Fraunhofer IFAM automatiseert de voormontage van CFRP-rompframes
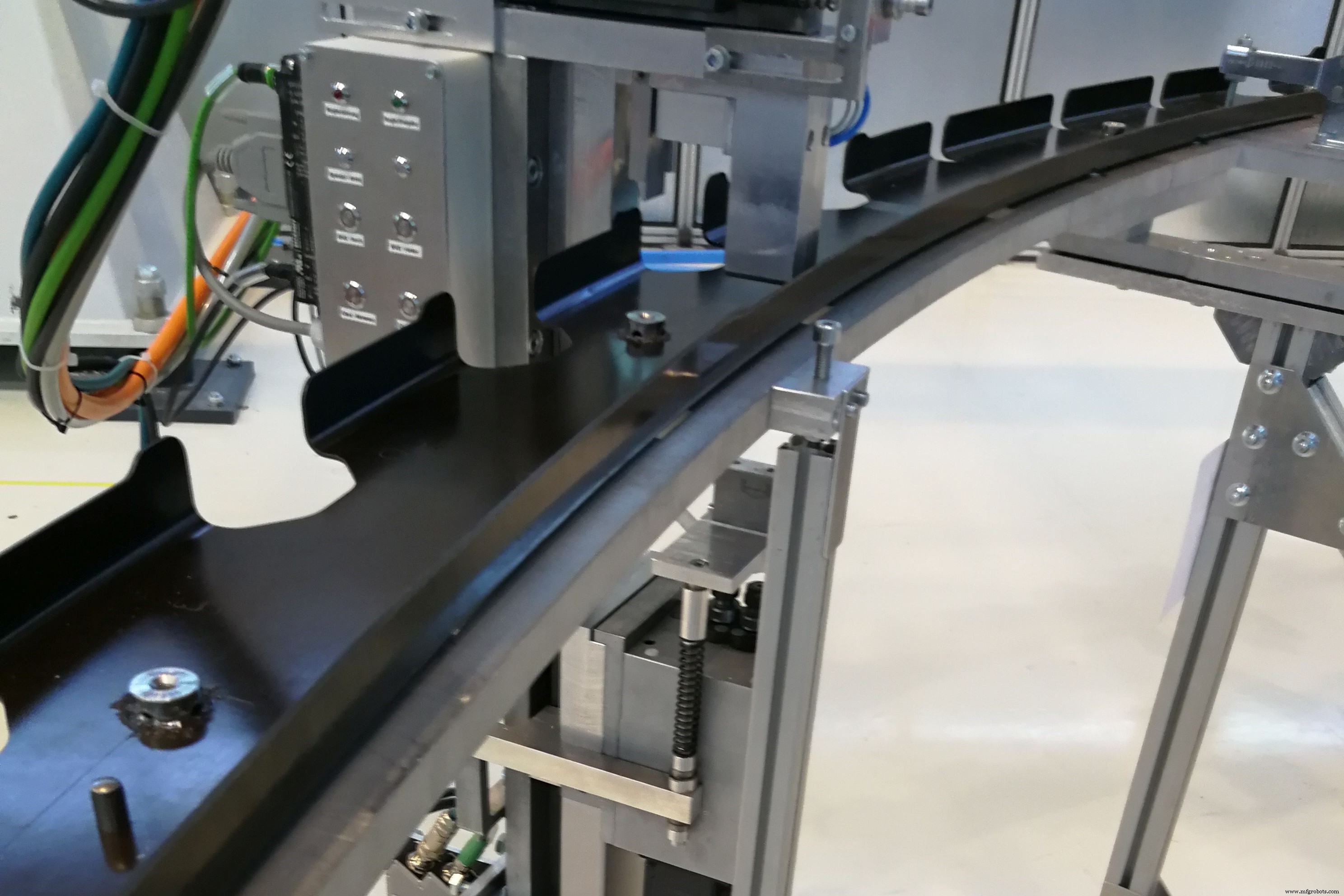
Automatisering is een van de belangrijkste strategieën om de efficiëntie in de productie te verhogen. Een nieuwe positionerings- en booreindeffector is ontwikkeld binnen het project "Impulse" - gefinancierd door het Duitse federale ministerie van Economische Zaken en Energie (BMWi) - en het "Tempo" ("Technologieën voor de efficiënte montage en productie van CFRP-rompcomponenten ”) subproject.
