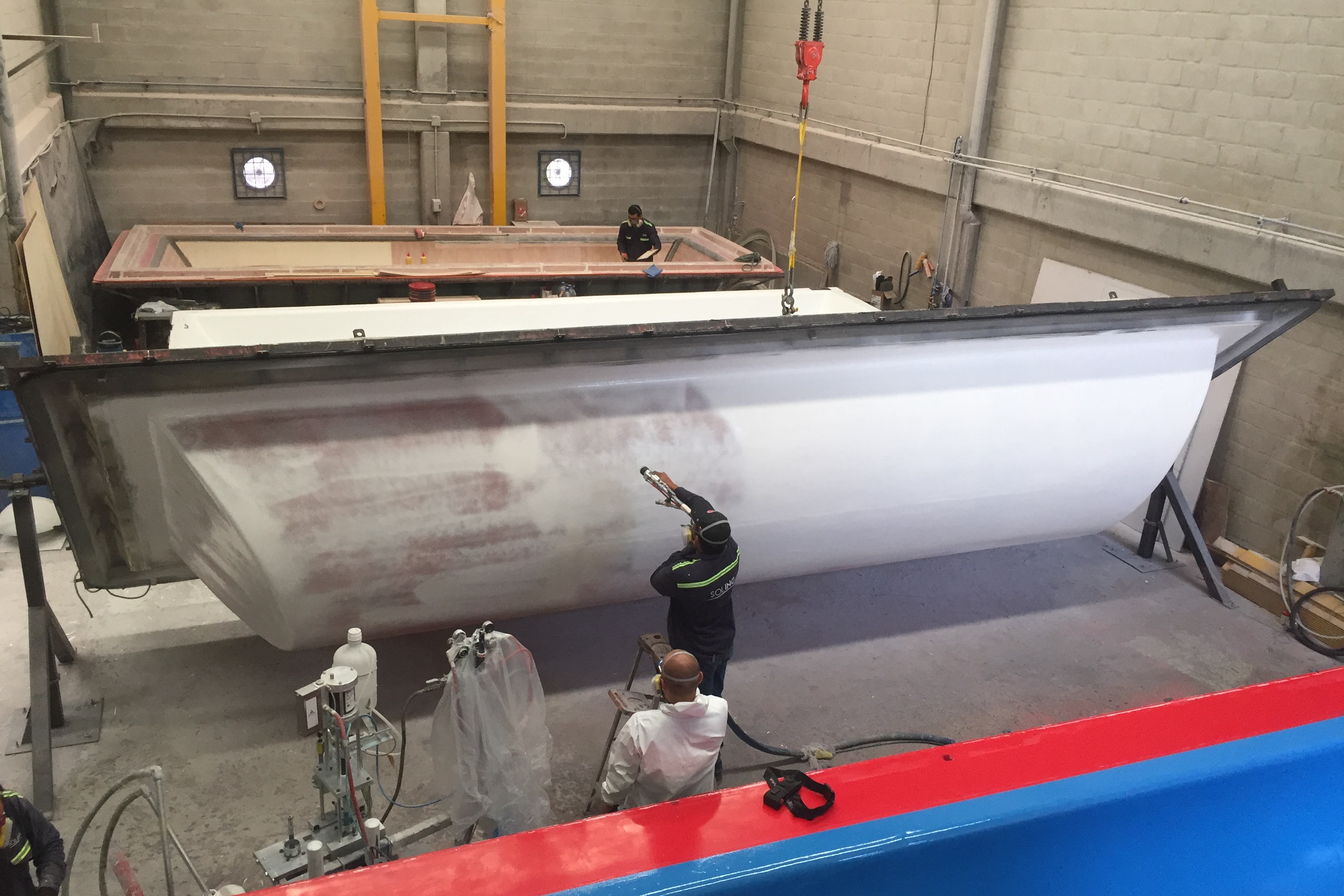
Soling, die samenwerkt met EAAB, legt Vergara uit, kwam tot een productieschema dat zes hoezen per dag zou opleveren. In een fabriek met drie ploegen van acht uur per dag waren er twee mallen nodig, die elk in staat waren om één hoes per ploeg te vervaardigen. De mallen, zegt hij, werden in eigen huis gebouwd en waren samengesteld uit een mannelijk/vrouwelijk ontwerp van glasvezelcomposiet, ondersteund door een stalen draagstructuur.
