Depositieproces en eigenschappen van stroomloze Ni-P-Al2O3-composietcoatings op magnesiumlegering
Abstract
Om de corrosieweerstand en slijtvastheid van stroomloze nikkel-fosfor (Ni-P) coating op magnesium (Mg) legering te verbeteren. Ni-P-Al2 O3 coatings werden geproduceerd op een Mg-legering uit een samengesteld galvaniseerbad. De optimale Al2 O3 de concentratie werd bepaald door de eigenschappen van het galvaniseerbad en de coatings. Morfologie groei-evolutie van Ni-P-Al2 O3 composietcoatings op verschillende tijdstippen werden waargenomen met behulp van een scanning elektronische microscoop (SEM). De resultaten laten zien dat nano-Al2 O3 deeltjes kunnen de vervangingsreactie van Mg en Ni 2+ . vertragen in de vroege fase van het afzettingsproces, maar het heeft bijna geen effect op de snelheid van het autokatalytische reductieproces van Ni-P. De anticorrosie- en microhardheidstesten van coatings tonen aan dat de Ni-P-Al2 O3 composietcoatings vertonen betere prestaties in vergelijking met Ni-P-coating dankzij meer geschikte kristalvlakafstand en korrelgrootte van Ni-P-Al2 O3 coatings. Thermische schoktest geeft aan dat de Al2 O3 deeltjes hebben geen invloed op de hechting van coatings. Bovendien is de levensduur van het composietbeplatingsbad 4,2 metaalomzet, wat suggereert dat het potentiële toepassing heeft op het gebied van magnesiumlegeringen.
Achtergrond
Magnesium (Mg) legeringen hebben veel aandacht en wetenschappelijk onderzoek getrokken vanwege de lage dichtheid, hoge specifieke sterkte en uitstekende bewerkbaarheid [1, 2]. Daarom worden Mg-legeringen meestal gebruikt in de ruimtevaart, elektronica en auto's [3, 4]. De toepassing van Mg-legeringen is echter beperkt vanwege de ongewenste gebreken in anticorrosie en slijtvastheid [5, 6]. Zo zijn anticorrosie- en antifrictiemethoden aan het oppervlak ontwikkeld, zoals micro-arc-oxidatiefilm, chemische conversiecoating, thermisch spuiten, fysieke dampafzetting, galvanisatie en stroomloos plateren, voor Mg-legeringen [7,8,9, 10,11,12,13].
Chemische nikkel-fosfor (Ni-P)-plating is een van de meest effectieve oppervlaktetechnologieën voor Mg-legeringen, omdat het uitstekende uitgebreide voordelen biedt op het gebied van goedkope, efficiënte, corrosieweerstand en slijtvastheid [14, 15]. Daarom speelt stroomloze Ni-P-coating een belangrijke rol in het anticorrosieveld van Mg-legeringen. Om de prestaties van de Ni-P-coating verder te verbeteren, kunnen nanodeeltjes, bijvoorbeeld SiC, ZrO2 , TiO2 , SiO2 , en Al2 O3 , enz. worden meestal toegevoegd aan een stroomloos galvaniseerbad om Ni-P nanodeeltjes composietcoatings te bereiden [16,17,18,19,20]. Volgens eerdere studies [20,21,22,23] wordt de prestatie van de Ni-P-coating effectief verbeterd door nanodeeltjes. Hoewel de Ni-P nanodeeltjes composietcoatings relatief hoge prestaties leveren in vergelijking met de Ni-P-coating, zijn er drie problemen die opgemerkt moeten worden. Ten eerste zijn nanodeeltjes gemakkelijk te aggregeren en vormen ze het actieve centrum in het stroomloze galvaniseerbad, wat de stabiliteit van de galvaniseeroplossing vermindert. Ten tweede bepalen procesparameters van een composietplaatbad meestal de inhoud en verdeling van nanodeeltjes in de coatings, en ze zijn ook sleutelfactoren voor het verbeteren van de eigenschappen van coatings. Ten derde is het proces van co-depositie van nanodeeltjes met Ni-P een andere invloedsfactor op de coatingeigenschappen. Daarom zijn deze factoren de aandacht waard. Nano-Al2 O3 deeltjes zijn een goedkoop schuurmiddel met een hoge hardheid en goede chemische stabiliteit [24, 25]. Het kan goed in het stroomloze vernikkelbad worden gedispergeerd. Daarom is Ni-P-Al2 O3 composietcoatings worden gewoonlijk gebruikt als anticorrosie- en antislijtagecoatings om stalen of koperen ondergronden te beschermen. Slechts enkele rapporten waren echter gericht op de stroomloze Ni-P-Al2 O3 plateren op een magnesiumlegeringssubstraat [20, 22, 26]. Bovendien is de studie van het groeiproces van de Ni-P-Al2 O3 coating op Mg-legeringen en de stabiliteit van een composietplaatbad is vrij zeldzaam. Daarom meer details over de prestaties van het composietbad en het co-depositieproces van Ni-P-Al2 O3 moeten worden bestudeerd.
