Gebruikmaken van grootformaat AM vergroot de flexibiliteit van de ruimtevaart
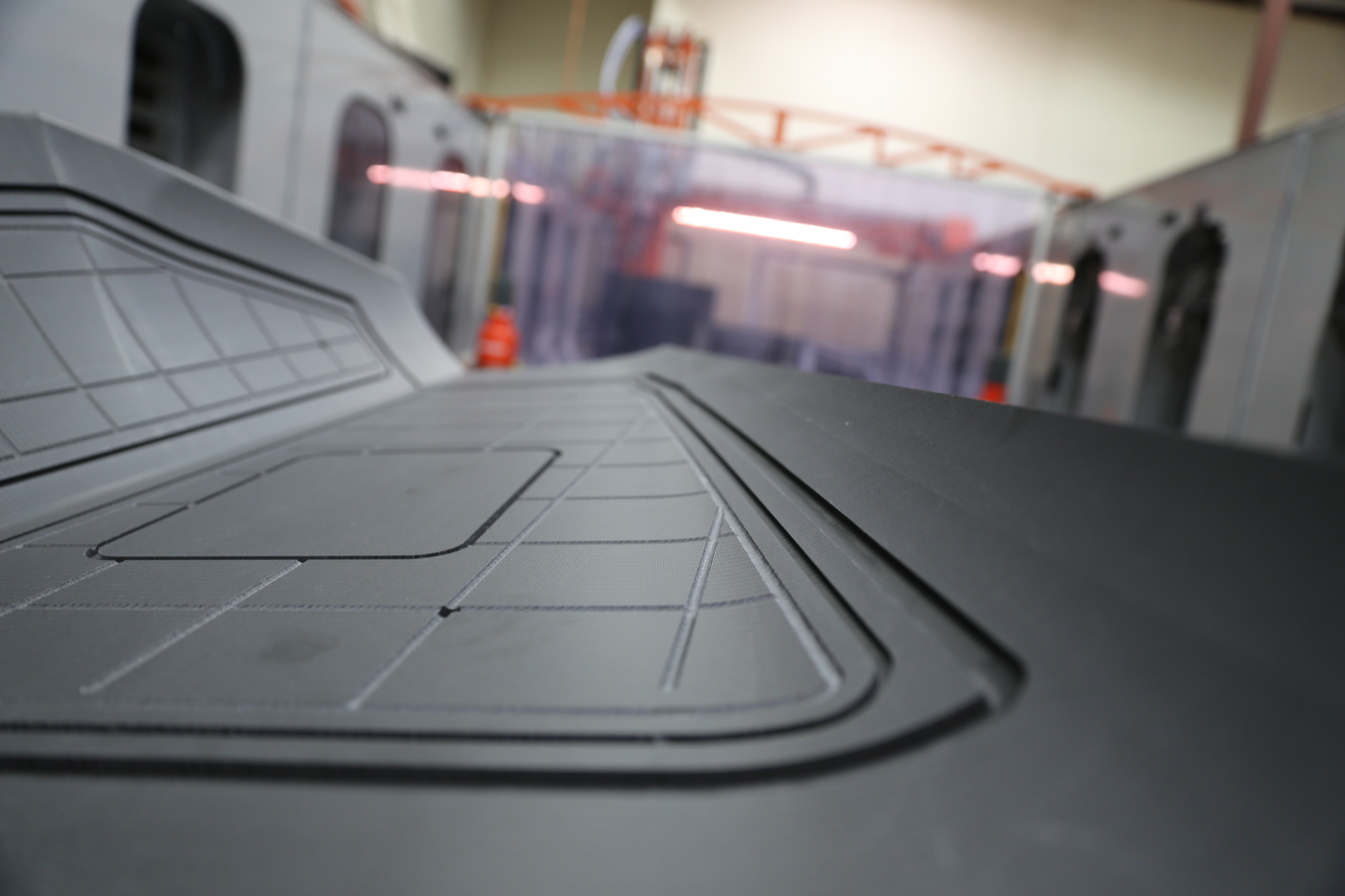
Ascent Aerospace (Macomb Township, Mich., V.S.; Santa Ana, Californië, V.S.) beschouwt zichzelf als 's werelds grootste leverancier van lucht- en ruimtevaartgereedschap en levert voornamelijk metalen oplossingen voor matrijzen, assemblage en trim- en boorinrichtingen. De focus van het bedrijf op het maken van matrijzen ligt op grote aerostructuren, zoals motorgondels, vleugels, rompen, rondhouten, stringers en frames. De trim- en booropspanningen worden gebruikt bij CNC-bewerkingen, robotlassen, automatische persen, inspectiesystemen en assemblagetoepassingen.