Met de mallen gebouwd, begon Soling vervolgens met het vaststellen hoe de koepels specifiek zouden worden vervaardigd. In samenwerking met Minepro en MVP zegt Vergara dat werd besloten dat elke mal zou worden gevoed door twee harsinjectiepoorten, met één vacuümpoort. Voor harsinjectie raadde MVP het gebruik aan van zijn Patriot Innovator-pompeenheid voor hoogvolume harsoverdracht (RTM), die in staat is om het grote volume hars te leveren dat nodig is voor elke afdekking. MVP leverde ook zijn Turbo Autosprue-kleppen, evenals universele koppelingen, afdichtingen en matrijsaccessoires.
Om de productie van een hoes te starten, zegt Vergara, werd de vrouwelijke helft van de mal bespoten met witte gelcoat en de mannelijke helft van de mal werd bespoten met blauwe gelcoat. Zoals opgemerkt werden beide gelcoats geleverd door Andercol. Vervolgens werden de door Jushi geleverde E-glasmatten en stoffen met de hand in de vrouwelijke helft van de mal gelegd. Dit werd gevolgd door het via een kraan neerlaten van de mannelijke helft van de mal in de vrouwelijke helft, met de twee helften aan elkaar geklemd. Nadat het vacuüm was getrokken, begon de harsinjectie. Vergara zegt dat de injectie van elke hoes in ongeveer 40 minuten was voltooid, gevolgd door uitharding bij kamertemperatuur. Nadat elk deksel uit de vorm was gehaald, werd het bijgesneden tot de uiteindelijke afmetingen en werden toevoerkanalen voor regenwaterbeperking in het oppervlak van de dekselflens gesneden.