Deze eindeffector automatiseert de voormontage van verstijvingselementen (schoenplaatjes) op integrale CFRP-frames voor de vervaardiging van vliegtuigrompen. De vorige handmatige productie vereiste ook meer processtappen. Als alternatief kan de compacte eindeffector ook worden opgepakt door standaard industriële robots. Dit maakt een verhoging van de productiesnelheid mogelijk, zowel met constante kwaliteit als tegen lagere kosten.
Deze automatiseringsoplossingen, ontwikkeld door partners Airbus Hamburg (Duitsland) en Fraunhofer Institute for Manufacturing Technology and Advanced Materials (IFAM, Stade), zijn al gevalideerd in een bijna-serieproductie-omgeving op een volledig prototype. Het project is in 2020 succesvol afgerond.
Voormontage van CFRP-frames
Frames zijn de dwarse verstijvingselementen in een vliegtuigromp. Het gebruik van CFRP en de innovatieve, integrale constructie van rompen in de Airbus A350 bespaart gewicht en productiestappen. Extra verstevigingselementen (klampen) zijn nodig om te voorkomen dat het frame zijwaarts doorbuigt. De ribben - die tot 6 meter lang kunnen zijn - verschillen allemaal geometrisch van elkaar, zodat voor elke ribbe een speciaal malsjabloon nodig zou zijn om de componenten handmatig te voorzien van meenemers met toleranties tot 0,2 millimeter. Deze sjablonen zijn duur en complex in gebruik. Bovendien vereisen handmatige invoer en voormontage grote verschillen. Uitgebreide meetstappen op de samengevoegde onderdelen voor exacte positie-uitlijning zouden ook essentieel zijn.
“Het ‘Tempo’-project stelde ons voor de uitdaging om de processtappen zo te automatiseren dat zowel de duur als de complexiteit van het proces wordt verminderd”, legt Leander Brieskorn, projectmanager van Fraunhofer IFAM, uit. “De schoenplaatjes moeten automatisch worden opgepakt en naar het frame worden gevoerd. Om het frame en de schoenplaat aan elkaar te klinknagelen, was het toen noodzakelijk om door beide componenten te boren. Dit hebben we bereikt door het frame uit te rusten met de schoenplaatjes met behulp van onze nieuw ontwikkelde, uiterst nauwkeurige eindeffector. Bovendien werd het frame zonder gaten op de romp gemonteerd in onze bijna-serie rompassemblagefabriek in Stade.”
Positionerings- en booreindeffector voor geautomatiseerde, uiterst nauwkeurige en kwaliteitsverzekerde voormontage van integrale CFRP-frames
De ontwikkelde positionerings- en booreindeffector vervult de taken van het ontvangen van verschillende schoenplaten, het positioneren ervan op verschillende integrale frames en het gelijktijdig dubbel boren van beide componenten. De compact gebouwde eindeffector kan zowel door het gebruikte portaalsysteem als door standaard industriële robots worden opgepakt. Het portaalsysteem is geselecteerd voor meer precisie bij het positioneren. Het integrale frame is op palen gespannen onder het portaal en kan met meerdere mechanische verstelmogelijkheden in de ruimte worden georiënteerd. De eindeffector heeft een symmetrische houder waarmee hij schoenplaatjes met verschillende oriëntaties kan oppakken en aan de houder kan klemmen. Met behulp van veergedempte mechanische aanslagen benadert het de respectievelijke verbindingsposities met lokale precisie. Terwijl het klampverstijvingselement van bovenaf op het integrale frameoppervlak wordt geplaatst en beide componenten worden vastgeklemd met behulp van een ingebouwd mechanisme, wordt het boorproces uitgevoerd vanaf de achterkant van het frame om te voorkomen dat de CFRP gaat rafelen. Een afzuiginstallatie vangt het ontstane boorstof op. Nadat de componenten zijn geboord, worden de posities van de schoenplaatjes op het frame bepaald. De schoenplaatjes kunnen dan aan het frame worden vastgeklonken.