In het huidige werk hebben we, om de eigenschappen van de Ni-P-coating op Mg-legeringssubstraat verder te verbeteren, nikkelsulfaat en melkzuursysteem gebruikt als respectievelijk het belangrijkste zout en complexvormer in het galvaniseerbad. Ondertussen nano-Al2 O3 poeder werd toegevoegd aan het stroomloze Ni-P galvaniseerbad. Om een geschikt stroomloos samengesteld plateerbad voor de AZ91D Mg-legering te verkrijgen, werden de procesparameters van dit bad geëvalueerd op afzettingssnelheid en coatingeigenschappen. Verder werd een periodieke cyclustest uitgevoerd om de levensduur en stabiliteit van het galvaniseerbad bij de optimale procesomstandigheden te evalueren. Het effect van nano-Al2 . bestuderen O3 deeltjes op het groeiproces van de coatings, het depositiegedrag en de fasestructuur van de Ni-P coating werden besproken. Daarnaast werden de eigenschappen, waaronder corrosieweerstand, microhardheid en hechting van coatings, geanalyseerd op basis van morfologie en structuur. De resultaten toonden aan dat de eigenschappen van de Ni-P-Al2 O3 composietbekledingen hadden de voorkeur boven die van de Ni-P-bekleding, en het stroomloze composietbekledingsbad had een goede stabiliteit in de levensduur. Daarom zijn onze resultaten in dit werk een nuttige referentie voor de toepassing van stroomloze Ni-P nanodeeltjes composietcoatings op Mg-legeringen.
Methoden
Voorbereiding van de composietcoatings
In dit werk werd AZ91D gegoten Mg-legering met een afmeting van 2 cm × 1 cm × 0.5 cm gebruikt als experimenteel materiaal, dat de chemische samenstelling in gew.% bevat:8.5 Al, 0.34 Zn, 0.1 Si, 0.03 Cu, 0.002 Ni , 0,005 Fe en 0,02 andere en rest Mg. Het AZ91D-substraat werd achtereenvolgens gepolijst met nr. 500 en 1000 SiC-papier, gespoeld met gedeïoniseerd water en 5 minuten ondergedompeld in alkalische oplossing bij 65 ° C, gevolgd door zuurbeitsen in een chroomzuuroplossing (CrO3 200 g/L) gedurende 60 s. Daarna werd het substraat van de Mg-legering ondergedompeld in een fluorwaterstofzuuroplossing met een concentratie van 380 ml/L voor een activeringsbehandeling van ongeveer 10 minuten. Het Mg-substraat werd bij elke stap gereinigd met gedeïoniseerd water. De basisbadsamenstelling en bedrijfsomstandigheden van stroomloos vernikkelen voor magnesiumlegeringen werden als volgt geïllustreerd:35 g/L NiSO4 ⋅6H2 O, 35 g/L melkzuur, 30 g/L Na2 H2 PO2 ⋅H2 O, 10 g/L NH4 HF2 , 3 mg/L stabilisator, pH 4,5~7,0, en temperatuur 70~90 °C. Het stroomloze galvaniseerbad werd bewaard in een glazen beker, die in een thermostaatgestuurd waterbad werd geplaatst. Een elektrische roerder met digitale display werd gebruikt om roerkracht te verschaffen. De gemiddelde deeltjesgrootte van de nano-Al2 O3 deeltjes is ongeveer 50 nm. De nano-Al2 O3 deeltjes werden voldoende gedispergeerd in het bad onder de ultrasone golfconditie vóór stroomloos plateren.
Tests voor afzettingssnelheid en stabiliteit van plaatbaden
Het effect van nano-Al2 . bestuderen O3 deeltjes op de afzettingssnelheid van stroomloos vernikkelen bad, wordt de afzettingssnelheid uitgedrukt in Vgl. (1).
$$ v=\frac{\Delta w\times {10}^4}{\rho St} $$ (1)waar v , ρ , S , t , en △w vertegenwoordigen de depositiesnelheid (μm/h), dichtheid van de Ni-P-coating (~ -7,9 g/cm 3 ), oppervlakte van het Mg-substraat (cm 2 ), respectievelijk depositietijd (h) en het coatinggewicht (g). Bovendien is de inhoud van nano-Al2 O3 deeltjes in de coating werden geschat door middel van een weegmethode met behulp van een elektronische balans (AR2140, Ohaus). Om de stabiliteit van een stroomloos plateerbad te evalueren, werd een periodieke cyclustest (of metal turn-over, MTO) gebruikt om de levensduur en stabiliteit van het bad te evalueren. Hier heeft 1 MTO gedefinieerd dat het depositiegewicht van Ni gelijk is aan de initiële concentratie van Ni 2+ in het bad. Als we bijvoorbeeld 1 L galvaniseerbad nemen, wordt ongeveer 7,8 g Ni verkregen uit het bad \( \left({C}_{{\mathrm{Ni}}^{2+}}=7.8\kern0.5em \mathrm {g}/\mathrm{L}\right) \) beschouwd als 1 MTD. Daarnaast een verse mengseloplossing (\( {\mathrm{Ni}}^{2+}:{\mathrm{H}}_2{\mathrm{PO}}_2^{2-}=1:3 \) in molverhouding) werd toegevoegd aan het galvaniseerbad wanneer het bad een lage afzettingssnelheid had. De stabiliteitstest werd beëindigd tot de ontleding van het galvaniseerbad. De uitdrukking van MTO kan dus worden gepresenteerd als Vgl. (2).
$$ \mathrm{MTO}=M/m $$ (2)M en m vertegenwoordigen het cumulatieve depositiegewicht van Ni en de concentratie van Ni 2+ respectievelijk in het galvaniseerbad.