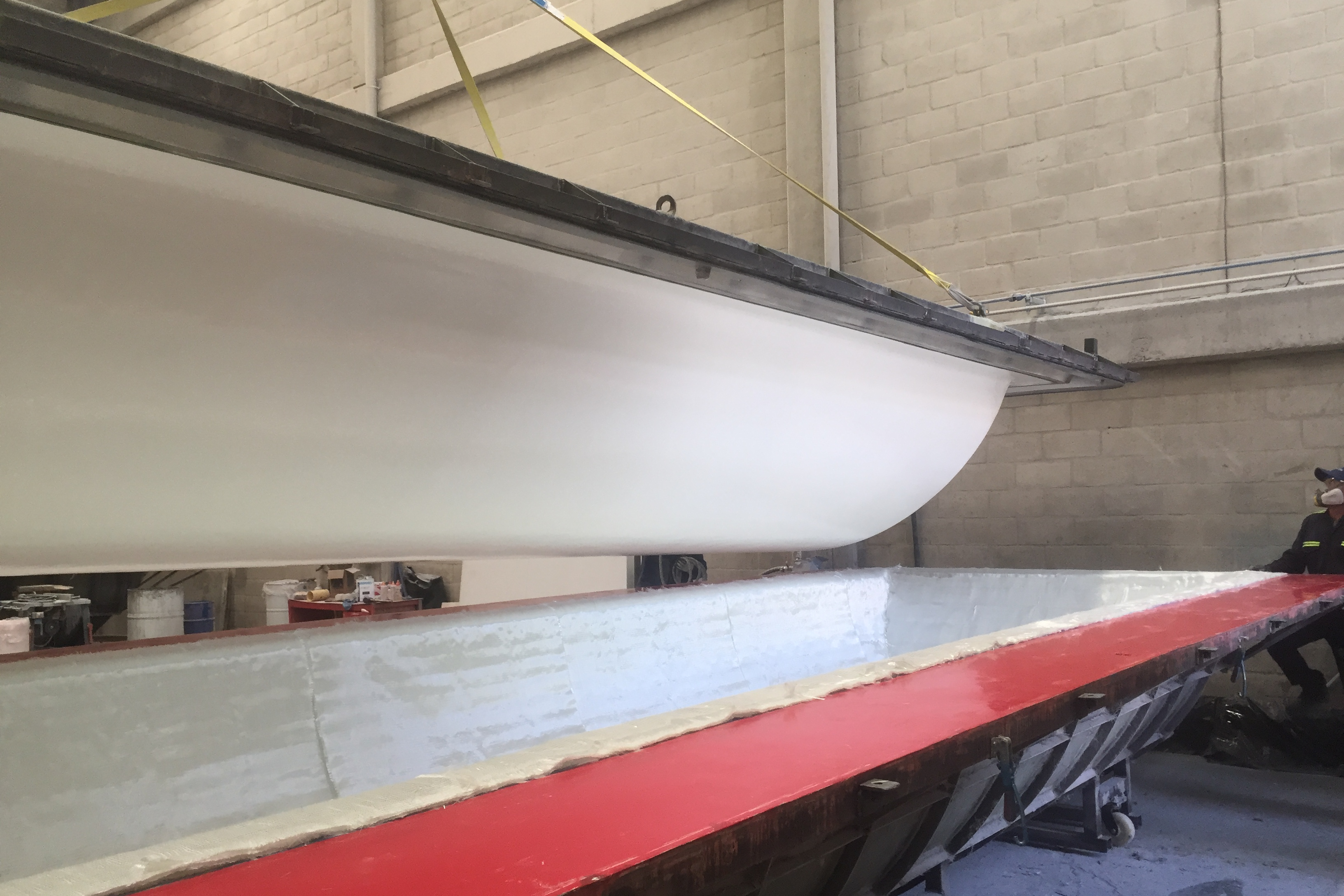
Vergara zegt dat de enorme omvang van de afdekkingen, in combinatie met strikte gewichts- en afmetingseisen, de grootste uitdaging vormden voor hun fabricage. Het bepalen van de locatie van de injectiepoort en het beheren van de injectietiming vergde veel vallen en opstaan en overleg met technische experts. Maar uiteindelijk, zegt Vergara, koos Soling voor een fabricageproces dat zeer herhaalbaar en betrouwbaar bleek te zijn.
"De grootste uitdaging was het gewicht van de elementen die we gingen installeren, omdat we het draagvermogen van de bestaande constructie niet konden overschrijden", zegt Vergara. “Hiervoor moesten alle stukken dezelfde eigenschappen hebben, zowel qua geometrie als qua gewicht. De enige manier om deze voorwaarden te garanderen, was door een proces te gebruiken dat herhaalbaarheid garandeerde.”
Afgewerkte afdekkingen werden over de 418 kilometer (260 mijl) van de fabriek van Soling in de buurt van Medellín naar de Casablanca-werkplaats in Bogotá verscheept en vervolgens met een kraan geïnstalleerd, op de steunconstructie neergelaten en door arbeiders gepositioneerd die op de balken stonden waarop de afdekkingen zouden rusten. Hoewel de afdekkingen niet mechanisch aan de ondersteunende structuren zijn bevestigd, zegt Vergara dat ze ook niet zijn ontworpen om te worden verplaatst of verwijderd, tenzij 'er iets heel ernstigs is gebeurd'.