De eindeffector kan worden bestuurd via een systeem-PLC en ontvangt zijn globale positiegegevens van geïmporteerde CAD-gegevens van de componenten. De nieuwe montagesituatie wordt aangepast via een snelle stroomopwaartse meting met een lasertracker. De innovatieve technologie maakt een betrouwbaar proces en een hoge positioneringsnauwkeurigheid mogelijk. Behalve het indrukken van de startknop op een bedieningspaneel, wordt al het andere automatisch uitgevoerd. De speciaal ontwikkelde gebruiksvriendelijke bedieningsinterface, met zelfverklarende afbeeldingen om de invoer te vergemakkelijken, stelt zelfs onervaren medewerkers in staat om snel vertrouwd te raken met de besturing van het systeem.
Door de juiste aanpassingen aan de schoenplaatopname aan te brengen, kan de eindeffector ook geometrisch enigszins verschillende soorten schoenplaten monteren en deze precies op verschillende soorten integrale frames positioneren. De nauwkeurigheid van de geautomatiseerde archivering is ± 0,1 millimeter en overtreft daarmee de nauwkeurigheidseisen met 200%.
De in de positioneer- en booreindeffector geïntegreerde meettechnologie documenteert exact de vereiste contactdruk van 200 Newton en vele andere parameters voor het bewaken van de optimale voorwaarden voor de voormontage van de meenemers op het integrale frame. Dit garandeert online kwaliteitsborging.
Verdere R&D-werkzaamheden in het deelproject “Tempo”
Het integrale frame uitgerust met schoenplaatjes werd geïnstalleerd op de rompschaal in een bijna-serie rompmontagesysteem in het "Tempo"-subproject in het technische centrum van Fraunhofer IFAM in Stade. De meting van de voegspleten tussen het integrale frame en de romphuid toonde aan dat ze allemaal kleiner waren dan 0,3 millimeter, waardoor extra spleetvulling niet nodig was.
De eindeffector ontwikkeld voor voormontage, positionering en boren van frames kan ook worden gebruikt voor de montage van componenten in andere industrieën, zoals windturbines, railvoertuigen, bedrijfsvoertuigen, automotive of scheepsbouw, door het montagesysteem aan te passen.
Na een periode van drie en een half jaar eindigde het onderzoeksproject "Impuls" ("Innovatieve, op middellange termijn implementeerbare en kostenbesparende oplossingen voor CFRP-rompcomponenten") gefinancierd door het Duitse federale ministerie van Economische Zaken en Energie BMWi in 2020 , inclusief het deelproject “Tempo”; BMWi financieringsnummer:20W1526F. De Fraunhofer IFAM wil de BMWi bedanken voor de verstrekte financiering.
vezel
- Oogmontuur
- BMW voor massaproductie van vastgeschroefd motorframe van koolstofvezel
- Maak een subtiel statement met deze kentekenplaatframes van koolstofvezel
- Fraunhofer IPT automatiseert de productie van thermoplastische CFRP-motorventilatorbladen
- 3D-printen van CFRP-mallen voor RTM-flaperon, exoskeletten en meer
- WMG prototypes CFRP frame voor Very Light Rail (VLR) demonstratievoertuig
- Arevo gaat Pilot 3D-geprinte composiet fietsframes produceren
- CFRP overtreft staal in precisiekogelgewrichten
- Plastic Omnium bevestigt positie in CFRP-waterstofopslagtanks
- REIN4CED gaat composiet fietsframes produceren voor Accell
- Duitse spoorbrug opgehangen aan CFRP-hangers