In 2018 begon het bedrijf te overwegen om additieve productie op groot formaat toe te voegen aan zijn Santa Ana-portfolio en voerde het een evaluatie uit van systemen, materialen en toepassingen op de markt. In het besef dat het een grootformaat machine nodig had die gereedschappen kon produceren van een formaat dat typisch is voor Ascent, investeerde het bedrijf in 2019 in een LSAM-systeem van Thermwood (Dale, Ind., VS) - een 10 x 40-voet dual-gantry/ dual-function, op extrusie gebaseerde additieve productiecel met aan de ene kant een grootformaatprinter en aan de andere kant CNC-bewerkingsmogelijkheden. Het systeem werd in het tweede kwartaal van 2020 geïnstalleerd, net toen de pandemie begon.
Sean Henson, wereldwijde productmanager composieten en additieve productie op de locatie in Santa Ana van Ascent, zegt dat hoewel de timing niet ideaal was, Ascent in staat was om de nieuwe LSAM onmiddellijk aan het werk te zetten en een maandenlange inspanning begon om de mogelijkheden en voordelen te begrijpen. en beperkingen van AM op groot formaat in een omgeving voor het maken van gereedschappen.
Ondanks de leercurve en de pandemie heeft Ascent in het eerste jaar van zijn werking meer dan 20 toolingprogramma's geleverd via de LSAM. Het grootste deel van dit werk was gericht op de productie van armaturen, vacuümtrimgereedschappen, prototypen en mallen. Voor sierlijsten gebruikte Ascent voornamelijk een ABS-hars van Techmer (Clinton, Tenn., V.S.) versterkt met 20 gew.% gehakte koolstofvezel. Voor toepassingen bij het maken van mallen die cycli bij hoge temperaturen vereisen, drukt Ascent af met polyethersulfon (PESU) of polyetherimide (PEI), beide versterkt met gehakte koolstofvezel. Ascent heeft ook, in een paar toepassingen, bedrukt met polycarbonaat (PC) omdat het iets betere eigenschappen biedt dan ABS en beter presteert bij hogere temperaturen. Henson zegt dat ongeveer 75% van de producten die met het LSAM-systeem worden gemaakt, voor gebruik op kamertemperatuur zijn, terwijl de rest bestemd is voor temperatuurwisselingen. Van de mallen die temperatuur kunnen zien, zijn sommige matrijzenmeesters en ontworpen voor omgevingen van <200 °F, terwijl andere zijn ontworpen voor autoclaafuitharding tot 350-400 °F en een druk van 100 psi.
Dus, wat is het grootste voordeel van LSAM? Snelheid en kosten, zegt Henson. De doorlooptijd van een door LSAM gemaakte mal is de helft van die van een metalen mal en ook de materiaalkosten zijn lager. "Dus snelheid is enorm", zegt Henson. “De reden dat we naar grootformaatadditieven gingen, waren de materiaaldepositiesnelheden en precies de hoeveelheid die we kunnen bouwen omdat onze tooling groot is. We kunnen heel snel heel grote dingen bouwen. Onze afdrukken duren doorgaans tussen de acht en 15 uur. In die tijd zijn we in staat om gereedschappen te fabriceren die tot 1.000 of 1.500 pond materiaal kunnen wegen. We kijken dus naar een voetafdruk van 13 tot 14 voet lang en 1,5 voet hoog en we drukken die in minder dan een dag af."
Omdat Ascent een machine met dubbele portaal/dubbele functie heeft, kan het bovendien mallen tegelijk printen en afwerken. "Het heeft wel het dubbele portaal", merkt Henson op. “Dus we hebben de mogelijkheid om op de ene helft van het systeem af te drukken en de machine op de andere helft, en we kunnen die onafhankelijk uitvoeren, zodat we iets kunnen printen dat 10 tot 15 voet lang is en iets aan de andere kant van de machine kunnen bewerken. tabel met dezelfde lengte, en voer die bewerkingen tegelijkertijd uit." Henson merkt ook op dat omdat printen en afwerken op dezelfde machine plaatsvinden, de "router weet waar de printer materiaal heeft neergelegd", wat het downstream-bewerkingsproces versnelt. Voor de juiste toepassing en de juiste klant, zegt Henson, levert 3D-printen een afgewerkt, bruikbaar product sneller op dan mogelijk is met enig verouderd materiaal of proces.