Kenmerken van materialen
De oppervlaktemorfologie van de coating werd waargenomen met behulp van een scanning elektronenmicroscopie (SEM, Hitachi S-4800). De structuur van de coating werd bestudeerd door de röntgendiffractometer (XRD, D/Max-2200, Japan) met een CuKα straling (γ = 0.154 nm).
Elektrochemische meting
Een potentiodynamische polarisatietest werd uitgevoerd op een elektrochemische analysator (CHI800, Chenhua, China). Elektrochemisch experiment werd uitgevoerd in een waterige oplossing van 3,5 gew.% NaCl met behulp van een klassieke configuratie met drie elektroden, die bestond uit een werkende elektrode (monster, 1 cm 2 ), een tegenelektrode (platina) en een referentie-elektrode (verzadigde calomelelektrode). Tijdens het potentiodynamische sweep-experiment werd het monster eerst gedurende 30 minuten ondergedompeld in de elektrolytoplossing om het open circuitpotentieel te stabiliseren (E 0 ). Tafelplot werd getransformeerd uit de geregistreerde gegevens en de corrosiestroomdichtheid (i corr ) werd bepaald door de lineaire doorsnede van de anodische en kathodische Tafel-lijnen te extrapoleren. De veegsnelheid van het experiment was 5 mV/s en werd uitgevoerd bij 25°C. De microhardheden van de magnesiumlegering met verschillende composietcoatings werden geëvalueerd met behulp van een HXD-1000 microhardheidsmeter met een Vicker-indenter bij een belasting van 100 g en een duurzame tijd van 15 s. Er werd een thermische schoktest uitgevoerd om de hechting van coatings te evalueren [23]. Het werd als volgt beschreven:in een luchtatmosfeer, het Mg-substraat met Ni-P-coating of Ni-P-Al2 O3 de coating werd in een hoge temperatuur box-weerstandsoven geplaatst en verwarmd tot 250 ±-10 °C met een verwarmingssnelheid van 20 °C min −1 daarna geblust in koud water. Dit proces werd 20 keer herhaald.
Resultaten en discussie
Figuur 1 toont de effecten van de concentratie van nano-Al2 O3 deeltjes, roersnelheid, pH en temperatuur op de depositiesnelheid, en Al2 O3 inhoud van composietcoatings. Zoals te zien is in figuur 1a, neemt de depositiesnelheid licht af met de toename van Al2 O3 deeltjesconcentratie van 0 tot 15 g/L. Aan de andere kant, de Al2 O3 het gehalte van de composietcoatings neemt geleidelijk toe terwijl de concentratie van Al2 O3 deeltjes neemt toe van 0 tot 10 g/L. Het neemt echter af wanneer de concentratie van Al2 O3 deeltje is hoger dan 10 g/L. Deze verandering is te wijten aan de aggregatie van deeltjes in hoge concentraties, die het co-depositiegedrag van Ni-P met Al2 verzwakt O3 . In Fig. 1b, wanneer de roersnelheid is ingesteld op 300~400 rpm, de depositiesnelheid en de Al2 O3 het gehalte aan composietcoatings is respectievelijk 18 m/h en 3,6%. De resultaten tonen aan dat de dispergeerbaarheid van Al2 O3 deeltje in het galvaniseerbad is het beste bij dit bereik van roersnelheid. Wat betreft het zuurcomposietbad, het effect van de pH-waarde op de depositiesnelheid en Al2 O3 inhoud van coatings wordt getoond in Fig. 1c. De maximale afzettingssnelheid is tot 18,5 m/u wanneer de pH-waarde binnen het bereik van 6,0~6,5 ligt, terwijl de Al2 O3 gehalte aan coatings neemt bijna toe met de pH-waarde. Figuur 1d laat zien dat zowel de depositiesnelheid als de Al2 O3 het gehalte aan composietcoatings neemt toe met de temperatuur, omdat de activiteit van ionen en deeltjes wordt verbeterd en de reactiesnelheid van het composietbad ook wordt versneld bij hoge temperatuur. De stabiliteit van het galvaniseerbad en de porositeit van coatings worden echter slechter bij hoge temperaturen (>-85 °C) [13, 22]. Op basis van de bovenstaande analyseresultaten worden de voorlopige procesparameters en bedrijfsomstandigheden van het composietbad bepaald voor magnesiumlegering, dat wil zeggen 35 g/L NiSO4 ⋅6H2 O, 35 g/L melkzuur, 30 g/L Na2 H2 PO2 ⋅H2 O, 10 g/L NH4 HF2 , 10 g/L nano-Al2 O3 deeltjes, 3 mg/L stabilisator, pH = 6.0~6.5, T = 85 °C en roersnelheid bij 350 rpm.