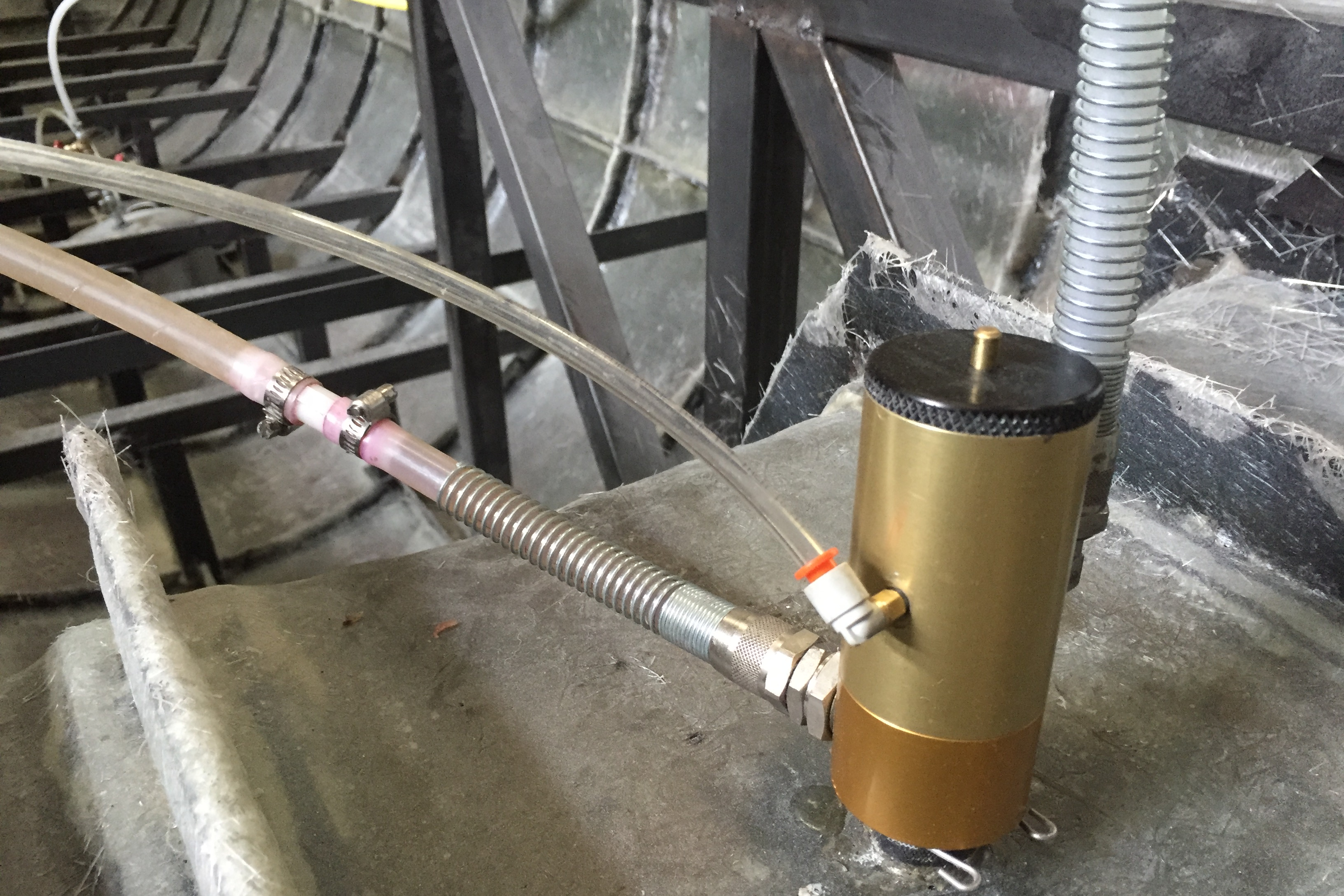
Soling begon begin 2019 met het ontwerpen van de hoezen en begon in 2020 met de fabricage van de eerste hoezen. De pandemie van het coronavirus en occasionele mechanische problemen zorgden ervoor dat de productie stopte en begon, maar volgens Vergara voltooide Soling de productie van alle 840 hoezen over een periode van 7- 8 maanden, afwerking eind 2020. De verwachting is dat de nieuwe afdekkingen aanzienlijk langer meegaan en veel minder onderhoud vergen dan de afdekkingen die ze hebben vervangen.
Het Casablanca-project, zegt Vergara, heeft de capaciteiten van Soling aangetoond als fabrikant van hoogwaardige, hoogwaardige, grote composietstructuren en heeft deuren geopend naar andere kansen. "Dit project was een uitdaging waarbij we paradigma's moesten doorbreken die zeiden dat delen van deze omvang niet gemaakt konden worden met deze productiemethode, en toch hebben we het gedaan", zegt hij. "Voor de toekomst van Soling is iets heel duidelijk:er is geen project dat we niet kunnen doen."