De nadelen? Er zijn er een paar, te beginnen met het bijna netvormige aspect van 3D-printen met een grote extruder. "Alles wat we doen is een overbouw met machinale bewerking na het proces", benadrukt Henson. “De afweging die je maakt om zo snel mogelijk zoveel materiaal neer te zetten als de LSAM kan, is de resolutie van je prints. Onze [geëxtrudeerde] kralen zijn meer dan driekwart inch breed en ongeveer een kwart inch hoog. Als je naar een geprint stuk kijkt, kun je die sint-jakobsschelpen zien, je kunt ze voelen. Het is een FDM-puntlaag, net 100 keer opgeblazen. En dus is er voor elk type glad oppervlak, of het nu een temperatuurmal of een trimgereedschap of zelfs maar een glad prototype is, een bewerkingscomponent nodig om een fijnere afwerking te krijgen, vooral voor ruimtevaarttoepassingen.”

De tweede uitdaging ligt in het feit dat een met koolstofvezel versterkte thermoplast zich niet gedraagt zoals Invar, aluminium of staal. De anisotrope aard van vezelversterkte materialen betekent dat hun zeer variabele thermische uitzettingscoëfficiënt (CTE) in een mal tijdens thermische cycli het moeilijk kan maken om afgewerkte onderdelen te produceren die voldoen aan de dimensionale specificaties. "Dat is de grote uitdaging die we hebben aan de ontwerpkant en aan de printkant", zegt Henson. "Klanten zullen ons een definitieve vorm geven en dan moeten we wat modelleerwerk doen om erachter te komen hoe de tool eruit moet zien, zowel vanuit een structureel oogpunt als vanuit een CTE-standpunt." Henson zegt dat Ascent aan het leren is om de CTE-variabiliteit in zijn ontwerpen aan te passen, vertrouwend op vallen en opstaan, gegevens die zijn afgeleid van eerdere afdrukprogramma's en feedback van klanten om het te helpen zijn ontwerpmogelijkheden te verfijnen.
Henson zegt dat deze kosten-batencombinatie - CTE versus snelheid en kosten - betekent dat de LSAM-mogelijkheden zorgvuldig moeten worden ingezet, waarbij de applicatievereisten worden afgewogen tegen de leverbare deadline. "Dit is echt een goede manier om een tool in een kwestie van weken te krijgen, in plaats van een paar maanden", zegt Henson. “Maar wees je bewust van de compromissen. Als je verwacht dat het reageert als een Invar-tool, waar je een perfect onderdeel krijgt, zal het dat niet doen. Maar voor veel klanten, en vooral veel R&D- en ontwikkelingsklanten, is het een heel goede manier om snel aan een tool te komen.”
Dat gezegd hebbende, ten minste één van de mallen die Ascent met zijn LSAM heeft geprint, is al in gebruik voor de productie van een vliegend vliegtuig, en er zullen er zeker nog volgen. En het bedrijf stelt zich een dag voor, niet te ver weg, waarop het zijn LSAM-capaciteit maximaal heeft en meer moet toevoegen. Het eigendom van het bedrijf, zegt Henson, ziet het potentieel van 3D-printen en ondersteunt het uitgebreide gebruik ervan ten zeerste.
Hars
- Waarom de lucht- en ruimtevaartindustrie dol is op plastic materialen
- Vespel®:het ruimtevaartmateriaal
- Koolstofvezel in ruimtevaarttoepassingen
- Collins Aerospace neemt thermoplastische onderdelenfabrikant Dutch Thermoplastic Components over
- Kaneka Aerospace behaalt AS9100D ruimtevaartcertificering
- Een zeer gespecialiseerde speler in een team van wereldklasse
- Kenmerken van Aerospace-prototyping
- Sensorfilm voor ruimtevaart
- Toleranties voor het gieten van aluminium in de ruimtevaart
- Additieve productie in de lucht- en ruimtevaart
- Sandvik Coromant in de ruimtevaart