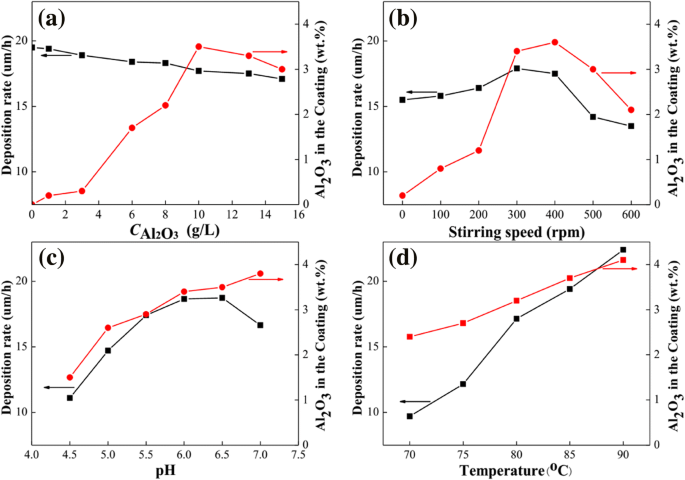
Effecten van procesparameters op depositiesnelheid en Al2 O3 inhoud van coatings
Het depositieproces van Ni-P-Al2 . onderzoeken O3 coatings, wordt de verandering van oppervlaktemorfologiebeelden van magnesiumlegering met afzettingsreactietijd getoond in Fig. 2. Voor vergelijkende analyse vertegenwoordigt Fig. 2a-c het afzettingsproces van Ni-P-coating, terwijl Fig. 2d-f de co -afzettingsproces van Ni-P-Al2 O3 (3,6 gew.%) composietcoatings. Figuur 2a is het morfologiebeeld van onderdompeling van Mg-substraat in het galvaniseerbad gedurende 0,5 min, een groot aantal kubische structuurdeeltjes verdeeld over het oppervlak. Deze kubische deeltjes zijn bevestigd als MgF2 , die zich voornamelijk vormt in het HF-activeringsproces, in overeenstemming met de literatuurrapporten [23, 27]. De morfologie van het beeld van figuur 2d is echter duidelijk verschillend van figuur 2a. Het belangrijkste verschil is dat de MgF2 deeltjes in figuur 2d zijn kleiner dan die in figuur 2a. Bovendien zijn veel nano-Al2 O3 deeltjes worden waargenomen op het oppervlak van Mg-substraat. De verandering van morfologie is afkomstig van Al2 O3 deeltjes die continu invloed hebben op het oppervlak van magnesiumlegering bij hoge temperatuur en roerproces. Wanneer de stroomloze Ni-P-plateringstijd maximaal 5 minuten is, zoals te zien is in figuur 2b, groeien Ni-deeltjes geleidelijk en bedekken ze vervolgens het hele oppervlak van de magnesiumlegering. Maar voor stroomloze composietbeplating (zie Fig. 2e), de grotere Ni-deeltjes en nano-Al2 O3 deeltjes worden waargenomen op het oppervlak van magnesiumlegering en de Ni-P-Al2 O3 coatings bedekken het Mg-substraat niet volledig binnen 5 minuten. Het geeft aan dat de groeisnelheid van Ni-P-Al2 O3 coatings in het composietbad is lager dan die van Ni-P coating in het bad zonder Al2 O3 deeltjes. Dit is een bewijs ter ondersteuning van de oorzaak van de lage afzettingssnelheid in het composietbekledingsbad. Wanneer de stroomloze galvanisatietijd gedurende 30 minuten wordt uitgevoerd, wordt de morfologie van Ni-P-coating en Ni-P-Al2 O3 coatings wordt respectievelijk getoond in Fig. 2c, f. Wat betreft Ni-P-coating, vertoont het oppervlak een dichte en nodulaire structuur met een gemiddelde grootte van 3 m. Maar in Fig. 2f, de gemiddelde nodulaire grootte van Ni-P-Al2 O3 composiet coatings is blijkbaar kleiner dan die van Ni-P coating. Bovendien kan duidelijk worden waargenomen dat de nano-Al2 O3 deeltjes ingebed in Ni-P coating. Belangrijk, gezien de oppervlakteverdeling van Al2 O3 deeltjes, de verdeling van Al2 O3 deeltjes in Fig. 2f is aanzienlijk minder dan die in Fig. 2c, e. Dit resultaat geeft aan dat de depositie van Ni-P dominant is, terwijl de depositie van Al2 O3 deeltjes worden ondergeschikt na een depositiereactietijd van 5 min. Soortgelijke gevolgtrekkingen kunnen ook worden verkregen uit de relatieve inhoud van Al2 O3 deeltjes in de coatings (Fig. 1). Met andere woorden, het effect van Al2 O3 deeltjes op het depositieproces zijn voornamelijk aanwezig in de beginfase van stroomloos vernikkelen.