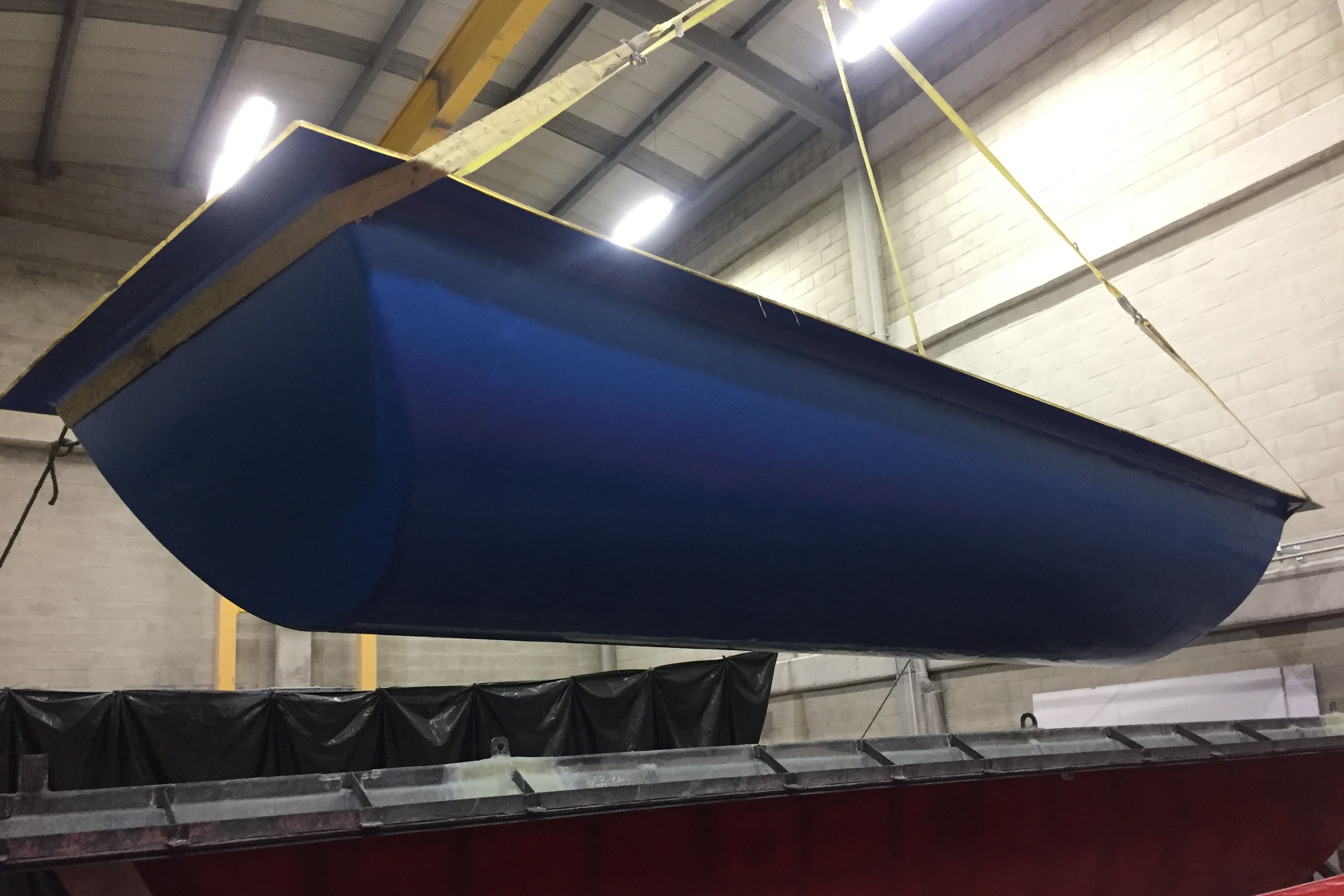
Hars