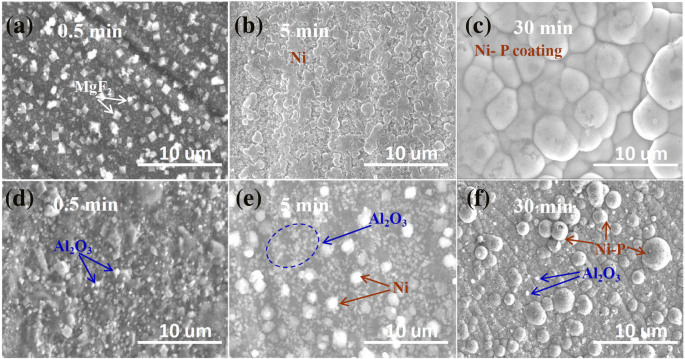
Oppervlaktemorfologie van Ni-P-coating (boven, a -c ) en Ni-P-Al2 O3 composietcoatings (onder, d -f ) op verschillende afzettingstijden
Het effect van nano-Al2 . onderzoeken O3 deeltjes op de structuur van Ni-P-coating, de XRD-patronen van de AZ91D Mg-legering, Ni-P-coating en Ni-P-Al2 O3 composietcoatings worden geanalyseerd in Fig. 3. Zoals te zien is in Fig. 3, concentreert de diffractiehoek van kristalvlakken van magnesiumlegering zich voornamelijk in het bereik van 30 ° ~ 70 °, bijvoorbeeld α (10\( \overline{1} \)0) 32,2°, α (0002) 34,2°, β (10\( \overline{1} \)1) 36,8°, enz. Wat betreft een Mg-legering gecoat met Ni-P-coating, vertoont het diffractiepatroon van Ni-P-coating een verbredende piek en diffractie met hoge intensiteit bij 44,7° die kan worden toegeschreven aan het (111) kristalvlak van een vlak-gecentreerde kubische (fcc) fase van nikkel (Tabel 1) [28]. Bovendien wijst het bestaan van een dergelijke brede piek op de vorming van Ni-P-coating met een gemengde amorfe kristallijne structuur. Na het plateren van de Ni-P-Al2 O3 (3,6 gew.%) composietcoatings, zijn er duidelijk drie nieuwe diffractiepieken te vinden bij 25,6°, 43,5° en 73,2°. Deze pieken worden toegeschreven aan de karakteristieke diffractiepieken van Al2 O3 vergeleken met de PDF-kaart nr. 88-0826. Vandaar dat Ni-P-Al2 O3 composietcoatings worden afgezet op het oppervlak van een Mg-legering. Bovendien verschuift de diffractiepiek van het (111) kristalvlak van Ni naar 45,2° (zie tabel 1) in Ni-P-Al2 O3 composietcoatings, suggererend nano-Al2 O3 deeltjes hebben een zekere invloed op de (111) kristalvlakafstand van Ni. Volgens de Bragg-formule, nλ = 2d sinθ (n = 1, 2, 3, ..., λ = 0,154 nm, d en θ vertegenwoordigen respectievelijk interplanaire afstand en diffractiehoek), de (111) kristalvlakafstand van Ni wordt met ongeveer 3% verminderd met Al2 O3 deeltjes. Verder zijn zowel de (111) diffractiepieken van Ni in de Ni-P-coating als Ni-P-Al2 O3 composietcoatings werden respectievelijk aangebracht door de Gauss-functie. Het resultaat laat zien dat de volledige breedte bij half maximum (FWHM) van deze diffractiepiek in Ni-P-Al2 O3 composietcoatings is breder dan die in Ni-P-coating (tabel 1). Volgens de Scherrer-formule, D = Kγ /B cosθ (D , K , B respectievelijk kristallijne korrel, Scherrer-constante en FWHM vertegenwoordigen), de kristallijne korrel van Ni-P-Al2 O3 composietcoatings worden met Al2 . met ongeveer 8% verminderd O3 deeltjes vergeleken met Ni-P coating. Dit houdt in dat nano-Al2 O3 deeltjes verfijnen de grootte van Ni-kristallijne korrels, wat consistent is met het waargenomen resultaat van SEM hierboven.
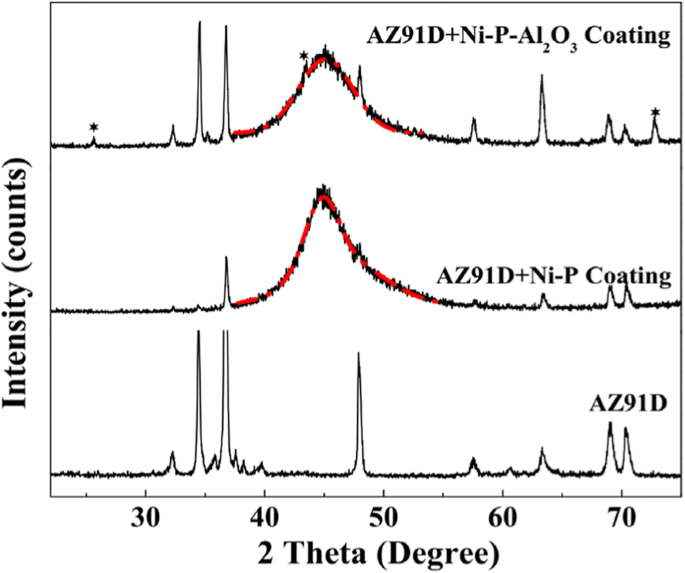
XRD-patronen van het AZ91D-substraat, Ni-P-coating en Ni-P-Al2 O3 (3,6 gew.%) composietcoatings
Figuur 4 en Tabel 2 tonen de polarisatiecurven en anticorrosieparameters van AZ91D Mg-legeringssubstraat, Ni-P-coating en Ni-P-Al2 O3 composietcoatings in een 3,5 gew.% NaCl-oplossing in water bij kamertemperatuur, respectievelijk. De kathodereactie in de polarisatiecurven komt overeen met de waterstofontwikkeling, terwijl de anodische polarisatiecurven de belangrijkste karakteristieke reactieprocessen van corrosieweerstand zijn [29]. Voor het AZ91D Mg-legeringssubstraat wordt een door activering gecontroleerd anodisch proces waargenomen wanneer het aangelegde potentieel toeneemt in het anodische gebied. Bovendien wordt het serieus opgelost in een elektrolytoplossing en is het corrosiepotentieel (E corr ) wordt afgelezen bij − 1,47 V. Maar voor de E corr van de Ni-P-coating, vertoont het een significante positieve verschuiving naar -0,51 V vergeleken met die van het Mg-legeringssubstraat (-1,47 V), en de corrosiestroomdichtheid (i corr ) neemt duidelijk af van 1.4 × 10 −4 A/cm 2 van het substraat tot 3,1 × 10 −6 A/cm 2 van de Ni-P-coating (zie tabel 2). Wat betreft Ni-P-Al2 O3 (1,7 ~ 4,2 gew.%) composietcoatings, hier de Al2 O3 het gehalte aan coatings wordt verkregen door de weegmethode. Zoals te zien is in Tabel 2, zijn alle E corr van de positieve verschuiving van de composietcoating en i corr van de composietcoatings neemt af in vergelijking met de Ni-P-coating, wat suggereert dat Ni-P-Al2 O3 coatings hebben hogere prestaties in corrosieweerstand. Hierin is de Ni-P-coating met 3,6 gew.% Al2 O3 toont de hoogste E corr (− 0,35 V) en laagste i corr (4.5 × 10 −7 A/cm 2 ). Echter, de E corr en ik corr van Ni-P-Al2 O3 (4,2 gew.%) worden gewijzigd in − 0,41 V en 1,0 × 10 −6 A/cm 2 , respectievelijk. Het kan zijn dat Al2 O3 deeltjes verhogen de porositeit van Ni-P-coating en verminderen de prestaties van composietcoatings. Daarom is de Al2 O3 Het gehalte aan composietcoatings heeft een belangrijk effect op de corrosieweerstand van composietcoatings. Het is ook gerelateerd aan de structuur inclusief kristalvlakafstand en korrelgrootte van de coatings (Fig. 3).
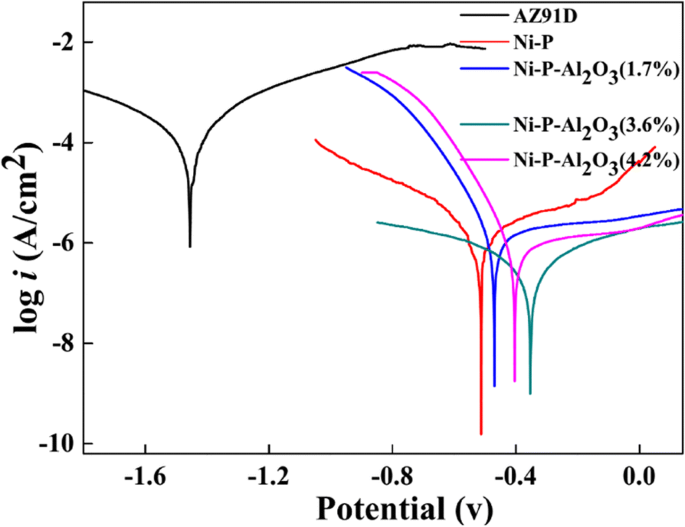
Polarisatiecurven van het AZ91D-substraat, de Ni-P-coating en de Ni-P-Al2 O3 composiet coatings
Om de microhardheid van de coatings te testen, werd de gemiddelde dikte van alle coatings bepaald op 18 m, geschat op basis van de depositiesnelheid en depositietijd. De resultaten van microhardheidstesten van Mg-legeringssubstraat en de coatings met verschillende Al2 O3 inhoud wordt getoond in Fig. 5. Zoals te zien is in Fig. 5, is de microhardheid van de kale AZ91D Mg-legering slechts ongeveer 120 HV, terwijl de microhardheid van een Mg-legeringssubstraat gecoat met een Ni-P-coating maximaal is 520 HV. Het is hoger dan het substraat ongeveer 400 HV, wat aangeeft dat Ni-P-coating de hardheid van de substraatcoating effectief kan verbeteren. Als resultaat wordt de slijtvastheid van het Mg-legeringssubstraat verbeterd door de Ni-P-coating. Bovendien is de Ni-P-Al2 O3 composietcoatings vertonen een aanzienlijke toename van de neiging tot microhardheid wanneer het gehalte aan Al2 O3 in de coating neemt toe van 0 tot 3,6 gew.%. Daarom is Ni-P-Al2 O3 (3,6%) composietcoatings vertonen de hoogste hardheidswaarde bij 638 HV. De reden komt van nano-Al2 O3 deeltjes die de fasestructuur optimaliseren (zie Fig. 3) van de Ni-P-legering en de microhardheid van coatings verbeteren. De inhoud van Al2 O3 in de composietcoatings bereikt 4,2 gew.%, en in plaats daarvan neemt de microhardheid van coatings af tot 576 HV. Dit betekent dat een hoger gehalte aan nanodeeltjes de Ni-P-kristalstructuren kan aantasten, wat leidt tot ongunstige prestaties van de composietcoatings.
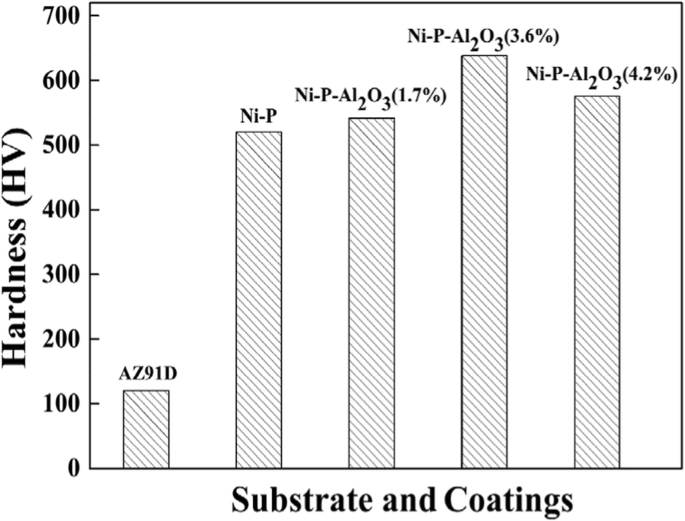
Hardheid van het AZ91D-substraat, de Ni-P-coating en de Ni-P-Al2 O3 composiet coatings
Adhesie tussen coatings en Mg-legeringssubstraat werd uitgevoerd door een thermische schoktest volgens het experimentgedeelte. Via 20 cyclustesten, zowel de Ni-P coating als Ni-P-Al2 O3 composietcoatings hechtten goed aan het Mg-legeringssubstraat. De defecten, zoals barsten, blaarvorming en afspatten, werden niet waargenomen tijdens het testproces, wat aangeeft dat de Ni-P of Ni-P-Al2 O3 coatings hadden een goede hechting met het Mg-legeringssubstraat tegen het thermische schokproces. Bovendien werden morfologiebeelden in dwarsdoorsnede tussen de coatings en het Mg-legeringssubstraat ook waargenomen met behulp van SEM. Zoals waargenomen in Fig. 6, blijkt verder dat er geen duidelijk defect is tussen de coatings en het substraat via thermische schoktest. Belangrijk is dat thermische schoktest en observatie van de dwarsdoorsnede aangeven dat nano-Al2 O3 deeltjes hebben geen invloed op de hechting van composietcoatings.
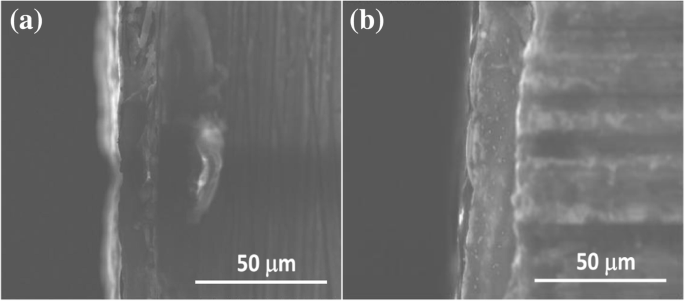
Morfologische dwarsdoorsnedebeelden van de Ni-P-coating (a ) en Ni-P-Al2 O3 (3,6 gew.%) composietcoatings (b )
In het huidige werk, 1-L galvaniseerbaden zonder en met nano-Al2 O3 deeltjes (10 g/L) werden respectievelijk bereid. Hierin werd het aanvankelijke gehalte aan nikkelbron in het galvaniseerbad berekend op 7,8 g, en de belastingscapaciteit van het bad werd ingesteld op 0,5 dm 2 /L. Volgens de regels van de periodieke cyclustest (zie experimentele sectie), werd eerst de MTO van het stroomloze Ni-P-plateringsbad geëvalueerd en werd ongeveer 48,2 g Ni-P-legering verkregen. Hier werd 90% nikkelgehalte geïdentificeerd in Ni-P-coating met behulp van EDS-analyse (zie Fig. 7). Daarom kan het nikkelgehalte in de coating worden berekend als 43,4 g. Dat wil zeggen, de MTO van het platerenbad zonder Al2 O3 deeltjes is 5,6 door gebruik te maken van Vgl. (2). Wat betreft de stroomloze Ni-P-Al2 O3 composiet plateerbad, totaal 38,8 g Ni-P-Al2 O3 coatings werden afgezet uit het composietbad. Evenzo werden 86,45% Ni, 9,84% P, 1,96% Al en 1,75% O bepaald door EDS-analyse (Fig. 7). Daarom kan het nikkelgehalte in de composietcoatings worden berekend als 33,5 g, en de MTO van het composietbad is 4,2. Uit de resultaten van de periodieke cyclustest blijkt dat de gebruikscyclus van het samengestelde galvaniseerbad 1,4 MTO minder is dan die van het stroomloze Ni-P galvanische bad. Het betekent dat nano-Al2 O3 deeltjes verminderen de levensduur van een stroomloos platingbad. Niettemin, de Ni-P-Al2 O3 composietbeplating heeft nog steeds potentiële toepassing op het gebied van magnesiumlegeringen.
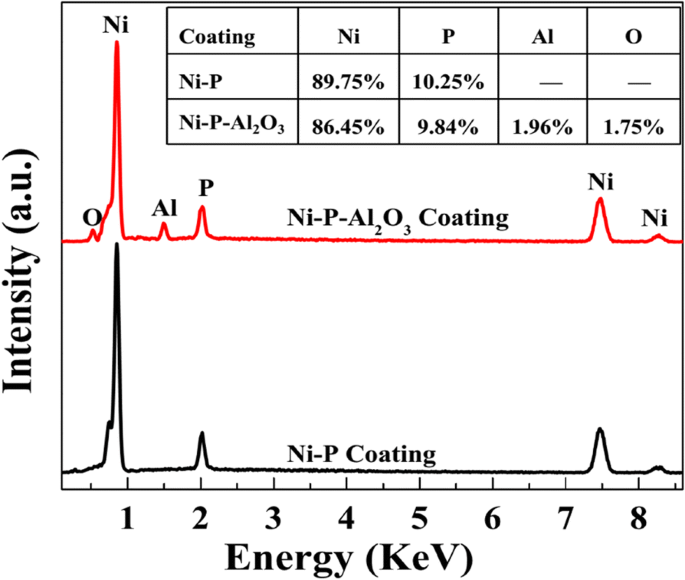
De EDS-spectra van de Ni-P-coating en de Ni-P-Al2 O3 composiet coatings
Conclusies
Samenvattend hebben we een stroomloos composietplaatbad en bedrijfsomstandigheden verkregen om het Ni-P-Al2 mede af te zetten O3 coatings op magnesiumlegering, d.w.z. 35 g/L NiSO4 ⋅6H2 O, 35 g/L melkzuur, 30 g/L Na2 H2 PO2 ⋅H2 O, 10 g/L NH4 HF2 , 10 g/L nano-Al2 O3 deeltjes, 3 mg/L stabilisator, en pH = 6.0~6.5, T =-85 °C en roersnelheid bij 350 rpm. Morfologische karakterisering en fasestructuuranalyse van de composietcoatings toonden aan dat nano-Al2 O3 deeltjes hadden een belangrijke invloed op het groeiproces en fasestructuren (kristalvlakafstand en korrelgrootte) van de coatings. 3,6 gew.% Al2 O3 inhoud verbeterde effectief de microhardheid en corrosieweerstand van de Ni-P-coating. Bovendien bleek uit de hechtingstest dat er bijna geen verschil was tussen Ni-P-coating en Ni-P-Al2 O3 bekleding. Levensduurtest identificeerde dat de MTO van een stroomloos composietplaatbad ongeveer 4 was. Kortom, stroomloos Ni-P-Al2 O3 composietbeplating is een belangrijke technologie om de toepassing van magnesiumlegeringen uit te breiden.
Afkortingen
- E 0 :
-
Open circuit potentieel
- i corr :
-
Corrosiestroomdichtheid
- Mg:
-
Magnesium
- MTO:
-
Metaalomzet
- Ni-P:
-
Nikkel fosfor
- SEM:
-
Scanning elektronenmicroscopie
- XRD:
-
Röntgendiffractie
Nanomaterialen
- Eigenschappen en gebruik van contragewicht van wolfraamlegering
- Eigenschappen en gebruik van Tungsten Alloy Balls
- Eigenschappen en toepassingen van wolfraam koperlegering
- Toepassingen en eigenschappen van wolfraam-nikkel-ijzerlegering
- Wat is kobaltlegering en wat zijn de eigenschappen van kobaltlegeringen?
- Aluminium eigenschappen en legeringskenmerken
- Preparatie en magnetische eigenschappen van kobalt-gedoteerde FeMn2O4-spinel-nanodeeltjes
- Op weg naar TiO2-nanovloeistoffen:deel 1:voorbereiding en eigenschappen
- Nanogestructureerde Silica/Gold-Cellulose-Bonded Amino-POSS Hybrid Composite via Sol-Gel Process en zijn eigenschappen
- Eigenschappen en toepassingen van kopernikkellegeringen
- VDM® Legering 40 B